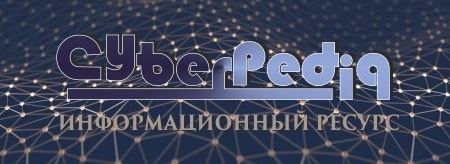
Архитектура электронного правительства: Единая архитектура – это методологический подход при создании системы управления государства, который строится...
Семя – орган полового размножения и расселения растений: наружи у семян имеется плотный покров – кожура...
Топ:
Отражение на счетах бухгалтерского учета процесса приобретения: Процесс заготовления представляет систему экономических событий, включающих приобретение организацией у поставщиков сырья...
Организация стока поверхностных вод: Наибольшее количество влаги на земном шаре испаряется с поверхности морей и океанов...
Устройство и оснащение процедурного кабинета: Решающая роль в обеспечении правильного лечения пациентов отводится процедурной медсестре...
Интересное:
Финансовый рынок и его значение в управлении денежными потоками на современном этапе: любому предприятию для расширения производства и увеличения прибыли нужны...
Влияние предпринимательской среды на эффективное функционирование предприятия: Предпринимательская среда – это совокупность внешних и внутренних факторов, оказывающих влияние на функционирование фирмы...
Инженерная защита территорий, зданий и сооружений от опасных геологических процессов: Изучение оползневых явлений, оценка устойчивости склонов и проектирование противооползневых сооружений — актуальнейшие задачи, стоящие перед отечественными...
Дисциплины:
![]() |
![]() |
5.00
из
|
Заказать работу |
|
|
В цилиндрических червячных передачах червяки разделяют на следующие основные виды (ГОСТ 18498-73): архимедовы (ZA), имеющие прямолинейный профиль в осевом сечении и архимедову спираль в торцовом; конва- лютные (ZN), имеющие прямой профиль в нормальном к витку сечению и удлиненную эвольвенту в торцовом сечении; эвольвентные (ZI), имеющие криволинейный профиль в нормальном сечении, эвольвентный в торцовом и прямолинейный в сечении плоскостью, касательной к основному цилиндру. В единичном производстве червяки с формами боковых поверхностей ZA, ZN, ZI как предварительно, так и окончательно могут быть изготовлены на токарном станке. Архимедовы червяки (ZA) нарезают резцами с прямолинейными режущими кромками, установленными в осевом сечении червяка (рис. 216, а). Обе стороны витка одновременно обрабатывают при черновом нарезании и раздельно каждую сторону при чистовом. По этой же технологии обрабатывают конвалютные червяки, с той разницей, что резцы с прямолинейными кромками для червяка ZN1 устанавливают в нормальном сечении витка (рис. 216, б), а для червяка ZN2— в нормальном сечении впадины (рис. 216, в). При обработке эвольвентных червяков ZI важное значение имеет установка токарных резцов. Чистовое нарезание эвольвентного червяка выполняют двумя резцами: один резец — для обработки правой, другой — для обработки левой стороны витка. Резцы, имеющие прямолинейные режущие кромки, устанавливают один выше, другой ниже оси червяка, в плоскостях, касательных к основному цилиндру червяка (рис. 216, г).
В серийном производстве используют более эффективные методы. Обработка ведется на резьбофрезерных и специально-фрезерных станках дисковыми или пальцевыми фрезами, профиль которых определяют для каждого конкретного типа червяка. Возможно также точение витков червяков (типа ZA и Z1) на зу- бофрезерных станках долбяком. Многоза- ходные эвольвентные червяки нарезают методом обкатки на зубофрезерных станках червячными фрезами. В крупносерийном и массовом производстве широко применяют вихревой метод обработки червяков в специальном приспособлении, установленном на резьбофре- зерном станке. Этот метод обладает большой производительностью. Подобно изготовлению резьбы, червяки небольших размеров, с малым углом подъема витка и небольшой глубиной профиля накатывают в холодном состоянии без снятия стружки.
|
У термически обработанных архимедовых, конвалютных и эвольвентных червяков окончательную обработку профиля витка осуществляют на специальных резьбошлифо- вальных станках или станках для шлифования червяков. Для повышения производительности шлифование осуществляют дисковыми шлифовальными кругами большого диаметра на скорости резания 40 — 45 м/с. Шлифовальный круг правят соответственно профилю червяка и наклоняют его (рис. 216, д) на делительный угол подъема витка. Оба профиля шлифовального круга правят алмазами по шаблону, ко-
![]() |
торые изготовляют по заданным координатам на профильно-шлифовальных станках. Профиль шлифовального круга соответствует шлифуемому профилю червяка в осевом сечении. При изготовлении червяков высокой точности необходимо использовать контрольно- измерительные приборы соответствующей точности. Окончательное шлифование осуществляют в термоконстантных помещениях. Соседние станки устанавливают на достаточном удалении от шлифовального, чтобы уменьшить влияние вибрации, нагрева и т. д. На современных станках, имеющих короткую кинематическую цепь, установлены механизмы устранения зазоров во время изменения направления вращения, что позволяет проводить шлифование в обоих направлениях: при движении в одном направлении шлифуют одну сторону профиля, а при обратном — противоположную. Припуски на обработку профиля червяков приведены в табл. 40.
|
Контроль червячных передач можно разделить на три этапа: раздельный контроль колеса и червяка после их окончательной обработки, контроль комплекта (пары) колеса и червяка перед сборкой, контроль червячной передачи в собранном агрегате. У червячного колеса контролируют: погрешность шага и накопленную погрешность шага, толщину зуба, форму и расположение пятна контакта в паре с червяком, кинематическую точность на приборе в однопрофильном зацеплении с сопряженным червяком или со специальным эталоном для передач высокой точности и комплексную погрешность в двухпрофиль- ном зацеплении для передач невысокой точности. Погрешность окружного шага червячного колеса чаще определяют специальным прибором непосредственно на зуборезном станке в процессе нарезания зубьев. Во время медленного вращения стола станка с обрабатываемым червячным колесом два измерительных штифта прибора последовательно вводятся в соседние впадины зуба на полный оборот колеса. Результаты измерения автоматически вычисляются и записываются: на
40. Припуски (мм) на толщину зуба профиля витков червяка
|
одном графике — погрешность шага от зуба к зубу, на другом — накопленная погрешность. Например, показатели точности червячного колеса (de = 250 мм: m = 3 мм) для зуборезного станка: погрешность шага 2 мкм, накопленная погрешность 10 мкм. Контроль погрешности шага и накопленной погрешности выполняют также на специальных приборах вне станка. У червяка контролируют: форму профиля, погрешность угла подъема витка, шаг между витками, толщину зуба, радиальное биение. Основные параметры контролируют на приборе для контроля червячных фрез. Ряд параметров можно контролировать на эволь- вентомере, шагомере и т. д. Перед сборкой у червячного колеса и сопряженного червяка в паре контролируют форму и расположение пятна контакта на зубьях колеса и кинематическую точность. Первый параметр определяет качество зацепления, второй — точность изготовления червячной передачи. Пятно контакта и кинематическую точность червячной передачи в однопрофильном зацеплении проверяют на специальном контрольном приборе с электронным и записывающим устройствами при номинальном межосевом расстоянии. Перед контролем пятна контакта зубья колеса покрывают тонким слоем краски (суриком с маслом), затем при легком торможении передачу вращают в обоих направлениях. Пятно контакта, характеризующее правильность зацепления, должно располагаться в средней части ширины зубчатого венца без выхода на головку, ножку и концы зубьев (см. рис. 215, г). Для высоконагруженных передач длина пятна контакта равна примерно половине ширины зубчатого венца колеса. У скоростных передач больших ограничений в размере пятна контакта не делают, чтобы не вызвать повышения уровня звукового давления вследствие уменьшения коэффициента перекрытия. При изготовлении точных червячных передач особое значение приобретает контроль кинематической точности в однопрофильном зацеплении. Этот метод позволяет сравнивать точность и равномерность вращательного движения контролируемой передачи с точностью и равномерностью почти идеальной исходной передачи. Измерение осуществляют с помощью двух электронных устройств: одно устанавливают на шпинделе червячного колеса, другое — на шпинделе червяка. Сравнение проводят с предварительно установленным передаточным числом. Отклонения регистрируются на графике, Цо которому можно определить погрешности отдельных параметров зубчатого зацепления. Контроль кинематической точности червячной передачи в сочетании с проверкой пятна контакта позволяют выявить погрешности зубчатого зацепления и иметь представление о характеристике червячной передачи в рабочих условиях. На приборе можно контролировать боковой зазор в червячной передаче и погрешности межосевого угла. Сборка является наиболее ответственной операцией, которая в значительной степени определяет работоспособность червячной передачи в собранном агрегате. При сборке высоконагруженных червячных передач главное внимание уделяют форме и расположению пятна контакта. Контакт проверяют после определенного периода прикатки; он должен быть таким же, как при обкатке червячной передачи на контрольном приборе перед сборкой. На этом этапе пятно контакта зависит не только от качества изготовления передачи, но и от правильности сборки передачи в корпусе и точности изготовления деталей агрегата. При сборке прежде всего нужно следить за соблюдением расстояния между осями, так как изменение межосевого расстояния существенно влияет на расположение пятна контакта. При выходе пятна контакта на кромки зубьев уменьшаются основные преимущества червячной передачи в отношении предельно допустимой нагрузки, плавности хода и равномерности вращения. Если пятно контакта расположено на одном конце обеих сторон зуба, — колесо неправильно расположено относительно оси червяка. Если пятно контакта расположено на противоположных концах зуба (см. рис. 215, д), причиной может быть неправильное межосевое расстояние или неправильный угол между осями колеса и червяка. Прецизионные станки для нарезания червячных колес, шлифования червяков и контрольно-измерительные приборы устанавливают в специальных термоконстантных помещениях с постоянной температурой воздуха 20°С (± 0,5 °С); влажность воздуха 54-58%.
|
|
ПРЕЦИЗИОННОЕ ТОЧЕНИЕ
Прецизионное точение (тонкое обтачивание и растачивание, алмазная обработка) характеризуется высокими скоростями резания (100—1000 м/мин и более), малыми подачами (0,01—0,15 мм/об) и глубинами резания (0,05 — 0,3 мм) при высокой виброустойчивости технологической системы. Детали из стали, в процессе обработки которых имеют место ударные нагрузки (при наличии пазов, пересекающих отверстий и др.), а также детали из стали и высокопрочного чугуна высокой твердости обрабатывают при более низких скоростях резания (до 50 м/мин). В некоторых случаях при обработке деталей из стали и высокопрочного чугуна повышенной твердости, при наличии оборудования высокой жесткости, мощности и соответствующей частоты вращения шпинделя целесообразно применять резцы, армированные СТМ; скорости резания могут быть увеличены до 150 м/мин и более.
Прецизионное точение обеспечивает получение поверхностей правильной геометрической формы, с точным пространственным расположением осей и параметр шероховатости поверхности Ra — 0,63 -г- 0,063 мкм; вместе с тем этот метод высокопроизводителен.
При растачивании деталей из медных сплавов резцами, армированными алмазами или композиционными материалами, с использованием шпиндельных головок с высокоточными подшипниками можно получить параметр шероховатости поверхности Ra=0,032 0,020 мкм, при растачивании деталей из алюминиевых и бронзовых сплавов Ra = 0,063 -т- 0,04 мкм. При использовании стандартных шпиндельных головок и тех же условиях можно обеспечить параметр шероховатости поверхности Ra = = 0,50^0,16 мкм.
|
Вследствие малых сечений стружки силы резания и нагрев детали во время обработки незначительны. Это исключает образование большого деформированного поверхностного слоя и позволяет ограничиваться малыми силами при закреплении детали для обработки. Точность получаемых размеров 8 —9-го квалитета, а при определенных условиях 5 —7-го квалитета. На отделочно-расточных станках обычно выдерживают допуск 5 — 15 мкм на диаметре 100 мм; отклонение от круглости и конусообразность — в пределах 3 — 10 мкм.
Более высокую точность получают при обработке деталей из цветных сплавов; при обработке деталей из стали и чугуна точность ниже, так как в большей степени сказывается влияние износа резца в процессе работы. Точность обработки при растачивании зависит от отношения длины к диаметру обрабатываемой поверхности. При обработке на отделочно-расточных станках отверстия, у которых отношение длины к диаметру меньше 2, принято считать короткими, равное 2—4 — средними, больше 4 — длинными.
Прецизионное точение часто применяют перед хонингованием, суперфинишированием, притиркой. У точных цилиндрических колес после токарной обработки на вертикальных многошпиндельных полуавтоматах одновременно растачивают отверстия и подрезают торцы с допуском 0,015-0,02 мм на диаметр и 0,05 мм на линейные размеры, хонингуют отверстия и суперфинишируют торцы.
Оборудование. При прецизионной обработке частота вращения шпинделя 1500 — 12000 мин-1, подача 0,01—0,2 мм/об. Для высокой точности обработки допускается радиальное биение подшипников рабочих шпинделей станка до 3 мкм; должна отсутствовать вибрация шпинделей и приспособлений с обрабатываемыми деталями. Необходимо обеспечить быстрый и удобный отвод стружки, удобное обслуживание и высокую степень автоматизации управления станком — автоматический останов, переключение и торможение шпинделей, ускоренные вспомогательные ходы. Оборудование должно иметь устройства: для тонкого регулирования положения и установки резцов, автоматического измерения детали и автоматической подналадки по мере износа инструмента, автоматический загрузки и выгрузки деталей.
При прецизионной обработке одним из методов размерной подналадки инструмента является метод регулирования малыми импульсами. Измерительное устройство, контролируя размеры каждой обработанной детали, по мере возникновения отклонений подает команду на их ' компенсацию. Для гарантированного получения заданного размера контакты измерительного устройства налаживают на меньшее предельное значение.
На вертикальных станках и станках с неподвижным столом автоматизация загрузки и выгрузки деталей удачно решается традиционными средствами. Значительные трудности возникают при автоматизации отделочно- расточных станков с подвижным столом, Когда требуется конкретное решение для обработки определенной детали.
Для устранения вибрации при большой частоте вращения шпинделя части станка должны быть отбалансированы, электродвигатели и гидронасосы расположены отдельно от станины или установлены на особых эластичных прокладках или виброопорах, шпиндель должен быть разгружен от натяжения ремней.
С целью повышения производительности обработки почти все отдел очно-расточные станки выполняют с большим числом шпинделей. В этом случае каждый вновь вступающий в работу шпиндель (отделочно-расточная головка) снижает точность обработки.
Для прецизионного точения используют станки: отдел очно-расточные горизонтальные одно- и многошпиндельные с двусторонним и односторонним расположением шпинделей (головок), с закреплением детали на подвижном столе или в шпинделях; специального назначения для обработки определенных деталей (наклонные, трех- и четырехсторонние и др.); общего назначения (быстроходные токарные, расточные и многооперационные с ЧПУ), обладающие необходимыми кинематическими параметрами и высокой точностью. Для прецизионного точения можно модернизировать обычные токарные и внутришлифовальные станки.
Инструмент. При презиционном точении применяют расточные, проходные и подрезные резцы с режущими элементами из алмазов, композиционных материалов, твердых сплавов, сверхтвердых материалов (гексанита, эльбора), минералокерамики и керметов (табл.
41).
Резцы с режущими элементами из алмазов и СТМ имеют высокую твердость; после доводки таких инструментов можно снимать стружку толщиной 0,02 мм на высоких скоростях резания. Этот инструмент обеспечивает малые параметры шероховатости при обработке деталей из баббитов, порошковых материалов, графитов, пластмасс, материалов, оказывающих абразивное действие на инструмент. Однако из-за большой хрупкости алмазов и СТМ, а также недостаточной жесткости и виброустойчивости технологической системы на многих заводах не удается широко использовать инструмент, армированный этими материалами, для обработки деталей из стали и чугуна.
Обработка алмазными инструментами деталей из материалов с твердыми включениями окиси алюминия исключается.
Наиболее удобны для точной установки и регулирования резцы с цилиндрическим стержнем и резцы-вставки с механическим креплением пластины режущего материала (твердого сплава), либо специально изготовленные пластины с напайным или заделанным алмазом, СТМ и др. В зависимости от условий обработки резцы и резцы-вставки закрепляют в борштангах или резцовых головках на шпинделе станка, в резцедержателе на столе станка, в промежуточных державках, закрепленных в резцедержателе токарного станка; в последнем случае можно применять токарные резцы обычной конструкции. На точность обработки влияет способ закрепления
42. Рекомендуемые диаметры борштанг и резцов в зависимости от диаметра растачиваемого отверстия
Диаметр, | мм | Диаметр, мм | |||
растачиваемого отверстия | борштанги | резца | расста- чивае- мого отверстия | борштанги | резца |
10 15 20 30 35 40 45 50 55 60 65 70 | 9 13 15-16 22-25 25-27 30 32 36 40-42 42-43 45 50 | 4-5 6 8 10 10 12-13 12-13 12-13 14-15 14-15 14- 15 15- 17 | 75 80 85 90 95 100 105 110 120 140 150 | 54 58-60 60 65 67-68 70 72-75 80 85-90 95-100 100-105 | 15-17 18-19 18-19 18-19 20-22 20-22 25-30 25-30 30-35 35-40 40-45 |
резца и регулирования его на заданный размер. Для повышения жесткости расточных борштанг следует уменьшать их длину и увеличивать диаметр, оставляя между борштан- гой и отверстием зазор, необходимый для выхода стружки (табл. 42).
При конструировании приспособления для установки детали следует исходить из минимальной длины борштанги. В расточных борштангах резец следует устанавливать так, чтобы его вершина была выше оси растачиваемого отверстия О на величину h (табл. 43).
Способы установки резцов в расточной борштанге различны; все они должны обеспечивать возможность точного регулирования резцов и их надежное закрепление.
41. Инструментальные материалы для прецизионного обтачивания и растачивания
|
На рис. 217 показана одна из схем закрепления резца 3 в бортштанге 7, при которой применением упорно-регулировочного винта 2 исключается смещение резца под нагрузкой и облегчается регулирование на размер. После наладки на заданный размер осущест-
43. Рекомендуемые значения h (мм) при установке резца в борштанге
|
![]() |
вляется окончательная затяжка и закрепление резца винтом 4.
Схемы закрепления резцов с точным регулированием (резцы «микроборы») показаны на рис. 218, а — в. Резец 1 перемещается при регулировании в борштанге 3 с помощью точного винта (стержень резца 1 выполнен с точной резьбой) и поддерживающего кольца 4 отсчетом по нониусной гайке 2. После регулирования резец закрепляют контргайкой 6 и затяжным винтом 5. Этот способ применяют при растачивании отверстий диаметром 15 мм и выше; точность установки резцов 0,001 мм.
Рис. 218. Схемы закрепления резцов в расточной борштанге с точным регулированием на размер |
![]() |
ТО iTi |
---- АфА--- |
4- |
U ЦА |
Рис. 220. Регулируемая расточная борштанга |
На рис. 219 показана многорезцовая расточная борштанга. Отклонение от перпендикулярности базового торца борштанги относительно оси рабочего хвостовика — не более 0,01 мм; биение рабочего хвостовика относительно направляющего выступа — не более 0,01 мм. Фланец 1 регулируемой расточной борштанги (рис. 220) с эксцентрически расположенным хвостовиком (эксцентриситет г = ОД мм) устанавливают в отверстие шпинделя станка. На фланце болтами закреплено кольцо 2 с борштангой 3. В гнезде борштанги установлен резец б; грубое регулирование на размер осуществляется упорно-регулировочным винтом 4, а фиксация и окончательное закрепление резца — винтом 5. Поворотом кольца 2 изменяют положение борштанги относительно оси шпинделя и тем самым устанавливают окончательный размер. Такие борштанги используют при точности установки 0,015 мм, а также при подналадке по мере износа резца в этих же пределах. Борштанги с виброгасителями применяют, если необходимо устранить вибрации, появляющиеся в процессе обработки, а также, когда требуется получить параметр шероховатости поверхности Ra = 0,125 ч- 0,04 мкм и ниже, либо в случае использования борштанги большой длины (L/D ^ 5 -г- 6). Имеется много различных конструкций борштанг (рис. 221, а) с виброгасителями. Виброгаситель из свинцобого или твердосплавного грузика 3 (рис. 221, б) со втулкой 4, вставляют в отверстие борштанги 1 с зазо-
259
![]() |
ром в радиальном направлении 0,08 — 0,1 мм и осевом направлении 0,25 — 0,3 мм, затем закрывают пробкой 2, которую приваривают. Гашение вибрации борштанги происходит из- за разных амплитуд колебаний грузика и борштанги. Для надежной работы виброгасителя важно, чтобы отверстие в борштанге и наружный диаметр втулки, в которой размещен грузик, были точно обработаны и имели малый параметр шероховатости поверхности.
Борштанги для прецизионного растачивания изготовляют из легированных сталей 18ХГТ, 40Х, 20Х и др., цементуют и закаливают до твердости HRC 56-62. При выполнении ответственных прецизионно-расточных операций для повышения вибростойкости борштанги изготовляют из спеченного вольфрама либо составными — фланец стальной, а стержень твердосплавный.
При установке резцов в расточных борш- тангах применяют приборы типа «наездник» (рис. 222) с магнитным корпусом призматической формы.
Прибор, оснащенный индикатором с ценой деления 0,001 или 0,002 мм, настраивают на радиус растачивания по специально изготовленному для данной операции эталону с базовой поверхностью d; настроенному размеру соответствует нулевое положение стрелки индикатора. Перенеся прибор на борштангу того же диаметра d, регулируют положение вершины резца, добиваясь нулевого положения стрелки индикатора. Приборы типа «наездник» с постоянным магнитом бывают с выключением и без выключения магнитов, могут иметь призму или корпус с плоским основанием; стойка и передвижной кронштейн служат для закрепления переходной державки с индикатором. Благодаря магнитным свойствам прибор прочно удерживается на плите, борштанге или эталоне для настройки на размер. Таким образом, руки наладчика освобождены и он может выполнять все операции по регулированию и настройке инструмента. Приборы с невыключающимися магнитами притягивают к себе металлическую пыль и стружку, загрязняющие базирующие поверхности. Более удобны в эксплуатации приборы с выключающимися магнитами. Точность установки резцов по прибору ± 0,005 — 0,015 мм.
Установка деталей для обработки. Детали устанавливают по заранее обработанным базам, а иногда по отверстиям, подлежащим окончательной обработке на данной операции. В этом случае применяют приспособления с ловителями, которые после закрепления детали удаляют из отверстий. Приспособления с задним или передним и задним направлениями борштанги во втулках применяют для рас-
L л
тачивания отверстии с отношением — > 4 (рис. 223).
Поступательно-индексирующиеся в горизонтальном направлении приспособления служат для предварительного растачивания нескольких отверстий одним шпинделем или для
![]() |
предварительной и окончательной обработки одного отверстия двумя шпинделями. Находят применение также комбинированные приспособления для установки различных деталей на многошпиндельных станках.
Рис. 223. Приспособления для установки и закрепления деталей на столе станка: а — для растачивания с базированием по отверстию; б — с ловителем для растачивания шатуна; в — с направлением борштанга; г — поступательно-индексирующееся в горизонтальном направлении для растачивания двух отверстий; д — станок с поворотным приспособлением для последовательной обработки отверстий |
Детали можно закреплять на шпинделе станка с помощью патронов-цанг и центровых оправок (рис. 224). Приспособления этого типа требуют хорошей балансировки и должны обеспечивать равномерное и легкое закрепление детали и ее точную фиксацию.
В отдельных случаях используют комбинированные приспособления для одновременного растачивания нескольких деталей, установ-
струмента зависит от конфигурации и размеров детали, а также типа станка.
При обтачивании наружных цилиндрических поверхностей деталь закрепляют в шпинделе станка, а резцы — в резцедержателе на столе (рис. 226).
Конические поверхности обрабатывают только при вращении детали (рис. 227). Лишь на специальных станках возможна обработка таких поверхностей при установке детали в приспособлении на столе станка. Обработку эллиптических и сферических поверхностей также осуществляют с установкой детали в шпинделе станка.
![]() |
Внутренние и наружные уступы небольших размеров обрабатывают «в упор» в конце рабочего хода резца, обрабатывающего примыкающую к уступу цилиндрическую поверхность (рис. 228).
![]() |
![]() |
б) |
![]() |
Ж
Рис. 225. Схемы растачивания отверстий с установкой и закреплением детали на столе станка:
а — на горизонтальном двустороннем станке; б — на горизонтальном одностороннем станке (последовательное растачивание двух отверстий); в — на горизонтальных одно- и двустороннем станках с применением многорезцовой наладки
ленных на столе станка, либо для одновременного растачивания и обтачивания деталей, часть которых устанавливают на столе, а часть — в шпинделе станка. Приспособления такого типа позволяют на одном станке без переналадки получать комплектную продукцию. При прецизионном точении применяют копиры, дополнительные резцедержатели и суппорты, позволяющие обрабатывать фасонные поверхности; кроме того можно применять приспособления для координатного растачивания.
Схемы и условия обработки поверхностей. При прецизионном растачивании небольших отверстий деталь закрепляют на столе станка (рис. 225), и он совершает движение подачи, а инструмент вращается, так как целесообразнее вращать с большой частотой хорошо сбалансированную борштангу, чем громоздкую деталь.
Внутренние цилиндрические поверхности можно обрабатывать на станках любого типа, а способ закрепления детали и установки ин-
Рис. 226. Схема прецизионного обтачивания наружных поверхностей
![]() |
Рис. 227. Схемы прецизионной обработки конических поверхностей: а — растачивание; б — обтачивание
![]() |
Рис. 228. Схема обработки внутренних цилиндрических поверхностей с уступами |
|
|
Кормораздатчик мобильный электрифицированный: схема и процесс работы устройства...
Особенности сооружения опор в сложных условиях: Сооружение ВЛ в районах с суровыми климатическими и тяжелыми геологическими условиями...
Опора деревянной одностоечной и способы укрепление угловых опор: Опоры ВЛ - конструкции, предназначенные для поддерживания проводов на необходимой высоте над землей, водой...
Типы сооружений для обработки осадков: Септиками называются сооружения, в которых одновременно происходят осветление сточной жидкости...
© cyberpedia.su 2017-2024 - Не является автором материалов. Исключительное право сохранено за автором текста.
Если вы не хотите, чтобы данный материал был у нас на сайте, перейдите по ссылке: Нарушение авторских прав. Мы поможем в написании вашей работы!