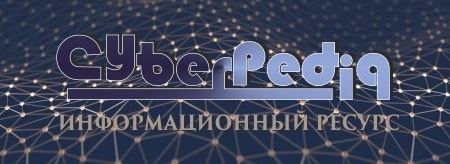
Поперечные профили набережных и береговой полосы: На городских территориях берегоукрепление проектируют с учетом технических и экономических требований, но особое значение придают эстетическим...
Биохимия спиртового брожения: Основу технологии получения пива составляет спиртовое брожение, - при котором сахар превращается...
Топ:
Техника безопасности при работе на пароконвектомате: К обслуживанию пароконвектомата допускаются лица, прошедшие технический минимум по эксплуатации оборудования...
Генеалогическое древо Султанов Османской империи: Османские правители, вначале, будучи еще бейлербеями Анатолии, женились на дочерях византийских императоров...
Интересное:
Средства для ингаляционного наркоза: Наркоз наступает в результате вдыхания (ингаляции) средств, которое осуществляют или с помощью маски...
Инженерная защита территорий, зданий и сооружений от опасных геологических процессов: Изучение оползневых явлений, оценка устойчивости склонов и проектирование противооползневых сооружений — актуальнейшие задачи, стоящие перед отечественными...
Лечение прогрессирующих форм рака: Одним из наиболее важных достижений экспериментальной химиотерапии опухолей, начатой в 60-х и реализованной в 70-х годах, является...
Дисциплины:
![]() |
![]() |
5.00
из
|
Заказать работу |
Задание к курсовой работе
Вариант <0> б: Рассчитать отделение помола цемента на цементном заводе производительностью 1,2 млн. тонн в год с выпуском портландцемента с минеральными добавками марки 500 в количестве 20% и сульфатостойкого шлакопортландцемент марки 500 в количестве 80%. Состав цементной шихты для портландцемента с минеральными добавками (цемент №6): клинкер - 81%, доменный гранулированный шлак - 14%, двуводный гипс - 5%; для сульфатостойкого шлакопортландцемента (цемент № 15): клинкер - 80%, диатомит - 15%, двуводный гипс - 5%. Влажность шлака - 21%, диатомита - 18%. Устанавливаются мельницы размером 5,2 × 16,5 м, работающие в закрытом цикле. Коэффициент заполнения мельниц - φ = 0,26. тонкость помола по остатку на сите с сеткой 008 для цемента №6 - 6%, для цемента №15 - 3%.
Введение
Цемент - важнейший строительный материал. В строительной практике он применяется уже более 150 лет. Крупные научные открытия, послужившие основой создания новых видов цемента и улучшения качества существующих, относятся к последним пяти десятилетиям, причем большинство из них принадлежит советским учёным.
Главные виды цемента, выпускающиеся в настоящее время - это портландцемент, шлакопортландцемент, пуццолановый цемент. Основой всех этих видов цемента является клинкер, получаемый путём обжига в печах сырьевой массы. Обжиг может производится в печах вращающегося или шахтного типа. Из-за малой производительности печей шахтного типа, обжиг в них применяют крайне редко.
При обжиге во вращающихся печах, клинкер получают двумя способами: сухим и мокрым. При мокром способе сырьё поступает в печь в виде полужидкой массы - шлама, с содержанием воды около 40% от общей массы. При сухом способе, сырьевые материалы, обычно предварительно подсушенные, измельчаются и подаются на обжиг в виде порошкообразной массы.
На отечественных заводах наибольшее распространение получил мокрый способ производства цемента. Общая технологическая схема этого способа выглядит следующим образом: 1) добыча сырья и доставка его на сырьевой склад завода; 2) дробление и мокрый помол сырья; 3) корректирование сырьевой массы - доведение её до нужного химического состава; 4) подготовку топлива для обжига шлама; 5) обжиг шлама и получение полупродукта - клинкера; 6) помол клинкера и получение цемента.
Основными видами сырья для производства цемента являются глина и известняк. Доставка сырья в сырьевой цех осуществляется различными транспортирующими установками (ленточные транспортёры, железнодорожный и автомобильный транспорт, воздушноканатные дороги т.п). Известняк, поступивший в сырьевой цех, измельчается в дробилках. Тип дробилки и её производительность определяется производительностью завода и физическими свойствами сырья.
Для измельчения глины и перемешивания её с водой применяют валковые дробилки и глиноболтушки. Дробление известняка на современных заводах осуществляется в две стадии. В дробилках первичного, крупного дробления известняк измельчается до размеров 200 - 300 мм, а затем в дробилках мелкого, вторичного дробления, на куски размером 25 - 30 мм.
Мелкодроблёный известняк и глина с водой направляются в шаровую мельницу для дальнейшего тонкого измельчения. В эту мельницу вода подаётся из расчёта, чтобы готовая сырьевая масса имела влажность 36 - 40%. Готовый шлам центробежными насосами транспортируется для хранения в цилиндрические бассейны. Если шлам нужно корректировать по химическому составу, его перекачивают из одного бассейна в другой.
Для хранения готового, откорректированного шлама используют горизонтальные прямоугольные или цилиндрические бассейны. В этих бассейнах шлам перемешивается с помощью пневмомеханических мешалок. Из горизонтальных бассейнов шлам перекачивается в питательные устройства печи. Питатели обеспечивают равномерную, в определённых количествах, подачу шлама на обжиг в печь.
При вращении печи. Шлам под действием силы тяжести перемещается к разгрузочному концу. Навстречу ему движется поток горячих газов. После целого ряда физических и химических превращений шлам перемещается в зону спекания. Здесь при температуре 1450 - 1550◦ происходит спекание шлама: из простой смеси глины и известняка он превращается в новый продукт - цементный клинкер.
Достигнув разгрузочного конца печи, клинкер попадает в холодильник. Охлажденный клинкер транспортирующими устройствами подается на клинкерный склад. На этом же складе хранятся добавки (трепел, шлак, гипс и т.п.). Используя те или иные добавки, можно получить различные виды цемента. Для получения готового цемента клинкер вместе с добавками подают в мельницы тонкого помола. Загрузка бункеров мельниц осуществляется грейферными кранами.
Для помола клинкера применяются трубные мельницы диаметром до 3,2 м. и длиной до 15 м. Во время работы внутреннюю полость цементной мельницы необходимо вентилировать, чтобы удалять водные пары и снижать температуру выходящего цемента. Пылевоздушная смесь из мельницы поступает в фильтр, в котором улавливается и осаждается тонкая цементная пыль, вынесенная воздушным потоком при движении через внутреннюю полость мельницы.
Готовый цемент обычно с помощью пневматических транспортирующих устройств из мельницы подается для хранения в железобетонные емкости, именуемые силосами. Из силосов цемент поступает в упаковочные отделения, где специальные машины упаковывают его в специальные мешки, или же специальными пневматическими устройствами подается непосредственно в железнодорожные вагоны.
Кроме основного технологического оборудования, применяемого в производстве цемента, цементные заводы снабжаются различными вспомогательными установками и транспортирующими устройствами. На каждом заводе имеется насосные станции, подающие воду для производственных и бытовых нужд, и компрессорные станции для получения сжатого воздуха и подачи его в производственные цехи.
Расчёт сушильного отделения
Необходимость сушки активных минеральных добавок, измельчаемых совместно с клинкером, определяется высокой влажностью добавок. Доменные гранулированные шлаки также имеют высокую влажность, так как их получают грануляцией огнненожидкого шлама в специальных водных бассейнах. Содержащаяся в добавках влага начнёт реагировать с клинкерной частью цемента и качество его в результате преждевременной гидратации резко ухудшится. Кроме того тонко измельчённый материал налипает на мелющие тела, броневые плиты, замазывает междукамерные и разгрузочные перегородки мельницы, затрудняя или полностью прекращая в ней измельчение.
Так как в цементах 6 и 15 разные добавки, то расчёт сушильного отделения будем производить отдельно для доменного шлака, имеющего влажность 21 %, и отдельно для диатомита влажностью 18 %.
Производительность сушильного барабана для шлака
Выход высушенного шлака
Qбш = (1000×Q)/3600 = (1000×3,835)/3600 = 1,065 кг/сек.
где Q - количество материала, нуждающегося в сушке (по высушенной массе), т/час;
Выход влаги Qwш
Qwш = Qобщ (Wн/(100 - Wн)-Wk/(100 - Wk)) = 1,065×
×(21/(100 - 21) - 1/(100 - 1)) = 0,272 кг/сек.
где Wн - начальная влажность материала,%к - конечная влажность материала, % (0,5 - 1,0 %).
Производительность сушильного барабана для диатомита.
Выход высушенного диатомита:
Qбд = 1000×Q / 3600 = 1000×16,438 / 3600 = 4,566 кг / сек.
Выход влаги Qwд = Qбд×(Wн/(100 - Wн) - Wk/(100 - Wk)) = 4,566×(18/(100-18) - 1/(100 - 1)) = 0,956 кг/сек.
Определение рабочего объёма сушильного барабана для шлака и выбор его по таблицам.
V = 3600×Qwш/А = 3600×0,272/55 = 17, 8 м³
Где А - удельный паросъём, кг/(м³ч), для шлака 55 - 60 кг/(м³ч), для остальных материалов А = 45 - 55 кг/(м³ч).
Время прохождения материала через сушильный барабан:
τ = (120×β×ρ×(Wн - Wk))/(А(200×(Wн - Wk))) =
= (120×500×0,2×(21 - 1)/(55×(200×(21 -1))) =
= 24,2 минуты.
где ρ - средняя насыпная плотность материала, кг/м³,
β - коэффициент заполнения барабана в долях единицы, β = 0,2.
Необходимая мощность привода для вращения барабана N (кВт):
N = 0,0013×Dб³×Lб×n×ρ×δ = 0,0013×2,2³×14×3,6×500×0,02 =
= 7 кВт
где - D, L диаметр и длина барабана, мчастота вращения выбранного барабана
ρ средняя насыпная плотность 500 кг/м³
δ коэффициент учитывающий вид теплообменных устройств в барабане, δ = 0,04 - 0,07 для лопастного теплообменника или при навеске цепей, и δ = 0,01 - 0,02 для ячейково - сепараторного теплообменника.
Из выпускаемых сушильных барабанов наиболее оптимальным является СМЦ - 440.
Размеры барабана:
D = 2,2 м, L = 14 м, V = 53 м³
Наклон барабана 1-4%
Производительность по сухому материалу 14 т/ч
Влажность материала:
На входе 22 %
На выходе 3 %
Частота вращения барабана 3,6 об/мин
Мощность привода двигателя 36 кВт
Масса 35 тонн.
Определение рабочего объёма сушильного барабана для сушки диатомита и выбор его по таблицам.
Рабочий объём сушильного барабана для диатомита
Vд = 3600 Qwд / А = 3600×0,95 / 45 = 76,48 м³
где А - удельный паросъём кг/(м³×ч) = 45 - 55 кг/(м³×ч)
Время прохождения через сушильный барабан τ
τ = 120×β×ρ×(Wн - Wк) / (А×(200 - (Wн - Wк))) =
= 120×0,2×1100×(18 - 1)/ (45×(200 - (18 - 1))) = 54,50 мин.
где - β коэффициент заполнения барабана = 0,1 - 0,25;
ρ средняя насыпная плотность материала = 900 - 1100 кг / м³
Мощность привода для вращения барабана N (кВт)
N = 0,0013×Dб³×Lб×n×ρ×δ = 0,0013×2,8³×14×4,68×1100×0,02 = 41,13 кВт
где Dб, Lб диаметр и длина барабана,число оборотов выбранного барабана об/мин,
δ коэффициент, учитывающий вид теплообменных устройств = 0,01 - 0,02 Из выпускаемых сушильных барабанов подходит СМЦ - 429, имеющий характеристики:
Диаметр барабана 2,8 м
Длина барабана 14 м
Наклон барабана 5 %
Производительность по 20 - 25 т/ч сухому материалу
Влажность материала
на входе 20 - 22 %
на выходе 1 - 8 %
Частота вращения барабана 4,68 об \мин
Мощность привода двигателя 55 кВт
Масса 62,4 т
Подбор сепараторов
Воздушные сепараторы являются принадлежностью размольных установок, работающих по замкнутому циклу, и служат для разделения предварительно размолотого материала на отдельные фракции по крупности зёрен.
Воздушная сепарация осуществляется двумя способами: при первом способе, через сепаратор проходит пылевоздушный поток, из которого осаждаются лишь крупные частицы материала (крупка), а мелкие выносятся из него воздушным потоком и улавливаются дополнительными устройствами. При втором способе в сепаратор подаётся только материал, который подхватывается потоком воздуха, циркулирующим внутри сепаратора. Из сепаратора выходит крупная и мелкая фракция по различным патрубкам.
Для сепарации по первому способу применяются простые по конструкции проходные сепараторы, а для работы по второму способу используют более сложные по устройству центробежные сепараторы с замкнутым потоком воздуха.
Сепаратор для мельницы портландцемента №6.
Q = Qм×(1,20….1,40) = 182,3×(1,20…1,40) = 218,6….255,2 т/ч
где Qм - производительность мельницы по данному виду цемента.
Фирма «Полизиус» вместе с мельницей поставляет сепараторы Ø 7,3 м, производительностью 210 т/ч, частота вращения ротора 140 об/мин, максимально допустимое количество воздуха 2830 м³/мин.
Сепаратор для мельницы сульфатостойкого портландцемента №15.
Q = Qм×(1,20….1,40) = 146,0×(1,20….1,40) = 175,2….204,0 т/ч
Также применим сепаратор фирмы «Полизиус»
Общее количество сепараторов.
Сепараторы Ø7,3 м, Q воздуха = 2830 м³/мин, Q = 210 т/ч, 2 штуки.
Транспортное и вспомогательное оборудование.
Пневматические насосы
Производство цемента связано с перемещением внутри цехов и между цехами больших масс кусковых и порошкообразных материалов, а так же шлама. В процессе приготовления цемента роль транспортирующих устройств в такой же степени значительна, как и роль основных машин. Непрерывность производственных процессов и равномерность питания технологических установок сырьём, топливом и полупродуктом невозможно осуществлять при плохой работе транспортёров.
Узлы и детали транспортёров подвергаются чрезвычайно быстрому износу, поскольку все перемещаемые ими материалы обладают сильным абразивным действием, а часть из них, например, клинкер, выпадающий из холодильников печей, и цемент из трубных мельниц, имеют иногда высокую температуру. Всё это неблагоприятно отражается на работе транспортёров и требует большого внимания к выбору их конструкций, режимов работы и разработке методов ремонта.
Выбор пневмокамерных или пневмовинтовых насосов производят в зависимости от наибольшей производительности мельниц и расположения цементных силосов.
Qmax = 182,3 т/ч
Предлагаю установить на каждую мельницу 3 пневмокамерных насоса ТА - 28, соединённых параллельно. Третий насос является запасным, он будет использоваться при неисправности, техническом обслуживании или ремонте одного из двух других насосов.
Итого количество пневмокамерных насосов 6 штук.
Техническая характеристика насосов ТА - 28
Производительность, т/ч 100 - 125
Приведённая дальность подачи, м 1000
Внутренний диаметр трубопровода, мм 250
Рабочее давление сжатого воздуха, МПа 0,6
Расход сжатого воздуха, м³/мин 90,4
Масса, кг 14795
Расчёт компрессорной
Общая производительность 6-ти пневмокамерных насосов
Σ Qв = 6×90,4 = 542,4 м³/мин
Общий расход воздуха в цехе помола.
Вобщ = Σ Qв × 1,1 = 542,4 × 1,1 = 596,6 м³/мин ≈ 600 м³/мин
где - 1,1 коэффициент запаса
Из выпускающихся компрессоров выбираем поршневой компрессор 5Г - 100/8
Производительность 100 м³/мин
Рабочее давление 0,8 МПа
Число оборотов компрессора 187 об/мин
Мощность электродвигателя 625 кВт
Количество компрессоров:
n = Вобщ/К + 1 = 600/100 + 1 = 7 компрессоров
где - К производительность одного компрессора
Список используемой литературы
1. Борщ И.М., Вознесенский В.А., Мухин В.З. Процессы и аппараты в технологии строительных материалов. - Киев: Высшая школа, 1981.
. Бауман В.А. Механическое оборудование предприятий строительных материалов, изделий и конструкций. Москва. «Машиностроение» 1975.
.Боганов А.И. Механическое оборудование цементных заводов. Свердловск. «Машгиз» 1961.
. Краткий справочник технолога цементного завода. Москва. «Стройиздат» 1974.
. Крыхтин Г. С., Кузнецов Л.Н. Интенсификация работы мельниц Новосибирск «Наука» 1993.
. Колокольников В.С. Производство цемента. Москва. «Высшая школа». 1967.
. Сатарин В.И. Современные цементные заводы. Москва. Издательство литературы по строительству. 1967.
. Холина И.И. Справочник по производству цемента. Москва. Государственное издательство литературы по строительству, архитектуре и строительным материалам. 1963.
. Вальтер Г. Дуда. Цемент. Москва. Стройиздат. 1980.
Задание к курсовой работе
Вариант <0> б: Рассчитать отделение помола цемента на цементном заводе производительностью 1,2 млн. тонн в год с выпуском портландцемента с минеральными добавками марки 500 в количестве 20% и сульфатостойкого шлакопортландцемент марки 500 в количестве 80%. Состав цементной шихты для портландцемента с минеральными добавками (цемент №6): клинкер - 81%, доменный гранулированный шлак - 14%, двуводный гипс - 5%; для сульфатостойкого шлакопортландцемента (цемент № 15): клинкер - 80%, диатомит - 15%, двуводный гипс - 5%. Влажность шлака - 21%, диатомита - 18%. Устанавливаются мельницы размером 5,2 × 16,5 м, работающие в закрытом цикле. Коэффициент заполнения мельниц - φ = 0,26. тонкость помола по остатку на сите с сеткой 008 для цемента №6 - 6%, для цемента №15 - 3%.
Введение
Цемент - важнейший строительный материал. В строительной практике он применяется уже более 150 лет. Крупные научные открытия, послужившие основой создания новых видов цемента и улучшения качества существующих, относятся к последним пяти десятилетиям, причем большинство из них принадлежит советским учёным.
Главные виды цемента, выпускающиеся в настоящее время - это портландцемент, шлакопортландцемент, пуццолановый цемент. Основой всех этих видов цемента является клинкер, получаемый путём обжига в печах сырьевой массы. Обжиг может производится в печах вращающегося или шахтного типа. Из-за малой производительности печей шахтного типа, обжиг в них применяют крайне редко.
При обжиге во вращающихся печах, клинкер получают двумя способами: сухим и мокрым. При мокром способе сырьё поступает в печь в виде полужидкой массы - шлама, с содержанием воды около 40% от общей массы. При сухом способе, сырьевые материалы, обычно предварительно подсушенные, измельчаются и подаются на обжиг в виде порошкообразной массы.
На отечественных заводах наибольшее распространение получил мокрый способ производства цемента. Общая технологическая схема этого способа выглядит следующим образом: 1) добыча сырья и доставка его на сырьевой склад завода; 2) дробление и мокрый помол сырья; 3) корректирование сырьевой массы - доведение её до нужного химического состава; 4) подготовку топлива для обжига шлама; 5) обжиг шлама и получение полупродукта - клинкера; 6) помол клинкера и получение цемента.
Основными видами сырья для производства цемента являются глина и известняк. Доставка сырья в сырьевой цех осуществляется различными транспортирующими установками (ленточные транспортёры, железнодорожный и автомобильный транспорт, воздушноканатные дороги т.п). Известняк, поступивший в сырьевой цех, измельчается в дробилках. Тип дробилки и её производительность определяется производительностью завода и физическими свойствами сырья.
Для измельчения глины и перемешивания её с водой применяют валковые дробилки и глиноболтушки. Дробление известняка на современных заводах осуществляется в две стадии. В дробилках первичного, крупного дробления известняк измельчается до размеров 200 - 300 мм, а затем в дробилках мелкого, вторичного дробления, на куски размером 25 - 30 мм.
Мелкодроблёный известняк и глина с водой направляются в шаровую мельницу для дальнейшего тонкого измельчения. В эту мельницу вода подаётся из расчёта, чтобы готовая сырьевая масса имела влажность 36 - 40%. Готовый шлам центробежными насосами транспортируется для хранения в цилиндрические бассейны. Если шлам нужно корректировать по химическому составу, его перекачивают из одного бассейна в другой.
Для хранения готового, откорректированного шлама используют горизонтальные прямоугольные или цилиндрические бассейны. В этих бассейнах шлам перемешивается с помощью пневмомеханических мешалок. Из горизонтальных бассейнов шлам перекачивается в питательные устройства печи. Питатели обеспечивают равномерную, в определённых количествах, подачу шлама на обжиг в печь.
При вращении печи. Шлам под действием силы тяжести перемещается к разгрузочному концу. Навстречу ему движется поток горячих газов. После целого ряда физических и химических превращений шлам перемещается в зону спекания. Здесь при температуре 1450 - 1550◦ происходит спекание шлама: из простой смеси глины и известняка он превращается в новый продукт - цементный клинкер.
Достигнув разгрузочного конца печи, клинкер попадает в холодильник. Охлажденный клинкер транспортирующими устройствами подается на клинкерный склад. На этом же складе хранятся добавки (трепел, шлак, гипс и т.п.). Используя те или иные добавки, можно получить различные виды цемента. Для получения готового цемента клинкер вместе с добавками подают в мельницы тонкого помола. Загрузка бункеров мельниц осуществляется грейферными кранами.
Для помола клинкера применяются трубные мельницы диаметром до 3,2 м. и длиной до 15 м. Во время работы внутреннюю полость цементной мельницы необходимо вентилировать, чтобы удалять водные пары и снижать температуру выходящего цемента. Пылевоздушная смесь из мельницы поступает в фильтр, в котором улавливается и осаждается тонкая цементная пыль, вынесенная воздушным потоком при движении через внутреннюю полость мельницы.
Готовый цемент обычно с помощью пневматических транспортирующих устройств из мельницы подается для хранения в железобетонные емкости, именуемые силосами. Из силосов цемент поступает в упаковочные отделения, где специальные машины упаковывают его в специальные мешки, или же специальными пневматическими устройствами подается непосредственно в железнодорожные вагоны.
Кроме основного технологического оборудования, применяемого в производстве цемента, цементные заводы снабжаются различными вспомогательными установками и транспортирующими устройствами. На каждом заводе имеется насосные станции, подающие воду для производственных и бытовых нужд, и компрессорные станции для получения сжатого воздуха и подачи его в производственные цехи.
Ассортимент выпускаемой продукции
Рассматриваемый цех выпускает цемент двух видов: портландцемент с минеральными добавками марки 500, и сульфатостойкий шлакопортландцемент марки 500.
Портландцементом называют вяжущее вещество, получаемое путём тонкого измельчения клинкера с гипсом и добавками и образующее при затворении с водой удобнообрабатываемое тесто, способное твердеть в воде или воздухе.
Химико-минералогический состав портландцементного клинкера характеризуется следующими показателями:
· Коэффициента насыщения кремнезёма известью - КН, представляющего собой отношение количества окиси кальция в клинкере, фактически связанного с кремнекислотой, к её количеству, теоретически необходимому для полного связывания кремнекислоты до трёхкальциевого силиката. Величина КН находится в пределах 0,85 - 0,95.
· Силикатным кремнезёмным модулем, представляющего собой отношение процентного содержания в клинкере кремнекислоты к сумме процентного содержания окислов алюминия и железа. Величина СМ находится в пределах 1,7 - 3,5.
· Глинозёмным модулем, представляющим отношение процентного содержания в клинкере окиси алюминия к процентному содержанию окиси железа. Величина ГМ для обычных портландцементов находится в пределах 1 -2,5.
Основные свойства портландцемента. Портландцемент представляет собой тонкий порошок серо - зелёного цвета. Его удельный вес 3,25. Объёмный вес в рыхлом состоянии γ - 1220 кг/м3, в уплотнённом состоянии путём вибрации γуп - 1780 кг/м3, угол естественного откоса φ = 41 - 42◦. Отличительной особенностью портландцемента является быстрое нарастание прочности, полная воздухостойкость, водостойкость в пресной воде, достаточная морозостойкость в растворах и бетонах.
Объёмные деформации. Наличие в составе затвердевшего цементного камня значительных масс гидросиликатных гелей обуславливает в зависимости от условий твердения возникновение деформаций усадки или набухания, величина которых в некоторой степени связана с минералогическим составом цемента.
Тепловыделение. В процессе твердения портландцемент выделяет тепло. Экзотермия цемента в большей степени зависит от его минералогического состава. Тепловыделение цемента зависит также от тонкости помола, количества воды затворения и температуры окружающей среды, т.е. от ряда условий характеризующих кинетику его гидратации. Поэтому расчётным путём невозможно точно установить величину тепловыделения данного цемента, даже если известен его минералогический состав.
Водопроницаемость бетонов и растворов на портландцементе в значительной степени зависит от состава последних и водоцементного отношения, в плотных бетонах она характеризуется маркой В 8 - 10.
Морозостойкость и коррозиеустойчивость портландцемента в основном зависят плотности бетона или раствора и минералогического состава цемента. Наименее морозостойки и коррозиеустойчивы цементы, имеющие в своём составе повешенные количества алюминатов кальция и трёхкальциевого силиката. Морозостойкость и коррозиеустойчивость бетона уменьшается с увеличением его пористости и повышением тонкости помола цемента.
Морозостойкость растворов и бетонов, приготовленных на цементах с добавками, как правило, ниже, чем у бетонов и растворов приготовленных без добавок. Поверхностно - активные и воздухововлекающие добавки увеличивают морозостойкость бетонов и растворов.
Сцепление со стальной арматурой бетона на портландцементе через 28 суток твердения составляет R сц = 50 кг/см2, отношение Rсц/R28= 0,14.
Портландцемент марки 500 применяется:
· Для изготовления сборных железобетонных конструкций
· Для гидротехнических сооружений (при службе в пресной воде), для наружных частей монолитного бетона массивных сооружений, для производства плит оболочек, находящегося в зонах переменного уровня воды
· Для аэродромного строительства
· При производстве бетонных работ с быстрой распалубкой и для зимних бетонных работ по способу ' термоса ' и с применением дополнительного подогрева (пропаривание, электроподогрев)
· Для производства асбестоцементных изделий
· Для дорожного строительства.
Не допускается применение портландцемента в подводных частях гидросооружений, подвергающихся воздействию морской или минерализованной воды без специальных мер защиты. Для этих сооружений следует применять различные специализированные портландцементы - сульфатостойкий, пуццолановый сульфатостойкий, пуццолановый для пресной воды, шлакопортландцемент.
Сульфатостойкий портландцемент отличается более высокой стойкостью в сульфатных водах.
Причиной разрушения отвердевшего цемента в воде, содержащей растворённые сульфаты, является взаимодействие сернокислого кальция с трёхкальциевым алюминатом клинкера. Образующийся при этом гидросульфоалюминат кальция, называющийся из-за своего разрушающего действия «цементной бациллой “, значительно увеличивается в объёме по сравнению с исходным трёхкальциевым алюминатом. Это вызывает появление в цементном камне растягивающих напряжений и последующее разрушение.
Получают этот цемент путём совместного помола цементного клинкера, гипса, и добавок. Химический и минералогический состав клинкера, используемого при производстве сульфатостойкого портландцемента, должен удовлетворять следующим требованиям:
Расчётное содержание трёхкальциевого силиката не более 50 %;
Расчётное содержание трехкальциевого алюмината не более 5 %;
Величина глинозёмного модуля не менее 0,7.
Расчётное содержание в клинкере суммы С3А + С4АF недолжно превышать 22 %.
Необходимость получения клинкера нормированного химико-минералогического состава предопределяет требования к сырью.
Весьма целесообразно использовать трепел либо диатомит или опоку в составе глинистого компонента.
В сульфатостойкий портландцемент не вводят активных минеральных добавок, и лишь при благоприятных условиях его службы в отдельных случаях (по соглашению между поставщиком и потребителем) допускается введение при помоле небольшого количества таких добавок. Последние должны отвечать ГОСТ 6269 - 54 на активные минеральные добавки к вяжущим веществам или в случае применения в качестве добавки гранулированных доменных шлаков - требованиям ГОСТ 3476 - 60 на шлаки доменные гранулированные для производства цементов. Сопротивляемость сульфатостойких портландцементов действию сульфатной агрессии повышается при введении в его состав поверхностно - активной добавки. Поэтому согласно ГОСТ 970 - 61 допускается введение в его состав сульфитно-спиртовой барды либо мылонафта.
По прочностным показателям этот цемент подразделяют на три марки: 400, 500, 600.
В связи с умеренным содержанием в клинкере трёхкальциевого силиката и малым содержанием трёхкальциевого алюмината сульфатостойкий портландцемент отличается от обычного портландцемента пониженным тепловыделением.
Присущие сульфатостойкому портландцементу свойства обуславливают и возможности его практического использования.
Наиболее целесообразно применять этот цемент для бетонных и железобетонных конструкций, в том числе и предварительно напряжённых, гидротехнических сооружений, подвергающихся сульфатной агрессии на переменном уровне горизонта воды, а также для изготовления свай, сооружения опор мостов, молов, предназначенных для службы в минерализованных водах.
Допускается применение сульфатостойкого портландцемента для подводных частей морских и океанских сооружений, однако для этих целей более экономичным является использование сульфатостойкого пуццоланового портландцемента. Поскольку в сульфатостойком портландцементе активные тепловыделяющие минералы (С3S и С3А) содержатся в малом количестве, его в отдельных частях можно применять вместо портландцемента с умеренной экзотермией в наружных зонах массивных гидротехнических сооружений.
Общие условия выбора системы дренажа: Система дренажа выбирается в зависимости от характера защищаемого...
История создания датчика движения: Первый прибор для обнаружения движения был изобретен немецким физиком Генрихом Герцем...
Опора деревянной одностоечной и способы укрепление угловых опор: Опоры ВЛ - конструкции, предназначенные для поддерживания проводов на необходимой высоте над землей, водой...
Особенности сооружения опор в сложных условиях: Сооружение ВЛ в районах с суровыми климатическими и тяжелыми геологическими условиями...
© cyberpedia.su 2017-2024 - Не является автором материалов. Исключительное право сохранено за автором текста.
Если вы не хотите, чтобы данный материал был у нас на сайте, перейдите по ссылке: Нарушение авторских прав. Мы поможем в написании вашей работы!