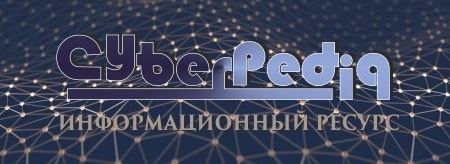
Своеобразие русской архитектуры: Основной материал – дерево – быстрота постройки, но недолговечность и необходимость деления...
Автоматическое растормаживание колес: Тормозные устройства колес предназначены для уменьшения длины пробега и улучшения маневрирования ВС при...
Топ:
Марксистская теория происхождения государства: По мнению Маркса и Энгельса, в основе развития общества, происходящих в нем изменений лежит...
Характеристика АТП и сварочно-жестяницкого участка: Транспорт в настоящее время является одной из важнейших отраслей народного хозяйства...
Генеалогическое древо Султанов Османской империи: Османские правители, вначале, будучи еще бейлербеями Анатолии, женились на дочерях византийских императоров...
Интересное:
Берегоукрепление оползневых склонов: На прибрежных склонах основной причиной развития оползневых процессов является подмыв водами рек естественных склонов...
Финансовый рынок и его значение в управлении денежными потоками на современном этапе: любому предприятию для расширения производства и увеличения прибыли нужны...
Что нужно делать при лейкемии: Прежде всего, необходимо выяснить, не страдаете ли вы каким-либо душевным недугом...
Дисциплины:
![]() |
![]() |
5.00
из
|
Заказать работу |
|
|
|
Наиболее часто применяют магнитный порошковый метод. В этом случае индикаторами полей рассеяния около поверхностных дефектов служат магнитные порошки или водно-мыльные суспензии. Порошок оседает на дефектах.
Ультразвуковая дефектоскопия. Ультразвуковые волны, используемые в дефектоскопии, представляют собой упругие колебания, возбуждаемые в материале объекта. При неразрушающей контроле используют следующие методы ультразвукового прозвучивания деталей: теневой, резонансный и эхо-метод.
|
Теневой метод заключается в непроходимости пучка ультразвуковых колебаний через инородное включение (расслоение, раковину и т.д.). Интенсивность пучка, падающего на приёмный щуп (7), резко уменьшается, т.е. на приёмный щуп упадёт тень от дефекта (9).
Эхо-метод основан на том, что в объект вводятся пучки колебаний – импульсы. Упругие колебания, встречая на своём пути препятствие в виде дефекта (9), отражаются и, как эхо, попадают обратно на излучающую головку (5).
Разряд.
Испытание на растяжение подробно описано в разряде 1-2. См. рисунок 19.
Для испытания на вытяжку применяют образцы в виде полосы, шириной 70-90 мм.
Образец зажимается между матрицей и прижимным кольцом и вытягивается лунка под действием движения пуансона. Признаком окончания испытания является появление на лунке сквозной трещины, видимой на просвет. На шкале индикатора фиксируется глубина лунки.
|
Испытание на изгиб применяют для малопластичных металлов, главным образом чугунов, а так же для закалённых и отпущенных сталей в состоянии высокой твёрдости (например, для инструментальных сталей).
Испытание состоит в изгибе образца вокруг оправки под действием статического усилия и служит для определения способности металла выдерживать заданную пластическую деформацию, характеризуемую углом изгиба, или для оценки предельной пластичности металла, характеризуемой углом изгиба до появления первой трещины. А так же при необходимости проводят испытания до параллельности сторон, до соприкосновения сторон.
Тема №4. Чугуны
Разряды.
1. Чугун получают восстановлением из природных руд железа с последующим насыщением его углеродом. Чугун выплавляют в высоких шахтных печах- домнах. Выплавляемые чугуны разделяют на передельные, специальные (ферросплавы) и литейные. Передельные и специальные чугуны в основном применяют для выплавки стали, а литейные чугуны – для отливки различных деталей станков и машин.
Чугун обладает важными физическими и технологическими свойствами: невысокой температурой плавления (1180-1200°С), повышенными литейными свойствами и высокой износостойкостью. Значительная хрупкость и малая пластичность обычных чугунов является их основным недостатком. Однако экономичность и другие свойства вполне компенсируют его недостатки. Присутствие эвтектики в структуре чугуна обуславливает его использование исключительно в качестве литейного сплава.
2. Металлическая основа ковкого чугуна: феррит - ферритный ковкий чугун, реже перлит - перлитный ковкий чугун. Наибольшей пластичностью обладает ферритный ковкий чугун, который применяют в машиностроении. Ферритный ковкий чугун КЧ37-12 и КЧ35-10 используют для деталей, работающих при ударных и вибрационных нагрузках. Максималь-ная твердость ферритного ковкого чугуна достигает 163 НВ. Тогда как перлитный ковкий чугун КЧ50-5, КЧ 56-4, КЧ 60-3 и КЧ63-2 обладает более высокой прочностью, умеренной пластичностью и хорошими антифрикционными свойствами. Твердость перлитного чугуна составляет НВ269. Из перлитного ковкого чугуна изготавливают вилки карданных валов, звенья и ролики цепей конвейера, втулки, муфты, тормозные колодки и т.д.
|
Ковкий чугун маркируют по ГОСТ 1215-79 буквами - КЧ и цифрами. Первые две цифры указывают предел прочности при растяжении, вторые цифры - относительное удлинение.
Например, КЧ 30-6:
ковкий чугун с пределом прочности – не менее 30 кгс/мм²; с относительным удлинением не менее- 6%.
Серый чугун. В сером чугуне весь углерод или значительная его часть содержится в свободном состоянии - в виде отдельных включений графита различной формы (в виде пластинок- пластинчатый графит).
Его структура может состоять из перлита или перлита и феррита с мелкими или крупными включениями фосфидной эвтектики. Серый чугун маркируют по ГОСТ 1412-85. Например, у серого чугуна марки СЧ 18-36 буквы СЧ означают серый чугун, первые цифры указывают на предел прочности при растяжении, а вторые - на предел прочности при изгибе.
Серый чугун применяют для отливки станин металлорежущих станков, блоков цилиндров, картеров коробок скоростей, поршневых колец и других деталей. Плавку чугунов обычно ведут в вагранках.
Для повышения механических свойств чугуна и измельчения в нем пластинчатого графита в литейном производстве широко используют модифицирование. При этом способе перед разливкой в жидкий металл добавляют специальные присадки - модификаторы в количестве 0,1-0,4% к весу жидкого металла. Модификаторы раскисляют чугун и создают искусственные центры графитизации. Модификаторами могут быть силикокальций, ферро-силиций, алюминий и др.
Высокопрочный чугун. В литейном производстве применяют модифицирование чугуна магнием, церием, висмутом для получения в нем графита не в виде пластинок как в сером чугуне, а в форме глобулей (сфер - шаровидный графит). Модифицирование магнием, а потом ферросилицием, позволяет получить структуру, состоящую из перлита, феррита и шаровидного графита. Такой чугун называется высокопрочным.
|
Магниевый чугун обладает прочностью литой стали и высокими литейными свойствами. Из магниевого чугуна изготавливают детали, подвергаемые ударам, воздействию переменных на-пряжений и износу, например, на Горьковском автомобильном заводе - коленчатые валы лег-кового автомобиля «Волга».
Маркировка высокопрочных чугунов осуществляется в соответствии с ГОСТ 7993-90.
ВЧ 40-10 означает - высокопрочный чугун со средним пределом прочности при растяжении - 40 кгс/мм²; с относительным удлинением – 10 %.
Разряд.
1. Влияние примесей. Обычный промышленный чугун не является двойным железоуглеродистым сплавом, а содержит те же примеси, что и углеродистая сталь, т.е. марганец, кремний, серу и фосфор, но в большем количестве, чем сталь. Эти примеси существенно влияют на условия графитизациии, следовательно, на структуру и свойства чугуна.
Кремний особенно сильно влияет на структуру чугуна, усиливая графитизацию. Содержание кремния в чугунах колеблется от 0,3-0,5 % до 3-5 %. Изменяя содержание кремния, можно получать чугуны, совершенно различные по свойствам и структуре, от белого до ферритного (серого с пластинчатым графитом или высокопрочного с шаровидным графитом).
При содержании 3 % С чугун содержанием до 0,5 % Si будет белым, от 1 до 2 % - серым перлитным, а свыше 3 % - серым ферритным. В промежуточных областях сочетания кремния и углерода таково, что образуются либо половинчатые (графит + цементит), либо ферритно - перлитные чугуны. При меньшем содержании углерода надо иметь большее количество кремния, чтобы получить те же структуры.
Марганец в отличие от кремния препятствует графитизации или, как говорят, способствует отбеливанию чугуна.
Сера также способствует отбеливанию чугуна, но ухудшает литейные свойства, в част-ности, снижает жидкотекучесть. Поэтому содержание серы в чугуне лимитируется: для мелкого литья верхний предел устанавливается в 0,08 %, для более крупного, когда можно допустить худшую текучесть,- до 0,1-0,12 %.
Фосфор практически не влияет на процесс графитизации. Но фосфор является полезной примесью в чугуне, так как улучшает жидкотекучесть. Это объясняется образованием относи-тельно легкоплавкой тройной эвтектики, плавящейся при 950 °С. Эта эвтектика состоит в мо-мент затвердевания из аустенита, обогащенного фосфором, цементита и фосфида железа (Fe3Р).
|
Наличие твердых участков фосфидной эвтектики повышает твердость и износоустойчивость чугуна.
Кроме этих примесей, в чугун вводят и другие элементы. Такие чугуны называются ле-гированными. Растворение в цементите таких элементов, как хром, марганец, молибден, вольфрам, ванадий препятствует графитизации. Большинство других элементов, встречающих-ся в чугунах, не растворимо в цементите и способствует графитизации. К таким элементам относятся медь и никель.
Влияние углерода.
Структура чугуна состоит из металлической основы и графита и свойства чугуна будут зависеть от двух основных показателей – свойства металлической основы и количества и характера графитных включений. Графит по сравнению со сталью обладает ничтожно низкими механическими свойствами и поэтому графитные включения можно считать в первом приближении просто за пустоты, трещины, острые надрезы внутри металла. Тогда чугун можно представить как сталь, но испещренную большим количеством пустот и трещин.
При большем содержании углерода графитизация идет легче, т.е. углерод является тоже как бы графитизирующим элементом.
Чем больше углерода (графита), тем больший объем занят пустотами, тем ниже будут свойства чугуна; чем грубее включения графита, тем больше они разобщают металлическую основу, тем хуже свойства чугуна. Наиболее низкие механические свойства получаются тогда, когда графитовые включения образуют замкнутый скелет.
При растягивающих нагрузках облегчается образование очагов разрушения по концам графитных включений. В связи с этим, такие свойства чугуна, как сопротивление разрыву, изгибу, кручению, в основном обуславливаются количеством, формой и размерами графитных включений; здесь свойства чугуна сильно отличаются от свойств стали. Но в ряде случаев именно благодаря наличию графита чугун имеет преимущество перед сталью. Наличие графита облегчает обрабатываемость резанием, делает стружку ломкой, стружка ломается, когда резец дойдет до графитного включения; чугун обладает хорошими антифрикционными свойствами благодаря смазывающему действию графита; наличие графитных выделений быстро гасит вибрацию и резонансные колебания; чугун почти нечувствителен к дефектам поверхности, играющих роль надрезов.
Белый чугун. Такое название он получил по виду излома, который имеет матово - белый цвет. В белом чугуне углерод находиться в связанном состоянии – в химическом соединении в виде цементита. Степень графитизации равна нулю, т.е. графит отсутствует. Структура его (при нормальной температуре) состоит из цементита и перлита. Наличие большого коли-чества цементита придает белому чугуну высокую твердость, хрупкость и очень низкую обрабатываемость инструментом. Он имеет ограниченное применение. Его применяют глав-ным образом для отливки деталей с последующим отжигом на ковкий чугун, например, для прокатных валков, вагонных колес.
|
2.Диаграммы состояний представляют собой наглядное изображение процессов кристал-лизации сплавов. Любая диаграмма состояний строится экспериментально. Для построения диаграмм пользуются результатами термического анализа, т.е. строят кривые охлаждения и по остановкам и перегибам на кривых охлаждения, вызванных тепловым эффектом превращений определяют температуры превращения. Каждая точка на диаграмме состояния показывает состояние сплава данной концентрации при данной температуре, т.е. сама диаграмма демонстрирует состояние сплава данной системы ( данной пары компонентов) в нашем случае железа и углерода при любом их соотношении и при любой температуре. Диаграммы состоя-ния позволяют указывать, какую микроструктуру будут иметь медленно охлажденные сплавы, а также решить вопрос о том, как добиться изменения микроструктуры путем термической обработки сплава. Поскольку технологические и эксплуатационные свойства сплавов связаны с их микроструктурой, знание диаграмм состояния чрезвычайно важно для практического металловедения.
Сплавы железа с углеродом, в которых содержится более 2,14 % углерода, называют чугунами (см. Рисунок 14. Диаграмма железо - углерод (цементит). То есть для изучения чугунов необходимо рассматривать, ту часть диаграммы, на которой представлены такие сплавы.
Разряд.
1. Серый чугун -такое название он получил по виду излома, который имеет серый цвет из-за наличия в его структуре графита, количество, форма и размеры которого изменяются в широких пределах. В микроструктуре чугуна следует различать металлическую основу и графитные включения.
В обычном сером чугуне графит образуется в виде прожилок, лепестков - в форме пласти-нок; такой графит называется пластинчатым.
По строению металлической основы чугун разделяется на:
Серый перлитный чугун. Структура его состоит из перлита с включениями графита (гра-фит в виде прожилок). Так как перлит содержит 0,8 % С, следовательно, это количество угле-рода в сером чугуне находиться в связанном состоянии (т.е. в Fe3C), остальное количество находиться в свободном виде, т.е. форме графита.
Серый ферритно - перлитный чугун. Структура этого чугуна (феррит + перлит) и включения графита. В этом чугуне количество связанного углерода меньше 0,8 % С.
Серый ферритный чугун. В этом чугуне металлической основой является феррит и весь углерод, имеющийся в сплаве, присутствует в форме графита.
Из рассмотренных структур указанных трех видов чугуна можно заключить, что их металлическая основа похожа на структуру эвтектоидной стали, доэвтектоидной стали и железа. Следовательно, чугуны отличаются от стали тем, что в чугунах имеются графитовые включения, что предопределяет и специфические свойства чугунов.
Наиболее широкое применение получили доэвтектические чугуны, содержащие 2,4-3,8 % С.
2. Влияние углерода. Чем выше в чугуне углерода, тем больше образуется графита и тем ниже его механические свойства. Поэтому количество углерода обычно не превышает 3,8%. В тоже время для обеспечения высоких литейных свойств (хорошей жидкотекучести) углерода должно быть не меньше 2,4%.
Кремний, содержание которого в серых чугунах чаще всего находиться 1,2 - 3,5 %, оказывает большое влияние на строение, а, следовательно, и свойства чугунов.
Кремний способствует процессу графитизации.
Изменяя, с одной стороны содержание в чугуне углерода и кремния и, с другой,- скорость охлаждения, можно получить различную структуру металлической основы чугуна.
При данном содержании углерода, чем больше в чугуне количества кремния, тем полнее протекает процесс графитизации. Чем больше в чугуне углерода, тем меньше требуется кремния для получения заданной структуры.
Содержание графита в чугуне зависит не только от его химического состава, но и от скорости охлаждения отливки. Чем больше кремния и чем медленнее охлаждаются отливки, тем больше выделяется графита.
Примеси серы и марганца замедляют выделение графита (графитизацию). Но сера ухудшает литейные свойства чугуна - жидкотекучесть.
Фосфор практически не влияет на процесс графитизации. Но фосфор является полезной примесью в чугуне, так как улучшает жидкотекучесть. Это объясняется образованием относи-тельно легкоплавкой тройной эвтектики, плавящейся при 950°С. Эта эвтектика состоит в мо-мент затвердевания из аустенита, обогащенного фосфором, цементита и фосфида железа (Fe3Р).
Наличие твердых участков фосфидной эвтектики повышает твердость и износоустойчивость чугуна, но при этом увеличивается хрупкость отливок.
Кроме этих постоянных примесей в чугун часто вводят и другие элементы. Такие чугуны называют легированными. Если эти примеси содержались в рудах, из которых в доменной печи выплавлялся чугун, то такие чугуны называются природно - легированными. Наиболее часто чугун легируют хромом, никелем, медью. Хром препятствует графитизации чугуна, а медь и никель способствуют.
Улучшение механических свойств серого чугуна достигается главным образом путем улучшения (измельчения) графитовых включений, а не путем изменения структуры металлической основы. Наилучшим по своим свойствам (прочности, твердости, пластичности) является серый чугун марки СЧ 23-52 (а также СЧ 28-48 и СЧ 24-44). Такой чугун называется высококачественным, он имеет структуру мелко пластинчатого перлита (сорбит) с мелкими пластинчатыми включениями графита (мелко завихренными графитными включениями). Из такого чугуна изготовляются такие ответственные детали, как поршневые кольца двигателей внутреннего сгорания, отливки станин, поршни цилиндров и др.
Термическая обработка серых чугунов. В практике в основном серые чугуны подвергаются термической обработке: отжигу, нормализации, закалке, отпуску и химико-термической обработке.
Отжиг низкотемпературный применяют для полного снятия остаточных напряжений, по режиму одинаковому для всех видов чугунов: загрузка изделий при температуре не выше 250-300 °С, подогрев до 550-600 °С, выдержка 2-8 час; охлаждение со скоростью не более 20-30 °С в час до 200-150 °С.
Отжиг (графитизирующий) отливок из серого чугуна применяют при устранении отбеленной «корочки», получаемой на поверхности при заливке чугуна в металлические формы. Режим отжига, проводимого в камерных печах с выдвижным подом: температура отжига 900-950 С, время нагрева 2-5час, охлаждение отливок до 200-250 °С вместе с печью, затем на спокойном воздухе. В результате отжига идет распад белого чугуна с переходом в серый: Fe3C→ Fe + С (графит).
Применяется для уменьшения твердости и улучшения обрабатываемости отбеленного чугуна.
Нормализация. Применяется для повышения прочности и износостойкости серого чугуна. Режим нормализации: изделия нагревают до 850-900 °С, после полного прогрева охлаждение на воздухе. Детали сложной формы после нормализации отпускаютпри температуре 600-650 °С.
Закалка с отпуском предназначается для повышения твердости, прочности, износостойкости. Закалка может быть объемной, когда нагревается и охлаждается вся деталь, и поверхностной, когда деталь нагревается ТВЧ (токами высокой частоты) или газовым пламенем. Нагрев под закалку осуществляется при температуре 820-860 °С; охлаждение - в воде или масле. Температура отпуска в зависимости от требуемой твердости изделия принимается от 200-500 °С. Наилучшее сочетание прочности и износостойкости достигается при температуре отпуска 350-450 °С. Твердость при этом 321- 418 НВ.
Изотермическая закалка значительно уменьшает трещины и коробление изделий, производится при 830-900 °С в ванну, имеющую температуру 200-400 °С.
3. Серый чугун маркируют по ГОСТ 1412-85.
Улучшение механических свойств серого чугуна достигается главным образом путем улуч-шения (измельчения) графитовых включений, а не путем изменения структуры металлической основы. Металлическая основа в сером чугуне обеспечивает наибольшую прочность и изно-состойкость, если она имеет перлитную структуру. Присутствие в структуре феррита, не увеличивая пластичности и вязкости чугуна, снижает его прочность и износостойкость. Наименьшей прочностью обладает ферритный серый чугун. Эти чугуны (СЧ-00,СЧ12-28, СЧ15-32,СЧ18-36) применяют для малоответственных деталей сельскохозяйственных машин, станков, автомобилей, арматуры и др.
Серый чугун применяют для отливки станин металлорежущих станков, блоков цилиндров, картеров коробок скоростей, деталей работающих на износ в условиях больших давлений (компрессорное, арматурное и турбинное литье и др.) деталей.
Разряд.
1.Ковкиий чугун с хлопьевидной формой графита, который получается из белого путем специального графитизирующего отжига, томления.Образованный после отжига графит хлопьевидной формы по сравнению с пластинчатым, меньше снижает прочность и пластичность металлической основы структуры чугуна. Металлическая основа ковкого чугуна: феррит - ферритный ковкий чугун, реже перлит - перлитный ковкий чугун. Наибольшей пластичностью обладает ферритный ковкий чугун, который и применяют в машиностроении.
Состав ковкого чугуна ограничивается сравнительно узкими пределами по содержанию элементов: 2,2 -2,8 % С; 0,6 -1,4 % Si; Мn≤ 0,4 %; S ≤ 0,1 %; Р ≤ 0,2 %.
Отжиг на ковкий чугун проводят в две стадии. Первоначально отливки, чаще упакованные в ящики с песком выдерживают при 950-970 °С. В этом период протекает I стадия графитизации, т.е. распад цементита, входящего в состав ледебурита (А + Fe3 С), и установление стабильного равновесия аустенита + графит. В результате распада цементита диффузионным путем образуется хлопьевидный графит (углерод отжига).
Затем отливки охлаждают до температур, соответствующих интервалу эвтектоидного превращения. При охлаждении происходит выделение из аустенита вторичного цементита, его распада и в итоге рост графитных включений. При достижении эвтектоидного интервала температур охлаждение резко замедляют или дают длительную выдержку при температуре не-сколько ниже этого интервала. В этот период протекает II стадия графитизации: распад аустенита с образованием феррито - графитной структуры или распад цементита, входящего в состав структуры перлит, с образованием феррита и графита (в процессе выдержки ниже эвтектоидной температуры). После окончания второй стадии графитизации структура чугуна состоит из феррита и хлопьевидного графита.
Излом ферритного чугуна бархатисто-черный вследствие большого количества графита.
Если не проводить выдержку, ниже эвтектоидной температуры или, если в этом интервале температур скорость охлаждения повышенная, то образуется перлитный ковкий чугун (П+ Г), имеющий светлый (сталистый) излом. Время отжига достигает 60- 80 часов.
Для ускорения отжига применяют различные методы: чугун модифицируют алюминием (бором, висмутом и др. элементами), повышают температуру нагрева чугуна перед разливкой, применяют перед отжигом старение чаще в процессе нагрева до температуры отжига при 350-400 °С, повышают температуры I стадии графитизации (но не выше 1080 °С) или же выполняют отжиг в защитной атмосфере. В этом случае длительность отжига составляет 24-60 часов.
Наибольшей пластичностью обладает ферритный ковкий чугун, который применяют в машиностроении. Ферритный ковкий чугун КЧ37-12 и КЧ35-10 используют для деталей, работающих при ударных и вибрационных нагрузках. Максимальная твердость ферритного ковкого чугуна достигает НВ163.
Перлитный ковкий чугун КЧ50-5, КЧ 56-4, КЧ 60-3 и КЧ63-2 обладает более высокой прочностью, умеренной пластичностью и хорошими антифрикционными свойствами. Твердость перлитного чугуна составляет 269 НВ из перлитного ковкого чугуна изготавливают вилки карданных валов, звенья и ролики цепей конвейера, втулки, муфты, тормозные колодки и т.д.
|
|
Эмиссия газов от очистных сооружений канализации: В последние годы внимание мирового сообщества сосредоточено на экологических проблемах...
Кормораздатчик мобильный электрифицированный: схема и процесс работы устройства...
Архитектура электронного правительства: Единая архитектура – это методологический подход при создании системы управления государства, который строится...
Историки об Елизавете Петровне: Елизавета попала между двумя встречными культурными течениями, воспитывалась среди новых европейских веяний и преданий...
© cyberpedia.su 2017-2024 - Не является автором материалов. Исключительное право сохранено за автором текста.
Если вы не хотите, чтобы данный материал был у нас на сайте, перейдите по ссылке: Нарушение авторских прав. Мы поможем в написании вашей работы!