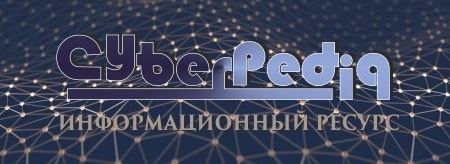
История создания датчика движения: Первый прибор для обнаружения движения был изобретен немецким физиком Генрихом Герцем...
Индивидуальные очистные сооружения: К классу индивидуальных очистных сооружений относят сооружения, пропускная способность которых...
Топ:
Эволюция кровеносной системы позвоночных животных: Биологическая эволюция – необратимый процесс исторического развития живой природы...
Определение места расположения распределительного центра: Фирма реализует продукцию на рынках сбыта и имеет постоянных поставщиков в разных регионах. Увеличение объема продаж...
Интересное:
Распространение рака на другие отдаленные от желудка органы: Характерных симптомов рака желудка не существует. Выраженные симптомы появляются, когда опухоль...
Искусственное повышение поверхности территории: Варианты искусственного повышения поверхности территории необходимо выбирать на основе анализа следующих характеристик защищаемой территории...
Средства для ингаляционного наркоза: Наркоз наступает в результате вдыхания (ингаляции) средств, которое осуществляют или с помощью маски...
Дисциплины:
![]() |
![]() |
5.00
из
|
Заказать работу |
|
|
ПРПИ»
ЕРГЕО»
Составил: Техническая обработка:
преподаватель горных дисциплин лаборант горных дисциплин
М.В. Ревука В.В. Бедило
Рассмотрено на методическом совете техникума
Протокол № ___ от «___» ___________ 2011 г.
Рассмотрено на заседании ц/к горных электромеханических дисциплин
Протокол № ___ от «___» ___________ 2011 г.
Председатель ц/к _______ М.В. Ревука
Рассмотрено на заседании ц/к горных технологических дисциплин
Протокол № ___ от «___» ___________ 2011 г.
Председатель ц/к _______ Т.А. Ефименко
Павлоград
СОДЕРЖАНИЕ
Тема 1. Транспорт под действием собственного веса: основы расчета транспорта, оборудование транспорта……………………………………………………………… | |
Тема 2.Монтаж и эксплуатация скребковых конвейеров. Правила безопасной работы…………………………………………………………………………………… | |
Тема 3. Монтаж и эксплуатация ленточных конвейеров. Правила безопасной работы……………………………………………………………………………………. | |
Тема 4.Специальные типы конвейеров………………………………………………. | |
Тема 5. Правила безопасности при установке грузолюдского конвейера. Автоматизация конвейерных линий…………………………………………………… | |
Тема 6. Пневмо- и гидротранспорт……………………………………………………. | |
Тема 7.Классификация и принципиальные схемы гидротранспортных установок.. | |
Тема 8. Тяговая сеть, преобразовательные подстанции, гаражи……………………. | |
Тема 9. Шахтные дизель-локомотивы………………………………………………… | |
Тема 10. Шахтные высокочастотные локомотивы, гировозы……………………….. | |
Тема 11. Штрекоподдирочные машины………………………………………………. | |
Тема 12. Транспорт скреперными установками: общие сведения, область применения и классификация скреперных установок; основные элементы; расчет скреперной установки…………………………………………………………………... | |
Тема 13. Расчет одноконцевой канатной откатки……………………………………. | |
Тема 14. Канатно-подвесные дороги………………………………………………….. | |
Тема 15. Подвесные монорельсовые дороги………………………………………….. | |
Тема 16. Нормы безопасности на подвесные дизельные монорельсовые дороги….. | |
Тема 17. Основные правила безопасности и противопожарные мероприятия при эксплуатации локомотивов……………………………………………………………... | |
Тема 18. Условные обозначения на транспортных схемах…………………………... | |
Тема 19. Технологические подземные транспортные схемы………………………... | |
Тема 20. Генеральный план угольной шахты………………………………………… | |
Тема 21. Технико-экономическая оценка работы транспортных машин и комплексов………………………………………………………………………………. | |
Тема 22. Пути совершенствования работы транспорта……………………………… | |
Список литературы…………………………………………………………………… |
Тема 1
|
Транспорт под действием собственного веса: основы расчета транспорта под действием собственного веса; оборудование транспорта
При достаточном угле наклона грузы могут перемещаться по горным выработкам под действием собственного веса. Транспорт под действием собственного веса, называемый иначе гравитационным или самотечным, используется также для передачи угля и руды, а иногда породы и закладочных материалов по скатам, печам, гезенкам и рудоспускам с одного горизонта на другой.
Тема 2
Монтаж и эксплуатация скребковых конвейеров. Правила безопасной работы
Монтаж и демонтаж скребковых конвейеров осуществляют по разработанным для каждого их типа инструкциям заводов-изготовителей.
|
Переноску разборных конвейеров на новую дорогу производят в следующем порядке: предварительно готовят новую дорогу для монтажа (подрывают или подсыпают почву дороги); ослабляют тяговую цепь конвейера и разделяют ее на отдельные отрезки; снимают рабочие рештаки и раскладывают их на новой подготовленной дороге; разъединяют и снимают холостую ветвь тяговой цепи; разъединяют и переносят нижние рештаки на новую дорогу; перетягивают приводную и натяжную головки.
При сборке конвейера на новой дороге: устанавливают приводную головку так, чтобы был хороший пересып; собирают нижний став рештаков и одновременно укладывают холостую ветвь тяговой цепи; соединяют нижний став с концевой головкой и протягивают через нее тяговую цепь; укладывают верхние рештаки и рабочую тяговую цепь; соединяют тяговую рабочую цепь с холостой и производят натяжение; рихтуют рештачный став. Затем производят проверку работы конвейера вхолостую и, если все нормально, проверяют его под нагрузкой.
Для передвижки конвейеров типа СП на новую дорогу применяют гидропередвижчики – систему гидродомкратов, рассредоточенных по длине лавы вдоль става работающего конвейера и объединенных общей насосной станцией.
Передвижку става конвейера осуществляют частями либо в конце цикла выемки по всей длине забоя. В первом варианте домкраты включают последовательно и став передвигают с изгибом вслед за проходом комбайна. Во втором варианте после прохода комбайна (струга) длины лавы полностью все домкраты включают одновременно и став конвейера передвигают на новую дорогу по всему фронту очистного забоя на шаг, равный стружке угля комбайном (стругом).
Гидропередвижчики оборудуют гидродомкратами для подъема рештачного става при расштыбовке холостой ветви или ее ремонте.
Безаварийная эксплуатация скребковых конвейеров обеспечивается выполнением технического обслуживания и правильной, согласно инструкции, эксплуатацией. В основу технического обслуживания положена система планово-предупредительных ремонтов с периодическими осмотрами, уходом и надзором за работой конвейера и своевременным устранением обнаруженных неисправностей.
При выполнении монтажных и эксплуатационных работ необходимо выполнять следующие правила безопасности: производить окончательный пуск конвейера спустя 4-8 с после подачи предупредительного сигнала; перед пуском проверять крепление приводной и натяжной головок, наличие защитных кожухов; не заливать муфты жидкостью, не рекомендованной заводской инструкцией; проводить осмотр и ремонт конвейера только при отключении пусковой аппаратуры и вывешивании предупреждающей надписи "Не включать, работают люди"; особо следить за правильным натяжением тяговой цепи, не допуская ее провисания на приводной станции более 150 мм.
|
Контрольные вопросы
1. Основные ПБ при работе скребкового конвейера.
2. Основные правила монтажа скребкового конвейера.
Тема 3
Монтаж и эксплуатация ленточных конвейеров. Правила безопасной работы
Монтаж магистральных конвейеров следует производить только по проекту. К началу монтажа должны быть:
подготовлены камеры и фундаменты для установки приводной и натяжной станций;
определены трасса установки и репер; проведены водосточные канавки;
осуществлена нивелировка почвы;
подготовлены ниши по длине става конвейера согласно ПБ с достаточным освещением и наличием противопожарного инвентаря;
закреплена горная выработка по всей длине установки конвейера огнестойким креплением и снабжена поручнями и сходнями (при монтаже выдержаны зазоры на высоте 1,8 м от почвы выработки), иметь проходы с одной стороны конвейера не менее 0,7 м, а с другой – 0,4 м, от верхней выступающей части груженого конвейера до верхняка крепи не менее 0,5 м, а у головных и приводных станций – не менее 0,6 м; в камерах приводных и натяжных станций (проход для людей не менее 1,0 м);
при дующих почвах смонтированы на мощных металлических рамах с анкерным креплением головная и приводная станции, а став конвейера подвешен к верхнякам крепи.
Монтаж механической части (концевые станции, опорные металлоконструкции, роликоопоры) ведут параллельно с монтажом электрического оборудования.
Начинают монтаж с головной секции бремсбергового конвейера, а при расположении привода вверху – с концевой секции. Для соблюдения правильности маркшейдерской оси начало монтажа совмещают с одновременной установкой головной и концевой станции, которые должны быть выставлены перпендикулярно оси конвейера. Соосность валов при соединении редуктора с электродвигателем и барабанами регулируют подкладками. Радиальное смещение осей валов редуктора и барабанов ленточных конвейеров не должно превышать 2,5 мм, а электродвигателя и редуктора – 0,5 мм. Перекос осей соединительных валов допускается не более 10. Направляющие рельсы для перемещения кареток натяжного или отклоняющего барабанов следует монтировать прямолинейно, а головки рельсов располагать на одном уровне, их отклонение от прямой линии не должно превышать 10 мм на длине 8 м. Запрещается расширение колеи более чем на 4 мм и сужение более чем на 2 мм. Став конвейера может быть установлен на почве выработки или подвешен к верхнякам. При этом допускается отклонение става от прямолинейности до 100 мм на длине конвейера 100 м и перекос секций става в плоскости, перпендикулярной к оси конвейера, не более 20 относительно горизонтальной плоскости. По окончании монтажа заливают масло в редукторы, навешивают ленту.
|
Правила эксплуатации конвейеров предписывают:
следить за правильностью хода ленты; очисткой приводной станции и работой всех роликоопор (нельзя, чтобы на какой-либо опоре не вращался ролик), целостью ленты и в первую очередь узлов ее соединения;
проверять натяжение ленты, не допуская ее провеса между роликоопорами более нормы;
устанавливать в местах перехода через конвейер переходные мостики шириной не менее 0,6 м с зазорами между лентой и нижней частью мостика не менее 0,4 м и высотой для перехода людей над мостиком не менее 0,8 м;
не производить смазку и мелкий ремонт работающего конвейера;
особо следить за исправностью загрузочного устройства, в наклонных конвейерах – за наличием ловителей лент, за безопасной работой тормозной системы;
поддерживать в исправности звуковую и кодовую сигнализацию;
иметь в наличии противопожарные средства.
Основными причинами схода ленты в сторону являются: нецентральная загрузка груза на ленту; перекос верхних и нижних роликоопор; неправильная стыковка ленты; искривление оси става конвейера; заштыбовка приводного барабана и става конвейера; разнотипность стыкуемых лент с разным линейным удлинением.
Если исключены указанные выше нарушения, а лента все-таки уходит в сторону, то по длине става этих участков устанавливают боковые прорезиненные ролики через каждые 10-20 м с обеих сторон ленты.
Совершенствование конвейерного транспорта происходит по пути внедрения конвейеров параметрического ряда, телескопических конвейеров, расширения области применения в магистральных наклонных выработках с углом наклона свыше -160 и +180, создания приводных конвейеров практически не ограниченной длины и конвейеров для искривленных в плане горных выработок.
|
Контрольные вопросы
1. Основные ПБ при работе ленточного конвейера.
2. Основные правила монтажа ленточного конвейера.
Тема 4
Специальные типы конвейеров
Основное достоинство ленточных конвейеров – выполнение функций тягового и несущего органов одним органом (лентой), обусловливающее конструктивную простоту и другие преимущества ленточных конвейеров, связано, однако, со сложностью увеличения длины одного става, так как повышение тягового усилия в этом случае требует повышения прочности ленты и вызывает значительное ее удорожание. В ленточно-канатных и ленточно-цепных конвейерах тяговое усилие воспринимается канатами или цепями, а связанная с ними лента служит только несущей поверхностью.
Общий недостаток ленточно-канатных и ленточно-цепных конвейеров – сложность конструкции. Однако применение их позволяет значительно снизить стоимость ленты и увеличить длину. Ленточно-канатные и ленточно-цепные конвейеры могут применяться как для транспортирования угля, так и руды и породы, а также для перевозки людей.
Ленточно-канатные конвейеры
В настоящее время предложен ряд конструкций ленточно-канатных конвейеров, которые по способу соединения ленты с канатом могут быть:
а) с глухим соединением (зажимы, муфты, гильзы);
![]() |
Рис. 4.1Ленточно-канатный конвейер: а – схема конвейера; б – поперечное сечение и вид сбоку |
б) с управляемыми захватами, разъединяющими канат и ленту при подходе к приводной и натяжной станциям и соединяющими после схода каната с них;
в) с лентой, свободно лежащей на канатах и приводимой в движение трением.
Наиболее многочисленны конвейеры третьей группы. Из них широкое практическое применение получили конвейеры, в которых канаты образуют два параллельных замкнутых в вертикальной плоскости контура, а лента специальной конструкции опирается на канаты. Такой ленточно-канатный конвейер (рис. 4.1) состоит из двух параллельных канатов 1, ленты 2 с завулканизированными в ней через определенные промежутки стальными полосами 3, на выступающие концы которых надеты башмаки 4, опирающиеся на канаты. Канаты движутся по поддерживающим блокам 5, увлекая в движение силой трения башмаки, а с ними и ленту. При подходе к приводной станции канаты огибают шкивы 6, установленные на торцах разгрузочного барабана 7, затем отклоняющие шкивы 8, верхняя часть которых наклонена от оси конвейера, и приводные шкивы 9. После сбегания с приводных шкивов канаты проходят под шкивами 6 так, что на них ложатся башмаки ленты, отделяющиеся в нижней точке шкива 6 от канатов. При подходе к натяжной станции лента огибает натяжной барабан 10, в результате чего башмаки поднимаются с канатов. Канаты огибают натяжные шкивы 11, отклоняющие шкивы 12 и шкивы 13, установленные на торцах барабана 10. В верхней точке шкивов 13 канаты вновь входят в соприкосновение с башмаками. Для натяжения ленты барабан 10 и шкивы 12 устанавливают на передвигающейся по рельсовым путям тележке, на которую воздействует натяжной груз 14; для натяжения канатов шкивы 11 также устанавливают на передвижной тележке, на которую воздействует натяжной груз 15. При такой конструкции конвейера часто происходили заклинивания кусков угля между лентой и канатом. Поэтому башмаки были заменены сплошными утолщениями ленты по обеим ее сторонам. В утолщениях сверху и снизу сделаны желобки, которыми лента опирается на канаты.
![]() |
Рис.11.2Схема ленточно-канатного конвейера с одним канатом |
Достоинства ленточно-канатных конвейеров: более продолжительный срок службы и удешевление ленты: бóльшая длина конвейера на один привод; небольшая величина сопротивления движению и расхода энергии. Недостатки: сложность конструкции и значительные размеры концевых станций; трудность изменения длины; необходимость применения специальной конвейерной ленты; меньший допускаемый угол подъема по сравнению с ленточными конвейерами.
Более простым является конвейер с одним канатом 1 (рис. 4.2), движущимся на рабочей ветви по среднему ролику обычной трехроликовой опоры и помещающимся в полукруглом желобке, сделанном в утолщенной средней части ленты 2. Однако в этом случае усложняется конструкция ленты и возникает необходимость поддержания холостой ветви двухроликовой опорой (между двумя роликами проходит утолщение ленты), а также уменьшается предельная длина конвейера, так как тяговое усилие воспринимается одним канатом.
Ленточно-цепные конвейеры
![]() |
Ленточно-цепные конвейеры по своей схеме аналогичны ленточно-канатным, но вместо канатов тяговым органом их является одна или две цепи. Наиболее простой является конструкция с двумя тяговыми цепями, прикрепленными к краям ленты и огибающими приводные звездочки. На верхней ветви цепи и лента движутся по роликам, смонтированным на раме конвейера; на нижней ветви цепи движутся по полосам из износоустойчивой стали, а лента поддерживается только цепями.
Один из недостатков конвейера с двумя цепями, присоединенными к ленте, - разрывы ленты в местах ее прикрепления. Поэтому в последующих конструкциях были применены другие способы передачи ленте тягового усилия от цепи.
В конвейере, схема и поперечное сечение которого показаны на рис. 4.3, к звеньям цепи 1 прикреплены тарельчатые пластины 2, покрытые фрикционным материалом, на которые опирается средняя часть рабочей ветви ленты 3. Боковые части рабочей ветви опираются на обычные ролики 4. Холостая ветвь ленты движется по однороликовым опорам 5, а холостая ветвь цепи лежит на ленте. Цепь движется по направляющим 6 на ходовых роликах 7 и огибает приводную 8 и натяжную 9 звездочки, а лента огибает разгрузочный 10 и натяжной 11 барабаны и приводится в движение силой трения между пластинами 2 и нижней обкладкой рабочей ветви. Достоинство такого конвейера – возможность установки промежуточных приводов, что позволяет получить любую величину длины одного става.
В ленточно-цепных конвейерах используется также присоединение ленты при помощи различного рода зажимов к подвижным кареткам, соединенным тяговой цепью. Каретки могут иметь как ходовые, так и направляющие ролики, что позволяет применять ленточно-цепные конвейеры в непрямолинейных выработках. Так как при проходке криволинейных участков лента с одной стороны сжимается, а с другой растягивается, то ее или закрепляют на каретках так, чтобы она могла растягиваться и сжиматься без повреждения, или делают гофрированной (складчатой). Гофрированная лента легко проходит криволинейные участки и позволяет транспортировать груз на подъем до 300.
Типажом на ленточно-цепные конвейеры предусмотрен выпуск 5 типов конвейеров. Их основные параметры: ширина несущего полотна 800 ÷ 1200 мм, производительность 250-600 т/ч, скорость движения 1,25 м/сек, ориентировочная длина 1500 м.
Пластинчатые конвейеры
![]() |
Рис. 4.4Схема пластинчатого конвейера |
![]() |
Рис. 4.5Типы настила пластинчатых конвейеров: а – плоский; б – плоско-чешуйчатый; в – волнистый; г - коробчатый |
Пластинчатый конвейер (рис. 4.4) состоит из одной или двух параллельных замкнутых тяговых цепей с укрепленными на них поперечными пластинами 1, частично перекрывающими друг друга. Пластины образуют сплошную чешуйчатую ленту. Цепи приводятся в движение от приводных звездочек 2. На противоположном конце конвейера цепи огибают хвостовые звездочки 3, которые соединяются с натяжным устройством. Пластинчатая лента перемещается на роликах, вследствие чего сопротивление передвижению и расход энергии на транспортирование в этих конвейерах значительно меньше, чем в скребковых.
Пластинчатые конвейеры применяются для транспортирования полезного ископаемого (уголь, руда), пустой породы и закладочного материала, а также для доставки материалов и оборудования и перевозки людей.
Достоинства пластинчатых конвейеров: перемещение груза несущим полотном (а не волочением по неподвижному желобу, как у скребковых конвейеров); небольшой расход энергии; незначительное измельчение перемещаемого груза; возможность установки в криволинейных выработках и применения промежуточных приводов, что позволяет транспортировать материалы практически на любое расстояние без перегрузки; прочность и долговечность конструкции.
Основные недостатки пластинчатых конвейеров: сложность конструкции, большой вес и высокая стоимость, трудность очистки пластин при влажных и липких материалах, склонность к заштыбовке направляющих для ходовых роликов, а также подшипников самих роликов. Однако вследствие значительных эксплуатационных достоинств пластинчатые конвейеры получают все большее применение в горной промышленности, особенно в криволинейных выработках.
Пластинчатые конвейеры, применяемые в горной промышленности, делятся:
1) по назначению: а) забойные, б) забойно-штрековые, в) штрековые и уклонные;
2) по исполнению несущего органа: а) жесткие (для прямолинейных выработок), б) изгибающиеся (для криволинейных выработок);
3) по типу опор несущего полотна: а) с неподвижными роликовыми опорами, б) с ходовыми роликами, движущимися вместе с полотном;
4) по числу цепей: а) одноцепные, б) двухцепные;
5) по количеству приводов: а) одноприводные, б) многоприводные;
6) по расположению приводов: а) с концевыми приводами, б) с промежуточными приводами.
Контрольные вопросы
1. Область применения конвейеров специальной конструкции.
2. Достоинства и недостатки ленточно-цепных, ленточно-канатных, пластинчатых конвейеров.
3. Особенности конструкции ленточно-цепных, ленточно-канатных, пластинчатых конвейеров.
Тема 5
Правила безопасности при установке грузолюдского конвейера. Автоматизация конвейерных линий
Тема 6
Пневмо- и гидротранспорт
В химической, нефтехимической, нефтеперерабатывающей и других отраслях промышленности наиболее широко используется пневмотранспорт, причем не только для перемещения материалов, но и как составная часть технологических установок для осуществления химических, тепловых, массо- и ионообменных процессов в системах газ-твердое тело. Преимущества пневмотранспорта перед другими видами транспорта - простота, высокая производительность и надежность, возможность полной автоматизации.
Наиболее распространенный транспортирующий агент - воздух, но по технологическим соображениям могут использоваться и другие газы, например, азот - для транспортирования пожаро- и взрывоопасных материалов. Воздействие транспортирующего газа на сыпучий материал может быть прямым или косвенным. В первом случае транспортирование материалов в трубопроводах и аппаратах осуществляют в потоке газа за счет перепада давления последнего. Во втором случае транспортируемый материал перемещается ("течет") по аэрожелобам и аппаратам в псевдоожиженном (аэрируемом) состоянии под действием силы тяжести. Сочетание прямого и косвенного воздействия транспортирующего газа на материал используют при пневмотранспортировании в плотном слое (когда сыпучая масса с высокой концентрацией твердой фазы перемещается в виде столба или "пористого поршня").
Для осуществления пневмотранспортирования применяют комплексы устройств -пневматические транспортные (пневмотранспортные) установки периодического или непрерывного действия. Основной элемент в них - транспортный трубопровод, который может быть прямым или составленным из колен, располагаться горизонтально, вертикально и наклонно. Он состоит из стальных бесшовных труб с приварными фланцами. Толщина стенок труб колеблется от 1 до 10 мм в зависимости от абразивного действия перемещаемого материала и давления в трубопроводе. Наиболее эрозионному износу от абразивного действия транспортируемых материалов подвергаются колена трубопроводов.
Для характеристики действия пневмотранспортных установок обычно определяют следующие показатели:
1) производительность по твердой фазе - масса твердой фазы, переносимая через поперечное сечение трубы в единицу времени;
2) массовый или объемный расход транспортирующего агента - соответственно масса или объем газа, прошедшего через поперечное сечение трубы в единицу времени;
3) массовая расходная концентрация m (в кг/кг) транспортируемого материала, равная отношению массового расхода твердой фазы к массовому расходу газа; различают установки с низкой (m < 4), средней (m = 4-20) и высокой (m > 20) концентрацией частиц материала; при транспортировании материалов в плотных слоях m может достигать 500-600 кг/кг;
4) скорость завала - скорость транспортирующего потока, при которой наступает завал (т.е. прекращение восходящего движения транспортируемых частиц в вертикальном трубопроводе); связана со скоростью потока, при которой частица находится во взвешенном состоянии (так называемой скоростью витания);
5) скорости транспортирующего агента и транспортируемого (перемещаемого) материала, равные отношениям соответственно объемных расходов газа и твердой фазы к площади поперечного сечения трубы; скорость транспортирующего газа определяется порочностью (долей объема свободного пространства между частицами в единице объема, занятого слоем материала) и должна превышать скорость завала. Скорость перемещения материала в пневмотранспорте зависит от размера и плотности частиц, концентрации твердой фазы, плотности, вязкости и скорости газа. Скорость транспортирования пылевидных материалов низкой концентрации может приближаться к скорости движения газа; при пневмотранспортировании в плотном слое скорость транспортирования обычно не превышает 4-7 м/с;
6) гидравлическое сопротивление - сопротивление движению газа, приводящее к потере механической энергии потока.
Так как теория пневмотранспорта разработана еще недостаточно, то для определения большинства названных величин используют обобщенные эмпирические зависимости, полученные в результате обработки экспериментальных данных для различных материалов. Эти зависимости приводятся в специальной литературе.
Конструкция пневмотранспортных установок различаются в зависимости от вида перемещаемых объектов и типа воздействия транспортирующего газа. Наиболее распространены установки для перемещения сыпучих материалов, в которых используется прямое или косвенное воздействие газа. В первом случае различают установки всасывающие, нагнетательные и всасывающе-нагнетательные, а во втором случае - аэрационные и аэротранспортные.
Во всасывающих установках (рис. 6.1, а) побудитель расхода газа (вентилятор или вакуум-насос) 6 "просасывает" газ через всю систему. Дисперсный материал захватывается потоком газа в заборное устройство (сопло) 1, перемещается по системе трубопроводов 2, выделяется в осадителе (бункер или аппарат) 3 из потока газа. После осадителя газ очищается от пыли в пылеуловителе 5 и сбрасывается в атмосферу. Материал из осадителя выводится через шлюзовые затворы 4. Всасывающие установки удобны тем, что они работают без пылевыделения и способны забирать сыпучий материал из нескольких пунктов и передавать его в единый сборник-накопитель. В них используется вакуум (40-90 кПа).
В нагнетательных установках (рис. 6.1, б) сжатый компрессором 6 газ через масловодоотделитель 7 поступает в ресивер 8, который предназначен для скапливания газа с целью сглаживания колебаний давления, а также для охлаждения газа и отделения капель масла и влаги. К ресиверу может быть подключено несколько трубопроводов. Сыпучий материал подается с помощью питателей 9 различных конструкций, обеспечивающих герметичность ввода материала. После перемещения по трубопроводу 2 материал отделяется от газа в отделителе 3; газ сбрасывается в атмосферу через пылеуловитель 5; материал и пыль выгружаются из пневмотранспортной системы через шлюзовые затворы 4. Сжатый газ, подаваемый компрессором, может переносить материал при высокой концентрации на большие расстояния. Нагнетатательные установки удобны тогда, когда материал из одного пункта перемещается в несколько приемных пунктов. Они могут работать при низком (0,15-0,20 МПа), среднем (0,2-0,3 МПа) и высоком (0,3-0,4 МПа) давлении.
Всасывающе-нагнетатательные установки сочетают основные преимущества рассмотренных выше установок. В них используются заборные устройства всасывающего типа, работающие без пылевыделения, а в наиболее протяженном трубопроводе материал переносится под давлением при довольно высоких концентрациях. В небольших установках обе ветви (всасывающая и нагнетающая) могут работать от одного вентилятора.
В аэрационной (рис. 6.1, в)и аэротранспортной (рис. 6.1, г) установках материал перемещается в псевдоожиженном состоянии при высокой концентрации. Состояние псевдоожижения достигается подачей газа под пористую газораспределительную решетку 10.
Менее распространены контейнерные пневмотранспортные установки (рис. 6.1, д) для перемещения специальных контейнеров (тележек или капсул), основанные только на прямом воздействии транспортирующего газа. Через станцию загрузки 12 контейнер 13 подается в транспортный трубопровод 2, и под действием перепада давления перед и за контейнером он перемещается к станции выгрузки 14.
![]() | Рис. 6.1 Схемы основных пневмотранспортных установок: а – всасывающая; б – нагнетательная; в – аэрационная; г – аэротранспортная; д – контейнерная: 1 – сопло; 2 – пневмотранспортный трубопровод; 3 – осадитель (отделитель); 4 – шлюзовой затвор; 5 – пылеуловитель; 6 – побудитель расхода газа; 7 – масловодоотделитель; 8 – ресивер; 9 – питатель; 10 – пористая газораспределительная решетка; 11 – аэрожелоб; 12 – станция загрузки; 13 – контейнер; 14 – станция выгрузки. Стрелки – незакрашенные, наполовину закрашенные и полностью закрашенные – указывают направления движения соответствующего транспортирующего газа, смеси газа и материала, материала. |
![]() |
В гидротранспорте, который используется в химических производствах значительно реже, чем в пневмотранспорте, транспортирующим агентом служит преимущественно вода. При этом можно перемещать только те материалы, которые с ней не взаимодействуют. Конструкции узлов и элементов, схемы и методы их расчета для пневмотранспортных и гидротранспортных установок аналогичны. Достоинство гидротранспорта - высокая скорость транспортирования больших масс материалов. Основные недостатки - относительно большой расход воды, необходимость сложных устройств для отделения сыпучего материала от воды. Гидротранспорт применяют главным образом для перемещения больших количеств тяжелых материалов (например, песка) в строительстве.
Контрольные вопросы
1. Область применения пневмотранспорта.
2. Типы пневмотранспортных установок.
3. Достоинства и недостатки пневмотранспортных установок.
Тема 7
Классификация и принципиальные схемы гидротранспортных установок
По принципу действия гидротранспорт может быть самотечным и напорным. Этот вид транспорта может быть применен для доставки горной массы при гидравлическом способе разработки месторождения, от очистного забоя до обогатительной фабрики на поверхность. При этом могут быть совмещены доставка, откатка и подъем груза по вертикальным выработкам. Гидротранспорт может использоваться для перемещения горной массы между отдельными механизмами и аппаратами на обогатительных фабриках, транспортирования хвостов в отвалы и породы при гидровскрышных работах на разрезах, а также для механизации закладочных и заиловочных работ.
![]() |
Рис. 7.1 Гидротранспортные установки: а – самотечный транспорт; б – с естественным напором; в, г – с искусственным напором |
Самотечный транспорт (рис. 7.1, а) применяют на шахтах для доставки полезного ископаемого по горизонтальным и слабонаклонным выработкам с углом наклона не менее 0,03-0,07 при грузопотоках до 600 т/ч с длиной транспортирования до 1500 м. Перемещение груза при самотечном транспорте производится по деревянным и металлическим желобам, лоткам и дренажным канавам. При самотечном транспорте перемещение гидросмеси происходит под действием силы тяжести (скорость грузу сообщается за счет разности отметок h).
Напорные гидротранспортные установки используют при транспортировании насыпных грузов. Принцип их работы – перемещение гидросмеси под напором по трубам на необходимую высоту. Гидротранспортные установки могут иметь естественный напор, для чего необходим вертикальный или наклонный став трубопровода, и искусственный, создаваемый углесосами или центробежными насосами с питателями.
Установки с естественным напором (рис. 7.1, б) применяют для подачи в шахту закладочных материалов в выработанное пространство лав или в другие погашаемые горные выработки. Такие установки сооружают на поверхности шахты вблизи ствола, в котором проложены трубы для спуска пульпы.
Из приемного бункера 1 дробленая порода крупностью до 50 мм поступает в трубы 3, одновременно с этим в трубопровод 2 подается вода в количестве, необходимом для создания нужной концентрации пульпы.
Пульпа перемещается по трубопроводу 3, затем под давлением столба жидкости высотой Н переходит в проложенные по горным выработкам трубы и перемещается по ним до места закладки. Длина транспортирования L составляет (5 ÷ 6) Н при грузопотоке до 150 м3/ч и крупности материала 50 мм.
Напорное гидротранспортирование с искусственным напором (рис. 7.1, в, г) осуществляется под действием напора, создаваемого углесосами или центробежными насосами. Напор должен обеспечивать перемещение пульпы по трубопроводам и подъем ее на необходимую высоту.
Для загрузки пульпы в пульпопроводы применяют две принципиально различные схемы.
Схема загрузки с помощью углесосов (рис. 7.1, в) целесообразна для транспортирования по горизонтальным выработкам и подъема пульпы на поверхность шахты. Схема обеспечивает производительность до 1000 т/ч при высоте подъема на один углесос до 300 м. Пульпа из пульпосборника 3 захватывается углесосом 4 и далее перемещается по пульпопроводу 5.
Схема загрузки посредством центробежных насосов с питателем (рис. 7.1, г) на гидрошахтах не применяется, так как насосы не приспособлены для перекачки пульпы. Такие установки используют для подачи породы в отвал. Производительность установок до 1600 м3/ч, при длине транспортирования до 10 км и крупности кусков до 100 мм. Перед подачей в питатель породу дробят. Насос 1 из водосборника 2 захватывает чистую воду и подает в трубы, куда по пути поступает дробленая порода из питателя 4.
В установках с углесосами высота и производителньость могут быть увеличены в несколько раз, если углесосы переключить на последовательную или параллельную работу. Однако для этого требуются дополнительно оборудование и сооружение камер, увеличение численности обслуживающего персонала, что обусловит рост стоимости транспортирования и возможной аварийности из-за увеличения количества оборудования.
При использовании углесосов (рис. 7.1, в) уголь в лаве поступает в рештаки, где смешивается с водой. Пульпа доставляется на откаточные штреки и с помощью транспортных средств 1 подается в зумпф 3 (пульпосборник), но перед этим дробится на
|
|
Адаптации растений и животных к жизни в горах: Большое значение для жизни организмов в горах имеют степень расчленения, крутизна и экспозиционные различия склонов...
Автоматическое растормаживание колес: Тормозные устройства колес предназначены для уменьшения длины пробега и улучшения маневрирования ВС при...
Поперечные профили набережных и береговой полосы: На городских территориях берегоукрепление проектируют с учетом технических и экономических требований, но особое значение придают эстетическим...
Индивидуальные очистные сооружения: К классу индивидуальных очистных сооружений относят сооружения, пропускная способность которых...
© cyberpedia.su 2017-2024 - Не является автором материалов. Исключительное право сохранено за автором текста.
Если вы не хотите, чтобы данный материал был у нас на сайте, перейдите по ссылке: Нарушение авторских прав. Мы поможем в написании вашей работы!