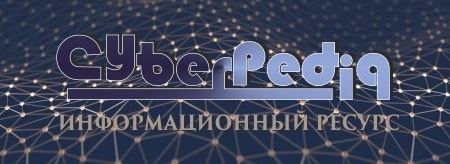
Опора деревянной одностоечной и способы укрепление угловых опор: Опоры ВЛ - конструкции, предназначенные для поддерживания проводов на необходимой высоте над землей, водой...
История создания датчика движения: Первый прибор для обнаружения движения был изобретен немецким физиком Генрихом Герцем...
Топ:
Устройство и оснащение процедурного кабинета: Решающая роль в обеспечении правильного лечения пациентов отводится процедурной медсестре...
Методика измерений сопротивления растеканию тока анодного заземления: Анодный заземлитель (анод) – проводник, погруженный в электролитическую среду (грунт, раствор электролита) и подключенный к положительному...
Отражение на счетах бухгалтерского учета процесса приобретения: Процесс заготовления представляет систему экономических событий, включающих приобретение организацией у поставщиков сырья...
Интересное:
Отражение на счетах бухгалтерского учета процесса приобретения: Процесс заготовления представляет систему экономических событий, включающих приобретение организацией у поставщиков сырья...
Берегоукрепление оползневых склонов: На прибрежных склонах основной причиной развития оползневых процессов является подмыв водами рек естественных склонов...
Мероприятия для защиты от морозного пучения грунтов: Инженерная защита от морозного (криогенного) пучения грунтов необходима для легких малоэтажных зданий и других сооружений...
Дисциплины:
![]() |
![]() |
5.00
из
|
Заказать работу |
|
|
Конструирование элементов корпуса.
Смазывание, смазочные устройства и уплотнения
Руководитель: Выполнили:
Преподаватель: Ст. гр. 8-40-1
Хмурович Ф.Л. Тихонова А.А.
Вострокнутова Ю.В.
.
Ижевск 2007
Конструирование крышек подшипников и стаканов
Конструирование стаканов
Стаканы обычно выполняют из чугунного литья марки СЧ 15, реже из стали. Толщину стенки δ, диаметр d и число z винтов крепления стакана к корпусу принимают в зависимости от диаметра D отверстия стакана под подшипник по следующим зависимостям:
D мм... До 52 Св. 52до80 Св. 80до 120 Св. 120 до 170
δ, мм.... 4...5 6...8 8...10 1О...12,5
d, мм..... 6 6 8 10
Z......... 4 4 6 6
Толщину упорного буртика δ1, и толщину фланца δ2 (рис. 1.4) принимают δ1 ≈ δ; δ2 ≈1,2δ
Высоту t упорного буртика назначают по той же зависимости, что и высоту заплечика вала h (табл. 1.6), диаметр буртика D1 = D – 2t.
Диаметр фланца Dф следует выполнять минимальным. Для этого принимают с ≈d: h = (1,0... 1,2)d;Dф = Dа + (4,0... 4,4) d, где d — диаметр винта (рис. 1.4).
Таблица 1.6
r, мм | 0,5 | 1,0 | 1,5 | 2,0 | 2,5 | 3,0 | 3,5 | 4,0 |
t, мм | 1,0 | 1,8 | 2,5 | 3,0 | 4,0 | 4,8 | 5,5 | 6,5 |
![]() |
Рис. 1.4. Стаканы подшипников
Иногда на наружной поверхности стакана делают проточку для уменьшения длины посадочного участка (см. рис. 1.4, а). Глубину проточки принимают равной 1,0 мм.
Длину посадочных участков принимают равной ширине кольца подшипника. Канавки в отверстиях стаканов делать не следует, поскольку выполнять их сложнее, чем на наружной поверхности. Кроме того, они затрудняют установку подшипников.
Стаканы для подшипников вала конической шестерни перемешают при сборке для регулирования осевого положения конической шестерни. В этом случае посадка стакана в корпус — H7js6. Другие стаканы после их установки в корпус остаются неподвижными, для них применяют посадки Н7/k6 или Н7/m6.
|
Смазывание, смазывающие устройства и уплотнения
Смазку машин применяют в целях защиты от коррозии, снижения коэффициента трения, уменьшения износа, отвода тепла и продуктов износа от трущихся поверхностей, демпфирования динамических нагрузок и, следовательно, снижения шума и вибраций. От правильности выбора смазочных материалов, методов смазки и способов уплотнений в значительной степени зависят работоспособность и долговечность машин.
Выбор смазочных материалов и условий смазки основывается на расчетах (например, расчет подшипников скольжения) или на экспериментальных данных и опыте эксплуатации (например, выбор типа смазки для зубчатых и червячных передач).
Смазочные материалы
В качестве смазочных материалов используют жидкие нефтяные и синтетические смазочные масла, пластичные (старое название — консистентные) и твердые смазки, а также воду, воздух и другие газы. Наибольшее распространение имеют нефтяные смазочные масла и пластичные смазки. Сырьем для получения нефтяных смазочных масел является мазут, который получают из нефти после отгона светлых продуктов — бензинов и керосинов.
Н е ф т я н ы е м а с л а разделяют на масла общего назначения — индустриальные и специальные — турбинные, автомобильные, автотракторные, трансмиссионные, авиационные и др. Специальные масла отличаются от общих наличием особых свойств, необходимых для соответствующих областей применения.
Важнейшей характеристикой жидких смазок, используемой при их подборе, является вязкость. Вязкость характеризует сопротивление отдельных слоев жидкости относительному сдвигу. При подборе масел учитывают также температуру застывания, температуру вспышки, наличие примесей и т. д. Работоспособность смазки зависит также и от способности защищать поверхности трения от заедания (схватывание и перенос металла) и задиров (глубокие и широкие борозды в направлении скольжения).
|
Для улучшения эксплуатационных свойств смазок применяют различные присадки.
Синтетические смазочные жидкости (гликоли, силиконы, фторуглероды и хлоруглероды) применяют при особых условиях эксплуатации, например при высоких или низких температурах, при которых нефтяные масла неработоспособны.
Пластичные смазки представляют собой масла, загущенные мылами, парафином или другими веществами. При малых нагрузках эти смазки проявляют свойства твердых тел (сохраняют первоначальную форму и не растекаются), при определенных критических нагрузках деформируются (текут подобно жидкости), а при снятии нагрузки снова обретают свойства твердых тел.
Пластичные смазки хорошо удерживаются в механизмах и не требуют сложных уплотнений. Вязкость смазок в гораздо меньшей степени зависит от температуры, чем вязкость масел, на основе которых они сделаны. В узлах с интенсивным тепловыделением пластичные смазки не применяются из-за неспособности отбирать тепло от трущихся поверхностей. Водостойкие смазки лучше, чем масла, защищают поверхности от попадания воды.
Т в е р д ы е с м а з к и (графит, дисульфид молибдена) применяют в виде порошков или паст также при особых условиях эксплуатации — при низких или высоких температурах, глубоком вакууме, в случаях, когда не допускается загрязнение среды жидкими или пластичными смазками.
Выбор смазочного материала.
Преимущественное применение имеют масла. Принцип назначения сорта масла следующий: чем выше окружная скорость колеса, тем меньше должна быть вязкость масла и чем выше контактные напряжения в зацеплении, тем большей вязкостью должно характеризоваться масло. Поэтому требуемую вязкость масла определяют в зависимости от контактного напряжения и окружной скорости колес по табл. 2.1.
По табл. 2.2 выбирают марку масла для смазывания зубчатых и червячных передач. В табл. 2.3 приведены рекомендуемые марки смазочных масел для волновых передач.
Таблица 2.1. Рекомендуемая кинематическая вязкость масел
Контактные напряжения σН, Н/мм2 | Рекомендуемая кинематическая вязкость, мм2/с При окружной скорости, м/с | ||
до 2 | 2…5 | св. 5 | |
Для зубчатых передач при 400 С | |||
До 600 | |||
600 - 1000 | |||
1000 - 1200 | |||
Для червячной передачи при 1000 С | |||
До 200 | |||
200 - 250 | |||
250 - 300 |
Таблица 2.2. Кинематическая вязкость масел
|
Марка масла | Кинематическая вязкость, мм/с2 |
Для зубчатых передач при 400 С | |
И – Л – А – 22 И – Г – А – 32 И – Г – А – 46 И – Г – А – 68 | 19 – 25 29 – 35 41 – 51 61 – 75 |
Для червячной передачи при 1000 С | |
И – Г – С – 220 И – Т – С – 320 Авиационное МС – 20 Цилиндровое 52 | 20,5 |
Таблица 2.3. Рекомендуемые марки масел для волновых передач
Обозначение индустриальных масел состоит из четырех знаков, каждый из которых обозначает: первый (И) - индустриальное, второй - принадлежность к группе по назначению (Г - для гидравлических систем, Т - тяжелонагруженные узлы), третий - принадлежность к группе по эксплуатационным свойствам (А - масло без присадок, С - масло с антиокислительными, антикоррозионными и противоизносными присадками, Д - масло с антиокислительными, антикоррозионными, противоизносными и притивозадирными присадками), четвертый (число) - класс кинематической вязкости.
Из пластичных смазочных материалов наиболее часто применяют ЦИАТИМ-201, Литол-24, Униол-2.
Смазывание подшипников
Подшипники смазывают тем же маслом, что и детали передач. Смазывание их другим смазочным материалом применяют редко (если требуется защитить подшипники от продуктов износа деталей передач).
При картерном смазывании передач подшипники смазывают брызгами масла. При окружной скорости колес v > 1 м/с брызгами масла покрыты все детали передач и внутренние поверхности стенок корпуса. Стекающее с колес, валов и со стенок корпуса масло попадает в подшипник.
Для свободного проникания смазки полость подшипника должна быть открыта внутрь корпуса, а для обеспечения лучшей циркуляции смазки подшипниковые гнезда желательно дренажировать.
При расположении рядом с подшипником шестерни, наружный диаметр которой меньше наружного диаметра подшипника, выжимаемое из зацепления масло при значительных скоростях обильным потоком выбрасывается в подшипник. Тогда для защиты подшипников от излишнего количества смазки, необходимо применять внутренние уплотнения в виде маслосбрасывающих колец (защитных шайб), изображенных на рис. 1.6, а, б.
|
Внутренние уплотнения одновременно защищают подшипник от попадания в него посторонних частиц и продуктов износа.
Рис.1.6. Смазка подшипников качения
При малых скоростях и в случаях, когда опоры удалены от направления потоков смазки, необходимо предусматривать специальные смазочные устройства.
Полость подшипника, смазываемого пластичными смазками, должна быть отделена от внутренней части корпуса. Для этого могут быть использованы уплотнения по рис. 1.7, а, б, в.
Уплотнения по рис. 1.7, а, б не рекомендуется применять на вертикальных валах.
Размеры внутренней полости корпуса под пластичную смазку должны иметь глубину с каждой стороны подшипника примерно в 1/4 его ширины. Смазку набивают в подшипник через крышку (рис. 1,7, в)или подают под давлением через масленку под шприц (рис. 1.7 а, б,). Рекомендуется, чтобы объем смазки не превышал 1/3-1/2 объема свободного пространства полости.
а) б) в)
Рис.1.7. Смазка подшипников качения
Если разбрызгиваемая смазка попадает на верхнюю часть корпуса, ее можно собирать в специальные сборники и по канавкам, расположенным на нижней части корпуса в плоскости разъема, подавать в полость подшипника
Смазочные устройства
Для подачи в подшипники пластичного смазочного материала можно применять пресс-масленки (рис. 1.9). Смазочный материал подают под давлением специальным шприцем. Для удобства подвода шприца в некоторых случаях применяют переходные штуцера 1. Основные параметры пресс-масленки указаны в таблице 2.5
Рис.1.9. Пресс – масленки
Таблица.2.5 Основные параметры пресс - масленки
При работе передач продукты изнашивания постепенно загрязняют масло. С течением времени оно стареет, свойства его ухудшаются. Браковочными признаками служат увеличенное кислотное число, повышенное содержание воды и наличие механических примесей. Поэтому масло, залитое в корпус редуктора или коробки передач, периодически меняют. Для замены масла в корпусе предусматривают сливное отверстие, сливные отверстия закрывают пробками с цилиндрической или конической рёзьбой (табл. 2.6). Надежнее уплотняет коническая резьба, поэтому ей следует отдавать предпочтение. Под пробки с цилиндрической резьбой необходимо ставить уплотняющие алюминиевые или медные прокладки. Пробку целесообразно совмещать с магнитным уловителем (табл. 2.7) для улавливания ферромагнитных частиц, являющихся продуктом износа и в свою очередь действующих на рабочие поверхности трущихся деталей как абразив.
Табл. 2.6. Пробки для маслоспускных отверстий
|
Табл. 2.7.Магнитные уплотнения
Во время работы передачи воздух внутри корпуса нагревается что при замкнутой системе приводит к повышению давления и утечке масла через уплотнения валов и разъемы. Чтобы предотвратить это, применяют вентиляцию корпуса с помощью отдушины. Простейшие отдушины представляют собой пробки с отверстиями (рис. 1,10,).
![]() |
Рис.1.10.Отдушины
Для наблюдения за уровнем масла в корпусе устанавливают:
· маслоуказатели крановые (рис. 1.11),
· маслоуказатели круглые и удлиненные из прозрачного материала (рис. 1.12);
· маслоуказатели жезловые (щупы) (рис. 1.13).
Исполнение щупа по рис. 1.13, б вызывает некоторые технологические трудности при формовке корпуса и сверлении наклонного отверстия. Поэтому исполнение щупа по рис. 1.13, а и особенно рис. 1.13, в предпочтительно.
Круглые маслоуказатели (рис. 1.12) удобны для корпусов, расположенных достаточно высоко над уровнем пола.
Рис.1.11. Маслоуказатели крановые
Рис.1.12
Маслоуказатели круглые и
удлиненные из прозрачного
материала
Рис.1.13
Маслоуказатели жезловые
Уплотнительные устройства
Уплотнительные устройства
Уплотнительные устройства применяют для предохранения от вытекания смазочного материала из подшипниковых узлов, а также для защиты их от попадания извне пыли и влаги. Ниже приведены наиболее распространенные в машиностроении уплотнения.
Манжетные уплотнения | |
![]() ![]() | Широко применяют при смазывании подшипников жидким маслом и при окружной скорости вала до 20 м/с Каркас придает манжете жесткость и обеспечивает ее плотную посадку в корпусную деталь без дополнительного крепления. Браслетная пружина стягивает уплотняющую часть манжеты, вследствие чего образуется рабочая кромка шириной b= 0,4... 0,6 мм. (г), плотно охватывающая поверхность вала. На рис. в показаны браслетная пружина и способ ее соединения. Манжеты, предназначенные для работы в засоренной среде, выполняют с дополнительной рабочей кромкой 4 (рис., б), называемой "пыльником". Нормальная работа манжеты возможна лишь при смазывании поверхностей трения |
Основные параметры манжетного уплотнения (табл. 2.8)
![]()
|
Установка манжеты
Манжету обычно устанавливают открытой стороной внутрь корпуса (рис. 1.14, а). К рабочей кромке манжеты в этом случае обеспечен хороший доступ смазочного масла. 95 %-ный ресурс для манжет - не менее 3000 ч.
Рис.1.14
При подаче шприцем пластичного смазочного материала давление внутри подшипниковой камеры может быть очень высоким. Чтобы не повредить манжету, ее устанавливают в этом случае рабочей кромкой наружу (рис. 1.14, б). Тогда при повышении давления смазочный материал отогнет кромку манжеты, и избыток его вытечет наружу.
Рис.1.1.4
При высоком уровне масла ставят рядом две манжеты (рис. 1.15, а). При запыленной внешней среде также ставят две манжеты или одну с пыльником (рис. 1.15, б).
Рис. 1.15
Свободное пространство между манжетами, а также между рабочими кромками манжеты и пыльника заполняют при сборке пластичным смазочным материалом (ЦИАТИМ-221).
Торцовые уплотнения.
При смазывании подшипников жидким маслом в последнее время получили распространение очень эффективные уплотнения по торцовым поверхностям. Однако применение их сдерживается вследствие конструктивной сложности, значительных размеров и относительно высокой стоимости. Конструкция одного из них приведена на рис. 1.16.
Рис.1.16
1, 2 - уплотнительных колец
3 - пружины.
Кольцо 1 изготовляют из антифрикционного материала марок АМС-1, 2П-1000-Ф, а кольцо 2 - из ста ли марок 40Х, ШХ15,закаленной до высокой твердости. Кольцо 2 устанавливают на валу с натягом.
Ширину b поверхности трения кольца 1 принимают при диаметре вала (мм) свыше 20 до 40 - 3 мм, свыше 40 до 80 - 4 мм и свыше 80-5 мм. Ширину поверхности трения кольца 2 делают больше b на 2... 4 мм. Рабочие поверхности уплотнительных колец должны иметь отклонения от плоскостности не более 0,9 мкм, а шероховатость Ra 0,16 мкм. С помощью пружины 3 создают на уплотняющей поверхности давление 0,05... 0,15 Н/мм2.
Кольцо 1 снабжают дополнительным, так называемым статическим, уплотнением 4. Статическим уплотнением чаще всего служит резиновое кольцо круглого сечения. Размеры резиновых колец принимают (рис. 1.17): диаметр сечения d2 = 4,6 мм; диаметр отверстия d1 = D - 8 мм. Здесь D - диаметр (мм) отверстия уплотняемого сопряжения, который принимают из ряда чисел:
36, 38, 40, 42, 43, 44, 45, 46, 48, 50, 52, 53, 55, 56, 58, 60, 62, 63, 65, 66, 68, 70,71,72,73, 75, 76, 78, 80, 82, 83, 85, 86, 88, 90, 92, 95, 98,100.
Форма канавки для резинового кольца дана на рис. 1.17; размеры
рис. 1.17 резиновые кольца. канавки: b = 5,6 мм; d3 = (D- 7,4) мм.
Применяются так же уплотнение упругими стальными шайбами (рис. 1.18), которые применяют при скорости скольжения до 6 м/с и смазывании подшипников любым смазочным материалом.
Толщина шайб в зависимости от их диаметрального размера составляет а = 0,3... 0,6 мм. Торцовая рабочая грань шайб выступает за их плоскость на с = 0, 5... 0,6 мм, что создает после закрепления шайб достаточную силу прижатия рабочей грани к торцу кольца подшипника. Размеры стальных уплотнительных шайб приведены в табл.2.9.
Рис.1.18 Уплотнение упругими стальными шайбами
![]() |
Щелевые (рис. 1.19, а, б) и лабиринтные (рис. 1.19, в) уплотнения создают сопротивление протеканию жидкости. Это узкие щели, радиальные и осевые выточки (лабиринты) сложной формы. Уплотнения надежно защищают подшипники от грязи и пыли при смазывании их любым смазочным материалом, не имеют трущихся деталей, применимы практически при любой окружной скорости
Рис. 1.19. Щелевые и лабиринтные уплотнения
Формы канавок показаны на рис. 1.19, а и б; их размеры (мм) принимают по таблице 2.18
Таблица 2.18. Формы канавок щелевых и лабиринтных уплотнений
Диаметр вала d | 20...50 | 50...80 | 80...120 |
b | 2,0 | 3,0 | 4.0 |
е | 0,2 | 0,3 | 0.4 |
r | 1,5 | 2,0 | 2.5 |
Зазоры щелевых и лабиринтных уплотнений целесообразно заполнять пластичной смазкой, создающей дополнительный жировой заслон для попадания на подшипник извне пыли и влаги.
Для повышения уплотняющего эффекта различные виды уплотнений комбинируют. На рис. 1.19, в показана комбинация лабиринтного и щелевого уплотнений.
В случае применения пластичной смазки (при ресурсном смазывании) подшипниковые узлы должны быть изолированы от внутренней полости во избежание вымывания пластичной смазки жидкостной, применяемой для смазывания зацепления. В этом случае подшипниковый узел закрывают маслосбрасывающим кольцом (рис. 1.20). Кольцо устанавливают с внутренней стороны корпуса редуктора так, чтобы гребенка наружного диаметра выходила за торец подшипникового гнезда на 1... 2 мм; зазор между наружной поверхностью кольца и корпусом (стаканом) равен приблизительно 0,2 мм; D0 =— 0,2 мм, где D — диаметр подшипникового гнезда; а = 6... 9 мм; t = 2... 3 мм. Размер b равен высоте бурта вала. Размеры l и с выбирают из условий конструкции.
Рис. 1.20. Маслосбрасывающие устройства
Конструирование элементов корпуса.
|
|
Таксономические единицы (категории) растений: Каждая система классификации состоит из определённых соподчиненных друг другу...
Папиллярные узоры пальцев рук - маркер спортивных способностей: дерматоглифические признаки формируются на 3-5 месяце беременности, не изменяются в течение жизни...
Механическое удерживание земляных масс: Механическое удерживание земляных масс на склоне обеспечивают контрфорсными сооружениями различных конструкций...
Индивидуальные очистные сооружения: К классу индивидуальных очистных сооружений относят сооружения, пропускная способность которых...
© cyberpedia.su 2017-2024 - Не является автором материалов. Исключительное право сохранено за автором текста.
Если вы не хотите, чтобы данный материал был у нас на сайте, перейдите по ссылке: Нарушение авторских прав. Мы поможем в написании вашей работы!