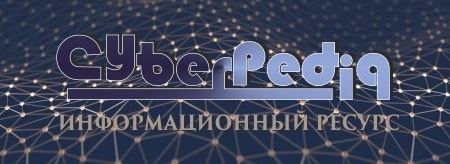
Общие условия выбора системы дренажа: Система дренажа выбирается в зависимости от характера защищаемого...
Поперечные профили набережных и береговой полосы: На городских территориях берегоукрепление проектируют с учетом технических и экономических требований, но особое значение придают эстетическим...
Топ:
Организация стока поверхностных вод: Наибольшее количество влаги на земном шаре испаряется с поверхности морей и океанов...
Особенности труда и отдыха в условиях низких температур: К работам при низких температурах на открытом воздухе и в не отапливаемых помещениях допускаются лица не моложе 18 лет, прошедшие...
Основы обеспечения единства измерений: Обеспечение единства измерений - деятельность метрологических служб, направленная на достижение...
Интересное:
Наиболее распространенные виды рака: Раковая опухоль — это самостоятельное новообразование, которое может возникнуть и от повышенного давления...
Лечение прогрессирующих форм рака: Одним из наиболее важных достижений экспериментальной химиотерапии опухолей, начатой в 60-х и реализованной в 70-х годах, является...
Распространение рака на другие отдаленные от желудка органы: Характерных симптомов рака желудка не существует. Выраженные симптомы появляются, когда опухоль...
Дисциплины:
![]() |
![]() |
5.00
из
|
Заказать работу |
|
|
Патентная проработка
Методы повышения эффективности ректификационных колон.
Введение
Понятием «ректификация» обозначают процесс разделения гомогенных бинарных и многокомпонентных смесей летучих жидкостей за счет двустороннего массообмена и теплообмена между неравновесными газообразной (паровой) и жидкой фазам и, движущимися противоположно друг другу. Во время ректификации разделяемой смеси одновременно протекают процессы ее частичного испарения и конденсации.
Разделение смесей обычно осуществляется в противоточных колонных аппаратах с контактными элементами (на садками и тарелками) при многократном, либо непрерывном контакте фаз. При каждом контакте фаз из жидкой разделяемой смеси преимущественно испаряется низкокипящий компонент, обогащающий пары, а из паровой фазы происходит конденсация и переход в жидкость преимущественно высококипящего компонента.
Ректификация является одним из наиболее важных технологических процессов химической промышленности, без которого немыслимы нефтеперерабатывающие, спиртовые и многие другие производства. Область применения ректификации в химической технологии постоянно расширяется. Особенно процесс важен при производстве веществ высокой чистоты.
Литературный обзор
В процессе ректификации одной из важнейших технологических задач является воздействие на его протекание с целью получения продуктов необходимой чистоты.
В ходе проектирования ректификационной колонны такое воздействие возможно путем увеличения числа тарелок или высоты слоя насадки, а также использования наиболее эффективных конструкций тарелки или типа и размера элементов насадки.
|
В ходе эксплуатации ректификационной колонны повысить чистоту продуктов можно, повышая флегмовое число R – увеличением потока флегмы при сохранении отборов дистиллята и кубового остатка, если кипятильник и конденсатор рассчитаны с некоторым запасом и позволяют повысить тепловую нагрузку – уменьшением производительности колонны по исходной смеси, а значит, и по продуктам при этом, сохраняя поток флегмы и понижая дистиллят, получают более высокое R. Повысить флегмовое число можно также путем захолаживания флегмы, т. е. возвращения ее в колонну при температуре ниже температуры дистиллята холодная флегма будет нагреваться в верхних зонах колонны до температуры кипения за счет конденсации части парового потока, и поток флегмы по колонне возрастает.[1]
Известна ректификационная колонна для разделения трехкомпонентной смеси, содержащая вертикальный корпус с тарелками и продольную вертикальную перегородку, пересекающую часть тарелок и разделяющую корпус колонны на вертикальные секторы. Колонна содержит регулятор потоков флегмы и регулятор потоков паровой фазы.
Известен аппарат колонный с колпачковыми тарелками. В этом
колонном аппарате с колпачковыми тарелками корпус выполнен из царг, между их
основаниями зажаты опорные кольца, на которые опираются тарелки с эластичными
уплотнениями. Центральные опоры снабжены фиксаторами. Основание тарелки
куполообразное. Все элементы колонны выполнены из фторопласта и предназначены для обработки коррозионно-активных материалов.
Недостаток обеих перечисленных колонн заключается в том, что в них в силу
жесткого закрепления всех элементов колпачковой тарелки не представляется возможным изменять такие технологические параметры, как, например, толщину слоя жидкости на тарелке и перепад уровней жидкости под колпачками относительно уровня ее на тарелке, что не позволяет изменять режим работы колонны по высоте в зависимости от изменяющихся свойств отрабатываемых продуктов, т.е. влиять на процесс тепло- и массообмена в колонне.
|
Целью авторов [2] является исключение перечисленных недостатков и повышение эффективности работы колонны.
По существу задача решается за счет того, что верхний конец каждого переливного патрубка закреплен в тарелке с возможностью осевого перемещения патрубка относительно последней, и его нижний конец снабжен тарельчатым перфорированным диском, а также стаканом, концентричным переливному патрубку и образующим с ним гидрозатвор.
В результате такого технического решения парожидкостная смесь проходит паровой патрубок и колпачок, барботируя через щели колпачка и контактируя с жидкостью на тарелке. Парогазовая смесь уходит на вышележащую тарелку, а избыточная жидкая (тяжелая) фракция через переливной патрубок сливается в стакан гидрозатвора, откуда попадает на тарельчатый перфорированный диск. Часть жидкости переливается через бортик диска, образуя кольцевую пленку. Другая часть жидкости в форме капель и струй проходит через перфорацию в диске и сливается на нижележащую тарелку. Легко испаряющая жидкость, находящаяся на тарелке в пленке, каплях, струях, испаряется и через паровые патрубки поступает навышележащую тарелку. Учитывая изменение температуры, вязкости жидкости, состава и агрегатного состояния среды по высоте колонны, можно отрегулировать соотношение и высоту (зазоры) между паровыми патрубками и колпачками, между переливными патрубками и стаканами гидрозатворов с тарельчатыми дисками, а также с помощью переливных патрубков изменить высоту (и, соответственно, сопротивление барботажу) жидкости на тарелке и живое сечение для борботажа паров через щели колпачков.
Это позволяет оптимизировать процесс разделения перерабатываемого продукта на заданные фракции.
Рис.1. Продольный разрез колонны.
1 – корпуса, 2 – штуцер, для входа парожидкостной смеси, 3 – штуцер, для выхода жидкости (тяжелой фракции), 4 – штуцер, для выхода паров (легкой фракции), 5 – тарелки с паровыми патрубками 6 и переливными патрубками 7, 8 – колпачки, 9 – стаканы гидрозатворов, 10 – кронштейны с фиксаторами 11, шпильками 12, поперечными планками 13 и тарельчатыми перфорированными дисками 14.
Таким образом, изменение высоты переливного патрубка (ислояжидкости) на тарелке, в сочетании с тарельчатым перфорированным диском на переливном патрубке, позволило оптимизировать уровень жидкости на тарелке и значительно
|
увеличить поверхность межфазного контакта на каждой тарелке, совокупную высоту столба жидкости (сопротивление) вколонне, режим работы колонны по высоте, поверхность тепло- и массообмена в зависимости от изменяющихся свойств перерабатываемых продуктов (температуры кипения, вязкости жидкости, состава смеси).
При этом обеспечивается возможность разделения продуктов на более четкие фракции и, соответственно, повышения качества целевых продуктов. Изложенные выше преимущества приводят к существенному повышению эффективности работы колонны.
Известна тарелка для контактирования газа (пара) сжидкостью, включающая горизонтальную перегородку, контактные устройства, выполненные в виде полых
вертикальных цилиндров, коаксиально которым установлены гидрозатворные устройства, а в корпусе контактных устройств в верхней части выполнены тангенциально направленные отверстия для прохода пара газа, закрытые крышкой с пропущенной через нее паровой трубой.
Однако колонна, состоящая из таких тарелок, имеет низкую эффективность и металлоемка. По известным в литературе данным эффективность такой ступени составляет 0,3-0,8, что явно не достаточно. Металлоемкость вызвана большим количеством тарелок и некомпактным конструктивным размещением контактных устройств на горизонтальных перегородках.
Известна пленочная тарелка Лева, состоящая из царг, в которых размещены горизонтальные перегородки (листы) с отверстиями и патрубки для прохода пара и стекающей жидкости.
Данное устройство имеет низкое гидравлическое сопротивление и несложное
конструктивное оформление, однако эффективность таких тарелок по Мерфри не превышает 0,1.
Авторами [3] решается задача повышения эффективности колонны, уменьшения ее габаритов и металлоемкости за счет: получения пара из дополнительной флегмы с высокой концентрацией легколетучих компонентов, что позволяет укрепить поднимающийся пар и тем самым увеличить эффективность процесса ректификации;
|
интенсивного перемешивания пара на ступенях вызванного поперечным движением части поднимающегося пара к охлаждаемой поверхности относительно движения основного потока поднимающегося пара; увеличения разделяющей способности паров на ступени путем обеспечения фракционной конденсации непосредственно на ступенях (заключающейся в получении конденсата из поднимающего пара с более высокой концентрацией высококипящих компонентов (труднолетучих), чем в самом паре, что обеспечивает повышение концентрации легколетучих (низкокипящих) компонентов в поднимающемся паре и увеличивает эффективность разделения).
Технический результат заключается: в получении дополнительной флегмы на поверхности змеевиков, размещенных в паровом пространстве царг под горизонтальными перегородками; в получении дополнительного пара с высокой концентрацией легколетучих компонентов путем нагревания и испарения дополнительной флегмы, размещенной на поверхности пластин, отбортованных с торцов, и горизонтально установленной с зазором под витками змеевиков; в образовании на поверхности пластин, отбортованных с торцов конденсата, с повышенной концентрацией труднолетучего компонента (ТЛК) разделяемой смеси, вызванной эффектом фракционной ректификации;
интенсивного перемешивания пара вызванного поперечным движением части поднимающегося пара к охлаждаемой поверхности относительно движения основного потока поднимающегося пара.
Все это позволяет повысить концентрацию легколетучего компонента в паре и тем
самым увеличить эффективность процесса ректификации, снизить высоту колонны, а
следовательно, уменьшить ее габариты и металлоемкость, чему также способствует установка на верхнем конце цилиндрического гидрозатворного стакана дополнительного завихрителя с тангенциальными каналами.
Известна ректификационная установка, где смесь в колонну подается вниз укрепляющей секции колонны. Колонна имеет куб в нижней части для подвода в нее тепла и образования парового орошения колонны и дистиллятор сверху колонны для отвода тепла с образованием верхнего жидкостного орошения (флегмы) и получения дистиллята в виде жидкости. Для подвода тепла в кубе колонны обычно используют водяной пар. Для отвода тепла сверху колонны наиболее часто используют охлаждение водой.
Недостатками этой установки являются большая высота ректификационной колонны, потери тепла через стенки колонны в окружающую среду и с отходящими продуктами - дистиллятом и остатком.
Известна ректификационная установка. Она состоит из колонны, куба, дистиллятора и компрессора для сжатия паров, выходящих из верха колонны. Такая установка обладает высокой эффективностью. Она позволяет использовать отходящее тепло конденсации паров дистиллята для испарения жидкости в кубе колонны (создание парового орошения) и тем самым сэкономить затраты тепла в колонне.
|
Недостатками такой установки является большая высота колонны и потери тепла через ее стенку в окружающую среду даже при наличии тепловой изоляции колонны, потери энергии дросселирования и потери тепла с остатком, отходящим из нижней части колонны.
Известна ректификационная установка. Эта установка обладает более высокой эффективностью. Впервые такой процесс ректификации был предложен Б.Г.Берго. Автор сообщает, что использование изобретения при ректификации легких углеводородных газов дает до 30% экономии энергетических затрат.
Недостатками этой колонны является малая поверхность контакта фаз в как в межтрубном, так и в трубном пространстве колонны, минимальная общая поверхность труб в колонне теплообмен между трубчатой и межтрубной зоной колонны, что снижает ее эффективность, потери энергии при дросселировании паров и потери тепла с остатком, отходящим из нижней части колонны.
Технический результат изобретения заключается в повышении эффективности работы установки за счет энергосбережения.
Технический результат авторами [4] изобретения достигается за счет того, что ректификационная установка включает ректификационную колонну в виде кожухотрубного теплообменного аппарата, трубное пространство которого образует укрепляющую секцию колонны, межтрубное пространство образует отгонную секцию колонны с давлением в трубном пространстве больше давления в межтрубном пространстве, оборудованную компрессором для сжатия паров, оборудованную дистиллятором для отбора паров с верха концентрационной секции колонны, причем межтрубное пространство ректификационной колонны заполнено насадкой, установлены детандер на одном валу с компрессором и теплообменник-подогреватель для подогрева исходной смеси.
Сущность изобретения заключается в том, что с целью повышения эффективности работы установки межтрубное пространство ректификационной колонны заполнено насадкой, увеличивающей поверхность контакта паровой и жидкой фаз, вместо дросселя установлен детандер на одном валу с компрессором для использования энергии расширения паров в детандере на вращение компрессора, а для использования теплоты отходящего остатка для подогрева исходной смеси установлен теплообменник-подогреватель. Ректификационная колонна может быть выполнена в виде теплообменного аппарата типа «труба в трубе», причем пространство труб ректификационной колонны может быть заполнено насадкой, а стеки труб иметь гофрированную форму.
Новые методы повышения эффективности ректификационных колон.
Чрезмерное загрязнение теплообменников влечет за собой низкую регенерацию тепла в аппаратах подогрева сырой нефти на многих нефтеперерабатывающих заводах. В свою очередь низкая регенерация тепла может привести к таким проблемам при работе установки как потеря продукта, снижение производительности, чрезмерно большая нагрузка на ректификационную колонну, на подогреватель исходного сырья и на многие другие аппараты. Новая схема расположения группы аппаратов подогрева сырой нефти может свести к минимуму их загрязнения. Этот подход может обеспечить большую эксплуатационную гибкость и в то же время повысить надежность работы ректификационной установки перегонки сырой нефти.
Рис.2.Схема подогрева сырой нефти в базовой системе и в модернизированной системе
На рис. 2 показана типичная схема системы подогрева сырой нефти вместе с новым проектным решением. На схеме сплошными линиями показана базовая система.
Новое решение отличается от стандартной системы следующим.
1. Циркулирующие потоки подводятся в трубные полости теплообменников, при этом обеспечиваются оптимальные скорости течения в трубах при расчетном расходе. Хотя подача слабозагрязненных потоков жидкостей в трубные полости теплообменников
отличается от стандартного решения подачи, тем не менее, такая схема позволяет более гибко изменять расход жидкости, подаваемой в трубные полости, в соответствии с изменениями подачи сырой нефти в ректификационную колонну или с изменениями.
распределения получаемых продуктов без увеличения загрязнения труб теплообменников
2. Продукт из нижней части ректификационной колонны сырой нефти – малосернистые содержащие парафин (low sulfur waxy residue – LSWR) нефтяные остатки – подается в полости кожухов теплообменников. Для LSWR/сырой нефти рекомендуется использовать теплообменники со спиральными перегородками с максимально возможной скоростью жидкости в полости кожуха при расчетном расходе. Выбор аппаратов со спиральными перегородками снижает риск загрязнения полости в кожухе. Такая схема сводит к минимуму изменения напора насоса при подаче LSWR вследствие изменения подачи сырой нефти или изменения распределения получаемого продукта без роста загрязнения в полости кожуха теплообменника (со спиральными перегородками). Подача сырой нефти в полости кожухов теплообменников обеспечивает необходимую гибкость при изменении подачи сырой нефти в колонну без изменения напора насосов подачи сырой нефти (оптимальная скорость в трубной полости при расчетном расходе).
3. Сырая нефть поступает в полости кожухов теплообменников в противоточном направлении относительно всех подаваемых в них циркулирующих потоков. Используется максимально возможная скорость в полости кожуха теплообменников при расчетной нагрузке, что приводит к меньшему загрязнению полости кожуха.
Авторами [5] было выявлено, что использование слишком больших запасов при проектировании теплообменников системы подогрева сырой нефти часто приводит к значительному загрязнению теплообменников и, следовательно, к значительному ухудшению их характеристик. Ухудшение характеристик приводит к уменьшению производительности установки переработки сырой нефти, к чрезмерно большой нагрузке нагревательной печи подаваемого сырья и к более высоким температурам продуктов в резервуарах, что в результате приводит к уменьшению дохода, к более высоким эксплуатационным расходам и к увеличению вредных выбросов. Новая схема системы подогрева исходного сырья уменьшает риск загрязнения за счет поддержания оптимальных скоростей потоков жидкостей в полостях кожухов и в трубах теплообменников при расчетных расходах подаваемого сырья. Новая схема системы обеспечивает гибкость в работе системы подогрева при увеличенных расходах подаваемого сырья.
Области применения метода
Обычно анализируемое соединение вводится в масс-спектрометр в газообразном состоянии и для получения масс-спектра подвергается действию ионизирующих электронов. Если материал недостаточно летуч или нестабилен для его введения в прибор в виде паров, возможности метода сильно ограничиваются, хотя в ряде случаев можно простыми химическими операциями получить летучие производные исследуемого вещества. Например, простой способ введения в прибор многоосновных кислот состоит в их этерификации. Однако в общем случае для получения спектра соединения должны быть стабильны при температуре, при которой упругость их пара составляет 10~6 мм рт. ст. Специальные методы введения образца непосредственно в ионизационную камеру позволяют работать с веществами, обладающими низкой упругостью пара, однако эти методы не обеспечивают возможности достаточно быстрого выполнения большого числа анализов. Применение температуры выше 350° для испарения образца в ионизационную камеру, как правило, связано с возможностью конденсации образца в этой области температур, поскольку основные части прибора обычно не нагреваются выше этой температуры. Образование изолирующих слоев при термическом разложении образца в ионизационной камере или конденсация исходного образца, трудность удаления образца при откачке, если он имеет упругость пара при 350° около 10~6 мм рт. ст. приводят к загрязнению источника и необходимости его частого демонтирования для чистки.
Обычно систему напуска располагают на некотором расстоянии от источника и отделяют от него «натекателем». Образец должен находиться в системе напуска при давлении около 0,1 ммргп. ст., при котором он должен быть полностью испарен, и состав паров и исходного материала должен быть идентичным. Проблемы напуска образца будут рассмотрены ниже, но следует указать, что используемые в большинстве лабораторий методы не обеспечивают возможности анализа соединений, имеющих упругость пара менее 0,1 мм рт. ст. при 350°. Температура 350° — это температура, при которой большая часть органических кислород- и азотсодержащих соединений термически неустойчивы. Из этого следуют серьезные ограничения аналитических возможностей масс-спектрометра. Упругостью пара 0,1 мм рт. ст. обладают парафиновые углеводороды (наиболее летучие высокомолекулярные органические соединения, за исключением галогеносодержащих) с молекулярным весом около 600 или ароматические углеводороды с конденсированными кольцами с молекулярным весом около 400; присутствие в молекуле атома азота или кислорода в заметной степени снижает летучесть органических веществ. Тем не менее для тех соединений, для которых масс-спектр может быть получен, он является источником наиболее полной информации по сравнению со сведениями, получаемыми любыми другими методами. Обширная информация, получаемая на основании масс-спектров, обеспечивает дальнейшее расширение применения приборов для качественного анализа и более полное использование потенциальных возможностей метода. Ниже описывается последовательность операций, необходимых для идентификации.[6]
Система вода образца
Для того чтобы избежать нежелательных химических реакций в результате взаимодействия молекул и ионов, в источнике масс-спектрометра, как правило, поддерживается высокий вакуум (10-5-10-6 ммрт. ст.). Поэтому уже сам ввод образца является самостоятельной технической задачей.
2.3.1. Баллон напуска
Одной из первых систем ввода, практически не используемой в настоящее время, служил баллон напуска (рис. 7). Анализируемое вещество находилось в газообразном состоянии (давление около Ю-2 мм.рт.ст.) в баллоне объемом 50-2000 см3, внутренняя поверхность которого была остеклена для предотвращения нежелательных химических реакций на стенках сосуда. В поздних вариантах предусматривалась система нагрева пробы в баллоне. Этот резервуар соединялся с источником ионов отверстием очень небольшого диаметра, через которое осуществлялось молекулярное натекание образца в масс-спектрометр.
Рис.7. Баллон напуска.
Альтернативными вариантами соединительного отверстия служили капилляры или пористые диафрагмы. Эти устройства позволяли получить стабильную концентрацию вещества в источнике и были необходимы на начальных этапах развития органической масс-спектрометрии, когда применялись малоэффективные вакуумные системы, а скорость развертки масс-спектра составляла минуты. Очевидным недостатком данного ввода является необходимость переводить вещество в газовую фазу в условиях неглубокого вакуума, что для многих образцов весьма проблематично. Конструкции стыковки баллонов напуска с ионными источниками подробно описаны в фундаментальном труде Джона Бейнона.
2.3.2. Прямой ввод.
Развитие техники позволило в 60-х годах XX века перейти на более совершенную систему ввода, которая является общепринятой и широко распространенной в настоящее время. Это — прямой ввод вещества в область ионизации. Твердый образец помещается в специальную микрокапсулу (стекло, кварц, керамика, металл), которая штоком вводится непосредственно в ионный источник, т. е. испарение осуществляется прямо в источнике ионов в условиях глубокого вакуума. При необходимости образец может быть нагрет с помощью программируемой печки до температуры 400-500°С, а в некоторых случаях, как, например, в условиях десорбционной химической ионизации, — выше 1000°С. Понятно, что в этих условиях количество соединений, доступных
масс-спектрометрическому анализу, значительно возрастает. Полное испарение введенного образца позволяет измерить количество соединения, т. е. прямой ввод позволяет наряду с качественным проводить и количественный анализ веществ.
Важно обращать внимание не только на температуру прямого ввода, но и на температуру источника ионов. Если вещество труднолетучее, а прямой ввод перегрет, оно может конденсироваться на стенках источника, что ведет к его быстрому загрязнению. Кроме того, последовательные процессы испарения и конденсации приводят к увеличению роли деструкции вещества и, соответственно, к искажению масс-спектра. Процессы деструкции имеют место и в случае слишком высокой температуры источника. Принципиальная схема прямого ввода представлена на рис. 8.
Программируемый нагрев образца в вакууме позволяет решить одновременно три задачи: во-первых, перевести в газовую фазу широкий круг органических соединений;
Рис.8. Система прямого ввода.
во-вторых, подобрать оптимальную температуру съемки, когда воспроизводится качественный масс-спектр; в-третьих, анализировать смеси соединений с разной степенью летучести. Такое фракционное испарение позволяет в некоторых случаях провести достаточно быстрый качественный и количественный анализ смеси без ее предварительного разделения.
Важной характеристикой прямого ввода является существенное уменьшение количества образца, необходимого для получения масс-спектра. В данном случае следует опасаться ввести слишком много вещества. Считается, что твердый образец в капилляре на конце штока должен быть едва различим глазом. Избыточное количество образца может привести к искажению масс-спектра из-за протекания ионно-молекулярных реакций и вызвать быстрое загрязнение источника ионов. Многие масс-спектрометристы предпочитают наносить вещество из раствора и вводят шток в источник после испарения растворителя.
Еще один важный параметр съемки для наиболее распространенных спектров электронного удара связан с положением образца относительно пучка электронов. Если образец расположен достаточно далеко, его молекулы достигают пучка электронов только после ряда последовательных столкновений со стенками источника. При этом возрастает роль процессов термодеструкции. Однако если поместить образец слишком близко к пучку электронов, наконечник штока может приобрести отрицательный заряд и начать отталкивать электроны, что приводит к расфокусировке пучка.
Система прямого ввода применяется в основном в сочетании с методами электронного удара и химической ионизации, хотя его модификации используются в случае бомбардировки быстрыми атомами и для некоторых других методов
ионизации.
2.3.3. Мембранный ввод.
Достаточно перспективным является мембранный ввод пробы. Мембрана изготавливается из органического материала и пропускает в источник масс-спектрометра соединения, растворимые или адсорбируемые материалом мембраны и обладающие высоким коэффициентом диффузии в нем. Анализируемое соединение должно быть достаточно летучим, чтобы испаряться на вакуумированной стороне мембраны. В одном из приводимых ниже вариантов мембрана размещается вне источника ионов (рис. 9), в другом — капиллярная мембрана вводится непосредственно в источник (рис. 10). Достоинством такого ввода является селективность в пропускании веществ разной природы. Поскольку мембрана не пропускает воду, неорганические газы и соли, она может использоваться для эффективного мониторинга загрязнения воздуха или воды органическими соединениями, а также для контроля биохимических процессов. Например, в работе показано, что предел обнаружения в воде для широкого круга органических соединений с молекулярной массой <300 Да может достигать нанограммов в литре. В литературе описаны возможности непрерывного мониторинга органических соединений в сточных и природных водах, в воздухе, мониторинга биологических реакций.
Рис. 9. Размещение мембраны вне Рис. 10. Размещение мембраны внутри
источника ионов источника ионов
2.3.4. Хроматомасс-спектрометрия, ГХ-МС (GC-MS).
На сегодняшний день хроматомасс-спектрометрия (хромасс, ГХ-МС) является
наиболее широко используемой разновидностью органической масс-спектрометрии, хотя, начиная с 90-х годов XX века, многочисленные варианты комбинированного метода высокоэффективная жидкостная хроматография — масс-спектрометрия используются все шире и в ближайшее время, вероятно, займут лидирующее положение.
Стыковка газового хроматографа и масс-спектрометра была абсолютно логичной, поскольку оба метода использовались для анализа смесей органических соединений в газовой фазе и обладали приблизительно равной чувствительностью. Единственной проблемой для объединения двух методов в едином приборе являлось рабочее давление. Газовый хроматограф работает при атмосферном давлении, а масс-спектрометр— в условиях глубокого вакуума. Основные принципы стыковки были сформулированы и претворены в жизнь в 1957 году. Первоначальные проблемы, связанные с недостаточной мощностью вакуумных систем и набивными колонками с рабочими потоками газа-носителя 30 мл/мин, решались установкой сепараторов различного типа. Эти устройства размещались между выходным концом колонки хроматографа и ионным источником масс-спектрометра и предназначались для обогащения пробы анализируемым веществом за счет избирательной откачки значительно более легкого газа-носителя (водород, гелий). Появление более мощных вакуумных систем и капиллярных колонок с меньшими потоками (0,5-2,0 мл/мин) значительно облегчило задачу, а замена металла или стекла, из которых изготавливались колонки, на плавленый кварц позволила ввести конец колонки непосредственно в ионный источник. Все это сделало метод ГХ-МС простым и эффективным.
Метод прежде всего предназначен для анализа смесей органических соединений и заключается в их разделении на колонке хроматографа с последовательным выходом компонентов из колонки в ионный источник масс-спектрометра, где происходит их ионизация. Масс-спектрометр должен проводить запись спектра (сканирование) с достаточной частотой, чтобы зарегистрировать масс- спектр каждого соединения несколько раз. Это условие является важнейшим, поскольку концентрация вещества очень быстро изменяется. В зависимости от того, на восходящей или нисходящей стороне хроматографического пика будет записан масс-спектр, будут дискриминированы или низкие, или высокие массы (рис. 11).
Рис. 11. Масс-спектры л-фторбензофенона на восходящей стороне (а), на нисходящей
стороне (б) и вершине хроматографического пика (в)
Безусловно, лучшим будет спектр, зарегистрированный на вершине хроматографического пика, где максимальна концентрация вещества и минимальны ее изменения во времени. Желательно получить 5-10 спектров каждого компонента смеси, а для улучшения качества спектра часто необходимо проводить усреднения и вычитания фона. Очень важна скорость сканирования и для количественного анализа. Недостаточное число сканирований приводит к значительному искажению площади хроматографического пик.
Хромасс добавляет к масс-спектрометрической информации еще один очень важный параметр — время удерживания. Именно благодаря этому параметру появляется возможность во многих случаях проводить качественный и количественный анализ изомеров, масс-спектры которых практически неразличимы. Хромасс позволяет также детектировать ультрамикрокомпоненты на фоне высоких концентраций других соединений.
В методе реакционной хроматомасс-спектрометрии перед колонкой хроматографа или между колонкой и масс-спектрометром устанавливается реакционная камера, в которой можно осуществлять заданные превращения анализируемых соединений. В таком варианте дериватизация, разделение и анализ компонентов пробы осуществляются в режиме «on-line». Реакционная хроматомасс-спектрометрия может использоваться для улучшения разделения компонентов смеси или для проведения структурных анализов.
2.3.5. Жидкостная хроматография—масс-спектрометрия, ЖХ-МС (LC-MS)
Решить проблему анализа тяжелых полярных термолабильных соединений
можно при замене газового хроматографа на жидкостный. Наиболее сложным моментом оказывается стыковка жидкостного хроматографа с масс-спектрометром. Масс-спектрометр обычно работает в условиях глубокого вакуума (10-6 мм рт. ст.), а скорость потока через стандартную колонку жидкостного хроматографа составляет примерно 1 мл/мин. Две наиболее часто используемые в современной хроматографии жидкие фазы —метанол и вода. Испаряясь в источнике ионов, 1 мл метанола образует 0,55л пара, а 1 мл воды—1,24 л пара.
2.3.5.1. Ленточный транспортер (Moving Belt)
Исторически первым интерфейсом можно считать ленточный транспортер, появившийся в 1976 г. Принципиальная схема устройства представлена на рис. 12.
Его основной конструкционной деталью является тонкая полиимидная кольцевая лента. Элюат из колонки хроматографа попадает на ленту, движущуюся по направлению к источнику ионов. На пути следования он проходит вдоль инфракрасных испарителей, которые переводят в газовую фазу значительную долю подвижной фазы. Далее лента проходит вакуумный замок, и в условиях вакуума остатки растворителя откачиваются насосами. В месте перегиба ленты, в ионном источнике, находится импульсный нагреватель, который переводит в газовую фазу молекулы образца, подвергающиеся электронному удару или химической ионизации. Двигаясь в обратном направлении, лента очищается от избытка нанесенного образца благодаря дополнительным испарителям, а
иногда и растворителям, и возвращается за новой порцией элюата в исходном (теоретически чистом) виде.
Рис. 12. Принципиальная схема ленточного транспортера.
К достоинствам метода следует отнести:
1. Возможность использования стандартных библиотек масс-спектров электронного удара для идентификации исследуемых веществ.
2. Возможность работы со стандартными колонками для жидкостной хроматографии, поскольку метод использует скорости потока до 1.5 мл/мин. Такие потоки приемлемы при распылении элюата на ленту.
3. Неорганические соли, используемые в качестве буфера при хроматографировании, не мешают анализу.
Тем не менее ленточные транспортеры не получили широкого признания, поскольку лишь незначительно расширяли круг органических соединений, доступных масс-спектрометрическому анализу.
2.3.5.2. Прямой ввод жидкости (Direct Liquid Introduction, DLI)
Данный метод тоже следует рассматривать скорее как историю масс-спектрометрии. Он более или менее активно использовался в 80-х годах XX века, но уступил место более прогрессивной технике, основанной на аналогичном принципе. Фактически все современные интерфейсы ЖХ-МС, за исключением проточного варианта бомбардировки быстрыми атомами, могли бы быть названы прямым вводом жидкости.
Для реализации прямого ввода жидкости на выходе из хроматографической колонки устанавливается диафрагма с отверстием 2-5 мкм (рис. 13). Возникающая струя мелких капель, движется с большой скоростью к источнику ионов.
Рис. 13. Принципиальная схема метода прямого ввода жидкости.
На пути следования капли проходят через камеру испарения, где большая часть растворителя переходит в газовую фазу. Оказываясь в источнике масс-спектрометра, молекулы анализируемого вещества подвергаются химической ионизации, тогда как молекулы растворителя играют роль газа-реагента. Основной недостаток метода— низкая скорость потока. Давление в источнике становится слишком высоким при потоках более 50 мкл/мин. Поэтому требуется либо разделять поток из стандартных хроматографических колонок, уменьшая тем самым чувствительность метода примерно в 20 раз, либо использовать узкие колонки. Кроме того, узкое отверстие диафрагмы постоянно забивается, а добавки неорганических солей к подвижной фазе приводят к быстрому ухудшению работы масс-спектрометра.
2.3.5.3 Поток частиц (Particle Beam)
В этом варианте интерфейса поток из колонки хроматографа направляется через капилляр в стеклянный распылитель, где элюат превращается в облако мелких капель, разорванных кон<
|
|
Поперечные профили набережных и береговой полосы: На городских территориях берегоукрепление проектируют с учетом технических и экономических требований, но особое значение придают эстетическим...
Индивидуальные и групповые автопоилки: для животных. Схемы и конструкции...
История развития пистолетов-пулеметов: Предпосылкой для возникновения пистолетов-пулеметов послужила давняя тенденция тяготения винтовок...
Механическое удерживание земляных масс: Механическое удерживание земляных масс на склоне обеспечивают контрфорсными сооружениями различных конструкций...
© cyberpedia.su 2017-2024 - Не является автором материалов. Исключительное право сохранено за автором текста.
Если вы не хотите, чтобы данный материал был у нас на сайте, перейдите по ссылке: Нарушение авторских прав. Мы поможем в написании вашей работы!