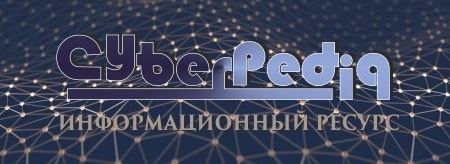
Опора деревянной одностоечной и способы укрепление угловых опор: Опоры ВЛ - конструкции, предназначенные для поддерживания проводов на необходимой высоте над землей, водой...
Поперечные профили набережных и береговой полосы: На городских территориях берегоукрепление проектируют с учетом технических и экономических требований, но особое значение придают эстетическим...
Топ:
Определение места расположения распределительного центра: Фирма реализует продукцию на рынках сбыта и имеет постоянных поставщиков в разных регионах. Увеличение объема продаж...
Выпускная квалификационная работа: Основная часть ВКР, как правило, состоит из двух-трех глав, каждая из которых, в свою очередь...
История развития методов оптимизации: теорема Куна-Таккера, метод Лагранжа, роль выпуклости в оптимизации...
Интересное:
Аура как энергетическое поле: многослойную ауру человека можно представить себе подобным...
Средства для ингаляционного наркоза: Наркоз наступает в результате вдыхания (ингаляции) средств, которое осуществляют или с помощью маски...
Инженерная защита территорий, зданий и сооружений от опасных геологических процессов: Изучение оползневых явлений, оценка устойчивости склонов и проектирование противооползневых сооружений — актуальнейшие задачи, стоящие перед отечественными...
Дисциплины:
![]() |
![]() |
5.00
из
|
Заказать работу |
|
|
В радиально – осевых турбинах газ может подводиться к сопловым лопаткам по направлению вращения ротора или в обратном направлении. В связи с этим профилировать лопаточные аппараты следует исходя из условий подвода газа. С целью обеспечения безударного входа, средний геометрический угол на входе в сопловые лопатки должен быть близким к основному направлению потока газа.
В случае попутного подвода газа конструкция соплового аппарата аналогична конструкции лопаточного диффузора компрессора. В импульсных турбинах с двумя и более подводами газа в большинстве случаев сопловой аппарат составляется из лопаток двух видов: к части лопаток газ подводится в попутном направлении, к другой части – во встречном направлении. При попутном направлении угол лопаток на входе определяется из условия:
, (4.14)
где - площадь поперечного сечения улитки на входе.
При встречном подводе газа лопатки соплового аппарата оказываются очень изогнутыми, и определяется из условия:
. (4.15)
Как правило, сопловые аппараты с попутным подводом газа имеют меньшие потери энергии, чем сопловые аппараты со встречным подводом. При встречном подводе газа профилирование сопловых лопаток ведётся с учётом дополнительных условий. Число лопаток принимают на 20÷30% больше, чем при попутном подводе; радиальная протяжённость соплового аппарата выбирается из условия обеспечения равномерного сужения вдоль всего межлопаточного канала. При встречном подводе газа требуется значительная радиальная протяжённость соплового аппарата. При малой радиальной протяжённости приходится применять сопловые аппараты с большим числом лопаток, что для малых турбин ведет к снижению и, соответственно,
.
|
При смешанном (попутном и встречном) подводе газа необходимо фиксировать правильное положение соплового аппарата (например, штифтованием).
Угол потока на выходе из соплового аппарата в первом приближении можно считать равным эффективному углу выхода и определить по формуле:
. (4.16)
Угол потока и ширина сопловых лопаток
определяются в результате газодинамического расчета. Обычно
=12÷23°, а отношение
0,08÷0,15. Толщина выходной кромки зависит от типа размера турбокомпрессора и равна 0,5÷1,0 мм.
Радиальная протяженность сопловых лопаток , существенно влияющая на габариты и вес турбины, частично зависит от угла
и не может быть уменьшена за счёт увеличения числа лопаток в связи с ограничением по конфузорности и
. При
=12÷20,
=(0,15÷0,20)
, то есть
=1,35÷1,50.
Относительный шаг соплового аппарата выбирают в пределах =0,55÷0,75. Большие значения соответствуют сопловым лопаткам с попутным подводом газа, меньшие – со встречным.
Условия работы колеса турбины и вероятность поломки лопаток из-за вибрации существенно зависят от неравномерности поля скоростей и давлений на входе в рабочее колесо, которая определяется величиной радиального зазора между сопловыми и рабочими лопатками.
Увеличение радиального зазора между сопловыми и рабочими лопатками приводит к снижению неравномерности параметров газа на входе в колесо и существенному снижению уровня шума. В тоже время, увеличение радиального зазора приводит к росту потерь энергии на трение в безлопаточной части. Применение увеличенного зазора в турбине, работающей в потоке переменного давления, может привести к росту потерь энергии вследствие перетекания газа из одного патрубка в другой. Во избежание такого явления необходимо установить разделительные лопатки с минимальным зазором между их кромками и колесом. В выполненных конструкциях радиально-осевых турбин радиальный зазор между сопловыми лопатками и рабочим колесом составляет (0,04÷0,08) .
|
Число лопаток колеса определяется его геометрическими размерами, быстроходностью, технологией изготовления и условиями работы турбины. Достижение высоких значений КПД турбины возможно при безотрывном течении потока газа в межлопаточных каналах колеса. Профиль и форма межлопаточного канала зависят от количества лопаток.
Время разгона ротора турбокомпрессора пропорционально его моменту инерции. Момент инерции колеса турбины составляет 70÷80% от момента инерции ротора и пропорционален числу лопаток колеса турбины. В ряде случаев целесообразно идти на уменьшение числа лопаток для получения минимального момента инерции, допускается даже некоторое снижение КПД турбины. Число лопаток колеса турбины определяет возможность создание жестких и прочных лопаток, что может явиться основным фактором, определяющим надёжность турбокомпрессора. Жесткие и прочные лопатки получаются при их достаточной толщине у корня. Число лопаток в радиально - осевых турбинах равно 12÷18.
Угол потока газа на выходе из рабочего колеса в относительном движении
, (4.17)
где =1,0÷1,1- коэффициент, зависящий от формы и толщины выходной кромки лопаток.
Некоторое увеличение КПД турбины может быть получено за счет выбора минимально допустимого угла , но при этом может произойти ухудшение межлопаточного канала в меридиональном сечении.
Обычно в радиально – осевых турбинах = 15÷25°;
;
90°;
=70÷90°;
25÷45°;
;
0,5÷0,6.
Газоотводящий корпус
Когда позволяют габариты, для снижения потерь энергии с выходной скоростью за рабочим колесом турбины устанавливают диффузор. Повышение давления газа в диффузоре происходит за счет преобразования части кинетической энергии в потенциальную энергию давления. В этом случае давление газа за выходными кромками рабочих лопаток будет ниже давления в случае без диффузора, что позволит увеличить располагаемую работу и повысить мощность турбины.
Давление газа за турбиной с диффузором можно определить по выражению:
, (4.18)
где - скорость газа на выходе из диффузора;
и
- площади проходных сечений соответственно на входе в диффузор и на выходе из него;
|
- КПД диффузора.
КПД кольцевых диффузоров с углами раскрытия менее 15° составляет 0,65÷0,8. Незначительные углы раскрытия диффузоров позволяют исключить отрыв потока от стенок и обеспечить достаточно высокий КПД. Однако при этом существенно увеличиваются осевые размеры турбины. Увеличение угла раскрытия более 15° приводит к резкому снижению КПД диффузора, что делает его не эффективным.
Длину кольцевого диффузора можно определить по уравнению:
, (4.19)
где - средний диаметр рабочей решетки;
- длина рабочей лопатки;
- угол раскрытия диффузора;
- степень диффузорности;
.
В этом выражении: - внутренний диаметр кольцевого диффузора на выходе;
- наружный диаметр кольцевого диффузора во входном сечении.
Для турбокомпрессоров степень диффузорности целесообразно выбирать меньше 1,6. В большинстве турбокомпрессоров диффузор за турбиной не устанавливается.
Подшипники и уплотнения
Подшипники турбокомпрессора воспринимают нагрузки создаваемые ротором. Они складываются из силы тяжести ротора, динамических усилий, вызываемых неуравновешенными массами, инерционных и гироскопических нагрузок, возникающих при вибрации турбокомпрессора на двигателе, осевых усилий от равнодействующей давлений газа и воздуха в рабочих аппаратах компрессора и турбины.
В турбокомпрессорах применяются подшипники качения и подшипники скольжения. Подшипники качения имеют меньшие механические потери и обеспечивают хорошие условия пуска турбокомпрессора, особенно при низких температурах окружающего воздуха. К недостаткам этих подшипников относится высокая стоимость, меньшая долговечность, особенно при высоких πк, большая сложность подшипникового узла, необходимость индивидуальной системы смазки.
Подшипники скольжения более просты по конструкции и дешевле, имеют большую долговечность и могут работать на масле, которое используется в системе смазки двигателя. Эти качества обеспечили преимущественное распространение подшипников скольжения, несмотря на увеличение потерь энергии на трение в два-три раза. В малых турбокомпрессорах с консольным расположением колес эти потери могут составлять ощутимую величину (до 10÷15% от суммарных потерь энергии). В крупных турбокомпрессорах они редко превышают 4÷6%, что вполне допустимо.
|
Подшипники качения применяются главным образом при расположении подшипниковых узлов по концам ротора, когда сравнительно легко получить малые диаметры шеек вала. При консольном расположении рабочих колес диаметр шеек вала возрастает, и обеспечить хорошую работоспособность подшипников качения трудно. Подшипники качения следует устанавливать на упругие демпфирующие опоры, уменьшающие динамические нагрузки. Отсутствие упругих опор резко снижает долговечность подшипников.
На рисунке 4 приведена конструкция подшипниковых узлов с упругой опорой. Подшипники имеют индивидуальную систему смазки, циркуляция масла обеспечиваются вращающимися дисками, подающими его в верхнюю часть полсти, откуда оно стекает в подшипники. В крупных турбокомпрессорах для подачи масла применяются встроенные масляные насосы, приводимые во вращение ротором. При нормальной работе уплотнений масло длительно сохраняется в полости подшипников. Для смазки применяется масло с пониженной вязкостью. Смена таких подшипников производится без разборки турбокомпрессора и занимает немного времени. Ресурс подшипников качения достигает 16000 часов.
Условия работы подшипников скольжения определяются, в основном, нагрузкой. Общим свойством всех подшипников скольжения является склонность к автоколебаниям ротора на масляном слое при малых нагрузках. В крупных турбокомпрессорах при расположении опор по концам ротора, когда нагрузки на них велики, применяют неподвижные цилиндрические подшипники, а при высоких степенях повышения давления применяют многоклиновые подшипники. В турбокомпрессорах с консольным расположением рабочих колес, в которых нагрузки на подшипники малы по причине большого диаметра вала, применяют, главным образом, качающиеся и плавающие подшипники.
Качающаяся втулка подшипника устанавливается в корпус с небольшим зазором по наружному диаметру и фиксируется от вращения и осевого перемещения радиальным штифтом, выполняющим также роль маслоподводящего штуцера, шпонкой, ось которой перпендикулярна к оси подшипника, или наружным буртом, зажимаемым между корпусом и крышкой.
Плавающие втулки подшипника свободно вращаются в корпусе, частота вращения их составляет 0,25÷0,30 от частоты вращения ротора. Осевая фиксация осуществляется стопорными кольцами. Качающиеся и плавающие подшипники обладают хорошими демпфирующими свойствами.
Длина втулки подшипника в выполненных конструкциях составляет 0,65÷1,2 от диаметра вала, меньшие значения относятся к турбокомпрессорам с радиально-осевыми турбинами.
|
Зазоры в подшипниках скольжения зависят от частоты вращения. С ростом частоты вращения необходимо увеличивать зазоры для обеспечения большего расхода масла и сохранения температуры подшипника на приемлемом уровне. Максимальная температура масла на выходе из подшипников не должна превышать 100÷110 °С. Зазор между валом ротора и втулкой подшипника обычно составляет 0,002÷0,005 от наружного диаметра шейки вала. Наружный зазор в плавающих втулках лежит в пределах 1,0÷2,0 от внутреннего зазора. Наружный зазор в качающейся втулке определяется посадками (скользящей или ходовой).
Потери в упорных подшипниках составляют значительную долю суммарных потерь на трение в подшипниках. В турбокомпрессорах с опорами по концам ротора применяются упорные подшипники с четырьмя - шестью неподвижными подушками. Между подушками фрезеруются каналы для подачи смазки. От каналов по направлению вращения упорной пяты на подушках выполняются скосы под углом 15÷30', способствующие образованию масляного клина. Обычно упорный подшипник объединяется с опорным и в последнем фрезеруется канал для подачи масла к упорной поверхности. Скосы для подачи масла могут выполняться и на упорной пяте. Для компенсации перекосов и выравнивания нагрузок на упорной поверхности последняя может устанавливаться упруго через пакет тонких прокладок, зазоры между которыми заполняются маслом (рис. 5).
В турбокомпрессорах с радиально – осевыми турбинами, у которых осевые силы малы, скосы на подушках не делают. Зазоре в упорных подшипниках составляют 1÷3 от зазора в опорном подшипнике.
Уплотнения турбокомпрессора должны препятствовать попаданию масла из подшипников в его проточные части, а также газа и воздуха из проточных частей в масляные полости и газа в машинное отделение. В турбокомпрессорах применяются лабиринтные и контактные уплотнения. Лабиринтные уплотнения практически не имеют износа, однако они пропускают некоторое количество воздуха и газа, что может приводить к увеличению давления в картере двигателя, а также масла, попадающего в проточные части турбокомпрессора и загрязняющего их. Размещение лабиринтных уплотнений требует большей по сравнению с контактными уплотнениями длины. Они применяются, как правило, в турбокомпрессорах с консольными рабочими колесами. Большое распространение получили уплотнения из ленты, завальцованной в кольцевую канавку на валу и закрепленной завальцовочной проволокой. Толщина ленты 0,3 мм.
Из контактных уплотнений в турбокомпрессорах применяется, в основном, кольцевое, которое представляет собой разрезное упругое кольцо типа поршневого, установленное в канавку вала. Уплотнение долговечно только в том случае, если кольцо не вращается и не прижимается боковой поверхностью к торцу канавки. Для того чтобы кольцо не вращалось, сила трения по наружной поверхности, определяемая упругостью кольца, должна быть больше осевой силы от перепада давлений.
|
Рисунок 4-Компоновка подшипниковых узлов с подшипниками качения
Рисунок 5 — Компоновка подшипниковых узлов с подшипниками скольжения
|
|
Наброски и зарисовки растений, плодов, цветов: Освоить конструктивное построение структуры дерева через зарисовки отдельных деревьев, группы деревьев...
Историки об Елизавете Петровне: Елизавета попала между двумя встречными культурными течениями, воспитывалась среди новых европейских веяний и преданий...
Механическое удерживание земляных масс: Механическое удерживание земляных масс на склоне обеспечивают контрфорсными сооружениями различных конструкций...
Состав сооружений: решетки и песколовки: Решетки – это первое устройство в схеме очистных сооружений. Они представляют...
© cyberpedia.su 2017-2024 - Не является автором материалов. Исключительное право сохранено за автором текста.
Если вы не хотите, чтобы данный материал был у нас на сайте, перейдите по ссылке: Нарушение авторских прав. Мы поможем в написании вашей работы!