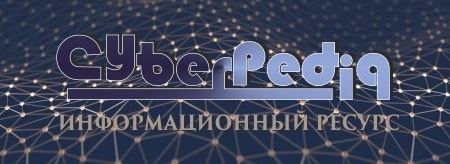
Наброски и зарисовки растений, плодов, цветов: Освоить конструктивное построение структуры дерева через зарисовки отдельных деревьев, группы деревьев...
Автоматическое растормаживание колес: Тормозные устройства колес предназначены для уменьшения длины пробега и улучшения маневрирования ВС при...
Топ:
Установка замедленного коксования: Чем выше температура и ниже давление, тем место разрыва углеродной цепи всё больше смещается к её концу и значительно возрастает...
Оценка эффективности инструментов коммуникационной политики: Внешние коммуникации - обмен информацией между организацией и её внешней средой...
Интересное:
Что нужно делать при лейкемии: Прежде всего, необходимо выяснить, не страдаете ли вы каким-либо душевным недугом...
Инженерная защита территорий, зданий и сооружений от опасных геологических процессов: Изучение оползневых явлений, оценка устойчивости склонов и проектирование противооползневых сооружений — актуальнейшие задачи, стоящие перед отечественными...
Уполаживание и террасирование склонов: Если глубина оврага более 5 м необходимо устройство берм. Варианты использования оврагов для градостроительных целей...
Дисциплины:
![]() |
![]() |
5.00
из
|
Заказать работу |
|
|
Можно выделить следующие основные технологические направления работ по модернизации производства стали в дуговых электрических печах:
комплексное использование сырья;
более глубокое обогащение руд, максимально возможная переработка накопленного и образующегося металлического лома с целью снижения энергетических затрат;
минимизация издержек производства, включая транспортные расходы на перевозку сырья и готовой продукции;
организация производства отдельных видов металлопродукции, снижающих уделбную металлоемкость национального дохода, включая холоднокатанный лист, коррозионно-защищенные металлические изделия, холодногнутые профили и др.;
повышение качества стальной заготовки (содержание химических элементов в узких пределах, бездефектная поверхность, качественная макро- и микропродукция.
Повышение эффективности работы дуговых сталеплавильных печей возможно за счет применения автоматизированной системы контроля и управления (АСКиУ) технологией выплавки стали.
Общеизвестно, что на сегодняшний день экономически наиболее целесообразной является выплавка высококачественной стали в дуговых сталеплавильных печах переменного тока (ДСП).
На многих существующих ДСП, разработанных 15-20 и более лет назад, используется аналоговая или простейшая цифровая система управления, которая уже морально устарела и не соответствует современным требованиям к производительности печи, удельному расходу энергии, качеству выплавляемой стали, надежности и т.д. Вместе с тем в последнее время наметился качественный скачок в области микропроцессорных систем автоматического управления и электрического привода, связанный с новым подходом к решению задач управления, проектирования систем управления и автоматизации, новыми технологиями монтажа и наладки. Существующие системы управления ДСП реализуют достаточно простые законы управления и имеют низкое быстродействие, определяемое датчиками и исполнительными устройствами. Это, в свою очередь, ведет к высокому удельному расходу электроэнергии и низкому качеству выплавляемой стали.
|
Все эти требования можно удовлетворить при использовании современных программируемых контроллеров, приводов перемещения электродов на нижнем уровне автоматизации и промышленных ЭВМ на верхнем. При этом существенную роль играют алгоритмы регулирования и быстродействие отдельных элементов системы. Последнее связано с тем, что одним из основных параметров, определяющих и качество стали, и удельный расход электроэнергии, является дисперсия тока дуги, а ее снижение следует считать одной из главных задач модернизации печи.
Раньше в качестве регулируемого электропривода традиционно использовался привод постоянного тока. В конструкции двигателя постоянного тока имеется коллектор и щеточный аппарат, что усложняет эксплуатацию двигателя, приводя к дополнительным расходам на его техническое обслуживание. Асинхронный двигатель имеет прочную конструкцию, надежен и практически не требует обслуживания, а совместно с частотно-регулируемым приводом обеспечивает характеристики, аналогичные приводам постоянного тока
В результате модернизации системы управления ДСП возможны следующие изменения:
•- аналоговый регулятор мощности дуги заменяется на цифровой, построенный на базе программируемого логического контроллера;
• тиристорные электроприводы постоянного тока заменяются частотно-регулируемыми асинхронными на основе преобразователей частоты;
• электродвигатели постоянного тока в приводе перемещения электродов заменяются на асинхронные;
|
• системы автоматики, защит и диагностики выполняются программно;
• пульт оператора заменяется на новый, выполненный на основе цветного промышленного монитора. С монитора осуществляется ввод заданий на текущую плавку, отображается состояние печи, системы защит и автоматики;
• пульт сталевара, мастера заменяется на современные, с которых возможно также плавное управление движениями ДСП, без использования коммандо-контроллеров;
• управление переключателем ступеней напряжения заменяется на цифровое, построенное на базе программируемого логического контроллера;
Необходимо увеличить применение современной микропроцессорной техники, что ещё в большей степени позволит реализовать оригинальный алгоритм регулятора мощности дуги, существенно увеличить точность и скорость перемещения электродов, что обеспечит стабилизацию мощности дуги в необходимых пределах.
Для комплексного решения задачи рационального управления технологией требуется значительное расширение информационной базы за счет оперативного контроля параметров, отражающих текущее состояние процесса, а также параметров входа и выхода. Наряду с автоматическим контролем массы шихты, сплава и шлака, температуры металла на выпуске и в характерных точках внешней поверхности печи, необходимо контролировать постоянную составляющую напряжения дуги. Изменение последнего параметра отражает изменение температуры металла и состава шлака.
Процесс накопления расплава можно отследить по изменению его электрического сопротивления. В Институте металлургии УрО РАН разработан и апробирован в автоматизированной системы управления АСУ метод определения электрических параметров зон рабочего пространства ферросплавной печи. Его адаптация к условиям сталеплавильного процесса позволит оперативно (с частотой выше 1 измерения в секунду) контролировать распределение энергии по зонам дуги и расплава.
Программная реализация метода возможна лишь при переходе от определения действующих значений исходных электрических сигналов к анализу их мгновенных значений и динамической вольт-амперной характеристики полезной нагрузки. Это требует замены медленных аналогоцифровых преобразователей быстродействующими, что не значительно, но повышает стоимость аппаратурного обеспечения. Однако указанный переход позволяет построить автоматический регулятор (АР), функционирующий по принципу симметрирования активной мощности дуг, и существенно расширить круг контролируемых параметров состояния процесса.
|
Заключение.
1. Сталь является одним из важнейших материалов практически во всех сферах производства.
2.Дуговые электрические печи являются одними из наиболее совершенных сталеплавильных агрегатов для производства стали и сплавов.
3. Основные преимущества способа получения стали в электрических печах - возможность создания высокой температуры в плавильном пространстве печи (более 2000 'С) и выплавки стали и сплавов любого состава; использование известкового шлака (до 50...60 % СаО), способствующего хорошему очищению металла от вредных примесей - серы и фосфора; возможность ведения плавки при всех режимах и условиях производства.
4. Главным недостатком электрических печей является большой расход электроэнергии, поэтому главной задачей совершенствования является снижение элктропотребления.
5. Также необходимо улучшить допечную обработку сырья.
Список литературы:
1. М а р и н ч е н к о В. А., Электрооборудование дуговых печей трехфазного тока, Металлургиздат, 1955.
2. Электроплавильные печи черной металлургии, 3 изд., М., 1950.
Б. С. Барский.
3. Производство стали в дуговых печах, Материалы конференции, изд-во «Металлургия», 1967.
4. Линчевский Б.В., Соболевский А.Л., Кальменев А.А. (1986) Металлургия черных металлов.
5. Основы металлургического производства (черная металлургия)
Москва «Металлургия» 1988
6. В.Г. Антипин, С.З. Афонин, Л.К. Косырев "О направлении развития и структуре сталеплавильного производства", "Сталь" №3 1993 г.
7. Марочник сталей и сплавов, Машиностроение, 1989 г.
8. В. П., Дуговые вакуумные печи и электронные плавильные установки, Металлургиздат, 1962.
9. Сисоян Г. А., Электрическая дуга в электрической печи, Металлургиздат, 1961.
|
|
Типы сооружений для обработки осадков: Септиками называются сооружения, в которых одновременно происходят осветление сточной жидкости...
Археология об основании Рима: Новые раскопки проясняют и такой острый дискуссионный вопрос, как дата самого возникновения Рима...
История развития хранилищ для нефти: Первые склады нефти появились в XVII веке. Они представляли собой землянные ямы-амбара глубиной 4…5 м...
Архитектура электронного правительства: Единая архитектура – это методологический подход при создании системы управления государства, который строится...
© cyberpedia.su 2017-2024 - Не является автором материалов. Исключительное право сохранено за автором текста.
Если вы не хотите, чтобы данный материал был у нас на сайте, перейдите по ссылке: Нарушение авторских прав. Мы поможем в написании вашей работы!