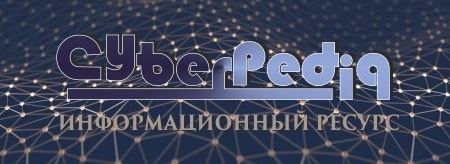
Опора деревянной одностоечной и способы укрепление угловых опор: Опоры ВЛ - конструкции, предназначенные для поддерживания проводов на необходимой высоте над землей, водой...
Биохимия спиртового брожения: Основу технологии получения пива составляет спиртовое брожение, - при котором сахар превращается...
Топ:
Характеристика АТП и сварочно-жестяницкого участка: Транспорт в настоящее время является одной из важнейших отраслей народного хозяйства...
Определение места расположения распределительного центра: Фирма реализует продукцию на рынках сбыта и имеет постоянных поставщиков в разных регионах. Увеличение объема продаж...
Интересное:
Национальное богатство страны и его составляющие: для оценки элементов национального богатства используются...
Подходы к решению темы фильма: Существует три основных типа исторического фильма, имеющих между собой много общего...
Средства для ингаляционного наркоза: Наркоз наступает в результате вдыхания (ингаляции) средств, которое осуществляют или с помощью маски...
Дисциплины:
![]() |
![]() |
5.00
из
|
Заказать работу |
|
|
Другой критерий относится к способности метода испытания измерить ранее упомянутые фундаментальные свойства. Результаты эмпирических проверок имеют ценность только для тех эмпирических методов проектирования, из которых они были разработаны. Попытки использования эмпирических методов для оценки основных свойств через корреляции, в лучшем случае очень неэффективны и должны с осторожностью использоваться только тогда, когда нет другой возможности. Большая часть корреляций между действительной работой и исследованными в результате испытаний свойствами, показали, что физические свойства асфальтобетонных смесей показывают лучшую корреляцию с их работой. Однако, для развития практических фундаментальных тестов, остается необходимость в глубоком исследовании этого вопроса. Эти тесты могут быть использованы в разработках дизайна смесей и контроле качества смесей, для оценки их работоспособности на высоком уровне надежности.
Простота тестирования
Простота тестирования также является важным критерием, применимым к любому предлагаемому методу испытаний. Часто «несовершенный» метод испытаний более предпочтителен из-за его простоты и легкой доступности выполнения без дорогого оборудования, длительного времени или интенсивного обучения персонала. Наиболее предпочтительно испытание, которое легко выполняется.
Однако простота и низкая стоимость испытаний не должна быть главным критерием для выбора данного метода испытания. Обычно, в сравнении с полной стоимостью проектирования, изготовления и техобслуживания дорожного покрытия, стоимость программы испытаний минимальна. Важно, чтобы использовались тесты, которые относятся к работе смеси, чтобы можно было определить эксплуатационную долговечность горячих асфальтобетонных смесей при различной нагрузке от движения транспорта и в различных климатических условиях.
|
Воспроизводимость результатов испытаний
Другой критерий относится к ошибке тестирования. В идеале метод испытаний должен быть составлен таким образом, чтобы две лаборатории испытывая одинаковую смесь, получили примерно равные результаты проверки. Один из способов измерения воспроизводимости, это коэффициент изменчивости, получаемый между определенным количеством лабораторий для идентично изготовленных и проверенных в лабораторных условиях образцов определенной смеси. Коэффициент изменчивости, полученный при использовании этого метода, предоставляет изменчивость присущую этому методу испытаний, которое появляется в процессе изготовления образца, от испытательного оборудования и ошибок персонала. Чтобы тест был полезен, он должен содержать минимальное количество ошибок, вызванных изменчивостью от испытательного оборудования и работы специалиста, иначе вместо того чтобы измерять истинные изменения в свойствах смеси, испытание измерит лишь коэффициент изменчивости этого метода. Испытания с высокой ошибкой измерений бесполезны для измерения свойств материалов, так как невозможно с уверенностью определить их истинные свойства.
СОВРЕМЕННЫЕ ИСПЫТАНИЯ
В течении многих лет было разработано большое разнообразие методов испытаний асфальтобетонных смесей, многие из которых используются до сих пор. Все эти разнообразные методы можно классифицировать по следующим различным категориям: испытания в реальных условиях в сравнении с лабораторными испытаниями; эмпирические в сравнении с фундаментальными испытаниями. Эти тесты группируются согласно типу испытаний (т.е., прямое растяжение, косвенное растяжение, сжатие, сдвиг, изгиб или скручивание). Наиболее предпочтительны те тесты, которые непосредственно описывают фундаментальные качества. Так как существует изменчивость в методах испытаний, основываясь на практическом опыте, сложились определенные предпочтения одних методов испытаний в пользу одних материалов и других методов испытаний в пользу других материалов.
|
Примеры испытаний, проводимых в реальных условиях, для косвенного определения технических свойств горячих асфальтобетонных смесей, это использование таких приборов измеряющих отклонение, как прогибомер (балка Бенкельмана), дефлектомер и дефлектомер падающего груза. В большинстве случаев полевые испытания можно использовать только для оценки существующего состояния. Таким образом, перед разработкой конструкции предполагаемой дорожной одежды, их можно использовать для оценки основания. Также в случае разработки программы восстановления уже существующего дорожного покрытия их можно использовать для оценки основного структурного состояния полотна или определения параметров его основания. Чтобы получить модуль упругости для различных слоев дорожного покрытия или композитного земляного полотна, при чтении результатов следует принимать во внимание условия, в которых проводились испытания, и необходимо применять технику обратного расчета по результатам измерений. Эти неразрушающие полотно испытания, хотя очень важны, не рассматриваются в этой главе.
Лабораторные испытания для определения свойств асфальтобетонных смесей, которые используются в настоящее время, состоят из оценки индивидуальных свойств асфальтового вяжущего и заполнителя, и затем оценки горячей асфальтобетонной смеси. Наиболее часто используемые испытания для определения параметров битумного вяжущего подробно рассматриваются во второй главе. Термическое растрескивание в горячих асфальтобетонных смесях это одно из повреждений, которое непосредственно зависит от свойств асфальтового вяжущего. Так как битумное вяжущее, прежде всего, противостоит растягивающему напряжению в асфальтобетонной смеси, развитие трещин часто зависит от способности битумного вяжущего выдерживать нагрузку без потери эксплуатационной пригодности.
Эффект воздействия заполнителя на работу смеси описывается в третьей главе. Главным образом, заполнитель дает поддержку при нагрузке от движения транспортных средств. В сопротивлении остаточной деформации важную роль играют угловатость, текстура поверхности, гранулометрический состав и твердость заполнителя.
|
Испытание асфальтобетонных смесей осуществляется для оценки их общего качества. До некоторой степени эти испытания оценивают соответствие качества битумного вяжущего, заполнителя, содержание битума и плотность. В идеале, эти испытания должны дать общее представление об эксплуатационной пригодности асфальтобетонных смесей. К сожалению, для оценки работы асфальтобетонных смесей нельзя использовать только испытания всей смеси. Поэтому, чтобы убедиться в ее удовлетворительных свойствах, необходимо также провести испытания заполнителя и битумного вяжущего.
Смесь для проверки изготавливается в лаборатории или забирается с асфальтобетонного завода во время ее изготовления. Точное определение свойств горячей асфальтобетонной смеси требует, чтобы ее сжали до той плотности, которую она приобретает после нескольких лет воздействия дорожного движения. За все время эксплуатации, плотность асфальтобетонной смеси увеличивается, при этом наибольшее увеличение плотности происходит во время первых двух, трех лет эксплуатации, полагая, что интенсивность дорожного движения не претерпевает значительных изменений. Правильно разработанная и изготовленная смесь сразу после изготовления обычно имеет 6 – 8 % воздушных пустот и приблизительно 4% после 2 – 3 лет движения транспорта.
Существуют два основных вида испытаний для определения свойств асфальтобетонных смесей: испытание физических свойств и испытание механических свойств. Испытание физических свойств включает в себя: измерение плотности, наличие воздушных пустот, пустот в минеральном заполнителе, пустот заполненных битумным вяжущим и параметров старения. Эти свойства, за исключением параметров старения, описываются в четвертой главе. Испытание механических свойств включает в себя: измерение стабильности по Маршаллу и подвижности, стабильности по Хвиму и сцепления, индекса вращательного сдвига (GSI), динамического модуля, модуля упругости, модуль прочности на изгиб, косвенного растяжения, сдвига и чувствительности к влаге.
|
Определение свойств асфальтобетонных смесей, при использовании процедуры смешивания по Маршаллу, в основном включает в себя измерение воздушных пустот, пустот в минеральном заполнителе, пустот заполненных битумным вяжущим, стабильности по Маршаллу, подвижности и чувствительности к влаге. Определение свойств асфальтобетонных смесей, при использовании процедуры смешивания по Хвиму в основном включает в себя: измерение воздушных пустот, пустот в минеральном заполнителе, стабильности по Хвиму и чувствительности к влаге. Другие тесты, например индекс вращательного сдвига, динамический модуль, модуль упругости, модуль прочности на изгиб, прочность при косвенном растяжении, прочность при сжатии, усталостность и сдвиг, в основном используются для исследовательских целей. Эти тесты важны и возможно некоторые из них будут использоваться в рабочем порядке в будущем, но на сегодняшний день они в основном не используются при разработке или контроле качества асфальтобетонных смесей. После завершения программы стратегических исследований в области автомобильных дорог (SHRP) некоторые из этих тестов, которые ранее использовались только для исследований, вполне вероятно будут использоваться в рабочем порядке для разработки или контроля качества горячих асфальтобетонных смесей.
Физические свойства
Воздушные пустоты. Физическое свойство, которое наиболее часто соотносится с эксплуатационными качествами смеси, это наличие воздушных пустот (для количественного вычисления пустот, смотри главу четыре). Исследования показали, что от количества воздушных пустот в горячей асфальтобетонной смеси зависит ее стабильность и долговечность. Когда содержание пустот в дорожном полотне уменьшается до 3%, наиболее вероятно из-за пластической деформации произойдет колееобразование (2, 3, 4).Однако когда наличие пустот превышает 8%, смесь начинает страдать от воздействия воды и воздуха, а также увеличивается скорость окисления битумного вяжущего (5, 6, 7), что приводит к преждевременному растрескиванию или расслоению. Скорость окисления зависит от общего объема воздушных пустот и толщины пленки асфальтового вяжещего. Сила уплотнения в лабораторных условиях (50-75 ударов/место по методу Маршалла) выбирается таким образом, чтобы обеспечить плотность асфальтобетонной смеси и наличия пустот, примерно равным, ожидаемым после двух трех лет дорожного движения. После этого воздушные пустоты в образцах, уплотненных в лабораторных условиях, дают представление о минимальном количестве воздушных пустот после двух трех лет воздействия дорожного движения.
|
Пустоты заполненные асфальтовым вяжущим. Пустоты, заполненные битумным вяжущим инверсивно соотносятся с воздушными пустотами. Когда процент воздушных пустот приближается к нулю, процент пустот заполненных асфальтовым вяжущим приближается к 100. В начале изготовления асфальтобетонной смеси, некоторый процент пустот становиться заполнен битумным вяжущим (обычно 50 – 70%). В процессе уплотнения асфальтобетонной смеси от нагрузки дорожного движения, процент пустот, заполненных асфальтовым вяжущим, начинает увеличиваться. Когда заполненность пустот становится больше 80% – 85%, обычно асфальтобетонная смесь становится нестабильной и начинается колееобразование.
Пустоты в минеральном заполнителе. Пустоты в минеральном заполнителе (VMA) в основном зависят от его гранулометрического состава, его формы и структуры поверхности. Когда пустот в наполнителе слишком мало, к смеси невозможно добавить достаточное количество битумного вяжущего, чтобы обеспечить достаточную толщину слоя без переполнения пустот. Смеси с низким количеством пустот в заполнителе более чувствительны к небольшим изменениям в содержании битума, чем те, где количество пустот больше. Большинство компаний не уточняют максимальный процент пустот в заполнителе, однако если он слишком высок, стабильность смеси может уменьшиться до нежелательного уровня. Необходимо следовать руководству для пустот в заполнителе, данному в главе 4.
Старение. Старение асфальтобетонных смесей затрагивает вязкость битумного вяжущего и может привести к ее повышению. Чтобы адекватно охарактеризовать асфальтобетонную смесь необходимо, чтобы образец был оценен с точки зрения старения. Для этого необходимо максимально приближенно смоделировать свойства асфальтобетонной смеси, которые она приобретет в процессе эксплуатации. Программа стратегических исследований в области автомобильных дорог (SHRP) разработала испытание на старение битумного вяжущего и горячих асфальтобетонных смесей.
Битумное вяжущее старится с помощью испытания на тепловое старение тонко-плёночной укаткой, чтобы имитировать его старение во время изготовления. Также битумного вяжущее старится в сосуде под давлением (PAV), чтобы имитировать старение после нескольких лет работы на месте. Измерение старения только битумного вяжущего, не самый лучшей метод для прогнозирования его свойств на все время эксплуатации, хотя это хороший и простой метод оценки его потенциального эксплуатационного возраста.
Так как скорость старения битумного вяжущего в смеси зависит от свойств самой смеси, например наличие воздушных пустот в дорожном покрытии, необходимо измерять старение все смеси. Системы смешивания Superpave требует, чтобы смесь испытывалась на старение в течении 2 – 4 часов перед смешиванием и перед уплотнением. Этот процесс имитирует старение смеси во время изготовления и укладки на полотно. Это также позволяет битумному вяжущиму поглощаться в крупный заполнитель, для имитации того, что будет происходить со смесью во время конструкции.
Superpave, также разработало метод старения уплотненной смеси, чтобы имитировать старение смеси, после укладки ее в качестве дорожного покрытия. Уплотненная смесь помещается в печь на долгий период времени, что приводит к окислению битумного вяжущего. После старения образцов подобным образом, они могут быть протестированы в условиях, подобных воздействию дорожного движения, что даст лучшее измерение ожидаемых эксплуатационных характеристик.
Механические испытания
Для оценки или проектировании горячих асфальтобетонных смесей используются два наиболее распространенных теста, это испытание на стабильность по Маршаллу и испытание на стабильность по Хвиму. Эти два теста и процедуры смешивания, широко применялись в индустрии раньше и будут и дальше использоваться, пока не будут разработаны и внедрены более совершенные методы испытаний. Так как оба этих метода имеют эмпирическую природу и не очень сильно соотносятся с работой смеси, остается необходимость в улучшенных методах испытаний.
Испытание на стабильность по Маршаллу. Испытание на стабильность по Маршаллу (ASTM D 1559) было разработано Инженерным корпусом в 1940-х и основано на концепции и методе, сформулированным Брюсом Маршаллом из дорожного департамента штата Массачусетс. Целью испытания является измерение прочности асфальтобетонной смеси, которую уплотнили стандартным лабораторным уплотнительным усилием. Это испытание также является частью процедуры смешивания по Маршаллу, где оно используется для выбора расчетного содержания битума, а также в контроле качества асфальтобетонных смесей.
Процедура испытания на стабильность по Маршаллу включает в себя применение, посредством полукруглых захватов, сжимающей нагрузки к цилиндрическому образцу 101,6мм (4 дюйма) в диаметре и 63,5мм (2,5 дюйма) в высоту, как это описывается в четвертой главе. Температура образца составляет 60°С (140°F); нагрузка подается со скорость 2 дюйма в минуту. Выбор температуры в 60°С (140°F) был обусловлен тем, что это средняя максимальная температура дорожного покрытия летом, таким образом имитируются самые сложные условия для асфальтобетонных смесей. Стабильность по Маршаллу - это максимальная нагрузка, которую выдерживает образец, или нагрузка необходимая, чтобы образец потерял эксплуатационную пригодность. Индекс текучести или коэффициент пассивного давления грунта – это полная вертикальная деформация (0,25мм (0,01 дюйма)) образца при максимальной нагрузке. Текучесть это полная деформация, от начала применения нагрузки до момента, когда она начинает уменьшаться. Для расчета характеристик смесей используется еще один параметр, это коэффициент жесткости по Маршаллу, который рассчитывается, как стабильность по Маршаллу разделенная на текучесть. Это эмпирическое значение жесткости и оно используется некоторыми инженерами, особенно в Европе, для определения качества смесей. Более высокое значение стабильности, разделенное на текучесть, указывает на более жесткую смесь и подразумевает, что смесь будет более устойчива к остаточной деформации. Существует очень мало эксплуатационных данных, которые указывали бы, что стабильность по Маршаллу/текучесть связана с эксплуатационными качествами дорожного покрытия. Испытание стабильности по Маршаллу подробно описывается в Четвертой Главе.
Стабилометр Хвима. Стабилометр Хвима был разработан Франциском Хвимом когда он работал в отделе управления шоссейных дорог штата Калифорния. Испытание с помощью стабилометра было разработано для эмпирического измерения внутреннего трения внутри смеси. Однако прочность или стабильность асфальтобетонной смеси зависит не только от внутреннего трения но и от сцепления. Поэтому для измерения параметров сцепления был разработан параллельный тест с использованием когезиометра. Вкратце, к образцу асфальтовой смеси 101,6 мм (4дюйма) в диаметре и 63,5мм (2,5 мм) в высоту применяется вертикальная осевая нагрузка и измеряется деформация. Во время испытания температура образца составляет 60°С (140°F), чтобы создать самые сложные условия для горячих асфальтобетонных смесей. Значение стабильности может варьироваться в диапазоне от 0 до 100; стабильность воды равна 0, стабильность стали равна 100.
Некоторые компании немного модифицировали процедуру и уравнение. В стабилометре устанавливается резиновая мембрана, которая обеспечивает ограничивающее давление, которое в нормальных условиях обеспечивается асфальтового вяжущим (сцепление). Таким образом, показания стабилометра становятся относительно не чувствительными к характеристикам битумного вяжущего, но указывают на параметры заполнителя. Подробно испытание по Хвиму описывается в Четвертой Главе.
Когезиометр. Когезиометр был разработан для измерения сцепления или параметров прочности при растяжении горячих асфальтобетонных смесей и является вспомогательным тестом. Образец 101,6 мм (4дюйма) в диаметре и 63,5мм (2,5 мм) в высоту испытывается при температуре 60°С (140°F). Посредством рычага на образец с постоянной интенсивностью подается нагрузка, что вызывает растягивающую нагрузку в образце, после чего считывается эмпирическое значение когезиометра или примерное значение прочности на растягивание. Таким же образом можно получить примерное значение деформации. Когезиометр стали использовать только сейчас, так как ошибка тестирования очень высока и измеренная когезия имеет очень небольшую взаимосвязь с эксплуатационными характеристиками смеси. Также, большинство горячих асфальтобетонных смесей проходят этот тест. С недавнего времени, в большинстве лабораторий, для исследования параметров прочности на растягивание, используется испытание на косвенное растяжение.
Модуль упругости. Для измерения модуля упругости используются динамический модуль упругости и модуль вязкости. Папазиан (Papazian (8)) представил концепцию и определение динамического модуля и Сид (Seed (9)) ввел концепцию модуля вязкости. В этих двух типах испытаний к образцу прилагается повторяющаяся нагрузка и измеряется деформация. Эти значения измеряются при одноосном сжатии или на образце при косвенном растяжении. Значение модуля вычисляется как соотношение нагрузки к обратимой деформации (упругость). Основная разница между модулем упругости и динамическим модулем заключается в том, что при измерении динамического модуля, измеряются упругость и упругая деформация. Другая разница в том, что при измерении динамического модуля нагрузка подается синусоидальными импульсами, тогда как при измерении модуля упругости нагрузка подается прямоугольными импульсами. Расчет нагрузки и деформации при измерении модуля упругости обсуждаются в разделе косвенного растяжения.
Третье испытание для измерения жесткости использует балку, которая подвергается повторному сгибанию, чтобы измерить модуль жесткости. Модуль изгибной жесткости вычисляется от центральной точки изгиба при приложенной нагрузке. Этот метод используется для вычисления жесткости при усталостности от изгиба.
Большинство современных измерений жесткости получают, используя версию повторной нагрузки в испытании косвенного растяжения (тест на раскалывание). Обычно этот тест выполняется в диапазоне температур, и тогда можно показать взаимосвязь между модулем упругости и температурой на участке покрытия.
Модуль упругости (Косвенное растяжение при повторяющейся нагрузке) (М r). Из-за его простоты и легкости применения к образцам полотна, Мr стал популярным среди многих лабораторий. Это самый распространенный метод измерения модуля жесткости для горячих асфальтобетонных смесей. Для измерения Мr используется в некоторой степени похожий комплект испытательного оборудования как и для испытания на косвенное растяжение. Главная разница в способности испытательного оборудования применять повторяющуюся нагрузку. Процедура проведения этого испытания описывается в ASTM D4123, и обычно данные наносятся на диаграмму как показано в Рис 5-2. Уравнения для вычисления прочности на растяжение и деформации при разрыве, в испытании косвенного растяжения, можно также использовать для вычисления нагрузки и деформации, в испытании на определение модуля упругости. Приложенная нагрузка вычисляется также как и при вычислении прочность на растяжение; однако, при измерении модуля упругости, образец не нагружается до потери эксплуатационной пригодности. Для определения модуля упругости, обычно образец нагружается до уровня нагрузки, между 5 и 20% от прочности при косвенном растяжении. Поэтому, перед выполнением испытаний по определению модуля упругости, необходимо измерить или оценить прочность на растяжение. Обычно нагрузка применяется в течении 0,1 секунды с перерывом (нет нагрузки) в 0,9 секунды. Таким образом, образец асфальтобетонной смеси получает один цикл нагрузки в секунду. Также используются другие комбинации времени нагрузки и перерыва.
Уравнение, которое выведено для оценки коэффициента Пуассона немного отличается для 4-х дюймовых и 6-ти дюймовых образцов. Далее приводятся два уравнения.
m=3,59Н/ V – 0,27 для 4-х дюймовых (101,6мм) образцов
m=4,09Н/ V – 0,27 для 6-ти дюймовых(152,4мм) образцов
Рис 5-2. Соотношение Нагрузки и деформация ко времени
где,
m – коэффициента Пуассона;
Н – горизонтальная деформация, в дюймах;
V – вертикальная деформация, в дюймах.
Как уже говорилось ранее, обычно предполагается, что коэффициент Пуассона должен быть 0.35, поэтому он не рассчитывается вышеприведенным уравнением. Однако коэффициент Пуассона варьируется с изменением температуры. Используются типичные значения 0.25 для температуры 5°С и 0.40 для 40°С.
Уравнение, получаемое для вычисления Модуля упругости одинаково для 4-х дюймовых(101.6мм) и для 6-ти дюймовых(152.4мм) образцов.
Уравнение:
Mr= P/ Ht (0.27 + m)
где:
Mr = модуль упругости;
P = приложенная нагрузка, фунты;
H = горизонтальная деформация, дюймы
T = толщина образца, дюймы
m = коэффициент Пуассона
Предположив, что коэффициент Пуассона равен 0.35, данное уравнение может быть далее сведено к:
Mr=0.62Р/ Ht
Испытание на модуль упругости становится установившейся практикой среди многих лабораторий потому, что делается упор на измерении основных технических параметров. Однако на сегодняшний день не обнаружено хорошей взаимосвязи между Mr и колееобразованием. Но при низких температурах Mr так или иначе соотносится с растрескиванием. Было обнаружено, что более жесткие смеси при низких температурах начинают проявлять признаки растрескивания раньше, чем более пластичные смеси.
Пример 5-1. Предположим что повторяющаяся нагрузка, равная 100 фунтов (444N) применяется к образцу горячей асфальтобетонной смеси. Цилиндрические образцы высотой в 63.5 мм. Горизонтальная деформация составила 0.00015 дюймов (3.8 микрон). Определите Модуль упругости.
Помните, что
Mr = 0.62Р/Ht
Заменяем,
Mr = 0.62(100)/ 0.00015(2.5)
Решение,
Mr = 165000 psi (1138.5 МПа)
Определения модуля жесткости с помощью косвенных методов. Другой метод определения модуля жесткости битумного вяжущего и горячих асфальтобетонных смесей, был разработан Ван дер Поэлом (Van der Poel) и представлен в форме номограммы. Процедура была описана в многочисленных ссылках, а также в Главе 2. Ссылка 11 содержит полное описание, включая модификации разработанные Хекелом (Heukelom) и МакЛеодом (McLeod). Он быстр и прост в применении. Используется значение проникновения и точки размягчения, для получения жесткости битумного вяжущего при желаемом времени и температуре. Затем вязкость битумного вяжущего используется для вычисления жесткости смеси. Так как эти корреляции включают в себя эмпирические свойства, полученное значение жесткости смеси подходит в лучшем случае только для аппроксимации.
Динамический модуль упругости. Динамический модуль, который иногда называют комплексным модулем, определяется измерением деформации при применении синусоидальных вертикальных нагрузок к цилиндрическим образцам. Процедура испытания для измерения динамического модуля содержится в ASTM D3497. Соотношение высоты к диаметру образца должно быть по крайней мере 2: 1, чтобы уменьшить эффект трения сверху и снизу образца. Когда используется уменьшающий трение материал, соотношение высоты к диаметру равняется 1.0,. Чтобы уменьшить конечное воздействие, он помещается между образцом и нагрузочными пластинами.
Диаметр образца должен быть, по крайней мере, в 2 раза больше размера заполнителя. Наиболее часто используются следующие размеры образцов:
101.6 х 203.2 мм и 152.4 х 304.8 мм.
Применяемая нагрузка обычно варьируется до 35psi (241.5КПа) и обычно определяется как процент от максимальной прочности смеси. Обычно образцы испытывают при 3-х различных температурах и 3-х различных частотах нагрузки. Образцы испытываются при стандартных температурах 5, 25 и 40°С и стандартных частотах применения нагрузки 1, 4 и 16 Гц.
Давление, примененное к образцу, определяется делением примененной нагрузки на площадь поперечного сечения. Деформация измеряется, прикрепив тензометр на противоположных сторонах образца и усредняя деформацию, измеренную двумя датчиками. Также она вычисляется из вертикальной деформации, измеряемой с помощью датчика смещения с линейной характеристикой. На Рис.5-3 показано типичное испытательное оборудование для определения динамического модуля. На Рис5-4 показано типичное нанесение данных на график. Данные показывают, что к образцу применялась повторная нагрузка (постоянной продолжительности и величины) и была измерена полученная деформация.
Рис 5-3 Типичное испытательное оборудование для определения динамического модуля
Динамический модуль вычисляется делением повторяющейся нагрузки на повторяющуюся деформацию.
Е = s /e
где
Е = динамический модуль;
s = примененная нагрузка;
e = измеренная вертикальная деформация.
Используя измерительное оборудование можно также определить коэффициент Пуассона, измерив горизонтальную деформацию во время испытаний. Однако, обычно попытки измерить коэффициент Пуассона горячих асфальтобетонных смесей не были успешными.
Главная цель измерения динамического модуля это определение взаимосвязи нагрузки и деформации в дорожном покрытии, при примененной нагрузке. Так как динамический модуль это не измерение прочности, асфальтобетонная смесь с высоким динамическим модулем не обязательно будет более прочной. Более высокое значение динамического модуля показывает, что при применении данной нагрузки в смеси меньшее натяжение.
Из-за продолжительности во времени, сложного оборудования для проведения испытания и большой высоты испытываемого образца, это испытание используется редко. Это испытание не проводится для стержней изъятых из дорожного покрытия, так как обычно в дорожном покрытии слой толщиной не более двух дюймов, а образец должен быть не меньше 8 дюймов (203,2 мм) в высоту и 4 дюйма в диаметре. В некоторых случаях образцы ставили друг на друга, чтобы обеспечить необходимую высоту в 8 дюймов (203,2 мм), на такой подход весьма сомнительный.
Рис 5-4 Зафиксированный след при испытании по определению динамического модуля
Испытание на изгиб. Испытание на многократный изгиб проводится для определения усталостных характеристик асфальтобетонной смеси, что позволяет оценить время сохранения эксплуатационной пригодности, перед появлением трещин (12, 13, 14). В трех точках к образцу в виде балки применяется многократная гаверсинусная нагрузка. Интенсивность нагрузки непостоянна, но обычно 1 или 2 цикла в секунду. Это производит постоянный изгибающий момент в центральной части балки. Часто нагрузка применяется в противоположных направлениях, заставляя балку возвращаться в изначальное положение во время перерыва, чтобы поддерживать нулевое положение. Прогиб от нагрузки измеряется от центра балки. Схематическое изображение испытательного аппарата приводится в Рис. 5-5.
Рис 5-5. Аппарат многократного изгиба для определения жесткостных и усталостных характеристик (1)
После примерно 200 применений нагрузки вычисляются нагрузка и деформация на крайних волокнах, а также модуль жесткости, используя основное соотношение для нагрузки и деформации в балках. Упрощение этой информации предоставляет следующие уравнения:
s = 3аР/ bh2
e=12 hd/3 L2 – 4 a2
E= Pa(3 L2 – 4 a2)/48 Id
где
s = растягивающее напряжение в крайних волокнах, psi;
e = деформация растяжения в крайних волокнах, в дюймах;
Es = модуль изгибной жесткости, psi;
Р = полная динамическая нагрузка с ½ Р применяемой в трех точках, psi;
b = ширина образца, дюймы;
h = высота образца, дюймы;
L = Длина участка реакции, дюймы
I = момент инерции образца, квадратные дюймы;
D = динамический прогиб в центре балки, дюймы.
Это испытание можно проводить в режиме постоянной нагрузки и деформации. В режиме применения постоянного давления, оно (Р) применяется, пока не произойдет отказ смеси. В некоторых случаях, под отказом подразумевается разрушение образца. Для небольших нагрузок время выполнения этого испытания может быть несколько часов, несколько дней или даже несколько недель. Данные испытаний до отказа образца нанесены на график против данных о применяемом давлении (Рис5-6) В режиме постоянной нагрузки, материалы с более высоким значением жесткости показывают лучшие эксплуатационные характеристики, чем материалы с более низкой жесткостью. Часто для режима постоянной нагрузки составляется диаграмма соотношения начальной нагрузки к циклам нагрузки до отказа образца.
Рис 5-6 Типичный график данных усталостности, при использовании метода постоянной нагрузки
В режиме постоянной деформации, поддерживается постоянное отклонение и с увеличением циклов, примененная нагрузка уменьшается. В испытании с постоянной деформацией, отказ смеси трудно определить, так как обычно образец не разрушается. Обычно отказом считается момент, когда примененная нагрузка достигает некоторого заранее установленного процента от изначально примененной нагрузки. Например, типичные значения, которые часто выбирают для обозначения отказа, это 25 и 50% от изначальной нагрузки. Обычно данные, полученные в этом испытании, наносят на две диаграммы. Первый график, это данные вызванной деформации к количеству циклов до отказа образца. Второй, данные начальной нагрузки к количеству циклов до отказа. Материалы, которые более эластичные (с низкой жесткостью) показывают лучшие эксплуатационные характеристики при испытании с постоянной деформацией, когда данные вызванной деформации наносятся на диаграмму против циклов до отказа образца.
Пример 5-2. Проводится испытание балки на усталость при изгибе. Реакции 12 дюймов (305мм) в сторону, с полной нагрузкой в 100 фунтов (444N) приложенной в тройной точке (50 фунтов (222 N) в каждой 1/3 точки). После 1000 применений нагрузки, измеренный прогиб составил 0,0011 дюйма (0,28 мм) на одно приложение нагрузки. Определите напряжение при изгибе, деформацию изгиба и модуль жесткости. Поперечное сечение балки составляет 3 дюйма на 3 дюйма (76.2мм х 76,2мм).
Как уже описывалось, напряжение при изгибе определяется по формуле:
s = 3аР/ bh2
поэтому
s = 3(4)(100)/3(3)2
Решение уравнения: напряжение при изгибе для условий, указанных в этом примере:
s = 44,4 ЮЮЮ (306,4 КПа)
Деформацию изгиба определяется по следующему уравнению:
e=12 hd/3 L2 – 4 a2
поэтому
e=12(3)(0,0011)/3(12)2 – 4(4)2
e=108 х 10-6 дюймов (мм/мм)
Теперь можем определить жесткость при изгибе, разделив напряжение на деформацию, и включаем в следующее уравнение:
Es= Pa(3 L2 – 4 a2)/48 Id
Помните, что момент инерции (I) для прямоугольного сечения:
I= bh3/12
Решение
I= 3(3)3/12
Момент инерции равен
I= 6,75 кв.дюймов (281,0 кв.см)
Теперь решаем уравнения для определения модуля жесткости.
Es=100(4) (3(12)2 – 4(4)2)/48(6,75)(0,0011)
Модуль жесткости равен:
Es=413000
Также можно показать, что модуль жесткости равен напряжению, разделенному на деформацию. Для этого примера:
Es= s/ e = 44,4/108х10-6
Решение
Es=411000 psi (2835,9МПа)
Разница между результатами двух вычислений обусловлена ошибкой округления.
Испытание на усталость при изгибе занимает значительное время, поэтому необходимо испытывать примерно 10 образцов, чтобы получить достаточно данных для создания необходимых диаграмм (13). Время для проведения достаточного количества испытаний для создания одной диаграммы, наиболее вероятно превысит две недели. Вдобавок необходимое оборудование очень сложное и дорогое. Вследствие чего, это испытание проводится только в исследовательских целях, а не для определения параметров смесей во время их изготовления или при контроле качества.
Опыт показывает, что толстое асфальтобетонное дорожное покрытие (толще 5 дюймов (130мм)) в основном работает близко к режиму нагрузки постоянной нагрузки, тогда как тонкий слой асфальтобетонной дорожной одежды работает близко к режиму постоянной деформации. Однако на практике, жесткость смеси не зависит от толщины дорожного покрытия.
В режиме постоянного давления, основное уравнение для нанесения на диаграмму данных о примененной нагрузке к количеству циклов до отказа, будет выглядеть следующим образом:
Nf = K1(1/ s) n1
где
Nf = количество циклов до отказа;
s = напряжение на изгибе в наиболее удаленном волокне, psi;
K1, n2 = коэффициент регрессии
Подобное уравнение получается при сравнении данных по циклам до отказа, с данными по деформации.
Nf = K2 (1/ e) n2
где
Nf = количество циклов до отказа;
e = деформация при изгибе в наибо
|
|
Типы оградительных сооружений в морском порту: По расположению оградительных сооружений в плане различают волноломы, обе оконечности...
Папиллярные узоры пальцев рук - маркер спортивных способностей: дерматоглифические признаки формируются на 3-5 месяце беременности, не изменяются в течение жизни...
Организация стока поверхностных вод: Наибольшее количество влаги на земном шаре испаряется с поверхности морей и океанов (88‰)...
Общие условия выбора системы дренажа: Система дренажа выбирается в зависимости от характера защищаемого...
© cyberpedia.su 2017-2024 - Не является автором материалов. Исключительное право сохранено за автором текста.
Если вы не хотите, чтобы данный материал был у нас на сайте, перейдите по ссылке: Нарушение авторских прав. Мы поможем в написании вашей работы!