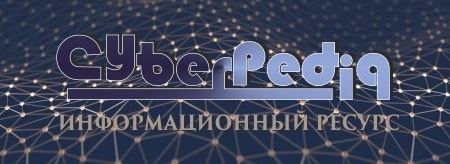
Опора деревянной одностоечной и способы укрепление угловых опор: Опоры ВЛ - конструкции, предназначенные для поддерживания проводов на необходимой высоте над землей, водой...
Двойное оплодотворение у цветковых растений: Оплодотворение - это процесс слияния мужской и женской половых клеток с образованием зиготы...
Топ:
Генеалогическое древо Султанов Османской империи: Османские правители, вначале, будучи еще бейлербеями Анатолии, женились на дочерях византийских императоров...
Проблема типологии научных революций: Глобальные научные революции и типы научной рациональности...
Особенности труда и отдыха в условиях низких температур: К работам при низких температурах на открытом воздухе и в не отапливаемых помещениях допускаются лица не моложе 18 лет, прошедшие...
Интересное:
Искусственное повышение поверхности территории: Варианты искусственного повышения поверхности территории необходимо выбирать на основе анализа следующих характеристик защищаемой территории...
Влияние предпринимательской среды на эффективное функционирование предприятия: Предпринимательская среда – это совокупность внешних и внутренних факторов, оказывающих влияние на функционирование фирмы...
Аура как энергетическое поле: многослойную ауру человека можно представить себе подобным...
Дисциплины:
![]() |
![]() |
5.00
из
|
Заказать работу |
|
|
О.В. Терехина
Л.В. Красильникова
АНГЛИЙСКИЙ ЯЗЫК ДЛЯ ПОЛИГРАФИСТОВ
Учебное пособие
Москва
2011
Рецензенты:
Р. И. Воронов, канд. истор. наук, доцент кафедры английского языка для технических специальностей МГУП
Т.А. Быля, доцент кафедры английского языка для технических специальностей МГУП
Терехина О.В., Красильникова Л.В.
Английский язык для полиграфистов: Учебное пособие / О.В. Терехина, Л.В. Красильникова – М.: МГУП, 20011. - с.
Печатается в авторской редакции
Данное учебное пособие дает возможность ознакомиться с историей развития полиграфии, особенностями допечатной подготовки и послепечатной обработки, видами традиционной и цифровой печати. Авторами разработана система лексических и грамматических упражнений, сопровождающих каждую тему курса.
Учебное пособие предназначено для преподавателей, студентов и аспирантов технических вузов(полиграфических специальностей), для представителей полиграфической отрасли, изучающих английский язык.
ПРЕДИСЛОВИЕ
Данное учебное пособие предназначено для студентов очного, очно-заочного и заочного отделений технических факультетов полиграфического вуза и является профильно-ориентированным, хотя не исключена возможность его использования и в других учебных заведениях, в системе дополнительного и второго высшего образования, базирующегося на основах полиграфических знаний.
Учебное пособие рассчитано на развитие навыков устной и письменной речи в результате овладения речевыми образцами, содержащими новые лексические и грамматические явления. В пособие включены специальные упражнения для формирования и поддержания языковых и речевых навыков при работе, как в аудитории, так и самостоятельно. Это обеспечивает более глубокую и детальную проработку предложенных тем и более качественное закрепление изучаемого материала.
|
Курс состоит из восьми уроков, последовательно описывающих историю, развитие, становление и современное состояние полиграфической индустрии, а также основные этапы печатного процесса, современные печатные технологии. Каждый урок содержит текст, где главный упор делается на изучение, перевод, пересказ текста, на расширение словарного запаса студентов.
Тексты, на которых строится работа каждого урока, взяты из английских и американских полиграфических источников и несколько сокращены. За текстом следует список речевых образцов (Words and Word Combinations).
Упражнения по обучению чтению на материале текста урока составлены с учетом принципа нарастания трудности и призваны развивать культуру чтения и понимания прочитанного. Одновременно с работой над содержанием текста изучается активный словарь урока, который в дальнейшем используется в текстах и упражнениях по принципу преемственности. Имеются упражнения на перевод с английского языка на русский и с русского на английский. Значительная роль отводится грамматическим упражнениям на повторение и закрепление времен английского глагола, модальных глаголов и других грамматических явлений и структур. Заключительным этапом каждого урока является устное выступление студента по изученной теме.
Unit ONE
TEXT
HISTORY OF PRINTING
Printing is a process for reproducing text and image, typically with ink on paper using a printing press. It is often carried out as a large-scale industrial process, and is an essential part of publishing and transaction printing.
The history of printing began as an attempt to make easier and reduce the cost of reproducing multiple copies of documents, fabrics, wall papers and so on. Printing streamlined the process of communication, and contributed to the development of commerce, law, religion and culture.
Woodblock printing is a technique for printing text, images or patterns used widely throughout East Asia and originating in China in antiquity as a method of printing on textiles and later paper. Block printing first came to Christian Europe as a method for printing on cloth, where it was common by 1300. Images printed on cloth for religious purposes could be quite large and elaborate, and when paper became relatively easily available, around 1400, the medium transferred very quickly to small woodcut religious images and playing cards printed on paper. These prints were produced in very large numbers from about 1425 onwards.
|
Around the mid-century, block-books, woodcut books with both text and images, usually carved in the same block, emerged as a cheaper alternative to manuscripts and books printed with movable type. These were all short heavily illustrated works, the bestsellers of the day, repeated in many different block-book versions: “Ars moriendi” and “Biblia pauperum” were the most common.
Movable type is the system of printing and typography using movable pieces of metal type, made by casting from matrices struck by letterpunches.
Around 1040, the first known movable type system was created in China by Bi Sheng out of porcelain. Metal movable type was first invented in Korea during the Goryeo Dynasty (around 1230). Neither movable type system was widely used, one reason being the enormous Chinese character set.
It is traditionally believed that Johannes Gutenberg, of the German city of Mainz, developed European printing technology around 1439 and in just over a decade, the European age of printing began, but new research may indicate that it was a more complex evolutionary process spread over multiple locations. Also, Johann Fust and Peter Schöffer experimented with Gutenburg in Mainz. Genealogically, all modern movable type printing can be traced back to a single source, Gutenberg's printing press which he derived from the design of long known agricultural presses.
Compared to woodblock printing, movable type pagesetting was quicker and more durable. The metal type pieces were more durable and the lettering was more uniform, leading to typography and fonts. The high quality and relatively low price of the Gutenberg Bible (1455) established the superiority of movable type, and printing presses rapidly spread across Europe, leading up to the Renaissance, and later all around the world. Today, practically all movable type printing ultimately derives from Gutenberg's movable type printing, which is often regarded as the most important invention of the second millennium.
Gutenberg is also credited with the introduction of an oil-based ink which was more durable than previously used water-based inks. Having worked as a professional goldsmith, Gutenberg made skillful use of the knowledge of metals he had learned as a craftsman. Gutenberg was also the first to make his type from an alloy of lead, tin, and antimony, known as type metal, printer's lead, or printer's metal, which was critical for producing durable type that produced high-quality printed books, and proved to be more suitable for printing than the clay, wooden or bronze types used in East Asia. To create these lead types, Gutenberg used what some considered his most ingenious invention, a special matrix wherewith the moulding of new movable types with an unprecedented precision at short notice became feasible. Within a year Gutenberg also published the first coloured prints.
Gutenberg's invention of the printing press revolutionized communication and book production leading to the spread of knowledge. Rapidly, printing spread from Germany by emigrating German printers, but also by foreign apprentices returning home.
Ivan Fedorov (later changed to Fedorovych) (born around 1510, died December 14, 1583 in Lviv), was one of the fathers (meaning Belarusian Francysk Skaryna) of Russian and Ukrainian printing. He was also a master cannon maker and the inventor of a multibarreled mortar. He knew several foreign languages: Church Slavonic, Polish, Latin Greek.
In 1532 he graduated from Jagiellonian University in Krakow with bachelor degree. During the reign of Ivan the Terrible Fedorov and the Belarusian P. Mstsislavets published in Moscow several liturgical works in Church Slavonic and the first book in Russian. It was “Apostol” (1563). This technical innovation created competition for the Muscovite scribes, who persecuted Fedorov and Mstsislavets. And fire which destroyed their workshop caused them to flee to the Grand Duchy of Lithuania. There they were received by the Great Lithuanian Hetman H. Khodkevych at his estate in Zabłudów (Zabludiv) (northern Podlachia), where they published Ievanheliie uchytel’noie (Didactic Gospel, 1569) and Psaltyr’ (Psalter, 1570). In Zabłudów, Fedorov changed his surname from Fedorov to Fedorovych. He moved to Lviv in 1572 and resumed his work as a printer the following year at the Saint Onuphrius Monastery. (Fedorovych's tombstone in Lviv is inscribed ‘drukovanie zanedbanoe vobnov[yl]’ [renewed neglected printing].) In 1574 Fedorovych, with the help of his son published the second edition of the Apostol, with an autobiographical epilogue, and Azbuka (Alphabet book). Fedorovych was known as the ‘Muscovite printer’ or Iwan Moschus (Ivan the Muscovite) in Lviv, a name used more to identify his place of origin than his nationality. In 1575 Fedorovych, in the service of Prince Konstantin Ostrozky, was placed in charge of the Derman Monastery; in 1577–79 he established the Ostrih Press, where, in 1581, he published the Ostrog Bible and a number of other books. Fedorovych returned to Lviv after a quarrel with Prince Konstantin Ostrozky, but his attempt to reopen his printing shop was unsuccessful. His printery became the property of the Lviv Dormition Brotherhood (later the Stauropegion Institute). The brotherhood used Fedorovych's original designs until the early 19th century. The first monument to Fedorov was opened in Moscow in 1909.
|
Letterpress
Letterpress is the oldest printing technology invented by Gutenberg in 1440. His invention is based on three things: cast print types, a hand-casting instrumentto make these types, and a printing pressdesigned for this purpose, which was adapted from the wine presses of the time. For many centuries the platen designof this hand press remained the only design for printing presses and basically only underwent various refinements with the change from the printing principle of the threaded spindle to the toggle lever principle, and of the structural material from wood to metal.
Intaglio
Intaglio engraving, as a method of making prints, was invented in Germany by the 1430s, after the woodcut print. Engraving had been used by goldsmiths to decorate metalwork, including armour, musical instruments and religious objects since ancient times, and the niello technique, which involved rubbing an alloy into the lines to give a contrasting colour, also goes back to late antiquity. It has been suggested that goldsmiths began to print impressions of their work to record the design, and that printmaking developed from that.
The golden age of artists engraving was 1450-1550, after which the technique lost ground to etching as a medium for artists, although engravings continued to be produced in huge numbers until after the invention of photography. Today intaglio engraving is largely used for currency, banknotes, passports and occasionally for high-value postage stamps. The appearance of engraving is sometimes mimicked for items such as wedding invitations by producing an embossment around lettering printed by another process (such as lithography or offset) to suggest the edges of an engraving plate.
Lithography
Lithography was invented by Alois Senefelder - Czech - in Bohemia in 1796. In the early days of lithography, a smooth piece of limestone was used (hence the name "lithography"—"lithos" (λιθος) is the ancient Greek word for stone). After the oil-based image was put on the surface gum arabic, a water soluble solution, was then applied, sticking only to the non-oily surface and sealing it. During printing, water adhered to the gum arabic surfaces and avoided the oily parts, while the oily ink used for printing did the opposite.
|
Chromolithography was the first method for making true multi-color prints. Earlier attempts at polychromed printing relied on hand-coloring. The type of color printing stemmed from the process of lithography, and it includes all types of lithography that are printed in color. It replaced coloring prints by hand, and eventually served as a replica of a real painting. Lithographers sought to find a way to print on flat surfaces with the use of chemicals instead of relief or intaglio printing. Depending on the amount of colors present, a chromolithograph could take months to produce. To make what was once referred to as a “’chromo’”, a lithographer, with a finished painting in front of him, gradually built and corrected the print to look as much as possible like the painting in front of him, sometimes using dozens of layers.The process can be very time consuming and cumbersome contingent upon the skill of the lithographer.
Offset press was invented in 1870s. Offset printingis the major lithographic technology. It is an indirect lithographic technology, in which the ink is first transferred from the printing plate onto a flexible intermediate carrier – the blanket – and then onto the substrate. Offset printing has spread markedly since approximately 1970 and has, to a great extent, ousted the letterpress printing technology which prevailed until that time. The offset printing technology is now the major printing technology.
Rotary printing press
In 1843, Richard March Hoe invented the rotary printing press, a design much faster than the old flat-bed printing press. In rotary printing press the impressions are curved around a cylinder so that the printing can be done on long continuous rolls of paper, cardboard, plastic, or a large number of other substrates.
In 1890, the first patented press was built in England by “Bibby, Baron and Sons”. The water-based ink smeared easily, leading the device to be known as “Bibby’s Folly”. In the early 1900’s, other European presses were developed using rubber printing plates. But by the 1920s, most presses were made in Germany, where the process was called “gummidruck”.
Screen printing
The modern screen printing process originated from patents taken out by Samuel Simon in 1907 in England. This idea was then adopted in San Francisco, California, by John Pilsworth in 1914 who used screen printing to form multicolor prints in a subtractive mode, differing from screen printing as it is done today.
Xerography
Xerographic office photocopying was introduced by Xerox in the 1960s, and over the following 20 years it gradually replaced copies made by Verifax, Photostat, carbon paper, mimeograph machines, and other duplicating machines. The prevalence of its use is one of the factors that prevented the development of the paperless office heralded early in the digital revolution.
The laser printer, based on a modified xerographic copier, was invented at Xerox in 1969 by researcher Gary Starkweather, who had a fully functional networked printer system working by 1971.Laser printing eventually became a multibillion-dollar business for Xerox.
The first commercial implementation of a laser printer was the IBM model 3800 in 1976, used for high-volume printing of documents such as invoices and mailing labels. It is often cited as "taking up a whole room," implying that it was a primitive version of the later familiar device used with a personal computer. While large, it was designed for an entirely different purpose. Many 3800s are still in use.
The first laser printer designed for use with an individual computer was released with the Xerox Star 8010 in 1981. Although it was innovative, the Star was an expensive ($17,000) system that was only purchased by a small number of laboratories and institutions. After personal computers became more widespread, the first laser printer intended for a mass market was the HP LaserJet 8ppm, released in 1984, using a Canon engine controlled by HP software. The HP LaserJet printer was quickly followed by other laser printers from Brother Industries, IBM, and others.
Most noteworthy was the role the laser printer played in popularizing desktop publishing with the introduction of the Apple LaserWriter for the Apple Macintosh, along with Aldus PageMaker software, in 1985. With these products, users could create documents that would previously have required professional typesetting.
|
In 1970 the first dot matrix printer (or impact printer) LA 30 was introduced by Digital Equipment Corporation of Maynard, Massachusetts. It printed 80 columns of uppercase-only 5x7 dot matrix characters across a unique-sized paper. The printhead was driven by a stepper motor and the paper was advanced by a somewhat-unreliable and definitely noisy solenoid ratchet drive. The LA30 was available with both a parallel interface and a serial interface; however, the serial LA30 required the use of fill characters during the carriage-return operation.
Inkjet printing
ESSENTIAL VOCABULARY
Words and Word Combinations
1. printing
2. publishing
3. woodblock printing
4. technique
5. image
6. woodcut books
7. movable type
8. letterpunches
9. printing press
10. pagesetting
11. durable
12. oil-based ink (water-based ink)
13. an alloy of lead and tin
14. coloured prints
15. the inventor of smth.
16. intaglio engraving
17. gravure (intaglio) printing
18. relief printing (letterpress)
19. impression
20. goldsmith
21. to produce an embossment
22. lithography
23. chromolithography
24. offset printing
25. printing plate
26. blanket cylinder
27. surface
28. gum arabic
29. water soluble solution
30. to apply
31. adhere to smth.
32. multi-color prints
33. time consuming process
34. flexible intermediate carrier
35. a substrate
36. rotary printing press
37. screen printing
38. xerographic copier
39. digital printing
40. inkjet printing
41. thermal printing technology
42. 3D (three-dimensional) printing
43. print on demand
44. printing area
45. variable data
ACTIVITIES
Grammar reference. Adverbs.
· We use adverbs to give extra information about verbs, adjectives and other adverbs.
· We usually add -ly to an adjective to form an adverb. (definite-definitely; efficient-efficiently)
· We add –ally to adjectives ending in –ic. (dramatic-dramatically)
· Some adverbs are ‘irregular’ and are not formed with –ly. (good-well; fast-fast)
· Some adverbs ending in –ly have different meaning from the adjective. (hard-hardly)
· Some words ending in –ly are adjectives and not adverbs. (friendly; lovely)
Find the adverbs in the text and complete the table according to the rules:
-ly | -ally | ‘irregular’ | adjective |
Unit TWO
TEXT 1
CONVENTIONAL PREPRESS
The process of producing printed products can be divided into three parts: prepress, printing (press), and print finishing (postpress).
Prepress includes all the processing steps required to go from the preparation of the text, original images and graphics as well as the design concept right up to the production of the ready-for-print a printing plate, it is then employed at the printing stage to produce the job.
A fundamental technological change has taken place within prepress. The use of conventional typesetting machines, repro cameras, and film has been replaced by computer technology in virtually all branches of this industry. Text and image are digitized or actually created digitally, processed electronically and output directly onto the printing plate in print format, and increasingly without the use of film intermediates.
For many companies film remains an indispensable information carrier, that’s why both conventional and digital prepress technologies are used nowadays. The distinguishing factor between them is the way the films are used: all technological variations where individual films are used for the page or print sheet composition and require conventional, mechanical/manual film assembly processes, and do not there-fore employ digital full-page film exposure systems, are dealt with under the category “conventional prepress.”
The first step in producing a printing plate is the creation of the film copies for the printing plates. Film copies contain all of the information to be printed on the printed sheet corresponding to each color, but also opaque black-and-white originals especially for single-color work. In contrast to the digital production of masters where text and image processing are carried out at the same time, in conventional prepress text creation and image processing are carried out separately.
Today’s typesetting begins with the inputting of text into a computer. Word processing on computers with powerful, user friendly word processing programs has become state of the art.
Text input is the first stage of typesetting. This task is undertaken by the author himself. Text input is followed by word processing, which creates the design parameters planned in the layout such as the choice of font, font size, line length and spaces for images to be added later.
Word processing is followed by text output. The designed blocks of text are output onto film or paper. In this form they are ready for manual page make-up that is, for completion with images and graphics required by the page of the book. If page layout including the integration of text and image is carried out electronically in the computer, the completed page is output on film or paper. The file forms a useful starting point either for electronic/digital processing, such as computer to plate or computer to film, for digital printing by direct imaging, and so on, or for further use in electronic media.
Corrections to the output text are time-consuming and expensive and should therefore be avoided as much as possible. For this reason a number of correction stages are incorporated into the procedure. “House corrections” are made in the printing house with the help of paper printouts of the digitally stored text. Corrections by the author follow the completion of the designed columns of text. These are output as galley proofs on paper and sent to the author for proofreading.
When corrections have been made the page is made up. The main function of the correction process which forms page make-up is the placing of the pictures in the correct position on the page, the correct and complete assigning of the picture captions, footnotes, cross references to other pages, and the arranging of headers and footers including page numbering. After further proofreading and checking the author signs to confirm that the pages are correct and ready for printing, that is, he passes them for press.
Should the further processing of the text into a film be done conventionally, that is manual assembly, exposed films are required.
Output devices used for the exposure of films are called “film imagesetters”. There are imagesetters of the flatbed design, capstan imagesetters, and internal and external drum imagesetters. In all of them exposure takes place spot by spot in lines across the whole area being exposed.
The combination of text and images to form a page occurs during the page “make-up”. In the production of conventional printing plates the complete page is put together manually by repro experts from text and images that exist mainly as cut films. The films are placed on a carrier sheet, adjusted for position, and fastened in place. The quality of the print depends directly on the precision and care of the makeup. Register errors caused at this stage are unlikely to be able to be compensated for later in the print. Film stripping is carried out on a light table. Its work surface consists of a glass plate that is illuminated from below with diffuse white light. Two steel rulers at exact right angles, which may be moved in parallel, are used to ensure accurate stripping.
In preparation for the stripping a millimeter sheet is first placed on the light table with the carrier sheet on top and fastened with adhesive tape. The carrier sheet is a plastic film that is dimensionally stable, insensitive to moisture, crystal clear, clean, and free of scratches and should be as resistant as possible to build-up of electrostatic charge. Polyester film with a thickness of 0.15 mm has proved useful for this purpose.
The several films are always mounted with the coating facing uppermost so that during subsequent copying exposure occurs coating to coating to avoid undercutting.
The assembly of multicolored images must be carried out with particular care as imprecision translates directly into register errors.
Sheet assembly is an information-gathering point of central importance for achieving trouble-free results.
The first step in producing a sheet assembly is to draw a layout sheet containing the correct measurements. It is the same format as the sheet with an additional border and is made of dimensionally stable transparent material/paper. If we take a layout sheet for a sheet-fed offset press as an example, after positioning on the light table parallel to the axes and fastening with adhesive tape, the sheet format, gripper edge, the beginning of the print, and the center line are marked in. The data required for this are in the documentation referring to the press or may be obtained from the job itself.
The exact outlines of all of the pages to be accommodated on the top surface of the sheet must be accurately drawn, in reverse (wrong-reading). These include the distances between the pages taking into account allowances for folding and trimming. The page number must be entered in the bottom outside corner of each page.
The result of prepress – in particular error-free typesetting and its correct location on the page, the quality of the images, the registration, the quality of color reproduction on the paper, the reproduction of details and their correct location on the sheet in all color separations/colors in accordance with the original – should be checked for accuracy at the earliest possible stages in the process.
The following proofs are typical of what is used in conventional prepress:
• galley proof;
• position proof/blueprint;
• color proof;
• press proof;
Galley proofs are produced for corrections to typesetting products such as continuous text, headings and titles, headers and footers for individual pages, picture captions, footnotes, indexes, and tables of contents, as well as to control the completeness and correct location of marks and control strips. They are produced as a paper printout of typesetting files, or as a paper print or blueprint of typeset columns preset in film form or film assemblies. After checking and marking necessary corrections the originals are altered and released for the next processing steps.
Position proofs are required to check the completeness and correct location of text and image. Blueprints from the film assemblies or full-page films fulfill this purpose very well and are also cost-effective.
Color proofs are necessary for judging the quality of multicolor products. The color proof may be produced for individual images, but it is preferable to produce them for the whole page, although this is less often feasible for the whole sheet – mainly due to reasons of format.
For the printing side the color proof may be used to control the correct position of the individual color separations on the page, accurately registered assembly, the approximate overall color effect of the page or the representative color reproduction of the printed product to be produced, but with certain limitations, since the proofing process and materials used are generally not the same as the technology and materials used to produce the job; color management assists in optimizing this.
Press proofing process has the best achievable correlation with the subsequent printing of the job, especially if the printing press used is the same one that will be used to print the job. This requires a full set of printing plates. The printed proof is produced on the paper and with the ink used for the job. The effort for producing such a printed proof is considerable and only justified
for very high quality requirements. To keep high speed production machines available during the time it takes to produce the printed proofs, special proofing machines are available.
Platemaking
Printing plates vary according to the individual technology – offset, letterpress/flexography, gravure, and screen printing.
During platemaking itself, the film is transferred optically onto the unexposed printing plate. This is done by means of either a contact copy or projection. In the former process a film is used whereas projection is done either from film or a reflection copy, that is, a paste-up. A printing plate is produced for each primary color of the intended print on the basis of the corresponding color separation.
Radiation or exposure of the unexposed printing plate in accordance with the image may be followed by an intermediate step (such as heating) before the printing plate is developed using the chemical/physical processes appropriate to its material. This is followed by the final treatment of the plate, in which the latter undergoes after-treatment (e.g., baking to increase possible run length) or preservative measures (e.g., gumming-up to improve storage properties and printability) and is prepared for fitting in the press (e.g., punching, beveling).
ESSENTIAL VOCABULARY
Words and Word Combinations
ACTIVITIES
DIGITAL PREPRESS
The extensive standardization and compatibility between systems (PC or Mac/Apple), software, and data formats used by the customer, the agency, and the prepress company allow for a division of the workflow. Text, images, and layout can be prepared either by the customer, the author, or the agency. This division of work is also applicable to the jobs carried out within a printshop with a prepress stage included.
The text data are primarily prepared in “Word” format, which has virtually become the word processing standard, since it is most widely used and offers many professional tools. The text data are very rarely edited directly in Word; instead they are positioned and typographically edited in a layout program (QuarkXPress, InDesign, or PageMaker).
The picture objects of a printed product are usually available as photograph, slide,or reflectioncopy, and are scanned in, or digitized, for publication. The digital data are then available at a workstation for further processing (corrections of the image contents or geometry).
Further alternatives have been added to this classical procedure: for instance the principle of the Photo CD. This procedure still includes the use of a camera and the development of the film. However, very often the result is not a slide, but a data file, for example stored on a Photo CD, containing original pictures that are already digitized. As for the scanned image, these data can also be processed directly onto the workstation.
Graphics constitute the third main element of a printed page. They are generally generated in so-called illustration programssuch as Freehand, Illustrator, or CorelDraw. These data are usually saved in the form of vector-based data files, which cannot be edited or positioned in a layout program. These software programs offer an opportunity to save graphics or drawings in EPS format and make them available in the layout for geometric processing (scaling, cropping).
Layout programs are software packages allowing for flexible, creative work and for integrating the elements (text, images, and graphics) on pages or a sequence of pages, or to position them on the page depending on the current job.
In many cases, production servers make it possible to prepare data for output on different output systems such as film imagesetters (computer to film systems), computer to plate, computer to press/direct imaging or computer to print systems. The data to be made available do not really differ from each other. The settings for the resolution, screen frequency, and so on, are defined in or by the RIP. For conventional workflows, that is, for workflows based on the PostScript file (the newer workflow management systems are based on PDF technology), all the settings required for imaging are defined on the server or at a workstation and this information is transferred to the RIP. This is also the case when selecting the screening method to be used.
Input and Output Resolution
One obvious quality feature is the image definition, which can be determined at a deliberately low level inthe original for artistic reasons, or it is limited by theresolution when scanning the original and transferringit to the film, plate, or substrate.
The original is scanned by either a digital camera or an input scanner. The image information is not transferred entirely, but only in accordance with a scanning pattern of a specified resolution
and number of tone value levels or gray levels. The pattern consists of the smallest image elements resolved by the scanning device, the pixels. This word is a neologism created from “picture” and “element.”
When an image is to be output on film, plate, or directly on a print substrate, the dot shape, screen frequency, and screen anglesmust be specified first. Since the dots to be written are made up of individual pixels (except in gravure printing), the pixel size must also be specified.
Modern imposition programs offer virtually any imposition pattern in prepress. Communication and consultation from accepting the order up to the binding is as essential as ever in spite of all the automation.
The technological development that has taken place in the area of film imagesetters and computer to plate systems has rendered the working methods outlined unnecessary. Powerful output devices, coupled with special software programs have made it possible to have an integrated process for single-color and multicolor jobs. Producing entire sheets through large-format laser imagesetters is not only of technological interest but is also of economic significance as a result of rationalizing the workflow and saving material. For example, when printing eight made-up pages it is not necessary to expose the individual pages. The use of material is consequently more effective and more economical.
Color management
Color management is the calibration of all input and output devices within an image processing chain with the aim of always achieving the desired color reproduction independent of the devices used. Color management ensures optimum color reproduction irrespective of the input device, monitor, and output device used, as long as the device is characterized by an ICC profile(International Color Consortium).
An important reason for using color management today is the certainty that the correct output result will be achieved at the first attempt. When using color management, there are now several
intermediate steps inserted between the output of the RGB values and calculation of the CMYK values. This appears at first sight to be lengthening the process. However, these intermediate steps ensure that the weaknesses of the conventional system mentioned earlier are eliminated.
Digital proof
The proof should be a perfect sample of the later print run. Various paper qualities and printing processes should be taken into account. The ideal conditions for a proof would be to use the same press, same paper, and same ink. However, the question of cost and time constraints severely limits the demand for this perfect scenario.
The broader the range of application of a proof, the more comprehensive the requirements. Such demands often stretch from the presentation through color-reliable proofs right up to the proof that serves as a “contract proof” (it can be used as evidence in legal disputes).
The demands on a proof therefore vary quite significantly. For this reason, the market offers proof systems that can reproduce an original at various rendering qualities in accordance with the color print of the production run. Selecting the optimal system means balancing costs and benefits and analyzing what is to be expected from a proof:
• reproduction of the complete page contents and/or sheet;
• color reliability (visually similar or color-true);
• reproduction of the screen structure (and the halftone dot arrangement) which is used for the
production run;
• same substrate surface and sheet size as used for production;
• time required to produce the proof is acceptable;
• job-specific cost situation.
Digital proofing systems can be classified into two basic process variants based on intended use and quality required:
• soft proof;
• hard proof.
Soft proof describes the simulation of the print result on a monitor. The color reliability of images on the monitor depends heavily on the viewing conditions, and colors do not always match those of the printed copies. While the color-reliable representation of the image on the screen normally requires a darkened room, a sample print must be viewed under standard light conditions close to daylight. Although a few compromises have to be made from the virtually perfect simulation of the later print quality on the monitor, soft proofs offer interesting, forward-looking solutions for the cooperation between customers and service providers in reproduction technology.
In so-called “remote proof” applications, files can be sent rapidly via global networks and later print runs simulated on site with the customer. Color management systems perform a key function when implementing this kind of production scenario.
Hard proofs can be further divided into five general classifications:
•blueprint;
•imposition proof (layout proof);
•color proof;
•screen proof;
•press proof.
Blueprint is created to gain an initial overview of the contents, impositionlayout, and completeness of a data set to be printed, asingle-color. Here a so-called “Ozalid/diazocopy” (which is monochrome and blue due to theprocess involved) is produced after assembly and offersinformation about the completeness of the pages, theirposition on the sheet, and the imposition layout. Indigital printing technology this technical context nolonger exists. Blueprint has become a generic term.
In order to gain a color impression (but not color reliable) of the file a layout can be created. Today blueprint and layout proofing are applications ideally suited to reasonably priced large-format printersand are normally equipped with ink jet printing units
In practice, the process most commonly understood under the term digital proofing is “color proof.” In the printing industry and in the context of high quality prints, this proof provides the color-reliable/color-true reproductionof the contents of the file intended for printing. More and more standard printing systems are being used for this, such as ink jet printers, four-page A4 format or thermal sublimation printers, two-page format in combination with powerful color management systems. The color proofs created in this way serve as a guideline (reference) for the printer in charge of the production run.
If the screen structuresof the later printing procedure can also be simulated using a digital printing process, the term “screen proof”is used (also true proof since, with this level of quality, reproducing the dot structure too, this proof is the closest to that in the print run).Among other
things, information about the screen structure enables the printing expert to recognize changes to the tone value and the color shifts associated with this or to see the effects of color register deviations early on.
The effects of halftone dot, screen angle, and screen frequency are reproduced in the screen proof and show the print quality of multicolor overprinting.
Press proofis a test printof the data directly in a printing press. This can be the press for the production run or a comparable press (using the same print technology) prepared especially for proof purposes. Short runs of 50 or 100 copies can be produced more cost-effectively than with
other color proof processes. The individual proof is hardly economically justifiable.
ESSENTIAL VOCABULARY
Words and Word Combinations
ACTIVITIES
Unit THREE
TEXT 1
Inking Units
During the printing process, a thin film of ink is transferred from the image areas of the plate to the substrate. The inking unit’s function is to provide a constant supply of fresh ink to the image areas on the plate to maintain a constant inking process. The amount of ink “used up” must be fed back to the system. There must be an equal balance between ink fed and ink dispensed in order to avoid variations in the ink density on the printed image. Another important factor for the print quality is the uniformity of the ink film thickness on the image areas of the plate or the image areas of the substrate. (It is a postulate of offset printing that the film of ink should be of the same thickness across the entire printed sheet. Reproduction technology for the creation of color separations is based on this principle). Consequently, the criteria determining quality are:
• temporary fluctuations of the average ink film thickness (quantity balances) and
• uniformity of the ink film thickness on the image areas of the plate or the printed areas of the substrate.
Dampening Units
Conventional offset printing requires a dampening system to supply a very thin film of dampening solution to the non-printing elements of the printing plate. Since part of the dampening solution is printed via the ink, plate, and blanket and another part evaporates, it is necessary to have a constant supply of dampening solution.
Printing Unit
Printing unit consists of inking and dampening units, the plate cylinder with the printing plate, the blanket cylinder with the blanket fixed to it, and the impression cylinder. The plate cylinder with the inked printing plate rolls over the circumference of the blanket cylinder. The blanket cylinder, in turn, rolls over the circumference of the impression cylinder, on which the sheet of paper is held by grippers. The contact line between the blanket cylinder and the impression cylinder is called the printing nip.
The printing plate (an up to 0.3 mm thick sheet of metal or a foil) carries the image elements of the respective color separation. The blanket is an approximately 2 mm-thick, exchangeable cylinder cover made from flexible material and layers of fabric. The plate cylinder’s circumference is interrupted by an axial recess, the cylinder gap. This recess holds the plate clamping mechanism. The blanket cylinder, likewise, has a gap to hold the blanket clamping mechanism, and the impression cylinder has a gap to accommodate the gripper system for paper transportation.
To ensure perfect transfer of the print image from plate to paper, all three cylinders must have the same circumferential speed at the contact line/printing nip. Due to the recesses in the cylinder’s circumferences, the relative rolling motion necessary for continuous production cannot be achieved simply by friction between the cylinder surfaces. Along with the frictional connection via the cylinder surfaces, the cylinders are also connected via a gear train for this reason.
The printing unit is driven by the impression cylinder via a gear train. The printing unit in turn transmits the necessary drive power for the inking unit. Printing problems arising from the gear train (the unwelcome “gear marks” in particular) are avoided by the narrow tolerances specified for the design of gearwheels and thanks to tried and tested production technology and quality control.
For the proper transfer of ink between plate and blanket and between blanket and paper, a sufficiently high contact pressure between the cylinders as well as the same circumferential speed of the cylinders are necessary.
Рис. 1
Advantages of offset printing are:
• materials with different sheet size and grammages can be processed;
• nearly all finishing operations are possible
• the quality is rather high.
Disadvantages are:
• complicated method – causes misprints
• sheet size just as big as machine size
• expensive printing machines.
ESSENTIAL VOCABULARY
Words and Word Combinations
ACTIVITIES
13. What units does the offset printing press consist of?
16. Why is offset printing considered to be the major technology now?
1 | non-printing | a | tension |
2 | physical | b | speed |
3 | dampening | c | areas |
4 | printing | d | phenomena |
5 | ink | e | units |
6 | plate | f | cylinder |
7 | blanket | g | solution |
8 | gear | h | pigments |
9 | surface | i | train |
10 | circumferential | j | cylinder |
5. Fill in the gaps with an appropriate word or phrase from the box:
Dampening solution, hydrophilic, oleophilic, ousted, graining, circumferential speed, hue, plate, a highly viscous mixture, non-printing areas, blanket, impression. |
1. Offset printing has spread since 1970 and ……….. the letterpress printing technology.
2.The printing areas of the printing plate are ………...
3. The non-printing areas of the printing plate are ……….
4. The dampening system covers the non-printing areas of the printing plate with a thin film of ……… ………...
5. The ………. of the surface can be done mechanically.
6. The ink used in offset printing is usually…………..
7. The pigments determine the ….. of the ink.
8. The dampening solution spreads over ………. ………...
9. Printing unit consists of inking and dampening units, the ……. cylinder, the …….. cylinder and the …… cylinder.
10. High contact pressure between the cylinders and the same ……….. ……… of the cylinders are necessary for the proper transfer of ink between the plate, blanket and the paper.
6. Put the verbs in brackets in appropriate form, translate the sentences into Russian:
1. Offset printing (to spread) markedly since approximately 1970.
2. The dampening solution (to spread) over the non-printing areas.
3. Aluminum (to be gaining) ground for a long time among the metal-based plates over zinc and steel.
4. The cylinders (to be connected) via a gear train.
5. Mineral oils (to be used) as carrier substances for offset inks.
6. The dampening solution (to consist) mainly of water.
7. Letterpress printing technology (to prevail) until the spreading of the offset printing.
7. Find the sentences with the following prepositions in the text. Give some examples of your own using the prepositions under study:
Due to, along with, for, via, as well as, since, in turn.
8. Translate the following expressions from Russian into English. Use these expressions in the sentences of your own:
Печатная технология, пробельная зона, печатная зона, олеофильный, гидрофильный, красковпитывающий, водоотталкивающий, физический феномен, увлажняющий раствор, хорошее смачивание (увлажнение), поверхностное натяжение, легко установить, широко использоваться долгое время, основной компонент, частицы неправильной формы, порошкообразный, толщина красочного слоя, формный цилиндр, офсетный цилиндр, печатный цилиндр, печатная форма.
9. Transfer the sentences from passive voice into active:
e .g.: Physical phenomena create this effect at the contact surfaces.
Sheet-fed Offset Printing
Sheet-fed offset printing has impressive economic and qualitative advantages over other printing technologies. Fundamental attributes of sheet-fed offset are flexible production options and the relatively economical production of printed products of a very high quality for a wide range of print volumes. The color combination ranges from one to four-color prints up to twelve-color prints (with perfecting). In sheet-fed offset printing, substrates of different sheet sizes and grammages are processed and these can generally be obtained off-the-shelf at short notice.
Just as important for the client as the free choice of format is the range of special substrate qualities. The great variety of standard substrates for sheet-fed offset necessitates well-organized stock-keeping in the paper industry. In-line or off-line finishing operations, such as coating, imprinting, numbering, perforating, and punching are popular technologies used in sheet-fed offset. And finally the sheet finishing variants available are virtually inexhaustible.
A sheet-fed offset press must basically perform the following tasks:
• provide a high-precision conveyance of the flexible substrate at high speeds, under very dynamic, process-specific strains;
• enable a complicated printing process, involving several material flows (of dampening solution, ink, paper, air), to run in a controlled and reliable way.
High-precision conveyor systems, guide elements, and monitoring systems are necessary in order to route the sheet from the feed pile via the feeder, through the printing units, and finally to the delivery, where the printed sheet is stacked in a pile again.
There is a great variety of constructive solutions for feeder variants used in printing and print finishing machinery. Single-sheet feeders or stream feeders are found on sheet-fed offset presses.
The single-sheet feeder has the advantage that it is easier to adjust to the sheet size and the paper quality. High-speed presses processing large formats, on the other hand, are exclusively equipped with stream feeders, so that the highly dynamic processes and the accurate sheet alignment can still be mastered in accordance with quality requirements.
The feed system has the task of picking up the sheets from the feed pile, separating them, conveying them to the feed table via a feed system, and aligning them at the feed guides. Since each sheet is individually aligned at the feed guides the print image can be positioned on the sheet with an adequate degree of accuracy (position in relation to the paper edges and, if applicable, to a preprinted image on the front or reverse side).
Sheets are usually printed on both sides. To achieve this, they have to pass through the press a second time, unless a perfecting press is being used, in which straight printing and perfecting can be done in one pass.
Work and Turn. For the second pass (verso printing) the sheets are usually turned over before being prepiled again. This means that the pile is turned so that the side edges are changed over.
So that the sheet can always be aligned at the same three points, the sheet-fed offset press needs a second side lay on the opposite side from the first side lay. After work and turn, the second side lay has to be used to ensure an accurate register alignment. The change of side lay after work and turn only becomes unnecessary if all sheets in the pile are of the same size. Only then can the accurate register alignment be ensured for the front and reverse sides without having to change the side lays.
In the production print sheets, meaning that the indi
|
|
История развития пистолетов-пулеметов: Предпосылкой для возникновения пистолетов-пулеметов послужила давняя тенденция тяготения винтовок...
Семя – орган полового размножения и расселения растений: наружи у семян имеется плотный покров – кожура...
Папиллярные узоры пальцев рук - маркер спортивных способностей: дерматоглифические признаки формируются на 3-5 месяце беременности, не изменяются в течение жизни...
История создания датчика движения: Первый прибор для обнаружения движения был изобретен немецким физиком Генрихом Герцем...
© cyberpedia.su 2017-2024 - Не является автором материалов. Исключительное право сохранено за автором текста.
Если вы не хотите, чтобы данный материал был у нас на сайте, перейдите по ссылке: Нарушение авторских прав. Мы поможем в написании вашей работы!