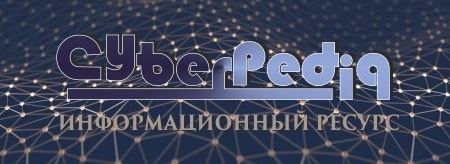
Типы оградительных сооружений в морском порту: По расположению оградительных сооружений в плане различают волноломы, обе оконечности...
Таксономические единицы (категории) растений: Каждая система классификации состоит из определённых соподчиненных друг другу...
Топ:
Когда производится ограждение поезда, остановившегося на перегоне: Во всех случаях немедленно должно быть ограждено место препятствия для движения поездов на смежном пути двухпутного...
Марксистская теория происхождения государства: По мнению Маркса и Энгельса, в основе развития общества, происходящих в нем изменений лежит...
Оценка эффективности инструментов коммуникационной политики: Внешние коммуникации - обмен информацией между организацией и её внешней средой...
Интересное:
Подходы к решению темы фильма: Существует три основных типа исторического фильма, имеющих между собой много общего...
Лечение прогрессирующих форм рака: Одним из наиболее важных достижений экспериментальной химиотерапии опухолей, начатой в 60-х и реализованной в 70-х годах, является...
Искусственное повышение поверхности территории: Варианты искусственного повышения поверхности территории необходимо выбирать на основе анализа следующих характеристик защищаемой территории...
Дисциплины:
![]() |
![]() |
5.00
из
|
Заказать работу |
|
|
О.Б. УШАКОВА
ПОСТРОЕНИЕ РАБОЧЕЙ ХАРАКТЕРИСТИКИ ОДНОШНЕКОВОГО ЭКСТРУДЕРА
Учебно-методическое пособие
для студентов, обучающихся по направлению
подготовки 18.03.01 «Химическая технология»
Профиль «Технология и переработка полимеров»
Москва МИТХТ 2016
УДК 678.027
ББК 74.58
П 18
Утверждено редакционно-издательским советом МИТХТ в качестве учебного пособия для студентов
Подготовлено на кафедре химии и технологии переработки пластмасс и полимерных композитов
Рецензенты: к.т.н. проф. Буканов А. М. и к.т.н.доц. Чалая Н.М.
Ушакова О.Б.
Построение рабочей характеристики одношнекового экструдера.
Учебно-методическое пособие
М.:МТУ. 2016. - 32 с
.
ISBN 978-5-7339- © Ушакова О.Б., 2016
© МИТХТ, 2016
Введение
Первые экструдеры были созданы в 19 в. в Великобритании, Германии и США для нанесения гуттаперчевой изоляции на электрические провода. В начале 20 в. было освоено серийное производство экструдеров. Примерно с 1930г. экструдеры стали применять для переработки пластмасс; в 1935 – 37 г.г. паровой обогрев корпуса заменили электрическим; в 1937 – 39г.г. появи-лись экструдеры с увеличенной длиной шнека (аналог современ-ного экструдера), был сконструирован первый двухшнековый экструдер.
На базе одно- и двушнековых экструдеров созданы уста-новки (линии) для производства листов, пленок, труб, пластмас- совой вагонки, нанесения изоляции на кабели, формования по-лых изделий методом раздува и др. Современные экструдера имеют производительность до 1500кг/час.
Рисунок 1 – Общий вид одношнекового экструдера
ОПИСАНИЕ ПРОЦЕССА ЭКСТРУЗИИ
Процесс экструзии полимеров на одношнековых (одночервяч-
|
ных) машинах – это процесс получения из исходного полимерного материала (гранулы, порошок) непрерывных профильных изделий (труб, листов, пленок и т.п.) путем непрерывного выдавливания расплава через формующий инструмент (головку).
Основным рабочим органом одночервячного экструдера явля-ется обогреваемый материальный цилиндр (1), внутри которого вращается шнек, называемый иногда червяком (2). Привод враще-ния шнека осуществляется двигателем (6) через редуктор (5). Шнеки характеризуют длиной (L), диаметром (D ), геометрией
поперечного сечения канала шнека (высотой нарезки, углом подъ ема, шириной гребня нарезки), шагом t, степенью сжатия i, и чис- лом заходов нарезки.
Рисунок 2 – Схема устройства одношнекового экструдера
Глубина винтового канала переменна по длине шнека: умень-шается по мере удаления от загрузочного окна. В зависимости от перерабатываемого материала и назначения одношнекового экс-трудера шнеки имеют разное отношение длины к диаметру (L/D). Наиболее часто используются шнеки с L/D = 20 – 25.
![]() |
Рисунок 2 – Фотографии материального цилиндра
и шнеков разных диаметров
Материал в виде гранул (крошки) или порошка подается в бункер-дозатор(4), откуда поступает через загрузочное окно в мате-риальный цилиндр и попадает на витки шнека.
Попав на витки шнека, материал перемещается в винтовом канале, образованном внутренней поверхностью материального цилиндра и нарезкой шнека. При движении по винтовому каналу от загрузочного окна к головке материал уплотняется, расплавля ется, из него удаляется воздух, происходит гомогенизация рас-плава.
В соответствии с характером процессов, протекающих в одношнековом экструдере в направлении движения материала выделяют 3 зоны (рисунок 3):
Рисунок 3 – Схема деления шнека экструдера на зоны
|
Длина зон экструдера может колебаться в значительных пре-делах в зависимости от типа перерабатываемого материала (рису-нок 4).
В зоне загрузки (I) происходит прием перерабатываемого материала и его перемещение в направлении зоны уплотнения и плавления. Чтобы материал не подплавлялся и не образовывал пробку, загрузочную горловину охлаждают водой.
Перемещение материала по направлению к формующей головке будет происходить только в том случае, если сила тре-ния материал - поверхность шнека будет меньше, чем материал - поверхность материального цилиндра.
Рисунок 4 – Основные типы шнеков для экструзии термопластов:
а – шнек общего назначения с тремя (I, II, III) зонами;
б – шнек для переработки высококристаллических полимеров,
в – шнек для экструзии ПВХ;
Коэффициент трения термопластичных материалов возрас-тает до температуры плавления (текучести), а затем снижается. Поэтому при переработке ряда материалов внутри шнека в зоне загрузки предусматривают охлаждающий канал.
Производительность экструдера по зоне загрузки можно рассчитать по формуле
Q загр = 0,06 S t N ρ нас η ε [кг/час], (1)
где: S – площадь полезного сечения шнека, см2
t – шаг нарезки шнека, см
N – число оборотов шнека,об/мин
ρ нас – насыпная плотность гранул или порошка, кг/дм3
η – коэффициент полезного действия шнека в зоне загрузки (0,6 – 0,98)
ε – коэффициент заполнения шнека (при отсутствии зависания 0,95 – 1,0).
В зоне плавления (пластикации) (II) происходит переход материала в вязко-текучее состояние, его уплотнение и удаление воздушных включений. Канал червяка в этой зоне выполняется с постепенно уменьшающимся объемом, что достигается либо уменьшением глубины винтового канала h1, либо шага винтовой линии t, или обоих параметров.
В начале зоны плавления (пластикации) происходит под-плавление полимера, примыкающего к поверхности цилиндра. Расплав постепенно накапливается и воздействует на убываю-щую по ширине пробку (рисунок 3) поскольку глубина нарезки шнека уменьшается по мере продвижения материала от зоны I к зоне III, то возникающее давление заставляет пробку плотно прижиматься к горячей стенке цилиндра, где и происходит плав-ление полимера.
В зоне пластикации пробка плавится также и под действии ем тепла, выделяющегося из-за внутреннего, вязкого трения в материале в тонком слое расплава (поз. 3 на рисунке 5), где про исходят интенсивные сдвиговые деформации – материал пласти-цируется, т.е переходит в текучее состояние.
|
На поверхности пробки образуется тонкий слой расплава. Постепенно толщина этого слоя увеличивается, и в тот момент, когда ширина пробки уменьшится до 0,1+0,2 ширины винтового канала червяка, циркуляционное движение в слое расплава, соби рающемся перед толкающей стенкой, разрушает остатки проб- ки, дробя ее на мелкие куски.
Рисунок 5 – Схема плавления пробки материала в зоне плавления в межвитковом сечении шнека:
1 – стенки цилиндра; 2 – гребень шнека; 3 – потоки расплава полимера; 4 – спрессованный твердый полимер (пробка) в экструдере.
Когда толщина пленки расплава становится равной толщи-не радиального зазора между стенкой корпуса и гребнем винто-вой нарезки червяка, последний начнет соскребать слой распла-ва со стенки, собирая его перед своей толкающей гранью. Это сечение червяка является фактическим концом зоны питания и началом зоны плавления.
Наличие в зоне плавления интенсивных сдвиговых деформа-
ций приводит к выраженному смесительному эффекту. Расплав интенсивно гомогенизируется, а составляющие композицион-ного материала перемешиваются.
Зона плавления наиболее сложная из зон червяка – харак-теризуется пребыванием в канале полимерного материала в двух состояниях: расплавленном и твердом
Конец зоны II характеризуется распадом пробки на отдель- ные фрагменты. Далее расплав полимера с остатками твердых
частиц попадает в зону дозирования.
Уменьшающаяся глубина нарезки шнека создает давление, ко-торое необходимо для продавливания расплава через фильтрующие сетки, подачи его в головку, уплотнения и в итоге – для выхода сформованного изделия.
Основной подъем давления расплава (P) происходит на границе зон I и II. На этой границе образующаяся пробка из спрессованного материала как бы скользит по шнеку: в зоне I это твердый материал, в зоне II – плавящийся. Наличие этой пробки и создает основной вклад в повышение давления распла-ва. Запасенное на выходе из цилиндра давление расходуется на преодоление сопротивления сеток, течения расплава в каналах головки и формования изделия.
|
Рисунок 6 – Схема распределение давления по длине шнека
Распределение давления по типу А соответствует случаю, когда производительность зоны плавления шнека намного ниже производительности зоны выдавливания, а. кривая типа В – слу-чаю, когда плавление полимера идет с такой же скоростью как и выдавливание расплава через головку. В этих условиях давление начинает повышаться в зоне плавления, а перед головкой развивает-ся более высокое давление, что ведет к повышению производитель-ности по сравнению с вариантом А.
Кривая типа С соответствует условиям, при которых произво-дительность зоны плавления выше, чем производительность зоны дозирования.
Зона дозирования (III). Продвижение гетерогенного мате-риала (расплав, частички твердого полимера) продолжает сопро-вождаться выделением внутреннего тепла, которое является ре-зультатом интенсивных сдвиговых деформаций в полимере. Рас-плавленная масса продолжает гомогенизироваться, что проявля-
ется в окончательном плавлении остатков твердого полимера, усреднении вязкости и температуры расплавленной части.
В межвитковом пространстве расплав имеет ряд потоков, основными из которых являются продольный и циркуляционный. Величина продольного (вдоль оси шнека) потока определяет производительность экструдера Q, а циркуляционного – каче-ство гомогенности полимера или смешения компонентов.
В свою очередь продольный поток складывается из трех потоков расплава: прямого, обратного и потока утечек.
На рисунке 7 показаны эпюры распределения скоростей прямого (а), обратного (б) и результирующего (в) потоков рас-плава в межвитковом пространстве шнека.
Рисунок 7 – Эпюры скоростей расплава:
а – прямой поток; б – обратный поток; в – результирующий поток; h – расстояние между движущейся (шнек) и неподвиж-ной (цилиндр) поверхностями.
Если бы не было сопротивлений потока (например, при от-сутствии сеток и головки), то распределение скоростей V резуль-тирующего потока изобразилось бы рисунком 5-а, у поверхности шнека V = max, у неподвижной поверхности цилиндра V = 0. Это имело бы место в случае отсутствия сопротивления течению расплава.
При наличии сеток, оснастки, трения о поверхность цилинд-ра и шнека создается обратный поток, или противовоток (рис.5 б).
Результирующий поток, изображенный на рисунке 5- в, пред-ставляет собой сложение эпюр, приведенных на рисунке 5- а и 5- б.
При отсутствии сопротивления расплаву (сняты головка, сетки) давление P чуть больше атмосферного при максимальном сопротивле нии (заглушка вместо головки) P максимально, а величины прямого и обратного потоков равны. Часть материала перетекает в направлении противотока в зазор между гребнем шнека и поверхностью цилиндра.
|
Таким образом, производительность Q экструдера, с уче-том распределения скоростей различных потоков, описывается уравнением:
Q = QА – QB – QG (2)
где Q А, Q B, Q G – производительности экструдера по прямому потоку, противотоку и утечке расплава, соответственно.
В свою очередь, Q А, Q B, Q G – зависят от технологических параметров и конструкции экструдера:
Q=АN – (B+ G)P/ η (3)
где N – частота вращения шнека; P – давление на выходе из шнека (в конце зоны III); η – средняя вязкость расплава; A, B и G –постоянные коэффициенты, зависящие от геометрических параметров шнека.
A = (π2D2h sin φ cos φ) /2; B = (π Dh3sin2 φ) /12L;
G = (π 2D2 δ 3tg φ)/ 10 L e,
где: D – диаметр, L – длина, h – глубина нарезки; φ – угол подъема винтовой линии шнека; δ – зазор между гребнем и поверхностью цилиндра; е – ширина гребня шнека.
Для определения вязкости расплава по кривым течения необходимо рассчитать скорость сдвига в спиральном канале шнека:
ск =
[c-1] (4)
где: D – диаметр шнека, мм; h ср – средняя глубина канала в зоне дози-рования, мм; N – скорость вращения шнека, об/с; t – шаг нарезки шнека в зоне дозирования, мм
h ср = , h2 и h3 – глубина канала в начале и в конце зоны дозирования, мм.
Графическое изображение аналитической зависимости (3) представлено на рисунке 8 прямыми 1 и 2. Из рисунка следует, что при отсутствии сопротивлений течению расплава (Р = 0) экструдер работает как винтовой насос с максимальной произ-водительностью Q.
Если на выходе из экструдера стоит заглушка, т. е. прямой поток равен сумме обратного и потока утечек: АN = (B + G)P/ η, то в нем развивается максимальное давление Р, а Q = 0.
Анализируя уравнение (3) и значения коэффициентов А, B, G можно проследить влияние геометрических параметров шнека и свойств расплава полимера на производительность Q и харак-тер изменения Q от Р, т. е. угол наклона прямых 1 и 2 на рис. 8. Последнее имеет важное практическое значение.
Рисунок 8 – Зависимость производительности Q от
давления Р расплава на выходе из экструдера:
1, 2 – характеристики шнека; 3 – характеристика головки;
а и б – рабочие точки
При небольшом колебании Δ P (см. рисунок 6), которое может возникнуть при практической работе, последнее сказыва-ется на величине колебания ΔQ1 или ΔQ2. Чем больше ΔQ, тем больше пульсация расплава, т. е. больше неравномерность во времени скорости и выхода расплава. Это сказывается в первую очередь на разнотолщинности получаемых изделий.
Разнотолщинность тем больше, чем выше Δ Q. Из уравне-ния (3) легко показать, что при прочих равных условиях у экст-рудеров с большим L/D колебания ΔQ, т.е. пульсация, меньше, чем у экструдеров с меньшим L/D.
При равенстве D первый тип экструдера называется длин-ношнековым, второй – короткошнековым. Кроме того, увеличе-ние L способствует получению расплава более гомогенного, так как время воздействия на него шнека больше, чем в короткошне-ковых экструдерах. Изделия, получаемые из гомогенного рас-плава, обладают лучшими свойствами.
ОДНОШНЕКОВОГО ЭКСТРУДЕРА
Цель работы: Построение рабочей характеристики экструдера (зависимость производительности экструдера от давления перед формующей головкой).
Используемые материалы: Вязкая жидкость, моделирующая расплав полимера (глицерин, поливиниловый спирт, силиконо-вая жидкость)
Используемое оборудование: Модель одношнекового экст-рудера, снабженная датчиком давления и головкой с изменяе-мым проходным сечением; секундомер, воронка для залива рабочей жидкости; стакан для слива жидкости; мерный цилиндр.
Порядок выполнения работы:
1.Ознакомиться с устройством модели одношнекового экстру-дера. Выполнить эскиз модели с указанием основных геометри- ческих параметров шнека, определяющих производительность экструдера.
2.Подключить к электросети (220 V) через розетку привод моде-ли. Убедиться в свободном вращении шнека. Проверить возмож-ность свободного перемещения заслонки, регулирующей про-ходное сечение головки.
3.При вращающемся шнеке и незаполненном рабочем цилиндре откорректировать показания манометра, замеряющего давление перед головкой. Манометр должен показывать "0" при полнос-тью закрытой заслонке.
4. При вращающемся шнеке и полностью закрытой заслонке го-ловки установить стеклянную воронку в загрузочное окно рабо-чего цилиндра экструдера, под выходное отверстие головки подставить стакан для слива жидкости и заполнить рабочий ци-линдр жидкостью, моделирующей расплав полимера. Наблю-дать за изменением показаний манометра в процессе заполнения рабочего цилиндра. Отметить максимальное значение давления по манометру и записать его в таблицу 1. Повторить замеры трижды.
5. При вращающемся шнеке полностью открыть заслонку и, про-должая приливать в цилиндр рабочую жидкость, наблюдать за изменением показаний манометра. Записать в таблицу 1 устано-вившееся значение давления при полностью открытой заслонке. Вытекающую жидкость собирать в стакан.
Таблица 1 – Результаты экспериментального определения производительности установки.
№ п/п | Ширина зазора, м | Показания манометра, Па | Время отбо-ра порции жидкости, с | Расход жидкости, Q, м куб |
δ1,1; δ1,2, δ1,3… δ1ср | Р11, Р12, Р13 Р1ср | Q11, Q12, Q13 Q1 ср | ||
δ2,1; δ2,2, δ2,3 δ2ср | Р21, Р22, Р23 Р2ср | Q21, Q22, Q23 Q2 ср | ||
… | … | |||
δ 7,1; δ7,2, δ7,3 δ7ср | Р 71, Р 72, Р7, Р7ср | Q71, Q7,2, Q7,3 Q7 ср |
6. Изменяя положение заслонки (приоткрывая ее постепенно), записывать в таблицу 1 ширину проходного сечения головки (м) и показания манометра, ему соответствующие.
Подставить под головку мерный цилиндр и определить объем жидкости, вытекающей из головки за 30 сек (Q,cм3).
Величину проходного сечения головки изменять последо-вательно от 0 до 12 делений таким образом, чтобы в данном про-межутке получить 7 замеров.
Три раза (по 7 замеров, которые могут соответствовать разным значениям δi) определить изменение расхода и давления при изменении ширины щели и записать результаты.
По этим данным построить зависимости Q = f (δ i) и P = f (δ i) для каждой из трех серий измерений (рисунки 1 и 2). При этом значения δ i могут не совпадать в каждой серии измерений.
На полученных графиках найти геометрическим способом средние значения Q = f (δ i) и P = f (δ i), задав δ i, равными 0, 2, 4, 6, 8, 10 и 12 делениям.
Рисунок 1 – Результаты определения P = f (δ i),
Рисунок 2 – Результаты определения Q = f (δ i)
Рисунок 3 – Зависимость Q по шнеку от давления Р
7. Построить график зависимости расхода от давления для шне-ка модельной установки (рисунок 3). При этом значения Q и P для нанесения на график брать по усредненным кривым Q = f (δ i)
и P = f (δ i) при равных значениях зазора (рисунок 1 и 2).
8. Рассчитать теоретические производительности головок при давлениях, установленных в п. 7, для соответствующих раз-меров проходного сечения головки (δ i), по формуле:
Q гол = K●Р / η, (1)
где Р – давление перед головкой (показания манометра), Па
η – вязкость рабочей жидкости, Па с (для глицерина при 25 0С: динамическая вязкость η = 0,95 Па с, при 200 С η = 1,49 Па с; для индустриального масла ИП-40 при 25оС: кинематическая вязкость μ = 0,69 мм2/с и ρ = 0,888 г/см3).
К – коэффициент сопротивления головки, рассчитываемый для щелевой головки по формуле:
К= b●h3 / 12●L, (2)
где b – ширина канала, (зазор, δ изменяемый при выполнении работы), м.
h – высота канала, м (27 мм).
L – длина канала, м (150мм).
Полученные расчетные данные внести в таблицу 2.
9. По данным таблицы 1 построить для модели эксперименталь-ную зависимость расхода от давления перед головкой по шнеку и теоретическую по головке («Q – P» диаграмму, рисунок 4).
10. Определить экспериментальную рабочую точку экструдера (т. А на рисунке 4)
11. Рассчитать теоретическую производительность модельной установки по головке. При этом расчет производительности го-ловки вести, задавая произвольно 2 - 5 значений давления в интервале, установленном в п.7. Внести результаты расчета в таблицу 2 и построить зависимость «Qт – P» для головки.
Рисунок 4 – Рабочая диаграмма экструзионной установки.
1 – производительность по шнеку; 2 – производительность
по головке; т. А – рабочая точка экструдера
Использовать полученные значения Q э для построения как экспериментальной, а Q т теоретической рабочей характеристи-ки экструдера (количество расходных характеристик для голо-вок построить по указанию преподавателя).
Таблица 2 – Результаты определения теоретической производительности по шнеку и головке.
№ п\п | Ширина зазора, м | Давление, Па | Производи- тельность по шнеку м 3/с | Производи-тельность по головке, м 3/c |
12.Задавая давления в интервале, полученном в п. 7, и, исходя из геометрических параметров шнека модельной установки, рассчитать ее теоретическую производительность по шнеку, используя формулу:
Qт = А●N – В●Р/ η – С●P/ η, (3)
где η – вязкость рабочей жидкости, Па с
N – число оборотов шнека, об/с (0,55 об/с)
A, B и С – константы прямого, обратного потоков и пото-ка утечек, рассчитываемые по формулам:
A = (π2D2h sin φ cos φ) /2; (4)
B = (π Dh3sin2 φ) /12L; (5)
G = (π 2D2 δ 3tg φ)/ 10 L e, (6)
где m – число заходов шнека, m = 1
t – шаг винтовой нарезки шнека, м (20мм)
D – диаметр шнека, м (24 мм)
δ – зазор между гребнем шнека и корпусом цилиндра, м (δ = 0,5мм)
φ – угол подъема винтовой линии шнека, (18 град)
е – ширина гребня шнека, м (5 мм)
L – длина нарезной части шнека, м (190мм)
h – высота нарезки шнека, м (4 мм)
Результаты расчета внести в таблицу 2 и построить зависимость «QT – P» для шнека.
14. Графически определить теоретическое положение рабочей точки. Сопоставить экспериментальные и расчетные данные по производительности в рабочей точке. Указать причины, обус-ловливающие расхождение теоретических расчетов и экспери-ментальных данных.
15. Обсудить полученные экспериментальные данные, сравнить экспериментальную рабочую диаграмму экструдера и теорети- ческую, сделать выводы по результатам работы.
Вопросы для подготовки к работе и ее защите:
1. Рассмотреть процесс перемещения материала в рабочем ци-линдре экструдера и изменение его агрегатного состояния. Назвать основные факторы, влияющие на производительность экструдера.
2. Как влияет на производительность экструдера вязкость мате-риала, температура расплава, геометрические параметры шнека и головки?
3. Как изменится производительность экструдера, головки и уста-новки в целом при изменении вязкостных свойств материала, конфигурации головки, геометрических размеров каналов го-ловки при сохранении их конфигурации?
4. Рассчитать скорость вращения червяка, при которой обеспечи-вается заданное (по указанию преподавателя) значение произво-дительности и давления в головке.
5. Какое явление называется «пульсация расплава», как она влияет на качество изделий и как можно снизить пульсацию?
Список литературы к работе
1.Основы технологии переработки пластмасс /Под ред. Кулезнева В.Н. и Гусева В.К. – М.: Химия, 2006 – с. 372 – 418.
2.Раувендааль К. Экструзия полимеров. С-Пб.: Профессия,
2006. – 850 с.
3.Бортников В.Г. Основы технологии переработки пластических масс: Учебное пособие для вузов. – Л.: Химия,1983. – С.103 – 132.
4.Тадмор З., Гогос К. Теоретические основы переработки поли-меров. //Пер.с англ. – М.: Химия, 1984. – С 418 – 423;
С. 428 - 438.
5.Шембель А.С., Антипина О.М. Сборник задач и проблемных си-
туаций по технологии переработки пластмасс, Л.: Химия, 1990. – С. 9 – 30.
Приложение А.
Таблица 1 – Конструктивные параметры шнеков и значения средних градиентов скорости сдвига, рекомендуемые для переработки термопластов
Материал | Тип изделия | Тип сырья | ![]() | hзагр / hдозир | m в зоне дозиро-вания | m в зоне сжа- тия |
ПЭВП | трубы | грану-лы | 50 -110 | 3,7 – 4,35 | ||
листы | грану-лы | 100 -230 | 3,7 – 4,35 | |||
ПЭНП | пленки | грану-лы | 50 -110 | 3,7 – 4,35 | ||
трубы | грану-лы | 50 -110 | 3,7 – 4,35 | |||
Полипрпилен | все | грану-лы | 55 -110 | 4,35 | ||
ПВХ жесткий | все | грану-лы | 15 -40 | 2,7 - 3,1 | 5 - 6 | 5 - 6 |
ПВХ пластикат | все | грану-лы | 90 -210 | 3,35 – 4 | ||
Полистирол | грануляция | грану-лы | 100 -200 | 4 – 4,35 | ||
Ударопрочный ПС | листы | грану-лы | 50 -110 | 4 – 4,35 | ||
Полиакрилаты | листы | грану-лы | 40 -100 | 3,35 - 3,7 | ||
Полиамид 6,6 | все | грану-лы | 20 -110 | 4 – 4,35 |
Учебное издание
Ушакова Ольга Борисовна
О.Б. УШАКОВА
ПОСТРОЕНИЕ РАБОЧЕЙ ХАРАКТЕРИСТИКИ ОДНОШНЕКОВОГО ЭКСТРУДЕРА
Учебно-методическое пособие
для студентов, обучающихся по направлению
подготовки 18.03.01 «Химическая технология»
|
|
История создания датчика движения: Первый прибор для обнаружения движения был изобретен немецким физиком Генрихом Герцем...
История развития пистолетов-пулеметов: Предпосылкой для возникновения пистолетов-пулеметов послужила давняя тенденция тяготения винтовок...
Таксономические единицы (категории) растений: Каждая система классификации состоит из определённых соподчиненных друг другу...
Состав сооружений: решетки и песколовки: Решетки – это первое устройство в схеме очистных сооружений. Они представляют...
© cyberpedia.su 2017-2024 - Не является автором материалов. Исключительное право сохранено за автором текста.
Если вы не хотите, чтобы данный материал был у нас на сайте, перейдите по ссылке: Нарушение авторских прав. Мы поможем в написании вашей работы!