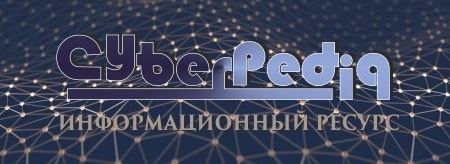
Типы сооружений для обработки осадков: Септиками называются сооружения, в которых одновременно происходят осветление сточной жидкости...
Своеобразие русской архитектуры: Основной материал – дерево – быстрота постройки, но недолговечность и необходимость деления...
Топ:
Характеристика АТП и сварочно-жестяницкого участка: Транспорт в настоящее время является одной из важнейших отраслей народного хозяйства...
Установка замедленного коксования: Чем выше температура и ниже давление, тем место разрыва углеродной цепи всё больше смещается к её концу и значительно возрастает...
История развития методов оптимизации: теорема Куна-Таккера, метод Лагранжа, роль выпуклости в оптимизации...
Интересное:
Наиболее распространенные виды рака: Раковая опухоль — это самостоятельное новообразование, которое может возникнуть и от повышенного давления...
Подходы к решению темы фильма: Существует три основных типа исторического фильма, имеющих между собой много общего...
Что нужно делать при лейкемии: Прежде всего, необходимо выяснить, не страдаете ли вы каким-либо душевным недугом...
Дисциплины:
![]() |
![]() |
5.00
из
|
Заказать работу |
|
|
Технологическая свариваемость определяется совокупностью свойств основного металла, характеризующих его реакцию на термодеформационный цикл сварки. Кроме того, она зависит от способа и режима сварки, свойств присадочного металла, применяемых флюсов, электродных покрытий и защитных газов, от конструктивных особенностей свариваемого изделия и условий его последующей эксплуатации.
Манипуляции с химическим составом, дает легированные стали универсальными и способными отображать специфические характеристики, подвергаясь подходящей термической обработки.
Используя максимальную отдачу от повышенной прочности, твердости, пластичности и ударной прочности через инновационный дизайн, можно построить более легкие конструкции со значительной экономической выгодой.
Хорошая свариваемость стали обеспечивается благодаря низкому (меньше 0,25 %) содержанию углерода. Если углерода больше, то в сварном шве могут образовываться микропоры при выгорании углерода и возникать закалочные структуры, что ухудшает качество шва. Еще одно достоинство этой марки состоит в том, что сталь 09Г2С не склонна к отпускной хрупкости, то есть ее вязкость не снижается после процедуры отпуска. Она также устойчива к перегреву и образованию трещин.
При сварке листов 09Г2С, толщина которых не превышает 40 мм, применяют способ без разделки кромок. Прочность по всей длине сварного шва обеспечивается переходом легирующих элементов в металл шва из электрода. При многослойной сварке лучше применять каскадный метод с использованием токов 40-50 А на 1 мм электрода, для предупреждения перегрева стали. Рекомендуемая толщина электрода – 4-5 мм. При сварке более толстых листов лучше использовать многослойную сварку с небольшими временными промежутками перед наложением следующих слоев. При дуговой сварке кромок с разной толщиной большую часть дуги нужно направлять на более толстую кромку и параметры тока выбирать по ней же. Для того, чтобы устранить закалку и повысить твердость шва следует нагреть изделие до 650 С, выдержать при этой температуре (время выдержки зависит от толщины материала, в среднем дается 1 час на каждые 25 мм толщины). После этой процедуры изделие нужно охладить на воздухе или в горячей воде.
|
Широкое распространение и популярность стали 09Г2С объясняется тем, что ее высокие механические свойства позволяют экономить при изготовлении строительных конструкций. Более того, такие конструкции имеют меньший вес. Области применения этой марки стали весьма разнообразны. Из нее изготавливаются элементы и детали сварных металлических конструкций, которые могут работать при температурах от -70 С до +450 С. Используется 09Г2С лист и для производства листовых конструкций в нефтяной и химической промышленности, судостроении и машиностроении. После закалки и отпуска из этого сплава можно изготавливать детали трубопроводной арматуры. Устойчивость к низким температурам позволяет применять трубу 09Г2С в условиях крайнего севера для прокладки нефти – и газопроводов.
Сталь 09Г2С, характеристики которой значительно отличаются от аналогов малым содержанием углерода и присадок подходит под сварку любыми электродами, предусмотренными для низколегированных металлов. Стали этого класса применяются для:
- изготовления паровых, отопительных котлов;
- изготовления емкостей, ресиверов, работающих в условиях высоких;
- температур и давления;
- производства сложных сварных конструкций, практически, во всех отраслях и сферах жизнедеятельности.
Помимо листовой стали, труб и других профильных изделий, сталь выпускается в виде проката:
- квадратный, размером 63 – 200 мм;
|
- круглый, размером 28 – 180 мм;
- полосовой, толщиной 12 – 50 и шириной 40-160 мм.
Способ сварки изделия
Сварка – это процесс получения неразъемных соединений материалов путем создания межатомных связей при их местном или пластическом деформировании. С помощью нее в основном соединяют металлы и сплавы, как однородные, так и разные по составу.
Наиболее распространенными типами производства изделия:
- ручная дуговая сварка;
- сварка под флюсом;
- сварка в защитных газах;
- электронно-лучевая сварка.
При ручной дуговой сварке покрытыми металлическими электродами, сварочная дуга горит с электрода на изделие, оплавляя кромки свариваемого изделия и расплавляя металл электродного стержня и покрытие электрода (рисунок 2).
Рисунок 2 – Схема сварки покрытым металлическим электродом
Кристаллизация основного металла и металла электродного стержня образует сварной шов.
Электрод состоит из электродного стержня и электродного покрытия. Электродный стержень – сварочная проволока; электродное покрытие – многокомпонентная смесь металлов и их оксидов.
По функциональным признакам компоненты электродного покрытия разделяют:
Газообразующие:
- защитный газ;
- ионизирующий газ.
Шлакообразующие:
- для физической изоляции расплавленного металла от активных газов атмосферного воздуха;
- раскислители;
- рафинирующие элементы;
- легирующие элементы;
- связующие;
- пластификаторы.
Перед зажиганием (возбуждением) дуги следует установить необходимую силу сварочного тока, которая зависит от марки электрода, типа сварного соединения, положения шва в пространстве и др.
Зажигание (возбуждение) производиться двумя способами. При первом способе электрод подводят перпендикулярно к месту начала сварки и после сравнительно легкого прикосновения к изделию отводят верх на расстояние 25 мм. Второй способ напоминает процесс, зажигая спички. При обрыве дуги повторное зажигание ее осуществляется впереди кратера на основном металле с возвратом к наплавленному металлу для вывода на поверхность загрязнений, скопившихся в кратере. После этого сварку ведут в нужном направлении.
Применение того или иного способа зажигания дуги зависит от условий сварки и от навыка сварщика.
Положение электрода зависит от положения шва в пространстве. Различают следующие положения швов: нижнее, вертикальное и горизонтальное на вертикальной плоскости, потолочное. Сварку вертикальных швов можно выполнять сверху вниз и снизу вверх.
|
При сварке в нижнем положении электрод имеет наклон от вертикали в сторону направления сварки. Перемещение электрода при сварке может осуществляться способами к себе и от себя.
Достоинства способа:
- простота оборудования;
- возможность сварки во всех пространственных положениях;
- возможность сварки в труднодоступных местах;
- быстрый, по времени переход от одного вида материала к другому;
- большая номенклатура свариваемых металлов.
Недостатки способа:
- большие материальные и временные затраты на подготовку сварщика;
- качество сварного соединения и его свойства во многом определяются субъективным фактором;
- низкая производительность (пропорциональна сварочному току, увеличение сварочного тока приводит к разрушению электродного покрытия);
- вредные и тяжёлые условия труда.
Рациональные области применения:
- сварка на монтаже;
- сварка непротяжённых швов;
- шлаковая и др.
Сварка под флюсом.
При автоматической дуговой сварке под флюсом электрическая дуга горит под слоем флюса между концом сварочной проволоки и свариваемым металлом.
Схема процесса сварки под флюсом показана на рисунке 3.
Рисунок 3 – Схема сварки под флюсом
Ролики механизма автоматически вытягивают электродную проволоку в дугу. Сварочный ток, переменный или постоянный, прямой или обратной полярности подводится к электродной проволоке, а другим контактом к изделию.
Сварочная дуга горит в газовом облаке, образованном в результате плавления и испарения флюса и металла. При гашении электрической дуги расплавленный флюс, остывая, образует шлаковую корку, которая отделяется от поверхности шва. Флюс засыпается перед дугой из бункера слоем толщиной 40 – 80 и шириной 40 – 100 мм. Количество флюса, идущего, в шлаковую корку, равно массе расплавленной сварочной проволоки. Не расплавившаяся часть флюса отсасывается пневмоотсосом в бункер и используется вновь.
Потери металла на угар и разбрызгивание при горении дуги под флюсом меньше, чем при ручной дуговой и сварке в защитных газах. Расплавленные электродный и основной металлы перемешиваются в сварочной ванне. Кристаллизуясь, они образуют сварной шов.
|
В промышленности используется сварка проволочными электродами - сварочной проволокой. Иногда сварку проводят ленточными, толщиной до 2 мм и шириной до 40 мм, или комбинированными электродами. Дуга, перемещаясь от одного края ленты к другому, равномерно оплавляет её торец и расплавляет основной металл. Изменяя форму ленты, можно изменить и форму поперечного сечения шва, достигая необходимого проплавления металла или получая равномерную глубину проплавления по всему сечению шва.
При сварке флюс насыпается слоем толщиной 50 – 60 мм; дуга утапливается в массе флюса и горит в жидкой среде расплавленного флюса, в газовом пузыре, образуемом газами и парами, непрерывно создаваемыми дугой. При среднем насыпном весе флюса около 1,5 г/см3 давление слоя флюса на жидкий металл составляет 7 – 9 г/см2. Этого давления достаточно для устранения механических воздействий дуги на ванну жидкого металла, приводящего к разбрызгиванию жидкого металла, нарушению формирования шва даже при очень больших токах.
Для электрической дуги, горящей без флюса нельзя проводить сварку при силе тока выше 500 – 600. А из-за разбрызгивания металла и нарушения формирования шва. Дуга же во флюсе позволяет увеличить токи в до 3000-4000 А с сохранением качества сварки и правильным формированием шва.
В качестве флюсов при сварке применяют искусственные силикаты имеющие слабо кислый характер. Основой флюса являются двойной или тройной силикат закиси марганца, окиси кальция, окиси магния, алюминия и т. д. В качестве добавки, снижающей температуру плавления и вязкость, применяется плавиковый шпат.
Недостатки сварки под флюсом:
- велики трудозатраты, связанные со стоимостью флюса;
- трудности корректировки положения дуги относительно кромок свариваемого изделия;
- экологическое воздействие газов на оператора;
- невидимость места сварки, расположенного под толстым слоем флюса;
- нет возможности выполнять сварку во всех пространственных положениях без специального оборудования;
- повышенная жидко текучесть расплавленного металла и флюса;
- требуется тщательная сборка кромок под сварку;
- при увеличенном зазоре между кромками возможно вытекание в него расплавленного металла и флюса и образование в шве дефектов.
Преимущества сварки под флюсом:
- повышенная производительность;
- минимальные потери электродного металла;
- отсутствие брызг;
- максимально надёжная защита зоны сварки;
- минимальная чувствительность к образованию оксидов;
|
- не требуется защитных приспособлений от светового излучения, так как дуга горит под слоем флюса;
- низкая скорость охлаждения металла обеспечивает высокие показатели механических свойств металла шва.
Дуговая сварка в защитных газах - при сварке в зону дуги через сопло горелки подается защитный газ. Электрическая дуга расплавляет основной металл и электродную проволоку или электрод. Расплавленный металл сварочной ванны, кристаллизуясь, образует шов. При сварке неплавящимся электродом электрод не расплавляется. Защитный газ препятствует взаимодействию расплавленного металла с газами воздуха.
Схема процесса сварки в защитных газах представлена на рисунке 4.
Рисунок 4 – Схема сварки в защитных газах
Дуговая сварка в защитных газах разделяется по виду используемых газов на сварку:
- сварку в инертных газах;
- сварку в активных газах;
- сварку с смеси инертных и активных газах;
- сварку со струйной защитой.
По виду дуги дуговая сварка в защитных газах разделяется на:
- сварка постоянной дугой;
- сварка импульсной дугой.
Инертные газы применяются при сварке химически активных металлов (титан, цирконий, молибден, тантал, ниобий и др.), активные газы используют, когда свойства металла обеспечивается металлургической обработкой. Газовые смеси повышают устойчивость дуги, улучшают форму шва, уменьшают разбрызгивание металла.
В зависимости от электродов— сварка плавящимся или неплавящимся (вольфрамовым) электродом. Для сварки неплавящимся электродом используются в основном инертные газы — аргон и гелий или их смеси. Защитные газы оказывают влияние на свойства дуги и форму швов.
В качестве защитных газов применяют инертные (аргон и гелий), активные (углекислый газ, водород, кислород и азот) газы, а также их смеси (Аг + Не, Аг + СО2, Аг + О2, СО2 + О2 и др.).
Недостатки:
К недостаткам способа по сравнению со сваркой под флюсом относится необходимость применения защитных мер против световой и тепловой радиации дуги, использование защитных газов.
Преимущества:
- высокое качество соединения при работе с разными металлами и сплавами вне зависимости от пространственного положения детали;
- широкий диапазон толщин свариваемого металла— от десятой доли до нескольких десятков миллиметров;
- возможность визуального контроля сварочной дуги и ванной, процесса образования сварочного шва;
- узкая зона термического воздействия;
- при многослойной сварке не надо зачищать швы;
- высокая производительность работ;
- не надо удалять флюс или шлак, зачищать швы.
Электронно-лучевая сварка (ЭЛС).
Сущность процесса состоит в использовании кинетической энергии потока электронов, движущихся с высокими скоростями в вакууме. Для уменьшения потери кинетической энергии электронов за счет соударения с молекулами газов воздуха, а также для химической и тепловой защиты катода в электронной пушке создают вакуум порядка 10-4... 10-6 мм рт. ст.
Техника сварки.
Плавление металла происходит на передней стенке кратера, а расплавляемый металл перемещается по боковым стенкам к задней стенке, где он и кристаллизуется. При сварке электронным лучом проплавление имеет форму конуса (рисунок 5).
1 - электронный луч; 2 - передняя стенка кратера;
3 - зона кристаллизации; 4 - путь движения жидкого металла
Рисунок 5 – Сварка электронным лучом
Проплавление при электронно-лучевой сварке обусловлено в основном давлением потока электронов, характером выделения теплоты в объеме твердого металла и реактивным давлением испаряющегося металла, вторичных и тепловых электронов и излучением. Возможна сварка непрерывным электронным лучом. Однако при сварке легкоиспаряющихся металлов (алюминия, магния и др.) эффективность электронного потока и количество выделяющейся в изделии теплоты уменьшаются вследствие потери энергии на ионизацию паров металлов. В этом случае целесообразно сварку вести импульсным электронным лучом с большой плотностью энергии и частотой импульсов 100... 500 Гц. В результате повышается глубина проплавления. При правильной установке соотношения времени паузы и импульса можно сваривать очень тонкие листы. Благодаря теплоотводу во время пауз уменьшается протяженность зоны термического влияния. Однако при этом возможно образование подрезов, которые могут быть устранены сваркой колеблющимся или расфокусированным лучом.
Основные параметры режима электронно-лучевой сварки:
- сила тока в луче;
- ускоряющее напряжение;
- скорость перемещения луча по поверхности изделия;
- продолжительность импульсов и пауз;
- точность фокусировки луча;
- степень вакуумизации.
Основные типы сварных соединений, рекомендуемые для электронно-лучевой сварки, приведены на рисунке 6.
а - стыковое (может быть с бортиком для получения выпуклости шва); б - замковое; в - стыковое деталей разной толщины; г - угловые; д и е - стыковые при сварке шестерен; ж - стыковые с отбортовкой кромок
Рисунок 6 – Основные типы сварных соединений при ЭЛС
Перед сваркой требуется точная сборка деталей (при толщине металла до 5 мм зазор не более 0,07 мм, при толщине до 20 мм зазор до 0,1 мм) и точное направление луча по оси стыка (отклонение не больше 0,2... 0,3 мм).
При увеличенных зазорах (для предупреждения подрезов) требуется дополнительный металл в виде технологических буртиков или присадочной проволоки. В последнем случае появляется возможность металлургического воздействия на металл шва. Изменяя зазор и количество дополнительного металла, можно довести долю присадочного металла в шве до 50 %.
Преимущества:
- высокая концентрация ввода теплоты в изделие, которая выделяется не только на поверхности изделия, но и на некоторой глубине в объеме основного металла;
- фокусировкой электронного луча можно получить пятно нагрева диаметром 0,0002... 5 мм, что позволяет за один проход сваривать металлы толщиной от десятых долей миллиметра до 200 мм.
- появляется возможность сварки тугоплавких металлов (вольфрама, тантала и др.), керамики и т.д.;
- уменьшение протяженности зоны термического влияния снижает вероятность рекристаллизации основного металла в этой зоне;
- малое количество вводимой теплоты;
- отсутствие насыщения расплавленного и нагретого металла газами.
Недостатки электронно- лучевой сварки:
- возможность образования не сплавлении и полостей в корне шва на металлах с большой теплопроводностью и швах с большим отношением глубины к ширине;
- для создания вакуума в рабочей камере после загрузки изделий требуется длительное время.
В результате проделанного анализа, для сварки продольного шва корпуса фильтра выберем сварку в защитных газах в среде СО2.
|
|
Наброски и зарисовки растений, плодов, цветов: Освоить конструктивное построение структуры дерева через зарисовки отдельных деревьев, группы деревьев...
Таксономические единицы (категории) растений: Каждая система классификации состоит из определённых соподчиненных друг другу...
Типы оградительных сооружений в морском порту: По расположению оградительных сооружений в плане различают волноломы, обе оконечности...
Поперечные профили набережных и береговой полосы: На городских территориях берегоукрепление проектируют с учетом технических и экономических требований, но особое значение придают эстетическим...
© cyberpedia.su 2017-2024 - Не является автором материалов. Исключительное право сохранено за автором текста.
Если вы не хотите, чтобы данный материал был у нас на сайте, перейдите по ссылке: Нарушение авторских прав. Мы поможем в написании вашей работы!