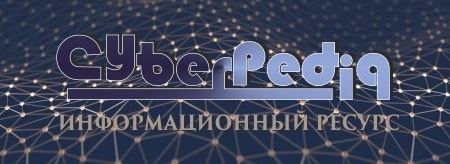
Опора деревянной одностоечной и способы укрепление угловых опор: Опоры ВЛ - конструкции, предназначенные для поддерживания проводов на необходимой высоте над землей, водой...
Адаптации растений и животных к жизни в горах: Большое значение для жизни организмов в горах имеют степень расчленения, крутизна и экспозиционные различия склонов...
Топ:
Определение места расположения распределительного центра: Фирма реализует продукцию на рынках сбыта и имеет постоянных поставщиков в разных регионах. Увеличение объема продаж...
Методика измерений сопротивления растеканию тока анодного заземления: Анодный заземлитель (анод) – проводник, погруженный в электролитическую среду (грунт, раствор электролита) и подключенный к положительному...
Интересное:
Как мы говорим и как мы слушаем: общение можно сравнить с огромным зонтиком, под которым скрыто все...
Распространение рака на другие отдаленные от желудка органы: Характерных симптомов рака желудка не существует. Выраженные симптомы появляются, когда опухоль...
Финансовый рынок и его значение в управлении денежными потоками на современном этапе: любому предприятию для расширения производства и увеличения прибыли нужны...
Дисциплины:
![]() |
![]() |
5.00
из
|
Заказать работу |
|
|
Каждая зубчатая пара имеет ведущее и ведомое колесо, в процессе работы вращение от первого передаётся второму.
В основу определения параметров зубчатого колеса положена делительная окружность.
Диаметр делительной окружности обозначается буквой d и называется делительным. По делительной окружности откладывается окружной шаг зубьев, обозначаемый pt и представляющий собой расстояние по дуге делительной окружности между соседними (смежными) зубьями колеса. Таких шагов можно отложить столько, сколько зубьев Z имеет колесо, иначе говоря, отрезки, равные шагу р t делят делительную окружность на Z частей, отсюда ее название.
Делительная окружность делит высоту зуба h на две неравные части - головку высотой h а и ножку высотой hf,
Зубчатый венец ограничивается окружностью вершин зубьев диаметром da и окружностью впадин диаметром d f.
На чертежах поверхность и образующую вершин зубьев показывают сплошными основными линиями, поверхность и образующую впадин показывают сплошными тонкими линиями. Делительные окружности показывают штрихпунктирными линиями.
Одним из основных параметров зубчатых колес является модуль зацепления, который представляет собой длину делительной окружности d, приходящуюся на один зуб колеса; численно модуль равен отношению диаметра делительной окружности к числу зубьев
m = d / Z
Модуль выражается всегда в миллиметрах, его значения (приведённые в таблице) должны соответствовать ГОСТ 9563—60 При выборе модуля следует отдавать предпочтение первому ряду.
Таблица 2.10 - Модули зубчатых колёс
1-й ряд | 1 | 1.25 | 1.5 | 2 | 2.5 | 3 | 4 | 5 |
2-й ряд | 1.125 | 1.375 | 1.75 | 2.25 | 2.75 | 3.5 | 4.5 | 5.5 |
Таблица 2.11 - Параметры цилиндрических зубчатых колёс
|
Параметр | Обозн. | Расчетная формула |
Высота головки зуба | h а | ha = m |
Высота ножки зуба | h f | hf = l,25 m |
Высота зуба | h | h = ha + hf = 2,25 m |
Диаметр делительной окружности | d | d = m Z |
Диаметр вершин зубьев | d а | da = d + 2ha = m (Z + 2) |
Диаметр впадин зубьев | df | df = d- 2hf = m (Z - 2,5) |
2.10 Алгоритм выполнения чертежа готового прямозубого цилиндрического колеса
Чертёж каждого зубчатого колеса выполняют с количеством изображений, видов, разрезов, сечений, достаточным для полного изображения всех его элементов. На главном виде колесо следует размещать в том положении, в котором будут обрабатываться на станке большинство его поверхностей, или ось колеса располагать параллельно основной надписи.
В большинстве случаев для выявления формы зубчатого колеса достаточно одного изображения (фронтального разреза на месте вида спереди). Для показа отверстия в ступицах зубчатых колёс и шпоночных пазов вместо полного изображения детали допускается давать лишь контур отверстия и паза.
2.10.1 Последовательность построения
Этап 1. Измеряют диаметр окружности выступов d а, подсчитывают число зубьев колеса Z и подставляют их значения для определения модуля зацепления m, в формулу
m = da / ( Z + 2).
Значение модуля округляют дo ближайшего значения из таблицы модулей. В зависимости от модуля вычисляют диаметры делительной окружности d и окружности впадин df, соответственно по формулам
d = m z ; и df = m (z - 2,5).
Этап 2. Все остальные размеры, необходимые для вычерчивания, находят путем измерения элементов колеса:
- диаметр вала (отверстия под вал);
- длину и наружный диаметр ступицы;
- ширину зубчатого венца;
- толщину и диаметр диска и т.д.;
- если есть шпоночный паз, то его размеры: глубина, ширина).
Этап 3. Вычерчивают изображение в выбранном масштабе.
Примечание. В большинстве случаев для выявления формы зубчатого колеса достаточно одного изображения (фронтального разреза на месте вида спереди). Для показа отверстия в ступицах зубчатых колёс и шпоночных пазов вместо полного изображения детали допускается давать лишь контур отверстия и паза.
|
Чертежи зубчатых колес выполняют в соответствии с требованиями, установленными ГОСТ 2.404-68:
- окружности и образующие поверхности выступов зубьев и витков показывают сплошными основными линиями;
- делительные, начальные окружности показывают штрихпунктирными тонкими линиями на всех изображениях колеса;
- окружности и образующие поверхностей впадин зубьев в разрезах и сечениях показывают сплошными основными линиями, на видах допускается показывать сплошными тонкими линиями;
- зубья вычерчивают только в осевых разрезах и сечениях, в остальных случаях изображения зубьев ограничивают поверхностями выступов;
- если секущая плоскость проходит через ось зубчатого колеса, то на разрезах и сечениях зубья показывают не рассеченными (не штрихуются);
- если секущая плоскость проходит через оси обоих зубчатых колес, сходящихся в зацеплении, то на разрезе в зоне зацепления зуб одного из колёс (предпочтительно ведущего) показывают перед зубом сопрягаемого колеса
Этап 4. Проставляют размеры.
Примечание. Размеры делительного диаметра и окружности впадин на чертеже не указывают
Этап 5. Обозначаем шероховатость рабочих поверхностей
Примечание. Для поверхности ступицы, сопряженной с валом, назначают следующие значения параметра шероховатости Ra: для диаметра вала менее 80 мм – 2,5…3,2, более 80 мм – 3,2…6,3.
Для диаметра вершин и боковых базовых поверхностей венца в зависимости от точности и ответственности изделия назначают Ra 1,6…6,3.
Для свободных поверхностей, как правило, назначают Ra 6,3…12,5.
Этап 6. Заполняют таблицу параметров, которая располагается в правом верхнем углу по форме. Оформляем чертёж.
2.11 Алгоритм выполнения чертежа цилиндрической зубчатой передачи
Цилиндрическая зубчатая передача образуется парой цилиндрических зубчатых колёс, находящихся в зацеплении. Зубчатое колесо передачи, сообщающее движение другому (парному) колесу, называется ведущим (шестерня - индекс 1), а которому сообщается движение называется ведомым (колесо - индекс 2).
Простейшая цилиндрическая прямозубая передача состоит из шестерни 1 и колеса 4, находящихся в зацеплении, двух валов 3 и 6, расположенных параллельно, и двух шпонок 2 и 5. Шестерня и колесо имеют одинаковый модуль и параметры зубьев.
|
Исходными данными для расчёта и построения передачи являются (карточка-задание):
- модуль зацепления - m;
- количество зубьев шестерни - Z 1;
- количество зубьев колеса - Z 2.
-посадочные диаметры для валов - d в1 и d в2;
- длина ступицы - l ст.1 l ст.2
Этап 1. Выполняемрасчёты параметров передачи по формулам
Шестерня |
Колесо
Рассчитываем диаметры
d 1 = m Z 1
da 1 = m (Z 1 + 2)
df 1 = m (Z 1 - 2,5)
Рассчитываем межосевое расстояние - расстояние между осями зубчатых колес:
aw = 0.5 (d 1 + d 2)
Выбираем параметры шпонок по справочнику
для d в1 и l ст.1
h1 =
b1 =
t =
t1 =
Соединение шпоночное состоит из вала, колеса и шпонки. Шпонка представляет собой деталь призматической (шпонки призматические или клиновые) или сегментной (шпонки сегментные) формы, размеры которой определены стандартом. Шпонки применяют для передачи крутящего момента.
Размеры призматических шпонок определяются ГОСТ 23360-78.
В специальную канавку - паз на валу закладывается шпонка. На вал насаживают колесо так, чтобы паз ступицы колеса попал на выступающую часть шпонки. Размеры пазов на валу и в ступице колеса должны соответствовать поперечному сечению шпонки |
Шпоночное соединение показывают во фронтальном разрезе осевой плоскостью. Шпонку при этом изображают неразрезанной, на валу выполняют местный разрез. Вторым изображением шпоночного соединения служит сечение плоскостью, перпендикулярной оси вала. Зазор между основаниями паза во втулке (ступице колеса) и шпонкой показывают увеличенным. |
Таблица - Размеры призматических шпонок в зависимости от диаметра вала
Диаметр вала dв | Шпонка | Глубина паза | |||
b (ширина) | h (высота) | l (длина) | t1 (вал) | t2 (втулка) | |
6...8 | 2 | 2 | 6...12 | 1,2 | 1,0 |
8...10 | 3 | 3 | 6...36 | 1,8 | 1,4 |
10...12 | 4 | 4 | 8...45 | 2,5 | 1,8 |
12...17 | 5 | 5 | 10...56 | 3,0 | 2,3 |
17...22 | 6 | 6 | 14...70 | 3,5 | 2,8 |
22...30 | 7 | 7 | 18...90 | 4,0 | 3,3 |
30...38 | 10 | 8 | 22...110 | 5,0 |
Примечание
Ряд стандартных длин l шпонок, мм: 6; 8; 10; 12; 14; 16; 18; 20; 22; 25; 28; 32; 36; 40.
|
Примеры условного обозначения:
Шпонка 18 x 11 x 100 ГОСТ 23360-78 - шпонка исполнения 1 с размерами b - 18 мм, h = 11 мм; l =100 мм.
Этап 2. Вычерчиваем изображения передачи зубчатой цилиндрической
Построение изображения зубчатого зацепления выполняется тонкими линиями и начинается с нанесения межосевого расстояния aw, проведения на виде слева осевых линий, начальных окружностей dl и d 2, окружностей вершин зубьев dal и da 2, окружностей впадин df 1 и df 2. Начальные окружности должны касаться друг друга в точке, расположенной на оси, соединяющей центры зубчатых колес. Одновременно проводятся окружности, соответствующие отверстиям для валов d в1 и d в 2, а также наружные диаметры ступиц d ст l и d ст 2.
Для построения фронтального разреза из точек пересечения окружностей с вертикальной, линией центров проводят в направлении стрелок линии связи. |
После выполненных построений приступают к окончательному оформлению чертежа. На обоих изображениях вычерчивают ступицы колес. По диаметрам валов, используя ГОСТ 23360—78, подбирают размеры шпоночных пазов, в местах шпоночных соединений выполняют местные разрезы валов. Вычерчивают отверстия. Удаляют лишние линии, обводят чертеж, заштриховывают разрезы. На фронтальном разрезе зуб ведущего колеса изображается расположенным перед зубом ведомого зубчатого колеса (рисунок внизу)). Ввиду имеющейся разницы высот головки и ножки зубьев получаются радиальные зазоры, равные 0,25 m.
Этап 3. Проставляем размеры: межосевое расстояние, посадочные диаметров валов
Этап 4. Обозначаем позиции.
Этап 5. Оформляем основную надпись
Этап 5. Оформляем спецификацию на формате А4.
.
3 ЧТЕНИЕ И ДЕТАЛИРОВАНИЕ СБОРОЧНОГО ЧЕРТЕЖА
Прочитать сборочный чертёж - это значит определить назначение, устройство, принцип работы изображённого на нём изделия. При этом выяснить взаимодействие, способы соединения и форму каждой детали.
На производстве чтение сборочных чертежей осуществляют при изучении станков, машин, приборов, а также при их сборке, монтаже, ремонте. В конструкторских бюро по чертежам сборочных единиц выполняют рабочие чертежи деталей.
В учебной практике чтение сборочного чертежа помогает развить и закрепить знания и умения, приобретённые при выполнении проекционных чертежей.
3.1 Алгоритм чтения сборочного чертежа
3.1.1 Ознакомление с изделием по карточке - заданию
По основной надписи выясняют наименование изделия, масштаб изображения и его соответствие, если это карточка-задание. Пояснительная записка, описание или спецификация позволяют ознакомиться с назначением изделия и его принципиальным устройством.
3.1.2 Чтение изображений
|
Определяют, какие виды, разрезы, сечения даны на чертеже, и каково назначение каждого изображения. Выясняют положение секущих плоскостей, при помощи которых выполняют разрезы и сечения, а при наличии дополнительных и местных видов - направление проецирования, по которым они выполнены.
Определяют наличие выносных элементов и их назначение на чертеже. Перечисляют условности и упрощения, предусмотренные стандартами ЕСКД ГОСТ 2.109-78 для сборочных чертежей.
3.1.3 Изучение составных частей изделия
По спецификации выясняют их наименование, а по чертежу - форму, взаимное положение и назначение, Изучают составные части изделия по порядку номеров позиций в спецификации. Изображения сначала находят на том виде, на котором указан номер позиции, а затем и на остальных. При наличии разрезов выявлению формы детали способствуют одинаковые наклон и частота штриховки сечений одной и той же детали.
3.1.3 Изучение конструкции изделия
Выясняют характер соединения отдельных деталей между собой. Для неразъёмных соединений: сварных, клепаных, поясных и т.п. определяют каждый элемент и места их соединения. Для разъёмных соединений выявляют все крепежные детали. При наличии подвижных соединений устанавливают, какие детали перемещаются, и по каким поверхностям происходит их сопряжение с другими деталями.
3.1.4 Определение последовательности сборки и разборки изделия
Пример чтения сборочного чертежа "Клапан впускной".
На сборочном чертеже изображён клапан впускной, что видно из основной надписи. По наименованию и пояснительной надписи на поле чертежа можно установить, что клапан служит для пуска в тормозную систему воздуха, который под давлением подаётся из магистрали при механическом нажатии рычага этой системы на верхний конец клапана.
На сборочном чертеже даны три изображения:
- разрез простой фронтальный на месте главного вида;
- вид сверху, на котором показано положение секущих плоскостей, при помощи которых получен сложный ломаный разрез, местный вид. С помощью разреза выявляют внутреннюю конструкцию изделия. Вид сверху поясняет форму фланца крышки и форму верхней части клапана. На местном виде показана форма нижней части корпуса. Выполнен он по направлению, указанному стрелкой с буквенным обозначением.
По спецификации определяют, что изделие состоит из шести деталей: корпуса, клапана, крышки, опоры, прокладки и пружины. Корпус поз.1 показан на разрезе, виде сверху и местном виде. Отверстие с резьбой в его левой нижней части служит для присоединения воздухопровода. Надпись R 3/8 означает, что резьба в отверстии коническая дюймовая, размер её 3/8. Она обеспечивает плотность соединения. Местный вид помогает выяснить, что нижняя часть корпуса имеет шестигранную форму. Такая форма необходима для удерживания корпуса при завинчивании крышей. Форма клапана определяется по его главному виду и виду сверху. Крышка показана на разрезе и виде сверху. Четыре отверстия на фланце крышки служат для крепления изделия к корпусу тормозной системы, который показан тонкими сплошными линиями, как пограничная деталь. Пружина, опора и прокладка показаны на разрезе. Прокладка обеспечивает герметичность соединения крышки с корпусом. Пружина, упираясь в нижнюю торцовую плоскость опоры, передаёт через неё усилие на клапан.
Крышка соединяется с корпусом резьбой. Рабочая поверхность клапана коническая, она соприкасается с конической поверхностью крышки. Герметическое закрывание обеспечивается плотностью прилегания этих поверхностей, что достигается благодаря высокому классу шероховатости поверхностей. Клапан открывается под действием механического давления рычага тормозной системы на его верхний сферический конец. Опускаясь под действием рычага вниз, он, сжимая пружину, открывает проходное отверстие в крышке и воздух под давлением поступает в корпус тормозной системы.
Разбирают изделия в такой последовательности:
- отвинчивают крышку;
- снимают прокладку;
- вынимают из корпуса клапан, опору, пружину.
Сборку изделия выполняют в обратной последовательности.
3.2 Алгоритм деталирования сборочного чертежа
Изучают сборочную единицу, прочитав её чертёж в указанной ранее последовательности.
Устанавливают детали, чертежи которых необходимо выполнить, и намечают последовательность деталирования. Начинают с простых по форме деталей.
В соответствии с ГОСТ 2.305 - 2008 выбирают главное изображение детали, которым может быть вид, фронтальный разрез или сочетание вида с разрезом для симметричных деталей.
Положение детали на главном изображении может не соответствовать её изображению на чертеже сборочной единицы. Количество изображений должно быть минимальным, но достаточным для полного представления о форме и размерах деталей.
Выбирают масштаб изображений в соответствии с ГОСТ 2.305 - 68. При деталировании необязательно придерживаться одного и того же масштаба для всех деталей. Мелкие детали, особенно сложной формы, изображают в более крупном масштабе.
Выбирают необходимый формат по ГОСТ 2.301 - 68 листа чертёжной бумаги, наносят рамку и основную надпись.
Компонуют и последовательно выполняют изображения. На чертеже детали изображают и те её элементы, которые на сборочном чертеже не показаны или показаны упрощённо, например: фаски, галтели, проточки и другие элементы. Размеры этих конструктивных элементов определяют не по сборочному чертежу, а по соответствующим стандартам на эти элементы.
Проводят выносные и размерные линии. Определяют истинные размеры элементов детали и проставляют их на рабочем чертеже. Особое внимание обращают на то, чтобы номинальные размеры сопряжённых деталей не имели расхождений.
Наносят обозначение шероховатости поверхностей исходя из технологии изготовления детали или её назначения
Тип материала, из которого изготовлена деталь, находят в спецификации в колонке "Примечание" или в прилагающемся описании.
Проверяют чертёж и окончательно его оформляют: заполняют основную надпись, указывают при необходимости технические требования.
Аналогично выполняют чертежи остальных деталей сборочной единицы.
Примечание 1
На сборочном чертеже допускается не показывать мелкие конструктивно технологические элементы (фаски, скругления, проточки и др.). При деталировании все эти условности и упрощения должны быть восстановлены. В глухих резьбовых отверстиях следует показывать резьбу с учётом запаса глубины сверления, величины недореза, вводить фаски на всех резьбовых элементах.
Обычно при деталировании на студенческих рабочих чертежах в случае необходимости делают надписи, которые располагают над основной надписью, типа:
"Неуказанные радиусы 3...5мм"
*"Размеры для справок"
Примечание 2
Требования к шероховатости поверхности устанавливают исходя из их функционального назначения. По сборочному чертежу устанавливают взаимодействие деталей и способ их соединения, определяют также поверхности сопрягаемые и свободные.
Шероховатость поверхностей определяют по техническим требованиями условиям работы детали в изделии. Рекомендуемые значения шероховатости:
- свободных поверхностей Rz 320...80;
- сопряженных неподвижных поверхностей Rz 40 или Ra 2,5;
- сопряженных трущихся поверхностей Ra 2,5...0,32;
-отверстий под болты, винты, шпильки Rz 40... Ra 2,5;
- привалочных поверхностей, пазов, проточек Ra 6,3 ...Ra 2,5;
- для рабочих поверхностей зубьев зубчатых колес Ra 1.6...0,63
|
|
Адаптации растений и животных к жизни в горах: Большое значение для жизни организмов в горах имеют степень расчленения, крутизна и экспозиционные различия склонов...
Археология об основании Рима: Новые раскопки проясняют и такой острый дискуссионный вопрос, как дата самого возникновения Рима...
Биохимия спиртового брожения: Основу технологии получения пива составляет спиртовое брожение, - при котором сахар превращается...
Типы оградительных сооружений в морском порту: По расположению оградительных сооружений в плане различают волноломы, обе оконечности...
© cyberpedia.su 2017-2024 - Не является автором материалов. Исключительное право сохранено за автором текста.
Если вы не хотите, чтобы данный материал был у нас на сайте, перейдите по ссылке: Нарушение авторских прав. Мы поможем в написании вашей работы!