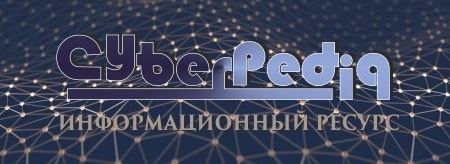
Адаптации растений и животных к жизни в горах: Большое значение для жизни организмов в горах имеют степень расчленения, крутизна и экспозиционные различия склонов...
Эмиссия газов от очистных сооружений канализации: В последние годы внимание мирового сообщества сосредоточено на экологических проблемах...
Топ:
Характеристика АТП и сварочно-жестяницкого участка: Транспорт в настоящее время является одной из важнейших отраслей народного...
Определение места расположения распределительного центра: Фирма реализует продукцию на рынках сбыта и имеет постоянных поставщиков в разных регионах. Увеличение объема продаж...
Интересное:
Что нужно делать при лейкемии: Прежде всего, необходимо выяснить, не страдаете ли вы каким-либо душевным недугом...
Уполаживание и террасирование склонов: Если глубина оврага более 5 м необходимо устройство берм. Варианты использования оврагов для градостроительных целей...
Средства для ингаляционного наркоза: Наркоз наступает в результате вдыхания (ингаляции) средств, которое осуществляют или с помощью маски...
Дисциплины:
![]() |
![]() |
5.00
из
|
Заказать работу |
|
|
Рисунок 3-11. Линии максимальной плотности на диаграмме ФАДУ США с показателем степени 0,45
Обычно в технических условиях для обозначения смеси используют номинальный максимальный размер частиц заполнителя. Например, в стандарте ASTM D3515 требуется смесь, имеющая номинальный максимальный размер 1 дюйм (25,4 мм), чтобы 100 % материала проходило через сито 1,5 дюйма (38 мм) и 90—100 % проходило через сито 1 дюйм (25,4 мм).
При разработке системы Superpave были использованы следующие определения размера заполнителя:
Максимальный размер: на один размер сита больше, чем номинальный максимальный размер.
Номинальный максимальный размер на один размер сита больше, чем первое сито, на котором остается более 10 %.
Линию максимальной плотности в смеси Superpave получают, соединяя начало координат в левом нижнем углу с максимальным размером частиц заполнителя в правом верхнем углу диаграммы с помощью линии с наклоном степенью 0,45 (16).
С конструктивной точки зрения максимальный размер заполнителя обычно ограничен примерно половиной толщины слоя. Недавно было увеличено использование больших частиц в смеси, чтобы минимизировать потенциальное колееобразование АГС. Введение боллее крупных зерен щебня увеличивает объемную концентрацию заполнителя. Этот фактор вносит вклад в снижение как содержания битума в составе смеси, так и цены смеси. Эти смеси из крупных зерен щебня более устойчивы к колееобразованию, чем смеси из заполнителей с маленькими размерами. Однако, использование заполнителя с максимальным размером больше 1 дюйма (25.4 mm) часто дает грубые смеси, которые имеют тенденцию к расслоению при укладке. Поэтому, если смеси с заполнителями с максимально большим размером частиц, особое внимание следует обратить на состав смеси, толщину подложки,, обработку материала, смешивание и методику нанесения дорожного покрытия.
|
Типичные технические условия на полосы и допуски. Технические требования к гранулометрическому составу заполнителя для АГС были разработаны на основе накопленного опыта полевых экспериментов. Во многих случаях они были установлены путем проб и ошибок и отражают местные условия. Большинство технических условий на АГС требуют, чтобы гранулометрический состав заполнителя был хорошо отсортирован и давал плотную смесь, при этом средние части кривых были приблизительно параллельны кривым максимальной плотности. Таблица 3-7 содержит предельные гранулометрические составы, рекомендуемые в ASTM D3515, а в таблице 3—8 даны допуски. На практике большинство технических условий не позволяют сильных колебаний гранулометрического состава, как это указано в таблицах 3-7 и 3-8. Полоса гранулометрического состава по ASTM D3515 для сита 3/4-дюйма (19 мм) с номинальным максимальным размером смеси нанесена на диаграмме ФДА, приведенной на рисунке 3—12. Для большей части кривой максимальной плотности для размера частиц заполнителя 3/4-дюйма (19 мм) максимальный размер заполнителя находится в этих пределах. Некоторые указания на развитие полос гранулометрического состава и потенциальные проблемные области даны на рисунке 3-13 (17).
Другая проблема, часто вызываемая бедным гранулометрическим составом заполнителя (отсутствием необходимого количества щебня) - образование подвижных смесей. Эти смеси не могут быть уплотнены обычным образом из-за того, что они медленно набирают необходимую стабильность в противостоянии нагрузкам, создаваемым уплотняющим оборудованием. Рисунок 3-14 иллюстрирует типичную картину гранулометрического состава таких смесей. Наиболее заметны максимум на кривой вблизи сита № 40 и плоский наклон кривой между ситами № 40 и № 8. Наиболее вероятно, это вызвано тем, что смеси заполнителей, имеющие такую форму кривой, чрезмерно используют природные пески с неблагоприятным гранулометрическим составом. Имеются и другие причины, приводящие к хрупким смесям, которые будут обсуждены в главе 6.
|
Ситовой анализ (ASTM C136 и C117). Гранулометрический состав заполнителя определяют ситовым анализом. Стандартная методика сухого ситового анализа дана в ASTM C136, а для мокрого - ситовой анализ для определения количества материала, прошедшего через сито № 200 (75 мкм), методика дана в ASTM C117. Мокрый ситовой анализ более точно определяет истинный гранулометрический состав, но сухая методика быстрее и часто используется для оценки действительного гранулометрического состава. Если используется сухая методика, измеренное количества материала, прошедшего через сито № 200 (75 мкм) наиболее вероятно значительно ниже, чем истинное количество в смеси заполнителей. Для чистого заполнителя сухой ситовой анализ может быть достаточно точным, поскольку количество материала, проходящего через сито № 200 (75 мкм), мало.
Пример 3—3. Предположим, что смесь заполнителей была разделена на два образца. Определим процент, проходящий через каждый из размеров сита при сухом и мокром методе определения гранулометрического состава. Сухой метод было проведено на первом образце, вес которого был 2012 г (Таблица 3-9). Мокрое определение было выполнено на втором образце, вес которого 2074 г. Веса и расчеты для мокрого определения показаны в таблице 3-10.
Шаги сухого ситового анализа включают: разделение образца для корректировки размера, определение общего сухого веса, просеивание через набор сит и перемешивание, взвешивание материала, собранного на каждом из сит, определение процента, остающегося на каждом сите, и определение процента, проходящего через каждое сито. Когда проводят мокрый ситовой анализ, чтобы получить гранулометрический состав мокрого образца, материал промывают через сито № 200 (75 мкм) для удаления пыли. Затем материал сушат, взвешивают, насыпают на следующее сито, вибрируют, и определяют количество, оставшееся на каждом сите.
Рисунок 3-12. Технические требования ASTM D 3515 для заполнителя номинального максимального размера 3/4-дюйма, нанесенный на график степенной зависимости степени 0,45
|
Таблица 3-7. Технические требования ASTM D 3515 для плотных смесей
Размер сита | Плотные смеси | ||||||||
Обозначение смеси и номинальный максимальный размер заполнителя | |||||||||
2 дюйма (50 мм) | 1 1/2 дюйма (37,5 мм) | 1 дюйм (25,0 мм) | ¾ дюйма (19,0 мм) | 1/2 дюйма (12,5 мм) | 3/8 дюйма (9,5 мм) | № 4 (4,75 мм) (песчаный асфальт) | № 8 (2,16 мм) | № 16 (1.18 мм) (битумный раствор) | |
Общий гранулометрический состав заполнителя (rрупные + мелкие + наполнитель по требованию) количество материала более мелкого, чем каждое из лабораторных сит (квадратные отверстия), вес. % | |||||||||
2 1/2 дюйма (63 мм) | 100 | - | - | - | - | - | - | - | - |
2 дюйма (5O мм) | 90 до 100 | 100 | - | - | - | - | - | - | - |
1 1/2 дюйма (37,5 мм) | - | 90 до 100 | 100 | - | - | - | - | - | - |
1 дюйм (25,0 мм) | 60 до 80 | - | 90 до 100 | 100 | - | - | - | - | - |
3/4дюйма (19,0 мм) | - | 56 до 80 | - | 90 до 100 | 100 | - | - | - | - |
1/2 дюйма (12,5 мм) | 35 до 65 | - | 56 до 80 | - | 90 до 100 | 100 | - | - | - |
3/8 дюйма (9,5 мм) | - | - | - | 56 до 80 | - | 90 до 100 | 100 | - | - |
№ 4 (4,75 мм) | 17 до 47 | 23 до 53 | 29 до 59 | 35 до 65 | 44 до 74 | 55 до 85 | 80 до 100 | - | 100 |
№ 8 (2,36 мм) | 10 до 36 | 15 до 41 | 19 до 45 | 23 до 49 | 28 до 58 | 32 до 67 | 65 до 100 | - | 95 до 100 |
№ 16 (1,18 мм) | - | - | - | - | - | - | 40 до 80 | - | 85 до 100 |
№ 30 (600 мкм) | - | - | - | - | - | - | 25 до 65 | - | 70 до 95 |
№ 50 (300 мкм ) | 3 до 15 | 4 до 16 | 5 до 17 | 5 до 19 | 5 до 21 | 7 до 23 | 7 до 40 | - | 45 до 75 |
№ 100 (150 мкм ) | - | - | - | - | - | - | 3 до 20 | - | 20 до 40 |
№ 200 (75 мкм) | 0 до 5 | 0 до 6 | lдо7 | 2 до 8 | 2 до 10 | 2 до 10 | 2 до 10 | - | 9 до 20 |
Рисунок 3-13. Пределы гранулометрического состава для АГС и ожидаемые проблемы при выходе за эти пределы (17)
Смешивание заполнителей для выполнения технических требований. По разным причинам, главным образом, по причинам, связанным с достижением максимальной плотности и желаемых характеристик пористости, от заполнителей для АГС обычно требуются определенные предельные значения гранулометрического состава. Поскольку невероятно, чтобы один природный материал или материал из одного карьера удовлетворяли этим требованиям, для выполнения предельных требований обычно смешивают два или более заполнителей различного гранулометрического состава. Заполнители разделяют на размерные фракции также и для улучшения характеристик управляемости. Смешивание крупных и мелких заполнителей в одном отвале приводит к сегрегации, следовательно, заполнители следует разделять по размерам, например, 3/4 дюйма-3/8 дюйма (19 мм-9,5 мм), 3/8 дюйма-№ 4 (9,5 мм-4,75 мм), и минус 4 (4,75 мм) до транспортировки и складирования. Другая причина для смешивания заполнителей та, что зачастую объединение встречающихся в природе и обработанных материалов экономически выгоднее для удовлетворения технических требований, чем использование всех обрабатываемых материалов.
|
Таблица 3-8. ASTM D 3515 Допуски для гранулометрического состава
Размер сита | Допуски, % |
1/2 дюйма (12,5 мм) и более | 8 |
3/8 дюйма (9,5 мм) | ±7 |
№ 4 (4,75 мм) | ±7 |
№ 8 (2,36 мм) | ±6 |
№ 16 (1.18 мм) | ±6 |
№ 30 (600 мкм ) | ±5 |
№ 50 (300 мкм) | ±5 |
№ 200 (75 мкм) | ±3 |
Содержание битума, весовые % от общего веса | ±0.5 |
Таблица 3-9. Расчет гранулометрического состава сухого заполнителя
Размер сита | Вес остатка | Остающийся процент | Проходящий процент |
3/4 дюйма | 0,0 | 0,0 | 100,0 |
1/2 дюйма | 86,5 | 4,3 | 95,7 |
3/8 дюйма | 154,9 | 7,7 | 88,0 |
№ 4 | 253,5 | 12,6 | 75,4 |
№ 8 | 269,6 | 13,4 | 62,0 |
№ 16 | 344,1 | 17,1 | 44,9 |
№ 30 | 380,3 | 18,9 | 26,0 |
№ 50 | 323,9 | 16,1 | 9,9 |
№ 100 | 158,9 | 7,9 | 2,0 |
№ 200 | 22,1 | 1,1 | 0,9 |
В поддоне | 18,2 | 0,9 | |
Суммарно | 2012,0 | 100,0 |
Рисунок 3-14. Характеристики хрупкой смеси на степенном графике гранулометрического состава степени 0,45
Таблица 3-10. Расчет гранулометрического состава промытого заполнителя
Размер сита | Вес остатка | Остающийся процент | Проходящий процент |
3/4 дюйма | 0 | 0 | 100 |
1/2 дюйма | 89,2 | 4,3 | 95,7 |
3/8 дюйма | 159,7 | 7,7 | 88,0 |
№ 4 | 238,5 | 11,5 | 76,5 |
№ 8 | 311,1 | 15,0 | 61,5 |
№ 16 | 300,7 | 14,5 | 47,0 |
№ 30 | 398,2 | 19,2 | 27,8 |
№ 50 | 327,7 | 15,8 | 12,0 |
№ 100 | 149,3 | 7,2 | 4,8 |
№ 200 | 16,6 | 0,8 | 4,0 |
В поддоне | 24,9 | 1,2 | |
Смывается | 58,1 | 2,8 | |
Суммарно | 2074,0 | 100,0 |
Характер распределения частиц по размеру может быть рассмотрен графически (a) суммарного процента проходящего через сито в полулогарифмическом масштабе, или (b) суммарного процента проходящего через сито в зависимости от размера сита в степени 0,45. Обычно исполнители используют для выбора смеси заполнителей оба метода.
Если характеристика выражена в терминах общего процента, проходящего через сито, она может быть нанесена на график в виде полосы или огибающей (Рисунок 3-15). Методика преобразования характеристики, выраженной в виде проходящего/остающегося материала, в приближенно эквивалентную ей характеристику общего процента прошедшего материала была описана Дальхаузом (18). Это преобразование позволяет построить диаграмму характеристики проходящее/остающееся в зависимости от общего процента проходящего, делая возможным визуальные наблюдения и сравнение различных характеристик. Однако, в этой главе, если иное не оговорено, все распределения и характеристики выражены в виде общего процента проходящего через определенное сито материала.
|
Было разработано большое число методов смешивания (методик определения относительных пропорций различных заполнителей, чтобы получить желаемый гранулометрический состав) после принятия кривых максимальной плотности по Фуллеру и Томпсону (15). Пригодность этих методов зависит от типов характеристик и числа участвующих заполнителей, опыта исполнителей и того, на что делается основной упор при смешивании (на близость к желаемому гранулометрическому составу или на экономику).
Независимо от числа заполнителей и выбранной методики смешивания, основная формула, отображающая состав имеет вид
p = Aa + Bb + Cc+... (9)
где,
p = процент материала, проходящий через данное сито для смеси заполнителей A, B, C,
A, B, C,... = процент материала, проходящий через данное сито для каждого из заполнителей A, B, C,
a, b, c,... = доли заполнителейproportions (десятичные дроби) A, B, C, используемых в смеси, a + b + c... = 1.00
Желательно, независимо от того, какой из методов используется, перед тем, как приступить к смешиванию, сначала графически нанести на диаграмму гранулометрических составов гранулометрический состав заполнителей, подлежащих смешиванию, и предельные технические требования. Из этих графиков, до любых расчетов может быть принято решение по следующим вопросам: (a) могут ли быть выполнены предельные требования в смеси, использующей доступные заполнители, (b) каков критический размер сита (c) выбрать приблизительные пробные пропорции. Эти решения могут быть сделаны на основе следующих простых фактов и гранулометрических составов, приведенных на рисунке 3-15:
Рисунок 3—15. Анализ гранулометрического состава заполнителя с помощью задания зоны технических требований
Кривые гранулометрического состава для всех возможных комбинаций заполнителей А и В ложатся между кривыми А и В. Независимо от выбранного метода невозможно смешать заполнители С и В так, чтобы удовлетворить техническим требованиям.
1. Если две кривые пересекаются в какой либо точке (B или D), кривые гранулометрического состава при любых возможных комбинациях проходят через эту точку.
2. Кривая для смеси, содержащей большее содержание заполнителя А, чем заполнителя В, проходит ближе к кривой А и наоборот.
Наиболее обычным способом определения пропорций компонентов для удовлетворения технических требований является метод проб и ошибок. Как это отражено в названии выбирают пробную смесь (полагаясь на опыт, графики индивидуальных кривых распределения гранулометрического состава и предельные технические требования) и выполняют расчеты по уравнению 9 для определения процента материала, проходящего через каждое сито для данной смеси. Распределение, рассчитанное для данной пробы, сравнивается с требованиями технических условий. Для второй пробной смеси делаются регулировки состава, расчеты повторяют для критических размеров сит, пока не будет получена удовлетворительная или оптимальная смесь. Этот метод приводит к определенному количеству умозаключений, математических расчетов и опытов и является наиболее широко используемым методом с наиболее простой процедурой определения удовлетворительного состава смеси.
Метод проб и ошибок включает следующие шаги:
1. Выбор критических сит для заполнителей в смеси;
2. Определение начальных установок пропорций a, b, c, и т.д., которые удовлетворяют требованиям технических условий для критических сит;
3. Сравнение рассчитанной смеси, использующей пропорции, определенные для всех сит, указанных в технических условиях;
4. Корректировка состава, чтобы обеспечить удовлетворение предельных значений технических условий для всех сит.
Пример 3-4. Методом проб и ошибок определить смесь из двух заполнителей, показанную в Таблице 3-11, которая бы удовлетворяла требованиям технических условий.
Изучение гранулометрического состава показывает, что имеется возможность найти смесь, которая лежит в пределах требований технических условий, возможно, что это смесь 50 на 50, потому что равны относительные расстояния кривых до центра полосы (желаемое распределение). Первую пробную смесь разумнее можно определить, если выбраны определенные критические размеры сит. Проверяя гранулометрический состав, видим, что весь материал остается на сите 3/8—дюйма или 9,5 мм (желательно 100—80 = 20) может состоять из заполнителя A, а весь материал более мелкий, чем сито № 30 (0,6 мм) может состоять из заполнителя В. Что касается заполнителя А, из-за того, что на сите 3/8-дюйма (9,5 мм) остается 100-59 = 41 % заполнителя А, для того, чтобы на этом сите осталось 20 % А (среднее значение технических условий), нужно взять A = 20/41 = 0,49; тогда процент В будет 1-0,49 = 0,51. Что касается заполнителя B, через сито № 30 (0,6 мм) проходит 51 %, следовательно, для получения желаемых 24 % требуется взять заполнителя В = 24/51 = 0.47; процент заполнителя А для этой смеси должен быть 1-0,47 = 0,53. Следовательно, анализ по двум критическим размерам сит дает очень похожие результаты.
Таблица 3-11. Смешивание двух заполнителей
Размер сита
Оценка по одному из критических размеров сита показывает, что процент заполнителя А должен быть 49 % а по другому критическому размеру – заполнителя А следует взять 53 %. Для первой пробы возьмем 50 % заполнителя А и 50 % заполнителя В.
Форма, которой удобно пользоваться, показана в Таблице 3-11. Умножаем на 0,50 проценты, проходящие через каждое сито для заполнителей А и В. Складывая результаты получим нужное распределение для смеси. Результирующее распределение сравнивается с желаемым, оказывается, что смесь, состоящая из 50 % каждого из заполнителей, очень близка к желаемому распределению. Следовательно в этом примере пропорции между заполнителями А и В должны быть 50 % и 50 %. Содержание этих двух заполнителей можно слегка изменить не нанося ущерба свойствам смеси. Например, если заполнитель А стоит дороже заполнителя В, можно немного увеличить содержание В и уменьшить содержание А, тем самым снизив общую стоимость смеси. Требования технических условий будут выполнены, но с помощью менее дорогой смеси.
Пример 3-5. Дано распределение заполнителей A, B, и C, определить требуемое процентное соотношение каждого заполнителя. Чтобы результирующая смесь удовлетворяла требованиям технических условий (см. таблицу 3—12).
Критические сита в этом случае будут № 4 (4,75 мм) и № 30 (0,6 мм). Сито № 200 (75 мкм) также является критическим, так как 88 % заполнителя С проходит через это сито и только 11 % удовлетворяет требованиям технических условий. Желательные 52 % материала больше, чем должно проходить через сито № 4 (4,75 мм). Следовательно, в первой пробе процент заполнителя А должен быть:
Процент A =2±= 64 %
Теперь посмотрим на сито № 30 (0,6 мм), очевидно, что 75 % материала это больше, чем проходит через сито № 30 (0,6 мм) заполнителей A и B. Так как 75 % общее желательное количество, остающееся на сите № 30 (0,6 мм) и 0,64(95) есть доля, поставляемая заполнителем А.
Процент B= 75-0,64 (95) = 75-61 = 14
На основании этих расчетов, оказывается, что наилучшая первоначальная оценка даст 64 % заполнителя A, 14 % заполнителя B, и 22 % заполнителя C. Очевидно, однако, что использование 22 % заполнителя C даст слишком много материала, прошедшего через сито № 200 (75 мкм). Процент заполнителя C вероятно должен быть не выше 8 %, так как только один этот заполнитель дает приблизительно 7 % материала проходящего через сито № 200 (75 мкм). На основании этого анализа по первичной оценке должно быть: 71 % заполнителя А, 21 % заполнителя В, и 8 % заполнителя С. Расчеты приведены в таблице 3—13.
Таблица 3-12. Смешивание трех заполнителей
Размер сита
Заполнитель
Технические требования
Среднее значение технических требований
Предполагаемые проценты 71 для А, 21 для B, и 8 для C дают смесь, удовлетворяющую техническим требованиям. Однако, смесь можно улучшить, слегка сместив ее к желательному гранулометрическому составу. Для улучшения смеси используем на 2 % меньше заполнителя С и на 5 % меньше заполнителя А, следовательно, заполнителя В следует взять на 7 % больше. На каждый 1 %, на который изменяются оба заполнителя, конечная смесь изменится на разность между процентами, проходящими через сито данного размера для двух заполнителей, кратное 1 %. Например, увеличение заполнителя B на 5 % и уменьшение заполнителя A на 5 % приведет к изменению (0,81) 5 или на 4 % 4.0 на сите № 4.
После выполнения расчетов (Таблица 3—13) можно видеть, что количества каждого из заполнителей составляют: 66 % - А, 28 % - В и 6 % - С.
Расчеты, которые требуются для метода проб и ошибок и показаны в приведенном примере, были выполнены вручную, чтобы показать шаги расчета. Однако успешное испытание может быть легко и просто выполнено с помощью персонального компьютера и электронных таблиц. По желанию, гранулометрический состав смеси и технические требования могут быть нанесены на график и проверены с использованием графических возможностей обычного персонального компьютера.
Таблица 3—13. Расчеты для смешения трех заполнителей
Заполнитель
Процент
Размер сита
Имеется несколько графических методов, которые могут быть использованы для определения процентного содержания каждого из заполнителей в смеси. Эти методы обычно не используются, потому что метод проб и ошибок в большинстве случаев быстрее и проще. Эти методы особенно трудны для использования, если смешивают более двух заполнителей, что нормально для случая АГС. Дополнительная информация о графических методах приведена в обзорах (6,19,21,22).
Были разработаны компьютерные программы для определения оптимальных смесей для заданного числа заполнителей. Ни одна из этих программ не была достаточно успешной, так как опытный инженер может определить желаемые пропорции методом проб и ошибок и одновременно может ввести данные в компьютер. Другая проблема компьютерного метода состоит в том, что трудно количественно описать оптимальную смесь. Например, значимость 2 % отклонения от желательного гранулометрического состава не так критична для сита № 4 (4,75 мм) как для сита № 200 (75 мкм). Когда оценивают важность отклонений от желаемой смеси, должны быть рассмотрены многие факторы.
Должны использоваться некоторые технические оценки и не может быть разработана одна программа, которая учитывала бы все факторы, которые должны быть учтены при смешивании заполнителей. Более подробная информация о компьютерных методах расчета рассмотрена в работах (20, 22, 23). Большинство обычных компьютерных методик при смешивании заполнителей основано на методе проб и ошибок (с использованием технических оценок для наилучшей смеси), нанесении на график технических требований и пробного смешивания. Компьютерные программы могут помочь при учете соображений стоимости (24, 25, 26).
Площадь поверхности
Площадь поверхности - важное свойство, которое может быть рассчитано из гранулометрического состава заполнителя. Площадь поверхности заполнителя важна, потому что она влияет на количество битума, необходимое для покрытия частиц заполнителя. Плотные асфальтобетонные смеси обычно различаются по содержанию желательного количества воздушных пустот воздуха; следовательно, площадь поверхности заполнителя не является решающим фактором. Можно увеличить площадь поверхности и одновременно снизить оптимальное содержание битума. Один из путей, как это сделать, увеличить содержание минерального наполнителя в смеси. Асфальтобетонные смеси с высокой площадью поверхности и низким оптимальным содержанием битума нежелательны, потому что имеют тонкую пленку битума на частицах заполнителя и, вероятно, будут иметь недостаточный срок службы. Дальнейшее обсуждение роли толщины пленки будет проведено главе 4.
Наиболее общий способ, используемый для оценки площади поверхности заполнителя, включает расчеты, сделанные на основании гранулометрического состава заполнителя. Площадь поверхности определяется умножением коэффициента площади поверхности на процент материала, проходящего через сита разных размеров. Эти коэффициенты рассчитываются на основании принятого удельного веса заполнителя и в предположении, что все частицы имеют круглую форму. Площадь поверхности на 1 фунт заполнителя можно определить для каждого из размеров частиц заполнителя.
Коэффициенты площади поверхности для различных размеров сит показаны в таблице 3—14. Площадь поверхности определяется умножением коэффициента на процент, проходящего через каждое сито материала и суммируется для всех размеров сит. В этих расчетах принята за единицу измерения 1 фут2/фунт. Должны использоваться все коэффициенты площади поверхности для всех размеров сит, приведенные в таблице 3-14. Площадь поверхности лишь незначительно влияет на процент материала, проходящего через сита больших размеров, но значительно влияет для сит малых размеров.
Одна из главных причин для оценки площади поверхности, состоит в определении толщины пленки битума. Это оценочная величина, но она позволяет делать сравнения различных смесей.
Таблица 3-14. Коэффициенты площади поверхности
Размер сита | Коэффициенты площади поверхности |
Процент прохождения через максимальный размер сита | 2 |
Процент, проходящий через сито № 4 | 2 |
Процент, проходящий через сито № 8 | 4 |
Процент, проходящий через сито № 16 | 8 |
Процент, проходящий через сито № 30 | 14 |
Процент, проходящий через сито № 50 | 30 |
Процент, проходящий через сито № 100 | 60 |
Процент, проходящий через сито № 200 | 160 |
Пример 3-6. Асфальтобетонная смесь имеет гранулометрический состав заполнителей, показанный ниже. Определить площадь поверхности на 1 фунт заполнителя.
Размер сита | Процент прохождения |
3/4 дюйма | 100 |
1/2 дюйма | 88 |
3/8 дюйма | 72 |
№ 4 | 60 |
№ 8 | 47 |
№ 16 | 35 |
№ 30 | 25 |
№ 50 | 20 |
№ 100 | 10 |
№ 200 | 5 |
Используя коэффициенты площади поверхности и процент проходящего материала на каждом сите показанные выше, площадь поверхности (SA) рассчитывается следующим образом:
SA= 2(100) + 2(0,60) + 4(0,47) + 8(0,35) + 14(0,25) + 30(0,20) + 60(0,10) + 160(0,05)
После упрощений получаем:
SA = 31,38 квадратных футов поверхности на один фунт заполнителя.
Дополнительное обсуждение заполнителей предоставляет «Справочник Заполнителей Национальной Геологической ассоциации» (27).
Литература
1. A Handbook of Crushing, Bulletin 4030, Pennsylvania Crusher Corporation, Broomall, Pennsylvania, 1974.
2. American Society for Testing and Materials, Volume 0402, ASTM C 294 Standard Descriptive Nomenclature of Constituents of Natural Mineral Aggregates, 1989.
3. The Identification of Rock Types. Bureau of Public Roads, 1960.
4. State-of-the-Art: Effect of Water on Bitumen-Aggregate Mixtures. Highway Research Board, Special Report 98, 1968.
5. Cordon, W.A. Properties, Evaluation, and Control of Engineering Materials, McGraw-Hill, N.Y., 1979.
6. McLaughlin, J.E et al. Distribution, Production, and Engineering Characteristics of Aggregates. Highway Engineering Handbook, ed. by K.B. Woods, McGraw-Hill, N.Y., 1960.
7. Mertens, E.W. and J.J. Borgfeldt. Cationic Asphalt Emulsions. Bituminous Materials: Asphalts, Tars, and Pitches, ed. by A.J. Hoiberg, Vol. 2, Part 1, Interscience Publishers, John Wiley & Sons, N.Y., 1965.
8. Petersen, J.C. Chemical Composition of Asphalt as Related to Asphalt Durability: State—of—the-Art. Transportation Research Board, Transportation Research Record 999, 1984.
9. Marek, C.R., H. Herrin, C.L. Kesler, and EJ. Barenberg. Promising Replacements for Conventional Aggregates for Highway Use. Highway Research Board, NCHRP Report 135, 1972.
10. McLeod, N.W. and J.K. Davidson. Particle Index Evaluation of Aggregates for Asphalt Paving Mixtures. Proceedings Association of Asphalt Paving Technologists, Volume 50, 1981.
11. Asphalt Concrete Mix Design and Field Control. FHWA, Technical Advisory T 5040.27, 1988.
12. Kandhal, P.S., M.A. Khatri, and J.B. Motter. Evaluation of Particle Shape and Texture of Mineral Aggregates and Their Blends. Asphalt Paving Technology, Vol. 61, 1992.
13. Brown, E.R. and S.A. Cross. A National Study of Rutting in Asphalt Pavement. Asphalt Paving Technology, Vol. 61, 1992.
14. Lee, D.Y. The Relationship Between Physical and Chemical Properties of Aggregates and Their Asphalt Absorption. Proceedings Association of Asphalt Paving Technologists, Volume 38, 1969.
15. Fuller, W.B. and S.E. Thompson. The Laws of Proportioning Concrete. Journal of Transportation Division, American Society of Civil Engineers, Vol. 59, 1907.
16. McGennis, R.B., R.M. Anderson, T.W. Kennedy, and M. Solaimanian. Background of Superpave Asphalt Mixture Design & Analysis. FHWA, Report № FHWA-SA-95-003, November 1994.
17. Hveem, F.N. Gradation of Mineral Aggregate for Dense-Graded Bituminous Mixtures. Proceedings Association of Asphalt Paving Technologists, Volume 11,1940.
18. Dalhouse, J.B. Plotting Aggregate Gradation Specifications for Bituminous Concrete. Public Roads, Vol. 27, № 7, 1953.
19. Lee, D.Y. Review of Aggregate Blending Techniques. Highway Research Board, Highway Research Record 441, 1973.
20. Lutter, B.E. and T.D. White. Computer Method for Aggregate Blending. U.S. Army Engineers Waterways Experiment Station, Instruction Report S-70-5, 1970.
21. Rothfuchs, G. Graphical Determination of the Proportioning of the Various Aggregates Required to Produce a Mix of a Given Grading. Betonstrasse, Vol. 14, № 1, 1939.
22. Mackintosh, C.S. Blending of Aggregates for a Premix Carpet. Transvaal Roads Department, Pretoria, 1959.
23. Nuemann, D.L. Mathematical Method for Blending Aggregates. Journal of Construction Division, American Society of Civil Engineers, Vol. 90, № 2, 1964.
24. Ritter, J.B. and L.R. Shafter. Blending Natural Earth Deposits for Least Cost. Journal of Construction Division, American Society of Civil Engineers, Vol. 87, № 1, 1961.
25. Easa, S.M. Trade-Off of Gradation and Cost Requirements in Aggregate Blending. Cement, Concrete, and Aggregates, Vol. 7, № 1, 1985.
26. Miller, L.J. and D.C. Bean. Selection of Aggregate Components by Computer for Optimum Mix Design. Proceedings Canadian Technical Asphalt Association, Vol. 25, 1980.
27. Barksdale, R.D. (Editor). The Aggregate Handbook. National Stone Association, Washington, DC, 1991.
|
|
Эмиссия газов от очистных сооружений канализации: В последние годы внимание мирового сообщества сосредоточено на экологических проблемах...
Папиллярные узоры пальцев рук - маркер спортивных способностей: дерматоглифические признаки формируются на 3-5 месяце беременности, не изменяются в течение жизни...
Архитектура электронного правительства: Единая архитектура – это методологический подход при создании системы управления государства, который строится...
Поперечные профили набережных и береговой полосы: На городских территориях берегоукрепление проектируют с учетом технических и экономических требований, но особое значение придают эстетическим...
© cyberpedia.su 2017-2024 - Не является автором материалов. Исключительное право сохранено за автором текста.
Если вы не хотите, чтобы данный материал был у нас на сайте, перейдите по ссылке: Нарушение авторских прав. Мы поможем в написании вашей работы!