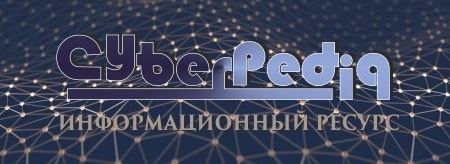
Семя – орган полового размножения и расселения растений: наружи у семян имеется плотный покров – кожура...
Опора деревянной одностоечной и способы укрепление угловых опор: Опоры ВЛ - конструкции, предназначенные для поддерживания проводов на необходимой высоте над землей, водой...
Топ:
Методика измерений сопротивления растеканию тока анодного заземления: Анодный заземлитель (анод) – проводник, погруженный в электролитическую среду (грунт, раствор электролита) и подключенный к положительному...
Техника безопасности при работе на пароконвектомате: К обслуживанию пароконвектомата допускаются лица, прошедшие технический минимум по эксплуатации оборудования...
Выпускная квалификационная работа: Основная часть ВКР, как правило, состоит из двух-трех глав, каждая из которых, в свою очередь...
Интересное:
Берегоукрепление оползневых склонов: На прибрежных склонах основной причиной развития оползневых процессов является подмыв водами рек естественных склонов...
Распространение рака на другие отдаленные от желудка органы: Характерных симптомов рака желудка не существует. Выраженные симптомы появляются, когда опухоль...
Мероприятия для защиты от морозного пучения грунтов: Инженерная защита от морозного (криогенного) пучения грунтов необходима для легких малоэтажных зданий и других сооружений...
Дисциплины:
![]() |
![]() |
5.00
из
|
Заказать работу |
|
|
Проверяемый параметр
Колебание измерительного межосевого расстояния:
за оборот колеса
на одном зубе Разность окружных шагов
0,02-0,04 0,04-0,08 |
0,007-0,015 0,03-0,05 |
Погрешность направления зуба на длине 25 мм Погрешность профиля зуба Радиальное биение
зубьев осуществляется без снятия стружки путем пластического деформирования металла в холодном состоянии. В процессе прикатыва- ния, обычно двумя накатниками, выполненными в виде зубчатых колес, обкатывают заготовку с предварительно обработанными зубьями, расположенными на параллельных осях. Вращающийся накатник, перемещаясь к заготовке, при достижении беззазорного зацепления начинает процесс прикатки под определенной силой. Расстояние между осями накатника и детали постепенно уменьшается до получения требуемого размера зубьев колеса. Во время прикатывания на зубьях обрабатываемого колеса и накатника имеет место взаимное скольжение, которое вызывает на сторонах зубьев колеса сдвиг металла. По опыту ЗИЛа обработка цилиндрического колеса (z = 26; тп = 2,54 мм; р = 39031') на прикатном автомате с двумя накатниками по сравнению с шевингованием позволила увеличить производительность в 4 — 5 раз, уменьшить параметр шероховатости поверхности на профилях зубьев до Ra = 0,32 мкм, снизить уровень звукового давлейия на 2 — 3 дБ, повысить стабильность размеров зубчатого зацепления и качество. Стойкость накатников составляет 274400 деталей, время прикатки колеса 14 с. Зубья прикатанных колес во время термической обработки вследствие более однородной структуры поверхностных слоев деформируются меньше, чем шевингованные. Точность зубчатых колес перед прикатыванием должна быть выше, а припуск на сторону зуба меньше, чем перед шевингованием, наполовину.
|
Зубофрезерование перед шевингованием |
Шевингование |
0,04-0,08 0,015-0,04 |
0,01-0,04 0,02-0,04 |
0,005-0,02 0,005-0,025 |
0,02-0,04 0,01-0,02 |
12 Пол ред. А. Г.. Косиловой и Р. К. Мещерякова, г. 1
Зубохонингование применяют для чистовой отделки зубьев закаленных цилиндрических колес внешнего и внутреннего зацепления. Хо- нингование зубьев осуществляют на специальных станках. Закаленное обрабатываемое колесо вращается в плотном зацеплении с абразивным зубчатым хоном при угле скрещивания осей 10—15°. Поджим детали,к хону осуществляется пружиной с силой 150 — 450 Н. Зубчатое колесо, кроме вращения, совершает возвратно-поступательное движение вдоль оси. Направление вращения инструмента меняется при каждом ходе стола. Хонингование позволяет уменьшить параметр шероховатости поверхности до Ra = 0,32 мкм, удалить забоины и заусенцы размером до 0,25 мм, снизить уровень звукового давления на 2 — 4 дБ и повысить долговечность зубчатой передачи. В процессе хонингования погрешности в элементах зацепления устраняются незначительно при съеме металла порядка 0,01—0,03 мм на толщину зуба. Припуск под хонингование не оставляют. Частота вращения хона 180 — 200 об/мин, подача стола 180 — 210 мм/мин, число ходов стола четыре — шесть. Время хонингования зубчатого колеса автомобиля 30 — 60 с. Срок службы монокорундовых хонов при обработке зубчатых колес коробки передач автомобиля — 1500 — 3000 деталей. Зубчатые колеса, имеющие забоины и заусенцы перед хо- нингованием, целесообразно обкатывать на специальном станке или приспособлении между тремя накатниками под нагрузкой для устранения погрешностей профиля зубьев. Забоины и заусенцы на зубьях обрабатываемого колеса сокращают срок службы и вызывают преждевременную поломку зубьев хона.
Зубчатые колеса высокой точности. Высокая точность цилиндрических зубчатых колес может быть достигнута шлифованием. По сравнению с другими методами шлифование позволяет устранить не только погрешности предварительной обработки, но и неизбежные деформации при закалке. В табл. 25 приведены достигаемая точность и время чистовой обработки зубчатых колес широко распространенными методами шевингования и шлифования. По опыту станкостроительной промышленности зубчатые колеса 3 —4-й степени точности (ГОСТ 1643 — 81) можно изготовить по следующей технологии: фрезерование зубьев под шлифование (5 —6-я степень точности); термическая обработка — цементация и закалка; шлифование баз и предварительное шлифование зубьев (5 —6-я степень точности); искусственное старение; шлифование баз; полу-
|
![]() |
25.Достигаемая точность и время шлифования при чистовои обработке цилиндрических зубчатых колес различными методами
![]() |
Степень точности. по ГОСТ 1643-81 | ШевингоВание | Шлифование методом копирования | Шлифование методом обката абразивным червяком на станках. типа 538J3 | Шлифование методом обката с периодическим делением | |
'двумя шлифовальными кругами на станках типа 5853 | одним коническим шлифовальным кругом на станках типа 5А8Ч1 | ||||
2 | |||||
J | ШШ> | щт | шш | ||
Ч | щш | ||||
til | |||||
6 | |||||
Время шлифования, о/о | — | 100 | J10 | 130-160 |
Примечание: 1 -шлифовальный круг; 2-о5рабатываемое колесо; д-шевер '//У/ - Повышенная трудоемкость обработки и благоприятные Z//Л параметры зубьев колеса |
-Нормальные условия обработки
чистовое шлифование зубьев (4 —5-я степень точности); искусственное старение; окончательное шлифование баз и других поверхностей колеса; окончательное шлифование зубьев (3-4-я степень точности).
Контроль. Высокое качество зубчатых колес можно обеспечить при условии применения современных методов и средств контроля, а также технического контроля на протяжении технологического цикла изготовления, начиная с заготовки и кончая финишными операциями и сборкой. Для обеспечения взаимозаменяемости и надежной работы зубчатой передачи погрешности изготовления зубчатых колес и передач ограничены допусками, которые установлены ГОСТ 1643 — 81. Зубчатые колеса при изготовлении проходят обычно три этапа контроля: производственный, выборочный и приемочный.
|
Производственный контроль. Перед обработкой зубьев приборами контролируют поверхности заготовок, которые используют в качестве баз. Визуально проверяют наличие забоин и заусенцев. После фрезерования и долбления непосредственно на рабочем месте при плотном двухпрофильном зацеплении обрабатываемого колеса с измерительным рабочий или наладчик проверяют размер зубьев с учетом припуска под шевингование, колебание измерительного межосевого расстояния (МОР) за оборот колеса и на одном зубе. Шероховатость поверхности проверяют визуально. После шевингования, кроме размера зубьев и колебания межосевого расстояния дополнительно проверяют форму и расположение пятна контакта, уровень звукового давления и более тщательно шероховатость поверхности на профилях зубьев. Производственному контролю подвергают первые два-три зубчатых колеса с каждого станка в начале рабочей смены, после замены инструмента и под- наладки станка, а также через каждые 1 — 2 ч работы станка. По результатам проверки, если это необходимо, наладчик вносит изменения в наладку станков.
Выборочный контроль предназначен для контроля отдельных элементов зубчатого зацепления после фрезерования, долбления, шевингования и окончательно изготовленных зубчатых колес. Выборочный контроль осуществляет контролер специальными приборами с записывающим устройством, установленными в комнате, хорошо защищенной от шума, рядом с участком изготовления зубчатых колес. В лаборатории контролируют: погрешность профиля, погрешность направления зуба, разность шагов, радиальное биение, колебание МОР, уровень звукового давления, пятно контакта, отклонения длины общей нормали. Основными параметрами, которые определяют геометрию профиля зуба, являются погрешности профиля и направления зуба. Оба эти параметра измеряют на четырех рав- норасположенных по окружности зубьях с обеих сторон профиля на одном приборе. После зубофрезерования и зубодолбления погрешности профиля и направления зуба обычно контролируют один раз в смену, а также после замены инструмента и наладки станка. В процессе шевингования контроль погрешностей профиля и направления зубьев осуществляют чаще, особенно по мере затупления шевера. Контроль проводят в начале смены, после замены инструмента, а также каждой 100-й детали с каждого станка. Результаты измерения контролер вносит в таблицу для каждого станка, что позволяет постоянно анализировать его работу. Пятно контакта и уровень звукового давления после шевингования проверяют у тех же зубчатых колес, у которых измеряли профиль и направление зуба. Разность шагов, радиальное биение и отклонение длины общей нормали контролируют по мере необходимости. Для контроля деформации в процессе термической обработки измеряют два зуба, расположенных под углом 180°. Погрешность профиля зуба измеряют в трех сечениях по длине зуба (середине и двух крайних), а погрешность направления — в трех сечениях по высоте (середине, головке и ножке).
|
Приемочный контроль осуществляют после термической обработки и шлифования баз. На этой стадии у каждого колеса проверяют базы (отверстия, торцы и шейки) после шлифования и параметры зубьев. Выбор основных контролируемых параметров зубчатого зацепления и средств для контроля определяет завод-изготовитель зубчатых колес. Например, у зубчатых передач легковых автомобилей основным параметром оценки качества является плавность зацепления, у зубчатых передач грузовых автомобилей — форма и расположение пятна контакта, у зубчатых передач автобусов — плавность зацепления и пятно контакта. Перед сборкой зубчатые передачи легковых автомобилей подбирают в пары (комплекты) по плавности зацепления, боковому зазору и пятну контакта на контрольно-обкатном станке. Зубчатые колеса для грузовых автомобилей контролируют также на контрольно-обкатном станке с отобранным на производстве сопряженным колесом (срок службы которого 800—1000 деталей), после чего его заменяют новым, а использованное колесо отправляют на сборку. Погрешности профиля и направления зуба, а также разность шагов контролируют на отдельных приборах у 2 —5% колес из общего выпуска. Зубчатые колеса в приборостроении, работающие с минимальным боковым зазором, изготовляют с жесткими допусками по отклонению шага зубьев и биению зубчатого венца. Для колес обычной точности при малом выпуске комплексный двухпро- фильный контроль является достаточным средством проверки качества.
Конические зубчатые колеса
Типы конических зубчатых колес. В зависимости от формы зуба различают прямозубые конические колеса, нулевые, с криволинейными зубьями и гипоидные.
У прямозубых колес зубья при своем продолжении пересекают ось колеса (рис. 205, а). Эти колеса просты для изготовления и сборки. Их применяют для передачи небольших крутящих моментов с окружными скоростями до 5-10 м/с.
|
У нулевых колес зубья криволинейные с углом наклона в середине венца, равным нулю. Эти колеса изготовляют на тех же станках и тем же инструментом, что и конические колеса с криволинейными зубьями. Нулевые ко^ леса устанавливают в тех же узлах, что и прямозубые. Они могут работать плавно и бесшумно при более высоких окружных скоростях, чем прямозубые колеса.
У колес с криволинейными зубьями угол рт наклона линии зуба в середине венца не ра- 1
![]() |
а) б) 6)
Рис. 205. Типы конических колес: а — прямозубые; б — с криволинейными зубьями; в — гипоидные; 1 — шестерня; 2 — колесо
вен нулю (рис. 205,6). Вследствие кривизны зубьев при зацеплении обеспечивается непрерывный контакт одновременно на нескольких зубьях. Они способны передавать крутящие моменты примерно на 30% выше, чем нулевые и прямозубые конические колеса тех же размеров. Конические колеса с криволинейными зубьями применяют в оборудовании всех типов, при окружных скоростях до 40 м/с.
У гипоидных колес ось ведущей шестерни
1 смещена относительно оси ведомого колеса
2 выше или ниже на величину Е (рис. 205, в). Гипоидные колеса прочнее и бесшумнее в эксплуатации, чем конические колеса с криволинейными зубьями. Их применяют в узлах и механизмах с окружными скоростями 5 — 40 м/с и менее.
Методы получения заготовок. Объемная холодная штамповка является наиболее эффективным методом малоотходного изготовления деталей. При высокой производительности она обеспечивает минимальный припуск (0,1—0,3 мм) на сторону, получение гладкой поверхности без окалины, значительно сокращает или полностью устраняет последующую механическую обработку. Например, коническую шестерню-вал с диаметром зубчатого венца 40 мм изготовляют за пять переходов с производительностью 30 шт/мин. Потеря металла в стружку составляет 2 — 7%.
Горячая щтамповка конических колес с припуском 0,6 — 0,8 мм на сторону под чистовое зубонарезание разработана ЗИЛом совместно с НИИТавтопромом. Применяется для конических колес дифференциала автомобиля с модулем 5 мм и выше. Предварительно нагретую с помощью ТВ.Ч до температуры ковки мерную заготовку 1 сателлита дифференциала (zt — 11; mte = 6,35 мм; b = 30 мм) штампуют за два перехода: осадка заготовки 2 для очистки от окалины и приближения ее диаметра к диаметру поковки и штамповка заготовки 3 с формообразованием зуба (см. рис. 198, в). Штамповку выполняют на кривошипном горячештамповочном прессе с номинальным усилием 16 МН и производительностью 300 шт/ч. Масса заготовки снижена на 0,37 кг. При этом за год экономится 472 т легированной стали, сокращена операция чернового зубонарезания, высвобождены рабочие, станки, производственная площадь и т. д.
Метод порошковой металлургии позволяет получить значительную экономию металла. Прямозубые конические колеса дифференциала автомобиля изготовляют на автоматической линии в три последовательных перехода: точное взвешивание порошка и изостатическое формование в эластичной или деформируемой оболочке, спекание при температуре 1315 °С и окончательная горячая штамповка на горизонтальном эксцентриковом прессе за один ход. Производительность пресса 360 — 450 шт/ч. Прямозубые конические колеса, обработанные этим методом, не требуют дополнительной механической обработки; их точность соответствует точности колес, нарезанных методом кругового протягивания. Отход металла в стружку составляет около 5%.
Заготовки, полученные методом пластической деформации в холодном или горячем состоянии, обычно имеют неоднородную твердость и неблагоприятную для резания структуру металла. Для устранения указанных недостатков заготовки перед механической обработкой подвергают нормализации, улучшению, отжигу, отпуску. Наилучших результатов при обработке заготовок из легированных сталей достигают при изотермическом отжиге. После изотермического отжига заготовки имеют крупнозернистую ферритно-перлитную структуру с твердостью НВ 156 — 207 и пределом прочности при растяжении ав = = 520 -т- 686 МПа. Если заготовки имеют пониженную твердость, то при обработке зубьев металл налипает на режущие кромки инструмента, параметр шероховатости поверхности повышается. Слишком твердый материал вызывает повышенное изнашивание инструмента.
Точность обработки заготовок. Качество окончательно изготовленных конических и гипоидных зубчатых передач в значительной степени определяется точностью обработки заготовок. Наиболее ответственными поверхностями являются шейки, отверстия и опорные торцы, которые являются базами при зубообработке, контроле и сборке. В табл. 26 приведены допуски на отверстия и шейки типовых конических зубчатых колес в закаленном и незакаленном виде в зависимости от их степени точности (ГОСТ 1758 — 81).
Максимальное биение поверхностей Т, Di и D2 шестерни относительно оси детали в незакаленном и закаленном виде составляет 0,005 — 0,01 мм (рис. 206, а). Биение незакаленной цилиндрической поверхности D4, служащей для контроля точности установки зубчатого колеса при сборке в редукторе, относительно поверхностей Dl и D2 должно быть в пределах 0,005-0,01 мм. Биение поверхности Z)3 ограничивается допуском в том случае, если она используется для зажима во время зу- бонарезания и контроля. После термической обработки и зачистки центров необходимо править деталь таким образом, чтобы максимальное биение поверхности после правки не превышало 0,025 мм, а поверхности D2 — 0,04 мм. Для конических колес (рис.
![]() |
206,6) устанавливают допуски плоскостности опорного торца (табл. 27). Допуск плоскостности опорного торца до термической обработки для поверхностей Тх и Т2 составляет 0,025 мм; допуск круглости отверстия d до термической обработки — 0,025 мм, а после термической обработки — 0,08 мм.
У зубчатых колес, которые закаливают в штампах, биение конуса вершин зубьев и поверхности прижимного фланца Т3 до термической обработки не должно превышать 0,075 мм. Указанные поверхности в процессе закалки соприкасаются с поверхностями штампа, поэтому при давлении незначительные погрешности могут вызвать деформацию заготовки колеса.
Кроме допусков на базы заготовок конических зубчатых колес устанавливают допуски на внешний диаметр вершин зубьев dae (табл. 28), расстояние С от базы до внешней окружности вершин зубьев, угол 5а конуса вершин зубьев (табл. 29), угол заднего конуса со, базовые расстояния Ах и Л2, ширину зубчатого венца b и др.
26. Рекомендуемые допуски на заготовки конических зубчатых колес, мм (см. рис. 206, а)
|
Когда конус вершин зубьев или задний конус используют в качестве баз при механической и термической обработках, допуски на
27. Рекомендуемые допуски (мм) плоскостности торца (см. рис. 206,6)
|
28. Рекомендуемые допуски на внешний диаметр и расстояние от базы до внешней окружности вершин зубьев, мм
Внешний окружной модуль, мм | dae | С |
До 1 1-10 Св. 10 | -0,075 -0,150 -0,250 | -0,05 -0,05 -0,10 |
29. Рекомендуемые допуски на угол кофуса вершин и угол заднего конуса, угловые минуты | ||
Внешний окружной модуль, мм | 5а | 0) |
До 0,75 0,75-1,5 Св. 1,5 | + 30 + 15 + 8 | + 60 + 30 + 15 |
угол конуса вершин и угол заднего конуса необходимо ужесточить.
Нарезание конических колес с прямыми зубьями. Наибольшее распространение в промышленности получили три метода нарезания зубьев: зубострогание, зубофрезерование и зу- бопротягивание.
Зубофрезерование дисковыми модульными фрезами осуществляют методом врезания с единым делением. Этим методом изготовляют зубчатые колеса невысокой точности (9 —10-й степени); его в основном применяют для чернового нарезания зубьев в условиях серийного производства. Обработку проводят на зубофрезерном станке ЕЗ-40 (de = 320 мм; mte = 8 мм) с двухпозиционным поворотным столом. Стандартные модульные фрезы не обеспечивают равномерного припуска под чистовую обработку, поэтому, когда необходим минимальный припуск, применяют специальные фрезы, спроектированные только для данного колеса. Время нарезания одной впадины зубьев 5 — 20 с. Скорость резания при обработке быстрорежущими фрезами чугунных колес 20 — 25 м/мин, стальных 25 — 30 м/мин. Черновое нарезание зубьев модульными фрезами можно проводить в делительной головке на фрезерном станке. Номер фрезы определяют по табл. 30 в зависимости от приведенного числа зубьев zx = z/cos 8.
Зубострогание является наиболее простым и менее производительным методом по сравнению с другими методами нарезания прямозубых конических колес. Благодаря универсальности и несложной конструкции режущего 30. Дисковые модульные фрезы для нарезания зубьев конических колес
Приведенное | Номер | Приведенное | Номер |
число зубьев | фрезы | число зубьев | фрезы |
12-13 | 26-34 | ||
14-16 | 35-54 | ||
17-20 | 55-134 | ||
21-25 | 135 -зуб | ||
чатая рейка |
инструмента он получил широкое распространение в единичном и серийном производстве. Обработку зубьев проводят на зубостро- гальных станках методом обкатки с единичным делением. В основу процесса нарезания зубьев на этих станках положено станочное зацепление обрабатываемого колеса 3 (рис. 207) с воображаемым производящим колесом 4, роль зубьев которого выполняют зубострогальные резцы 1 и 2. При обработке зубострогальные резцы, установленные в резцедержателях ползунов станка, получают возвратно-поступательное движение, необходимое для резания. Совместно с обрабатываемым колесом резцам сообщают также движение обкатки. В результате последовательных огибающих резов прямолинейные режущие кромки резцов формируют октоидный профиль зубьев обрабатываемого колеса.
Конические колеса с модулем до 4 мм нарезают из целой заготовки за одну операцию методом обкатки, а с модулем свдлше 4 мм за две операции — черновую и чистовую. Черновое нарезание зубьев можно выполнять методами обкатки, врезания или комбинированным, включающим врезание и обкатку.
Черновое нарезание методом врезания является наиболее простым и экономичным. При этом методе движение обкатки отсут-
![]() |
а) |
б) |
Рис. 207. Схемы расположения зубострогальных резцов: а — в начале резания; б —в конце резания |
|
|
Индивидуальные очистные сооружения: К классу индивидуальных очистных сооружений относят сооружения, пропускная способность которых...
История создания датчика движения: Первый прибор для обнаружения движения был изобретен немецким физиком Генрихом Герцем...
История развития пистолетов-пулеметов: Предпосылкой для возникновения пистолетов-пулеметов послужила давняя тенденция тяготения винтовок...
Архитектура электронного правительства: Единая архитектура – это методологический подход при создании системы управления государства, который строится...
© cyberpedia.su 2017-2024 - Не является автором материалов. Исключительное право сохранено за автором текста.
Если вы не хотите, чтобы данный материал был у нас на сайте, перейдите по ссылке: Нарушение авторских прав. Мы поможем в написании вашей работы!