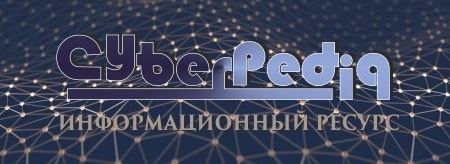
Механическое удерживание земляных масс: Механическое удерживание земляных масс на склоне обеспечивают контрфорсными сооружениями различных конструкций...
Таксономические единицы (категории) растений: Каждая система классификации состоит из определённых соподчиненных друг другу...
Топ:
Техника безопасности при работе на пароконвектомате: К обслуживанию пароконвектомата допускаются лица, прошедшие технический минимум по эксплуатации оборудования...
Отражение на счетах бухгалтерского учета процесса приобретения: Процесс заготовления представляет систему экономических событий, включающих приобретение организацией у поставщиков сырья...
Комплексной системы оценки состояния охраны труда на производственном объекте (КСОТ-П): Цели и задачи Комплексной системы оценки состояния охраны труда и определению факторов рисков по охране труда...
Интересное:
Лечение прогрессирующих форм рака: Одним из наиболее важных достижений экспериментальной химиотерапии опухолей, начатой в 60-х и реализованной в 70-х годах, является...
Мероприятия для защиты от морозного пучения грунтов: Инженерная защита от морозного (криогенного) пучения грунтов необходима для легких малоэтажных зданий и других сооружений...
Аура как энергетическое поле: многослойную ауру человека можно представить себе подобным...
Дисциплины:
![]() |
![]() |
5.00
из
|
Заказать работу |
|
|
Оборудование перерабатывающих производств
Оборудование для дробления и измельчения сырья и полуфабрикатов (оборудование истирающего, раздавливающего и ударного действия; резательные машины).
КЛАССИФИКАЦИЯ ОБОРУДОВАНИЯ
Измельчение относится к механическим процессам, в результате которых происходит изменение формы и размеров материала без изменения его физико-химических характеристик.
Измельчение широко используют в мукомольном, пивоваренном производствах, при производстве растительного масла, при переработке плодов, овощей и мяса. Сырье и полуфабрикаты измельчают для облегчения или ускорения тепловой обработки, перемешивания, транспортирования, дозирования и других процессов обработки, а также для увеличения площади поверхности твердых материалов с целью ускорения биохимических и диффузионных процессов.
В зависимости от конечного диаметра наибольших получаемых частиц различают измельчение крупное (250...25 мм); среднее (25...S мм); мелкое (5...1 мм); тонкое (1...0,075 мм); коллоидное (до 1 • 10-4 мм).
Для крупного и среднего дробления применяют дробилки; для среднего, мелкого, тонкого и коллоидного измельчения — мельницы.
Измельчающие машины подразделяют на вальцовые станки, молотковые, штифтовые, дисковые дробилки; шариковые, дисковые, молотковые и комбинированные мельницы; резательные машины; мясорубки; гомогенизаторы.
Материалы измельчают раздавливанием, ударным воздействием, истиранием и резанием.
К измельчающим машинам истирающего и раздавливающего действия относятся вальцовые станки, различные мельницы, кут- теры, эмульситаторы, дезинтеграторы; к машинам ударного действия — молотковые, штифтовые, ножевые дробилки; к резательным машинам — шинковальные, овощерезки, свеклорезки.
|
При производстве муки наряду с основным измельчающим оборудованием используют вспомогательные машины, повышающие эффективность измельчения: вымольные машины, деташер, бичевые машины.
Измельчители раздавливающего действия
Гладковалковые дробилки (вальцовые мельницы). По своему устройству гладко-валковые дробилки отличаются от зубовалковых отсутствием зубьев на валках. Обычно валки имеют одинаковое число оборотов, но есть конструкции, в которых валкам придают разные окружные скорости. В результате к раздавливающему действию валков присоединяется еще истирание. Непрерывная и равномерная подача сырья достигается с помощью загрузочных воронок, длина которых одинакова с длиной валка и питающих валков, вращающихся со скоростью, близкой к окружной скорости валков. Кроме того, диаметр поступающих на дробление кусков (г) должен быть примерно в 20 раз меньше диаметра валков /?ж20 г. Зубчатые валки обеспечивают захват более крупных кусков; для них #«5—10 г.
Гладковалковые дробилки могут иметь одну или две пары валков. Из двухвалковых для измельчения растительных материалов пригодна дробилка ДВГ-2 с диаметром валков 40 см и длиной 25 см. Скорость вращения ведущего валка 220 об/мин, ведомого — 190 об/мин. Из четырех-валковых дробилок интерес представляет дробилка БДА-7м, предназначенная для дробления солода. Между первой и второй парами валков установлено вибросито. На вторую пару валков поступает сырье, предварительно измельченное на первой паре валков. Производительность 1000 кг/ч. Диаметр валков 25 см, длина 50 см. Число оборотов в минуту верхней пары валков (ведущего/ведомого) 240/238, нижней пары — соответственно 268/254.
Поверхность валков может быть как гладкая, так и нарезная (рифленая); в последних истирающая способность выше, чем в гладких.
Измельчители истирающе-раздавливающего действия
На сочетании раздавливания с истиранием построен принцип работы жерновых мельниц, бегунов и дисковых мельниц. В качестве иллюстрации приводим краткое описание дисковой мельницы.
|
Дисковые мельницы
Основной деталью являются два вертикально установленных диска. Вращается обычно один из них. Поверхность дисков имеет режущие или ударные выступы той или иной конструкции. Исходный материал поступает в просвет между дисками, где он измельчается.
Одной из наиболее простых дисковых мельниц является мельница типа «Эксцельсиор», широко применяющаяся в фармацевтическом производстве. В мельнице (рис. 26) диски установлены вертикально. Один диск неподвижный, другой вращается со скоростью 250—300 об/глин. Поверхность дисков покрыта мелкими зубцами, расположенными по окружности в таком порядке, чтобы зубцы движущегося диска попадали в промежутки между зубцами неподвижного диска. Помимо истирания, к раздавливающему эффекту присоединяется срезывающее действие от острых зубцов. Производительность при диаметре дисков 400 мм до 50 кг/ч.
Молотковые мельницы
В этих мельницах (рис. 27) на центральном валу ротора укреплено несколько дисков один возле другого. На этих дисках висят на шарнирах молотки, представляющие стальные плитки. Ротор с молотками вращается в массивном корпусе, стенки которого защищены броневыми плитами. Дно корпуса представляет собой подовую решетку (сито). Вследствие большой скорости вращения ротора (500-1500 об/мин) и развивающейся центробежной силы молотки отбрасываются по радиусу.
Поступающий через загрузочную воронку материал попадает под действие этих молотков, куски его отбрасываются на стенки корпуса, на подовую решетку, ударяются друг о друга и, достигнув определенного размера, проходят через решетку. Область применения молотковых мельниц обширна. В химической и фармацевтической промышленности применяются для измельчения хрупких материалов (соли, растительное сырье). Небольшие молотковые мельницы, изготовляемые в СССР, имеют размер ротора 60/45 см (С-218) и 80/40 см (ДМ-2).
Резательные машины, применяемые в перерабатывающих производствах, как правило, используют в своем технологическом процессе один из трех известных видов резания (пуансоном, резцом, лезвием) или их комбинацию. При этом наибольшее распространение получили машины, принцип работы которых основан на измельчении материала с помощью одного или нескольких лезвий (ножей).
|
Конструктивное исполнение таких машин очень разнообразно и зависит от цели технологического процесса и свойств измельчаемого продукта. Например, мягкие и пластичные пищевые продукты и полуфабрикаты (мясо, рыба, тесто) нарезаются круглыми и дисковыми ножами. Лезвие при этом гладкое или с плавными зубьями. Твердые и хрупкие пищевые продукты режут такими же ножами, но с лезвием, оснащенным острыми зубьями. Серпообразные и дугообразные ножи используют прежде всего для поперечной резки жгутообразных материалов и мелкого дробления при переработке рыбы, мяса, овощей.
Наиболее обширную группу резательных машин составляет оборудование для измельчения мясного сырья и полуфабрикатов.
К нему относятся различные мясорезательные машины, волчки, кут-теры и другое оборудование.
Принципиально все мясорезательные машины схожи в одном — мясо разрезается в двух плоскостях относительно его движения: в продольной и поперечной. Однако реализуется этот принцип по-разному. В двухкаскадных мясорезательных машинах (рис. 4.15) необходимую степень измельчения мяса регулируют расстоянием между дисковыми ножами первого и второго каскадов. Вторая группа мясорезательных машин работает по принципу шпигорезок: два размера получаемых кусочков мяса регулируют с помощью плоских ножей, расположенных в двух рамках, а третий (длина) зависит от скорости подачи измельчаемого мяса или частоты вращения вала с серповидным дисковым ножом.
В двухкаскадной мясорезательной машине мясо измельчается вращающимися дисковыми ножами первого каскада и подается на поворотный барабан, после чего попадает на дисковые ножи второго каскада, расположенные перпендикулярно первому. В результате прохождения ножей первого каскада мясо нарезается на полоски; после второго каскада оно представляет собой отдельные кусочки, размеры которых регулируются расстоянием между дисковыми ножами. Производительность такой машины — около 3 т/ч; мощность привода — 3,6 кВт.
|
Машина Я2-ФИА для измельчения мяса на куски и охлажденного шпика на кусочки при производстве ветчины в оболочке или некоторых сортов сырокопченых колбас (рис. 4.16) состоит из сварной станины, к которой крепятся все сборочные единицы и детали: планетарный нож; блок плоских ножей; бункер; валы главный, правый и левый эксцентриковые; механическая блокировка; горловина и электрооборудование.
Планетарный нож закреплен с помощью шлицевого соединения на главном валу и служит для поперечной резки сырья, предварительно разрезанного в продольном направлении плоскими ножами.
Блок плоских ножей выполнен в виде корпуса и двух перпендикулярно расположенных рамок с набором ножей, которые, совершая колебательные движения, разрезают мясо или шпик в направлении его подачи.
Бункер служит для приема загружаемого сырья: главный вал — для синхронной работы дискового планетарного ножа и подающего шнека: правый и левый эксцентриковые валы — для приведения в колебательное движение рамок с наборами плоских ножей: блокировка для предохранения рабочих узлов машины от возможных перегрузок. В качестве привода используется электродвигатель мощностью 10 кВт. Производительность машины зависит от размеров измельчаемого сырья и составляет: по мясу — от 3,4 до 2,1 т/ч; по шпику — от 0,8 до 1,2 т/ч.
Шпигорезки предназначены для измельчения охлажденного шпика на куски размерами 4... 12 мм. В зависимости от расположения питателя и измельчающего механизма они подразделяются на вертикальные и горизонтальные.
Вертикальная гидравлическая шпигорезная машина ФШГ состоит из станины, горизонтального и вертикального валов, шестеренного насоса, маслопроводов, золотниковой коробки, цилиндра с траверсой, предохранительного клапана, ножевых рамок, стола с приемником, стопорного устройства и переключателя. Куски шпика загружают в приемную камеру, имеющую две секции. После загрузки одной из секций шпиком она поворачивается и устанавливается под шток толкателя, при перемещении которого вниз шпик подается к механизму резания.
Механизм резания состоит из пластинчатых ножей, закрепленных в ножевых рамках, и серповидного ножа. Ножевые рамки двигаются возвратно-поступательно в двух взаимно-перпендикулярных направлениях горизонтальной плоскости. Серповидный нож расположен под ножевыми рамками и совершает непрерывное круговое движение по часовой стрелке. Таким образом, принцип работы механизма резания шпигорезки практически не отличается от измельчающего аппарата мясорезательной машины Я2-ФИА (см. рис. 4.16).
После проталкивания шпика через механизм резания в первой секции толкатель поднимается и процесс повторяется во второй секции. Полученные кубики шпика через наклонный патрубок поступают в приемную емкость. Скорость подачи шпика в механизм резания регулируется количеством масла, нагнетаемого в цилиндр толкателя.
|
В зависимости от требуемых размеров кубиков производительность шпигорезки составляет от 250 до 1000 кг/ч; мощность электродвигателя — 4 кВт.
Горизонтальная гидравлическая шпигорезка ГГШМ по принципу действия практически не отличается от шпигорезки ФШГ и имеет горизонтально скомпонованные подающий и измельчающий механизмы.
Наиболее обширную группу машин для среднего измельчения мясного сырья составляют волчки. С помощью этих машин обычно осуществляется первичное измельчение продукта перед его посолом и тонким измельчением. Все волчки имеют одинаковое устройство исполнительного механизма (рис. 4. 17). В корпусе расположена рабочая камера для обработки продукта, представляющая собой цилиндр, внутри которого расположены ребра, препятствующие проворачиванию продукта относительно шнека. Расположение ребер может быть винтовым (спиралеобразным) или продольным (параллельно оси цилиндра). Направление ребер, если они выполнены спиралеобразно, должно быть противоположно направлению витков шнека.
Для перемещения мяса в рабочей камере, подачи его к ножам и проталкивания через ножевые решетки служит вращающийся шнек с шагом витков, уменьшающимся в сторону выгрузки продукта. Создаваемое шнеком давление должно быть достаточным для продав-ливания мяса через режущий механизм без выделения в продукте жидкой фазы.
Режущий механизм волчка состоит из неподвижной подрезной решетки, вращающихся крестообразных ножей, неподвижных ножевых решеток с отверстиями разных диаметров и зажимной гайки. Основным технологическим параметром волчка является диаметр его решетки. В различных марках машин он составляет от 82 до 200 мм.
Степень измельчения мяса в волчке и его производительность зависят от величины отверстий выходной решетки и числа режущих пар (решетка—нож). При небольшой степени измельчения (16...25 мм) достаточно одной пары — волчок собирают с одним ножом и одной решеткой (рис. 4.18, а, г); при более тонком измельчении (2...3 мм) число режущих пар следует увеличить. В этом случае режущий механизм собирают по схемам, представленным на рис. 4.18, б, в.
39. Оборудование для разделения и соединения продуктов переработки (оборудование для разделения жидких пищевых сред, сыпучих продуктов, оборудование для перемешивания жидких и сыпучих продуктов, оборудование для получения тестообразных продуктов)
К оборудованию этой группы относятся машины для разделения жидких пищевых сред и машины для разделения сыпучих продуктов измельчения пищевых сред. Первую группу составляют машины и аппараты для отстаивания, центрифугирования, фильтрования и сепарирования жидких пищевых сред. Отстаивание — процесс разделения неоднородных жидких смесей на фракции, различающиеся по плотности, в поле гравитационных сил. Его проводят в аппаратах различных конструкций, называемых отстойниками. В отстойниках суспензии и эмульсии разделяют на составляющие путем осаждения их под действием сил тяжести. Отстойники применяют в сахарной промышленности для разделения сока первой сатурации, в пивоваренной отрасли для осветления пивного сусла. Центрифугирование — разделение неоднородных суспензий на фракции в поле центробежных сил с помощью центрифуг различных конструкций. По характеру работы центрифуги делятся на осадительные и фильтрующие; по принципу действия — на непрерывные и периодически действующие; по способу разгрузки — на центрифуги с ручной и механизированной выгрузкой. В конструктивном плане различают центрифуги с горизонтальным и вертикальным ротором. Осадительные центрифуги снабжены сплошным ротором, фильтрующие — перфорированным, покрытым фильтрующей тканью. Центрифуги с ручной выгрузкой применяют обычно для обезвоживания штучных материалов в опытных и малотоннажных производствах. Фильтрация — процесс разделения неоднородных систем с твердой дисперсной фазой. Фильтры предназначены для удаления из пищевых сред различных механических примесей, осадка и отдельных составных компонентов с помощью пористой перегородки, способной пропускать жидкость, но задерживать взвешенные в ней твердые частицы. Основная часть любого фильтра — фильтровальный элемент, в качестве которого используют ткани из волокон растительного и животного происхождения, а также из синтетических, стеклянных, керамических и металлических материалов. Фильтровальные элементы, изготовленные из синтетических волокон (поливинилхлоридные, полиамидные, лавсановые), по своим свойствам во многих отношениях превосходят хлопчатобумажные и шерстяные, так как в них высокая механическая прочность сочетается с термоустойчивостью и невосприимчивостью к воздействию микроорганизмов. Металлические элементы выполняют в виде сеток и тканей из нержавеющих сталей, а также перфорированных листов. Последние обычно используют при разделении систем, содержащих грубодисперсные частицы, и в качестве опорных перегородок для фильтровальных тканей. В перерабатывающих производствах применяют фильтры периодического и непрерывного действия. Большинство из них работает в закрытом потоке под вакуумом или при избыточном давлении в системе. В зависимости от конструкции фильтрующего элемента фильтры делятся на цилиндрические и дисковые. Цилиндрические фильтры периодического действия бывают с одноразовыми и многоразовыми фильтрующими элементами. Частным случаем фильтрования пищевых сред является обработка их мембранными методами. Наряду с разделением эти методы позволяют повышать концентрацию отдельных составляющих пищевых сред. Сущность всех мембранных методов — разделение и концентрирование сырья в процессе фильтрации через специальные мембраны под действием давления или электрического поля (электродиализ). В перерабатывающей промышленности находит применение баромембранное разделение под действием перепада давления — микрофильтрация, ультрафильтрация и обратный осмос. Для осуществления этих процессов используют мембраны, изготовленные из одинакового материала, но с порами разного размера. Микрофильтрацию применяют для разделения растворов, состоящих из частиц размером 0,02...Ю мкм, ультрафильтрацию — 0,001...0,02 и обратный осмос — 0,0001—0,001 мкм. Основная часть фильтрующего аппарата — полупроницаемая мембрана, которая представляет собой тонкую пористую пленку с порами размером менее 0,5 мкм. Пленку помещают на макропористую подложку, усиливающую ее механическую прочность. Обычно в качестве подложки применяют пористую нержавеющую листовую сталь толщиной 0,5—3 мм с порами 0,5—10 мкм. Сепарирование — процесс разделения неоднородных жидких смесей на фракции, различающиеся по плотности, в поле действия центробежных сил. По технологическому признаку сепараторы делятся на три класса: сепараторы-осветлители, применяемые для разделения суспензии (выделения тяжелой дисперсной фазы), сепараторы- разделители, предназначенные для разделения эмульсий (выделения легкой дисперсной фазы) и комбинированные сепараторы с двойным пакетом тарелок, т. е. снабженные как осветительными, так и разделительными тарелками. По типу ротора различают сепараторы тарельчатые и камерные. Ротор тарельчатых сепараторов комплектуется пакетом конических вставок (тарелок), которые делят поток обрабатываемой жидкости на параллельные тонкие слои. Ротор камерных сепараторов снабжен реберной вставкой (при одной камере) или комплектом концентрических цилиндрических вставок, разделяющих его объем на кольцевые камеры, по которым обрабатываемая жидкость протекает последовательно. По способу выгрузки твердой фракции из ротора различают сепараторы с ручной и центробежной выгрузкой. По характеру выгрузки твердой фракции из ротора различают сепараторы с периодической, непрерывной и пульсирующей выгрузкой. Периодическую выгрузку шлама из сепаратора производят, как правило, вручную (после остановки сепаратора и разборки его ротора). По конструктивному исполнению устройства для выгрузки твердой фракции сепараторы подразделяют на сопловые и клапанные. Сопловые сепараторы эффективны при отсутствии крупных частиц в сепарируемом продукте и возможности добавления воды для облегчения выгрузки шлама. Клапанные разгрузочные устройства могут быть с верхним или нижним расположением подвижного затворного элемента. Клапанные сепараторы можно применять, в частности, для непрерывного получения дрожжей влажностью 70...75 % вместо жидкого дрожжевого концентрата, получаемого с помощью сопловых сепараторов. По способу подачи исходного продукта и вывода полученных жидких фракций различают сепараторы открытые, полузакрытые и герметические. В открытых сепараторах подача в ротор жидкой смеси и отвод полученных жидких фракций осуществляются открытым потоком. Процесс сепарирования не изолирован от доступа воздуха. В полузакрытых сепараторах жидкость подается в ротор открытым потоком, а отводятся одна или обе жидкие фракции под давлением по закрытым трубопроводам. Процесс сепарирования также не изолирован от доступа воздуха. Роторы полузакрытого типа отличаются от рот.оров открытого типа наличием устройства для вывода продуктов сепарирования под давлением. В герметических сепараторах подача в ротор исходной жидкости и отвод жидких фракций происходят под давлением по закрытым трубопроводам, герметически соединенным с выпускными патрубками. Сепарирование происходит без доступа воздуха. Роторы герметических сепараторов отличаются от роторов открытых и полузакрытых сепараторов конструкцией подводящих и отводящих устройств. В герметических сепараторах исходная жидкость подается в ротор через нижнее подводящее устройство и по каналу полого вертикального вала или через верхнее подводящее устройство; жидкая фракция выводится всегда через верхнее отводящее устройство. Подводящие и отводящие устройства снабжены специальными уплотняющими элементами между неподвижными и вращающимися деталями. Едкость можно подавать насосом, расположенным в технологической линии, или насосом, смонтированным в станине сепаратора. Исходная жидкость поступает в патрубок и нагнетается в ротор напорным диском, выполняющим роль центробежного насоса, через полый вертикальный вал. К группе оборудования для разделения сыпучих продуктов измельчения пищевых сред относятся рассевы, ситовеечные машины, виброцентрофугалы, крупосортировочные машины. При переработке зерна в муку и крупу на различных этапах технологического процесса образуется смесь частиц, разных по размерам, форме и плотности. Эту смесь направляют в машины для ее разделения на более однородные фракции. Сортирование промежуточных продуктов размола зерна, сортирование зерна крупяных культур по размерам перед шелушением, сортирование продуктов шелушения, контроль муки и крупы производят в рассевах. По исполнению ситовых корпусов рассевы подразделяют на пакетные и шкафные. В рассевах первого типа корпус собран из ситовых рам, уложенных друг на друга и стянутых в вертикальной плоскости стяжными болтами. В шкафных рассевах ситовые рамы вдвигают по направляющим в ситовой корпус, как ящики в шкаф. Ситовые корпуса приводятся в круговое поступательное движение самобалансным колебателем, поэтому такие рассевы называют самобалансирующимися. Их подразделяют на две группы: с жестким приводным валом (веретеном) и безверетенные с постоянным статическим моментом дебаланса. К самобалансирующимся безверетенным рассевам шкафного типа относят рассевы ЗРШ4-4М, ЗРШ6-4М и А1-БРУ, а к самобалансирующимся веретенным рассевам шкафного типа —рассевы РЗ-БРБ и РЗ-БРВ, входящие в комплект высокопроизводительного оборудования для переработки зерна. Для сортирования измельченных продуктов по совокупности свойств, в том числе по плотности частиц, в процессе переработки зерна в муку применяют ситовеечные машины. Контроль муки перед ее затариванием в мешки проводят в просеивающих машинах. К этой же группе машин следует отнести виброцентрофугал, применяемый в комплекте высокопроизводительного мельничного оборудования, и крупосортировки. На крупяных заводах в результате шелушения зерна крупяных культур получают смесь различных продуктов: основной продукт — шелушеное ядро, часть зерен остается нешелушеными, образуется лузга (отделенные наружные пленки), дробленое ядро и мучка. Для разделения продуктов шелушения зерна проводят сортирование. Мучку и дробленое ядро для большинства крупяных культур выделяют в просеивающих машинах, а для гречихи просеивающие машины используют для разделения шелушеных и нешелу- шеных зерен. На мукомольных заводах просеивающие машины применяют для контрольного просеивания муки и выделения из нее случайно попавших грубых и посторонних примесей. |
Для перемешивания сыпучих материалов при производстве комбикормов используют смесители различных конструкций.
По принципу работы их подразделяют на смесители непрерывного и периодического действия.
К группе смесителей непрерывного действия относятся горизонтальные, двухвальные смесители 2СМ-1 и МСН.
Двухвальный смеситель 2СМ-1 представляет собой два полых вала 1, расположенных горизонтально в корытообразном кожухе 2 (рис. 6.13). Смеситель герметично закрыт крышкой с встроенным в нее приемным патрубком 6. Отверстие для выпуска перемешиваемых компонентов расположено на противоположном конце в днище кожуха.
По всей длине каждого вала закреплены лопасти 3 прямоугольной формы, расположенные в четыре ряда. Между лопастями и валом находятся специальные шайбы, на поверхности которых сделаны радиальные вырезы, позволяющие установить лопасти под определенным углом к оси вала. Лопасти, закрепленные гайками, расположены в двух взаимно перпендикулярных плоскостях в шахматном порядке.
Лопасти чередуются так, чтобы две из них находились под углом 50° к оси вала для продвижения продукта по направляющим к разгрузочному устройству, а третья — под углом 20° к оси в противоположном направлении для создания местных (локальных) встречных потоков продукта.
Смеситель приводится в действие от электродвигателя клиноременной передачей через шкив ведущего вала. Ведомый вал связан с ведущим цилиндрическими зубчатыми колесами.
Смеситель МСН предназначен для смешивания муки при ее витаминизации, а также компонентов комбикормов и по принципу действия аналогичен смесителю 2СМ-1. Наиболее существенное отличие заключается в способе перемешивания. Рабочие органы смесителя МСН — два параллельно расположенных лопастных шнека, вращающихся в противоположных направлениях. Один шнек (подающий) перемещает основную массу продукта от входа к разгрузке, другой (возвращающий) подает часть продукта в обратном направлении.
Угол наклона лопастей к оси подающего шнека 14°, возвращающего—12°. Шаг подающего шнека 120 мм, возвращающего — 105 мм. Диаметры обоих шнеков одинаковы и составляют 160 мм.
Компоненты из приемного патрубка поступают в шнек, который смешивает их и перемещает к выходному патрубку. Одновременно часть продукта перебрасывается на второй, параллельный шнек, с помощью которого она возвращается вновь к приемному отверстию. Остальная часть продукта достигает выходного патрубка и выгружается.
Винтообразные лопасти перемешивают и одновременно перемещают продукт к середине смесителя, что позволяет быстро выгружать смесь. Вытяжной зонт 3 изготовлен из листовой стали и нижней отбортовкой с помощью болтов соединен с корпусом. Напередней стенке зонта расположено окно для загрузки продукта, которое во время работы смесителя закрывают задвижкой.
Патрубок в нижней части зонта предназначен для присоединения машины к аспирационной сети. В нем установлена поворотная заслонка для регулирования количества воздуха, отсасываемого из машины.
Смеситель приводится в действие от индивидуального мотор- редуктора мощностью 0,55 кВт через клиноременную передачу, закрытую съемным ограждением.
Рабочие органы и отдельные узлы смесителя (корыто, ротор, боковые стенки, решетка, заслонка) изготовлены из нержавеющей стали.
Производительность смесителя 40кг/ч, габаритные размеры 960 х 385 х 1485 мм, масса 135 кг. '
Горизонтальные смесители СГК-1М и СГК-2,5М также относятся к смесителям периодического действия и предназначены для смешивания компонентов комбикормов после порционного дозирования в автоматических весовых дозаторах. По конструкции оба смесителя одинаковы.
Смеситель СГК-1М состоит из корпуса 2 (рис. 6.15), установленного на станине 12. Внутри корпуса вращается лопастной вал, представляющий собой трубу, на которой закреплены четыре спиральные лопасти 3, две из которых внутренние, по направлению навивки противоположные наружным. Для интенсификации процесса смешивания на валу смонтированы лопасти, наклон которых по отношению к оси вала можно регулировать в значительных пределах.
Лопастной вал установлен в выносных подшипниковых опорах / и 7, установленных на станине.
На крышке расположены фланец 4 для соединения смесителя с бункером группы весовых дозаторов и патрубок для аспирации.
В нижней части корпуса находится люк, который закрывается поворотной крышкой. Для управления крышкой служат команд-
Смеситель приводится в действие от электродвигателя 14 через двухступенчатый цилиндрический редуктор 15 и клиноременную передачу. Цепная муфта 13 соединяет выходной вал редуктора с передней опорой лопастного вала. Ремни натягивают, перемещая электродвигатель на салазках. Смесь выгружается через разгрузочный бункер 9, подвешенный к корпусу смесителя.
Технологический процесс в смесителе СГК.-1М происходит следующим образом. От группы весовых дозаторов компоненты комбикормов поступают в смеситель самотеком через приемный патрубок.
Наружные спиральные витки лопастного вала перемещают компоненты вдоль корпуса в одном направлении, а внутренние витки — в обратном направлении, в результате чего они интенсивно и равномерно смешиваются.
Для выгрузки смеси с помощью командного прибора КЭП-12У переключается воздухораспределитель в пневмоприводе поворотной крышки. Поршень пневмоцилиндра перемещается вверх и через систему рычагов открывает крышку разгрузочного люка. Выгрузка смеси продолжается 1 мин, после чего крышка вновь закрывает разгрузочный люк. Крайние положения поворотной крышки (открыто, закрыто) контролируются конечным выключателем.
Основные технические данные смесителей СГК приведены в табл. 6.6.
Жидкие продукты, такие, как молоко и сливки, обрабатывают в гомогенизаторах клапанного типа.
Принцип действия гомогенизаторов этого типа заключается в следующем. Молоко в цилиндре гомогенизатора сжимается с помощью плунжера при давлении 15...20 МПа. Выход его из цилиндра возможен только при подъеме клапана, который прижат к седлу пружиной. Она отрегулирована таким образом, что клапан перемещается только при достижении в цилиндре рабочего давления. При прохождении молока через узкую круговую щель между седлом и клапаном скорость его возрастает от нулевой до
· 100 м/с и выше. Давление в потоке резко падает, и капля жира, попавшая в такой поток, вытягивается, а затем в результате действия сил поверхностного натяжения дробится на более мелкие капельки-частицы.
При работе гомогенизатора на выходе из клапанной щели раздробленные частички часто слипаются с образованием «гроздьев», ухудшающих эффект гомогенизации. Для предотвращения этого применяют двухступенчатую гомогенизирующую головку (рис. 6.1). Обе ступени устроены одинаково. В двухступенчатых головках на второй ступени устанавливается рабочее давление, на первой — давление, равное 75 % рабочего.
Гомогенизация может происходить только при условии, что молочный жир находится в жидком состоянии, поэтому температура гомогенизируемого продукта должна составлять 45...85 °С.
Гомогенизатор с двухступенчатой гомогенизирующей головкой А1-ОГМ-5 состоит из станины (рис. 6.2), корпуса, плунжерного блока, гомогенизирующей головки, привода и кривошипно-шатунного механизма.
Станина изготовлена из швеллеров и снаружи обшита листовой сталью. Внутри нее установлен электродвигатель на плите, которая прикреплена к станине шарнирно на двух кронштейнах.
Плунжерный блок состоит из корпуса плунжеров, манжетных уплотнений, всасывающих и нагнетательных клапанов и седел клапанов.
При работе одной плунжерной пары жидкость поступает к гомогенизирующей головке пульсирующим потоком. Для его выравнивания в гомогенизаторе применен трехплунжерный насос, приводимый в действие коленчатым валом, колена которого смещены на 120° относительно друг друга.
К плунжерному блоку на болтах прикреплены двухступенчатая плунжерная и манометрическая головки и предохранительный клапан, расположенный с противоположной стороны гомогенизирующей головки. Дросселирующее устройство манометрической головки позволяет уменьшить амплитуду колебаний стрелки манометра во время работы гомогенизатора.
Для перемешивания пластично-вязких (тестообразных) продуктов применяют фаршемешалки, смесители, тестомесильные машины и гомогенизаторы-пластификаторы. Смесители и гомогенизаторы относятся к оборудованию непрерывного действия, все остальные машины — к оборудованию периодического действия.
Эффективность перемешивания мясного сырья зависит главным образом от конструктивных особенностей и типа фаршемешалок. В зависимости от расположения рабочих органов в резервуаре они делятся на вертикальные и горизонтальные.
В фаршемешалках первого типа перемешивающее устройство закреплено на вертикальном валу, опускаемом в чашу-резервуар; в фаршемешалках второго типа перемешивающие рабочие органы, которые могут представлять собой шнеки, лопасти или лопатки, закреплены на одном или двух горизонтальных валах.
ОБОРУДОВАНИЕ ДЛЯ ЭКСТРАКЦИИ
Прессовым способом невозможно добиться полного обезжиривания масличного материала, так как на поверхности жмыха остаются слои масла, удерживаемые большими поверхностными силами.
Наиболее полно извлечь масло позволяет экстракционный способ. Экстракция — это процесс массопереноса масла из маслосодержащего материала в растворитель, осуществляемый посредством молекулярной и конвективной диффузии. В настоящее время в качестве экстракционного растворителя применяют бензин (температура кипения при атмосферном давлении 65...68 °С).
Вертикальный шнековый экстрактор НД-1250 (рис. 6.37) работает по способу погружения и состоит из загрузочной колонны 3 с шнековым валом 4, горизонтальной колонны, представляющей собой горизонтальный передаточный шнек 2, и вертикальной экстракционной колонны 12 с шнековым валом 4.
Горизонтальный передаточный шнек 2 подает экстрагируемый материал на шнековый вал 4. На загрузочной колонне расположен декантатор 6, в котором отходящая из экстрактора мисцелла очищается путем отстаивания от основного количества крупных взвешенных в ней частиц. В верхней части экстракционной колонны на валу 4 расположен механизм сбрасывателя 9 отходящего из экстрактора шрота. Шнеки всех трех колонн имеют индивидуальные приводы 1, 7, 8. В экстракционной колонне и передаточном горизонтальном шнеке для предотвращения проворачивания материала вместе со шнеками предусмотрены направляющие планки 14 и 15. В верхней части царги экстракционной колонны расположены патрубок 10 для выхода шрота, смотровые окна 11, люк-лаз 13.
Торцы всех трех колонн экстрактора закрыты крышками, через центр которых проходят валы диаметром 120 мм (места прохода валов уплотнены). К валам приварены витки шнеков. Толщина перьев шнеков 10 мм. В загрузочной колонне число витков шнека, находящихся в зоне растворителя, составляет 9,5 шт. При этом шаг верхнего шнека 460 мм, а шаг остальных витков 560 мм. В передаточном горизонтальном шнеке — 3,5 витка, а в экстракционной колонне —
27,5 витка. В этих колоннах шаг шнековых витков постоянный и одинаковый — 450 мм. Поверхность перьев шнеков перфорирована круглыми отверстиями с раззенковкой, расположенной на той стороне пера шнека, которая не соприкасается с экстрагируемым материалом. Диаметр отверстий на перьях шнека загрузочной колонны 8 мм, а на перьях передаточного горизонтального шнека и экстракционной колонны — 10 мм.
Технологический процесс экстракции заключается в следующем. Экстрагируемый материал в виде лепестка, крупки или гранул поступает в загрузочную колонну экстрактора по центральной и наклонной питающим течкам. Материал движется по течкам и в горловине, образуя опускающийся слой, который соприкасается с поверхностью мисцеллы в декантаторе. При этом частицы материала смачиваются и осаждаются, образуя фильтрующий слой в конической части декантатора. Направляющие пластины 5 в конической части декантатора препятствуют захвату его шнеком. Масличный материал перемещается вниз, од
|
|
Механическое удерживание земляных масс: Механическое удерживание земляных масс на склоне обеспечивают контрфорсными сооружениями различных конструкций...
Архитектура электронного правительства: Единая архитектура – это методологический подход при создании системы управления государства, который строится...
История создания датчика движения: Первый прибор для обнаружения движения был изобретен немецким физиком Генрихом Герцем...
Кормораздатчик мобильный электрифицированный: схема и процесс работы устройства...
© cyberpedia.su 2017-2024 - Не является автором материалов. Исключительное право сохранено за автором текста.
Если вы не хотите, чтобы данный материал был у нас на сайте, перейдите по ссылке: Нарушение авторских прав. Мы поможем в написании вашей работы!