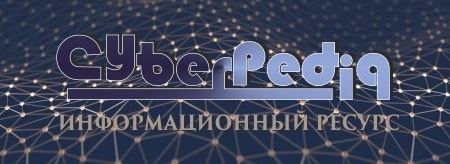
Биохимия спиртового брожения: Основу технологии получения пива составляет спиртовое брожение, - при котором сахар превращается...
Наброски и зарисовки растений, плодов, цветов: Освоить конструктивное построение структуры дерева через зарисовки отдельных деревьев, группы деревьев...
Топ:
Когда производится ограждение поезда, остановившегося на перегоне: Во всех случаях немедленно должно быть ограждено место препятствия для движения поездов на смежном пути двухпутного...
Генеалогическое древо Султанов Османской империи: Османские правители, вначале, будучи еще бейлербеями Анатолии, женились на дочерях византийских императоров...
Характеристика АТП и сварочно-жестяницкого участка: Транспорт в настоящее время является одной из важнейших отраслей народного...
Интересное:
Инженерная защита территорий, зданий и сооружений от опасных геологических процессов: Изучение оползневых явлений, оценка устойчивости склонов и проектирование противооползневых сооружений — актуальнейшие задачи, стоящие перед отечественными...
Средства для ингаляционного наркоза: Наркоз наступает в результате вдыхания (ингаляции) средств, которое осуществляют или с помощью маски...
Лечение прогрессирующих форм рака: Одним из наиболее важных достижений экспериментальной химиотерапии опухолей, начатой в 60-х и реализованной в 70-х годах, является...
Дисциплины:
![]() |
![]() |
5.00
из
|
Заказать работу |
|
|
Дуговая печь (рис. 1.) состоит из рабочего пространства (собственно печи) с электродами и токоподводами и механизмов, обеспечивающих наклон печи, удержание и перемещение электродов и загрузку шихты.
Плавку стали ведут в рабочем пространстве, ограниченном сверху куполообразным сводом, снизу сферическим подом и с боков стенками. Цикл плавки занимает от 42-48 мин., в зависимости от соотношения: скрап- жидкий чугун. Расход электроэнергии составляет 235-365 кВт/т. Температура плавления 1400-1600
Рис. 1. Дуговая сталеплавильная печь ДСП-200 ёмкостью 200 т:
1-графитированный электрод; 2- электрододержатель; 3- свод; 4- водоохлаждаемое сводное кольцо; 5- цилиндрический кожух; 6- водоохлаждаемая вспомогательная дверка; 7- электромеханический механихм поворота печи вокруг вертикальной оси; 8- электромеханический механизм наклона печи; 9- сливной носок; 10- подвижный токоподвод из водоохлаждаемых гибких кабелей; 11- шток для вертикального перемещения системы: стойка- рукав- электрододержатель- электрод; 12- токоподвод из охлаждаемых медных труб.
Огнеупорная кладка пода и стен заключена в металлический кожух. Съемный свод набран из огнеупорных кирпичей, опирающихся на опорное кольцо. Через три симметрично расположенных в своде отверстия в рабочее пространство введены токопроводящие электроды, которые с помощью специальных механизмов могут перемещаться вверх и вниз. Печь питается трехфазным током.
Шихтовые материалы загружают на под печи, после их расплавления в печи образуется слой металла и шлака. Плавление и нагрев осуществляется за счет тепла электрических дуг, возникающих между электродами и жидким металлом или металлической шихтой.
|
Выпуск готовой стали и шлака осуществляется через сталевыпускное отверстие и желоб путем наклона рабочего пространства. Рабочее окно, закрываемое заслонкой, предназначено для контроля за ходом плавки, ремонта пода и загрузки материалов.
Печь оснащается системой хранения, дозирования и подачи сыпучих материалов и ферросплавов. Конструктивно, электродуговая печь выполнена наклоняющейся для выпуска металла, а так же с подъемом и поворотом свода для обеспечения механизированной загрузки через верх (свод). Основной несущей конструкцией печи является двух- секторная люлька, на которой установлены составные части печи.
Кожух печи представляет собой сварную конструкцию и имеет разъем на уровне порога. Верхняя часть кожуха цилиндрическая, нижняя часть выполнена цилиндро- сферической формы.
Свод электропечи представляет собой комбинированную конструкцию:
-Футерованная купольная часть дельта- видной формы;
-Переферийная, из водоохлаждаемых элементов;
-Электрододержатели- выполнены с токоведущими водоохлаждаемыми рукавами с подачей воды на орошение электрода;
-Механизм подъема и поворота свода- служит для открывания печи под загрузку через верх.
Для обеспечения безопасности, в системе управления предусмотрены электрические блокировки.
Конструкция печи включает: систему водоохлаждения, воздухоподвода и маслоподвода.
Рис. 2. Кинематическая схема механизма подъема свода.
В схеме механизма подъема свода, сводное кольцо 3 соединено тягами 1 с трех-шарнирными рычагами 2, в свою очередь связанные между собой горизонтальными тягами 4. Система подвески свода образует механизмы с обеих сторон свода и обеспечивает его плоскопараллельное движение. Поворот сторон свода и рычагов 2 производится через промежуточные рычаги, систему, состоящую из горизонтальных 6 и вертикальных 8 тяг и трех- шарнирных рычагов 7. Привод снабжен двумя электродвигателями 19 и двумя червячно-винтовыми рудукторами-9, связанными между собой для синхронизации вала18. Скорость подъема свода 0,69 м/мин.
|
Рис. 3. Кинематическая схема механизма наклона электропечи
Механизм наклона электропечи выполнен с индивидуальным приводом реек 4, шарнирно связанных с люлькой 7. Реечные передачи 5 заключены в качающиеся обоймы 6. Опорно-поворотная часть люльки с опорными сегментами 8 и фундаментными балками 9. Для предупреждения возможного самопроизвольного опрокидывания, в сторону слива металла установлен убирающийся упор поворотного типа с гидроприводом.
Рис. 4. Кинематическая схема механизма перемещения электрода
Электропечь снабжена тремя независимыми механизмами перемещения электродов реечного типа. Один из механизмов перемещает две рейки, из которых одна связана с электрододержателем, а вторая с подвижным кронштейном, бифилярной системы токоподвода. Электрододержатель 2 (рис. 8.) закреплен на колонне 10, перемещающийся в направляющих роликах 11 шахты. Зубчатая рейка 5 соединяется с электрододержателем через амортизирующую пружину 4. Масса подвижных частей уравновешена противовесами 12, связанных с колонной пластинчатыми цепями 13. Привод состоит из электродвигателя 8, червячного редуктора 9, открытой 7 и реечной 6 передач. Масса подвижных частей- 31тонна. Механизм зажатия электрода 1 рычажно- пружинного типа. Освобождение электрода 14 производится пневмоцилиндром 3. Печь оборудована устройством для электромагнитного перемешивания металла.
Рис.5. Кинематическая схема механизма отворота свода
Механизм отворота свода (рис.5.) снабжен навесным приводом, состоящим из двух электродов 43 со встроенными тормозами, двух быстроходных трехступенчатых редукторов 44 и тихоходного одноступенчатого редуктора 46 с двумя ведущими валами. Электродвигатель и быстроходные редукторы установлены на качающихся рамах 54, шарнирно соединенных пружинными буферами 55 с корпусом тихоходного редуктора. Валы быстроходного редуктора посажены на конические хвостовики валов шестерен 45. Корпус тихоходного редуктора связан с платформой сферическим шарниром 56, исключающим поворот корпуса. Форсирование поворотной платформы в случае наклона электропечи осуществляется механизмом, состоящим из стопора 49 и гидроцилиндра 48 двойного действия. Гидроцилиндр и направляющие стопоры закреплены на металлической конструкции люльки.
|
Печь ДСП - 25 имеет следующие основные параметры:
емкость номинальная, т | |
мощность трансформатора, МВ | 7.5 |
пределы вторичного напряжения, В | (761-654)-250 |
диаметр электрода, мм | |
время расплавления под током, мин | <30 |
расход электроэнергии на расплавление, мДж/т | |
расход воды на охлаждение печи, м3/час |
В состав оборудования ДСП - 25 входят:
· электрогидравлический регулятор электрического режима АРФГ - 400/6, 3-Н с гидравлическим приводом перемещения электродов;
· печной трансформатор; механизм наклона ванны печи; механизм подъема и поворота свода;
· система охлаждения элементов стен, свода и токопровода;
· фурма для продувки металла кислородом; устройство замера температуры металла в печи;
· система отвода газов из печи;
· датчики технологических параметров (температура, давление, вес, расход) смежных с ДСП —100 систем;
· насосно-аккумуляторная станция.
Технология производства стали в ДСП - 25 высокой производительности, характеризуется следующими основными положениями:
1. Марочный сортамент включает углеродистые, низколегированные, легированные стали.
2. Основным принципом технологического процесса является ориентация плавки в печи на расплавление шихты, окислительное рафинирование (дефосфорация, обезуглероживание) и нагрев металла до температуры выпуска (1600 - 1700°С) с последующей десульфурацией, легированием, корректировкой состава и температуры в ковше при внепечной обработке, в том числе и с дуговым подогревом стали. При отсутствии подогрева в ковше операция легирования может частично осуществляться в печи.
3. Основными составляющими шихты являются подготовленный стальной лом и внутризаводские отходы, а также чушковый чугун. При наличии особых требований к качеству стали в состав шихты включаются металлизированные окатыши. Металлозавалка готовится в скрапном отделении цеха, где подготовленный лом с помощью кранов загружается в завалочные корзины. Корзины в процессе заполнения шихтой взвешиваются. Металлозавалка должна составляться таким образом, чтобы обеспечить загрузку печи не более чем в два приема: завалка - 70 - 75 т., подвалка - 35 - 40 т. Общий вес загружаемой шихты - не более 115 т.
|
4. Добавочные материалы (шлакообразующие, ферросплавы, кокс, окатыши) догружаются в печь через отверстие в своде. В отдельных случаях легирующие вводятся через рабочее окно мульдозавалочной машиной. Предусматривается также подача материалов в ковш. Шлакообразующие материалы и ферросплавы, используемые для выплавки и внепечной обработки металла, соответствуют стандартам и техническим условиям.
5. Для интенсификации расплавления шихты используются газокислородные горелки ориентировочной мощностью по 7 МПа. При общей длительности расплавления под током 50-55 мин. длительность работы горелок составляет 15-20 мин. Максимальный расход газа на горелку составляет 700 нм3/час, максимальный расход кислорода 1400 нм3/час.
6. Кислород для окислительного рафинирования подается через фурму, вводимую в печь. Расход кислорода составляет 50 м3/мин при давлении 1,2 - 1,5 Мпа. Длительность продувки – 15 - 40 мин.
7. Для обеспечения необходимой стойкости футеровки и снижения потерь энергии во время доплавления шихты и нагрева жидкого металла формируют пенистый шлак, экранирующий дуги, присадками по ходу плавки известняка или извести, кокса, окислительных окатышей или вводя кислород через погруженную в металл фурму.
8. Для контроля химического состава металла в процессе плавки отбираются 3 - 4 пробы металла из печи и 1 - 2 - из ковша при внепечной обработке. Время от момента отбора проб да получения результатов анализа составляет 8-10 мин.
9. Выпуск стали из печи, производиться без печного окисленного шлака, оставляемого в электропечи с некоторым количеством металла (до 10 т.). Масса металла, сливаемого в ковш, измеряется взвешивающим устройством на сталевозе. Периодически, через 5-7 плавок, металл и шлак выпускаются полностью, после чего производится заправка футеровки печи.
|
|
Общие условия выбора системы дренажа: Система дренажа выбирается в зависимости от характера защищаемого...
История создания датчика движения: Первый прибор для обнаружения движения был изобретен немецким физиком Генрихом Герцем...
Состав сооружений: решетки и песколовки: Решетки – это первое устройство в схеме очистных сооружений. Они представляют...
Археология об основании Рима: Новые раскопки проясняют и такой острый дискуссионный вопрос, как дата самого возникновения Рима...
© cyberpedia.su 2017-2024 - Не является автором материалов. Исключительное право сохранено за автором текста.
Если вы не хотите, чтобы данный материал был у нас на сайте, перейдите по ссылке: Нарушение авторских прав. Мы поможем в написании вашей работы!