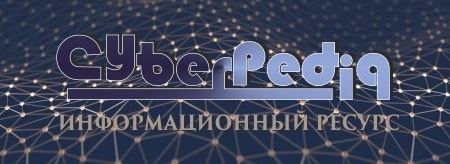
Историки об Елизавете Петровне: Елизавета попала между двумя встречными культурными течениями, воспитывалась среди новых европейских веяний и преданий...
Эмиссия газов от очистных сооружений канализации: В последние годы внимание мирового сообщества сосредоточено на экологических проблемах...
Топ:
Характеристика АТП и сварочно-жестяницкого участка: Транспорт в настоящее время является одной из важнейших отраслей народного хозяйства...
Интересное:
Национальное богатство страны и его составляющие: для оценки элементов национального богатства используются...
Искусственное повышение поверхности территории: Варианты искусственного повышения поверхности территории необходимо выбирать на основе анализа следующих характеристик защищаемой территории...
Что нужно делать при лейкемии: Прежде всего, необходимо выяснить, не страдаете ли вы каким-либо душевным недугом...
Дисциплины:
![]() |
![]() |
5.00
из
|
Заказать работу |
|
|
![]() |
Рис. 85. Схема установок для закалки с нагревом газокислородным пламенем 142 |
Нагрев деталей газо-кислородным или ацетилено-кислородным пламенем или пламенем с использованием метана, природного либо светильного газа и др. осуществляется при помощи специаль-
Рис. 86. Формы наконечников для пламенной закалки: о — плоский; б — для полутавровой поверхности; в — для закалки внутренней поверхности; г — для закалки цилиндрических тел; д — Для эакалкн зубчатых колес |
ных горелок. После нагрева следует охлаждать поверхности деталей водой, эмульсией или маслом. Эти методы нагрева применяют для деталей, которые должны обладать высокой износостойкостью и не могут быть обработаны обычными методами (крупные зубчатые колеса диаметром 800 мм и более, валы, направляющие и др.).
В качестве закалочных машин на практике чаще всего применяют токарные станки, с помощью которых можно осуществить поступательное движение горелки и вращение детали (рис. 85, а).
Места закалки Рис. 87, Газопламенная закалка зубчатых колес для каждого зуба: / — горелна; 2 — зубчатое колесо |
Схема установки для газопламенного нагрева цилиндрической детали показана на рис. 85, б. Четыре горелки 1 для пламенной закалки неподвижно укреплены в специальных державках 2. Нагреваемый шпиндель 3 вращается. Сверху установлен оптический пирометр 4 для контроля температуры. Однако для контроля теплового цикла чаще используются сигнальные электрочасы с секундной и минутной фиксацией времени. После окончания нагрева детали охлаждаются в закалочном баке.
Для закалки с нагревом газо-кислородным пламенем используют обычные сварочные горелки с набором наконечников (рис. 86). Горелки разделяются на однопламенные, щелевидные и многопламенные. На рис. 87 показана схема газопламенного нагрева зубчатых колес. Горелка (рис. 86, д) передвигается вдоль зуба. Нагрев происходит с двух сторон и ведется для каждого
|
ИЗ
зуба отдельно (глубина нагретой и закаленной части зуба заштрихована).
Горелки скоростного нагрева (рис. 88, о и б) установлены по окружности зубчатого колеса на небольшом расстоянии друг от друга вблизи вершин зубьев.
Рис. 88. Нагрев зубчатых колес специальными горелками:
а — радиационного типа; б — конвекционного типа; / — горелка; 2 — зубчатое колесо
Для закалки крупных зубчатых колес применяют также установки, в которых осуществляется движение газо-кислородной горелки и расположенного за ней устройства, подающего воду вдоль образующей зуба колеса по всей его длине. Пламя горелки движется вдоль зуба со скоростью около 120 мм/мин и с той; же скоростью движется струя воды.
§ 35. УСТАНОВКИ ДЛЯ КОНТАКТНОГО НАГРЕВА И ИНДУКЦИОННЫЙ НАГРЕВ Т. В. Ч.
Метод контактного поверхностного нагрева, разработанного Н. В. Гевелингом,-заключается в следующем: электрический ток от трансформатора при помощи специального медного электрода-ролика подводится к поверхности обрабатываемой детали. В месте соприкосновения ролика с деталью происходит нагрев вследствие большой плотности тока, доходящей до 450 а на 1 мм ширины ролика. Электрическая схема установки для контактного нагрева приведена на рис. 89.
Поверхностной закалке с контактным нагревом подвергаются шейки шпинделей станков, шейки коленчатых валов, головки рельсов, направляющие станков и т. д. Для закалки с контактным нагревом также могут быть использованы различные металлообрабатывающие станки. Например, для закалки тел вращения диаметром до 200 и длиной до 1500 мм может быть использован токарно-винторезный станок.
Охлаждение деталей при закалке производится водой или эмульсией, подача которых осуществляется насосом в количестве
|
25—30 л/мин. Баки для жидкости емкостью 300—500 л помещают под корытами станков или в углублении пола. Иногда используют воду непосредственно из водопроводной сети со спуском в канализацию. Для контактного нагрева и закалки плоских поверхностей могут быть использованы горизонтально-фрезерные или продольно-строгальные станки.
Сущность методов поверхностной закалки с нагревом т. в. ч.
заключается в следующем. При пропускании т. в. ч. через индук
тор внутри него возникает
переменное магнитное тюле. ~50гк
ft-t |
I! |
■_пз*а |
![]() |
Если в зону этого поля поместить стальную деталь, подлежащую нагреву, то в ней будет возбуждаться той же частоты индуктированный ток, который концентрируется в небольшом поверхностном слое и вызывает нагрев этого слоя до высокой температуры. В зависимости от применяемой частоты различают повышенную частоту — от 500 до 1.0 000 гц и высокую частоту — от 50 000 до 1 млн. гц1.
Машинный генератор
Рис. 89. Электрическая схема установки для контактного нагрева: / — двухполюсный рубильник; 2 — пульт управления; 3—магнитный пускатель; 4 —автотрансформатор; 5 — силовой трансформатор; 6 — гибкие шины; 7 — калящие ролики; в — нагреваемая деталь |
представляет собой установку, состоящую из электродвигателя трехфазного тока и соединенного с ним генератора, дающего ток высокой (повышенной) частоты. Двигатель и генератор монтируют в одном агрегате (мотор-генератор). При работе мотор-генераторов их обмотки нагреваются, поэтому мотор-генераторы охлаждают воздухом или оборудуют специальным устройством с водяным охлаждением.
Существуют следующие типы преобразователей повышенной частоты: ПВ, ПВВ и ПВС (о дно корпусные горизонтальные), ВГО и ВПЧ (вертикальные).
1 Частота в интервале 10 000—50 000 гц в практике применяется редко. 10 С. Л. Рустем 145 |
Преобразователь типа ПВ состоит из генератора однофазного тока повышенной частоты индукторного типа с независимым возбуждением и трехфазного асинхронного двигателя, смонтированных в одном корпусе. Преобразователи серии ПВВ предназначаются для установки непосредственно в термических цехах.
![]() |
о ел |
о о |
t-. чо" |
CO |
CO |
CO CO" |
CO_ сеГ 1Л |
![]() |
3-50ги |
Преобразователи типа ВГО изготовляют с воздухоохладителями, расположенными в специальных проемах фундамента под агрегатом и смонтированными на машинах. При работе агрегатов серии ВГО создается значительный шум. Вертикальные преобразователи типа ВПЧ предназначены для работы в закрытом вентилируемом помещении. Они изготовляются вертикаль-
|
Рис. 90. Схема высокочастотного нагрева при питании от машинного генератора:
а ■— схема установки: б — схема преобразования тока: / — магнитный пускатель; 2 — автотрансформатор; 3 — выпрямитель; 4 — контактор пусковой; 5 — преобразователь повышенной частоты: б — обмотка возбуждения преобразователя; 7 —■ контактор повышенной частоты; S — конденсаторная батарея; 9 — закалочный трансформатор; 10 — индуктор; II — нагреваемая деталь
ными, закрытыми с воздушно-водяным охлаждением. Приводные двигатели преобразователей асинхронные с короткозамкнутым ротором с синхронной скоростью вращения 3000 об/мин. Эти агрегаты требуют меньшей площади. Закрытое исполнение сокращает шум и позволяет устанавливать их непосредственно в цехе. Характеристика преобразователей повышенной частоты серии ВПЧ приводится в табл. 6. Схема высокочастотного нагрева с применением машинного генератора и преобразования тока представлена на рис. 90.
Одним из основных элементов установки для высокочастотного нагрева является индуктор. Его изготовляют из медных трубок круглого и прямоугольного сечения. Толщина стенок индук-
в
I
3* С as
I
О
к к
U
а а
о
о с
IS
S
а. С
10»
э1 С в
В" С
m
о1 П
6 & |
S т с
Э1
с
3"
с
Я"
с
га
О CD О LO
S |
о ел о со
со —
о |
е> ел Э
s; |
-is-
![]() |
г |
-J о-Г
со
о со |
8 3s Я
CO
CD
о со |
lis
со
о _"
о С] |
§~8
4"ira ю
о _*- ю
о см |
§ = 8 t£
CO 00 t~-
о c |
j Я
о о u га |
и 5 о |
и и м и
N. | |
-^ | о |
•J'-i. | CTJ |
со | о |
CN | |
•а1 | |
77 45/25 | о со о" |
■ч-ю
о
СО
О) ,сч |
о"
1!Ъ
о"
О) Г- |
- й-
ю о о
о'5 ■»
СО I-. О
ю
*| S
о ОО о' |
со
■-1 см со
р |
ш
J
я |
Ч>"5 о
S3; |
1ГЭ |
1 СО
со
о СО |
1С |
I
о со со |
ю со |
3S о £2 Ш
о СО |
ю СО |
82 g 22 Ш
|
о ГО | ОО t-~ О СГ> СО | |||||
о | о | о О) О о со | ||||
ю СМ | 0 о 01 СО | |||||
СМ | 1090 800 | |||||
CO """ | т g | |||||
3 <u * и з 5 & ag4gJ | fa | flit | ||||
Тора зависит от частоты генератора. При частоте 1000 гц толщина стенки индуктора должна быть 2,7 мм, а при частоте 8000 гц — 1,1 мм. Индуктор имеет форму, соответствующую конфигурации нагреваемой детали. Охлаждение индуктора во время работ производится водой, протекающей внутри индуктора. Индукторы для высокочастотного нагрева деталей показаны на рис. 91.
Рис. 91. Индукторы для нагрева т. в. ч,:
а — многовитковый индуктор нз медной трубки круглого сечения. 6 — разъемный индуктор с душнрующин устройством, в — трехвитвовый индуктор для нагрева внутренней поверхности, г — индуктор для нагрева цилиндрической поверхности при вертикальном движении детали и ее вращении, д -~ индуктор для местного нагрева плоских деталей. е — индуктор для термической обработки коренных шеек коленчатого вала, I — место нагрева, 2 — тоноподводящие щеки, 3 — штуцер для охлаждающей воды. 4 — магните-
провод, 5 — прокладка
Закалка производится погружением детали после нагрева в закалочный бак или охлаждением с помощью специального устройства, которое располагается вблизи индуктора или в самом индукторе; в этом случае в индукторе имеется вторая полость, в которой со стороны нагреваемой детали расположены мелкие отверстия, после нагрева детали вода автоматически поступает во вторую полость и направляется под давлением на нагретую. часть детали. В других случаях индуктор имеет одну полость с отверстием для закалочной воды и для того, чтобы не было сильного нагрева индуктора (не более 200—300° С), толщина стенки его увеличивается до 7—10 мм. Машинные генераторы применяют в том случае, когда обрабатывают однородные детали достаточной толщины или диаметра (не менее 16 мм) при глубине закаленного слоя яе менее 1,2 мм. Машинные генераторы имеют высокий к. п. д., равный 0,7—0,8, и требуют сравнительно простого обслуживания, что позволяет успешно использовать их в массовом производстве. Например, машинные генераторы применяют для поверхностного нагрева и закалки шеек коленчатых валов и других деталей в автомобильной и тракторной промышленности.
Ламповые генераторы преобразуют электрический ток промышленной частоты (50 гц) в ток высокой частоты. В ламповом генераторе отсутствуют вращающиеся и трущиеся детали. Ток высокой частоты получается в генераторных лампах различной мощности. В практике термической обработки применяют частоты 200 000—500 000 гц.
Принципиальная схема работы лампового генератора показана на рис. 92, а и б. К первичной обмотке 1 трансформатора генератора подводится переменный ток промышленной частоты и низкого напряжения (220 или 380 в). Во вторичной обмотке 2 трансформатора напряжение тока повышается примерно до 8000 в. Затем переменный ток высокого напряжения проходит через газотронный выпрямитель 3 и превращается в постоянный ток высокого напряжения. Далее постоянный ток подается на анод 4 генераторной лампы, дающей ток высокой частоты. Полученный т. в. ч. имеет высокое напряжение и не пригоден для питания индуктора, так как требует увеличения зазора между индуктором и нагреваемой деталью и, следовательно, понижает к. п. д. нагрева. Поэтому ток подвергается еще вторичному преобразованию в высокочастотном трансформаторе 5, во вторичной обмотке которого напряжение.понижается до 1000 е. Отсюда ток поступает в индуктор 6 и нагревает деталь 7. Напряжение на индукторе зависит от типа установки и размеров индуктора и составляет от 30 до 300 в. Как видно из схемы, ток в ламповых генераторах претерпевает несколько преобразований. Каждое преобразование вызывает потерю мощности, вследствие чего к. п. д. лампового генератора не превышает 60%. Конструкции установок с ламповыми генераторами за последнее время значительно улучшены, они
|
стали более надежными и имейт более высокие эксплуатационные показатели. Типы и характеристика высокочастотных установок с ламповыми генераторами представлены в табл. 7.
Индукторы для ламповых генераторов изготовляют по тому же принципу, что и для машинных генераторов, но вследствие более высокой частоты индукторы для ламповых генераторов могут быть изготовлены из трубок с меньшей толщиной стенки (около 0,5—1,0 мм). Использование для индукторов трубок прямоуголь-
Рис. 92. Принципиальная схема лампового генератора
ного сечения дает увеличение его к. п. д., так как при прямоугольном сечении имеется большая внутренняя поверхность и, следовательно, уменьшается сопротивление.
Для закалки деталей машин с нагревом т. в. ч. применяются закалочные станки. Такие станки могут быть специализированными — для обработки отдельных деталей в массовом и крупносерийном производстве и универсальные — когда могут быть использованы для обработки различных деталей по размерам и форме. На закалочном станке ВЧ1-63-ЗП можно обрабатывать детали как при непрерывно последовательном нагреве (закалка длинных деталей осей, валиков и др.), так и при одновременном нагреве коротких деталей или отдельных участков длинных деталей. Станок имеет программное устройство с системой передвижных кулачков. На станке установлены подвижная каретка, гидропривод для вращения деталей и спрейер, а также индуктор, который закреплен на закалочном трансформаторе станка. Кроме того, на станке расположены привод, электрооборудование элек-
Таблица 7
Технические характеристики установок для поверхностной закалки и сквозного нагрева с ламповыми генераторами
Параметры | ЛЗ-13 | Л31-25 | Л32-67 | Л 3-107 В |
Для поверхностной закалки * | Для поверхностной закалки и сквозного нагрева ' | |||
ВЧИ-10/О.44-ЗП | а т о о" & К | ВЧИ-63/0.07-ЗП ВЧИ-63/0.07-НС | су §1 m ей | |
Напряжение питающей Колебательная мощ- Частота в кгц.... Колебательная мощность, потребляемая от сети, в ква... Тип генераторной лам- Анодное напряжение Производительность за каленного объема в смг1мин..................... Расход охлаждающей воды на установку (без учета закалочной воды), в м3/ч.... Вес установки в кг.. | 220 или 380 10 440±2,5% ГУ-ЮЛ 2,0 860 | 220 или 380 +12 66—10% ГУ-4А 10,5 3,2 1900 | 380 63 + 12 66—10% ГУ-23А 10,5 5,0 2400 | +12 66—10% ГУ-23А 11,0 6,5 3500 |
' Первые три буквы обозначают вид нагрева: ВЧИ — высокочастотный индукционный (в магнитном поле индуктора:), дробь обозначает: числитель — колебательная мощность в кет, знаменатель — рабочая частота в Мщ, ЗП -закалка поверхностная и НС — нагрев сквозной. |
трогидравлические клапаны для подачи воды в гидропривод и спрейер, а также пульт управления. Все управляющие кнопки, ручки и аппаратура контроля и сигнализации вынесены на лицевую панель. Детали для закалки устанавливают между верхним и нижним центрами каретки. Короткие и плоские детали закрепляются в планшайбах или патронах, устанавливаемых на нижней траверсе каретки вместо центра. Нажатием соответственных кнопок задается программа закалки. Во время закалки открытая часть станка закрывается опускающейся прозрачной шторой из оргстекла. Последовательность операций производится автоматически, кроме того, на станке имеется и ручное управление операциями.
Техническая характеристика станка ВЧ1-63-ЗП следующая: диаметр закаливаемых деталей до 90 и длина до 900 мм, скорость рабочего хода каретки 2—20, холостого 90 мм1сек, скорость вращения деталей 200—300 об/мин, давление закалочной воды 2—6 атм, расход закалочной воды 50 л!мин, расход воды на гидропривод 10 л/мин, давление воды на гидропривод не менее 2 атм, потребляемая мощность 0,7 ква, напряжение питающей сети (частотой 50 гц) 380—220 в.
Для сложных деталей в массовом производстве изготовляют специальные закалочные станки Для закалки коленчатых валов автомобиля был сконструирован полуавтоматический станок [351, который работает от машинного генератора (частота 2000— 3000 зц, мощность 150 кет). В станке смонтировано 13 разъемных индукторов, питаемых от двух трансформаторов. Одна половина каждого индуктора находится в верхней поднимаемой части, а другая половина — в нижней, неподвижной части станка. После установки вала в центрах его зажимают вручную в трех точках по одной шейке с помощью штифтов люнета. Нагрев и охлаждение шеек коленчатого вала происходят последовательно. Продолжительность нагрева и мощность регулируют с помощью электроавтоматики. После окончания нагрева снимают напряжение и через индукторы подают воду для закалки шеек. После нагрева первой шейки происходит включение электродвигателя, который переводит коммутатор и распределители в положение для нагрева следующей шейки и т. д. Продолжительность нагрева одной шейки составляет 3,7—7 сек, охлаждение водой нагретой шейки 7,5 сек. Процесс нагрева и закалки всех шеек длится 2,4 мин, загрузка и разгрузка I мин 40 сек. Следовательно, производительность установки составляет 35 валов в час. Коленчатый вал закаливается на глубину 2—4 мм.
В дальнейшем этот станок был модернизирован так, что вал укреплялся в станке по двум коренным шейкам с помощью двух автоматически действующих люнетов, вследствие чего уменьшалась деформация вала. Перевод коммутатора и распределителей осуществлялся при помощи храпового механизма с гидроприводом вместо электродвигателя. Для удобства загрузки валов верхняя часть станка не поднимается, а поворачивается на шарнирах, что облегчает загрузку валов в станок с помощью подъемных механизмов. Весь процесс нагрева и закалки осуществляется в двух механизированных станках. В первом станке закаливается шесть шеек, а во втором остальные семь шеек коленчатого вала; производительность установки из двух станков вследствие указанных изменений возрастает вдвое и составляет 30 валов в час.
Для закалки зубчатых колес малого модуля можно применять нагрев т. в. ч. с самоотпуском, например, для зубчатых колес коробок скоростей станков с модулем 3 мм, изготовленных из стали 40Х, рекомендуется нагрев со скоростью 30 град/сен в индукторе шинного типа.
![]() |
Для последовательной закалки зубьев зубчатых колес С модулем m ^ 6 может быть использован другой станок. Процесс работы на этом станке заключается в следующем. Зубчатое колесо на специальном приспособлении помещается в бак. С помощью пневматического устройства приспособление поднимает колесо из воды так, что зуб колеса попадает в индуктор, и начинается нагрев зуба. После окончания нагрева генератор отключается и воздушный клапан перекрывается электромагнитом, вследствие чего поршень в цилиндре опускается, все колесо с приспособлением погружаете^ в воду и происходит охлаждение нагретого зуба. При этом зубчатое колесо поворачивается на один зуб. Затем цикл повторяется со вторым зубом и т. д. 118].
Для равномерного нагрева зубьев колеса необходимы разные зазоры между индуктором.. и нагреваемым зубом. В средней части зуба зазор должен быть меньше, чем у торцов. Если принять зазоры одинаковыми, то торцы будут перегреваться. Величина зазора между торцом зуба и индуктором не Должна превышать 8—10 ММ. Рис. 93. Индуктор с железным маг-
Для того чтобы предохра- нитопроводом
нить от индукционного нагрева
смежные закаленные зубья, рекомендуется надевать на них экраны, изготовленные из листовой меди (толщина —2 мм). При отсутствии экрана повторный нагрев закаленного зуба образует отпущенную полосу с пониженной твердостью. Нагрев одного зуба происходит в течение 12 сек от лампового генератора типа ЛГ-60 с частотой 300 000 гц. Весь -цикл нагрева и охлаждения одного зуба продолжается 25 сек. При использовании последовательного нагрева впадина между зубьями зубчатых колес не закаливается и у основания зуба образуются растягивающие остаточные напряжения, которые снижают прочность. Для повышения прочности зубьев цилиндрических колес с модулем т ^ 10 производят закалку «по впадине».
Для закалки этим.методом применяют индуктор с железным war нитопроводом (рис. 93). Магнитопровод J собирается из П-образных пластин трансформаторной стали толщиной 0,35 мм. Сбоку магнитолровода установлены медные экраны 2, которые охлаждаются водой. Вода подается по патрубкам 3; выходя из отверстий в экранах, она охлаждает закаливаемое зубчатое колесо. Токопровод 4 отделен от магнитопровода изолирующими миканитовыми прокладками. Питание индуктора осуществляется
С помощью шин 5 и 6 от машинного генератора токов повышенной частоты.
Для закалки крупногабаритных цилиндрических, шевронных и конических зубчатых колес Всесоюзный проектно-технический институт тяжелого машиностроения разработал и внедрил полуавтоматический станок. На станке можно осуществлять непрерывно-последовательным методом по впадине зуба закалку зубчатых колес диаметром 300—2000 мм, с модулями 10—50 мм,
![]() |
с длиной зуба 60—1000 мм и весом до 7 т.
Рис. 94. Схема двухчастотного нагрева зубчатых колес: а — в двух индукторах: б •— в одном индукторе с переключением |
Для закалки зубчатых колес среднего модуля по кон-ТУРУ зуба применяют двухча-стотный нагрев, при котором зубчатое колесо сначала нагревается в одновитковом индукторе, охватывающем его по высоте зуба, от генератора повышенной частоты, например, 5000—2000 гц. Глубина проникновения тока будет больше половины высоты зуба. Нагрев начнется во впадинах зубьев, так как сами зубья поглощают при этом меньше электромагнитной энергии. При переносе зубчатого колеса в индуктор, соединенный с высокочастотным генератором, или при переключении питания индуктора на генератор высокой частоты (—300 000 гц) будет выделяться тепло в головках зубьев, а при дальнейшем охлаждении происходит закалка по контуру всех зубьев. Схема двухчастотного нагрева представлена на рис. 94. Для применения этого способа нагрева нужны два генератора и, кроме того, требуется дополнительная площадь для их размещения.
Для достижения контурной закалки зубчатых колес среднего модуля с одного нагрева К. 3. Шепеляковским было предложено изготовлять зубчатые колеса из сталей, имеющих более низкую прокаливаемость по сравнению с применяемыми. Исследования показали, что зубчатые колеса диаметром 180 мм, изготовленные из малопрокаливающейся стали марки 55ПП (0,55—0,63% С; Мп<0,2%; Si ^ 0,3%; Cr^0,15%; Ni<0f25%; P *S 0,04% и S«SO,04%), после нагрева в кольцевом индукторе на высокочастотной установке мощностью 100 кет с частотой 8000 гц и последующего охлаждения имеют контурную закалку, высокую
![]() |
прочность зуба и минимальную деформацию. Если для глубоко-прокаливающихся сталей глубина закалки определяется глубиной нагрева, то для сталей с низкой прокаливаемостью глубина закалки меньше глубины нагрева. Осуществление этого принципа нашло отражение в создании автоматической установки для контурной закалки цилиндрических шестерен заднего моста автомобиля. На такой установке выполняют индукционный нагрев до закалочной температуры, охлаждение при подаче воды в зазор между индуктором и деталью (рис. 95) и низкий самоотпуск.
Все вспомогательные операции: продвижение деталей по конвейеру, загрузка деталей в индуктор и выдача их обратно, продвижение по конвейеру закаленных деталей также осуществляются автоматически. Установки отличаются следующими конструктивными особенностями: загрузка деталей в индуктор и выдача их обратно производится автоматической рукой с электромагнитом.
Рис. 95. Схема подачи закалочной воды в зазор между индуктором и деталью: / — патрубок для подвода закалочной воды; 2 — основание для крепления индуктора и установки детали; 3 — индуктор; 4 — отражатель воды; S — зубчатое колесо |
Управление автоматической рукой осуществляет программный копирный барабан; протекание отдельных элементов процессов по времени осуществляется программным устройством, действующим на систему концевых выключателей; охла-ждениедеталей выполняется с помощью мощной системы, состоящей из центробежного насоса и специально сконструированного автоматического пневмогидравлического клапана. Поток закалочной воды в индукторе составляет 105 л/сек. Для снижения расхода воды служит замкнутая система циркуляции. Поэтому фактическое потребление воды установкой составляет'2—3 л/сек, т. е. 7—10 мЧч; нагрев до требуемой температуры выполняется с применением электромашинного усилителя и зеркальных приборов — индикаторов режима нагрева.
На ЗИЛе разработана поверхностная закалка с глубинным индукционным нагревом. Сущность этого процесса заключается в том, что нагрев производится значительно глубже, чем необходимо для закалки на мартенсит, а используемая сталь должна иметь ограниченную прокаливаемость. Таким образом, при закалке детали за мартенситным слоем следует троостит или сорбит закалки, вследствие чего наблюдается упрочнение сердцевины и повышение статической и усталостной прочности. Для
1S5
глубинного нагрева применяют стали регламентированной прока-ливаемости (обозначаемые РП), т. е. стали, прокаливаемость которых согласована с размером сечения деталей. Так, например, сталь марок 47ГТ и 45Г может применяться для нагрева деталей с сечением 40—50 мм. На ЗИЛе эту сталь используют для полуосей автомобиля ЗИЛ-130. Полуоси подвергают при закалке глубинному индукционному нагреву. На автоматической установке используется программное регулирование режима и при достижении необходимой температуры дается изотермическая выдержка в течение времени, необходимого для сквозного нагрева деталей.
таких деталей применяют метод экранирования торца. В этом случае деталь устанавливают на экран, которым может служить обычный огнеупорный кирпич, погруженный в электролит. Экрану может быть придана нужная форма поверхности, соответствующая конфигурации нагреваемой детали, вследствие чего плотность тока на торце детали не увеличивается, и нагрев получается однородным.
Для деталей цилиндрической формы поверхностный нагрев производится путем вращения детали и погружением при этом требуемой части де,тали в электролит, где она нагревается за один или несколько оборотов.
![]() |
§ 36. НАГРЕВ В ЭЛЕКТРОЛИТЕ
Одним из способов поверхностного нагрева деталей является нагрев в электролите, разработанный и впервые практически примененный на Харьковском тракторном заводе И. 3. Ясного-родским. Принцип нагрева в электролите заключается в следующем. Если пропустить постоянный ток через водный раствор электролита, то на катоде будет выделяться водород, а на аноде — кислород. Ток при достаточно высоком напряжении (220—300 в),
![]() |
проходя через большое сопротивление, каким является водородная оболочка, производит нагрев газовой оболочки, а через нее тепло передается катоду (рис. 96). Если после нагрева детали до температуры закалки выключить ток, то вследствие охлаждения раствором, находящимся в ванне, происходит закалка детали.
Рис. 96. Схема нагрева вэлектролите: / — нагреваемая деталь (катод); 2 — электролит; 3 — водородная оболочка; 4 — источник тока; 5 — анод |
Скорость нагрева в электролите зависит от состава и концентрации раствора (электролита), а также от напряжения и плотности тока. Для равномерного нагрева температура электролита должна быть постоянной 50—70^ С. Нагрев в электролите может быть произведен путем погружения детали в электролит. Нагрев может быть также местный и поверхностный, последовательный и при неподвижном экранированном катоде. При местном нагреве может быть также произведен нагрев конца, например, штоков клапанов, регулировочных винтов и других деталей. При этом способе деталь погружается в электролит на определенную глубину. К раствору подводят положительный полюс, а к детали — отрицательный. Однако детали с изменяющимся сечением или со сложным профилем торца нельзя нагревать этим способом, так как плотность тока на острых кромках и выступающих частях будет повышенной, что вызывает их оплавление. Поэтому для
От Ыйнш мтмтреви —_ <Jj _—_ ^ чвнапвзашид
Рис. 97. Схема автомата АЭ-5:
/ — вункер; 2 — питатель; 3 — приспособление для загрузки в бункер; 4 — генератор; Б — ванна нагрева; 6 — шина; 7 — устройство для удаления паров из ванн; в — закалочная ванна; 9 — мойка
Поверхностный нагрев может быть также произведен струей электролита: раствор под напором подводится через трубки на поверхность вращающейся детали (например, кулачкового валика). Расстояние конца трубки от нагреваемой поверхности составляет 20—30 мм. К трубке с раствором подводится ток 220 е, трубка с раствором является анодом, а деталь — катодом. Стекающий раствор перекачивается насосом в резервуар, охлаждается и подается вновь.
При последовательном нагреве в электролите деталь цилиндрической формы пропускается через электролит так, что в контакте с электролитом в каждый отдельный момент находится только часть детали. Нижняя часть детали проходит через изолирующую втулку, где она нагреву не подвергается.
Для повышения производительности при обработке в электролите используют автоматы, Автомат, показанный на рис. 97,
служит для нагрева концов стержней клапанов автомобильных и тракторных двигателей. Процесс нагрева, закалки в масле и мойки полностью автоматизирован. В результате этого автомат может быть встроен в автоматическую линию изготовления клапанов. Для термической обработки клапанов с помощью автомата АЭ-5 клапаны загружают в бункер, затем с помощью щелевого шибера они поступают на конвейер, по которому движутся до упора. Здесь они захватываются по одному зажимным приспособлением, устанавливаются на необходимую длину так, чтобы закаленная часть стержня была 3— 4 мм, и при помощи копира опускаются в ванну с электролитом. В качестве электролита используется 15%-ный водный раствор кальцинированной соды. После нагрева в течение 4—5 сек клапан поступает в масляный закалочный бак и охлаждается в течение 7 сек, а затем попадает в моечный бак с проточной водой. Напряжение постоянного тока 180+а в. Потребляемая мощность установки 7—10 кет. Производительность 1200 клапанов в час.
§ 37. НАГРЕВ И ОХЛАЖДЕНИЕ В КИПЯЩЕМ СЛОЕ
Кипящий или псевдоожиженный слой — это среда, которая может служить для охлаждения и для нагрева деталей. Псевдоожижение заключается в интенсивном перемешивании твердых
Рис. 98. Установка с кипящим слоен |
частиц, например кварцевого песка, корунда, дробленой руды, восходящим потоком газа. Устройство для получе- газ ния псевдоожиженного слоя показано на рис. 98, а. В цилиндр / на газораспределительную решетку 3 помещается измельченный материал, а под решетку подводится газ. При достаточной скорости газа, называемой критической,твердые частицы приобретают подвижность, и слой становится похожим на вязкую жидкость. Вследствие движения газа получается перемещение частиц, и это интенсифицирует процессы теплоотдачи, которая регулируется количеством подаваемого газа. Коэффициент теплоотдачи с увеличением скорости газа сначала растет, достигает максимальной величины, а затем постепенно уменьшается [7 ]. Максимальное значение коэффициента теплоотдачи зависит от тепло-158
проводности газа, от степени измельчения частиц среды. Кипящий слой может быть использован как охлаждающая и закалочная среда.
Скорость охлаждения в кипящем слое можно отрегулировать так, что она будет меньше, чем скорость охлаждения на воздухе, с другой стороны, охлаждение может быть в 10 и более раз интенсивнее, чем на воздухе. Интенсивность охлаждения может быть увеличена увлажнением зернистой среды, при этом коэффициент теплоотдачи увеличивается в 1,5—2 раза.
Скорость охлаждения в кипящем слое можно отрегулировать так, что она может быть равна скорости охлаждения в масле или в низкотемпературных соляных ваннах; в кипящем слое может быть проведена изотермическая обработка.
Закалочная среда, близкая к свойствам масла, может быть получена в кипящем слое при дополнительном вибрировании слоя. Такая среда называется вибропсевдоожиженным слоем. Цилиндру, в котором находятся твердые частицы, сообщается колеба
|
|
Таксономические единицы (категории) растений: Каждая система классификации состоит из определённых соподчиненных друг другу...
История создания датчика движения: Первый прибор для обнаружения движения был изобретен немецким физиком Генрихом Герцем...
Адаптации растений и животных к жизни в горах: Большое значение для жизни организмов в горах имеют степень расчленения, крутизна и экспозиционные различия склонов...
Семя – орган полового размножения и расселения растений: наружи у семян имеется плотный покров – кожура...
© cyberpedia.su 2017-2024 - Не является автором материалов. Исключительное право сохранено за автором текста.
Если вы не хотите, чтобы данный материал был у нас на сайте, перейдите по ссылке: Нарушение авторских прав. Мы поможем в написании вашей работы!