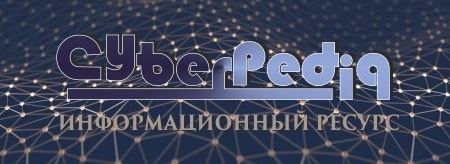
Архитектура электронного правительства: Единая архитектура – это методологический подход при создании системы управления государства, который строится...
Семя – орган полового размножения и расселения растений: наружи у семян имеется плотный покров – кожура...
Топ:
Оценка эффективности инструментов коммуникационной политики: Внешние коммуникации - обмен информацией между организацией и её внешней средой...
Организация стока поверхностных вод: Наибольшее количество влаги на земном шаре испаряется с поверхности морей и океанов...
Интересное:
Инженерная защита территорий, зданий и сооружений от опасных геологических процессов: Изучение оползневых явлений, оценка устойчивости склонов и проектирование противооползневых сооружений — актуальнейшие задачи, стоящие перед отечественными...
Искусственное повышение поверхности территории: Варианты искусственного повышения поверхности территории необходимо выбирать на основе анализа следующих характеристик защищаемой территории...
Подходы к решению темы фильма: Существует три основных типа исторического фильма, имеющих между собой много общего...
Дисциплины:
![]() |
![]() |
5.00
из
|
Заказать работу |
|
|
Программа тотальной оптимизации производства.
Этот метод был разработан компанией McKinsey и направлен на снижение себестоимости и повышение качества выпускаемой продукции. Основные задачи:
1) единовременное и существенное (40% от сокращаемых затрат) повышение эффективности, которое должно быть достигнуто в кратчайшие сроки;
2) создание внутри предприятия функций и механизмов, способных поддержать процесс преобразований в рамках программы тотальной оптимизации производства, превратить его в постоянный, эффективно работающий механизм, призванный обеспечить долговременное преимущество компании по затратам [27, с.5].
В ходе реализации программы тотальной оптимизации производства составляется полное описание функций производственных и непроизводственных служб предприятия, что служит основой для планирования численности персонала и разработки долговременных планов развития; используются идеи, исходящие от сотрудников, что порождает у них чувство сопричастности к изменению жизни компании, а это, в свою очередь, приводит к изменению корпоративного менталитета и способствует созданию системы постоянных, долгосрочных изменений.
Методология программы тотальной оптимизации производства существенно отличается от методологий, традиционно применяемых в программах повышения эффективности: она нацелена не только на повышение эффективности производства, но и на изменение мотивации и эффективности работы самих сотрудников. Только за счет хорошей мотивации на предприятии могут быть вовлечены в процесс выработки и реализации предложений практически все работники.
С целью внедрения программы тотальной оптимизации производства на предприятии должна быть создана центральная рабочая группа, в которую на конкурсной основе отбираются шесть человек из числа специалистов с переподчинением их директору по стратегическому развитию. Основными критериями отбора являются профессионализм, добровольность и стремление к самосовершенствованию и развитию. Затем проводится первая «пилотная волна» в трех – четырех цехах основного производства, для чего центральная рабочая группа разрабатывает этапы и время проведения программы тотальной оптимизации производства [27, с.15].
|
На первом этапе лидеры единицы (ответственные лица за проведение программы на местах) под руководством координаторов центральной рабочей группы приступают к сбору данных и заполнению специально разработанных форм с целью проведения анализа эффективности текущей деятельности подразделения, определения сократимых, частично сократимых и несократимых затрат. При этом в качестве начального постулата выдвигается предложение считать трудозатраты полностью сократимой величиной. Как правило, проведенный анализ обнаруживает множество упущений и недоработок начальников в различных структурных единицах. Одним из важных принципиальных моментов проведения тотальной оптимизации производства является «объявление амнистии» руководителям, так как «сведение счетов» моментально настроит организацию против проведения перемен, так как сотрудники станут тщательно скрывать информацию о реальном положении дел, и программа может оказаться под угрозой [27, с.25].
После этого переходят к следующим этапам программы тотальной оптимизации производства. Лидеры фиксируют все без исключения поступающие предложения. После проведения мозгового штурма идеи проходят предварительную оценку и сортируются по размеру экономического эффекта, риску внедрения, сроку внедрения (не более полугода, иногда до года) и простоте внедрения. Примерно 20% от общего числа поступивших предложений выносятся для окончательного решения на управляющий комитет, остальные отправляются на доработку. В состав Управляющего комитета, как правило, входят первые лица предприятия, которые, взвесив все «за» и «против», принимают решение по каждому предложению отдельно.
|
Не мало важный момент при проведении программы тотальной оптимизации производства – контроль внедрения. Группа контроллинга готовит подробный план мероприятий по внедрению со сроками внедрения и ответственными за внедрение лицами и оформляет приказ «О внедрении предложений программы ТОП». Как правило, при хорошей мотивации персонала, таких приказов много, и для облегчения их обработки создается специальная база данных, например, с применением Microsoft Excel», в которую входят такие разделы как, например [27, c.38]:
- № п/п;
- содержание идеи/предложения;
- № приказа о внедрении;
- подразделение, ответственное за внедрение;
- условно-годовой экономический эффект;
- дата внедрения;
- текущее состояние;
- фактический экономический эффект.
Данная база позволяет отслеживать «провинившихся», т.е. те подразделения, которые сорвали сроки внедрения того или иного мероприятия. Если причина невыполнения внедрения оказывается не уважительной, то виновнику предъявляется хозрасчетная претензия на сумму недополученной экономии. В то же время при своевременном внедрении должна быть предусмотрена премия не только лицам, подавшим предложения, но и лицам, содействовавшим его быстрому внедрению. Этот метод «кнута и пряника», как правило, оказывается весьма эффективным [27, с.41].
Группа контроллинга занимается не только контролем внедрения того или иного мероприятия, но и текущим состоянием дел по каждому предложению. За месяц до внедрения мероприятия, а затем за 10 дней, руководителю, ответственному за внедрение предложения, направляется карта контроля, в которой указан номер приказа, по которому он должен отчитаться за внедрение. Это является своеобразным напоминанием руководителям подразделений и способствует своевременному внедрению предложений. Если внедрение мероприятия сорвано по объективным причинам, руководитель подразделения оформляет карточку разрешения о переносе сроков внедрения на более поздний срок с обязательным указанием причины.
|
Как показывает опыт некоторых предприятий (например, компании McKinsey и ОАО «УАЗ») программа тотальной оптимизации производства способствует как повышению эффективности организации производственной деятельности предприятия, так и «выживанию» предприятия, находящегося на грани банкротства. Она побуждает руководство и работников к слаженной работе, инициативе, выдвижению предложений, анализ которых позволяет выявить «узкие» места на производстве и определить основные направления развития предприятия [27, с.60].
Обеспечение ритмичности производства. Наиболее полное определение ритмичности производства дается в работе [6, с.8]: «В общем виде ритмичность производства означает равномерность работы и выпуска продукции во всех звеньях предприятия». При этом отмечается, что «ритмичность выпуска в одинаковой мере определяется равным количеством одной и той же продукции и равными объемами различной продукции в каждом одинаковом периоде времени». А равномерность работы «достигается только при условии, если в каждый одинаковый период планируется и выполняется, по возможности, одинаковый или плавно возрастающий комплектный объем в нормо-часах, характеризующийся определенной структурой (соотношениями) между отдельными видами работ». В данном определении условиями ритмичности производства признаются и равномерность работы, и равномерность выпуска продукции.
Ритмичность является объективно необходимой для организации производственной деятельности и обеспечивает высокие технико-экономические показатели работы предприятия. Неритмичная работа наносит огромный ущерб. Она приводит, с одной стороны, к простоям оборудования и рабочих, использованию рабочих на работах, не соответствующих их квалификации, неполному использованию производственных площадей и снижению дисциплины и производительности труда, с другой – к штурмовщине, сверхурочной работе, снижению качества продукции [24, c.6].
Кроме замедления производственного цикла, оборачиваемости оборотных средств, увеличивается потребность в складских площадях, растут потери в связи с выплатами штрафов потребителям за просрочку выполнения договорных обязательств.
|
Сущность ритмичности производства заключается в непрерывности возобновления производства и выпуска продукции, которая означает, что всякий выход из производства готовой продукции должно быть компенсировано поступлением в производство через определенный ритм новой (неготовой) продукции, равнозначной по объему и структуре затрат и однородной по номенклатуре, по условиям изготовления. Именно в этом случае можно обеспечить рациональное использование рабочих в соответствии с их квалификации, оборудования (по мощности), технологического оснащения [36, c.4].
Организация ритмичного производства возможна только в том случае, если при разработке планов производства будут соблюдены принципы своевременности, пропорциональности, повторяемости, непрерывности и оптимальности.
Своевременность производства – это точное соблюдение (в количествах и сроках) директивного задания по выпуску продукции и ее движения по операциям производственного процесса.
Выполнение плана выпуска продукции по количеству, качеству, срокам и обеспечение комплектности оборудования, инструментов, приспособлений и состава рабочих возможно, если при разработке планов ритмичного производства в каждом отрезке планового периода будет соблюден принцип пропорциональности в объемах выпуска продукции, в объемах работ по каждой группе взаимозаменяемого оборудования и в объемах и структуре незавершенного производства. Это обеспечивает рациональное использование ресурсов предприятия [10, c.5].
Пропорциональность в объемах означает выпуск в каждом отрезке планового периода готовой продукции (заготовок, деталей, сборочных единиц, изделий) в объеме (в трудовом выражении), равном его среднему значению за один отрезок времени, пропорциональном составу трудовых затрат, обеспечивающих равную относительную пропускную способность рабочих мест и комплектное нарастание готовности предметов каждого типа [24, c.13]. Иными словами, подразделение должно выпускать продукцию равными количествами в равные отрезки времени (в трудовом выражении), эта продукция должна равномерно загружать каждую группу взаимозаменяемого оборудования и рабочих и должна обеспечивать стабильность связывания средств в незавершенном производстве. Объем выпуска и связывание средств должны быть или равновеликими, или максимально приближенными к таковым, или плавно возрастающими.
Номенклатура выпускаемой продукции может быть различной в каждом отрезке планового периода. Структура объема выпуска должна соответствовать структуре производственной мощности оборудования по отрезкам планового периода. Объем выпуска по отдельным видам работ должен быть или равновеликим по отрезкам планового периода, или максимально приближенным к таковым, или плавно возрастающим.
|
Выпуск готовой продукции в указанном объеме и структуре обеспечивает пропорциональность состава рабочей силы, оборудования и незавершенного производства, труда и потребления, объема платежеспособного спроса и объема товарооборота и тем самым – высокий уровень использования ресурсов [5, c.64].
Основным условием соблюдения принципа непрерывности в производстве должно быть обеспечение равенства длительности обработки партий предметов по каждой операции средней занятости рабочего места одной операцией. Чем точнее будет соблюдено это условие, тем меньше будут межоперационное время (время пролеживания), длительность цикла производства изделия и потребность в оборотных средствах [21, c.12].
Кроме пропорциональности ресурсов по объемам требуется пропорциональность их по времени использования, что достигается повторяемостью производственного процесса. Повторяемость производственного процесса повышает уровень использования оборудования, приспособлений, инструмента, создает предпосылки для специализации рабочих и тем самым для повышения производительности труда. Управление повторяемостью производственного процесса возможно только при условии разработки и организации ритмов выпуска продукции, являющихся важнейшими календарно-плановыми нормативами [23, c.15].
Кроме того, вышерассмотренные количественные пропорции ритмичного производства должны регулироваться принципом оптимума, вытекающего из объективных экономических законов, прежде всего – из закона, который предполагает максимально эффективное использование всех ресурсов, и закона неуклонного роста производительности труда [24, c.15].
Работа по обеспечению ритмичности производства должна состоять из двух основных частей. Первая заключается в более четком профилировании и, по возможности, более узкой специализации производственных подразделений, закреплении за каждым хозяйственным звеном – начиная с предприятия и кончая рабочим местом – строго ограниченной номенклатуры работ, подобранных по признаку конструктивно-технологической и организационно-плановой однородности. Вторая часть этой работы заключается в выполнении расчетов календарно-плановых нормативов, в построении объемных и календарных планов производства, учитывающих принципы ритмичности производства, в организации выполнения этих планов [16, c.24].
В современных условиях особенно возрастает значение календарно-плановых нормативов, поскольку только на их основе можно обеспечить своевременность, пропорциональность, повторяемость и непрерывность производственного процесса.
Своевременность производства обеспечивается разработкой таких нормативов, как длительность производственного цикла и опережение выпуска той или иной части изделия или операции относительно выпуска готового изделия. Основой для создания нормативов опережений является расчет длительности производственных циклов заготовок, деталей и сборочных единиц и построение графиков изготовления изделий [14, c.48].
Важнейшими календарно-плановыми нормативами, обеспечивающими пропорциональность ресурсов по объемам, являются размеры партий предметов (заготовок, деталей, сборочных единиц, изделий) и длительность их производственных циклов. Длительность производственного цикла определяет длительность нахождения изделия в процессе производства. Чем меньше затрачивается времени на производство изделий, тем меньше потребность в оборотных средствах в незавершенное производство.
Календарно-плановыми нормативами, обеспечивающими повторяемость производственного процесса, являются производственные ритмы. Производственный ритм представляет собой регулярное повторение через равные промежутки времени установленных норм и пропорций, обеспечивающих своевременность и эффективность выполнения плана выпуска готовой продукции. Повторяемость производственного процесса в определенной степени обеспечивается расчетом и соблюдением периодов повторения производства партий определенного наименования, т.е. отрезка времени между запуском в производство или выпуском из производства двух смежных партий одних и тех же предметов [37, с.190].
Период повторения производства зависит, прежде всего, от размера партии. В связи с различной трудоемкостью, сложностью, габаритными размерами, массой и другими параметрами частей изделий в производстве имеют место различные размеры партий предметов, входящих в одни и те же изделия. Крупные и трудоемкие детали и сборочные единицы обрабатываются партиями меньшего размера, чем мелкие и малотрудоемкие детали, изготовляемые на высокопроизводительном оборудовании, настройка которого требует длительного времени.
С одной стороны, размеры партий должны обеспечивать равенство объемов работ по операциям, что следует из условий пропорциональности, с другой стороны, число предметов в партии должно соответствовать потребности в них, определяемой планом выпуска изделий за тот или иной отрезок времени (день, неделю, декаду, половину месяца, квартал, полугодие, год), что диктуется удобством оперативно-производственного планирования и необходимостью создания условий для ритмичной работы [10, c.19].
В качестве показателя, обеспечивающего повторяемость производственных процессов, может использоваться групповой ритм выпуска продукции – отрезок времени между запуском в производство или завершением производства двух смежных однородных предметов или партий предметов.
Как следует из условий пропорциональности, признаками группирования могут быть: для деталей и заготовок – длительность производственного цикла; для сборочных единиц и изделий – длительность производственного цикла или объем работ, приходящийся на единицу длительности производственного цикла [24, c.17].
Таким образом, повторяемость производственного процесса может быть обеспечена за счет организации и соблюдения системы ритмов выпуска продукции, включающей периоды повторения производства, групповые ритмы выпуска однородных предметов или партий предметов, показатель соответствия запланированного объема выпуска продукции в тот или иной отрезок планового периода объему ритмичного выпуска.
Изложенное выше свидетельствует о том, что ведущая роль в организации ритмичного производства принадлежит календарно-плановым нормативам. Поэтому они должны быть научно обоснованными и прогрессивными, реальными для выполнения в конкретных условиях производства и учитывающими принципы ритмичности производства [24, c.21].
Размер партии предметов является важнейшим календарно-плановым нормативом. Он должен быть таким, чтобы обеспечивать пропорциональность длительности выполнения операций.
Одной из особенностей серийного производства является необходимость изготовления продукции партиями. Партией называется совокупность предметов одного наименования, количество которых заранее установлено, обрабатываемых или собираемых непрерывно на рабочем месте с однократной затратой подготовительно-заключительного времени [32, c.108].
Размер партии учитывается при определении длительности производственного цикла, периодов повторения производства, нормативного уровня незавершенного производства; распределении производственной программы по отрезкам планового периода; построении календарных и оперативных планов производства; нормировании технологических процессов. Он влияет на производительность труда, себестоимость продукции, использование оборотных средств, уровень использования оборудования и производственных площадей, сроки выпуска продукции, потребность в складских площадях, качество продукции и затраты на организацию и управление производством [20, c.159].
С увеличением размера партии растет производительность труда за счет сокращения затрат подготовительно-заключительного времени, приходящихся на один предмет, и за счет сокращения фактических затрат штучного времени на обработку предмета вследствие повышения производственных навыков исполнителя (врабатываемость).
При увеличении размера партии снижается себестоимость продукции за счет уменьшения заработной платы рабочих, приходящейся на один предмет, а также за счет уменьшении затрат на содержание диспетчерского и цехового линейного аппарата управления, на обслуживание рабочих мест. Уменьшение себестоимости единицы продукции происходит до определенного предела, при выходе за который она может увеличиваться за счет потерь от запаздывания выпуска продукции (доплат за сверхурочные работы, потерь в связи с дроблением партий предметов, штрафов за несвоевременную поставку продукции потребителям и т.д.). Выпуск продукции может запаздывать вследствие того, что производственное подразделение не может своевременно обработать большие партии предметов [5, c.27].
С увеличением размера партии повышается уровень использования оборудования вследствие сокращения доли подготовительно-заключительного времени, приходящейся на один предмет; появляется возможность увеличения выпуска продукции, упрощаются организация и управление производством, повышается их качество за счет уменьшения числа планово-учетных документов и объема информации.
Всякое увеличение размеров партии вызывает дополнительные издержки, связанные с необходимостью увеличения оборотных средств предприятия и с более медленной их оборачиваемостью в стадии производства. Оборотные средства увеличиваются в связи с пропорциональным увеличением количества и стоимости основных материалов и полуфабрикатов, поступающих одновременно в производство, объема и стоимости трудовых затрат, связанных в производстве до момента выхода готовой продукции, а также длительности цикла изготовления продукции.
С увеличением размера партии предметов может возникнуть дополнительная потребность в складских площадях.
Таким образом, размер партии предметов оказывает многостороннее и противоречивое влияние на экономику, организацию и управление производством. Это в определенной степени объясняет и то обстоятельство, что методика определения размеров партий предметов на протяжении многих лет является предметом изучения и дискуссий в специальной литературе. Однако этот вопрос до сих пор не получил полного решения. Применяемые в практике машиностроительных предприятий методы расчета размеров партий деталей и заготовок зачастую основаны на использовании отчетных данных прошлых периодов, хотя нормативы зависят от структуры формируемого плана. Определение размеров партий предметов требует дальнейшего исследования и совершенствования [24, c.24].
Вторым важнейшим календарно-плановым нормативом, обеспечивающим пропорциональность и своевременность производственного процесса и определяющим потребность в оборотных средствах в незавершенном производстве, является длительность производственного цикла [37, с.200].
Этот норматив необходим для технико-экономического и оперативно-производственного планирования. Без него нельзя правильно разработать производственную программу, согласовать во времени использование ресурсов и планы работ цехов, определить объемы выпуска продукции, потребность в оборотных средствах и прочие технико-экономические показатели.
Правильно рассчитанная длительность производственного цикла обеспечивает соблюдение принципа своевременности производства. Она предопределяет сроки запуска и выпуска изделий, своевременность снабжения цехов необходимой технологической оснасткой, сырьем, материалами и полуфабрикатами, сроки окончания технической подготовки производства.
Нормативная длительность производственного цикла изделия (партий изделий) определяется графо-аналитическим методом путем построения цикловых графиков изготовления изделия. Чтобы построить цикловой график, необходимо, прежде всего, определить длительность производственного цикла для той или иной части изделия – заготовок, деталей, сборочных единиц, общей сборки изделия. Поэтому для расчета столь важного норматива, прежде всего, нужна научно обоснованная методика [21, c.46].
Длительность цикла производства любой части изделия состоит из двух основных слагаемых: суммарной длительности выполнения технологических операций и межоперационного времени.
Первый параметр может быть величиной строго детерминированной и неизменной в течение определенного промежутка времени. Он может изменяться в основном при пересмотре размеров партий, норм времени, изменении технологии обработки, росте производительности труда [14, c.45].
Длительность производственного цикла в значительной степени определяется временем межоперационных перерывов, составляющим 50 – 80% всего времени производственного цикла.
Межоперационное время рассматривается как отрезок времени между окончанием обработки всей партии предметов на данной операции и началом выполнения следующей операции. Оно включает время: на контрольные операции; на транспортировку предметов к рабочему месту, где выполняется следующая операция; ожидания его освобождения от выполнения другой работы. Последнее возможно при закреплении за каждым рабочим местом нескольких операций.
В большинстве случаев время на выполнения вспомогательных операций – контроль качества и транспортирование предмета к рабочему месту, где выполняется следующая операция, - значительно меньше времени ожидания освобождения рабочего места. В тех случаях, когда операции сложны и трудоемки, время на их выполнение нормируется и включается в расчет аналогично времени выполнения основных технологических операций [35, c.122].
Суммарное и соответственно среднее значения межоперационного времени зависят от очередности запуска (выпуска) партий деталей. Причем эта величина тем меньше, чем раньше выпускаются и запускаются партии деталей с небольшой длительностью технологического цикла.
Поэтому для обеспечения наименьшего совокупного значения межоперационного времени следует при запуске деталей руководствоваться правилом: если начало обработки нескольких партий деталей на данном рабочем месте приходится на одно и то же время, то в первую очередь следует запускать партию деталей с минимальной остаточной длительностью технологического цикла. Если остаточная длительность у всех партий одинакова, то нужно запускать ту партию, у которой следующая по очереди операция имеет наименьшую длительность (правило кратчайшей операции) [24, c.45]. Первоочередной запуск и выпуск малооперационных и малотрудоемких партий деталей обеспечивает снижение оборотных средств в незавершенном производстве.
Учет очередности запуска предметов требует определения межоперационного времени конкретно по каждому предмету, только тогда длительность производственного цикла, являющаяся базой построения календарных планов, в совокупности с другими факторами обеспечит оптимальный запуск партий предметов [14, c.49].
Межоперационное время зависит также и от коэффициента загрузки оборудования. Из работ ученых следует, что между длительностью межоперационного времени и средним коэффициентом загрузки оборудования существует нелинейная зависимость: межоперационное время увеличивается с уменьшением коэффициента загрузки оборудования.
Таким образом, расчет межоперационного времени – весьма сложная проблема, поскольку методика нормирования этой величины должна учитывать все главные факторы, определяющие ее значение (очередность запуска, степень нарушения условия непрерывности производства и коэффициент загрузки оборудования).
Еще одним методом повышения эффективности деятельности предприятия является метод, разработанный компанией Toyota, «Производственная система Toyota». Этот метод, но с учетом особенностей российского автопроизводства, активно используется в настоящее время на предприятии ОАО «УАЗ» и позволяет достигать значительных результатов в области повышения эффективности производства.
Сердцевину любой экономики составляет производство, создание экономического продукта. Без производства не может быть потребления, именно предприятия выпускают продукцию, выполняют работы и услуги, то есть создают основу для потребления и преумножения национального богатства. Любое предприятие не может иметь хорошей перспективы, если не будет постоянно внедрять результаты научно-технического прогресса, так как от этого зависят качество выпускаемой продукции, издержки на ее производство. Себестоимость продукции является важнейшим качественным показателем работы предприятия, так как характеризует уровень использования всех ресурсов, находящихся в распоряжении предприятия. Управление издержками производства продукции с целью их минимизации на предприятии является составной частью управления предприятием в целом. Существенного снижения себестоимости продукции на предприятии можно достичь за счет эффективной организации производственной деятельности.
ГЛАВА 2 ОРГАНИЗАЦИЯ ПРОИЗВОДСТВЕННОЙ ДЕЯТЕЛЬНОСТИ В ОАО “УАЗ”
2.1 Организация производства ОАО “УАЗ” по методу “ПС ТОЙОТА”
Все процессы можно улучшать непрерывно. Некоторые усовершенствования могут быть постепенными, а некоторые резкими, но возможности улучшения следует постоянно иметь в виду всем группам, заинтересованным в деятельности предприятия.
Основной деятельностью рассматриваемого предприятия (ОАО “УАЗ”) является машиностроение, а именно – автомобилестроение. С целью создания эффективного производства с 2001 г. по 2002 г. на ОАО “УАЗ” работала программа “Тотальной оптимизации производства”, направленная на снижение себестоимости и повышение качества выпускаемой продукции. В ходе реализации программы тотальной оптимизации производства составлялось полное описание функций производственных и непроизводственных служб, что послужило основой для планирования численности персонала и разработки долговременных планов развития.
Программа тотальной оптимизации производства являлась важным этапом в истории предприятия и дала толчок к созданию производственной системы ОАО “УАЗ”, основные принципы которой представлены в приложении В.
Производственная система определяет саму основу организации труда и предполагает взаимодействие работников друг с другом без прямого вмешательства руководства. Это совершенно иная культура организации, принципиально иной стиль менеджмента и образ мышления. Хотя основные правила уже известны: четкое планирование, ритмичная работа, тщательный анализ всех отклонений на каждом рабочем месте, постоянное совершенствование системы мотивации и т.д.
Производственная система ОАО “УАЗ” основана на принципах работы компании Тойота, но с учетом особенностей российского автопроизводства. Она представляет собой определенную форму организации труда, которая позволяет работникам предприятия и специалистам выполнять свою работу качественно, быстро и с минимальными потерями.
Факт внедрения этих принципов позволил понять, что организовать производственную деятельность можно так, чтобы повысить качество, снизить издержки, повысить производительность, тем самым, повысить эффективность деятельности предприятия, без потерь для производственного процесса. Для этого специалистами ОАО “УАЗ” была разработана методика внедрения принципов производственной системы, методика улучшения на рабочих местах. Была организована учеба среди рабочих, специалистов, службы ИТР.
Внедрение производственной системы и создание эффективного производства происходит в соответствии с циклом улучшения, который содержит три основных этапа: определение; анализ; улучшение (таблица 2.1). Таблица 2.1 - Структура цикла «определение-анализ-улучшение»
Этап | Подэтап |
1. Определение | 1. Разработка задания 2. Формирование команды 3. Разработка процесса 4. Планирование работы |
2. Анализ | 1. Создание базы данных 2. Выявление проблем 3. Расстановка приоритетов |
3. Улучшение | 1. Выработка улучшений 2. выбор наилучшего варианта 3. Детальная разработка плана 4. Внедрение 5. Изучение результатов 6. Сообщение результатов 7. Институционализация подходов эффективного производства |
Цикл улучшения первоначально был разработан для помощи командам по совершенствованию существующих процессов. Любые процессы имеют свой жизненный цикл точно так же, как продукты и услуги. Они разрабатываются, внедряются, работают и в какое-то время ликвидируются. Все процессы следует постоянно анализировать для выявления возможностей их улучшения.
Внедрение производственной системы ОАО “УАЗ” ведется аналогично строительству дома. Схема “Дом ПС ОАО “УАЗ”” (приложение Г) является аналогом схемы “Дом TPS (производственная система Toyota)” [25, c.68]. Почему именно дом? Потому что дом – целостная структура. Чтобы дом был крепким и прочным, должны быть крепки и прочны все его составляющие. Слабое звено может разрушить всю систему.
Первый этап внедрения производственной системы ОАО “УАЗ” включает в себя: определение миссии и принципов предприятия, систему “Упорядочение”, визуализацию и стандартизацию процессов, устранение потерь и выравнивание производства, комплекс количественных показателей, позволяющих оценить надежность и стабильность производства.
Второй этап внедрения производственной системы ОАО “УАЗ”:
1) Система «точно вовремя» (JIT) и жесткая закладка, то есть такой производственный график, при котором колебания объемов и ассортимента будут минимальными. Сбалансированный производственный график поддерживает стабильность системы, помогая свести запасы к минимуму. Резкие всплески производства одного вида продукции за счет исключения из ассортимента других изделий приведут к дефициту деталей либо потребуют создания значительных запасов.
2) Методика «Визуализация и выявление проблем», ее цель – не допустить передачи дефектных деталей на следующую стадию процесса и освободить людей от машин, т.е. обеспечить автоматизацию с человеческим интеллектом.
Каждый элемент дома важен сам по себе, но еще важнее взаимосвязь между ними. Жесткая закладка сводит к минимуму запасы, что позволяет устранить многие проблемы в процессе производства. Поток единичных изделий обеспечивает последовательное изготовление изделий со скоростью, соответствующей запросам потребителя. Сведение запасов к минимуму означает, что дефекты качества выявляются немедленно. Этому способствует метод контроля качества на рабочем месте, который позволяет остановить производственный процесс. Чтобы возобновить производство, рабочие должны незамедлительно решить возникшую проблему.
Заключительный этап внедрения производственной системы ОАО “УАЗ” включает:
- обучение персонала замечать потери, разбираться с возникшими проблемами на месте, увидев ситуацию своими глазами, выявлять первопричины проблем;
- непрерывное совершенствование процессов, вовлечение в этот процесс всего персонала;
- организацию деятельности малых групп, создание эффективной системы мотивации с целью развития у рабочих стремления к неустанному самосовершенствованию;
- реализацию концепции QCDSM.
Рассмотрим более подробно этапы внедрения ПС УАЗ (производственной системы ОАО “УАЗ”).
2.2 Первый этап внедрения “ПС УАЗ”
Философия ОАО “УАЗ”. Философия ОАО “УАЗ” заключается в ее миссии и основных принципах производственной системы. Именно эти две составляющих и лежат в основе строительства “Дома”.
МиссияОАО “УАЗ”: “Быть лидером в России и на рынках развивающихся стран по производству и сбыту надежных малотоннажных автомобилей повышенной проходимости. Выпускать многофункциональные автомобили, которые помогают в работе и подходят для активного отдыха. Выпускаемые машины решают проблемы с перевозкой людей и грузов в условиях плохих дорог или полного бездорожья. Использовать свои технологические преимущества и достигать успеха за счет эффективного производства и минимизации затрат”.
Основные принципы “ПС УАЗ” представлены в приложении В, исходя из которых все (от рабочего до генерального директора) должны придерживаться установки: поступай так, как лучше для компании, ее сотрудников, потребителей и общества в целом. Компания видит свое предназначение в исполнении своих обязательств перед потребителями, сотрудниками и обществом, и именно это лежит в основе всех остальных принципов.
Рассмотрим основные принципы “ПС УАЗ” подробнее:
а) «Люди – самый ценный актив компании». Об этом никогда нельзя забывать и необходимо постоянно:
- совершенствовать систему мотивации;
- информировать своих работников о результатах работы;
- предоставлять возможность самореализации для каждого;
- уважительно относиться к людям, доверять им и так далее.
б) «Потребитель всегда прав!». Этот принцип также является одним из основных, так как в любой бизнес-системе первоочередная задача всех сотрудников орг
|
|
Автоматическое растормаживание колес: Тормозные устройства колес предназначены для уменьшения длины пробега и улучшения маневрирования ВС при...
Типы оградительных сооружений в морском порту: По расположению оградительных сооружений в плане различают волноломы, обе оконечности...
История развития пистолетов-пулеметов: Предпосылкой для возникновения пистолетов-пулеметов послужила давняя тенденция тяготения винтовок...
Архитектура электронного правительства: Единая архитектура – это методологический подход при создании системы управления государства, который строится...
© cyberpedia.su 2017-2024 - Не является автором материалов. Исключительное право сохранено за автором текста.
Если вы не хотите, чтобы данный материал был у нас на сайте, перейдите по ссылке: Нарушение авторских прав. Мы поможем в написании вашей работы!