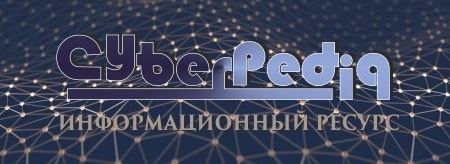
Двойное оплодотворение у цветковых растений: Оплодотворение - это процесс слияния мужской и женской половых клеток с образованием зиготы...
Индивидуальные и групповые автопоилки: для животных. Схемы и конструкции...
Топ:
Устройство и оснащение процедурного кабинета: Решающая роль в обеспечении правильного лечения пациентов отводится процедурной медсестре...
Выпускная квалификационная работа: Основная часть ВКР, как правило, состоит из двух-трех глав, каждая из которых, в свою очередь...
Методика измерений сопротивления растеканию тока анодного заземления: Анодный заземлитель (анод) – проводник, погруженный в электролитическую среду (грунт, раствор электролита) и подключенный к положительному...
Интересное:
Средства для ингаляционного наркоза: Наркоз наступает в результате вдыхания (ингаляции) средств, которое осуществляют или с помощью маски...
Влияние предпринимательской среды на эффективное функционирование предприятия: Предпринимательская среда – это совокупность внешних и внутренних факторов, оказывающих влияние на функционирование фирмы...
Наиболее распространенные виды рака: Раковая опухоль — это самостоятельное новообразование, которое может возникнуть и от повышенного давления...
Дисциплины:
![]() |
![]() |
5.00
из
|
Заказать работу |
|
|
УрФУ имени первого президента Российской Федерации Б.Н.Ельцина
Литые заготовки
Екатеринбург 2016
УДК 621.7.001.2(075.8)
Составитель: С.И. Фоминых
Научный редактор: доц., канд. техн. наук. М.Д. Харчук
ЛИТЫЕ ЗАГОТОВКИ: Методические указания и контрольные задания по дисциплине «Производство и механическая обработка заготовок» / С.И. Фоминых. Екатеринбург: УрФУ, 2016. 88 с.
Данная работа содержит методические указания по выполнению практической работы. Основой содержания работы является выбор и обоснование рационального способа производства литой заготовки, снижающего трудоемкость механической обработки, а также разработка ее рабочего чертежа, включающая назначение напусков, расчет припусков на механическую обработку и обеспечивающая технологичность конструкции изделия.
Библиогр.: 31 назв. Табл. 21. Прил. 2.
Подготовлено кафедрой «Технология машиностроения»
© УрФУ, 2016.
ОБЩИЕ ПОЛОЖЕНИЯ
Цель практической работы – овладеть основами конструирования исходных заготовок, выбором рационального способа ихполучения, обеспечивающего минимальный объем механической обработки, низкую материалоемкость и себестоимость производства заготовок.
В процессе выполнения практической работы студенты обосновывают выбор способа производства, определяют показатели точности и качества поверхности, припуски и допуски на механическую обработку отливок, технологических напусков и оформляют чертеж заготовки с учетом других требований технологии литья; разрабатывают маршрутную схему технологического процесса производства заготовки и обработки детали.
|
Задания на выполнение практической работы выдаются каждому студенту индивидуально. Задание, варианты контрольных заданий с чертежами деталей даны в прил.1 и 2. Допускается по согласованию с преподавателем использование других чертежей.
При выполнением практической работы проводится анализ технологичности конструкции детали по следующим основным направлениям:
1. Выбор материала должен соответствовать назначению и условиям работы детали. Рассмотреть возможность замены материала на более дешевый и технологичный материал. По возможности использовать новые прогрессивные материалы, например, сплавы, менее легированные никелем, хромом, вольфрамом и другими элементами, чугуны, алюминиевые сплавы, биметаллы.
2. По возможности сократить трудоемкость механической обработки.
Рассмотреть требования к точности и шероховатости поверхностей. Целесообразность назначения протяженности точно и чисто обработанных поверхностей, возможность сокращения их размеров и обработки нескольких поверхностей на проход без перестановки режущего инструмента. Возможность изменения конструктивных элементов детали с целью упрощения геометрических форм, обеспечение свободного доступа инструмента к обрабатываемым поверхностям, удобство врезания и выхода инструмента.
3.Стандартизация и унификация элементов конструкции детали. Отверстия, резьбы, толщина стенок, ребер и перемычек, уклоны должны быть по возможности однотипными. Число значений радиусов закруглений и переходов, применяемых в одной детали, должно быть минимальным и взято из ряда предпочтительных размеров по ГОСТ. Унификация элементов конструкции детали приводит к сокращению номенклатуры режущего и мерительного инструмента при механической обработке и снижению трудоемкости изготовления технологической оснастки.
МЕТОДИЧЕСКИЕ УКАЗАНИЯ ПО ВЫПОЛНЕНИЮ ПРАКТИЧЕСКОЙ РАБОТЫ
|
Выбор и обоснование способа производства заготовок
Тип производства.
Серийность выпуска деталей - один из главных показателей при выборе способа производства заготовок. По серийности различают следующие типы производства: единичное, мелкосерийное, серийное, крупносерийное и массовое. Для определения типа производства отливок из черных сплавов можно использовать данные по объему выпуска деталей и их массе (табл.1).
Специальные способы получения заготовок, требующие дорогой и сложной оснастки и специального оборудования, обычно рентабельны в серийном и массовом производстве. Минимальный размер партии литых заготовок, для которых целесообразно использование специальных способов литья, приведен в табл. 2.
Таблица 1
Определение типа производства
Масса детали, кг | Годовое число отливок одного наименования, шт. Производство | ||||
единичное | мелко-серийное | серийное | крупно-серийное | массовое | |
менее 1 | до 700 | 701-8000 | 8001-40000 | 40001-250000 | 250001 |
1-8 | 500 | 501-6000 | 6001-30000 | 30001-200000 | 200001 |
8-20 | 300 | 301-3000 | 3001-15000 | 15001-100000 | 100001 |
20-50 | 200 | 201-2500 | 2501-10000 | 10001-60000 | 60001 |
50-100 | 150 | 151-2000 | 2001-8700 | 8701-53000 | 53001 |
100-250 | 95 | 96-1400 | 1401-7000 | 7001-37500 | 37501 |
250-500 | 75 | 76-1000 | 1001-4500 | 4501-25000 | 25001 |
500-1000 | 50 | 51-600 | 601-3000 | 3001-20000 | 20001 |
1000-2000 | 40 | 41-400 | 401-2000 | 2001-13500 | 13501 |
2000-5000 | 20 | 21-150 | 151-550 | 551-4500 | ≥4501 |
Таблица 2
Минимальный размер партии литых заготовок, для которых целесообразно использование специальных способов литья
Масса детали, кг | Способ литья | |||
в оболочковые формы | в кокиль, центробежное | под давлением | по выплавляемым моделям | |
До 0,063 0,063 – 0,16 0,16 – 0,25 0,25 – 0,63 0,63 – 1,0 1,0 – 1,6 1,6 – 2,5 2,5 – 4,0 4,0 – 10,0 | 280 280 280 140 100 80 65 50 30 | 1700 1700 1700 900 700 520 415 330 225 | 26000 16500 12500 9000 7000 5500 4500 3700 2500 | 30000 20000 16000 12000 9300 7700 6500 5400 4000 |
Во многих случаях при использовании групповых методов изготовления заготовок оказывается эффективно применение специальных способов литья и в мелкосерийном производстве.
Ниже приводится краткая характеристика способов изготовления литых заготовок в зависимости от типа производства. Более подробные данные приведены в литературе [1, 2, 4, 6, 10–13, 15–21, 23, 24, 26].
До 80 % всех отливок в настоящее время изготовляется литьем в песчано-глинистые формы. Литье в песчано-глинистые формы –универсальный технологический процесс, который применяется в единичном и мелкосерийном производстве при ручной формовке по деревянным моделям, при механизированном изготовлении стержней, машинной формовке по металлическим моделям является экономичным вариантом изготовления сложных отливок в крупносерийном и массовом производстве.
|
Специальные способы литья, как правило, значительно повышают стоимость отливок, но позволяют повысить точность и качество поверхностей отливки, уменьшить припуски, снизить объем механической обработки.
Литье в кокиль – способ, применяемый в серийном производстве, а при использовании специальных многопозиционных машин – в крупносерийном и массовом производстве. Этим способом эффективно отливать отливки из цветных сплавов, чугуна и реже стали. При наличии сложных внутренних полостей применяют песчаные стержни. Применение литья в кокиль ограничивается из-за неподатливости металлической формы и, как следствие, затруднения усадки отливок.
Литье под давлением является наиболее совершенным методом получения сложных, тонкостенных, точных отливок в крупносерийном, массовом производстве, главным образом, из цветных металлов и пластмасс. Возможность армирования отливок из алюминиевых, цинковых, медных сплавов и пластмасс недефицитными сталями значительно расширяет возможности и эффективность данного способа литья. При групповом методе получения заготовок снижаются затраты на изготовление пресс-форм и способ литья под давлением становится рентабельным при производстве партий отливок от 3 до 5 тыс. шт. в зависимости от массы и сложности литья. Применение литья под давлением ограничивается высокой стоимостью прессформ, наличием в отливках воздушной пористости, а также невозможностью использования песчаных стержней.
Центробежный способ литья применяется в серийном и массовом производстве для получения отливок, имеющих в основном форму тел вращения (трубы, гильзы, втулки). Полые отливки могут изготавливаться без стержней, что упрощает и удешевляет процесс их производства.
Литье в оболочковые формы применяется в крупносерийном и массовом производстве деталей мелких и средних размеров и позволяет в 1,5 – 2 раза снизить трудоемкость механической обработки и уменьшить расход формовочных материалов в литейных цехах. Оболочковые формы целесообразно использовать для производства отливок массой до 80 кг. Более крупные отливки получаются с меньшей точностью размеров из-за коробления оболочек.
|
Литье по выплавляемым моделям эффективно в крупносерийном производстве. Этим способом можно отливать любые черные и цветные сплавы, в том числе высокопрочные, жаростойкие сплавы. Наиболее часто этот способ применяют для изготовления стальных мелких (до 1,5 кг) и сложных по геометрии деталей с большим объемом обработки резанием. Рационально также использование данного способа литья для сложных деталей, собираемых из нескольких механически обработанных частей и соединяемых с помощью пайки, винтов, сварки.
Требования к точности и шероховатости поверхности
Точность отливки характеризуют степенью ее приближения к готовой детали. Чем выше точность детали, тем больше переходов требуется выполнить при механической обработке отливки. Различают геометрическую и весовую точность отливок.
Геометрическая точность отливок определяется точностью размеров, формы, расположения поверхностей, шероховатостью и волнистостью поверхности и зависит от усадки материала, вида размера (верх, низ, бок), расположения установочных баз, точности оснастки и способа изготовления.
Геометрическая точность отливок, получаемых в песчано-глинистых формах по деревянным и металлическим моделям, при ручной и машинной формовке соответствует 14-18 квалитету, шероховатость Rz = 400 -160 мкм.
Специальные способы литья обеспечивают получение более точных отливок с точностью и шероховатостью, приближенными к готовой детали, что снижает, а в некоторых случаях исключает механическую обработку отдельных поверхностей детали. В табл. 4 приведены данные по точности и шероховатости заготовок, получаемых специальными способами литья.
Точность и шероховатость поверхности отливок зависит от вида материала и качества формы. Для отливок из цветных сплавов принимаются минимальные значения, для стального литья максимальные.
Таблица 4
Точность и шероховатость отливок
Способ литья | Квалитет (ГОСТ25347-82) | Параметр шероховатости, Rz, мкм. |
В кокиль | 13–16 | 80–20 |
Центробежное | 15–17 | 180–20 |
В оболочковые формы | 13–16 | 160–20 |
По выплавляемым моделям | I2–14 | 20–10 |
Под давлением | 11–14 | 40–2,5 |
Поверхность
Таблица 6
|
Минимальная толщина стенок отливки (мм) при литье в песчано-глинистые формы
Материал
Таблица 7
Минимальная толщина стенок отливки (мм) при литье под давлением
Материал
Площадь поверхности стенки, см2
ощадь поверхности
етенки, см2
Таблица 8
Минимальная толщина стенок отливки (мм) при литье по выплавляемым моделям и в оболочковые формы
Способ литья | Материал | ||||
Сталь | Чугун | Алюминиевые сплавы | Бронзы | Цинковые сплавы | |
по выплавляемым моделям, с толщиной стенки, мм: 25-100 100-400 Св. 400 | |||||
2,0 | 1,0-1,5 | 2,0 | 2,0 | 1-1,5 | |
2,5 | 2,0 | 2,5 | 2,5 | 2,0 | |
4,0 | 3,5 | 3,5 | 3.5 | 3,0 | |
в оболочковые формы с толщиной стенки, мм: 25-100 100-900 | |||||
2,5-4,0 | 2,5-3,5 | 2,5-4,0 | 3,0 | 2,0-3,0 | |
4,0-8,0 | 3,5-5,0 | 4,0-7,0 | 3.0-4,0 | 3.0-4,0 |
При проектировании литых деталей необходимо избегать острых углов. Стенки детали сопрягаются плавными радиусами закруглений и переходов. Наименьшие значения радиусов закруглений для отливок, отливаемых в песчано-глинистые формы, определяются из соотношений толщин сопрягаемых стенок отливок.
При равной толщине стенок:
· внутренний радиус: r = a / 2,
где, a – толщина стенки отливки, мм.
· Наружный радиус: R = a + r.
При различных толщина сопрягаемых стенок:
· внутренний радиус r = (a + b) /4,
· наружный радиус R = r + (a + b) / 2.
Для отливок, отливаемых литьем под давлением и в кокиль, величины радиусов закруглений могут быть определены из соотношений:
при равной толщине стенок:
· внутренний радиус r = a / 3,
· наружный радиус R = a + r;
при разных толщинах:
· внутренний радиус r = (a + b) / 6,
· наружный радиус R = r + (a + b) / 2.
Количество разных значений радиусов закруглений, применяемых в одной отливке, должно быть минимальным и они берутся из ряда предпочтительных размеров.
Таблица 9
Минимальные размеры и глубина отливаемых отверстий
Способ литья | Материал | |||||
Сталь | Чугун | Алюминиевые сплавы | Цинковые сплавы | Медные сплавы | Пластмассы | |
в кокиль: | ||||||
dmin, мм | 20 -40 | 10-20 | 8-12 | 6-8* | 10-14 | - |
глубина отверстия: глухого | 1,5 dmin | 1,5 dmin | 2 dmin | 2 dmin | 1,5 dmin | - |
сквозного | 2 dmin | 3 dmin | 3 dmin | 3 dmin | 2 dmin | - |
под давлением: | ||||||
dmin, мм | - | - | 1,5-2 | 1-1,5 | 2,5-5 | 1-3 |
глубина отверстия: глухого | - | - | 3 dmin | 3 dmin | 3 dmin | 1,2 dmin |
сквозного | - | - | 4 dmin | 6 dmin | 4 dmin | 2,5 dmin |
по выплавляемым моделям: | ||||||
dmin, мм | 3 | 2,5 | 2 | - | 4-7 | - |
глубина отверстия: глухого | - | - | 1,5 dmin | - | - | - |
сквозного | 2 dmin | 2 dmin | 2 dmin | - | 2 dmin | - |
в оболочковые формы: | ||||||
dmin, мм | 10 | 8 | 6 | - | - | - |
глубина отверстия: глухого | 2 dmin | 3 dmin | 5 dmin | - | - | - |
сквозного | 3 dmin | 4 dmin | 6 dmin | - | - | - |
*) набольшие значения диаметров отверстий принимаются для крупных отливок;
**) dmin – минимальный диаметр отливаемых отверстий.
Оформление чертежа отливки
Чертеж отливки выполняется в соответствии с требованиями стандартов ЕСКД [8].
На чертеже литой заготовки указывают:
– марку материала;
– массу;
– плоскость разъема формы
– шероховатость поверхности.
Чертеж отливки должен содержать технические требования, в которых отмечают:
– точность отливки, например: 8–5–10–8 см. 0,8, ГОСТ Р 53464–2009 (8 – класс размерной точности; 5 – степень коробления; 10 – степень точности поверхности; 8 – класс точности массы; допуск смещения – 0,8 мм);
– неуказанные литейные радиусы, формовочные уклоны;
– вид термообработки, твердость;
– вид контроля, требования к качеству отливок;
– величину усадки;
– уклоны;
– маркировку;
– размеры для справок.
Чертеж отливки выполняется толстыми сплошными линиями, а чертеж детали изображается тонкими сплошными линиями. На чертеже отливки дополнительно наносятся следующие данные:
– припуски на механическую обработку сплошной тонкой линией (рекомендуется красным цветом) с простановкой их числового значения;
– технологические базы, дополнительные опоры и зажимы для первой операции механической обработки указываются условным обозначением по ГОСТ 3.1107-83;
– плоскость разъема модели (формы) тонкой линией с обозначением верха и низа формы;
– стержни со стержневыми знаками условным обозначением поверхности стержней, а литниковая система, прибыли и выпоры – тонкой штрихпунктирной линией (ГОСТ 3.1125-88);
– внутренние контуры обрабатываемых поверхностей, отверстия малого диаметра, пазы, уступы, небольшой высоты, «закрываемые» в отливке или имеющие технологические напуски, перекрестной штриховкой.
По ГОСТ Р 53464–2009.
ПРИМЕРЫ ОПРЕДЕЛЕНИЯ ПАРАМЕТРОВ ОТЛИВКИ ПО ГОСТ Р 53464–2009
Пример 1- тело вращения. Деталь «Ступица»
1. Выбор баз механической обработки
На чертеже заготовки должны присутствовать базы черновой обработки. К сожалению, часто такая информация на чертежах отливок отсутствует, хотя без нее припуски на механическую обработку по ГОСТ Р 53464–2009 назначить правильно нельзя.
При выборе баз механической обработки предлагается использовать методику, изложенную в работе [6]. На чертеже детали буквами помечают поверхности, на которые необходимо назначить припуски на обработку. Базы механической обработки следует определять отдельно для плоских поверхностей и для поверхностей вращения. Определение баз механической обработки плоских поверхностей (на рис. П2.1. поверхности А, В, Е) выполняют в следующем порядке.
Во-первых, на чертеже детали находят конструкторскую базу (для плоских поверхностей). Конструкторская база — это поверхность, относительно которой изделие базируется в узле.
Признаки конструкторской базы: такая поверхность на чертеже детали координирована с другими поверхностями большим числом размерных связей; для данной поверхности указаны более высокие требования к точности размеров, выходящих на нее, к допускам формы и чистоте поверхности (поверхность фланца В).
Во - вторых, определяют поверхность, которую можно использовать в качестве черновой базы для назначения припуска на поверхность, обозначенную конструкторской базой. Выбор поверхности проводят из числа поверхностей, координированных с конструкторской базой размерными связями в порядке возрастания их номинальных размеров. На выбранную поверхность ставят знак базы – V1. в рассматриваемом на рис. П2.1. случае это противоположная поверхность фланца В.
В-третьих, принимают в качестве базы механическойобработки конструкторскую базу (поверхность В), при этомследует также поставить знак VII.
Рис. П2.1. Выбор баз механической обработки на чертеже детали:
А, В, С, D, E – обрабатываемые поверхности; Ст – стержень;
ВБ – встречный болван
Наконец, проверяют, все ли поверхности можно обработать относительно найденных баз. Если имеется поверхность, которую нельзя обработать от найденных баз, то для нее определяют базу механической обработки из числа поверхностей, координированных с ней размерными связями в порядке возрастания их номинальных размеров, и ставят знак VIII (в нашем случае для внутренней поверхности, координированной размером 172 мм, выбираем в качестве третьей базы поверхность Е, которая обозначается также знаком VIII).
Аналогично находят черновые базы VIbp и VIIBp для поверхностей вращения (на рис. П2.1. поверхности D, С).
2. Определение допусков и припусков на механическую обработку
После выбора плоскости разъема и решения вопроса о формировании внутренних и внешних поверхностей необходимо выполнить определение допусков и припусков на механическую обработку по ГОСТ Р 53464–2009. Ниже на примере детали ступицы заднего колеса автомобиля марки ЗИЛ-130 (рис. П.2.2, а) приведен расчет допусков и припусков на обработку. Исходные данные: материал - КЧ35-10, наибольший габаритный размер 326 мм, масса 22 кг, сложность отливки - средняя, термическая обработка – графитизирующий отжиг, способ литья - в сырые песчано-глинистые формы из смеси с влажностью 3,5-4,5%, прочностью 0,06...0,12 Н/мм2 и твердостью не ниже 70 ед. Уровень механизации – машинное поточно-механизированное производство, культура производства – средняя. Технический уровень технологии механической обработки по ГОСТ Р 53464–2009.
Рис. П2.2. Чертеж детали (а) и отливки (б) ступицы заднего колеса:
МФ – разъем модели и формы; А, В, С, D, E – обрабатываемые поверхности
Назначение точностных параметров отливки и соответствующих им допусков и припусков следует проводить в следующем порядке.
1.По ГОСТ Р 53464–2009 (см. в стандарте прил. 1, табл.9) для заданного технологического процесса, габаритного размера 326 мм и сплава КЧ35-10, подвергаемого термической обработке, находим интервал классов точности размеров КР 9— 13. Согласно примечанию, принимаем КР 11.
2. По тому же ГОСТ Р 53464–2009 (см. в стандарте прил. 1, табл. 10) находим степень коробления элементов отливки: фланца (рис. П2.3) и основной цилиндрической части отливки (f— стрела прогиба).
При этом при определении степени коробления фланца, точнее его свисающих концов, за высоту принимаем толщину h = 27 мм, за длину L — разность диаметров L = D – D1= 326 - 186 = 140 мм. Исходя из отношения h/L = 0,19 с учетом разовой формы и термической обработки отливки, интервал степени коробления составляет 5-8. В соответствии с примечанием к таблице стандарта принимаем СКэ 7.
|
|
Следует заметить, что при определении наибольшей длины коробящего элемента для кронштейнов, фланцев и т.п. берут удвоенную длину концов, как, например, для ступицы фланца. При определении степени коробления внутреннего цилиндра (рис. П2.4) за высоту принимается диаметр D = 166 мм, за длину – L = 230мм. Тогда по отношению D/L = 0,72 с учетом разовой формы и термической обработки отливки попадаем в интервал стандарта 4 -7. В соответствии с примечанием принимаем СКэ 6.
Степень коробления отливки в целом принимается по наибольшему значению степени коробления элемента отливки, для нашего случая это СК 7.
3. По ГОСТ Р 53464–2009 (см, в стандарте прил. 1, табл. 11) для заданного технологического процесса, габаритного размера 326 мм и материала КЧ35-10 (предусмотрена термическая обработка) находим интервал степеней точности поверхности 13— 19. С учетом примечания принимаем СП 15.
4.По тому же ГОСТ Р 53464–2009 (см. в стандарте прил. 1, табл. 13) для заданного технологического процесса, номинальной массы 22 кг и материала КЧ35-10 (предусмотрена термическая обработка) находим интервал классов точности массы, равный 8—15. С учетом примечания принимаем КМ 11.
5.Допуск смещения отливки определяем для наименьшей толщины стенки в плоскости разъема по классу точности размеров отливки, т. е. КР 11. В нашем случае h= 14 мм; по табл. 1 из ГОСТ Р 53464–2009 для КР 11 и Л = 14 мм находим Тсн = 2,8 мм.
Таким образом, найдены основные параметры точности отливки ступицы заднего колеса: класс точности размеров КР 11, степень коробления СК 7, степень точности поверхности СП 15, точность массы КМ 11 и допуск смещения Тсм=2,8 мм. В соответствии с ГОСТ Р 53464–2009 необходима соответствующая запись в ТУ отливки. Для нашего случая записываем:
Библиографический список
Основной
1. Салтыков В. А. Технология машиностроения. Технология заготовительного производства: учеб. пособие / В. А. Салтыков, Ю. М. Аносов, В. К. Федюкин. СПб: изд-во Михайлова В. А., 2004. 336 с.
2. Руденко П. А. Проектирование и производство заготовок в машиностроении: учеб. пособие / Руденко П. А., Харламов Ю. А. М.: Наукова думка, 1991.
3. Расчет припусков и межоперационных размеров в машиностроении: Учеб. пособие / Х. М. Радцевич и др.; под общ. ред. В. А. Тимирязева. М.: Высшая школа, 2004. 272 с.
4. Машиностроение: энциклопедия. В 40 т. М.: Машиностроение, 1999. Т.III -2. 840 с.
5. ГОСТ Р 53464–2009. Отливки из металлов и сплавов. Допуски размеров, массы и припуски на механическую обработку. М.: Изд-во стандартов, 2009. 54 с.
6. Справочник технолога–машиностроителя / под ред. А. Г. Косиловой и Р. К. Мещярекова. В 2 т. М.: Машиностроение, 1986. Т.1. 655 с.
7. Технология конструкционных материалов: метод. указания к выполнению курсовой работы по разделу «Литейное производство» / сост.: В. И. Черменский, и др. Екатеринбург: УГТУ – УПИ, 2000. 32 с.
8. ГОСТ 3.1125 – 88. Конструирование литых заготовок. М.: Изд-во стандартов, 1988. 31 с.
9. ГОСТ 3212 – 92. Формовочные уклоны. М.: Изд-во стандартов. 1992. 25 с.
10. Сборник практических работ по технологии машиностроения: учеб. пособие / А. И. Медведев и др.; ред. И. П. Филипова. Минск: БнТУ, 2003. 486 с.
11. Специальные способы литья: справочник / под общ. ред. В. А. Ефимова. М.: Машиностроение, 1991. 430 с.
12. В. Н. Иванов. Специальные виды литья: учеб. пособие / В. Н. Иванов, М.: МГИУ, 2007. 316 с.
13. М.Г. Афонькин, В.Б. Звягин. Производство заготовок в машиностроении. СПб.: Политехника, 2007. 380 с.
14. Выбор заготовок в машиностроении: уч. пособ. / А.С. Васильев, А.И. Кондаков. М.: МГИУ, 2002. 80 с.
Дополнительный
15. Технология литейного производства. Учебник / Чуркин Б.С., Гофман Э.Б., Майзель С.Г., Афонаскин А.В., Миляев В.М и др. Под редакцией Б.С.Чуркина. Екатеринбург: Изд-во Урал. Гос. Проф. – пед. Ун-та, 2000. 652 с.
16. Производство заготовок в машиностроении. / М.Г. Афонькин, М.В. Магницкая Л.: Машиностроение, 1987. 352 с.
17. ГОСТ 3212–92 стержневые знаки. Основные размеры. М: Изд-во стандартов. 1980. 24 с.
18. Литые заготовки и способы их получения. / Филлипов Г.И. Л: Машиностроение, 1985. 86 с.
19. Кокильное литье: Справочное пособие./ Дубинин Н.П., Беликов О.А., Вязков А.Ф. М.: Машиностроение, 1967. 460 с.
20. Литье по выплавляемым моделям / под ред. Н.И. Шкленника, В.А. Озерова. М.: Машиностроение, 1971. 456 с.
21. Коротков А И., Полевая А.М. Литье в оболочковые формы. М.: Машгиз, 1963. 360 с.
22. Юдин С.Б., Розенфельд С.Е., Левин М.М. Центробежное литье. – М.: Машиностроение, 1972. – 360 с.
23. Литье под давлением / А.К. Белопухов, В.И. Винберг, А.А. Дудин и др. М.: Машиностроение, 1975. 400 с.
24. Специальные способы литья / Под ред. Е.Б. Гуляева, А.М. Липницкого, Ф.Д. Оболенцова. Л.: Машиностроение, 1971. 286 с.
25. ОСТ 23.4.50 – 73., ОСТ 23.1.51.73 Отливки из алюминиевых сплавов. М.: Минсельхозмашиностроение, 1981. 47 с.
26. Воробьев Ю.А. Точность деталей, получаемых литьем и прессованием из цветных сплавов и пластмасс. М.: Машиностроение, 1963. 175 с.
27. Василевский П.Ф. Технология стального литья. М.: Машиностроение, 1974. 402 с.
28. Скарбинский М. Конструирование отливок. М. – Л.: Машгиз, 1961. 574 с.
29. Справочник по чугунному литью / Под. Ред. Н.Г. Гиршовича. Л.: Машиностроение, 1978 758 с
30. Рихтер Р.А. Конструирование технологичных отливок. М.: Машиностроение, 1968. 254 с.
31. Технологические основы обеспечения качества машин / под общ. ред. К.С. Колесникова, М.: Машиностроение,1990.256 с.
ПРИЛОЖЕНИЕ 1
Бланк задания на выполнение практической работы
Задание
на выполнение практической работы по дисциплине
«Производство и механическая обработка заготовок»
Студент___________________________ группы ____________________
Чертеж (вариант)___________, годовой объем производства __________ Содержание работы:
1. Определить тип производства, выбрать и обосновать способ производства отливки.
2. Разработать чертеж отливки, в том числе:
2.1. Установить плоскость разъема формы.
2.2. Выбрать базы для первой операции механической обработки.
2.3. Определить массу отливки.
2.4. Назначить классы точности, рассчитать припуски на механическую обработку, назначить допуски по ГОСТ Р 53464–2009.
2.5. Установить литейные уклоны, рациональные толщины стенок, место подвода литниковой системы, радиусы закруглений, напуски, минимальные диаметры отливаемых отверстий.
3. Разработать технологический процесс получения отливки.
3.1. Описать технологический процесс производства отливки.
Указать основные операции процесса изготовления отливки. Сделать анализ преимуществ и недостатков выбранного процесса. Выбрать оборудование и оснастку. Определить коэффициенты весовой точности и использования материала.
4. Оформить совмещенный чертеж заготовки и детали с нумерацией обрабатываемых поверхностей.
4.1. Выполнить анализ точности и шероховатости, выбрать способы обработки и количество переходов механической обработки для каждого элемента контура детали.
5. Разработать маршрутную технологию механической обработки, в которой для основных операций указать оборудование, оснастку, базы, обрабатываемые поверхности.
6. Выполненная практическая работа оформляется в следующем виде:
6.1. Расчетно-пояснительная записка объемом 10-15 листов (формат А4).
6.2. Совмещенный чертеж заготовки и детали (формат А3).
Срок выполнения практической работы устанавливается
с_____________________ по________________________201_ г.
Преподаватель
ПРИЛОЖЕНИЕ 2
Варианты заданий на выполнение практической работы
Вариант задания | Наименование деталей | № чертежей | Марка материала | Объем выпуска в год, шт. |
1 | Подшипник натяжного устройства | 4 | Чугун Кч 30-6 | | 100 |
11 | Сталь 35Л | 1500 | ||
21 | Чугун Сч-18 | | 600 | ||
31 | Чугун Вч 40 | 35000 | ||
2 | Крышка | 6 | Чугун Сч 15 | 3000 |
12 | Магниевый сплав Мл 5 | 60000 | ||
22 | Чугун Кч 35-10 | 300 | ||
32 | Алюминиевый сплав АЛ 9 | 200000 | ||
3 | Стойка правая | 16 | Сплав ЦАМ 4-1 | 200000 |
13 | Сталь 35Л | 20000 | ||
23 | Чугун ВЧ 40 | 1200 | ||
33 | Сплав Ал2 | 20000 | ||
4 | Крышка подшипника | 20 | Чугун Сч 18 | 24000 |
14 | Сплав ЦАМ 4 | 250000 | ||
24 | Сталь 10Х18Н9Л | 240 | ||
34 | Алюминиевый сплав АЛ2 | 65000 | ||
5 | Корпус подшипника | 24 | Сплав ЦАМ 4-3 | 200000 |
15 | Алюминиевый сплав АЛ2 | 6000 | ||
25 | Сталь 35Л | 2000 | ||
35 | Чугун Сч 20 | 65000 | ||
6 | Букса | 26 | Сплав АК 7ч | 3000 |
16 | Чугун Кч 40 | 2000 | ||
26 | Чугун Сч30 | 30000 | ||
36 | Сталь 30Л | 200 | ||
7 | Колодка тормозна я | 27 | Чугун Сч-18 | 1000 |
17 | Сталь 45Л | 30000 | ||
27 | Чугун Кч 37-12 | 10000 | ||
37 | Сталь 20ГЛ | 300 | ||
8 | Корпус подшипника | 31 | Чугун Сч 25 | 5000 |
18 | Сплав АК12 | 10000 | ||
28 | Сплав МЛ 9 | 50000 | ||
38 | Сталь 20Л | 100 | ||
9 | Корпус редуктора | 32 | Сталь 25Л | 5000 |
19 | Сплав МЛ 11 | 1000 | ||
29 | Чугун Сч-15 | 500000 | ||
39 | Алюминиевый сплав АЛ 9 | 1000 | ||
10 | Вилка | 34 | Бронза БрА10Мц2Л | 5800 |
20 | Чугун Сч 20 | 260000 | ||
30 | Сталь 25Л | 580 | ||
40 | Чугун ВЧ-70-2 | 2500 |
ПРИЛОЖЕНИЕ 3
Чертежи литых деталей
СОДЕРЖАНИЕ
I. ОБЩИЕ ПОЛОЖЕНИЯ ………………………………………….…..3
2. МЕТОДИЧЕСКИЕ УКАЗАНИЯ НА ВЫПОЛНЕНИЕ ПРАКТИЧЕСКОЙ РАБОТЫ ………………………………….…….…3
2.1. Выбор и обоснование способа производства заготовок ………..………………………………………………………………..….4
2.1.1.Тип производства …………………………………………….….…4
2.1.2. Вид сплава, размеры, форма и масса детали ……………….….…6
2.1.3. Требования к точности и шероховатости поверхности …….…...7
2.1.4. Учет технико-экономических показателей ……………….……...9
2.2. Разработка чертежа литой заготовки…………………….……9
2.2.1. Определение рационального положения отливки в форме ….….9
2.2.2. Назначение формовочных уклонов ………………………….…..10
2.2.3.Выбор минимальной толщины стенок, определение радиусов закруглений…………………………………………………………….……11
2.2.4.Определение минимальных диаметров отливаемых отверстий, назначение напусков...…………………………………….……………13
2.2.5.Выбор баз для первой операции механической обработки …….14
2.2.6. Определение мест установки стержней, прибылей …………….14
2.2
|
|
Автоматическое растормаживание колес: Тормозные устройства колес предназначены для уменьшения длины пробега и улучшения маневрирования ВС при...
Эмиссия газов от очистных сооружений канализации: В последние годы внимание мирового сообщества сосредоточено на экологических проблемах...
Биохимия спиртового брожения: Основу технологии получения пива составляет спиртовое брожение, - при котором сахар превращается...
Двойное оплодотворение у цветковых растений: Оплодотворение - это процесс слияния мужской и женской половых клеток с образованием зиготы...
© cyberpedia.su 2017-2024 - Не является автором материалов. Исключительное право сохранено за автором текста.
Если вы не хотите, чтобы данный материал был у нас на сайте, перейдите по ссылке: Нарушение авторских прав. Мы поможем в написании вашей работы!