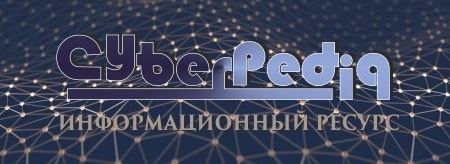
Своеобразие русской архитектуры: Основной материал – дерево – быстрота постройки, но недолговечность и необходимость деления...
Состав сооружений: решетки и песколовки: Решетки – это первое устройство в схеме очистных сооружений. Они представляют...
Топ:
Устройство и оснащение процедурного кабинета: Решающая роль в обеспечении правильного лечения пациентов отводится процедурной медсестре...
Особенности труда и отдыха в условиях низких температур: К работам при низких температурах на открытом воздухе и в не отапливаемых помещениях допускаются лица не моложе 18 лет, прошедшие...
Интересное:
Финансовый рынок и его значение в управлении денежными потоками на современном этапе: любому предприятию для расширения производства и увеличения прибыли нужны...
Наиболее распространенные виды рака: Раковая опухоль — это самостоятельное новообразование, которое может возникнуть и от повышенного давления...
Подходы к решению темы фильма: Существует три основных типа исторического фильма, имеющих между собой много общего...
Дисциплины:
![]() |
![]() |
5.00
из
|
Заказать работу |
Определяющим этапом проектирования технологии контроля является выбор средств контроля. Рассмотрим решение этой задачи на примере выбора стандартизованных средств контроля размеров гладких элементов деталей.
3.1. Теоретические аспекты выбора универсальных средств контроля размеров
Контроль размеров заключается в проверке соответствия размеров элементов изготовленных деталей полям допусков, установленным конструктором при проектировании изделия. Наибольшее применение на практике получили следующие два способа:
- контроль с помощью предельных калибров (гладких калибров пробок и скоб, а также калибров для глубин и высот уступов) [17-19];
- контроль с помощью стандартизованных универсальных средств измерений (измерительных линеек, штангенциркулей, микрометров и пр.) [17, 18, 25, 26].
При контроле предельными калибрами устанавливается факт выхода размера за нижнюю или верхнюю границы поля допуска или нахождения размера между этими границами. Для этого в комплект предельных калибров для отверстий и валов входит проходной калибр, проверяющий предельный размер, соответствующий максимуму материала контролируемой детали, и непроходной калибр, проверяющий предельный размер, соответствующий минимуму её материала. Размер признаётся годным, если проходная сторона калибра проходит относительно контролируемого элемента детали, а непроходная сторона не проходит относительно него. Для реализации этого условия предельные калибры должны быть правильно спроектированы. При этом наиболее актуальными являются задачи выбора номинальных значений размеров проходной и непроходной сторон, расчета исполнительных размеров калибров и распределения запаса на износ их проходных сторон. Решение этих задач подробно рассматривается в работах [17, 18, 23].
Контроль размеров универсальными средствами проводится в два этапа:
- на первом этапе осуществляется измерение элемента детали с целью установить числовое значение действительного размера D(d);
- на втором этапе в соответствии с условием:
D (d
) £ D(d) £ D
(d
) (3.1.)
осуществляется численное сравнение действительного размера с предельными - наименьшим D (d
) и наибольшим D
(d
) с целью сделать вывод о годности или негодности размера.
Согласно положений ГОСТ25346-89 [11] действительный размер - это размер, установленный измерением с допустимой погрешностью. В тоже время известно, что применение любого средства измерений сопровождается появлением погрешности измерения. Поэтому при использовании для контроля универсальных стандартизованных средств измерений наиболее актуальной является задача их правильного выбора.
При выборе универсальных средств измерений проектировщиком технологического процесса контроля должен учитываться ряд факторов, характеризующих как объект контроля, так и показатели самого процесса контроля. К этим факторам относятся следующие:
- вид объекта контроля (отдельная деталь или сборочная единица);
- номинальное значение размера и его допуск;
- погрешность средства измерений, которое планируется использовать при контроле;
- конструктивные особенности детали или изделия;
- возможность обеспечить совпадение конструкторской и метрологической баз;
- способность детали деформироваться при измерении;
- условия рабочего места контроля (температурный режим, влажность, вибрации и т.д.);
- производительность операции контроля;
- наличие средства измерения на данном предприятии или возможность его приобретения;
- стоимость средства измерения;
- необходимая квалификация контролёра;
- целесообразность проектирования специального средства измерения.
Производственная практика показывает, что определяющее значение при выборе универсального средства измерений играют первые пять факторов, а все остальные факторы имеют корректирующее значение.
В рассмотренных ниже примерах (см. гл. 4) будет продемонстрировано влияние многих из перечисленных факторов на результаты принятия решений в задачах, связанных с разработкой технологии контроля размеров различных деталей.
3.2. Погрешности измерения линейных размеров и условия проведения измерений.
Суммарное значение абсолютной погрешности прямых измерений линейных размеров может быть представлено в виде [18]:
(3.2.),
где - абсолютная погрешность средства измерений;
- погрешность метода измерений;
- температурная погрешность;
- погрешность от измерительного усилия;
- субъективная погрешность, зависящая от квалификации контролера;
- прочие составляющие погрешности измерения, не охваченные составляющими от
до
.
Влияние погрешностей на результаты измерений зависят от условий их проведения. ГОСТ 8.050-73 [6] устанавливает следующие нормальные условия проведения измерений линейных размеров в диапазоне от 1 мм до 500 мм:
- температура окружающей среды + 20°C;
- атмосферное давление 101324,72 Па (760 мм ртутного столба);
- относительная влажность окружающего воздуха 58 % (нормальное парциальное давление водяных паров 1333,22 Па);
- ускорение свободного падения 9,8 м×с ;
-направление линии измерения линейных размеров у наружных поверхностей - вертикальное, в остальных случаях - горизонтальное;
- относительная скорость движения внешней среды равна нулю;
- значения внешних сил, кроме силы тяжести, атмосферного давления, действия магнитного поля Земли и сил сцепления элементов измерительной системы равны нулю.
С практической точки зрения различают два вида нормальных условий измерений:
- унифицированные нормальные условия - условия, при которых дополнительные погрешности практически равны нулю независимо от вида средства измерений и объекта измерений;
- расширенные нормальные условия - условия, устанавливаемые в стандартизованных методиках выполнения измерений и другой нормативно-технической документации так, что при выполнении измерений не требуется вводить поправки вследствие практического исключения дополнительных погрешностей. Например, при измерении деталей с номинальными размерами от 18 мм до 50 мм с 5-го по 9-ый квалитеты допускаемые отклонения температуры составляют ± 1,5° С; с 10-го по 11-ый квалитеты ± 3° С; с 12-го по 17-ый квалитеты ± 4° С.
3.3. Методика выбора средств измерений для контроля линейных размеров
Выбор универсальных средств измерений основан на одновременном выполнении следующих двух условий [18]:
- должно обеспечиваться надёжное сопряжение средства измерений с элементом проверяемой детали (конструктивный критерий);
- должно выполняться условие (3.3) (метрологический критерий), где
- суммарное значение абсолютной погрешности прямого измерения линейной величины выбранным средством измерений (см. выше);
- допускаемая погрешность измерения размера по ГОСТ 8.051-81 [7], зависящая от допуска контролируемого размера.
При решении практических задач за величину обычно принимают предел допускаемой погрешности измерения (ПДПИ)[17,18]. Это величина наибольшей погрешности средства измерений, при которой оно признаётся годным и допускается к применению. Величины ПДПИ приводятся в паспортных данных средств измерений, каталогах или справочниках [18,25]. Например, для линейки измерительной металлической с ценой деления 1 мм, ГОСТ 427-89, ПДПИ = 0,5 мм; штангенциркуля ШЦ-1, ГОСТ 166-89, ПДПИ = 0,2 мм; штангенциркуля ШЦ-11, ГОСТ 166-89, ПДПИ = 0,1 мм; штангенглубиномера ШГ-160, ГОСТ 162-90, ПДПИ = 0,1 мм; микрометров МК25-2, МК50-2, МК75-2, МК100-2, ГОСТ 6507-90, ПДПИ = 0,008 мм [25].
Таким образом, «метрологический» критерий выбора стандартизованного универсального средства измерений может быть представлен в виде: ПДПИ £ (3.4).
По результатам сопоставления из имеющейся номенклатуры средств измерений, удовлетворяющих «конструктивному» критерию, выбирают те, предел допускаемой погрешности измерения которых удовлетворяет и второму критерию, а из них в технологический процесс контроля закладывается наиболее дешевое [18,19].
3.4. Оценка и учет влияния погрешности измерения на результаты контроля размеров
Погрешности измерения оказывают влияние на результаты приемочного контроля, которые ГОСТ 8.051-81 [7] оценивает следующими параметрами:
m - число деталей в процентах от общего числа измеренных, имеющих размеры, выходящие за предельные и принятые в числе годных (неправильно принятые - «брак в годных»);
n - число деталей в процентах от общего числа измеренных, имеющих размеры, не превышающие предельные и забракованные (неправильно забракованные - «годные в браке»);
c - вероятностная величина выхода размера за предельные у неправильно принятых деталей.
Величины параметров m, n, c зависят от точности измерения, которая в ГОСТ 8.051-81 [7] характеризуется величиной
, определяемой отношением среднего квадратического отклонения погрешности измерения
к допуску IT контролируемого размера и выраженной в процентах, то есть
=
× 100% (3.5).
Кроме того, параметры m, n, c зависят от заданной точности изготовления рассматриваемого элемента детали, характеризуемой параметрами вероятностного распределения действительных значений проверяемого размера относительно его поля допуска.
Значения параметров m, n, c, найденные при самых неблагоприятных характеристиках распределения погрешностей, табулированы в ГОСТ 8.051-81 [7] в зависимости от величины
. При этом рекомендуется принимать
= 16 % для размеров с допусками по квалитетам до 7-го включительно;
= 12 % для размеров с допусками по 8-му и 9-му квалитетам и
= 10 % для размеров с допусками по 10-му и более грубым квалитетам.
Влияние погрешности измерения на результаты контроля должны учитываться при установлении приёмочных границ, то есть тех предельных значений размеров в формуле (3.1.), с которыми сравниваются действительные размеры контролируемых деталей и по которым оценивается их годность при приёмке. Здесь возможны два способа.
Первый заключается в том, что приёмочные границы устанавливаются равными предельным размерам заданного конструктором поля допуска (этот вариант наиболее предпочтителен).
При втором варианте приёмочные границы устанавливаются смещенными относительно границ заданного поля допуска во внутрь этого поля. Таким образом устанавливается уменьшенный по сравнению с конструкторским производственный допуск. При введении производственного допуска смещение каждой приёмочной границы не должно превышать половины, допускаемой ГОСТ 8.051-81 [7] погрешности измерения.
Первый способ является основным. Второй применяется тогда, когда величины параметров m, n, c оказываются неприемлемыми, либо с точки зрения конструктора, отвечающего за функциональные свойства детали, либо по экономическим соображениям, связанным с потерями производителя продукции.
ПРИМЕРЫ ПРОЕКТИРОВАНИЯ ТЕХНОЛОГИЧЕСКИХ ОПЕРАЦИЙ КОНТРОЛЯ
Общие условия выбора системы дренажа: Система дренажа выбирается в зависимости от характера защищаемого...
Типы оградительных сооружений в морском порту: По расположению оградительных сооружений в плане различают волноломы, обе оконечности...
История создания датчика движения: Первый прибор для обнаружения движения был изобретен немецким физиком Генрихом Герцем...
Двойное оплодотворение у цветковых растений: Оплодотворение - это процесс слияния мужской и женской половых клеток с образованием зиготы...
© cyberpedia.su 2017-2024 - Не является автором материалов. Исключительное право сохранено за автором текста.
Если вы не хотите, чтобы данный материал был у нас на сайте, перейдите по ссылке: Нарушение авторских прав. Мы поможем в написании вашей работы!