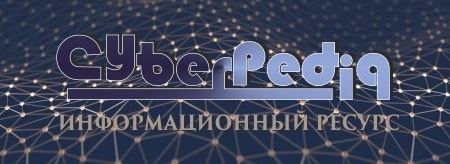
История развития хранилищ для нефти: Первые склады нефти появились в XVII веке. Они представляли собой землянные ямы-амбара глубиной 4…5 м...
Особенности сооружения опор в сложных условиях: Сооружение ВЛ в районах с суровыми климатическими и тяжелыми геологическими условиями...
Топ:
Характеристика АТП и сварочно-жестяницкого участка: Транспорт в настоящее время является одной из важнейших отраслей народного...
Основы обеспечения единства измерений: Обеспечение единства измерений - деятельность метрологических служб, направленная на достижение...
Организация стока поверхностных вод: Наибольшее количество влаги на земном шаре испаряется с поверхности морей и океанов...
Интересное:
Влияние предпринимательской среды на эффективное функционирование предприятия: Предпринимательская среда – это совокупность внешних и внутренних факторов, оказывающих влияние на функционирование фирмы...
Национальное богатство страны и его составляющие: для оценки элементов национального богатства используются...
Уполаживание и террасирование склонов: Если глубина оврага более 5 м необходимо устройство берм. Варианты использования оврагов для градостроительных целей...
Дисциплины:
![]() |
![]() |
5.00
из
|
Заказать работу |
|
|
Вид дробления | Конечный диаметр частиц, мм | Степень измельчения | Основные способы дробления |
Крупное Среднее Мелкое Тонкое | 100—30 20-5 2—0,7 0,5-0,07 | 1/2-1/4 1/2-1/6 1/3-1/6 1/6-1/10 | Ручное — молотками; механическое — ще-ковые дробилки «Блек» Ручное — молотками, крупные ступы; механическое— малые щековые дробилки, валки Ручное — ступы, растиратели; механическое — малые валки Ручное — малые ступы; механическое — дисковые истиратели, шаровые и стержневые мельницы |
колебательном движении приближаться и отдаляться от неподвижной щеки. Подвижная щека на дробилке «Блек» приводится в движение эксцентричным валом с двумя рычагами и пружинной тягой, которая возвращает щеку в исходное положение после рабочего хода. Размеры материала, выходящего из дробилки, зависят от ширины щели между щеками. Степень измельчения обычно составляет от х]2 до 1/4, редко больше. Размер щели регулируется вкладышами в виде клиньев. Максимальный диаметр раздробленных частиц 100—30 мм.
Среднее дробление осуществляется на малых щековых дробилках (аналогичных описанным выше) или на механических дробильных валках. Реже применяются ручное дробление молотками и крупные (большие) ступы. При работе в больших ступах пест подвешивается на гибкий балансир, что облегчает работу (рис. 39).
1о |
Рис. 38. Щековая дробилка «Блек» 1 — подвижная щека; 2 — неподвижная щека; з — эксцентриковый вал; 4 — шатун; 5 — рас й 7 |
ИЬптгпр ттппйириир ттгптчкппят порвые рычаги; в — приводной шкив; 7 — ма- .мелкое дроолениепроизводят ховик. s _ щ,™ина: 9_ТЯГа: ю — ось под- |
ховик; «— пружина; 9 — тяга; 10 — ось подвижной щеки; 11 Vi 12 — клинья; IS — щель, определяющая наибольший размер раздробленных частиц |
на малых валках, в ступах и на рас-тирателях. По своей конструкции |
Дробильные валки (рис. 40) в виде коротких тяжелых цилиндров с насаженными на них бандажами из специальной стали расположены на горизонтальных осях рядом друг с другом; расстояние между валками (щель) определяет максимальный диаметр раздробленного материала, выходящего из валков. При работе валки приводятся во вращение навстречу один другому, а материал засыпается из небольшого бункера. Поверхности валков могут быть гладкими или рифлеными для лучшего захвата кусочков породы, которую дробят. Степень измельчения от 1/2 до i/g. Конечный максимальный диаметр раздробленных частиц 20—5 мм.
|
![]() |
![]() |
малые валки аналогичны описанным выше и, как правило, работают от механического привода. Работа на ступах и растирателях производится вручную.
Рис. 39. Ступа для дробления пестом с балансиром 1 — свая; 2 — балансир; з — добавочная опора; 4 — пест; 5 — ступа |
Ручной растиратель представляет собой массивный башмак (молоток) с выгнутым основанием в виде пресс-папье, насаженным на рукоятку. При движении такого башмака (вес его достигает 5—6 кг) по металлической доске, на которую насыпают материал пробы, можно производить дробление — растирание этого материала. Доска имеет бортики, предохраняющие материал пробы от рассыпания.
Иногда для мелкого дробления используют механические бегуны, представляющие собой короткие цилиндры, вращающиеся на осях, которые катятся по дорожке (по кругу) и дробят материал, насыпаемый на дорожку. Бегунная установка ввиду большой тяжести бегунов обычно используется в заводских условиях и очень редко при разведке место-
Степень измельчения при мелком дроблении от г/3 до Ув- Конечный диаметр максимальных частиц 2—0,7 мм.
Тонкое дробление достигается в шаровых (стержневых) мельницах на дисковых растирателях, реже вручную в агатовых, фарфоровых, стальных ступах и на ручных растирателях.
|
![]() |
Шаровые мельницы представляют собой металлические сосуды цилиндрической формы, нередко с внутренней футеровкой, в которые загружаются шары (стальные, фарфоровые или кремневые) и помещается мелкоизмельченная проба. Мельница располагается горизонтально или несколько наклонно и приводится во вращение по оси цилиндра. При вращении шары двигаются, сталкиваются, а частицы руды, попадая между шарами, дробятся. В некоторой степени срабатываются при этом и шары. В 1956 г. советскими инженерами сконструированы вибрационные мельницы, в которых цилиндры с шарами не только вращаются, но и встряхиваются, что резко повышает производительность помола.
Рис. 40. Дробильные валки бункер для засыпки руды; 2 — валки со i ифлеными нешними бандажами; |
Стальные шары в мельнице засоряют пробу железом, и если
это недопустимо, то дробление,_
Ведется Кремневыми ИЛИ фарфо- стальными i рифлеными внешними бандажами;
г т-, х гх 3 —буферная' пружина; 4 — приемный ящик
рОВЫМИ Шарами. Вместо ШарОВ с лотком; 5 — щель (зазор) между валками
![]() |
могут работать металлические стержни. Степень измельчения в мельницах изменяется от г/ъ до г/10, конечный диаметр максимальных частиц может быть от 0,5 до 0,07 мм.
Рис. 41. Шаровые мельницы |
Лабораторные шаровые мельницы изготовляются небольших размеров длиной 10—25 см и диаметром 5— 15 см, вместимостью от 50 до 1000 г
_ 1 — металлическая рама — стол; г — ве-
измельченного материала. Обычно та- дущийролик (валик); з — направляющие
Кие МеЛЬНИЦЫ размещаются ПО не- валики;.4 и 5-^р^ицы с шарами или
скольку штук на параллельно расположенных валках, из которых один — ведущий, вращающийся (от мотора), а другие—направляющие. Валки имеют рифленую или резиновую поверхность и за счет трения приводят во вращение свободно лежащие на них мельницы (барабаны). Такая вращательная установка для малых мельниц называется фрикционным столом (рис. 41).
Дисковые истиратели могут быть вертикальные и горизонтальные (рис. 42). Руда измельчается между двумя дисками, один из которых укреплен в передней стенке рабочей камеры и является неподвижным, а другой, вращающийся диск установлен на горизонтальном валу, снабженном рабочим и холостыми шкивами. Подлежащий измельчению материал поступает через воронку в рабочее пространство между дисками (в центре); далее материал увлекается силой тяжести и центробежной силой по радиальным каналам к периферии дисков, измельчается и разгружается через нижнее отверстие в находящийся под аппаратом приемник. Тонкость измельчения регулируется установочным винтом. Подъемная
|
Рис. 42. Дисковый истиратель:
«— в закрытом виде при работе; б — в открытом виде. 1 — вращающийся диск; 2 — неподвижный
диск; з — шкив; 4 — воронка для загрузки материала; 5 — радиальные канавы; в — отверстие
для разгрузки измельченного материала; 7 — установочный винт; 8 — крышка кожуха
9 Заказ 15
крышка кожуха и откидывающийся на шарнире неподвижный диск дают свободный доступ ко всем частям аппарата для чистки и ремонта. Конечный максимальный диаметр частиц от 0,1 до 0,15 мм.
Контроль измельчения
Проверка (контроль) полноты измельчения при диаметре частиц более 2,5 мм осуществляется грохочением или просеиванием. Механическое грохочение производится на подвижных, качающихся грохотах с колосниковой решеткой (продольные отверстия) или сеткой, которые натягиваются на деревянную или металлическую раму. Грохот для крупного материала устанавливается обычно под большим углом (40—50°), а для мелкого — под пологим углом (10—20°).
Примером механического грохота может служить грохот типа Фер-рариса. Этот грохот представляет собой железную или деревянную раму, перекрытую проволочной или штампованной сеткой с соответствующими отверстиями. Рама устанавливается на качающихся опорах и соединена тягой с эксцентриком, делающим 200—350 об/мин. При каждом обороте эксцентрика грохоту сообщается энергичное встряхивание, в результате чего просеиваемый материал проходит через отверстия, передвигается вперед и высыпается через выпускной желоб.
Ручные грохота обычно с проволочной сеткой, натянутой на деревянную раму, приводятся в качательное движение ручным способом. Для этого удобнее всего подвесить грохот на веревках к небольшим козлам, и тогда один рабочий легко приводит его в качательное движение. Пользуются также и грохотом, у которого рама имеет рукоятки (в виде носилок). Тогда двое рабочих держат грохот на руках и покачивают его в горизонтальном и вертикальном направлениях. Эта работа более утомительна, чем при использовании подвесного грохота.
|
Сухой и легко рассыпающийся материал можно классифицировать и на неподвижных грохотах, устанавливаемых под углом 20—40°. В этом случае раздробленную породу бросают на верхнюю часть грохота, мелкий материал, двигаясь вниз, успевает пройти через сетку.
Размер сеток (ширина ячеек), или расстояния между продольными колосниками, т. е. щели грохота, определяются требуемой степенью
измельчения.
Просеивание мелкого материала с частицами менее 2,5 мм ведется на ситах. Размеры отверстий в ситах могут определяться: 1) их шириной (диаметром); 2) числом отверстий (от 3 до 200) на линейный дюйм (число отверстий на один дюйм называется «меш»), или числом отверстий на 1 см2. В настоящее время у нас изготовляются сита до 4500 и даже 10 000
отверстий на 1 см2.
Сита с различными отверстиями могут ставиться одно над другим, образуя стопку, где просеивание будет вестись одновременно через несколько сит. Такое просеивание может производиться ручным и механическим способами. Механическая установка с несколькими встряхивающимися ситами носит название «Ратап».
![]() |
Перемешивание
кольца кольцо; |
Рис. 43. Смешение способом п конуса 1 — развертывание конуса на 2 — кольцо в разрезе |
Перемешивание раздробленного материала проб можно производить перелопачиванием, когда с помощью лопат материал перебрасывается из одной кучи в другую. Чаще перемешивание производят способом «кольца и конуса». В этом случае материал сначала набрасывают лопатами в виде конуса, а затем конус разворачивают на кольцо с помощью короткой широкой доски, которая погружается через центр конуса и затем повертывается на полный круг (рис. 43).
Небольшие порции хорошо смешиваются на холсте размером (1 — 1,5) X (0,5—0,7) м, концы (углы) которого берут в руки двое рабочих и поочередно поднимают и опускают их, благодаря чему материал пробы перекатывается и перемешивается.
Сокращение
Сокращение раздробленного и перемешанного материала пробы должно контролироваться формулой Q = Kd2, согласно которой вес сокращенной части пробы (в кг) не должен быть меньше Q. Например, проба весом 40 кг, раздробленная до максимального диаметра частиц 6 мм, при К = 0,5 может быть сокращена только один раз (пополам) до 20 кг; повторное сокращение приведет к тому, что вес сокращенной части окажется равным 10 кг, т. е. менее 18 кг, предусмотренных формулой, что является недопустимым.
Любые порции материала можно сокращать методом квартования. При квартовании материал пробы рассыпается в виде усеченного конуса (диска) с небольшой высотой (0,1—0,2 м), а затем с помощью доски или лопаты делится на четыре примерно равных сектора (для небольших порций используется специально изготовляемая крестовина). Два противоположных сектора берутся в одну часть, а два других — в другую. Обе части считаются однозначными (равноценными), и одну часть удаляют. Таким образом, при каждом отдельном квартовании проба сокращается в два раза. Квартование можно производить несколько раз, если позволяет формула (И).
|
Небольшие количества материала можно квартовать на ящичных и конусных делителях. Ящичные делители («Джонса») состоят из нескольких пар небольших ящиков; в каждой паре ящиков нижние отверстия открыты в противоположные стороны (рис. 44, А). Если с широкой лопаты ссыпать сверху раздробленный материал в делитель, а внизу поставить ■сборный ящик, разделенный продольной перегородкой на две части, то
![]() |
7 / Бунн |
Составление общей схемы обработки проб Все описанные выше процессы, необходимые для сокращения первичных проб (дробление, просеивание, смешивание и собственно сокращение), должны быть увязаны в одну общую схему, которую обычно изображают в виде графика. В этой схеме указывают рациональную смену диаметров максимальных частиц, последовательность дробильных установок, способы просеивания и сокращения материала пробы. При составлении схемы последовательно решают следующие вопросы. 1. Возможность сокращения данной пробы без дробления при определенном весе Q, установленном коэффициенте К и наибольшем диа метре частиц d. Такое сокращение возможно, если Q = 2Kd2. 2. Определение веса конечной пробы (сокращенной) QKOli и макси мального размера кусков в ней dKOn. 3. Соотношение конечного dKQn и начального dRa4 диаметров наиболь ших частиц в пробе покажет общую степень измельчения и даст возмож ность путем разложения этого соотношения на множители наметить ста дии дробления материала пробы. 4. Определяют промежуточные веса проб Qnp после каждой стадии дробления, до которых данная проба может быть сокращена. Исходный наибольший диаметр частиц пробы и намеченные стадии дробления позволят определить виды дробления, подобрать для дробления оборудование, наметить диаметры сит для контрольного грохочения |
\ | / | |
\ |
![]() |
\
Рис. 44. Ящичный и конусный делители
А — ящичный делитель: о ■— вид сверху, б — вид сбоку. 1 —6 — делительные ящики; г — бункер; I и II — приемные сосуды. Б — конусный делитель (ручной): 1 — бункер; 2 — верхний конусный сосуд; з — нижний конусный сосуд; 4, — приемный сосуд
половина материала поступит в одно отделение (часть I), а половина — в другое отделение (часть II), как показано на рис. 44.
В лабораториях часто пользуются конусными делителями (см. рис. 44, Б). Каждый конус в делителе разделен на четыре сектора, из которых два противоположных открытые, а два закрытые. Если конус привести в движение вокруг оси и равномерно ссыпать сверху материал, то последний поступит в секторы примерно в равном количестве, и одна половина его просыплется вниз, а другая останется в двух конусах. Обычно несколько конусов располагают один над другим по оси делителя и при работе сразу получается несколько последовательных делений (сокращений). Такое сочетание нескольких конусных делителей ускоряет и уточняет работу по сокращению небольших проб.
и установить схему смешения и сокращения в каждой стадии. Контрольные грохота, или сита, следует ставить до дробления, чтобы не дробить лишнего материала, а также после дробления, чтобы случайно не попали крупные куски.
При сокращении в последнюю стадию следует взять одну половину расквартованного материала пробы в качестве лабораторной (основной) пробы, а другую сохранить как дубликат.
Составление схемы обработки и сокращения проб лучше всего видно на разборе конкретного примера.
Дана проба весом QHa4 = 500 кг с диаметром наибольших частиц ^нач = 20 мм. Требуется сократить данную пробу, отправляемую в лабораторию, до размеров химической пробы (вес конечной пробы QK0H = = 0,5 кг).
Для руд с весьма неравномерным распределением полезного компонента коэффициент К принимается равным 0,5.
Предварительно решаем следующие вопросы в последовательности, указанной выше:
1. Определяем возможность сокращения пробы без дробления. @нач
должно быть больше или равно 2Kd2. Подставляя известные величины,
получаем: 500 > 2-0,5-400, следовательно, сокращение возможно.
2. Определяем конечный диаметр дробления для химической пробы
QKOn = Kdlol,; 0,5 = 0,5-d5OH; dKOH=l мм. 3. Рассчитываем степень измельчения и намечаем стадии дробления
I. л.
4 ' 5 •
Следовательно, намечаются две стадии дробления:
После первой стадии дробления наибольший диаметр частиц d будет равен 20- — = 5 мм, а после второй — dK0H = Ъ- ~=\ мм.
4 О
4. После первого сокращения пробы до дробления промежуточный вес ее будет QuP = 250 кг; после первой стадии дробления промежуточный вес пробы составит: Q"np = Kd\ = 0,5-25 = 12,5 кг.
После получения предварительных расчетных величин нетрудно составить общую схему обработки и сокращения пробы, которая приведена на рис. 45.
При большом количестве химических проб, особенно при эксплуатационном опробовании на крупных рудниках (Тырны-Ауз и др.), для обработки проб используют специальные комбинированные механизмы, включающие крупное, среднее и мелкое дробление. Материал пробы загружают в щековую дробилку и вся проба автоматически передается на другие механизмы. Весь материал пробы измельчается без сокращения до диаметра 0,5—1 мм. При обычных пробах весом 15—25 кг такая обработка оказывается экономически выгодней.
![]() |
![]() |
Перемешивание |
Предварительное сокращение |
Квартование |
Отвал 250 кг |
Контрольный грохот, 5 мм Дробилка щековая t щель Б мм Контрольный грохот1 5 мм |
i стадия |
Перемешивание Сокращение- |
15,6 КГ |
QnP 15'5 кг Контрольный грохот. 1 мм Дробилка валковал, щель 1ммКонтрольный грохот, 1 м» |
II стадия |
*- 0,9 кг лабораторная проба 1,9 0,9 кг дубликат |
Рис. 45. Схема обработки и сокращения проб
Следует иметь в виду, что после обработки каждой пробы все обору^ дование (дробилки, валки, истиратели) следует тщательно очищать, так как возможно засорение последующей пробы материалом, оставшимся от предыдущей пробы, что может исказить результаты опробования.
Часто, особенно в полевых условиях, пробы для химических анализов измельчают до конечного диаметра частиц 1 мм, как принято в приведенном выше примере. В этих случаях очень важно проследить и проверить, чтобы химическая лаборатория при доведении пробы до навески для химического анализа пользовалась для сокращения той же формулой и тем же значением коэффициента К. Нарушение этого правила может привести к тому, что навеска окажется недостаточно представительной, а результаты анализа искаженными.
В приведенной выше схеме сокращения проб указано, что весь материал, остающийся после сокращения, направляется в отвал, однако это не всегда целесообразно. Особенно внимательно следует относиться к материалу проб на последних стадиях дробления и в тех случаях, когда начальный вес проб невелик.
Мелко раздробленный материал может быть промыт в лотке и из него получен шлих, который нередко представляет большую ценность и используется для предварительной оценки качества руды и направления работ.
Пробы, отобранные от керна, особенно с больших глубин и ограниченного веса, представляют большую ценность для геологического изучения. Поэтому все остатки после сокращения таких проб следует хранить вместе с керном (а не сбрасывать в отвал), так как часто приходится неоднократно возвращаться к изучению качества минерального сырья, производить контрольные анализы, повторные анализы на попутные компоненты, элементы-примеси, а нередко собирать материал и для лабораторных технологических испытаний. Эти замечания в первую очередь относятся к рудам цветных, редких и благородных металлов,
ОБРАБОТКА ПРОБ НА РОССЫПНЫХ МЕСТОРОЖДЕНИЯХ
Обработка проб на россыпных месторождениях начинается непосред^ ственно на месте работ — в полевых условиях. Материал проб раздроблен самой природой и дополнительного измельчения обычно не требует. Сокращение объема проб в соответствующих случаях производят при их отборе — способом вычерпывания, отбор в пробу каждой 3-й, 5-й или и-й лопаты при валовом опробовании и др. Рыхлый материал подвергается промывке, в процессе которой тяжелые и прежде всего рудные минералы и сростки отделяются от более легких безрудных фракций.
Промывка небольших проб (объемом 0,01—0,02 м3) производится в лотках или ковшах, которые могут быть нескольких типов (см. рис. 46). Вместе с материалом пробы лоток наполняется водой, крупные куски — обломки пород, галька — обмываются и отбрасываются с помощью специального гребка или руками. Затем разминается и размывается глина, из которой мелкие частицы смываются водой, а более крупные остаются в лотке. Путем резких коротких встряхиваний лотка создается подобие
рибрации, под действием которой зерна легких минералов устремляются к краевой части лотка и сбрасываются — смываются чистой водой, а тяжелые остаются в центре лотка.
В зимних условиях промывку осуществляют в специальных баках теплой водой. После промывки всех проб той или иной выработки, с того или иного интервала выработки «хвосты» еще раз промывают все целиком или часть их для контроля «сноса» полезного компонента.
Полученная после промывки часть пробы, состоящая преимущественно из тяжелых частиц, называется шлихом. Если в шлихе оказывается много легких минералов (серый шлих), его дополнительно промывают —
![]() |
«доводят», сохраняя минералы полезных компонентов — золото, касситерит, вольфрамит и др.
Полученный шлих ссыпают в спе-а циальный бумажный капсюль — пакетик, номеруют и документируют. Обработка шлихов обычно производится в специализированных шлиховых лабораториях с разделением минералов по удельному весу, электромагнитным и другим свойствам. Крупные пробы промывают на специальных приборах — вашгердах, бутарах (рис. 47). В последние годы работниками ЦНИГРИ сконструирована новая передвижная установка
о о о о о о о о о о
75 - 100 мм |
![]() |
о о о о о
Рис. 46. Инструменты для промывки Ы шлиховых проб о — поток (вид1 сверху и разрез); б — ковш (вид сверху и разрез); в — гребок |
Рис. 47. Вашгерд (план и продольный разрез)
1 — корпус; 2 — съемная воронка с грохотом;
з - головная часть шлюза; 4 — плоскость
шлюза; S — выдвижная плоскость
для промывки проб — УПБ, которая отличается высокой производительностью и хорошим извлечением золота из песков.
При промывке крупных проб получается обычно «серый» шлих, в котором еще много легких минералов, и его приходится дополнительно промывать в лотке или ковше.
На россыпных месторождениях касситерита, вольфрамита, ильменита, циркона и ряда других полезных минералов для промывки проб используют в последние годы поисковый сепаратор ПВС. Производительность таких сепараторов составляет 20—100 кг в час исходного материала»
ОПРЕДЕЛЕНИЕ НАЧАЛЬНОГО ВЕСА ПРОБ
По мере увеличения начального веса пробы ее приготовление, отбойки обработка до конечного веса, поступающего на химический анализ, становятся сложнее и дороже. Поэтому следует стремиться к сокращению первоначального веса проб. Однако какого-либо надежного способа определения этого веса пока не разработано и обычно он устанавливается по
^^ ^
ными работами. При определении начального веса проб и подборе аналогов рекомендуется учитывать следующие факторы.
1. Сложение, или текстура, руды (минерального сырья) оказывает
решающее влияние на величину начального веса проб. При опробовании
руд с полосчатой, ленточной или массивной текстурой бороздой, напра
вленной вкрест полосчатости, начальный вес пробы может быть резке/
уменьшен без нарушения ее представительности. При опробовании руд
с пятнистой, брекчиевидной или конгломератовидной текстурами, а также
вкрапленных руд с крупными выделениями рудных зерен начальный
вес проб приходится значительно увеличивать.
2. Крупность зерен рудного минерала — чем крупнее зерна рудного
минерала, тем больше вес пробы.
3. Количество зерен рудного минерала в пробе — чем больше числе?
зерен рудного минерала в пробе, тем менее вероятна ошибка в определе
нии содержания полезного компонента.
4. Различие в удельных весах рудных и нерудных минералов — чем
больше различие в удельных весах, тем больше вес пробы. Одно излишнее
зерно рудного минерала в пробе может исказить содержание полезного
компонента, так как оно в несколько раз тяжелее нерудного, которых для
компенсации этого зерна нужно 2—3 и более.
5. Порядок среднего содержания полезного компонента — чем выше
содержание металла в руде и равномернее его распределение, тем меньше
начальный вес пробы.
6. Требуемая точность химического анализа — чем выше требования
к точности анализов, тем больше должен быть начальный вес пробы»
КОНТРОЛЬ АНАЛИЗОВ
Тщательная оценка качества минерального сырья при разведке месторождений совершенно обязательна и ей всегда следует уделять большое внимание.
a % ± A |
Рис. 48. Характеристика анализов по их точности 1 — точно; 2 — с большой случайной погрешностью; з — с большой случайной и систематической погрешностью; 4 —с систематической погрешностью; а — истинное содержание компонента; ±Д — допустимые отклонения от истинного содержания |
Надежное определение качества минерального сырья имеет гораздо большее значение, чем определение его количества. Ошибки в определении качества минерального сырья оказывают влияние на выбор технологической схемы его переработки и с первых же дней существования предприятия нарушают его нормальную работу. Если содержания полезных компонентов окажутся завышенными по сравнению с фактическими, то предприятие не выполнит план по выпуску продукции и будет терпеть убытки. Занижение содержаний не позволит планировать полное использование ресурсов месторождения и создаст условия для бесконтрольных потерь при добыче и переработке.
Неправильная оценка количества запасов месторождения, разумеется, также влияет на выбор производительности предприятия и определение себестоимости продукции. Но построенное на базе месторождения предприятие может испытать затруднения от неподтверждения запасов лишь через ряд лет, за время которых чаще всего удается выявить дополнительные запасы за счет расширения уже известных или обнаружения новых тел полезных ископаемых.
Содержания полезных компонентов в минеральном сырье, определяемые теми или иными методами, должны обязательно проверяться специальными контрольными анализами, которые призваны подтвердить надежность основных массовых определений и правильность работы основной, обычно химической, лаборатории.
При оценке качества анализов различают их точность и верность. Эти понятия наглядно иллюстрируются схемой, приведенной на
рис. 48.
Точность анализов проверяется внутренними контрольными анализами, которые производятся той же лабораторией, где выполнялись анализы рядовых проб. Верность анализов проверяется внешними контрольными анализами, которые производятся в другой не менее квалифицированной лаборатории. Кроме того, в случае наличия серьезных расхождений между рядовыми и внешними контрольными анализами необходимо проведение арбитражных анализов в третьей, наиболее авторитетной лаборатории.
Рекомендуется направлять на контрольный анализ пробы, группируя их: по периодам основных анализов, пределам содержания металла в руде, объемному весу, типам руд, участкам месторождения, типам проб и аналитикам, выполнявшим рядовые анализы, и определять отклонения контрольных анализов по такого рода группам проб.
Пробы для контрольных анализов передаются в лабораторию в Зашифрованном виде. Однако для улучшения качества контрольных
анализов одновременно с передачей проб лаборатории следует сообщить сведения о минеральном составе руды и приблизительном содержаний полезного компонента для правильного выбора методики анализов.
Необходимо иметь в виду, что контрольные анализы (как внешнего, так и внутреннего контроля) должны быть представительными, особенно по содержанию контролируемого компонента. Нельзя допускать, чтобы, например, руды с высоким содержанием полезного компонента были проконтролированы, а для руд с низким содержанием полезного компонента контрольные анализы отсутствовали или их было недостаточно для надежных выводов о точности и верности анализов с этим содержанием полезного компонента.
При определении содержаний полезных компонентов в минеральной сырье могут быть допущены как случайные, так и систематические погрешности. Внутренний контроль призван выявлять случайные, а внешний —< систематические погрешности анализов. Кроме случайных и систематических погрешностей в математической статистике выделяют так назьн ваемые «промахи». К «промахам» относятся резкие расхождения между основными и контрольными анализами (как внутреннего, так и внешнего контроля), которые могут быть вызваны причинами, не имеющими прямого отношения к производству анализов, например перепутаны номера-проб и др.
До обработки результатов контрольных анализов такие «промахи>* должны быть исключены из общего списка контрольных анализов и каждый из них («промахов») должен быть проверен дополнительно с выявлением причин, вызвавших эти резкие расхождения.
Внутренний контроль
Основной задачей внутреннего контроля является своевременное выявление и устранение недопустимых случайных погрешностей рядовых анализов, связанных с неудовлетворительной работой лаборатории. Изве-* стно, что случайные погрешности определения той или иной величины подчиняются закону нормального распределения. Это дает основание величину средней случайной погрешности определять как среднеарифметическое из индивидуальных проб без учета их знака. Пример определения средней случайной погрешности приведен в табл. 13. Средняя абсолютная случайная погрешность определяется по формуле
Д = -4^, (15)
где А — средняя абсолютная случайная погрешность;
Дг — величина отклонений между основными х и контрольными у анализами без учета знака (х{ — yt);
п — количество анализов.
Наиболее важная величина — средняя относительная погрешность — определяется по формуле
(16)
где Аотн — средняя относительная случайная погрешность;
Со — среднее арифметическое содержание полезного компонента в основных пробах.
Величина средней относительной случайной погрешности должна вычисляться по отношению к среднему содержанию полезного компонента в основных, а не в контрольных анализах. Применяемое иногда определение величины средней случайной погрешности сопоставлением средних содержаний по основным и контрольным анализам является неправильным. В нашем примере разница между средними содержаниями по основным и контрольным анализам составляет всего 0,01% (2,88—2,87); такой расчет вуалирует фактическую величину случайной ошибки и не может приниматься во внимание.
Очень важно, чтобы внутренний контроль был систематическим. Для этой цели пробы на контрольный анализ необходимо отбирать от дубликатов проб регулярно, например один-два раза в квартал, и отпра-правлять в основную лабораторию с зашифрованными номерами. При большом количестве проб обычно достаточно 3—-5% от их общего количества, а при небольшом объеме опробования — 30—50 анализов, равномерно распределенных в течение периода контроля.
Точность анализов должна "быть проверена для каждого природного типа полезного ископаемого и по его сортам в зависимости от содержания полезного компонента. Допустимые средние случайные погрешности в определении содержаний компонентов для большинства руд предусмотрены инструкциями ГКЗ. В табл. 14 приведены некоторые из этих величин.
Таблица 13 Сопоставление внутренних контрольных анализов с основными
Jift пробы основной/контрольной | Содержание полезного комплекса, % | Отклонения А(= *1 — VI | |
по основному анализу х | по контрольному анализу у | ||
873/2001 874/2002 875/2003 876/2004 1906/2035 | 2,15 2,48 1,95 3,41 3,21 | 2,51 1,98 2,15 2,41 3,02 | —0,36 +0,50 -0,20 +1,00 +0,19 |
Итого | 100,78 | 100,41 | 10,75 |
Среднее содержание полезного компонента в основных пробах Со= 100,78: 35 =
= 2,88.
То же, в контрольных пробах Ск=100,41: 35 = 2,87. _
Средняя абсолютная величина случайной погрешности Д= 10,75:35 = 0,31%.
Средняя относительная величина случайной погрешности Дотн =0,31: 2,88-100=
= 10,7%.
Таблица
Допустимые средние случайные погрешности химических анализов руд черных и цветных металлов
Содержание | Предельно допустимая средняя | Содержание | Предельно допустимая средняя | ||
в руде (в по- | случайная пог- | в руде (в по- | случайная пог- | ||
Компоненты | роде) в абсолютных про- | решность в процентах к содер- | Компоненты | роде) в абсолютных про- | решность в процентах к содер- |
центах, а для | жанию опреде- | центах, а для | жанию опреде- | ||
серебра в г/т | ляемого элемен- | серебра в г/т | ляемого элемен- | ||
та в пробе | та в пробе | ||||
Железо | Выше 30 | 1—2 | 0,5—10 | 6—15 | |
10—30 | 2-4 | До 0,5 | |||
5-10 | 4-8 | Медь | Выше 3 | 3—7 | |
Марганец | Выше 5 | 2-4 | 0,5—3 | 7—10 | |
1—5 | 4—7 | До | |||
|
|
Опора деревянной одностоечной и способы укрепление угловых опор: Опоры ВЛ - конструкции, предназначенные для поддерживания проводов на необходимой высоте над землей, водой...
Типы оградительных сооружений в морском порту: По расположению оградительных сооружений в плане различают волноломы, обе оконечности...
Кормораздатчик мобильный электрифицированный: схема и процесс работы устройства...
Адаптации растений и животных к жизни в горах: Большое значение для жизни организмов в горах имеют степень расчленения, крутизна и экспозиционные различия склонов...
© cyberpedia.su 2017-2024 - Не является автором материалов. Исключительное право сохранено за автором текста.
Если вы не хотите, чтобы данный материал был у нас на сайте, перейдите по ссылке: Нарушение авторских прав. Мы поможем в написании вашей работы!