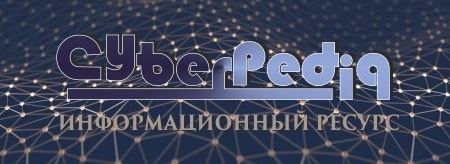
Типы сооружений для обработки осадков: Септиками называются сооружения, в которых одновременно происходят осветление сточной жидкости...
Автоматическое растормаживание колес: Тормозные устройства колес предназначены для уменьшения длины пробега и улучшения маневрирования ВС при...
Топ:
История развития методов оптимизации: теорема Куна-Таккера, метод Лагранжа, роль выпуклости в оптимизации...
Интересное:
Как мы говорим и как мы слушаем: общение можно сравнить с огромным зонтиком, под которым скрыто все...
Аура как энергетическое поле: многослойную ауру человека можно представить себе подобным...
Подходы к решению темы фильма: Существует три основных типа исторического фильма, имеющих между собой много общего...
Дисциплины:
![]() |
![]() |
5.00
из
|
Заказать работу |
|
|
Проектирование технологического процесса сварки представляет собой сложную оптимизационную задачу, основанную на использовании расчетных аналитических методов проектирования. Оптимальный вариант технологического процесса изготовления сложной сварной конструкции выбирается из нескольких расчетных вариантов технологии. В зависимости от основного назначения различают перспективные и рабочие технологические процессы. Типовой технологический процесс производства сварных узлов состоит из ряда основных операций в определенной последовательности: изготовление деталей, подготовка свариваемых поверхностей, сборка, прихватка, сварка, правка и механическая обработка, антикоррозионная защита.
Способ изготовления бензобака включает раздельное изготовление днищ (одного глухого и одного с горловиной) с цилиндрическими бортами на них посредством глубокой вытяжки и их последующая сварка.
Алюминий легко окисляется, образуя тугоплавкую окись алюминия (Аl2О3), плавящуюся при температуре свыше 2060°С. Поэтому перед сваркой поверхность алюминия необходимо подвергать предварительной обработке: обезжиривание растворителем (бензином, ацетоном, дихлорэтаном) и очистка механическим способом с помощью стальной вращающейся щетки из проволоки диаметром 0,15 мм. Химическая обработка по следующему режиму: обезжиривание в 5%-ном водном растворе едкого натра при температуре 60-65°С в течение 2 минут промывка в тепловой воде (не ниже температуры 45°С), а затем в холодной проточной воде осветление в 15%-ном водном растворе азотной кислоты при температуре 60-65°С в течение 2-5 минут промывка теплой водой, а затем холодной водой и сушка при температуре 60°С до окончательного удаления влаги. Сварку следует производить не позже 2-3 часов после очистки металла указанными способами. Очистке подвергают кромки детали и прилегающие к ним поверхности металла на ширине 20-30 мм в обе стороны от оси шва.
|
Прихватки представляют собой короткие сварные швы. Наложение прихваток необходимо для того чтобы положение свариваемых деталей и зазоры между ними сохранились постоянными в процессе сварки.
Прихватку осуществляем точеной сваркой рядом со швом в соответствие. Для более равномерного распределения сборочных зазоров прихватывают попеременно точками, расположенными диаметрально противоположными. Проверяем качество сборки визуальным осмотром и свариваем корпус бака. Проверяем качество сварки внешним осмотром [6].
7 Основные дефекты, возникающие в процессе образования сварного соединения
При контактной сварке:
• непровары;
• выплески;
• несплошности зоны сварки (трещины, раковины);
• снижение коррозионной стойкости соединений;
• неблагоприятные изменения структуры металла.
Непровар — наиболее опасный и трудновыявляемый дефект, при кото- ром зона совместного расплавления (при точечной сварке она определяется диаметром этой зоны меньше требуемой в чертеже изделия. Непровар может проявляться в виде полного отсутствия (см. рисунок 4, а) или уменьшения (см. рисунок 4, в) литого ядра, а также при частичном или полном сохранении оксидной пленки или плакирующего слоя в контакте деталь–деталь (см. рисунок 4, г, д). Наиболее опасен непровар, в котором образуется соединение в твердом состоянии (см. рисунок 4, б) по микрорельефам поверхности. Такое соединение трудно выявить, оно может выдержать иногда относительно большие статические срезывающие нагрузки и хрупко разрушиться при небольших напряжениях отрыва и знакопеременных нагрузках. При недостаточной энергии сварочного импульса размер ядра сварной точки оказывается меньше номинального значения, необходимого по условию эксплуатационной прочности (см. рисунок 4, в). Непровары, показанные на рис. 4, г, д, встречаются, например, при сварке алюминиевых сплавов (АМг6, Д16 и др.), имеющих на поверхности увеличенную толщину плакирующего слоя из чистого алюминия — металла, который обладает более высокой электропроводимостью, чем основной сплав. При плавлении основного металла плакирующий слой не расплавляется и препятствует образованию металлических связей в расплавленном состоянии. В этом случае, а также при относительно толстых тугоплавких оксидных пленках электромагнитные силы, необходимые для перемешивания расплавленного металла, оказываются недостаточными для их разрушения.
|
а — полное отсутствие соединения; б — соединение по отдельным микрорельефам; в — малый диаметр ядра; г — недостаточная зона взаимного сплавления; д — отсутствие совместного сплавления.
Рисунок 4 - Виды непроваров
Общая причина непроваров — неверный выбор параметров режима сварки, а также других технологических факторов (малые нахлестка и расстояние между точками, большие зазоры), приводящих к снижению плотности тока (тепловыделения). При шовной сварке отмечается постепенное снижение плотности тока и размеров литой зоны после сварки нескольких первых точек из-за накопления теплоты и снижения сопротивления пластической деформации металла. Это обстоятельство следует учитывать при выборе режима шовной сварки.
Для предупреждения непроваров следует обеспечить стабильность технологических факторов и работы сварочного оборудования, удаление перед сваркой тугоплавких оксидов и плакирующих слоев, препятствующих процессу образования зоны взаимного полного сплавления деталей.
Выплеск это выброс части расплавленного металла из зоны сварки (см. рисунок 5). Выплески разделяют на наружные (из области контакта электрод–деталь), внутренние (между деталями), начальные (на I этапе), конечные (на II этапе). Наружные выплески ухудшают внешний вид изделий и снижают стойкость электродов. Внутренние выплески часто препятствуют дальнейшему росту ядра вследствие повышенного растекания тока и охлаждения металла (с выплеском из зоны сварки «выносится» часть тепловой энергии). Конечные выплески часто являются причиной образования трещин, раковин и глубоких вмятин. Общая причина появления этого дефекта состоит в отставании скорости деформации от скорости нагрева. Например, начальные выплески объясняются перегревом отдельных участков (локальных контактов) относительно малой площади из-за перекоса электродов, плохой подготовкой поверхности. При сварке металлов с малым сопротивлением деформации выплески не характерны (алюминиевые и магниевые сплавы). Вероятность их появления возрастает при использовании жестких режимов сварки и небольших сварочных усилиях. Наиболее опасным и трудно выявляемым является внутренний конечный выплеск. Конечный внутренний выплеск связан с раскрытием зазора вследствие теплового расширения металла, прорывом уплотнительного пояска жидким металлом, находящимся под высоким давлением, и его «выбросом» из зоны сварки (см. рисунок 5, в). Недостаточное сварочное усилие при высоком давлении жидкого металла в ядре, а также не полностью сформированный уплотнительный поясок являются условиями, способствующими возникновению этого вида выплеска.
|
а — наружный; б — начальный внутренний;
в — конечный внутренний; г — конечный наружный
Рисунок 5 - виды выплесков
Предупредить раскрытие зазора и конечный выплеск возможно путем повышения усилия на 15–20% в конце цикла нагрева, а также размещения между деталями ленты или плакирующего слоя из пластичного металла. Почти полностью исключить его можно при обжатии металла вокруг электрода, что особенно важно при сварке деталей неравных толщин и из разноименных металлов.
Несплошности зоны сварки в стадии охлаждения часты случаи образования несплошностей в литом металле сварного шва: наружные и внутренние трещины, раковины (см. рисунок 6). Механизм образования несплошностей в кристаллизующейся точке объясняется неблагоприятным сочетанием деформационного и металлургического факторов. Температурное поле в условиях точечной и шовной сварки характеризуется значительной неравномерностью. Охлаждение металла в этих условиях приводит к возникновению растягивающих напряжений. Объемный характер совместных воздействий напряжений показан на рис.6 в приложении к элементарному объему металла. Такие напряжения наиболее опасны, так как сопротивление металла образованию несплошностей в этом случае оказывается наименьшим. Металлургические процессы в ядре характеризуются сходящимся ростом дендритов и скоплением в центре жидких или малопрочных составляющих расплава. Поэтому именно по центру наиболее вероятно нарушение сплошности точки под действием растягивающих напряжений.
|
Рисунок 6 - Схема образования трещин и рыхлот при точечной сварке
К образованию рассеянных или сосредоточенных несплошностей (раковин) приводит недостаток металла при кристаллизации ядра без внешнего давления (пластического деформирования металла). В связи с обычно высоким начальным давлением в ядре и большой скоростью охлаждения у большинства материалов образование центральной раковины маловероятно. Образование несплошностей наиболее часто наблюдается при сварке деталей толщиной свыше 1 мм из сплавов с широким температурным интервалом кристаллизации. Как показали исследования, рыхлости и трещины образуются преимущественно в температурном интервале хрупкости (ТИХ), соответствующем минимальной пластичности сплава. Разрушение металла носит в этом случае межкристаллический характер. Верхняя граница ТИХ близка к температуре ликвидуса и составляет, например, для углеродистых и конструкционных сталей 1200–1350 °C. Обычно с увеличением интервала кристаллизации расширяется область ТИХ и возрастает склонность сплава к образованию горячих трещин. Наибольшую чувствительность к горячим трещинам обнаруживают легированные алюминиевые сплавы (Д16, АМг6), особенно при значительной величине проплавления (объеме расплавленного ядра). По этой же причине при сварке высокоуглеродистых сталей трещины наблюдаются чаще, чем при соединении низкоуглеродистой стали. С другой стороны, увеличение количества легкоплавкой составляющей сплава (эвтектики) уменьшает вероятность образования трещин за счет увеличения пластичности сплава в ТИХ и возможности «залечивания» несплошностей и трещин жидкостью под действием усилия электродов.
Основные меры борьбы с указанными дефектами заключаются в созда-
нии благоприятного напряженного состояния металла с низким уровнем растягивающих напряжений и даже всесторонним сжатием. Это достигается в первую очередь резким повышением усилия на электродах (в 2–3раза) — проковкой соединения после выключения тока, когда металл находится в ТИХ.
Снижение коррозионной стойкости соединений в результате сварки.На химическую стойкость сварных соединений при их эксплуатации в агрессивных средах влияют: загрязнение их поверхности материалом электрода, повреждение защитных покрытий, электрохимический потенциал при сварке разнородных материалов, механический фактор. Снижение коррозионной стойкости соединений возникает в результате переноса части электродного металла на поверхность вмятины и может вызвать усиленную коррозию в этой части соединения, особенно у сплавов, чувствительных к коррозии в контакте с электроположительными элементами (например, на алюминиевых и магниевых сплавах в контакте с медью). Этот дефект на-зывается в практике контактной сварки «загрязнением» поверхностей деталей. Взаимодействие разнородных металлов в контакте электрод–деталь приводит, с одной стороны, к загрязнению рабочей поверхности электрода продуктами взаимодействия, с другой — к переносу электродного металла на поверхность детали. Формирование физического контакта, активация атомов и возникновение металлических связей (схватывание) происходит в основном в результате процессов сдвиговой пластической деформации в области наибольших касательных напряжений (зоне скольжения). Участки металлической связи служат каналами, по которым происходит диффузия металлов. Несмотря на малое время контактирования деталей при высокой температуре (в среднем менее 1 с), эти процессы часто получают достаточно большое развитие. Особенно большую чувствительность к процессам взаимодействия обнаруживают алюминиевые и магниевые сплавы, а также стали с легкоплавкими покрытиями, например цинком. Указанное свойство этих металлов связано с возможностью появления жидкой фазы в отдельных участках контакта с электродом. Наличие жидкой фазы значительно ускоряет процессы диффузии. Активность взаимодействия зависит от свойств поверхностных пленок. При сварке последующих точек ширина и глубина зоны взаимодействия в при контактном слое расширяются, тем самым существенно изменяя его физико-химические свойства. По мере сварки ряда точек металл в пределах вмятины все более и более насыщается продуктами взаимодействия. На определенном этапе требуется зачистка рабочей поверхности электрода для удаления продуктов взаимодействия, причем особенно часто это приходится делать при сварке магниевых сплавов (через 15–20 точек и через один оборот ролика при шовной сварке). Для сохранения коррозионной стойкости соединений следует принимать меры к торможению процессов массопереноса. К таким технологическим мероприятиям можно отнести: тщательную подготовку поверхности деталей перед сваркой, в том
|
числе для удаления продуктов, содержащих влагу и способствующих
вторичному окислению поверхности электрода, использование жестких режимов, сокращающих пребывание металла при повышенных температурах, применение предварительного обжатия деталей перед сваркой,
нанесение на поверхность деталей барьерных веществ (минеральных масел), препятствующих массопереносу (схватыванию) и вторичному окислению электродов, снижение температуры электродов посредством использования электродных материалов с высокой теплопроводностью, интенсивного охлаждения электродов и роликов водой и в ряде случаев — жидкими газами, удаление продуктов массопереноса с поверхности соединений после сварки.
Изменение структуры и свойств металла ядра и околошовной зоны вызывается термомеханическим воздействием на металл соединений. Литой металл ядра отличается относительно низкой пластичностью, особенно при сварке металлов, чувствительных к термическому циклу, например кон- струкционных закаливающихся сталей. Чаще всего при дендритной кристаллизации металла в центре ядра скапливаются (в результате ликвационных процессов) легкоплавкие компоненты, отличающиеся повышенной хрупкостью. Неравномерность состава ядра далеко не всегда удается устранить последующей термообработкой. Однако в большинстве случаев разрушение соединения происходит по металлу околошовной зоны, что в значительной степени снижает влияние свойств литого металла ядра на прочность сварного шва. В околошовной зоне могут наблюдаться изменения исходной структуры и свойств сплава в результате развития ряда процессов, связанных с термическим циклом сварки: закалки, оплавления легкоплавких составляющих по границам зерен (эвтектик), отпуска, рекристаллизации и т. п. При соединении низкоуглеродистой стали в участке, непосредственно примыкающем к ядру, наблюдается оплавление границ зерен (пережог металла). Далее расположен участок перегрева, отличающийся крупнозернистым строением и участками оплавления границ зерен аустенита. В участках, которые были нагреты выше температуры АC3, иногда обнаруживаются включения мартенсита, образующегося в результате быстрого охлаждения и торможения диффузии углерода. Для околошовной зоны характерно некоторое увеличение исходного зерна, что может привести к заметному снижению пластичности соединения, особенно при сварке холоднокатаной (наклепанной) стали.
Сплавы, не упрочняемые термообработкой, например сплавы АМг6 и МА2-1, склонны к рекристаллизации и укрупнению зерна, что может ска-заться на снятии эффекта нагартовки и снижении прочности соединений. Аустенитные стали, не стабилизированные введением карбидообразующих элементов (титана или ниобия), чувствительны к обеднению границ зерен хромом, что связано с диффузией углерода к границе зерна, и образованию на этих границах карбидов хрома. Подобное перераспределение примеси может привести к межкристаллитной коррозии. Однако заметное обеднение границ наблюдается при пребывании металла в интервале температур 550–700 °C более 1 мин. Степень развития указанных выше процессов можно в значительной мере регулировать за счет режимов сварки. В частности, явления рекристаллизации, выпадения (растворения) составляющих сплава и т. д., зависящие от процессов диффузии, легко подавляются при применении жестких режимов сварки. Склонность к закалке может быть снижена при использовании многоимпульсных режимов, замедляющих скорость охлаждения. Ширина зоны термического и механического влияния при точечной и шовной сварке, как правило, незначительна (иногда менее 1 мм) по сравнению с шириной этой зоны при других методах сварки в жидкой фазе, например при дуговой, вследствие малой длительности нагрева. Благоприятное влияние на свойства металла околошовной зоны оказывают в ряде случаев усилие сжатия и пластическая деформация, которая приводит к измельчению хрупких прослоек по границам зерен и снижению уровня растягивающих напряжений. Поэтому, как правило, сварные узлы, выполненные точечной и шовной сваркой, не нуждаются в последующей термообработке [6].
Заключение
В процессе выполнения курсовой работы подобран материал, рассчитаны параметры усиления на электродах, время включения сварочного тока, время цикла, шаг точек, силу сварочного тока, выбрано оборудование для контактной сварки. Описаны возможные дефекты и меры предотвращающие их появление.
Выбран рациональный способ контактной сварки. Разработан технологический процесс изготовления изделия.
|
|
Типы оградительных сооружений в морском порту: По расположению оградительных сооружений в плане различают волноломы, обе оконечности...
Своеобразие русской архитектуры: Основной материал – дерево – быстрота постройки, но недолговечность и необходимость деления...
Кормораздатчик мобильный электрифицированный: схема и процесс работы устройства...
Таксономические единицы (категории) растений: Каждая система классификации состоит из определённых соподчиненных друг другу...
© cyberpedia.su 2017-2024 - Не является автором материалов. Исключительное право сохранено за автором текста.
Если вы не хотите, чтобы данный материал был у нас на сайте, перейдите по ссылке: Нарушение авторских прав. Мы поможем в написании вашей работы!