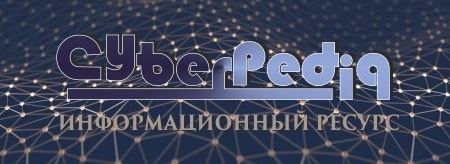
Общие условия выбора системы дренажа: Система дренажа выбирается в зависимости от характера защищаемого...
Автоматическое растормаживание колес: Тормозные устройства колес предназначены для уменьшения длины пробега и улучшения маневрирования ВС при...
Топ:
Характеристика АТП и сварочно-жестяницкого участка: Транспорт в настоящее время является одной из важнейших отраслей народного...
Организация стока поверхностных вод: Наибольшее количество влаги на земном шаре испаряется с поверхности морей и океанов...
Теоретическая значимость работы: Описание теоретической значимости (ценности) результатов исследования должно присутствовать во введении...
Интересное:
Средства для ингаляционного наркоза: Наркоз наступает в результате вдыхания (ингаляции) средств, которое осуществляют или с помощью маски...
Уполаживание и террасирование склонов: Если глубина оврага более 5 м необходимо устройство берм. Варианты использования оврагов для градостроительных целей...
Аура как энергетическое поле: многослойную ауру человека можно представить себе подобным...
Дисциплины:
![]() |
![]() |
5.00
из
|
Заказать работу |
|
|
Последовательное (цепное) расположение рабочих мест по ходу технологического процесса в непосредственной близости друг от друга позволяет перемещать детали между смежными операции мелкими партиями (3–5 шт.) или поштучно с помощью специального межоперационного (самодвижущегося и гравитационного) транспорта, а также механизировать/автоматизировать стандартизированные процессы обработки, загрузки/выгрузки и транспортировки предметов труда. Выравнивание продолжительности (синхронизация) операций по времени путем подбора пропорционального количества рабочих мест и мощности оборудования в соответствии с трудоемкостью обработки предметов труда обеспечивает параллельность (одновременность) выполнения работ, ритмичность и непрерывность производственного процесса. Все это в совокупности определяет высокую степень пространственно-временной организации (балансировки) процесса массового поточного производства, которая устраняет непроизводительные затраты труда и времени на перемещение и пролеживание деталей у рабочих мест в ожидании обработки, а, следовательно, значительно сокращает межоперационные запасы (незавершенное производство) и общее время изготовления продукции, повышая экономическую эффективность производства [97, 104].
В дополнение необходимо отметить, что высокий уровень организации массового производства позволяет изначально, на этапе проектирования предприятия, задавать устойчивую во времени (детерминированную) пространственно-временную структуру технологического процесса и, соответственно, автоматизировать/роботизировать большинство технологических операций, что объективно исключает необходимость в детальном технико-экономическом планировании и оперативном регулировании как способе перманентного определения наиболее оптимального сочетания (балансировки) ресурсов и задания эффективного алгоритма работы производственной системы предприятия. Относительно простая задача управления в этом случае сводится к нормативно-календарным расчетам такта/ритма работы поточной линии, числа рабочих мест и их загрузки, цикловых и складских заделов, а также организации технического обслуживания групп рабочих мест/станций/установок, их бесперебойного снабжения инструментом, материалами, заготовками и комплектующими изделиями с целью предотвращения незапланированных простоев и обеспечения ритмичной, взаимосвязанной работы всех участков поточной линии.
|
Оборотной стороной перечисленных преимуществ является жесткая детерминированность структуры подобных производственных систем, существенно ограничивающая их гибкость/адаптивность к изменениям внешней среды. Сетевая топология производственного процесса, включающая (предустанавливающая) распределенные пространственно-временные алгоритмы (схемы) движения предметов труда между звеньями технологической цепочки (набор и интенсивность операций обработки), задается на этапе организационно-технологической подготовки поточного производства, как это представлено на рис. 1.2.
Рис. 1.2. Сетевая топология поточного реконфигурируемого производства
(Кликните по изображению для его увеличения)
При различных вариантах развития производственной ситуации (например, при необходимости перехода производства с одного вида продукции на другой при изменении спроса; в случае простоя оборудования по причине ремонта, отсутствия сырья и комплектующих изделий) выполняется перенастройка/реконфигурация производственно-технологической цепочки/линии, связанная с перенесением потоков от одних звеньев к другим. При этом перенастройка ограничена количеством предусмотренных (возможных) схем переориентации материальных потоков. Однако, как будет показано далее, историческое развитие рынка потребителей требовало частой смены ассортимента продукции, наделенной особыми/отличительными свойствами, и, соответственно, выпуска разнообразной продукции малыми партиями/сериями. В этих условиях массовое поточное производство стало постепенно терять свои преимущества, и во второй половине XX века перед промышленностью возникла актуальная научно-техническая задача обеспечения гибкости производственных систем при условии сохранения ими преимуществ широкой механизации/автоматизации и высокого темпа изготовления изделий13.
|
Исследовательские и опытно-конструкторские работы по созданию гибких автоматизированных производств осуществлялись в период 1970–1990-х гг. в направлении повышения функциональной избыточности (степеней свободы) производственных систем на основе широкого использования многофункциональных станков и агрегатов с числовым программным управлением, промышленных роботовманипуляторов, транспортеров (робокаров) и автоматизированных складов, а также управляющих устройств на базе мини/микро-ЭВМ. В таких системах автоматизированы все операции. По программе выполняется загрузка заготовок в оборудование и выгрузка деталей из него. По заданной программе происходят обработка заготовок и изготовление изделий. Эти программы могут быть легко изменены или скорректированы. Автоматически происходит смена инструментов и вспомогательных материалов, а также их хранение, накопление и перемещение от одного оборудования к другому. Управление работой всей системы происходит централизованно от ЭВМ с помощью математического программного обеспечения. Автоматизированные производства быстро и без больших затрат времени и средств переналаживаются на выпуск разнообразной продукции, в пределах технических возможностей производственной системы, посредством замены программы технологического процесса, записанной в памяти ЭВМ. В своем законченном идеальном виде гибкие автоматизированные производства (ГАП) являются высшей, наиболее развитой формой автоматизации производственного процесса, которая позволяет совместить высокую производительность и универсальность (гибкость) в программноуправляемом/перенастраиваемом многофункциональном оборудовании, что открывает, по мнению их разработчиков, огромные возможности для интенсификации производства [10].
|
Тем не менее, создание полностью автоматизированного многопредметного (гибкого) поточного производства, отличающегося разнообразием выпускаемой продукции, осложняется необходимостью централизованной детальной инженерной подготовки, а также требует точной сквозной синхронизации технологических операций на потоке, которые должны выполняться различными станками и агрегатами в составе автоматической системы машин, как единый непрерывный процесс работы поточной линии. Исключение из автоматизированного производственного процесса живого труда и, соответственно, интеллектуального потенциала рабочих, способных не только быстро перенастраивать и ресинхронизировать технологический процесс, но и оперативно устранять периодически возникающие сбои в производственной системе, обусловили высокую чувствительность автоматического процесса производства к неслаженной работе оборудования. Неполадки в работе отдельных агрегатов вызывают рассогласование работы и полную остановку гибкой автоматизированной линии (ГАЛ), что приводит к значительным потерям по всему циклу производства и снижает реальную эффективность его автоматизации [63]. Ко всему прочему, игнорирование творческой инициативы рабочих, постоянно занятых в производственном процессе и, соответственно, способных более эффективно осуществлять его технологическую доводку и развитие, существенно ограничили возможности адаптации таких производственных систем к меняющимся условиям рынка и создания на их основе новых конкурентных преимуществ. В итоге это делает процесс оперативной подготовки и ресинхронизации (адаптации) гибкого автоматизированного/ роботизированного поточного производства очень трудоемким/затратным и, соответственно, экономически неэффективным в условиях масштабного производства, работающего в нестабильной экономической среде конкурентного рынка.
Учитывая данные недостатки гибкие автоматизированные линии, обладающие высокой производительностью и определенным уровнем гибкости/адаптивности, ограниченной техническими возможностями существовавших на то момент промышленных и информационных технологий, — нашли свое применение в непоточном/дискретном серийном производстве, которое представляло собой очередную ступень эволюционного развития производственных систем по завершении эпохи массового производства и потребления.
|
|
Историки об Елизавете Петровне: Елизавета попала между двумя встречными культурными течениями, воспитывалась среди новых европейских веяний и преданий...
Кормораздатчик мобильный электрифицированный: схема и процесс работы устройства...
История развития пистолетов-пулеметов: Предпосылкой для возникновения пистолетов-пулеметов послужила давняя тенденция тяготения винтовок...
Индивидуальные и групповые автопоилки: для животных. Схемы и конструкции...
© cyberpedia.su 2017-2024 - Не является автором материалов. Исключительное право сохранено за автором текста.
Если вы не хотите, чтобы данный материал был у нас на сайте, перейдите по ссылке: Нарушение авторских прав. Мы поможем в написании вашей работы!