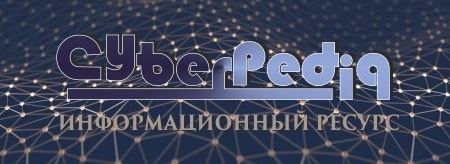
Таксономические единицы (категории) растений: Каждая система классификации состоит из определённых соподчиненных друг другу...
Археология об основании Рима: Новые раскопки проясняют и такой острый дискуссионный вопрос, как дата самого возникновения Рима...
Топ:
Особенности труда и отдыха в условиях низких температур: К работам при низких температурах на открытом воздухе и в не отапливаемых помещениях допускаются лица не моложе 18 лет, прошедшие...
Марксистская теория происхождения государства: По мнению Маркса и Энгельса, в основе развития общества, происходящих в нем изменений лежит...
Оценка эффективности инструментов коммуникационной политики: Внешние коммуникации - обмен информацией между организацией и её внешней средой...
Интересное:
Мероприятия для защиты от морозного пучения грунтов: Инженерная защита от морозного (криогенного) пучения грунтов необходима для легких малоэтажных зданий и других сооружений...
Принципы управления денежными потоками: одним из методов контроля за состоянием денежной наличности является...
Финансовый рынок и его значение в управлении денежными потоками на современном этапе: любому предприятию для расширения производства и увеличения прибыли нужны...
Дисциплины:
![]() |
![]() |
5.00
из
|
Заказать работу |
|
|
Гигроскопические свойства текстильных материалов характеризуются следующими показателями:
- влажностью – содержание влаги при фактической влажности воздуха, Wa =((ma –mc)\mс) 100: mф – масса элементарной пробы при фактической влажности воздуха, г; mс – масса элементарной пробы после высушивания до постоянной массы, г.
- гигроскопичность – содержание влаги при относительной влажности воздуха близкой к 100%, Н = (m1-m2\m2)100: m1 – влажность образца выдержанного во влажносте воздуха близкой к 100%.
- капиллярность – поглощение влаги продольными капиллярами материала и оцениваемой высотой подъема жидкости в пробе, погруженное одним концом в жидкость на 1 час, h мм.
- водопоглощаемость – количество поглощаемой пробой воды при ее полном погружении в воду, Вп %.
Для определения гигроскопических свойств используют аналитические весы и сушильный шкаф.
14. Характеристики проницаемости текстильных изделий. Применяемое оборудование и методы испытаний
Воздухопроницаемость полотен или изделий оценивают коэффициентом воздухопроницаемости, показывающим количество воздуха в м3 проходящего через площадь полотна в 1 м2 за время равное 0,1 секуде при постоянной разности давления по обе стороны образца.
Определяют на специальных приборах, в которых может создаваться перепад давления под счетом количеством воздуха, прошедшим через пробу в единицу времени. К примеру на приборе ВП ТМ.2 Точечную пробу испытуемого материала укладывают на столик лицевой стороной вверх и прижимают к столику кольцом до загорания красной сигнальной лампочки. Электродвигатель с вентилятором включается автоматически при подаче нагрузки на испытуемую точечную пробу. Открытием дросселя устанавливают разрежение под точечной пробой, равное 49 Па (5 мм вод.ст.), которое определяют по шкале индикатора разрежения.По шкале дифференциального манометра отсчитывают результат измерения с точностью до одного деления шкалы. При снятии нагрузки с точечной пробы электродвигатель с вентилятором автоматически отключается.Воздухопроницаемостьв дм3/м2·с каждой точечной пробы, куска или изделия вычисляют по формуле
|
,
где Vср - средний расход воздуха по одной точечной пробе, куску или изделию, дм3/с; S- испытуемая площадь, см2.Результат подсчитывают с погрешностью до 0,1 дм3/м2·с и округляют до 1,0 дм3/м2·с.
Паропроницаемость характеризуется коэффициентом паропроницаемости, В=А\St: А – количество воды, убывшей из сосуда, накрытого пробой материала в мг; S – площадь пробы м2; t - время прохождение паров в с.
Пылепроницаемость является одним из важнейших показателей для фильтровальных полотен, а также материалов для некоторых видов защитной одежду. Может определяться при помощи пылелоса, который в качестве фильтра закладывается в образец испытуемого полотна за определенное время пылесосом засасывается определенное количество пыли. Затем определяют количество пыли осевшей на образце (его взвешивании до и после испытания) и количество пыли выпавшей перед фильтром. Коэффициент пылепроницаемости вычисляют по формуле: П=g4\st. Коэффициент пылеёмкости: Пе=g2\st. Где g1 – количество пыли засасываемое пылесосом при испытании; g2 – количество пыли осевшей на образце; g3 – количество пыли выпавшей перед фильтром; g4 – количество пыли прошедшей через образец, грамм; s – площадь образца, t – время испытания в секундах.
g4=g1-(g2+g3) г\м2 с
Водопроницаемость характеризует способность материала пропускать воду при определенном перепаде давления. Оценивается для плащевых тканей и материалов с водоотталкивающими и водоупорными обработками.
Характеризуется коэффициентом водопроницаемости, оцениваемым количеством воды в дм3, проходящим за 1 секунду через образец площадью 1 м2 при постоянном давлении воды. Определяют на специальных приборах, создающих постоянное давление на пробу засчет разницы уровней жидкости.
|
Водоупорность характеризует сопротивление текстильных материалов первоначальному проникновению через них воды. Данную характеристику применяют для оценки палаточных полотен, брезентов, а также полотен со специальными водоотталкивающими пропитками. Определяют на специальных приборах пенетрометрах. В качестве показателя пименяют минимальное давление воды на пробу, вызывающее появление третей капли воды на противоположные поверхности пробы. Может характеризоваться также временем по истечению которого третья капля ли определенный объем воды проходят через пробу при постоянном давлении или падении капель с определенной высоты.ГОСТ 3816-81.Из точечной пробы вырезают не менее пяти проб круглой формы диаметром не менее 160 мм или квадратной формы размером 160х160 мм таким образом, чтобы они не содержали одинаковые группы нитей основы или петельных столбиков и уточных нитей или петельных рядов, а также местные пороки.Допускается проводить испытания на цельном куске полотна, отобранном в качестве пробы, в этом случае место испытания необходимо отметить.Сосуд наполняют дистиллированной водой температурой (27±2) °С для макроклимата тепло-влажного или (20±2) °С для макроклимата холодно-умеренного таким образом, чтобы в подающей воду трубке не оставались пузырьки. Перед началом испытаний поверхность воды заполненного доверху сосуда должна быть на уровне нулевого деления шкалы манометра. Перед каждым испытанием проверяют чистоту поверхности воды.Если прибор заполнили дистиллированной водой не перед самым испытанием, а поверхность воды не чистая, то ее очищают.Испытуемую пробу помещают на испытательную головку таким образом, чтобы лицевая сторона пробы соприкасалась с поверхностью воды и чтобы между ними не оставался воздух. В таком положении испытуемую пробу с помощью зажимного устройства механизма прижимают по периметру сосуда.После зажима испытуемой пробы давление водяного столба равномерно увеличивают со скоростью (1,00±0,05) кПа/мин или (6,0±0,3) кПа/мин до тех пор, пока через испытуемую пробу не просочится вода в трех местах.Капли воды, соприкасающиеся друг с другом, считают за одну каплю.За окончательный результат испытания принимают среднее арифметическое результатов определений всех проб (мест испытаний), вычисленное в килопаскалях с точностью до трех значащих цифр
|
15. Характеристики тепловых свойств текстильных изделий. Применяемое оборудование и методы испытаний.
Тепловые свойства текстильных изделий характеризуются теплозащитными свойствами, тепло-, морозо- и огнестойкостью.
Теплощатиные свойства характеризуются суммарным тепловым сопротивлением, Rcgm(град м2\Вм).
Теплозащитные свойства определяют методами стационарного и нестационарного режимов. Методы первой группы предусматривают измерение стационарного (установишегося во времени) теплового потока при постоянной разницы температур двух поверхностей, разделенной испытуемым образцом. Методы второй группы предусматривают применение приборов, позволяющих изменять темп охлаждения, т.е. разность температур ядра прибора, нагреваемого до определенной температуры и изолированного от окружающей среды, испытуемым образцом и окружающего воздуха через определенные промежутки времени.
Теплостойкость материалов характеризуется максимальной температурой, выше которой наступает ухудшение свойств, препятствующее их использованию.
В зависимости от назначения изделий за кретерий теплостойкости принимают ухудшение механических или других свойств, которые обычно изображают графически в зависимости от температуры нагрева.
Огнестойкость определяется воздействием пламени на материал по степени к огнестойкости материалы делят на 3 группы:
- негорючие (стеклянные, азбестовые)
- загарающиеся, но прекращающие горение и тление после удаления из пламени (шерстяные, полиамидные, полиэфирные)
- горючие, продолжающие гореть и тлеть после удаления из пламени (хб, льняные и вискозные).
Методы для определения огнестойкости текстильных материалов различаются положением образцов по отношению к пламени (вертикальным, наклонным по углом 45 или горизонтальном) и продолжительностью действия пламени на образец (от 10 до 120 секунд).
|
Морозостойкость – способность материала пропитанного водой выдерживать многократное попеременное замораживание и оттаивание без ухудшения прочности и видимых признаков разрушения.
16. Характеристики оптических свойств текстильных изделий. Применяемое оборудование и методы испытаний.
Оптическими свойствами материалов называют их способность количественно и качественно изменять световой поток. В резуьтате воздействия материалов на световой поток проявляются такие свойства как цвет, белизна, блеск, прозрачность и др.
Цвет материала изделий является основным элементом зрительного восприятия. Все цвета делят на хромотические и ахромотические.
Ахроматические получаются при отражении материалом лучей всех длин волн спектра в одинаковом соотношении. При практически полном отражении всего падающего света получается белый цвет, при полном поглощении черный. При неполном – серые цвета различной интенсивности. Различают ахроматические цвета по светлоте, определяемой коэффициентом отражения К0=s0\s.Где s0 – количество отраженного света, s – количество падающего света.
Белизна является одним из важнейших показателей характеризующих качество отбеленных маериалов. Для определения белезны текстильных изделий используют фатометры, принцип действия которых состоит в сравнении белизны поверхностиизделия с поверхностью контрольной пластины, затемняемой до светлоты измеряемого объекта.
Характеризуют хроматические цвета цветовым тоном, коэффициентом отражения (светлотой), а также чистотой и насыщенностью. Для оценки хроматических цветов пользуются специальными приборами – колориметрами различных конструкций. Наиболее распространены трехцветные колориметры, работающие на принципе получения цвета, наиболее совпадающего с измеряемым, путем оптического смешения касного, желтого и синего цветов.
Блеск материалов зависит от состояния их поверхности. Для оценки блеска текстильных материалов ипользуют два метода:
- метод отражения
- гониофотометрический.
Суть первого заключается в том, что свет падает под определенным углом на исследуемый образец, а интенсивность зеркально отраженного света под таким же углом измеряется фатометром как от образца, так и от блестящей эталонной поверхности такого же размера.
Второй метод под разными углами от плоскости падения луча и построений графических кривых, которые более полно характеризуют способность материала отражать свет.
17. Характеристики электрических и акустических свойств текстильных изделий. Применяемое оборудование и методы испытаний.
Определение электрических свойств текстильных материалов
|
К электрическим свойствам относят: электризуемость, диэлектрические (электроизоляционные) свойства.
Электризуемость харктеризуется способностью материалов к генерации и накоплению в определенных условиях зарядов статического электричества.
В качестве показателя используется уровень напряженности электростатического поля (КВ\м).
Для определения электрических свойств применяются специальные электронные приборы.
Определение акустических свойств текстильных материалов
Акустическими называют свойства, характеризующие отношение текстильных материалов к звуку. Наиболее важными в них являются звукоизолирующие и звукопоглащающие.
При падении звуковой волны на текстильные изделия с энергией j (Вт\м) происходит отражение звука, поглощением его материалом и похождение звука через материал. J=Jпогл+Jотр+Jпрох
Для определения характеристики акустических свойств чаще всего определяют коэффициент звукопоглощения альфа = Jпогл\sи коэффициент звука отражения бета. Обычно звукоизолирующие свойства текстиьных материалов увеличиваются с увеличением их поверхностной плотности. Зависит звукопоглощение и от характера поверхности материала. Материалы с гладкой поверхностью отражают большую часть падающего на них звука, если же поверхность материала имеет открытую пористость, то входя в поры звуковые колебания поглащаются материалом. Для определения значений коэффициентов звукоотражения и звукопоглощения используют акустические приборы, позволяющие оценить количество отражаемой образцом материала звуковой энергии
18. Определение показателей, характеризующих изменение строение и свойств текстильных изделий в процессе эксплуатации. Применяемое оборудование и методы испытаний.
При оценки качества текстильных материалов и изделий обычно сравнивают результаты измерений показателей с нормативными до их использования, однако для оценки надежности и прогнозирования срока службы необходимо знать как эти свойства изменяются в процессе эксплуатации изделий. Одним из важнейших показателей качества текстильных материалов и изделий из них является их износостойкость. В текстильных изделиях различают износ двух видов: общий и местный. Общий распространяизделия ется по всей поверхности и делает его непригодным для конечного использования. Местный характеризуется ослаблением, появлением потертости и дыр в отдельных местах при достаточной прочности или неповрежденности значительной части изделия. Факторы износа принято делить на следующие группы: механические (истирание, растяжение, смятие и тд), физ-хим (действие света, пота, моющих веществ и тд), биологические (разрушение микроорганизмами и повреждения зоологическими), комбинированные (цветопогода, стирка, химчистка и тд).
Стойкость текстильных материалов к неориентированнаму истиранию по плоскости поверхности определяют на специальных приборах с использованием мягких или жестких абразивов (ДИТ-М, ТИ-1М) и оценивается в циклах.По ГОСТ 18976-73.Для проведения испытания применяют прибор ДИТ-М, имеющий две головки и сменные пяльцы.(для льняных и полульняных тканей).Элементарные пробы тканей, заправляют в обоймы бегунков лицевой стороной наружу, затем в них вкладывают грибки, после чего обоймы навинчивают на бегунки. Подготовленную полоску серошинельного сукна шириной 95 мм заправляют в пяльцы, на которые накладывают кольцо и закрепляют его откидными винтами. Контактную нихромовую проволоку диаметром 0,2 мм марки Х 15 Н60 закрепляют зажимами, расположенными на кольце. При заправке контактной проволоки необходимо следить, чтобы она была распрямлена, не была туго натянута и свободно лежала на поверхности абразива-сукна.Элементарные пробы тканей, подготовленные, укладывают на эластичное основание пялец (токопроводящую резину) лицевой стороной наружу. На ткань накладывают металлическое кольцо и закрепляют элементарную пробу на пяльцах с помощью обоймы. Кружки абразива (серошинельного сукна) диаметром 25 мм закладывают в обоймы бегунков, затем обоймы навинчивают на бегунки.После заправки элементарных проб ткани и абразива пяльцы с помощью рычажно-грузовой системы осторожно доводят до соприкосновения с бегунками и включают прибор.Испытание всех тканей проводят при удельном давлении абразива на ткань, равном 1 МПа (1 кгс/см2)При разрушении элементарных проб прибор автоматически выключается в результате контакта нихромовой проволоки с грибком во время испытания хлопчатобумажных и шелковых тканей и в результате контакта токопроводящей резины со щупами - во время испытания льняных тканей. После автоматической остановки прибора записывают число циклов вращения головки прибора, при котором произошло разрушение испытуемой ткани, производят смену элементарных проб ткани и абразива и продолжают испытание.За показатель стойкости ткани к истиранию по плоскости принимают среднее арифметическое результатов испытания всех отобранных от партии точечных проб.Подсчет производят с точностью до 0,1 цикла и округляют до целых единиц.
Стойкость полотен и изделий к светопогоде. Определяют двумя способами: при естественных условиях или на аппаратах искусственной погоды (АИП). Стойкость материалов к различным воздействиям (светопогоде, стирке, химчистке и тд) оценивают по их усадке, изменению окраски, стойкости к истиранию, разрывной нагрузки и тд.
19. Методы отбора проб обуви и подготовки их к испытаниям.
Отбор пробы от партии обуви осушествляется в виде выборки, представляющей собой определенный процент изделий от общего числа пар в партии, т.е. с увеличением размера партии возрастает число отбираемых для испытаний пар обуви. При этом предусматривается отбор дифферинцированого количества проб для оценки различных свойств.
Партией считают обувь, изготовленную предприятием по единым ТНПА из однородных материалов, одного вида, метода крепления низа, назначения и одного времени выпуска (за период не более 6 дней), оформленную одним документом, уостоверяющую ее качество. Результаты испытаний распространяются на всю партию.
Если они оказываются несоответствующими требованиям ТНПА, то при проведении контрольных испытаний допускается повторный отбор пробы в удвоенном количестве. Результаты повторных испытаний являются окончательными.Подготовка проб обуви к испытаниям включает 2 этапа:
1. Кондиционирование
2. Разметка и маркировка пробы, вырубание образцов в соответствии с требованиями стандартов на определенный метод испытания.
20. Характеристики прочности крепления деталей обуви. Применяемое оборудование и методы испытаний
В зависимости от метода крепления низа обуви применяют различные методы оценки прочности крепления подошв.
Для определения прочности крепления подошв, прикрепляемые химическим способами (клеевым, литьевым) используют методы основанные на отслаивании подошвы и определении затрачиваемых при этом услий. Известны различные модификации данных методов, которые при одинаковом принципе испытаний отличаются конструкцией применяемых приборов, параметрами испытаний (различный угол приложения усилий; отслаивание подошвы начиная с носочного участка по направлению к геленочному или наоборот и др.), а также характером показателя, применяемого для оценки прочности крепления (величина нагрузки отслаивания, отношение нагрузки к ширине склеянных деталей и т.п.).ГОСТ 9292-82.Для проведения испытания применяют разрывные машины марки РТ-250 или другие, обеспечивающие скорость движения нижнего зажима (100±10) мм/мин. Мощность машины не должна превышать нагрузку разрушения более чем в 10 раз. На машину вместо верхнего и нижнего зажимов устанавливают специальное приспособление.Приспособление представляет собой скобу, в которой закрепляют надетую на затяжную колодку испытуемую полупару обуви с помощью винта, входящего в штуцерную втулку колодки. Скобу устанавливают на кронштейне, прикрепляемом к штоку разрывной машины вместо нижнего зажима, и фиксируют с помощью пальцев, закрепленных в соответствующих отверстиях серьги в требуемом положении.Геленочный участок подошвы закрепляют в зажиме винтом, а гибкий хвостовик зажима закрепляют в верхнем зажиме разрывной машины. Гибкий хвостовик в процессе испытания по мере необходимости передвигают вверх.Перед проведением испытания обувь должна быть вьдержана при нормальных условиях относительной влажности (65±5)% и температуры (20±3) °С не менее 24 ч.
В обуви на утолщенной подошве с помощью сапожного ножа утоньшают подошву путем удаления верхнего ходового слоя до толщины 10-12 мм. Для удаления запрессованного геленка на подошве делают разрез по предполагаемой продольной осевой линии геленка. Затем извлекают геленок из подошвы.На каждой испытуемой полупаре обуви проставляют соответствующий порядковый номер в двух местах: на ходовой поверхности подошвы в подметочном участке и на верхе обуви.Если носочный участок низа прикреплен дополнительно гвоздями, они должны быть удалены.При испытании обуви, изготовленной комбинированными методами крепления с подошвами, прикрепленными к подложкам по всей площади, или обуви с накладными подметками дополнительно в намечаемых точках отрыва определяют ширину подошвы или подметки с погрешностью не более 1,0 мм.
При проведении испытания оторванный геленочный участок подошвы закрепляют в специальном зажиме, хвостовик которого закрепляют в середине верхнего зажима разрывной машины.
Полупару обуви закрепляют в скобе прибора винтом, при этом необходимо следить за тем, чтобы продольная линия полупары на участке следа занимала вертикальное положение. Скобу прикрепляют к штоку разрывной машины таким образом, чтобы при вертикальном положении следа подошвы на участке отрываемая часть подошвы была параллельна этому участку. Это достигается перемещением скобы в нужное положение и закреплением ее в соответствующем отверстии серьги.
Расстояние между верхним зажимом разрывной машины и носком полупары устанавливают равным 5-10 мм путем опускания или подъема штока нижнего зажима и ходового винта, в который входит шток, а также вставки гибкого хвостовика в верхний зажим разрывной машины на различную глубину.
Если после опускания штока вниз и подъема гибкого хвостовика до отказа подошва или подложка окажется неоторванной, процесс отрыва прекращают и прибор приподнимают до верхнего исходного положения. При этом специальный зажим удаляют, а концы испытуемой детали низа закрепляют непосредственно в верхнем зажиме разрывной машины. После этого продолжают отрыв.
После отрыва по линии испытуемую деталь низа освобождают из верхнего зажима.
Нагрузку фиксируют в ньютонах с погрешностью до 1 Н.
Прочность крепления подошвы полупары в обуви химических методов крепления (клеевого, литьевого, котловой и прессовой вулканизации) в Н/см вычисляют по формуле
.
Прочность крепления подошвы, накладки и подметки полупары в обуви комбинированных методов крепления (гвозде-клеевого, рантово-кпеевого и др.) в Н/см вычисляют по формуле
,
где - нагрузка отрыва в участках 1, 2, 3,..., n, Н;
- суммарная ширина рабочей части затяжной кромки с внутренней и наружной стороны в участках 1, 2, 3,..., n, см;
- ширина подошвы, накладки или подметки в участках 1, 2, 3,..., n, см;
n - количество участков по измерению нагрузок при отрыве.
Прочность крепления подошвы и других деталей низа в обуви, изготовленной с применением ниточных, гвоздевых, шпилечных или винтовых креплений оценивается путем испытания образцов, выризаемых из определенных участков обуви и включающих все элементы, участвующие в креплении. Проводят испытание прочности крепления подошв на разрывных машинах с примением специальных приспособлений. Определение прочности крепления каблука и набоек также производят с помощью приспособлений разрывной машины. Эти приспособления различаются по конструкции, но все методы основаны на отрыве каблука от следа обуви (набойки от каблука) и определении затрачиваемых при этом усилий.
Определение прочности скрепления деталей заготовки основано на вырезании из обуви образцов, на которых имеется строчка, а также образцов без строчки и испытании их на растяжение до разрыва с применением разрывной машины.
Для характеристики прочности ниточных соединений заготовки применяют два показателя: прочность шва(отношение нагрузки в ньютанах при разрыве к длине шва в см); коэффициент прочности шва, представляющий собой отношение в % прочности простроченного образца к прочности не простороченного.
21. Характеристики жесткости и эластичности деталей и узлов обуви. Применяемое оборудование и методы испытаний
Подносок и задник, входящие в конструкцию основных видов обуви, способствуют сохранению формы, приданной ей в процессе изготовления, и предохраняют стопу при эксплуатации обуви.
Действие прибора ЖНЗО-2, применяемого для оценки жесткости и эластичности подноска и задника обуви, основана на вдавливании шарового сегмента штока прибора в поверхность носочной и пяточной частей обуви и определение величин общей и остаточной деформации. Закрепленную в приспособлении прибора обувь устанавливают таким образом, что бы намечанная на образце точка, располагалась под шаровым наконечником. Наконечник опускают в намечанную точку (без нагрузки) и отмечают по индикатору перемещения штока начальное положение намеченной точки. Затем передают на наконечник соответствующую нагрузку (зависящую от вида обуви), вдавливая его в поверхность образца. Образец выдерживают под нагрузкой в течении 30 секунд и отмечают по индикатору величину общей деформации. После этого нагрузку снимают и спустя 3 минуты, в течении которых образец находится без нагрузки, вновь опускают шаровый наконечник (также без нагрузки) в ту же точку и отмечают величину остаточной деформации. Величина общей деформации характеризует жесткость подноска и задника обуви, а величина остаточной – их упругие свойства.
22. Характеристики формоустойчивости обуви. Применяемое оборудование и методы испытаний
В комплексе свойств, определяющих качество обуви, большое значение имеет ее способность сохранять при эксплуатации или хранении форму, которая является не только важной составляющей в комплексе эстетических свойств обуви, но и предопределяет удобство ее эксплуатации. Т.к. форма обуви может изменяться сразу же после снятия ее с затяжной калодке в процессе производства, принято подразделять формоустойчивость на статическую и динамическую. По статической понимают способность обуви сохранять форму после снятия ее с колодки и последующий период до начала ее эксплуатации.
Большая часть методов оценки формоустойчивости основано на измерении линейных размеров или площадей деталей верха или площади отдельных сечений обуви в какой-то момент, которому предшествовали хранение обуви или ее эксплуатация. В качестве показателя формоустойчивости применяют абсолютные или относительные значения, изменения объема обуви по сравнению с объемом соответствующей части затяжной колодки.
23. Характеристики влагообменных свойств обуви. Применяемое оборудование и методы испытаний
Процесс жизнедеятельности организма человека сопровождается так называемой неощютимой персперацией (кожным дыханием), заключающейся в непрерывном выделении с поверхности кожи паров воды и газа. В связи с этим при возникновении затруднений для удаления с поверхности тела паров воды могут содаваться условия не благоприятные для жизнедеятельности организма.
Необходимость эксперементального изучения процесса удаления влаги из обуви, разработки конструкций обуви с заданными влагообменными свойствами и обосновании требованей, предъявляемых к соответствующим свойствам обувных материалов обусловили создание ряда методов оценки влагообменных свойств. Большинство из них предназначено для оценки свойств материалов или систем материалов, моделирующих узлы обуви.
Определение паропроницаемости и пароемкости обуви в статических условиях производят на приборе типа ТНО так называемом комфорт-тестере.
Прибор состоит из камеры В, на одной из стенок которой имеется устройства для закрепления образца обуви или ее отдельных узлов; двух термостатов Е и F, обеспечивающих поддержание заданной температуры; а также двух сосудов С и D, один из которых (С) наполнен насыщенным раствором хлорида натрия, второй раствором нитрата аммония. Образец обуви или ее часть после кондиционирования взвешивания помещают внутрь камеры В (открытый участок образца при этом закрывают специальной влагонепроницаемой прокладкой). Пользуясь двумя термостатами создают заданную разницу температур внутри образца и снаружи, т.к. сосуды С и D сообщаются с пространством А внутри обуви и камерой В снаружи, то создается разница в давлении пара по обе стороны испытуемого образца. Сосуды С и D перед и после испытания подвергают взвешиванию. В результате испытания величину паропроницаемости определяют по увеличению массы сосуда D; величину пароемкости - по увеличению массы испытуемого образца. Для того, что бы приблизить получаемые характеристики к реальным условиям носки перед испытанием образец подвергают многократному изгибу в пучковой части, в результате которого на деталях верха обуви появляются складки и микротрещены.
24. Характеристики водостойкости обуви. Применяемое оборудование и методы испытаний
Методы оценки водостойкости обуви подразделяют на две подгруппы: методы испытания в статических условиях, при которых испытуемый образец находится в неподвижном состоянии и методы испытаний в динамических условиях, предусматривающих сообщение образцам механических воздействий.
Простейшие методы первой группы основаны на заполнении испытуемого образца водой и органолептическом наблюдении за скоростью промокания ее различных участков (применяют в основном для испытаний резиновой обуви и обуви из полимерных материалов) или на определении изменение массы гигроскапичного материала, помещаемого внутрь обуви, распологаемого в сосуде с водой.
Поскольку промокание обуви при эксплуатации происходит главным образом при ее повторном изгибе, большинство методов испытаний второй группы предусматривает проведение испытаний при указанной деформации образца. Данные методы отличаются конструкцией применяемых приборов, параметрами и условиями испытаний, способом определения времени до момента промокания. С целью имитации стопы внутрь обуви при этом вставляют специально изготовленные колодки. Принцип действия приборов заключается в сообщении повторного изгиба пучковой части образца обуви, помещаемый в емкость с водой и определении в этих условиях времени до момента промокания различных участков, а так же в водопроницаемости (определаемым количеством воды проникшей внутрь образца) и намокаемости (определяемым количеством воды, поглощенной образцом) за определенный период испытаний.
25. Характеристики теплозащитных свойств обуви. Применяемое оборудование и методы испытаний
Методы определения теплозащитных свойств обуви подразделяют на две основные группы:
- методы, основанные на стационарном теплообмене;
- методы, предусматривающие проведение испытаний при нестационарном теплообмене.
При использовании методов первой группы внутрь образца вставляют металлическую колодку, соответствующую форме обуви, в которую помещают электронагреватель и устройство для измерения температуры. Температуру окружающего воздуха при испытаниях поддерживают постоянной, а колодку нагревают до температуры выше температуры окружающей среды, регулируя мощность подаваемого на электронагреватель тока и следовательно выделяемого тепла достигают режима стационарного теплообмена.
Теплозащитные свойства оценивают путем определения абсолютного количества тепла, передаваемого через образец в окружающую среду за единицу времени. К недостаткам методов первой группы относятся значительная продолжительность испытаний и необходимость строгого соблюдения граничных условий.
При использовании методов второй группы испытания проводят при помощи приборов, имеющих аналогичную конструкцию, определяя темп охлаждения ядра прибора, нагреваемого выше температуры окружающего воздуха. Для оценки теплозащитных свойств используют показатели теплопроводности и суммарного теплового сопротивления.
26. Характеристики гибкости и массы обуви. Применяемое оборудование и методы испытаний
Известен ряд методов определения показателей гибкости обуви. Все они основаны на сообщении образцам изгиба в пучках на заданный угол и определении усилий, затраченных на изгиб. Чаще всего испытания проводят с применением приспособлений к разрывной машине. Большинство методов предусматривают оценку гибкости обуви в статических условиях при ее однократном изгибе или нескольких повторных изгибах.ГОСТ 9718-88.Используют:
Разрывная машина с верхним пределом нагрузок 2500 Н; скорость движения нижнего штока (100±10) мм/мин.
Приспособление, разработанное УкрНИИКП для проведения испытаний гибкости обуви, состоящее из:устройства для крепления испытуемой полупары; устройства, изгибающего носочную часть обуви по линии изгиба на угол 25°.
Устройство для крепления испытуемой полупары обуви состоит из столика, винтового прижима, платформы, стойки.Винтовой прижим снабжен двумя съемными упорами. Для испытания дошкольной и гусариковой обуви с шириной опорной части 30 мм, для остальных половозрастных групп обуви шириной 50 мм.
Устройство, изгибающее носочную часть обуви по линии изгиба, состоит из упора, подвешенного к верхнему захвату разрывной машины.
Перед проведением испытания обувь должна быть выдержана при температуре (20±2) °С и относительной влажности воздуха (65±5)% не менее 48 ч.
Приспособление для испытания гибкости обуви зажимают в разрывную машину. Испытуемую полупару обуви закрепляют в приспособление так, чтобы прижимная сила действовала по линии изгиба. Устройство, изгибающее носочную часть, устанавливают по линии приложения силы изгиба.
Приводят в действие разрывную машину и подводят упор до касания с ходовой поверхностью подошвы. Шкалу удлинения устанавливают на нулевое значение.
Повторно включив разрывную машину, изгибают обувь. Когда шкала удлинения достигает 25 мм, что соответствует изгибу обуви на угол 25°, машину останавливают и отмечают по шкале нагрузок значение приложенной силы.
На одной полупаре проводят последовательно четыре измерения с интервалом не более 3 мин.
Гибкость обуви выражают значением силы в ньютонах, отмеченной по шкале нагрузок при четвертом измерении.
Масса обуви при одинаковом размере зависит от вида и свойств применяемых материалов, конструкций обуви и особенностей технологии изготавления. Определяют ее путем взвешивания каждой полупары с точностью до 0,1 грамма. В качестве показателя как правило используют массу полупары в граммах. Кроме того принимается показатель относительной массы, представляющий собой отношение массы полупары в граммах к размеру обуви.
27. Методы оценки свойств обувных материалов.
На обувных предприятиях и предприятиях по изготовлению кожгалентереи проводят контрольно выборочные испытания качества основных и вспомогательных материалов. Номенклатура показателей качества натуральной кожи включает общие и специализированные показатели. Общие: толщина и массовая доля влаги нормируются для всех видов кожи. А специализированные – различаются для разных видов. Различия в наборе специаизированных показателей объясняется структурой и методом производства материала, а также назначением деталей из него в изделие. Следует отметить, что такие показатели гигиенических свойств как паропроницаемость, влагоемкость и влагооддача кож для верха обуви не нормируются. Свойства кожи существенно зависят от содержания в ней влаги, которая в свою очередь зависит от температуры и влажности окружающего воздуха. В связи с этим перед испытаниями образцы должны быть подвергнуты кондицеонированию. Если в помещении испытательной лаборатории невозможно достигнуть нормальных климатических условий, то для их достижения используют кондиционные шкафы. Толщину обувных материалов определяют специальными толщиномерами с ценой деления прибора в 0,01 мм. Испытание на растяжение (предел прочности, удлинение при разрыве
|
|
История развития пистолетов-пулеметов: Предпосылкой для возникновения пистолетов-пулеметов послужила давняя тенденция тяготения винтовок...
Опора деревянной одностоечной и способы укрепление угловых опор: Опоры ВЛ - конструкции, предназначенные для поддерживания проводов на необходимой высоте над землей, водой...
Состав сооружений: решетки и песколовки: Решетки – это первое устройство в схеме очистных сооружений. Они представляют...
Таксономические единицы (категории) растений: Каждая система классификации состоит из определённых соподчиненных друг другу...
© cyberpedia.su 2017-2024 - Не является автором материалов. Исключительное право сохранено за автором текста.
Если вы не хотите, чтобы данный материал был у нас на сайте, перейдите по ссылке: Нарушение авторских прав. Мы поможем в написании вашей работы!