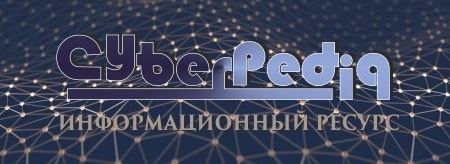
Биохимия спиртового брожения: Основу технологии получения пива составляет спиртовое брожение, - при котором сахар превращается...
Типы оградительных сооружений в морском порту: По расположению оградительных сооружений в плане различают волноломы, обе оконечности...
Топ:
Характеристика АТП и сварочно-жестяницкого участка: Транспорт в настоящее время является одной из важнейших отраслей народного хозяйства...
Оценка эффективности инструментов коммуникационной политики: Внешние коммуникации - обмен информацией между организацией и её внешней средой...
Техника безопасности при работе на пароконвектомате: К обслуживанию пароконвектомата допускаются лица, прошедшие технический минимум по эксплуатации оборудования...
Интересное:
Национальное богатство страны и его составляющие: для оценки элементов национального богатства используются...
Средства для ингаляционного наркоза: Наркоз наступает в результате вдыхания (ингаляции) средств, которое осуществляют или с помощью маски...
Наиболее распространенные виды рака: Раковая опухоль — это самостоятельное новообразование, которое может возникнуть и от повышенного давления...
Дисциплины:
![]() |
![]() |
5.00
из
|
Заказать работу |
|
|
ГЛАВА 1. АВАРИИ И КАТАСТРОФЫ НА ПРЕДПРИЯТИЯХ ПИЩЕВОЙ (ПЕРЕРАБАТЫВАЮЩЕЙ) ПРОМЫШЛЕННОСТИ
ГЛАВА 2. ОРГАНИЗАЦИЯ МЕДИЦИНСКОЙ ПОМОЩИ ПОСТРАДАВШИМ ПРИ АВАРИЯХ НА ПРЕДПРИЯТИЯХ ПИЩЕВОЙ (ПЕРЕРАБАТЫВАЮЩЕЙ) ПРОМЫШЛЕННОСТИ
ГЛАВА 1. АВАРИИ И КАТАСТРОФЫ НА ПРЕДПРИЯТИЯХ ПИЩЕВОЙ (ПЕРЕРАБАТЫВАЮЩЕЙ) ПРОМЫШЛЕННОСТИ
Чрезвычайные ситуации техногенного характера: причины возникновения, последствия, поражающие факторы
ЧС - это обстоятельства, возникающие в результате стихийных бедствий, производственных аварий, катастроф, диверсий, факторов военного, социального и политического характера и оказывающие значительное отрицательное воздействие на жизнедеятельность людей, экономику, социальную сферу и природную среду.
Классификация чрезвычайных ситуаций по скорости распространения их опасности.
. Внезапные (взрывы, транспортные аварии, землетрясения).
. С быстро распространяющейся опасностью (пожары, аварийно-химические опасные вещества).
. С умеренно распространяющейся опасностью (выброс РВ, аварии на коммунальных системах и т.д.).
. С медленно распространяющейся опасностью (авария на очистных сооружениях, оползни).
Необходимость такой классификации ЧС связана тем, что в при возникновения стихийных бедствий, аварий, катастроф часто оценив по-разному. Допускаются ошибки и просчёты при определении потребности в силах и средствах для ликвидации их последствий. Чтобы избежать ошибок и просчётов, установить единые подходы к оценке ЧС, было принято вышеуказанное постановление правительства от 13.09.96 г. № 1094.
В данной классификации чрезвычайные ситуации природного и техногенного характера классифицируются в зависимости от количества пострадавших людей, у которых оказались нарушены условия жизнедеятельности, от размера материального ущерба, а также границ, зон распространения ЧС.
|
Все чрезвычайные ситуации в зависимости от сферы возникновения
подразделяются:
. Чрезвычайные ситуации природного характера - возникают в природе.
. Чрезвычайные ситуации техногенного характера - возникают на производстве.
. Чрезвычайные ситуации экологического характера - возникают в экологической сфере.
Причины возникновения чрезвычайных ситуаций можно условно
разделить на объективные и субъективные.
К объективным причинам можно отнести такие явления, которые не подвластны человеку и пока наука не в состоянии точно прогнозировать их.
К субъективным причинам возникновения ЧС можно отнести:
невнимательность, недисциплинированность, порою халатность обслуживающего персонала;
нарушение технологии производства, несоблюдение правила техники безопасности;
несоблюдение правил хранения, транспортировки радиоактивных, сильнодействующих ядовитых и взрывоопасных веществ. Террористические акты, ЧС природного характера, пожары, взрывы и многие другие:
В настоящее время в народном хозяйстве широко применяются химические соединения, большинство из которых представляют опасность для человека. Из 10 млн. химических соединений, применяемых в промышленности, сельском хозяйстве и быту, более 500 высокотоксичные и опасны для человека.
Как мы знаем, предприятия пищевой, мясомолочной промышленности, хладокомбинаты, продовольственные базы, имеющие холодильные установки, в которых в качестве хладогена используется аммиак, относятся к химически-опасным объектам.
Причинами аварий на пищевом производстве, использующем химические вещества, чаще всего бывает:
- нарушение правил транспортировки и хранения ядовитых веществ
- несоблюдение правил техники безопасности
- выход из строя агрегатов, механизмов, трубопроводов
|
- неисправность средств транспортировки
- разгерметизация емкостей хранения
- превышение нормативных запасов
Каждые сутки в мире регистрируется около 20 химических аварий.
Примерами могут служить:
В результате аварий или катастроф на пищевых предприятиях возникает очаг химического заражения (ОХЗ). В очаге химического поражения или зоне химического заражения (ЗХЗ) может оказаться само предприятие и прилегающая к нему территория. В соответствии с этим выделяют 4 степени опасности пищевых предприятий:
I. В зону возможного заражения попадают более 75000 человек
II. В зону возможного заражения попадают 40000 - 75000 человек. В зону возможного заражения попадают менее 40000 человек. Зона возможного химического заражения не выходит за пределы предприятия.
Последствия аварий на пищевых предприятиях определяются степенью опасности химических веществ и их токсичностью.
Причины возникновения аварий на пищевых предприятиях бывают разнообразными. Сюда можно отнести взрыв холодильных компрессоров, взрыв паровых котлов, отравление аммиаком и другими отравляющими веществами.
К числу предприятий пищевой (перерабатывающей) промышленности, ведущих свою деятельность в Республике относятся:
1. Хасавюртовский консервный завод;
2. Буйнакский консервный завод;
. Дербентский консервный комбинат;
. Маджалисский консервный завод;
. Кегерский консервный завод;
. Чиркатинский консервный завод;
. Махачкалинский гормолзавод;
. Кизлярский гормолзавод;
. Махачкалинский мясокомбинат;
. Кизлярский мясокомбинат;
. Махачкалинский винзавод;
. Дербентский коньячный комбинат;
. Кизлярский коньячный комбинат;
. Шамхалский мелкомбинат;
. Хлебозаводы №1 и № 2 г.Махачкала.
На вышеперечисленных пищевых предприятиях основными вредными факторами, которые могут вызвать различные профессиональные заболевания и хронические отравления являются: низкая или высокая температура и относительная влажность, сквозняки, запыленность рабочей зоны, загазованность рабочей зоны, шум превышающий допустимые значения, вредные вибрации, недостаточное освещение рабочих мест, различные излучения от электроприборов промышленной частоты и высокой частоты (ВЧ) и др.
Кроме того, на указанных предприятиях опасными факторами, которые могут вызвать травмы, аварии и создать ЧС являются:
|
1. поражение электрическим током;
2. взрывы подогревателей, выпарных аппаратов, компрессоров холодильных установок, паровых котлов, баллонов со сжатым, сжиженным и растворенным газами;
3. попадание человека в опасную зону вращающих частей оборудования;
4. падение грузов при их перемещении на определенной высоте из-за обрыва тросов;
5. пожары и взрывы на пожаро и взрывоопасных помещениях и цехах;
. несоблюдение норм и правил при проведении технологических процессов и др..
Предприятия пищевой промышленности (мясная, молочная, рыбная, кондитерская, пивоваренная) применяют системы холодоснабжения в основном на базе аммиачных холодильных установок.
Известны преимущества аммиачных холодильных установок с непосредственным кипением аммиака в камерных охлаждающих устройствах:
Аммиак не входит в число веществ, регулируемых Монреальским протоколом и поправками к нему, а также Киотским протоколом.
Как рабочее вещество холодильных машин аммиак энергетически высокоэффективен в диапазоне используемых температур кипения и конденсации.
За годы применения аммиака накоплен большой практический опыт - хорошо изучены его теплофизические, энергофизические и гидродинамические характеристики, результат воздействия на живые организмы, определены основные компенсирующие мероприятия, обеспечивающие практически безопасное его использование.
Разработаны Нормы и Правила безопасной эксплуатации аммиачных холодильных установок (ПБ 09-595-03).
Вместе с тем известно, что аммиак - токсичное вещество 4-го класса опасности. Предприятия, эксплуатирующие аммиачных холодильных установок, попадают под действие Федерального закона «О промышленной безопасности опасных производственных объектов» № 116-ФЗ от 21.07.97 г. (далее - Ф.з. № 116-ФЗ) в первую очередь потому, что аммиак имеет среднюю величину смертельной концентрации в воздухе, соответствующую указанной в Законе (от 0,5 мг/л до 2,0 мг/л включительно), приводящей к гибели живых организмов. Кроме того, аммиачных холодильных установок потенциально взрыво- и пожароопасны. Поэтому, кроме лицензии на эксплуатацию химически опасного производственного объекта организации, эксплуатирующей аммиачные холодильные установки, необходимо оформление лицензии на эксплуатацию взрывоопасного производственного объекта.
|
Причины взрывов холодильных компрессоров
На предприятиях пищевой промышленности используются холодильные установки холодопроизводительностью 30…2500 кВт, обеспечивающие температуры охлаждающей среды - 45…+15 град. С. Масса аммиака в системах составляет 1…12 т.
Основные изменения в составе и конструктивном использовании холодильных установок, направленные на повышение уровня их безопасности, произошли за период с 80-х годов ХХ в. По настоящее время их можно обобщенно свести к следующему:
На базе поздних аммиачных холодильных установок стали применяться более безопасные насосно-циркуляционные системы вместо безнасосных.
На ряде предприятий поршневые компрессоры заменены винтовыми, для которых неопасно попадание жидкого аммиак в полость сжатия.
В машинных отделениях предприятий начали устанавливать сигнализаторы концентрации паров аммиака с порогами срабатывания на в основном на втором и редко на третьем уровнях.
На всех предприятиях установлены системы противоаварийной защиты (система ПАЗ), предусматривающие защиту компрессоров от гидравлического удара, защиту промышленных агрегатов от работы с повышенными давлением и температурой нагнетания, защиту компрессоров по системе смазки и др.
На ряде предприятий стали применять малоаммиакоемкие холодильные машины с пластинчатыми конденсаторами, испарителями и промежуточным хладоносителем (как правило, пропиленгликолем), охлаждающим камерные устройства.
Вместе с тем фактически в исполнительных технических решениях АХУ предприятий, а также в режимах их эксплуатаций по-прежнему имеются отклонения от требований ПБ 09-593-03.
Результаты обследований организаций, расположенных на территории Республики Дагестан и Российской Федерации, позволили выявить основные особенности систем холодоснабжения большинства действующих предприятий, а именно:
Количество аммиака практически на всех предприятиях остается высоким (2…12 т). В связи с изменившимися условиями хозяйствования часть камер остается без охлаждения, тепловая нагрузка на систему холодоснабжения снижена. По ПБ 09-595-03 и ФЗ № 116-ФЗ охлаждающие устройства этих камер должны быть либо законсервированы, либо демонтированы, причем количество аммиака в системе должно быть уменьшено. На самом деле такая работа на предприятиях не проводится, лишь перекрывается подача аммиака в охлаждающие устройства;
Наиболее опасным технологическим блоком является линейный или дренажные ресивер вместимостью 1,5…3,5 м3 с массой аммиак соответственно 1,2…2,7 т в блоке;
|
Обычно суммарная емкость установленных в машинном отделении или на наружной площадке линейных ресиверов значительно превосходит требуемую по ПБ 09-595-03, так как ресиверы по-прежнему используются для хранения запасов аммиака.
На большей части обследованных предприятий линейные ресиверы размещены на наружных площадках (до 2-4 шт. на площадке). Причем иногда ресиверы объединены по пару и жидкости, работая как сообщающиеся сосуды, что превращает их в единый технологический блок.
Согласно расчетам по нормативной методике Госкомгидромета и ГО ЧС России, при аварии с полным разрушением ресивера 5 РД, установленного без поддона на наружной площадке, при наиболее неблагоприятных атмосферных условиях глубина зоны химического заражения может достигать приблизительно 1,2 км.
Из-за близости расположения мест массового проживания людей наружные площадки предприятия с аммиачными блоками представляют особую опасность. Некоторые предприятия находятся от мест массового пребывания людей (жилые массивы, торговые точки и др.) на расстоянии много меньше, чем глубина зоны заражения при аварии на наружной площадке.
На предприятиях отсутствует система контроля утечек аммиака (если она установлена) не имеет автоматической блокировки с системой аварийной вентиляции, лишь дает сигнал на ручное включение вентиляции. Также отсутствуют акты с результатами испытаний, подтверждающих требуемую производительность системы вентиляции.
Систему подавления паров аммиака в машинном отделении нет ни у одного из обследованных предприятий.
В соответствии с ПБ 09-595 и ПБ 03-576-03 «Правилами устройств и безопасной эксплуатацией сосудов, работающих под давлением» предприятия проводят периодическое освидетельствование и экспертизу промышленной безопасности аммиачных аппаратов и сосудов, работающих под давлением. Однако при этом уделяется недостаточно внимания стороне низкого давления холодильных систем за пределами машинного отделения, которая охватывает большую часть производственных цехов (иногда и территории предприятия). На подавляющем числе предприятий не проводится освидетельствование и экспертиза промышленной безопасности камерных охлаждающих устройств и подводящих трубопроводов. Результатом этого по России являются аварии именно на воздухоохладителях, батареях и трубопроводах стороны низкого давления (от камерных охлаждающих устройств до циркуляционных ресиверов).
Большое количество аммиака в системах холодоснабжения хладокомбинатов в первую очередь связано с использованием батареи в качестве камерных охлаждающих устройств.
На подавляющей части обследованных предприятий отсутствует заключение экспертных организаций о состоянии строительных конструкций машинного отделения и холодильника.
На некоторых предприятиях отсутствует автоматическая сигнализация о пожаре в машинном отделении, а также блокировка автоматической пожарной сигнализации с системой вентиляции.
В плане организационно-техническом выявленные при проверках отклонения от ПБ 09-595-03 заключаются в следующем:
Не везде проводится своевременно проверка средств противоаварийной защиты.
На некоторых предприятиях отсутствуют учебно-тренировочные занятия по ликвидации аварий.
В связи с широким использованием арендных отношений на холодильниках сложилась ситуация двойного подчинения систем охлаждения камер: оборудование размещено в камерах, формально (на текущий момент) принадлежащих арендатору. Это создает трудности в доступе к данному оборудованию специалистов, обеспечивающих фактическую эксплуатацию холодильной установки.
Завышенная аммиакоемкость обследованных предприятий по сравнению с ожидаемыми расчетно-нормативными значениями обусловлена в первую очередь:
Использованием батарей вместо воздухоохладителей.
Повсеместным применением линейных ресиверов завышенной вместимости (или дополнительно установленных линейных ресиверов) для хранения запасов аммиака.
Наличием протяженных аммиачных трубопроводов между машинным отделением и потребителями холода.
Завышенными значениями кратности циркуляции аммиака в воздухоохладителях (батареях) и технологических аппаратах.
При анализе промышленной безопасности при эксплуатации аммиачных холодильных установок необходимо отметить: основное требование к системам холодоснабжения - их безопасность для населения. Систему можно считать практически безопасной, если в случае аварии с разрушением единичного самого опасного блока системы не происходит поражение людей за границей территории предприятия. Поскольку безопасность объекта в большей степени зависит от массы заправленного в систему аммиака, то принципиально речь идет о создании новых систем с малой массой аммиака в единичной системе.
Техническое перевооружение систем холодоснабжения с обеспечением безопасности должно предусматривать использование одного из приведенных ниже вариантов, выбор которого определяется на основании предпроектной проработки и ТЭО (технико-экономического обоснования):
Переход на охлаждение камер воздухоохлаждающими установками.
Переход на аммиачные системы холодоснабжения с промежуточным хладоносителем.
Разделение централизованной системы хладоснабжения на несколько автономных систем, обслуживающих каждое ограниченное число потребителей холода (при уменьшенной емкости отдельных аммиачных блоков).
Применение каскадных установок с СО2 в нижней ветви каскада и аммиаком в верхней.
Причины взрывов паровых котлов
На предприятиях пищевой и зерноперерабатывающей промышленности Республики Дагестан установлено и используется большое количество паровых котлов, баллонов, автоклавов, компрессоров, ресиверов, теплообменников и других видов оборудования, работающих под давлением.
Взрывы сосудов, сопровождающиеся большими разрушительными последствиями, характеризуются работой адиабатического расширения сжимаемого или сжатого газа.
Практика эксплуатации паровых котлов и сосудов, работающих под давлением, показывает, что при нарушении действующих правил по технике безопасности имеют место случаи взрывов и аварий, сопровождающиеся разрушениями зданий и сооружений, а также травматизмом обслуживающего персонала.
Под сосудом, работающим под давлением, подразумевается герметически закрытая емкость, - предназначенная для ведения химических и тепловых процессов, а также хранения и перевозки сжатых, сжиженных и растворенных газов и жидкостей под давлением выше атмосферного. Границей сосуда являются входные и выходные штуцера.
На предприятиях пищевой промышленности сосуды, работающие под давлением, широко применяются во всех отраслях как для технологических, так и энергетических целей.
В сахарной, консервной, кондитерской и других отраслях эксплуатируется многочисленная варочная аппаратура различной конструкции (двустенные варочные котлы, выпарные аппараты, вакуум-аппараты и т. п.), автоклавы (стерилизаторы); много сосудов, работающих под давлением, применяется в пиво-безалкогольной, винодельческой, спиртовой и других отраслях для сбраживания технологических продуктов. Bо всех отраслях пищевой промышленности применяются сосуды как энергетическое оборудование (теплообменники, аппаратура холодильных установок, воздушных компрессорных установок и т. д.).
Сосуды, работающие под давлением, относятся к оборудованию с повышенной опасностью, поэтому при их конструировании, изготовлении и эксплуатации особенно важно знать и выполнять требования правил безопасности.
В зависимости от величины рабочего давления все сосуды распределяются на две группы. К первой группе относятся сосуды, которые работают под давлением более 0,07 МПа (без учета гидростатического давления) и на которые в основном (за исключением отдельных случаев) распространяются «Правила устройства и безопасной эксплуатации сосудов, работающих под давлением», утвержденные Госгортехнадзором СССР в 1970 г, ко второй -сосуды, которые работают под давлением до 0,07 МПа. Требования техники безопасности к таким сосудам приведены в отраслевых правилах по технике безопасности и производственной санитарии.
Правила устройства и безопасной эксплуатации сосудов, работающих под давлением, не распространяются: на сосуды и баллоны вместимостью не более 25 л, для которых произведение вместимости (в л) на рабочее давление (в МПа) Vp составляет не более 20; на части машин, не представляющие собой самостоятельных сосудов (цилиндры двигателей паровых и воздушных машин- и компрессоров, неотключаемые промежуточные холодильники и маслоотделители компрессорных установок и т. п.); на сосуды, изготовленные из неметаллических материалов, независимо от рабочего давления; на трубчатые печи независимо от диаметра труб; на сосуды, состоящие из труб внутренним диаметром не более 150 мм; на сосуды, работающие под давлением воды температурой не выше 115 °С, а также других жидкостей температурой не выше точки кипения при давлении 0,07 МПа.
При определении полной вместимости того или иного аппарата (сосуда) не учитывается объем, занимаемый находящимися внутри аппарата (сосуда) различными устройствами (валы, мешалки, трубы и т. п.).
Группа сосудов, а также сосуды, состоящие из отдельных корпусов и соединенные между собой трубами внутренним диаметром не более 100 мм, рассматриваются как один сосуд, если между ними нет запорных органов.
При обогревании сосуда или аппарата открытым пламенем, горячими' газами температурой 250 °С и выше или открытыми электронагревателями расчетная температура стенки принимается равной температуре среды, находящейся внутри сосуда (аппарата), увеличенной не менее чем на 5 °С
Сосуды первой группы и их элементы, работающие под давлением, оснащаются предохранительными устройствами.
По статистическим данным, основными техническими причинами взрывов паровых котлов являются: упуск воды в котле, дефектность основных конструктивных элементов котла, превышение рабочего давления, неудовлетворительный водный режим котла и образование накипи, наличие взрывоопасных топочных газов.
Опасность эксплуатации указанных аппаратов заключается возможностью их взрыва. Взрыв - это высвобождение энергии перегретой воды, пара, газа или воздуха в результате разрушения стенок сосудов. При котором мгновенно снижается внутреннее давление до атмосферного.
Например, в паровых котлах перегретая вода превращается в пар. При этом из 1м3 воды образуется 1700м3 пара, что приводит к разрушению котла, помещений и травматизму работающих.
Взрыв может быть из-за нарушения целостности стенок котла, причинами которых являются:
. превышение рабочего давления выше критического, что увеличивает ползучесть материала, это может быть при неисправности манометров и предохранительных клапанов;
2. понижение уровня воды (пуск воды) в котле до такого положения, когда нагреваемые пламенем стенки котла не охлаждаются водой и перегреваются.
. недостатки конструкции и изготовления котла (несоответствие материала котла современным расчетным параметрам котлов, дефекты сварки или клепки при изготовлении и др.)
. местное ослабление котла в результате образования накипи и коррозии.
Накипь толщиной более 0,5 мм не допускается. Для этого соответствующим образом осуществляют подготовку воды (тщательный анализ воды, использование конденсата, смягчение питательной воды, отстаиванием, фильтрацией, обработкой сульфоуглем, синтетическими смолами и др.).
Содержание солей Са++ и Мg++ в воде должно быть не более 500мг-экв/л при рабочем давлении до 3,9 МПа, а для водотрубных котлов с рабочим давлением до 1,3 мПа - до 20 мг-экв/л.
При взрыве сосудов, работающих под избыточным давлением выделяется энергия адиабатического расширения сжатого газа или перегретой воды:
, Дж
где: Р1 - начальное давление в аппарате до взрыва, ПА;
Р2 - конечное (атмосферное) давление после взрыва, ПА;
V - начальный объем газа, м3;
К - показатель адиабаты (для воздуха К=1,41)
Мощность взрыва составляет:
,
где: τ- время взрыва, С.
Паровые котлы снабжаются арматурой, КИП и приборами безопасности. На каждом аппарате устанавливают не менее 2-х манометров (1 рабочий, а другой контрольный); не менее 2-х предохранительных клапанов, которые открывают пару (газу) свободный выход из аппарата (котла) в атмосферу при повышении в нем давления выше 10%.
Предохранительные клапаны рассчитывают по формуле:
, кг/ч
где: G - пропускная способность клапана, кг/ч;
α - коэффициент расхода газа (жидкости);
F - площадь сечения клапана, мм2;
В - коэффициент расширения истекающей струи, В=0÷1;
Р1 и Р2- максимальное избыточное давление перед предохранительным клапаном и за ним, Па;
g- плотность среды, кг/м3.э
Суммарная пропускная способность предохранительных, устанавливаемых на котле, должна быть не менее часовой производительности парового котла.
Для поддержания уровня воды в котле устанавливают автоматические регуляторы уровня воды, водопрочные краники, пьезометры достаточное количество питательных насосов (не менее 2, один из которых - паровой), а также устанавливают автоматические звуковые сигнализаторы верхнего и нижнего предельных положений уровней воды, а также автоматические регуляторы, которые прекращают подачу газа к горелкам в случае снижения уровня воды ниже допустимого предела.
На предприятиях пищевой промышленности установлены котлы, работающие в основном под избыточным давлением до 0,07 и выше 0,6 МПа; в хлебопекарной -0,07 МПа, кондитерской-0,4-1,0 МПа, сахарной--3,9 МПа и т. д.
Наибольшее количество аварий, имеющих место при эксплуатации паровых котлов, происходит обычно из-за упуска воды. Анализ причин показывает, что аварии из-за упуска воды происходят главным образом из-за нарушения трудовой дисциплины и несоблюдения правил техники безопасности. Упуск воды в котле может вызвать:
а) перегрев стенок котла в топочной части, что особенно опасно при нагреве конструкции выше критических точек В этом случае металл стенок котла может выдуваться под действием давления пара и создавать отдулины или выпучины которые иногда приводят к взрыву;
б) попадание воды на перегретые стенки котла. В этом случае металл подвергается закалке, вода мгновенно превращается „ пар, увеличиваясь в объеме в 1200-1700 раз, стенки котла разрушаются и может произойти взрыв.
Дефектность основных конструктивных элементов котла - вторая причина аварий сосудов, работающих под давлением.
Прочность котла зависит от правильности ее расчета и выбора материала при изготовлении основных его частей, а также соблюдения правильной эксплуатации котла. Для деталей котла применяется листовая и литая сталь. Для изготовления котлов, работающих под повышенным давлением, применяется низколегированная сталь с добавлением кремния, молибдена и хрома. Чугунное литье допускается только для водяных экономайзеров и арматуры незначительных диаметров, нагреваемой' до 300 °С при малых давлениях.
На заводах - изготовителях паровых котлов действует система контроля за качеством металла, применяемого для котлостроения.
Образование накипи может явиться еще одной причиной аварии. Под слоем накипи стенки внутри котла не охлаждаются, а перегреваются, так как ухудшаются условия теплопередачи от газов к воде, вследствие чего появляется опасность взрыва. Накипи толщиной более 0,5 мм допускать нельзя.
На пищевых предприятиях и предприятиях по хранению и переработке зерна в зависимости от паропроизводителыюсти котлов, качества воды, применяемой для питания котлов, и других факторов приняты соответствующие методы водоподготовки.
Все котлы паропроизводительностыо 0,7 т/ч и более должны быть оборудованы установками для докотловой обработки воды.
В котельной должен быть заведен журнал (ведомость) по водоподготовке для записей результатов анализов воды, выполнения режима продувки котлов и операции по обслуживанию оборудования водоподготовки.
У котлов паропроизводительностыо менее 0,7 т/ч период между чистками должен быть таким, чтобы толщина отложений на наиболее теплонапряженных участках поверхности нагрева котла к моменту его остановки на очистку не превышала 0,5 мм.
Нарушение правил подачи 'горючего в топочную часть также может явиться причиной аварии. Строгое соблюдение правил техники безопасности в отношении работы топочной части является непременным условием, исключающим взрыв топочных газов.
Техническое освидетельствование паровых котлов.
Для предупреждения аварий, взрывов и чрезвычайных ситуаций предусмотрено освидетельствование паровых котлов до пуска в работу, периодически в процессе их эксплуатации и досрочно после ремонта элементов котла, находящихся под давлением и во всех случаях при остановке котла на срок свыше 1 года.
Техническое освидетельствование производится инспектором Госгортехнадзора (котлонадзора) и состоит из внутреннего осмотра и гидравлического испытания.
Внутренний осмотр производится не реже 1 раза в 4 года с целью выявления состояния помещения, стен, перекрытий, арматуры, паропроводов, изоляции, внутренних и наружных поверхностей, влияния среды на стенки сосудов, состояния заклепочных соединений котла и труб, состояния дымоходов.
Гидравлическое испытание проводят не реже 1 раза за 8 лет.
Гидравлическое испытание проводится водой с целью проверки плотности и прочности швов парового котла, а также всех сварных и других соединений.
Температура воды должна быть не ниже 5оС.
Гидравлическое испытание сосудов, работающих при температуре до 200оС, проводят:
) пробным давлением 1,5 Рраб. Время выдержки котла под пробным давлением не менее 5 мин (при толщине стенки 50мм - 10 мин, а при толщине стенки 50-100 мм - 20 мин). Если за указанное время не будет течи, слезок, потемнения, разрывов, видимых деформаций, то паровой котел годен к эксплуатации.
Баллоны предназначены для наполнения, хранения, перевозки и использования сжатых, сжиженных и растворенных газов. Главная опасность баллонов - это возможность взрыва и утечки газов, которые приводят к отравлению людей и чрезвычайным ситуациям.
Основными причинами взрыва баллонов являются:
. внезапное расширение газов из-за повышения температуры;
. удары (падения) баллонов;
. переполнение баллонов сжиженными газами;
. ошибочное использование баллонов;
. порча нарезки вентиля (при этом действием реактивной силы баллон отбрасывается назад с большой силой, что возможны несчастные случаи и разрушения зданий);
. попадание масла на вентиль кислородного баллона или наличие окалины (ржавчины) внутри баллона;
. недоброкачественный материал баллона;
Баллоны с водородом могут взорваться при попадании в них кислорода в количестве более 1%, образованием взрывчатых смесей в процессе кислородно-водородной сварки и при накоплении в баллонах окалины.
Для предупреждения аварий необходимо при приемке баллонов придерживаться следующих основных требований:
. баллоны должны иметь специальную окраску и надпись;
. иметь четко выбитую пломбу (клеймо);
. должны быть снабжены предохранительными колпачками;
. не иметь видимых деформаций;
Окраска дает возможность внешне отличить баллоны друг от друга и предохраняет их от коррозий.
Таблица 1
Маркировка баллонов
Газ | Окраска баллонов | Текст надписи | Цвет надписи | Цвет полосы |
Аммиак | Желтая | Аммиак | Черный | - |
Ацетилен | Белая | Ацетилен | Красный | - |
Водород | Темно-зеленая | Водород | Красный | - |
Воздух | Черная | Сжатый воздух | Белый | - |
Кислород | Голубая | Кислород | Черный | - |
Сероводород | Белая | Сероводород | Красный | Красный |
Сернистый ангидрид | Черная | Сернистый ангидрид | Белый | Желтый |
Углекислота | Черная | Углекислота | Желтый | - |
Фреон | Алюминиевая | Фреон №11 №12 №13 №22 | Черный | Одна синяя полоса - 2 красные 2 желтые |
Горючие газы | Красная | Наименование газа | Белый | - |
Другие негорючие газы | Черная | Тоже | Желтый | - |
Хлор | Защитная | - | - | Зеленый |
Этилен | Фиолетовая | Этилен | Красный | - |
В зависимости от назначения все баллоны разделяются на типы (марки) А, Б, В, Г и Д.
Таблица 2
Классификация баллонов
Тип баллона | Газ, находящийся в баллоне | Давление, кгс/см2 | |
рабочее | испытательное | ||
А | О2, Н2, N2, СН4, сжатый воздух, инертные газы | 150 | 225 |
Б | СО2 | 125 | 190 |
В | Ацетилен С2Н2 | 30 | 60 |
Г | Сернистый ангидрид SО2 | 6 | 12 |
Д | Аммиак NН3, хлор С ![]() |
Боковые штуцера вентилей для баллонов, наполняемых водородом и другими горючими газами, должны иметь левую резьбу, а для баллонов, не наполняемых кислородом О2 и другими негорючими газами - правую.
Клеймо. На верхней сферической части баллона должны быть отчетливо нанесены клеймением следующие данные:
.товарный знак завода- изготовителя;
. номер баллона;
. масса пустого баллона, кг;
. емкость баллона, л;
. дата (месяц, год) изготовления и год следующего освидетельствования;
. рабочее давление;
. пробное гидравлическое давление;
. клеймо ОТК завода изготовителя диаметром 10мм;
. номер стандарта для баллонов объемом более 55л.
Место на баллоне, где выбиты паспортные данные, должно быть покрыто бесцветным лаком и обведено отличительной окраской в виде рамки.
Согласно требованиям техники безопасности на боковой штуцер навинчивают заглушку, предохраняющую его от засорения, а весь вентиль закрывают предохранительным колпаком для защиты от случайного повреждения.
Ацетилен в обычных баллонах взрывается при сжатии выше 0,1 МПа. Поэтому баллоны для ацетилена отличаются от других баллонов. Для хранения и перевозки ацетилена применяют стальные баллоны, заполненные пористой массой, пропитанной ацетиленом. Благодаря растворяющей способности ацетилена 40 литровый баллон вмещает 7,5м3 ацетилена под давлением 20 атм. В качестве пористой массы применяется активированный уголь БАУ.
Для газов, находящихся под давлением до 30 атм, допускается применение сварных баллонов, а при более высоком давлении - баллоны бесшовные.
Эксплуатация баллонов. Запрещается наполнять газом баллоны, у которых:
. истек срок технического освидетельствования;
. отсутствует клеймо;
. неисправный вентиль;
. поврежден корпус;
. окраска и надписи не соответствуют настоящим Правилам;
Не снимать с баллона предохранительный колпачок до начала работы. Открывать вентиль следует только усилием руки, без применения ключей, рычагов, за исключением ацетиленовых баллонов, вентили которых вместо маховичков имеют квадраты - их открывают торцовым ключом.
Выпуск газа из баллонов в емкости с меньшим давлением должен производиться через редуктор, предназначенный исключительно для данного газа. Камера низкого давления редуктора должны иметь манометр и пружинный предохранительный клапан, отрегулированный на соответствующее разрешаемое давление в емкости, в которую перепускается газ. Штуцер продуть для удаления загрязнения.
При замерзании вентиля или редуктора их обогревают тряпками смоченными в горячей воду, а не огневыми лампами. После окончания работы вентиль прикрывают колпачками, а боковой штуцер завинчивают глухой гайкой.
Хранение баллонов. Склады для хранения баллонов должны быть устроены из огнестойкого материала и должны быть сухими, светлыми и хорошо вентилируемыми.
Баллоны с газом, устанавливаемые в помещениях должны находиться от радиаторов отопления на расстоянии не менее 1м, а от открытых источников тепла - не менее 5м.
Баллоны с горючими газами могут находиться в одном помещении с инертными газами.
Полы складов должны быть асфальтированными, исключающие образование искр при ударе о них каких либо предметов; двери и окна должны открываться наружу.
Балл
|
|
Наброски и зарисовки растений, плодов, цветов: Освоить конструктивное построение структуры дерева через зарисовки отдельных деревьев, группы деревьев...
Архитектура электронного правительства: Единая архитектура – это методологический подход при создании системы управления государства, который строится...
Типы оградительных сооружений в морском порту: По расположению оградительных сооружений в плане различают волноломы, обе оконечности...
Типы сооружений для обработки осадков: Септиками называются сооружения, в которых одновременно происходят осветление сточной жидкости...
© cyberpedia.su 2017-2024 - Не является автором материалов. Исключительное право сохранено за автором текста.
Если вы не хотите, чтобы данный материал был у нас на сайте, перейдите по ссылке: Нарушение авторских прав. Мы поможем в написании вашей работы!