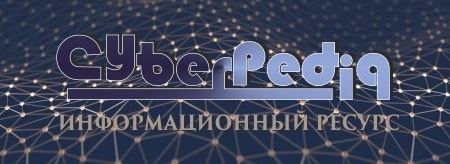
Механическое удерживание земляных масс: Механическое удерживание земляных масс на склоне обеспечивают контрфорсными сооружениями различных конструкций...
Индивидуальные и групповые автопоилки: для животных. Схемы и конструкции...
Топ:
Отражение на счетах бухгалтерского учета процесса приобретения: Процесс заготовления представляет систему экономических событий, включающих приобретение организацией у поставщиков сырья...
Генеалогическое древо Султанов Османской империи: Османские правители, вначале, будучи еще бейлербеями Анатолии, женились на дочерях византийских императоров...
Комплексной системы оценки состояния охраны труда на производственном объекте (КСОТ-П): Цели и задачи Комплексной системы оценки состояния охраны труда и определению факторов рисков по охране труда...
Интересное:
Лечение прогрессирующих форм рака: Одним из наиболее важных достижений экспериментальной химиотерапии опухолей, начатой в 60-х и реализованной в 70-х годах, является...
Распространение рака на другие отдаленные от желудка органы: Характерных симптомов рака желудка не существует. Выраженные симптомы появляются, когда опухоль...
Инженерная защита территорий, зданий и сооружений от опасных геологических процессов: Изучение оползневых явлений, оценка устойчивости склонов и проектирование противооползневых сооружений — актуальнейшие задачи, стоящие перед отечественными...
Дисциплины:
![]() |
![]() |
5.00
из
|
Заказать работу |
|
|
Возросшая в 1960-х гг. конкуренция подтолкнула промышленные предприятия к постоянному улучшению потребительских свойств товаров и технологий по их изготовлению, что вызвало необходимость непрерывного обновления ассортимента выпускаемой продукции, ее производство в небольших количествах (малыми сериями). Традиционные автоматизированные поточные производства, не могли обеспечить требуемую для этого гибкость/легкость перехода производства с одного вида продукции на выпуск другого, так как их пространственно-временная конфигурация имела ограниченное число степеней свободы (вариантов комбинации отдельных звеньев производственной технологической цепочки) и, соответственно, узкую товарную номенклатуру.
В целях увеличения технических возможностей реконфигурации (перестройки) технологического процесса, рабочие места/оборудование в цехах механической обработки деталей стали объединять в функциональные группы, без определенных связей, по типам выполняемых деталеопераций в виде однородных технологических участков (например, группы токарных, фрезерных, сверлильных и др. станков), которые позволяли создавать на основе их многофункциональной матричной структуры виртуальные технологические цепочки с неограниченным числом и разнообразной последовательностью соединения (комбинацией) неоднородных звеньев (см. рис. 1.3). При такой организации производственного процесса переход на выпуск новых и/или модернизированных изделий может осуществляться без трудоемкой перестановки специализированного оборудования, ограничиваясь его переналадкой. Поскольку процесс пространственно-временного сопряжения деталеопераций, в отличие от поточных методов производства, носит слабо согласованный (нечеткий) характер, то последовательность, режимы обработки деталей и алгоритм их перемещения от операции к операции задаются специально разрабатываемыми технологическими маршрутами. Последние представляют собой виртуальные пространственно-временные сети сопряженных технологических операций по обработке деталей, которые перемещаются между операциями партиями по сложным маршрутам с помощью специальных транспортных средств (краны, тележки, авто/электропогрузчики и т.п.)14.
|
Рис. 1.3. Функционально-технологическая (матричная) топология непоточного производства
(Кликните по изображению для его увеличения)
Преимуществом данного подхода к пространственно-временной организации технологического процесса в сравнении с поточным методом является повышение его гибкости, недостатками — увеличение времени последовательной обработки деталей партиями, которая предполагает многократное выполнение станком операций одного вида (А), и затем, многократное выполнение операций другого вида (В), после осуществления требуемой для этого переналадки оборудования (рис. 1.4).
Рис. 1.4. Последовательный (а) и параллельный (б) способ обработки партий деталей А и В
(Кликните по изображению для его увеличения)
Функционально-матричная организация технологического процесса обеспечивала возможность выпуска широкой номенклатуры изделий в небольшом количестве (серями), но существенно усложняла обслуживание заказчиков готовой продукции, запросы которых могли отличаться от производимых в текущий момент времени партий серийных изделий. Это было вызвано тем, что требование гибкости производства вступало в противоречие с существовавшей на тот момент технологической базой индустриальной экономики, основу которой составляло дорогостоящее, сверхточное (прецизионное) оборудование15.Необходимость постоянной загрузки, большие затраты времени и средств на его переналадку вели к увеличению размера партий деталей, одновременно запускаемых в производство, что неизбежно вызывало межоперационное пролеживание комплектующих в составе крупных партий либо в ожидании окончания их обработки (А), либо в очередях на обработку нескольких партий деталей для различных серийных изделий (В). Это влекло за собой простои оборудования на других технологических операциях, которые вызывали длительные перерывы на узловой сборке из-за отсутствия необходимых комплектующих. Как следствие, неритмичная работа сборочных линий, рост незавершенного производства и замедление оборота активов, а также неспособность оперативно реагировать на колебания спроса, неизбежно приводили к разорению машиностроительных предприятий в условиях конкурентной рыночной экономики.
|
Непоточные методы организации технологического процесса нашли широкое применение в серийном и единичном производстве, для которых характерны периодическая или относительно редкая повторяемость изготовления изделий и их производство в различных объемах (от крупных партий до отдельных единиц), определяющие в конечном итоге степень организации (структуру) производственного процесса и виды движения предметов труда [63, 97].
Крупносерийное/серийное производство, отличающееся относительно постоянным или регулярным выпуском ограниченной номенклатуры изделий в большом количестве (сериями), имеет простую хорошо организованную структуру (см.: рис. 1.5
Рис. 1.5. Структура непоточного производства: заготовительные участки/цехи, организованные по технологическому принципу (а); предметные участки поточного типа, применяемые на обрабатывающей и сборочной фазах производства (б).
Заготовительные участки/цехи организованы по технологическому принципу, а обрабатывающая и сборочная фазы производства осуществляются преимущественно предметными участками и цехами поточного типа (например, участки корпусных деталей, зубчатых коле, валов и т.п.). На предметных участках применяется специализированные станки (протяжные, токарные с копирами и гидросуппортами для обработки ступенчатых валов и т.п.), которые располагаются по ходу технологического процесса по аналогии с поточными методами организации производства, что сокращает время перемещения деталей между операциями и длительность производственного цикла в целом; на остальных участках преобладает групповая расстановка однотипного универсального оборудования со специальной оснасткой. Централизованно осуществляемая детальная разработка технологических процессов по повторяющимся сериям изделий снижает/исключает потребность в рабочих с универсальной квалификацией.
|
Мелкосерийное/единичное производство, для которого характерен нерегулярный выпуск небольшого количества или отдельных единиц изделий широкой номенклатуры, отличающихся значительным удельным весом нестандартных оригинальных деталей и узлов, характеризуется разнообразием работ, выполняемых на одном рабочем месте, большой трудоемкостью и длительностью операционного цикла изготовления продукции. Неустойчивость номенклатуры выпускаемых изделий, ее разнотипность, предопределяют ограниченное использование в данном типе производства стандартизованных конструкторских решений и типизированных деталеопераций, а также требуют гибкости/легкости перехода производства с одного вида изделий на выпуск другого. Последнее требует, чтобы пространственно-временная конфигурация производственной системы имела как можно большее число степеней свободы, которым в реальных условиях соответствуют различные варианты комбинации отдельных звеньев производственно-технологической цепочки. Поэтому мелкосерийное и единичное производство имеет сложную плохо организованную структуру по всем фазам производственного процесса, сформированную по технологическому принципу с разнообразными слабоструктурированными связями между смежными технологическими операциями — маршрутами движения деталей. Последнее обусловливает последовательное возвратно-встречное движение предметов труда между смежными технологическими операциями и, соответственно, большую длительность производственного цикла. Рабочие места, не имеющие постоянной специализации, загружаются неоднородной редко повторяющейся работой и/или разнообразнымидеталеоперациями, которые закрепляются за группой одномодельного (взаимозаменяемого) оборудования. Поскольку заказы на изготовление единичных изделий, как правило, не повторяются, то организационно-экономическая подготовка производства выполняется укрупнено. Детализация и определение очередности выполнения технологических операций по заказам, относящиеся к функции производственного планирования, осуществляются децентрализовано инженернотехническим персоналом производственных участков и цехов (мастерами, технологами) на основе текущих приоритетов [42, 63].
|
Из этого следует, что основные потери в непоточном производстве, обусловлены неполной загрузкой/простоями оборудования и возвратными движениями (петлянием) деталей по участку/цеху, которые происходят по причинам организационного характера и связаны с качеством составления календарного плана работ. Как показывает производственная практика, эффективно решить эту сложную управленческую задачу с помощью концепции и инструментария централизованного планирования, в частности с применением аппарата теории расписаний, — не представляется возможным по причинам объективного характера, в том числе с применением современных компьютерных технологий и мощных вычислительных систем.
Инертность мышления сторонников традиционной модели индустриального производства не позволяла преодолеть ограниченность ее концепции и базисных принципов, тем самым, инициируя безуспешные попытки с их стороны разрешить противоречия и проблемы данного способа производства методами и инструментами централизованного управления взамен поиска новых подходов к обеспечению технологической гибкости и оптимальному регулированию производственных систем16.
1.3. Система централизованного планирования и управления
Повышение гибкости производственных систем, увеличение степеней их свободы требует постоянной балансировки производственных ресурсов с периодически меняющейся программой выпуска продукции. В практике управления индустриальным производством это сводится к составлению расписания технологических операций с последовательной обработкой деталей партиями, поочередно выполняемых на различных участках производственного процесса. Теоретически, в целях уменьшения времени обработки очередей и сокращения производственного цикла, может быть сформирована минимальная по продолжительности выполнения последовательность операций, обеспечивающая непрерывную и согласованную работу всех производственных участков (рис. 1.6, таблица 1.1)17. Однако на практике выполнить это условие не представляется возможным, поскольку число вариантов последовательного запуска партий растет в месте с размером и сложностью номенклатуры изделий18. Последнее является причиной затяжных организационнотехнологических сбоев, которые приводят к сдвигу/совпадению операций по времени, в результате чего возникают простои оборудования и/или пролеживание деталей в очередях на обработку ввиду его занятости [104, 145].
|
Табл. 1.1
N9 работы п/п | Первое задание | Второе задание | ||
Порядок прохождения | Время выполнения работы, ед. | Порядок прохождения | Время выполнения работы, ед. | |
А Б В Г Д | А Г В Б Д | |||
Итого | Итого |
Рис. 1.6. Определение оптимальной последовательности обработки партий деталей А и В
Широко распространенный в массовом/непоточном производстве способ их устранения, компенсирующий недостатки планирования, предполагает принудительную координацию работы всех элементов производственной системы, которая осуществляется централизованно диспетчерской службой субъектом/системой оперативного управления (СУ), направляющей на производственные участки команды по корректировке очередности/приоритета выполнения операций исходя из текущей производственной обстановки (рис. 1.7).
Рис. 1.7. Процесс централизованного управления производством
(Кликните по изображению для его увеличения)
Результаты выполнения отдельных операций поступают через систему контроля и используются СУ для изменения (корректировки) состава и порядка выполнения производственного плана, исходя из фактических результатов работы участков, их текущего состояния и наличия необходимых ресурсов (см.: обратная связь). Основная проблема заключается в том, что данный способ организации управления операциями (при всей его кажущейся простоте) требует наличия в СУ полной непрерывно обновляемой в режиме реального времени (динамической) модели производственного процесса, учитывающей колебания рынка, а также непрерывной и надежной связи/коммутации субъекта и объектов управления. В условиях индустриального производства реализовать эти требования в полной мере не представляется возможным, поскольку моделью производственного процесса в этом случае является жесткийпланграфик (программа) выпуска изделий, низкая оперативность корректировки которого, несоизмерима с быстротой изменения параметров внутренней среды предприятия и конъюнктуры рынка. В результате неадекватности (неполноты) условно-статичной модели производственно-технологического процесса возникают и накапливаются ошибки в системе планирования, снижается эффективность управления, и растут средние издержки производства [73, 78, 145]19.
Основным недостатком централизованной системы управления массовым производством является несогласованная работа обособленных технологических участков в общем процессе изготовления продукции. Смежные участки по производству деталей функционируют независимо друг от друга, производя и выталкивая в межоперационное пространство (на промежуточный склад) продукцию в соответствии с планом-графиком, составленным планово-диспетчерской службой предприятия на основе предположений о том, что понадобится каждому производственному микропроцессу, игнорируя при этом его состояние и текущие потребности в деталях и комплектующих. Действуя в рамках плана, каждый участок самостоятельно устанавливает объемы партий и темп производства исходя из собственного (локального) представления задачи выполнения плановых заданий по производству продукции и экономической эффективности, а не общесистемного видения всего производственного процесса (глобальной оптимизации потока создания ценности). В такой ситуации предыдущие процессы будут иметь тенденцию выпускать изделия, которые не нужны последующим процессам (их потребителям) в настоящее время. Это означает выпуск одних изделий в большем количестве, чем это нужно для осуществления требуемых на данный момент технологических операций и, соответственно, нехватку других, что приводит к вынужденным простоям оборудования и потерям рабочего времени.
Для устранения этого несоответствия создаются большие запасы изделий на промежуточных (межоперационных) складах и запасы готовой продукции для быстрой отгрузки потребителям, а также отводится больше времени на выполнение заказа, чем это требуется по технологическому регламенту. Сборка партиями означает, что поставляемые комплектующие также будут потребляться партиями, что приведет к раздуванию объема запасов на промежуточных (межоперационных) складах выше по потоку движения изделий. При этом вариабельность процесса конечной сборки сильнее сказываться на вариабельности предшествующих сборке технологических операций, запасы для которых необходимо увеличивать кратно вверх по потоку. Возникает потребность в резервных мощностях, отсутствие которых приводит к возникновению в производственном процессе так называемых «узких мест», которые существенно ограничивают производительность и скорость реакции системы массового производства на изменение условий внешней среды (запросы потребителей). Как следствие этого, увеличиваются объемы незавершенного производства и продолжительность технологического цикла со всеми вытекающими из этого организационно-экономическими последствиями 20.
С целью преодоления недостатков централизованного способа управления, усиливающих отрицательный эффект масштаба индустриального производства в современных условиях, крупные машиностроительные корпорации разрабатывают автоматизированные системы управления. Тем не менее, это не приводит к кардинальному улучшению положения: в случае успешности их внедрения кривая средних долгосрочных издержек сначала падает, а затем, начиная с момента исчерпания действия положительного эффекта так называемого информационного реинжиниринга технологического процесса, становится более или менее горизонтальной [69]. Проблема заключается в том, что централизация управления была необходима и достаточна для обеспечения непрерывности стационарного процесса массового производства стандартной продукции, и совершенно не предназначена для организации и регулирования нестационарных потоков изделий и работ, характерных для гибкого рыночноориентированного производства. Именно это обстоятельство лишает предприятия индустриального типа свойства адаптации к меняющейся среде, делает их нежизнеспособным механизмом в новых реалиях конкурентной рыночной экономики.
Особенности балансировки планов и ресурсов машиностроительного предприятия
В традиционном/классическом понимании централизованное управление производством представляет собой непрерывный процесс выработки системой планирования (субъектом управления) регулирующих воздействий, которые по каналам информационных коммуникаций передаются на технологические участки (объекты управления) для обеспечения их слаженной работы в заданном режиме в соответствии с производственной программой (целевой функцией). С этой целью служба планирования предприятия при получении заказов составляет графики работ на определенный период (сутки/неделя/месяц) для всех этапов производственного процесса (изготовление заготовок, деталей и узлов, сборка изделий) с использованием автоматизированной системы планирования, которая рассылает инструкции каждому производственному участку о том, что надо сделать в предстоящий плановый период. Поскольку производственный процесс, как правило, не идет в точном соответствии с разработанным планом, то осуществляется наблюдение за ходом производства с помощью отчетов производственных участков о фактическом выполнении плановых заданий, на основании которых осуществляется корректировка плана и повторная передача инструкций/сменных заданий производственным участкам (рис. 1.8).
Основным инструментом производственного планирования выпуска конечного продукта является расписание работ, которое представляет собой алгоритм пространственно-временного распределения (балансировки) оборотных ресурсов предприятия между технологическими операциями по их обработке. В машиностроении распределение ресурсов осуществляется путем определения календарных сроков запуска деталеопераций и их закрепление за различными группами оборудования, на основании производственной программы и так называемой компоновочной структуры или дерева продукта, которую часто называют «ведомостью/спецификацией материалов».
Рис. 1.8. Процесс оперативного управления производством
Спецификация содержит полное описание состава продукта, с указанием деталей и узлов, а также технологической последовательности его производства, на основании которой, с учетом плановых нормативов на осуществление деталеопераций, определяются календарные сроки, необходимые для изготовления этих элементов [104, 145]. Данный пространственно-временной алгоритм (программа распределения, основанная на компоновочной структуре изделия и времени необходимом для изготовления его компонентов) указывает, что именно, посредством чего и когда необходимо производить. Для этого используются специально разработанные визуальные отображения предметов труда и операций по их обработке на t -временной оси, именуемые в организационной науке календарными планами-графиками. Планы-графики представляют собой графические/табличные (матричные) формы, в которых указываются точные количества деталей и материалов, необходимые для производства конечных изделий, а также календарные даты распределения/выдачи заказов на их изготовление по рабочим местам/группам оборудования (см. рис. 1.9).
Рис. 1.9. Дерево структуры и календарный план производства продукта Т21
Детали должны изготавливаться в соответствии с производственным графиком и поступать на сборочный участок по мере готовности. Расписание или календарный график работ должен обеспечить в этом случае одновременное поступление на финишную сборку всех деталей и узлов входящих в изделие точно к заданному сроку, путем опережающего запуска в производство деталей, имеющих более длительный цикл изготовления. По этой причине в единичном (преимущественно опытном/инструментальном) производстве вместо календарных планов-графиков изготовления изделий разрабатывается так называемые сетевые графики (циклограммы) работ по изготовлению изделий, в которых определяются исполнители работ по заказам (цеха/участки-изготовители), виды работ/обработки и инструмент, а также осуществляется закрепление технологических операций за оборудованием. Наличие/загрузка производственных мощностей, необходимых для выполнения работ непосредственно в расчет не принимается, равно, как не определяется очередность работ, выполняемых на каждом рабочем месте. Планирование, таким образом, ограничивается лишь проверкой/исключением перегрузки наиболее важных (задающих ритм процесса производства) групп рабочих мест/оборудования и оценкой времени выполнения заказа, которая выполняется сложением ожидаемой продолжительности операционного цикла (длительность выполнения подготовительных и основных работ), предполагаемой задержки деталей в очереди на обработку и времени доставки необходимых материалов и комплектующих изделий (рис. 1.10).
Рис. 1.10. Циклограмма процесса изготовления изделия c расчетом критического пути
Поскольку все производственные системы характеризуются ограниченными ресурсами (материалами и мощностями по их обработке), составление производственной программы как инструмента (алгоритма) их оптимального сочетания является сложной интеллектуальной (плановоаналитической) задачей. Сложность заключается в отыскании последовательности выполняемых операций обработки предметов труда и их закрепления за рабочими местами/оборудованием, согласно которой изготовление деталей, необходимых для сборки конечного изделия, будет выполняться непрерывно и слаженно (равномерно по времени). При одновременном изготовлении в цехе нескольких серий изделий (заказов) на рабочее место в ограниченный промежуток времени может поступить несколько заданий, трудоемкость (объем/продолжительность) которых может превышать установленную/располагаемую мощность (производительность) оборудования, что приводит к запаздыванию выполнения отдельных деталеопераций. Для устранения этой проблемы устанавливается очередность выполнения однородных технологических заданий, закрепленных за одним рабочим местом, посредством которой обеспечивается равномерность загрузки оборудования. В качестве прогнозно-аналитического инструментария планирования (распределения) загрузки оборудования используются соответствующие хронологические таблицы (ведомости деталеопераций), по аналогии с ведомостями деталей, позволяющие оценить вклад тех или иных производственных заданий/деталеопераций в суммарную загрузку рабочих мест на определенную контрольную дату. При этом для расчетов используются нормативы трудоемкости/времени выполнения технологических операций, проводимых на соответствующих группах оборудования, которые сравниваются с располагаемым фондом рабочего времени для каждого рабочего места. Однако отображение всех строк вышеуказанных операционных ведомостей приводит к очень большому размеру рабочего поля таблиц, так как для анализа оптимальности загрузки оборудования необходимо одновременно иметь/обрабатывать данные по нескольким (или всем) изготавливаемым изделиям (группам планирования)22. Подавляющее число строк в таблице не может быть физически рассмотрено специалистами-плановиками. По этой причине в современных системах планирования/управления используется искусственный интеллект вычислительных машин, основанный на скоростном выполнении простейших арифметических вычислений и сравнении/связывании их результатов посредством примитивного аппарата формальной (математической) логики. Применение ЭВМ позволяет осуществлять параллельное планирование одновременно по нескольким планово-учетным единицам (деталеоперациям/группам планирования/заказам), т.е. в различных масштабах их отображения, начиная от крупных единиц, например, ведущих/сложных деталей (узлов и агрегатов), к более подробному анализу распределения во времени процесса изготовления составляющих их простых деталей. Это обеспечивается благодаря автоматически поддерживаемым ЭВМ связям между строками таблиц, что предоставляет возможность суммировать/получать в итоге все необходимые данные по загрузке той или иной единицы оборудования.
При нехватке производственной мощности решение задачи календарного планирования предусматривает корректировку графика, в процессе которой выравнивается загрузка мощности и исключаются возможные запаздывания при выполнении заданий. Контрольными точками являются моменты начала/окончания операций обработки на конкретных единицах оборудования, которые позволяют анализировать их текущую загрузку, выявлять наиболее загруженные группы машин и агрегатов и принимать решения/меры по нормализации их текущей загрузки путем переноса времени запуска невыполненных деталеопераций на более позднее время или их переназначением (путем изменения расцеховки) на другие группы оборудования, а также изменением интенсивности/сменности работы. Для выполнения этой задачи программа оперативного планирования на ЭВМ должна быть оснащена модулем планирования потребностей в производственных мощностях, который позволяет автоматически выполнять корректировку плана, приводя его в соответствие с доступным уровнем мощности, цель которой заключается в том, чтобы распределить загрузку оборудования равномерно, не выходя при этом за ограничение мощности (рис. 1.11). Источником входных данных для автоматизированной системы планирования служит основной план производства. Программа «разворачивает» все детали, компоненты и прочие ресурсы, необходимые для его выполнения.
Рис. 1.11. Диаграмма загрузки рабочего центра23
Планирование загрузки производственной мощности начинается с анализа заданий, предусмотренных для выполнения операционными маршрутными картами. В карте указываются, какое задание и куда нужно направить, связанные с ним конкретные операции, а также нормативное время пусконаладочных работ и время выполнения заказа в расчете на одно изделие. Все эти показатели используются при вычислении общего объема работ на каждом рабочем центре/станции/установке. Задача равномерной загрузки производственной мощности заключается лишь в правильном построении графика выполнения заданий, т.е. в отыскании такой последовательности работы с ними, чтобы все они выполнялись вовремя в соответствии с установленными правилами приоритетного планирования/выполнения заказов с учетом ограничения мощности. В соответствии с окончательным вариантом календарного плана, отражающим потребности в материалах и мощностях, в производственную систему выдаются заказы. Далее наступает производственный этап, в ходе которого выполняются заказы, осуществляются мониторинг и сбор данных о ходе производства и выполнении заказов. Сведения о любых изменениях в производстве, использовании мощностей и материалов передаются обратно в систему, с помощью встроенной функции обратной связи, посредством которой осуществляется сравнение входной (плановой) и выходной (фактической) мощности/производительности рабочих центров, корректировка графиков и диспетчеризация.
К сожалению, прогнозный расчет плана/программы производства объективно не может обеспечить точное и полное его соответствие (адекватность) реальному производственному процессу и гарантировать отсутствие перегрузки отдельных групп оборудования (возникновения «узких мест» и организационно-технологических сбоев). Это объясняется тем, что нормативная трудоемкость/расчетное время выполнения операций в подавляющем большинстве случаев не совпадает с реальной продолжительностью обработки деталей24. По этой причине расчет носит прогностический (предположительный) характер и содержит существенные погрешности, что в совокупности с изменениями производственной обстановки неизбежно приводит к необходимости оперативного вмешательства (регулирования) производственного процесса посредством контроля выполнения и корректировки плановых заданий. Ограниченный интеллект ЭВМ не позволяет автоматизировать задачу регулирования производства, поэтому она выполняется плановиками (планово-производственным или диспетчерским отделом) в интерактивном (полуавтоматическом) режиме работы ЭВМ путем произвольного назначения календарного времени запуска деталеопераций. В свою очередь, интерактивный режим работы требует создания специального интеллектуального интерфейса ЭВМ — визуальной наглядно-образной формы графического представления плановых и фактических данных о ходе производственного процесса для их последующего сравнения и ручной корректировки плана производства. Таким графоаналитическим представлением (моделью) процесса производства, является одна из разновидностей столбцовых диаграмм, которая в производственном/операционном менеджменте известна как линейный планграфикГанта, с помощью которого планируют и отслеживают ход выполнения работ (рис. 1.12).
Рис. 1.12. Учетно-плановый график Ганта
График Ганта представляет собой линейную (аналоговую) модель, отображающую на t -временной оси последовательный (и параллельный, если работы независимы) набор всех работ, который позволяет подсчетом по горизонтали определить продолжительность всего комплекса работ, а подсчетом по вертикали — календарную потребность в персонале, оборудовании и материалах. Представление технологического процесса с помощью графиков Ганта позволяет планировать производство, получать и анализировать соответствующие показатели и на этой основе принимать прогнозные решения, направленные на оптимизацию объемов и сроков производства работ. Однако линейные модели не способны отразить основные свойства производственного процесса как системы, поскольку в них отсутствуют динамические связи, определяющие зависимости одной работы от другой. Проблема заключается в неадекватности условно-статичной аналоговой модели производственного процесса, представленной планом-графиком (программой) выпуска изделий, низкая оперативность корректировки которого, несоизмерима с быстротой изменения параметров внутренней и внешней среды предприятия. В результате неадекватности (неполноты) условно-статичной модели производственнотехнологического процесса, ошибок коммутации между элементами операционной системы и сбоев в работе производственно-технологических участков неизбежно усиливается рассогласование фактической работы операционной системы и нормативными параметрами и показателями плана. Это приводит к накоплению (наслоению) ошибок в процессе оперативного планирования и управления, нарушению координации работы производственных участков, и, как следствие, снижению производительности и эффективности работы предприятия. Представление процесса производства в виде детерминированной (статичной) системы базируется на следующем. Предполагается, что длительность производственного цикла детали является величиной строго определенной (неизменной), трудоемкость изготовления изделия распределяется равномерно в пределах каждой стадии производственного цикла и не меняется во времени, а общая длительность изготовления заказа зависит от его индивидуальных характеристик (сложности состава технологических процессов, средней трудоемкости операции на различных стадиях производства и т.п.).На самом деле длительность циклов/ трудоемкость изготовления деталей/заказов (интенсивность работ) является величиной вероятностной и зависит от характеристики того набора деталей/заказов, которые запланированы к производству на один плановый период и от особенностей организации процесса производства на предприятии (средний коэффициент закрепления операций за рабочим местом, размер партий деталей, управление движением узких мест в производстве). Игнорирование динамического характера производства приводит к тому, что в случае любого изменения производственной ситуации линейная модель перестает отображать реальный ход работ/событий. Поскольку в процессе корректировки планов в нее невозможно оперативно внести существенные изменения, то это приводит в конечном итоге к разбалансировке планов и ресурсов предприятия, дефициту деталей на сборке и, как следствие нарушению плановых сроков исполнения заказов (Э.М. Голдрат, 1987; О.Г. Туровец, 2002). По данной причине линейные модели не нашли широкого применения в качестве инструмента оперативного управления сложным производством или комплексом работ.
В большей степени несовершенство прогнозно-аналитических методов планирования проявляется в малосерийном и единичном производстве, так как на момент составления производственного плана выпуска опытной/уникальной продукции отсутствуют календарно-плановые нормативы трудоемкости/времени выполнения операций, которые являются центральным звеном теории расписаний и присущего ей метода календарного планирования. Важнейшим из нормативов является расчетная техническая или ожидаемая (статистически усредненная) норма времени выполнения работы/технологической операции в определенных организационных условиях, которая служит исходным пунктом для определения производительности труда, и широко используется при оперативно-производственном планировании. Сущность нормирования заключается в исследовании состава операций и статистических измерений (хронометрирования) продолжительности их отдельных элементов в увязке с производственными возможностями и эксплуатационными характеристиками применяемых при этом оборудования, инструмента и приспособлений, результаты которых сводятся в специальные справочно-расчетные таблицы, номограммы и аналитические зависимости. Необходимо учитывать, что в единичном производстве применяются укрупненные нормативы времени изготовления типовых деталей определенной группы, отличающихся размерами. При этом основой определения нормы времени является систематизированные данные о фактических затратах труда/времени на данный вид работы/операции и личный опыт нормировщика. Существенный недостаток нормирования заключается в большой погрешности укрупненной нормативной базы, которая по объективным причинам не может быть точной и своевременно обновляемой из-за отсутствия технических возможностей учета всех условий (факторов) динамичного процесса унифицированного единичного производства и их аналитической увязки со статистическими распределениями продолжительности выпол<
|
|
Опора деревянной одностоечной и способы укрепление угловых опор: Опоры ВЛ - конструкции, предназначенные для поддерживания проводов на необходимой высоте над землей, водой...
Индивидуальные и групповые автопоилки: для животных. Схемы и конструкции...
Адаптации растений и животных к жизни в горах: Большое значение для жизни организмов в горах имеют степень расчленения, крутизна и экспозиционные различия склонов...
Поперечные профили набережных и береговой полосы: На городских территориях берегоукрепление проектируют с учетом технических и экономических требований, но особое значение придают эстетическим...
© cyberpedia.su 2017-2024 - Не является автором материалов. Исключительное право сохранено за автором текста.
Если вы не хотите, чтобы данный материал был у нас на сайте, перейдите по ссылке: Нарушение авторских прав. Мы поможем в написании вашей работы!