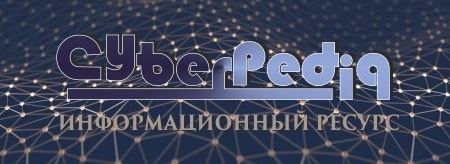
Архитектура электронного правительства: Единая архитектура – это методологический подход при создании системы управления государства, который строится...
Механическое удерживание земляных масс: Механическое удерживание земляных масс на склоне обеспечивают контрфорсными сооружениями различных конструкций...
Топ:
Проблема типологии научных революций: Глобальные научные революции и типы научной рациональности...
Определение места расположения распределительного центра: Фирма реализует продукцию на рынках сбыта и имеет постоянных поставщиков в разных регионах. Увеличение объема продаж...
Эволюция кровеносной системы позвоночных животных: Биологическая эволюция – необратимый процесс исторического развития живой природы...
Интересное:
Искусственное повышение поверхности территории: Варианты искусственного повышения поверхности территории необходимо выбирать на основе анализа следующих характеристик защищаемой территории...
Финансовый рынок и его значение в управлении денежными потоками на современном этапе: любому предприятию для расширения производства и увеличения прибыли нужны...
Что нужно делать при лейкемии: Прежде всего, необходимо выяснить, не страдаете ли вы каким-либо душевным недугом...
Дисциплины:
![]() |
![]() |
5.00
из
|
Заказать работу |
|
|
Поскольку экструдер работает вместе с головкой, то и про-изводительность его находится путем совместного решения урав нений (3) и (4) или графически (рисунок. 6) как точка пересече-ния прямых 1 или 2 с прямой 3. Точки пересечения а и б называ-ются рабочими точками.
Упрощенный аналитический расчет Q машины с одним шнеком, уменьшающейся глубиной нарезки канала шнека, с учетом сеток и головки можно производить по формуле
Q = АKN/(К + B + G), (9)
где Q – производительность, см3/мин; А+ B + G – постоянные прямого и обратного потоков и потока утечек, см3; К – постоян-ная головки, сеток, решетки, см3. Для различных головок К раз-лична и рассчитывается по соответствующим формулам общего вида:
K = 1/Σ(1/Ki), (10)
где К i – коэффициент сопротивления каждого из элементов головки, сеток и решетки.
Реальные зависимости Q – P (см. рисунок 6) не являются прямолинейными. Зоны экструдера, формующей оснастки име-ют различный внешний обогрев, кроме того, в зависимости от интенсивности вращения шнека в расплаве выделяется разное количество тепла. Поэтому такие важнейшие характеристики, как вязкость и плотность расплава зависят от температуры и не являются строго постоянными. Эти, и другие факторы, ведут к отклонению зависимостей (3) и (4) от прямолинейности.
ОСНОВНЫЕ ПАРАМЕТРЫ ПРОЦЕССА ЭКСТРУЗИИ
К технологическим параметрам процесса экструзии отно-сятся температура переработки полимера по зонам материально-го цилиндра и головки, давление расплава, скорость вращения шнека N, температурные режимы охлаждения сформованного экструдата.
К технологическим свойствам экструдируемого термоплас-та относятся температура плавления (или текучести), темпера-тура деструкции, температура кристаллизации (или температу-ра затвердевания), вязкость расплава при температурах и скорос-тях сдвига при экструзии, насыпная плотность материала и плот-ность расплава.
|
Основными технологическими характеристиками экструде-ра являются L, D, L/D, геометрический профиль шнека, степень изменения объема канала шнека, мощность привода.
Основной характеристикой формующей оснастки (вместе с фильтрующими сетками) является коэффициент сопротивления течению расплава K. Повышение давления на фильтрующих сет-ках служит показателем засорения, т. е. увеличения сопротивле-ния сеток и, следовательно, сигналом к их замене.
Показателем работы экструдера является его эффективность – отношение производительности (Q) к потребляемой мощности:(M)
Э = Q / M
ПОСТРОЕНИЕ РАБОЧЕЙ ХАРАКТЕРИСТИКИ
ОДНОШНЕКОВОГО ЭКСТРУДЕРА
Цель работы: Построение рабочей характеристики экструдера (зависимость производительности экструдера от давления перед формующей головкой).
Используемые материалы: Вязкая жидкость, моделирующая расплав полимера (глицерин, поливиниловый спирт, силиконо-вая жидкость)
Используемое оборудование: Модель одношнекового экст-рудера, снабженная датчиком давления и головкой с изменяе-мым проходным сечением; секундомер, воронка для залива рабочей жидкости; стакан для слива жидкости; мерный цилиндр.
Порядок выполнения работы:
1.Ознакомиться с устройством модели одношнекового экстру-дера. Выполнить эскиз модели с указанием основных геометри- ческих параметров шнека, определяющих производительность экструдера.
2.Подключить к электросети (220 V) через розетку привод моде-ли. Убедиться в свободном вращении шнека. Проверить возмож-ность свободного перемещения заслонки, регулирующей про-ходное сечение головки.
3.При вращающемся шнеке и незаполненном рабочем цилиндре откорректировать показания манометра, замеряющего давление перед головкой. Манометр должен показывать "0" при полнос-тью закрытой заслонке.
|
4. При вращающемся шнеке и полностью закрытой заслонке го-ловки установить стеклянную воронку в загрузочное окно рабо-чего цилиндра экструдера, под выходное отверстие головки подставить стакан для слива жидкости и заполнить рабочий ци-линдр жидкостью, моделирующей расплав полимера. Наблю-дать за изменением показаний манометра в процессе заполнения рабочего цилиндра. Отметить максимальное значение давления по манометру и записать его в таблицу 1. Повторить замеры трижды.
5. При вращающемся шнеке полностью открыть заслонку и, про-должая приливать в цилиндр рабочую жидкость, наблюдать за изменением показаний манометра. Записать в таблицу 1 устано-вившееся значение давления при полностью открытой заслонке. Вытекающую жидкость собирать в стакан.
Таблица 1 – Результаты экспериментального определения производительности установки.
№ п/п | Ширина зазора, м | Показания манометра, Па | Время отбо-ра порции жидкости, с | Расход жидкости, Q, м куб |
δ1,1; δ1,2, δ1,3… δ1ср | Р11, Р12, Р13 Р1ср | Q11, Q12, Q13 Q1 ср | ||
δ2,1; δ2,2, δ2,3 δ2ср | Р21, Р22, Р23 Р2ср | Q21, Q22, Q23 Q2 ср | ||
… | … | |||
δ 7,1; δ7,2, δ7,3 δ7ср | Р 71, Р 72, Р7, Р7ср | Q71, Q7,2, Q7,3 Q7 ср |
6. Изменяя положение заслонки (приоткрывая ее постепенно), записывать в таблицу 1 ширину проходного сечения головки (м) и показания манометра, ему соответствующие.
Подставить под головку мерный цилиндр и определить объем жидкости, вытекающей из головки за 30 сек (Q,cм3).
Величину проходного сечения головки изменять последо-вательно от 0 до 12 делений таким образом, чтобы в данном про-межутке получить 7 замеров.
Три раза (по 7 замеров, которые могут соответствовать разным значениям δi) определить изменение расхода и давления при изменении ширины щели и записать результаты.
По этим данным построить зависимости Q = f (δ i) и P = f (δ i) для каждой из трех серий измерений (рисунки 1 и 2). При этом значения δ i могут не совпадать в каждой серии измерений.
На полученных графиках найти геометрическим способом средние значения Q = f (δ i) и P = f (δ i), задав δ i, равными 0, 2, 4, 6, 8, 10 и 12 делениям.
Рисунок 1 – Результаты определения P = f (δ i),
|
Рисунок 2 – Результаты определения Q = f (δ i)
Рисунок 3 – Зависимость Q по шнеку от давления Р
7. Построить график зависимости расхода от давления для шне-ка модельной установки (рисунок 3). При этом значения Q и P для нанесения на график брать по усредненным кривым Q = f (δ i)
и P = f (δ i) при равных значениях зазора (рисунок 1 и 2).
8. Рассчитать теоретические производительности головок при давлениях, установленных в п. 7, для соответствующих раз-меров проходного сечения головки (δ i), по формуле:
Q гол = K●Р / η, (1)
где Р – давление перед головкой (показания манометра), Па
η – вязкость рабочей жидкости, Па с (для глицерина при 25 0С: динамическая вязкость η = 0,95 Па с, при 200 С η = 1,49 Па с; для индустриального масла ИП-40 при 25оС: кинематическая вязкость μ = 0,69 мм2/с и ρ = 0,888 г/см3).
К – коэффициент сопротивления головки, рассчитываемый для щелевой головки по формуле:
К= b●h3 / 12●L, (2)
где b – ширина канала, (зазор, δ изменяемый при выполнении работы), м.
h – высота канала, м (27 мм).
L – длина канала, м (150мм).
Полученные расчетные данные внести в таблицу 2.
9. По данным таблицы 1 построить для модели эксперименталь-ную зависимость расхода от давления перед головкой по шнеку и теоретическую по головке («Q – P» диаграмму, рисунок 4).
10. Определить экспериментальную рабочую точку экструдера (т. А на рисунке 4)
11. Рассчитать теоретическую производительность модельной установки по головке. При этом расчет производительности го-ловки вести, задавая произвольно 2 - 5 значений давления в интервале, установленном в п.7. Внести результаты расчета в таблицу 2 и построить зависимость «Qт – P» для головки.
Рисунок 4 – Рабочая диаграмма экструзионной установки.
1 – производительность по шнеку; 2 – производительность
по головке; т. А – рабочая точка экструдера
Использовать полученные значения Q э для построения как экспериментальной, а Q т теоретической рабочей характеристи-ки экструдера (количество расходных характеристик для голо-вок построить по указанию преподавателя).
Таблица 2 – Результаты определения теоретической производительности по шнеку и головке.
|
№ п\п | Ширина зазора, м | Давление, Па | Производи- тельность по шнеку м 3/с | Производи-тельность по головке, м 3/c |
12.Задавая давления в интервале, полученном в п. 7, и, исходя из геометрических параметров шнека модельной установки, рассчитать ее теоретическую производительность по шнеку, используя формулу:
Qт = А●N – В●Р/ η – С●P/ η, (3)
где η – вязкость рабочей жидкости, Па с
N – число оборотов шнека, об/с (0,55 об/с)
A, B и С – константы прямого, обратного потоков и пото-ка утечек, рассчитываемые по формулам:
A = (π2D2h sin φ cos φ) /2; (4)
B = (π Dh3sin2 φ) /12L; (5)
G = (π 2D2 δ 3tg φ)/ 10 L e, (6)
где m – число заходов шнека, m = 1
t – шаг винтовой нарезки шнека, м (20мм)
D – диаметр шнека, м (24 мм)
δ – зазор между гребнем шнека и корпусом цилиндра, м (δ = 0,5мм)
φ – угол подъема винтовой линии шнека, (18 град)
е – ширина гребня шнека, м (5 мм)
L – длина нарезной части шнека, м (190мм)
h – высота нарезки шнека, м (4 мм)
Результаты расчета внести в таблицу 2 и построить зависимость «QT – P» для шнека.
14. Графически определить теоретическое положение рабочей точки. Сопоставить экспериментальные и расчетные данные по производительности в рабочей точке. Указать причины, обус-ловливающие расхождение теоретических расчетов и экспери-ментальных данных.
15. Обсудить полученные экспериментальные данные, сравнить экспериментальную рабочую диаграмму экструдера и теорети- ческую, сделать выводы по результатам работы.
Вопросы для подготовки к работе и ее защите:
1. Рассмотреть процесс перемещения материала в рабочем ци-линдре экструдера и изменение его агрегатного состояния. Назвать основные факторы, влияющие на производительность экструдера.
2. Как влияет на производительность экструдера вязкость мате-риала, температура расплава, геометрические параметры шнека и головки?
3. Как изменится производительность экструдера, головки и уста-новки в целом при изменении вязкостных свойств материала, конфигурации головки, геометрических размеров каналов го-ловки при сохранении их конфигурации?
4. Рассчитать скорость вращения червяка, при которой обеспечи-вается заданное (по указанию преподавателя) значение произво-дительности и давления в головке.
5. Какое явление называется «пульсация расплава», как она влияет на качество изделий и как можно снизить пульсацию?
Список литературы к работе
1.Основы технологии переработки пластмасс /Под ред. Кулезнева В.Н. и Гусева В.К. – М.: Химия, 2006 – с. 372 – 418.
2.Раувендааль К. Экструзия полимеров. С-Пб.: Профессия,
2006. – 850 с.
3.Бортников В.Г. Основы технологии переработки пластических масс: Учебное пособие для вузов. – Л.: Химия,1983. – С.103 – 132.
|
4.Тадмор З., Гогос К. Теоретические основы переработки поли-меров. //Пер.с англ. – М.: Химия, 1984. – С 418 – 423;
С. 428 - 438.
5.Шембель А.С., Антипина О.М. Сборник задач и проблемных си-
туаций по технологии переработки пластмасс, Л.: Химия, 1990. – С. 9 – 30.
Приложение А.
Таблица 1 – Конструктивные параметры шнеков и значения средних градиентов скорости сдвига, рекомендуемые для переработки термопластов
Материал | Тип изделия | Тип сырья | ![]() | hзагр / hдозир | m в зоне дозиро-вания | m в зоне сжа- тия |
ПЭВП | трубы | грану-лы | 50 -110 | 3,7 – 4,35 | ||
листы | грану-лы | 100 -230 | 3,7 – 4,35 | |||
ПЭНП | пленки | грану-лы | 50 -110 | 3,7 – 4,35 | ||
трубы | грану-лы | 50 -110 | 3,7 – 4,35 | |||
Полипрпилен | все | грану-лы | 55 -110 | 4,35 | ||
ПВХ жесткий | все | грану-лы | 15 -40 | 2,7 - 3,1 | 5 - 6 | 5 - 6 |
ПВХ пластикат | все | грану-лы | 90 -210 | 3,35 – 4 | ||
Полистирол | грануляция | грану-лы | 100 -200 | 4 – 4,35 | ||
Ударопрочный ПС | листы | грану-лы | 50 -110 | 4 – 4,35 | ||
Полиакрилаты | листы | грану-лы | 40 -100 | 3,35 - 3,7 | ||
Полиамид 6,6 | все | грану-лы | 20 -110 | 4 – 4,35 |
Учебное издание
Ушакова Ольга Борисовна
|
|
Семя – орган полового размножения и расселения растений: наружи у семян имеется плотный покров – кожура...
Своеобразие русской архитектуры: Основной материал – дерево – быстрота постройки, но недолговечность и необходимость деления...
Таксономические единицы (категории) растений: Каждая система классификации состоит из определённых соподчиненных друг другу...
Механическое удерживание земляных масс: Механическое удерживание земляных масс на склоне обеспечивают контрфорсными сооружениями различных конструкций...
© cyberpedia.su 2017-2024 - Не является автором материалов. Исключительное право сохранено за автором текста.
Если вы не хотите, чтобы данный материал был у нас на сайте, перейдите по ссылке: Нарушение авторских прав. Мы поможем в написании вашей работы!