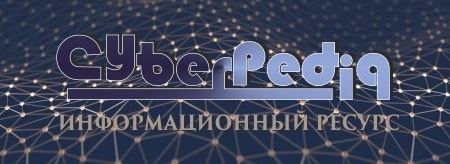
Механическое удерживание земляных масс: Механическое удерживание земляных масс на склоне обеспечивают контрфорсными сооружениями различных конструкций...
Папиллярные узоры пальцев рук - маркер спортивных способностей: дерматоглифические признаки формируются на 3-5 месяце беременности, не изменяются в течение жизни...
Топ:
Марксистская теория происхождения государства: По мнению Маркса и Энгельса, в основе развития общества, происходящих в нем изменений лежит...
Когда производится ограждение поезда, остановившегося на перегоне: Во всех случаях немедленно должно быть ограждено место препятствия для движения поездов на смежном пути двухпутного...
Интересное:
Национальное богатство страны и его составляющие: для оценки элементов национального богатства используются...
Отражение на счетах бухгалтерского учета процесса приобретения: Процесс заготовления представляет систему экономических событий, включающих приобретение организацией у поставщиков сырья...
Что нужно делать при лейкемии: Прежде всего, необходимо выяснить, не страдаете ли вы каким-либо душевным недугом...
Дисциплины:
![]() |
![]() |
5.00
из
|
Заказать работу |
|
|
Таблица 5 – Техническая характеристика станка СР6(К)
Наименование | Значение |
1 Наибольшая ширина обрабатываемой заготовки, мм | 620 |
2 Толщина обрабатываемой заготовки, мм | |
наибольшая, не менее | 300 |
наименьшая, не более | 5 |
3 Наименьшая длина обрабатываемой заготовки, не более, мм | 400 |
4 Частота вращения ножевого вала, не менее, об/мин | 4485 |
5 Наибольшая толщина снимаемого слоя за одни проход, не более, мм | 8 |
6 Наименьший диметр окружности резания, мм | 128 |
7 Скорость подачи, м/мин | 8; 16 |
8 Скорость механического перемещения стола, м/мин | 0,187 |
9 Норма обслуживания, чел | 2 |
10 Перемещение стола | механическое |
11 Номинальные размеры присоединительного патрубка эксгаустерной воронки, мм | 700x150 |
12 Габаритные размеры станка, не более, мм: | |
длина | 1100 |
ширина | 1200 |
высоты | 1560 |
13 Масса станка, не более, кг | 1300 |
Характеристики электрооборудования | |
14 Род тока питающей сети переменный | Переменный трехфазный |
15 Номинальная частота тока, Гц | 50 |
16 Номинальное напряжение сети, В | 380 |
17 Количество электродвигателей, шт | 3 |
18 Электродвигатель привода ножевого вала: | |
исполнение | АИР112М2 |
мощность, кВт | 7,5 |
частота вращения, об/мин | 3000 |
19 Электродвигатель привода подачи: | |
исполнение | AHP100S 8/4 |
мощность, кВт | 1,0/1,7 |
частота вращения, об/мин | 710/1410 |
20 Электродвигатель привода стола: | |
исполнение | АИР71А4 |
мощность, кВт | 0,55 |
частота вращения, об/мин | 1500 |
Режущий инструмент
Для строгания на рейсмусовом станке применяются строгально-фрезерные ножи. Они закрепляются во вращающихся валах или ножевых головках. Строгально-фрезерные ножи изготовляют двух типов:
а. тонкие, толщиной 3-5 мм без прорезей;
|
б. толстые, толщиной 6—10 мм с прорезями.
Ножи чаще всего изготовляются из инструментальных сталей, например, 9Х5ВФ - хромовольфрамованадиевая с содержанием углерода 0,9%, хрома 5%, вольфрама и ванадия до 1%.
Рисунок 16 - Конструкция ножа
Ножи выпускаются по ГОСТ 6567-61 «Ножи плоские с прямолинейной режущей кромкой для фрезерования древесины» толщиной 3 мм, шириной 25; 32; 40; 45 и длиной от 20 до 1610 мм. Согласно стандарту, в зависимости от расчетной ширины и длины (ширины обработки В = 620 мм) принимаются параметры ножа (см. таблицу 6). В ножевых валах применяется клиновое крепление ножей. Основное преимущество этого типа крепления ножей, обеспечившее его преимущественное применение в современных конструкциях ножевых валов, автоматическое увеличение силы закрепления ножа с увеличением частоты вращения фрезы.
Конструкция ножевого вала показана на рисунке 8.
Таблица 6 – Основные размеры плоского ножа (Тип I)
Длина L, мм | Ширина В, мм | Толщина а, мм | Угол заострения р, град. | Передний угол у, град. | Задний угол а, град. | Угол резания 5, град. |
1 | 2 | 3 | 4 | 5 | 6 | 7 |
640 | 32 | 3 | 40±3 | 30 | 20 | 60 |
Сущность клинового крепления состоит в том, что центробежная сила Рк, действующая на клин при вращении фрезы имеет составляющую Рку, прижимающую нож к опорной поверхности корпуса. Для предварительного закрепления ножа и клина в пазу корпуса служит распорный винт. Основной параметр, определяющий условие надежного закрепления ножа, - масса клина.
Нож крепится в ножевой вал по одной из схем, представленных на рисунке 17.
Рисунок 17 – Клиновое крепление ножа
Расчетная часть
Кинематические расчеты
Анализ кинематической схемы.
Целью анализа кинематической схемы является определение численных значений таких параметров как:
- скорость резания;
- скорость подачи;
- выявление потерь мощности в различных элементах кинематической цепи, свидетельствующей о степени совершенства передаточного механизма. Кинематическая схема представлена на рисунке 4.
|
Таблица 7 — Характеристика элементов кинематической цепи и результаты кинематических расчетов
№п/п | Наименование элементов | Характеристика элементов | Передаточное число i | Частота вращения вала n, мин-1 | Скорость подачи Vs, м/мин | Скорость резания V, м/с | |
D,мм | Z | ||||||
1 | 2 | 3 | 4 | 5 | 6 | 7 | 8 |
1 | Вал э/д привода подачи |
|
|
|
|
| |
n1 | 750 | ||||||
n2 | 1500 | ||||||
2 | Вал I | 750 | |||||
3 | Шестерня 1 | 36 | 1,14 | ||||
4 | Зубчатое колесо 2 | 41 | |||||
5 | Вал II |
|
|
|
|
| |
n1 | 657,9 | ||||||
n2 | 1315,8 | ||||||
6 | Шестерня 3 | 20 | 2,4 | ||||
7 | Зубчатое колесо 4 | 48 | |||||
8 | Шестерня 5 | 20 | 2,3 | ||||
9 | Зубчатое колесо 6 | 46 | |||||
10 | Шестерня 7 | 20 | 2,3 | ||||
11 | Зубчатое колесо 8 | 46 | |||||
12 | Шестерня 9 | 23 | 1,87 | ||||
13 | Зубчатое колесо 10 | 43 | |||||
14 | Вал III |
|
|
|
|
| |
n1 | 27,7 | ||||||
n2 | 55,4 | ||||||
15 | Звездочка 11 | 14 | 1,29 | ||||
16 | Звездочка 12 | 18 | |||||
17 | Вал IV |
|
|
|
|
| |
n1 | 21,47 | ||||||
n2 | 42,95 | ||||||
18 | Звездочка 13 | 12 | 1 | ||||
19 | Звездочка 14 | 12 | |||||
20 | Вал V |
|
|
|
| ||
n1 | 21,47 | 8,1 | |||||
n2 | 42,95 | 16,2 | |||||
21 | Звездочка 12 | 18 | 1 | ||||
22 | Звездочка 15 | 18 | |||||
23 | Вал VI |
|
|
|
| ||
n1 | 21,47 | 8,1 | |||||
n2 | 42,95 | 16,2 | |||||
24 | Вал э/д привода резания | 3000 | |||||
25 | Шкив 1 | 240 | 0,625 | ||||
26 | Шкив 2 | 150 | |||||
27 | Ножевой вал | 128 | 4800 | 32,2 |
Таблица 8 - Расчёт потерь мощности в кинематической цепи привода подачи
№ | Наименование i-ого элемента | КПД i-го элемента | Мощность, отводимая после i-го элемента, кВт
![]() | Потери мощности в i-ом элементе, кВт
![]() |
1 | Муфта | 0,99 | ![]() | ![]() |
2 | Подшипники качения | 0,99 | ![]() | ![]() |
3 | Цилиндрическая зубчатая передача | 0,98 | ![]() | ![]() |
4 | Цепная передача | 0,96 | ![]() | ![]() |
Общий КПД механизма привода подачи:
![]() | (1) |
Максимальная мощность, которая может быть израсходована на процесс подачи:
![]() | (2) |
Из таблицы видно, что общие потери мощности в кинематической цепи привода подач составляют 0,2 кВт. Учитывая эти потери строя ручьевую диаграмму потерь мощности в механизме подачи (рисунок 15).
Рисунок 18 - Ручьевая диаграмма потерь мощности в механизмах привода подачи станка СР6(К)
|
Таблица 9 - Расчет потерь мощности привода резания
№ | Наименование i-ого элемента | КПД i-го элемента | Мощность, отводимая после i-го элемента, кВт
![]() | Потери мощности в i-ом элементе, кВт
![]() |
1 | Клиноременная передача | 0,96 | ![]() | ![]() |
2 | Подшипники качения | 0,99 | ![]() | ![]() |
Общий КПД механизма привода резания:
![]() | (3) |
Максимальная мощность, которая может быть израсходована на процесс резания:
![]() | (4) |
Потери мощности в кинематической цепи для привода резания составляют 0,372 кВт. Учитывая эти потери строя ручьевую диаграмму потерь мощности в механизме подачи (рисунок 16).
Рисунок 19 - Ручьевая диаграмма потерь мощности в механизмах привода резания станка СР6(К)
Проведя кинематические расчеты были определены численные значения скорости резания, возможные значения скорости подачи и потерь мощности в приводе резания станка, построены ручьевые диаграммы, определены располагаемые мощности на процессы резания и подачи.
Технологические расчеты
2.2.1 Расчет скорости подачи
Данный вид расчета основывается на определении скорости подачи по мощности привода механизма резания и заданной шероховатости обрабатываемой поверхности. Условия расчета сводятся в таблицу 11.
Таблица 10 - Условия расчета скорости подачи
№ п/п | Наименование | Обозначение | Значение |
1 | Мощность электродвигателя механизма резания, кВт | Nnp | 7,5 |
2 | Ширина обработки, мм | В | 500 |
3 | Диаметр ножевого вала, мм | D | 128 |
4 | Толщина (глубина) снимаемого слоя, мм | Н | 2,0 |
5 | Период стойкости инструмента, мин | Т | 360 |
6 | Число ножей, шт | Z | 4 |
7 | КПД механизма резания | ![]() | 0,95 |
8 | Шероховатость обработанной поверхности, мкм | Rz max | 32 |
1. Расчет скорости подачи по мощности резания.
![]() | (5) |
где - удельная работа резания (коэффициент резания), работа затрачиваемая на удаление одного см3 древесины;
- объём срезаемой древесины за секунду.
Объем срезаемой древесины за секунду для процесса фрезерования древесины определится по выражению:
![]() | (6) |
Подставив в формулу (5) выражение (6) получим:
![]() | (7) |
Из этой формулы определить скорость подачи невозможно, так как неизвестно
, которое само зависит от скорости подачи. Значение
получают экспериментальным путем для определения усредненных условий фрезерования. Это значение называется табличным
. Для других условий вводятся поправочные коэффициенты.
|
Значение удельной работы резания определяется по формуле:
![]() | (8) |
где – табличное значение удельной работы резания, определяемой для средних, наиболее распространенных условий резания;
– произведение поправочных коэффициентов, учитывающих влияние различных факторов.
В свою очередь произведение поправочных коэффициентов определяется с учетом пиления по выражению:
![]() | (9) |
где – коэффициент, учитывающий породу. Для сосны
[1];
– коэффициент, учитывающий влияние влажности. При
[1];
– коэффициент, учитывающий степень затупления инструмента. Принимаем
[1];
– коэффициент, учитывающий влияние угла резания. Принимаем
(
) [1];
– коэффициент, учитывающий влияние скорости резания. Принимаем
[1].
Скорость подачи определяется по формуле:
![]() | (10) |
где – подача на один резец, мм.
С учетом ранее сделанных выражений мощность на резание можно определить по формуле:
![]() | (11) |
В формуле необходимо определить , но неизвестным является и
, который, в свою очередь, зависит от
. Поэтому определим произведение
.
![]() | (12) |
Подставив данные получим:
Зависимость получена экспериментальным путем. Пользуясь такой зависимостью, определяем
. Для наших условий фрезерования оказалось, что
[1].
Скорость подачи по мощности привода механизма резания будет равна:
2. Расчет скорости подачи по заданной шероховатости обработки.
Скорость подачи определяется по формуле:
![]() | (13) |
где – подача на оборот.
Подача на оборот определяется по формуле:
![]() | (14) |
где – предельная длина волны;
– высота волны;
– неточность установки резцов по радиусу,
.
Экспериментальным путем была установлена зависимость . При диаметре резания
и высоте неровностей
предельная длина волны
Высота волны определится по формуле:
![]() | (15) |
Тогда, подставив значения в формулу для определения подачи на оборот получим:
Определим скорость подачи:
Таким образом, произведён расчёт скорости подачи по различным критериям. Результаты расчёта заносятся в таблицу 11.
Таблица 11 – Сравнительные значения скоростей подач
Критерий | Скорость подачи, обусловленная конструкцией станка | Скорость подачи по мощности на резание | Скорость подачи по заданной шероховатости поверхности резания |
Скорость подачи ![]() | 8;16 | 11,9 | 30 |
Выбирается скорость подачи , которая ограничивается приводом механизмов подачи.
2.2.2 Моделирование процесса обработки
Рисунок 20 - Расчётная схема станка СР6(К)
|
а. Расчет окружной касательной силы
Для определения касательной составляющей силы резания воспользуемся формулой механики:
![]() | (16) |
Определим мощность, затрачиваемую на процесс резания по формуле(11):
Определим значение касательной составляющей силы резания:
б. Расчет окружной нормальной силы
Определяем нормальные составляющие силы резания, которые определяются по формуле
![]() | (17) |
где – переходный множитель (зависит от подачи на один резец и степени затупления), принимаем
– для затупленных резцов по табличным данным.
Тогда подставляя данные в формулу (17), получим:
в. Расчет проекций силы резания и
направленных вдоль и нормально к оси подачи соответственно, Н
Рисунок 21 – Схема фрезерования
Сумма проекций, составляющих силы резания на ось X определяется по формуле:
![]() | (18) |
![]() | (19) |
Средний угол определяется по формуле:
![]() | (20) |
Угол входа определится по формуле:
![]() | (21) |
Угол выхода определится по формуле:
![]() | (22) |
Подставляя данные в формулы (21), (22), (20), (18), (19) получим:
г. Расчет требуемой мощности необходимой для осуществления процесса обработки заготовки
Мощность электродвигателя определится по формуле:
![]() | (23) |
2.2.3 Расчет потребной мощности подачи и усилия прижима подающих вальцов
В основе расчёта лежит уравнение тягового баланса, имеющее вид:
![]() | (24) |
где – сила тяги (усилие подачи);
– суммарная сила сопротивления, состоит из сил действующих противоположно направлению подачи заготовки;
– коэффициент запаса (
).
Суммарная сила сопротивления определяется по формуле:
![]() | (25) |
где – сила трения скольжения;
– сила сопротивления качению.
Суммарная сила сопротивления при первом положении заготовки определится по формуле:
![]() | (26) |
где – коэффициент трения скольжения;
– вес заготовки;
– усилие прижимов подающих вальцов.
Тяговое усилие при первом положении заготовки определится по формуле:
![]() | (27) |
где – коэффициент сцепления рифленого вальца с заготовкой;
– коэффициент сцепления гладкого вальца с заготовкой;
– сила прижима подающего вальца.
Суммарная сила сопротивления при втором положении заготовки определится по формуле:
![]() | (28) |
Тяговое усилие при втором положении заготовки определится по формуле:
![]() | (29) |
Для определение усилия прижима , подставляем выражения (26) и (27) для передних вальцов и (28) и (29) для задних вальцов в уравнение тягового баланса (24), тогда:
![]() | (30) |
![]() | (31) |
Требуемое давление прижимных элементов определяется по формуле:
![]() | (32) |
где – коэффициент динамичности силы
;
, b и B ширина сучка и заготовки;
– коэффициент влияния пружины
.
– количество прижимов перед режущим инструментом.
Определим усилия прижима:
Определим тяговое усилие:
Определим мощность, затрачиваемую на процесс подачи, по формуле:
![]() | (33) |
Определим мощность, затрачиваемую электродвигателем привода подачи, по формуле:
![]() | (34) |
Таким образом, значение потребляемой мощности на процессы резания и подачи меньше значений располагаемых мощностей электродвигателей приводов резания и подачи соответственно:
Заданная технологическая операция выполняется
Расчет ножевого вала
|
|
Индивидуальные очистные сооружения: К классу индивидуальных очистных сооружений относят сооружения, пропускная способность которых...
Кормораздатчик мобильный электрифицированный: схема и процесс работы устройства...
Эмиссия газов от очистных сооружений канализации: В последние годы внимание мирового сообщества сосредоточено на экологических проблемах...
История развития пистолетов-пулеметов: Предпосылкой для возникновения пистолетов-пулеметов послужила давняя тенденция тяготения винтовок...
© cyberpedia.su 2017-2024 - Не является автором материалов. Исключительное право сохранено за автором текста.
Если вы не хотите, чтобы данный материал был у нас на сайте, перейдите по ссылке: Нарушение авторских прав. Мы поможем в написании вашей работы!