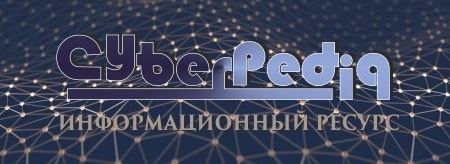
Адаптации растений и животных к жизни в горах: Большое значение для жизни организмов в горах имеют степень расчленения, крутизна и экспозиционные различия склонов...
Типы оградительных сооружений в морском порту: По расположению оградительных сооружений в плане различают волноломы, обе оконечности...
Топ:
Эволюция кровеносной системы позвоночных животных: Биологическая эволюция – необратимый процесс исторического развития живой природы...
Интересное:
Аура как энергетическое поле: многослойную ауру человека можно представить себе подобным...
Принципы управления денежными потоками: одним из методов контроля за состоянием денежной наличности является...
Подходы к решению темы фильма: Существует три основных типа исторического фильма, имеющих между собой много общего...
Дисциплины:
![]() |
![]() |
5.00
из
|
Заказать работу |
|
|
Технологический процесс производства неводостойких гипсовых вяжущих из природного сырья состоит из следующих основных переделов:
1. предварительная подготовка сырья (дробление, сушка и тонкое измельчение)
2. тепловая обработка подготовленного сырья (дегидратация)
. дополнительный помол при необходимости основной помол, предусмотренный на этой стадии технологической схемой производства.
В зависимости от порядка выполнения этих операций имеются три технологические схемы производства строительного гипса:
1. предварительная сушка и измельчение гипсового камня в порошок необходимой дисперсности с последующей дегидратацией гипса в различных обжиговых аппаратах;
2. обжиг гипса в виде кусков различных размеров в разных печах с измельчением полугидрата в порошок после обжига;
. совмещение операций сушки, помола и обезвоживания двугидрата в мельницах.
Последний способ получил название обжига гипса во взвешенном состоянии. Тепловую обработку гипсового камня производят в варочных котлах, сушильных барабанах, шахтных или других мельницах.
Наиболее распространена схема производства гипсового вяжущего с применением варочных котлов. Гипсовый камень, поступающий на завод в крупных кусках, сначала дробят, затем измельчают в мельнице, одновременно подсушивая его. В порошкообразном виде камень направляют в варочный котел периодического или в установку непрерывного действия. Последняя имеет в 2…3 раза выше производительность, но еще находится в стадии практического освоения. Варочный котел периодического действия представляет собой обмурованный кирпичом стальной котел со сферическим днищем, обращенным выпуклой стороной внутрь цилиндра. Разборное днище лучше выдерживает напряжения, возникающие при местном перегреве, а при износе отдельные его части легко заменяются новыми элементами. Для перемешивания гипса в процессе варки котел снабжен мешалкой, состоящей из вертикального вала, лопастей и привода. Котел закрывают крышкой с патрубком и пароотводной трубой, через которую удаляются пары воды, образующиеся при варке гипса. Устанавливают котел вертикально и обмуровывают кирпичной кладкой. Чтобы обеспечить равномерный прогрев гипса и увеличить поверхность нагрева, в варочных котлах большой емкости устанавливают жаровые трубы. В этом случае топочные газы обогревают сначала днище, затем боковые поверхности котла в кольцевых каналах, далее проходят через котел по жаровым трубам и, наконец, уходят в дымовую трубу. Часто газы из топок варочных котлов направляют в установки для совместной сушки и помола двуводного гипса, что способствует значительной экономии топлива. Загружают котел порошком двуводного гипса при помощи винтового конвейера, привод которого установлен на каркасе котла. Пары воды удаляются через трубу. Обжигают гипс в котле следующим образом. После прогрева котла включают мешалку и начинают постепенно загружать его гипсовым порошком. Продолжительность процесса варки зависит от размеров котла, температуры и степени влажности и частичной дегидратации поступающего в него гипса. Обычно продолжительность варки колеблется от 1 до 3 ч, при этом а первые 20-30 мин гипс нагревается от температуры 60-70°С, которую он имел при загрузке в варочный котел, до начала интенсивной его дегидратации, т.е. до 130-150°С. Далее температура материала почти не меняется вследствие интенсивного выделения и испарения кристаллизационной (гидратной) воды. В это время наблюдается как бы «кипение» гипсового порошка. После окончания дегидратации гипса начинается ступающего в установку гипсового порошка до температуры дегидратации (115-125°С); в следующих секциях температура греющей поверхности 220°С, материала - около 150°С, что почти исключает образование обезвоженных модификаций сернокислого кальция. Пар, образующийся при дегидратации гипса, отводят из установки через трубки с вентилями, что позволяет регулировать количество отводимого пара на каждом участке и создавать условия для преимущественного образования а-модификации полугидрата и сушки готового продукта. Применение установок непрерывного действия, как и котлов больших размеров периодического действия, позволяет значительно сократить количество обслуживающего персонала, уменьшить объем здания на единицу продукции. И повысить качество гипса. Поэтому при строительстве новых заводов предусматривается установка только этих котлов. Для улучшения качества готовой продукции на отдельных заводах после обжига в варочных котлах гипс подвергают вторичному помолу в шаровых мельницах. При этом обнажающиеся при помоле необезвоженные ядра частиц гипса под влиянием тепла, выделяющегося от трения и ударов шаров, дегидратируются, а обезвоженный полугидрат и растворимый ангидрит гидратируются выделяющимися водяными парами и переходят в полуводный гипс. Кроме того, полагают, что частицы при вторичном помоле приобретают таблитчатую форму, обеспечивающую повышение пластичности теста и раствора из такого материала. Гипс в варочных котлах непосредственно не соприкасается с топочными газами. Кроме того, в процессе варки он интенсивно перемешивается и равномерно нагревается, что обеспечивает получение однородного продукта высокого качества. Расход условного топлива при изготовлении строительного гипса в варочных котлах составляет 40-45 кг, электроэнергии - 20-25 кВт-ч на 1 т. Данный способ получил наибольшее распространение в промышленности. Капиталовложения в этом случае составляют 20-25 руб. на 1 т вяжущего.
|
|
Гипсовое вяжущее в сушильных барабанах получают путем обжига гипсового камня в виде щебня размером до 20 мм. Сушильный барабан представляет собой сварной стальной цилиндр, вращающийся на опорных роликах со скоростью 2-3 оборота в 1 мин. Барабан устанавливают с наклоном к горизонту 3-5° и приводят во вращение электродвигателем. Гипс для обжига в виде щебня размером до 35 мм с помощью питателя подают в приподнятый конец барабана через загрузочную воронку; благодаря наклону 1 барабана он перемещается в нем в осевом направлении к разгрузочной воронке. В зависимости от выбранного направления потока горячих газов в барабане к загрузочному или разгрузочному концу его пристраивают топку. В первом случае направление движения горячих газов! и материала в печи совпадает, и барабан работает по принципу прямотока; во втором случае - газы и материал движутся навстречу друг другу (противоток). Эта схема отличается пониженным расходом топлива. Сушильные барабаны могут работать на твердом (кусковом и пылевидном), жидком и газообразном топливе. Удельный расход топлива в них составляет около 5% массы готового продукта. Для обжига гипса применяют сушильные барабаны производительностью 5-15 т/ч. Технологические процессы производства гипса с обжигом его во вращающихся печах непрерывные, и поэтому легко осуществить их автоматическое управление. Получать гипс по этому способу экономично.
|
При обжиге гипса во взвешенном состоянии совмещают две операции: измельчение и обжиг. В мельницу (шахтную, шаровую или роликовую) подают гипсовый щебень и одновременно нагнетают горячие дымовые газы. Образующиеся при размоле мельчайшие зерна гипса товарной фракции увлекаются из мельницы потоком дымовых газов и в процессе транспортирования в раскаленном газовом потоке обжигаются. Пылевоздушная смесь поступает в циклоны и фильтры для осаждения гипса. Наибольшую производительность из рассмотренных схем имеет последняя, затем схема обжига в сушильных барабанах и, наконец, в варочных котлах. Однако первые две схемы существенно уступают по качеству продукции (как уже было описано выше) схеме с варкой гипса. При затворении порошка гипса водой полуводный сернокислый кальций CaSO4-5H2O, содержащийся в нем, начинает растворяться до образования насыщенного раствора и одновременно гидратироваться. В результате образовавшийся насыщенный раствор полугидрата оказывается пересыщенным по отношению к двугидрату. Пересыщенный раствор в обычных условиях не может существовать - из него выделяются мельчайшие частицы твердого вещества - двуводного сернокислого кальция. По мере накопления этих частиц они склеиваются между собой, вызывая загустевание (схватывание) теста. Затем мельчайшие частицы гидрата начинают кристаллизоваться, определяя этим образование прочного гипсового камня. Дальнейшее увеличение прочности гипса происходит вследствие высыхания твердеющей массы и более полной кристаллизации при этом. Твердение гипса можно ускорить сушкой, но при температуре не выше 65°С во избежание обратной дегидратации двуводного гипса.
|
На основании вышеизложенного можем придти к выводу, что наиболее рациональным вариантом с точки зрения качества готовой продукции будет использование технологической схемы с применением варочных котлов периодического действия.
В соответствии с выбранной технологической схемой используется гипсовый камень размером 300…500 мм, который подвергается первичному дроблению в щековых дробилках до размера кусков 30..50 мм. Рабочим раздавливающим органом щековой дробилки служат две дробящие поверхности - щеки, неподвижная и подвижная. Материал, поступая сверху через загрузочное отверстие, заклинивается между щеками и при надавливании на него подвижной щеки раздавливается. Образовавшиеся при этом мелкие куски ссыпаются в нижнюю часть дробящей полости и снова раздавливаются нажатием подвижной щеки. Так происходит до тех пор, пока размер зерен материала не окажется меньше размера нижней разгрузочной щели дробилки. Изменяя размер этой щели, можно регулировать наибольшую крупность дробленого продукта. Основной помольной установкой для измельчения гипса является шахтная мельница, представляющая собой молотковую мельницу с гравитационным сепаратором. Эта мельница служит не только для помола, но и для сушки гипса. Температура газов при выходе из мельницы находится в пределах 300…5000. Тонкость помола материала и производительность мельниц зависят от скорости газового потока. Газопылевая смесь после выхода из мельниц проходит через систему пылеулавливающих устройств - циклонов. Они имеют верхнюю цилиндрическую и нижнюю коническую части. Запыленные газы подводятся по касательной в верхней части циклона через входной патрубок. В циклоне газовый поток приобретает вращательное движение. При этом взвешенные частицы пыли под действием центробежной силы отбрасываются на внутреннюю поверхность цилиндра и по ней соскальзывают в коническую часть - пылесборник. В данном случаях нам необходимо очищать большие объемы газа, содержащего тонкую пыль, вместе с уже имеющимися циклонами установлены группы параллельно соединенных циклонов малого диаметра. Так как значение центробежной силы, создаваемой в циклоне, обратно пропорционально его радиусу, объединение циклонов меньшего диаметра в секции дает возможность, не уменьшая их производительности, довести степень очистки газов в батарейных циклонах до 80-98%.Движение газов в системе принудительное и осуществляется за счет работы центробежных вентиляторов. Осажденный в процессе пылеочистки гипсовый порошок поступает в расходные бункеры над варочными котлами. В зависимости от температуры газов при выходе из мельниц температура порошка может колебаться от 70 до 950С. По мере прекращения парообразования и увеличения плотности полученных продуктов дегидратации гипса масса уплотняется и снижается ее уровень в котле (первая «осадка» порошка). Вторая «осадка» наблюдается в последний период варки и соответствует обезвоживанию полугидрата сульфата кальция до растворимого безводного сульфата кальция (ангидрита). Готовый продукт выгружается из котла в приемный бункер, откуда механическим и пневматическим транспортом передается в силосные склады для хранения и отгрузки потребителю. Выбранная технологическая схема изображена на рисунке 1. Оборудование, участвующее в производственном процессе представлено таблице 4.
|
Таблица 4 - Сводная ведомость основного технологического оборудования и транспорта
Наименование оборудования | Краткая характеристика оборудования, транспорта | Количество машин, шт. |
бункер гипсового камня | мощность 0,7 кВт, объём бункера не менее, -3,0 м3, диаметр бункера-18000 высота с опорами не более-3300 мм | 1 |
ленточный конвейер ЛК-500 | производительность до 60 м3/ч; ширина ленты 500 мм; длина конвейера между осями барабанов до 30 м; скорость движения ленты 1.3, м/с*; нагрузка на погонный метр ленты 200 кг; мощность установленного электродвигателя 4-5.5 кВт; максимальный крутящий момент 273 Н*м | 1 |
щековая дробилка | размер загружаемого материала 200-600 мм; ширина загрузочной щели 13 мм; мощность двигателя 55 кВТ | 1 |
рукавные фильтры | скорость фильтрации от 0,7 до 1,5 м/мин | 2 |
циклоны ЦН-11 | допустимая запылённость газа, для слабо слипающихся пылей не более 1000 г./м3, температура очищаемого газа не более 250 0С; максимальное давление (разряжение) не более 3000 Па; эффективность очистки от пыли 10 мкм, плотностью 2,72 г./см3-50-99%; условная скорость в корпусе циклона - 2,2-2,8 м/сек | 2 |
Качество строительной продукции зависит от ряда факторов, и прежде всего от организации на производстве работы системы качества в соответствии с требованиями государственных стандартов. На производстве осуществляют следующие основные виды контроля качества:
· входной (контроль сырьевых материалов, вспомогательных материалов) осуществляется лабораторией предприятия.
· операционные - проверка соблюдения нормативных требований в процессе выполнения технологических операций в соответствии с технологическими регламентами, осуществляется техническим персоналом цехов.
· приемочный, осуществляется службой отдела технического контроля.
|
|
Наброски и зарисовки растений, плодов, цветов: Освоить конструктивное построение структуры дерева через зарисовки отдельных деревьев, группы деревьев...
Двойное оплодотворение у цветковых растений: Оплодотворение - это процесс слияния мужской и женской половых клеток с образованием зиготы...
Механическое удерживание земляных масс: Механическое удерживание земляных масс на склоне обеспечивают контрфорсными сооружениями различных конструкций...
Организация стока поверхностных вод: Наибольшее количество влаги на земном шаре испаряется с поверхности морей и океанов (88‰)...
© cyberpedia.su 2017-2024 - Не является автором материалов. Исключительное право сохранено за автором текста.
Если вы не хотите, чтобы данный материал был у нас на сайте, перейдите по ссылке: Нарушение авторских прав. Мы поможем в написании вашей работы!