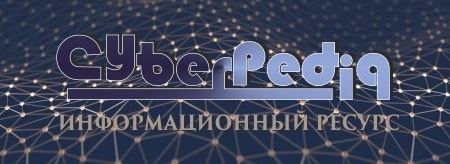
Типы оградительных сооружений в морском порту: По расположению оградительных сооружений в плане различают волноломы, обе оконечности...
Своеобразие русской архитектуры: Основной материал – дерево – быстрота постройки, но недолговечность и необходимость деления...
Топ:
Организация стока поверхностных вод: Наибольшее количество влаги на земном шаре испаряется с поверхности морей и океанов...
Проблема типологии научных революций: Глобальные научные революции и типы научной рациональности...
Характеристика АТП и сварочно-жестяницкого участка: Транспорт в настоящее время является одной из важнейших отраслей народного...
Интересное:
Аура как энергетическое поле: многослойную ауру человека можно представить себе подобным...
Наиболее распространенные виды рака: Раковая опухоль — это самостоятельное новообразование, которое может возникнуть и от повышенного давления...
Отражение на счетах бухгалтерского учета процесса приобретения: Процесс заготовления представляет систему экономических событий, включающих приобретение организацией у поставщиков сырья...
Дисциплины:
![]() |
![]() |
5.00
из
|
Заказать работу |
|
|
Получение низкоуглеродистой коррозионностойкой стали (процессы AOD и VOD)
Широкое распространение получают методы производства низкоуглеродистой коррозионностойкой стали за пределами электропечи. Метод AOD. В электропечи выплавляют основу нержавеющей стали, содержащей заданное число хрома и никеля, с использованием недорогих, высокоуглеродистых ферросплавов. Затем сталь совместно с печным шлаком заливают в конвертер. Футеровка конвертера изготовлена из магнезитохромитового кирпича. Стойкость футеровки до 200 плавок. В нижней зоне футеровки, в третьем ряду кирпичной кладки от днища конвертера. Фурмы представляют собой конструкцию из медной внутренней трубы и наружной трубы из нержавеющей стали, внутренний диаметр фурмы 12—15 мм. Начальное содержание углерода в стали может быть для ферритных хромистых сталей 2,0—2,5 %, а для аустенитных сталей 1,3—1,7 %. В первые 35 мин сталь продувают смесью кислорода и аргона в соотношении 3: 1. Во избежание перегрева металла в о, конвертер присаживают лом — этой марки стали, феррохром и т.п. Затем в течение 9 мин сталь продувают смесью кислорода и аргона в соотношении 1: 1. В это час концентрация углерода снижается до 0,18%. В третьем периоде в продувочном газе ещё больше уменьшают касательство кислорода к аргону до 1: 2, продувку продолжают ещё 15 мин. За это момент содержание углерода снижается до 0,035%. Температура повышается до 1720°С. В конце продувки присаживают известь и ферросилиций для восстановления хрома из шлака. После восстановления шлак, содержащий 1 % Cr2O3, скачивается и после этого наведения нового шлака проводят окончательную продувку аргоном. При данном в шлак переходит сера, ее содержание в металле снижается до 0,010 %. В результате процесса AOD получают высококачественную нержавеющую сталь с низким содержанием углерода, серы, азота, кислорода, сульфидных и оксидных неметаллических включений, с высокими механическими свойствами. Для повышения экономичности процесса аргон частично заменяют азотом. Средняя продолжительность продувки составляет 60—120 мин, расход аргона составляет 10—23 м^3/т, кислорода 23 м^3/т. На рис. 82 представлено трансформирование температуры и состава металла. Степень извлечения хрома составляет 98%.
|
Метод VOD. Этот приём вакуумно-кислородного обезуглероживания с продувкой аргоном. В основе способа лежит осуществление реакции [C]+[O]=CO, равновесие которой в вакууме сдвигается в правую сторону. Чем ниже парциальное давление СО, тем ниже должна быть остаточная концентрация углерода в стали. При данном создаются благоприятные условия для восстановления оксида хрома углеродом, что позволяет проводить ход обезуглероживания без заметных потерь хрома со шлаком. Коррозионностойкую сталь выплавляют в электропечи с довольно высоким содержанием углерода (0,3—0,5 %); сталь выпускают в особый ковш с хромомагнезитовой футеровкой, имеющим в днище фурму для подачи аргона. Ковш устанавливают в вакуумную камеру, откачивают воздух и начинают продувку кислородом сверху сквозь водоохлаждаемую фурму, которую вводят в камеру сквозь крышку. Одновременно производится продувка аргоном посредством дно ковша. После окончания продувки проводят присадку раскислителей и легирующих для корректировки состава. Расход аргона в данном способе немаловажно ниже чем в AOD (всего 0,2 м^3/т). Получаемая сталь содержит весьма низкие концентрации углерода (0,01 %) при низком содержании азота. Окисление хрома незначительное. Для удаления серы в ковш загружают известь, что позволяет вслед за тем раскисления и кратковременного перемешивания аргоном снизить концентрацию серы в металле до необходимых пределов. По сравнению с процессом AOD тот самый приём больше сложен и применяется для производства сталей ответственного назначения с низким содержанием углерода. К достоинствам того и иного процесса следует отнести экономию дорогого низкоуглеродистого феррохрома, просто использовавшегося при получении нержавеющей стали в дуговых печах, а кроме того достижение низких содержаний углерода без значительных потерь хрома.
|
2. Динамика трудозатрат при развитии технологического процесса производства стали.
Исходя из динамики трудозатрат,различают 2 возможных варианта развития технологического процесса – ограниченное и неограниченное. Построим график изменения живого и прошлого труда для определения варианта развития техпроцесса. Мы имеем следующие данные: Тж=1000/(3t ² + 1200) и Тп=0,002t ² + 0,8:
Таблица 2.1
t | 1 | 2 | 3 | 4 | 5 | 6 | 7 | 8 | 9 | 10 |
Тж | 0,831 | 0,825 | 0,815 | 0,801 | 0,784 | 0,765 | 0,742 | 0,718 | 0,693 | 0,667 |
Тп | 0,802 | 0,808 | 0,818 | 0,832 | 0,85 | 0,872 | 0,898 | 0,928 | 0,962 | 1 |
Тж+Тп = Тс | 1,633 | 1,633 | 1,633 | 1,633 | 1,634 | 1,637 | 1,640 | 1,646 | 1,655 | 1,667 |
Тж / Тп | 1,036 | 1,021 | 0,996 | 0,963 | 0,923 | 0,877 | 0,827 | 0,774 | 0,720 | 0,667 |
(Tж) ' = dТж / dТп | 1,036 | 1,021 | 0,996 | 0,963 | 0,923 | 0,877 | 0,827 | 0,774 | 0,720 | 0,667 |
Рис. 2.1. Ограниченная динамика трудозатрат.
С помощью графика и аналитической таблицы удается установить, что в нашем случае имеет место ограниченный вариант развития. И момент времени, до которого развитие целесообразно равен t* ≈ 3,01
В нашем техпроцессе имеет место трудосберегающий техпроцесс, потому что Тж уменьшается, а Тп – возрастает.
Установим в какой степени снижаются затраты живого труда по мере роста затрат прошлого труда,т.е. определим тип отдачи от дополнительных затрат прошлого труда и соответствующего уменьшения труда живого. Для этого найдем отношение (Тж)’=dТж/dТп.
(Данное соотношение отражено в таблице 2.1) Мы видим,что значение отношения убывает => реализуется убывающий тип отдачи дополнительных затрат овеществленного труда.
3. Уровень технологии технологического процесса.
В нашем техпроцессе мы обнаруживаем ограниченный путь развития, который называется рационалистическим. Он связан с уменьшением затрат живого труда за счет роста затрат прошлого труда. Вместе с тем живой труд уменьшается в большей степени, чем возрастет прошлый труд. Рационалистическое(эволюционное) развитие с экономической точки зрения всегда предпочтительнее, чем путь эвристического (революционного) развития технологического процесса. Это связано с дополнительными затратами на научно-исследовательские, работы при эвристическом совершенствовании технологии. Однако путь рационалистического развития принципиально ограничен.Рассчитаем параметры технологического процесса L, B, Y для момента времени t=3.
|
Воспользуемся моделью рационалистического развития техпроцесса.
L = (3.1.) где L- производительность труда; B - технологическая вооруженность; Y- уровень технологии, Y*-относительный уровень технологии.
L=1/Тж =1,2270
B=Тп/Тж =1,0037
У=(1/Тж)*(1/Тп) =1,2315
У*=У/L=1/Тп=1,2225
Это соотношение справедливо для механизированных процессов и является математической моделью закона рационалистического развития тех. процесса.
Таблица 3.1
Годы (t) | L=1/Тж | B=Тп/Тж | У=(1/Тж)*(1/Тп) | У*=У/L=1/Тп |
1 | 1,2030 | 0,9648 | 1,1607 | 1,2469 |
2 | 1,2120 | 0,9793 | 1,1869 | 1,2376 |
3 | 1,2270 | 1,0037 | 1,2315 | 1,2225 |
4 | 1,2480 | 1,0383 | 1,2958 | 1,2019 |
5 | 1,2750 | 1,0838 | 1,3818 | 1,1765 |
Очевидно, что У*>L на протяжение первых 3-х лет, отсюда следует, что рационалистическое развитие техпроцесса производства извести целесообразно до 3 года включительно. Далее оно становиться нецелесообразным
4. Структура технологического процесса.
Технологический процесс производства строительной извести состоит из следующих основных стадий, представленных на рисунке 4.1
![]() |
Рис. 4.1 Схема технологического процесса производства стали в дуговой сталеплавильной печи
Рис 4.2. Пооперационная структура технологического процесса производства стали в дуговой сталеплавильной печи:
- предметные связи; - временные связи.
ВСПОМОАТЕЛЬНЫЙ ПЕРЕХОД
![]() |
![]() ![]() ![]() ![]() ![]() ![]() |
ВСПОМОАТЕЛЬНЫЙ ПЕРЕХОД
![]() ![]() |
ПОДАЧА ВОЗДУХА В ПЕЧЬ |
ТЕХНОЛОГИЧЕСКИЙ ПЕРЕХОД
![]() |
![]() ![]() ![]() ![]() |
ВСПОМОГАТЕЛЬНЫЙ ПЕРЕХОД
![]() ![]() |
ОТВОД ГАЗОВ |
ВСПОМОГАТЕЛЬНЫЙ ПЕРЕХОД
![]() |
![]() ![]() |
|
Рис 4.3. Структура операций процесса производства извести:
- предметные связи; - временные связи.
Заключение.
1. Сталь является одним из важнейших материалов практически во всех сферах производства.
2.Дуговые электрические печи являются одними из наиболее совершенных сталеплавильных агрегатов для производства стали и сплавов.
3. Основные преимущества способа получения стали в электрических печах - возможность создания высокой температуры в плавильном пространстве печи (более 2000 'С) и выплавки стали и сплавов любого состава; использование известкового шлака (до 50...60 % СаО), способствующего хорошему очищению металла от вредных примесей - серы и фосфора; возможность ведения плавки при всех режимах и условиях производства.
4. Главным недостатком электрических печей является большой расход электроэнергии, поэтому главной задачей совершенствования является снижение элктропотребления.
5. Также необходимо улучшить допечную обработку сырья.
Список литературы:
1. М а р и н ч е н к о В. А., Электрооборудование дуговых печей трехфазного тока, Металлургиздат, 1955.
2. Электроплавильные печи черной металлургии, 3 изд., М., 1950.
Б. С. Барский.
3. Производство стали в дуговых печах, Материалы конференции, изд-во «Металлургия», 1967.
4. Линчевский Б.В., Соболевский А.Л., Кальменев А.А. (1986) Металлургия черных металлов.
5. Основы металлургического производства (черная металлургия)
Москва «Металлургия» 1988
6. В.Г. Антипин, С.З. Афонин, Л.К. Косырев "О направлении развития и структуре сталеплавильного производства", "Сталь" №3 1993 г.
7. Марочник сталей и сплавов, Машиностроение, 1989 г.
8. В. П., Дуговые вакуумные печи и электронные плавильные установки, Металлургиздат, 1962.
9. Сисоян Г. А., Электрическая дуга в электрической печи, Металлургиздат, 1961.
Производство стали в дуговых электрических печах
Выполнил
Студент
ФЭУТ, 2 курс, ДГГ Круглик П.О.
Проверил Бобрович В.А.
МИНСК 2008
Введение…………………………………………………………………………...4
1. Технологический процесс производства стали
1.1. Характеристика получаемой продукции…………………….…..…...5
1.2. Характеристика используемого сырья…………………………….... 8
1.3. Характеристика технологии производства…………………………11
2. Динамика трудозатрат………………………………………………………...22
3. Расчет уровня технологии……………………………………………………25
4. Структура технологического процесса производства стали………………………………………………………………………………26
|
5. Анализ перспективных направлений развития технологического процесса производства стали в электропечах 29
Заключение……………………………………………………………….………31
Список использованной литературы……………………………….…………..32
Работа содержит 32 страницы, 4 таблицы, 5 рисунков
Ключевые слова: технологический процесс, сталь, производство стали в дуговых электропечах, электрическая дуга, шлак, окисление, VOD,, уровень технологии, технологическая система.
В работе рассмотрен один из наиболее эффективных методов производства стали - в электрических печах. Даны расчеты характеристик технологического процесса и построены схемы данного процесса.
Введение:
В современном мире практически невозможно представить нашу жизнь без металлов. Они используются практически во всех сферах общественного производства.
Большая часть металлов присутствует в природе в виде руд и соединений. Они образуют оксиды, сульфиды, карбонаты и другие химические соединения. Для получения чистых металлов и дальнейшего их применения необходимо выделить их из руд и провести очистку. При необходимости проводят легирование и другую обработку металлов. Изучением этого занимается наука металлургия. Металлургия различает руды чёрных металлов (на основе железа) и цветных (в их состав не входит железо, всего около 70 элементов). Исключением можно назвать около 16 элементов: т. н. благородные металлы (золото, серебро и др.), и некоторые другие (например, ртуть, медь), которые присутствуют без примесей. Золото, серебро и платина относятся также к драгоценным металлам. Кроме того, в малых количествах они присутствуют в морской воде, растениях, живых организмах (играя при этом важную роль).
Сплавы железа с углеродам представляют наибольший интерес для человека. Благодаря своей плотной кристаллической структуре, углерод придает прочность сплавам железа. Эти сплавы образуют большую группу сталей и чугунов.
Сталь (польск. stal, от нем. Stahl) — деформируемый (ковкий) сплав железа с углеродом (и другими элементами), содержание углерода в котором не превышает 2,14 %, но не меньше 0,02 % Кроме углерода в ней могут содержаться примеси марганца, кремния, серы, фосфора и т.д. Сырьем для производства стали является чугун (жидкий и твердый), стальной и чугунный лом, железная руда, металлизированные окатыши, ферросплавы и т.д. Один из важнейших процессов производства стали является сталеплавильный процесс. Сталеплавильный процесс — окислительный процесс, так как сталь получается в результате окисления и удаления большей части примесей чугуна — углерода, кремния, марганца, серы и фосфора. Отличительной особенностью сталеплавильных процессов является наличие окислительной атмосферы. Окисление примесей чугуна и других шихтовых материалов осуществляется кислородом, содержащимся в газах, оксидах железа и марганца. После окисления примесей, из металлического сплава удаляют растворённый в нём кислород, вводят легирующие элементы и получают сталь заданного химического состава. В современной металлургии основными способами выплавки стали являются кислородно-конвертерный, мартеновский и электросталеплавильный процессы. В данной работе обратим внимание на электросталеплавильный процесс, а, конкретно, в дуговых электропечах.
1.Технологический процесс производства стали в дуговых электропечах и его характеристика.
1.1. Характеристика получаемой продукции-стали
Сталь (польск. stal, от нем. Stahl) — деформируемый (ковкий) сплав железа с углеродом (и другими элементами), содержание углерода в котором не превышает 2,14 %, но не меньше 0,02 % Кроме углерода в ней могут содержаться примеси марганца, кремния, серы, фосфора и т.д.
По химическому составу сталь разделяют на:
углеродистую сталь;
легированную сталь.
Углеродистая
Углеродистые стали нельзя использовать при температурах выше 250—300°С, иначе теряется их твердость, а из-за малой прокаливаемости их нельзя применять в инструментах, сечение которых больше 20—25 мм. Зато углеродистые стали нужны при производстве ручных метчиков, напильников, пил, стамесок, долот, зубил. Ведь в малых сечениях поверхностный слой стали достаточно тверд, а середина остается мягкой и вязкой, поэтому инструмент не ломается.
Лигированная
Добавление специальных примесей позволяет производить сплавы с требуемыми характеристиками — легированные стали. Они обладают повышенной прокаливаемостью, поэтому востребованы в машиностроении. Кроме того, легирующие элементы (никель, хром, медь и другие вещества) позволяют улучшить прочностные характеристики, повысить ударную вязкость и устойчивость к высоким температурам. При обозначении легированных сталей вводится буква, обозначающая легирующий элемент (кремний — С, хром — Х, азот — А), а затем идут цифры, отражающие среднее содержание элементов в процентах.
По качеству стали делятся на:
сталь обыкновенного качества;
качественная сталь;
сталь повышенного качества;
высококачественная сталь.
Сталь углеродистую обыкновенного качества подразделяют на группы:
А — поставляемую по механическим свойствам и применяемую в основном тогда, когда изделие из нее подвергается горячей обработке (напр. сварка, ковка), которая может изменить регламентируемые механические свойства (Ст0, Ст1 и прочие)
Б — поставляемую по химическому составу и применяемую дл деталей, подвергаемых такой обработке, при которой механические свойства меняютс, а их уровень определяется химическим составом (БСт0, БСт1 и др.)
В — поставляемую по механическим свойствам и химическому составу для деталей, подвергаемых сварке (ВСт1, ВСт2 и др.)
Сталь углеродистую обыкновенного качества изготовляют из следующих марок:
Ст0, Ст1кп, Ст1пс, Ст1сп, Ст2кп, Ст2пс, Ст2сп, Ст3кп, Ст3пс, Ст3сп, Ст3Гпс, Ст3Гсп, Ст4кп, Ст4пс. Ст4сп, Ст5пс, Ст5сп, Ст5Гпс. Здесь «Ст»-сталь, «0 5»-условный номер марки в зависимости от химического состава, «кп, пс, сп»-степень раскисления.
Сталь углеродистая качественная конструкционная по видам обработки в состоянии поставки делится на:
горячекатаную сталь;
кованую сталь;
круглую сталь;
калиброванную сталь;
сталь круглую со специальной отделкой поверхности (серебрянка).
Сталь легированная по степени легирования разделяют на:
низколегированную сталь (легирующих до 2,5%);
среднелегированную сталь (2,5-10%);
высоколегированную сталь (10-50%).
Сталь легированная конструкционная в зависимости от химсостава и свойств разделяют на:
качественную;
высококачественную (А);
особо высококачественную (электрошлаковый переплав).
Сталь легированная конструкционная по видам обработки в состоянии поставки делится на:
горячекатаную сталь;
кованую сталь;
калиброванную сталь;
серебрянку.
ГОСТы стали
Таблица 1.1 ГОСТы стали
Гост 19282-73 стали низколегированные толстолистовые и широкополосные
Гост 20072-75 стали теплоустойчивые
Гост 380-94 стали углеродистые обыкновенного качества
Гост 1435-74 сталь инструментальная углеродистая
Гост 1414-75 сталь конструкционная повышенной и высокой обрабатываемости
Гост 10702-78 сталь легированная для холодного выдавливания и высадки
Гост 5950-73 сталь легированная инструментальная
Гост 4543-71 сталь легированная конструкционная
Гост 801-78 сталь подшипниковая
Гост 14959-68 сталь рессорно-пружинная
Гост 1050-74 сталь углеродистая качественная конструкционная
Немагнитные стали являются заменителями цветных металлов в электромашиностроении.
Коррозионостойкие (нержавеющие) стали – это высокохромистые стали марок 1Х13, 2Х13, 3Х13 и др. (первая цифра указывает на содержание углерода в десятых долях %, остальные – содержание хрома в %). Кроме хрома, в состав сталей вводятся никель, титан, ванадий (марки 1Х13Н3, 1 Х17Н2 и др.)
Жаростойкие (окалиностойкие) стали не окисляются при действии высоких температур и небольших нагрузок. Стойкость против окисления в этих сплавах создается за счет введения хрома, алюминия, кремния. Марки: Х28, Х5, 1Х12 СЮ и др. Из них изготавливаются камеры сгорания, чехлы к термопарам, муфели.
Жаропрочные стали сохраняют прочность при высоких температурах и могут работать в этих условиях под действием больших нагрузок (детали реактивных двигателей, лопасти паровых и газовых турбин). Жаропрочные стали являются одновременно и жаростойкими. Марки жаропрочных сталей: ХН70ВМТЮ, ХН75МБТЮ и др.
Износоустойчивые стали используются для изготовления рабочих элементов землеройных машин, шаровых мельниц и других сильно изнашивающихся деталей. К ним относятся высокмарганцовистые стали марки Г13.
Существуют и другие сплавы с особыми физическими свойствами.
К группе сплавов с особыми химическими свойствами относятся высоколегированные коррозионностойкие, жаростойкие и жаропрочные стали.
|
|
История создания датчика движения: Первый прибор для обнаружения движения был изобретен немецким физиком Генрихом Герцем...
История развития пистолетов-пулеметов: Предпосылкой для возникновения пистолетов-пулеметов послужила давняя тенденция тяготения винтовок...
История развития хранилищ для нефти: Первые склады нефти появились в XVII веке. Они представляли собой землянные ямы-амбара глубиной 4…5 м...
Архитектура электронного правительства: Единая архитектура – это методологический подход при создании системы управления государства, который строится...
© cyberpedia.su 2017-2024 - Не является автором материалов. Исключительное право сохранено за автором текста.
Если вы не хотите, чтобы данный материал был у нас на сайте, перейдите по ссылке: Нарушение авторских прав. Мы поможем в написании вашей работы!