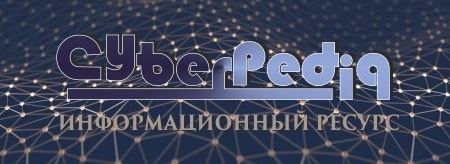
История развития пистолетов-пулеметов: Предпосылкой для возникновения пистолетов-пулеметов послужила давняя тенденция тяготения винтовок...
Биохимия спиртового брожения: Основу технологии получения пива составляет спиртовое брожение, - при котором сахар превращается...
Топ:
Оценка эффективности инструментов коммуникационной политики: Внешние коммуникации - обмен информацией между организацией и её внешней средой...
Проблема типологии научных революций: Глобальные научные революции и типы научной рациональности...
Интересное:
Как мы говорим и как мы слушаем: общение можно сравнить с огромным зонтиком, под которым скрыто все...
Отражение на счетах бухгалтерского учета процесса приобретения: Процесс заготовления представляет систему экономических событий, включающих приобретение организацией у поставщиков сырья...
Влияние предпринимательской среды на эффективное функционирование предприятия: Предпринимательская среда – это совокупность внешних и внутренних факторов, оказывающих влияние на функционирование фирмы...
Дисциплины:
![]() |
![]() |
5.00
из
|
Заказать работу |
|
|
РД 153-34.1-003-01.
«Сварка, термообработка и контроль трубных систем котлов и трубопроводов при монтаже и ремонте энергетического оборудования».
Настоящий руководящий документ определяет технологию сборочно-сварочных работ, термической обработки сварных стыков труб, а также объем и порядок контроля и нормы оценки качества сварных соединений; он охватывает все виды сварки, применяющиеся при монтаже и ремонте энергетического оборудования и трубных систем котлов и трубопроводов
1.1. Руководящий документ (РД) предназначен для организаций, осуществляющих монтаж и ремонт трубопроводов и трубных систем паровых и водогрейных котлов независимо от параметров рабочей среды, а также изготовление трубопроводов с рабочим давлением до 2,2 МПа (22 кгс/см2) и температурой не более 425 °С и отдельных элементов котлов.
Требования к подготовке кромок и сборке
6.1.4. Концы труб из углеродистых и низколегированных сталей разрешается обрабатывать кислородной, плазменно-дуговой или воздушно-дуговой резкой с последующей зачисткой кромок режущим или абразивным инструментом до удаления следов огневой резки. Подготовленные к сборке кромки должны быть без вырывов, заусенцев, резких переходов и острых углов.
6.2.1. Конструкции сварных соединений должны быть указаны в проектно-конструкторской документации. Рекомендуемый мин.зазор в стыке при подготовке труб с разделкой Тр-2 под РДС - 1±0,5
Основные рекомендуемые конструкции стыков св. соединений даны в табл. 6.2
6.2.4. Непосредственно перед сборкой изготовленные под сварку кромки и прилегающие к ним поверхности деталей должны быть.зачищены до металлического блеска и обезжирены. Ширина зачищенных участков должна быть не менее 20 мм с наружной и не менее 10 мм с внутренней стороны детали. Перед установкой штуцера (трубы) в коллектор или трубопровод поверхность вокруг отверстия должна быть зачищена на Ѕ 15-20 мм со стороны наложения сварного шва.
|
3.6. Блоки (узлы) трубопроводов и поверхностей нагрева котлов, в которых элементы соединены только прихватками или корневым швом, запрещается перемещать, транспортировать, подвергать воздействию каких-либо нагрузок во избежание образования трещин в швах, а также оставлять незаваренными на срок более одних суток.
6.3.4. К качеству прихваток предъявляются такие же требования, как и к сварному шву. Прихватки, имеющие недопустимые дефекты следует удалять механическим способом.
6.3.5. В стыках, собираемых без подкладных колец, число прихваток и их протяженность зависят от диаметра труб и должны соответствовать следующим нормам:
Диаметр труб, мм | До 50 | Свыше 50 до 100 | Свыше 100 до 426 | Свыше 426 |
Число прихваток по периметру | 1 – 2 | 1 – 3 | 3 – 4 | Через 300 – 400 мм |
Протяженность одной прихватки, мм | 5 – 20 | 20 – 30 | 30 – 40 | 40 – 60 |
Высота прихваток должна быть равна:
при их выполнении РДС на стыках труб с толщиной стенки S = 3 мм и менее – толщине стенки трубы; с S более 3 до 10 мм – (0,6 – 0,7) S, но не менее 3 мм; с S более 10 мм – 5 – 6 мм;
6.3.1. Прихватки на месте пересечения швов не допускаются
16.3.3. Зазор между свариваемыми плавниками независимо от способа сварки должен быть
не менее 1,5 и не более 3 мм.
6.2.5. Разность внутренних диаметров стыков труб, собираемых и свариваемых на остающемся подкладном кольце должна быть не более 2мм зазор между кольцом и внутренней поверхностью элемента не более 1 мм.
Требования к сварочным материалам
4.1.1. Для РДС стыков трубопроводов и котлов из углеродистых, низколегированных и высоколегированных сталей необходимо применять электроды, удовлетворяющие требованиям ГОСТ 9466, 9467, 10052 Марку электродов следует выбирать в зависимости от марки свариваемой стали.
|
Для сварки:
- труб поверхностей нагрева из сталей 12Х18Н10Т и 12Х18Н12Т используют электроды ЦТ-26, ЭА-400/10У, ЛЭЗЭА-400/10У, ЭА-400/10Т, ЦТ-26М, ЦТ-15, ЛЭЗЦТ-15, ЦТ-15-1, ЦТ-15К
- продольных швов по плавникам газоплотной панели из стали 12Х2М1 - электроды типа Э-09ХМ.
- стыков плавников труб газоплотной панели котла, гребней и накладок в узле разъема газоплотных панелей электроды УОНИ 13/55 (тип электрода Э50А) Æ 3мм,
- труб из стали 15Х1М1Ф – электроды марки ЦЛ -39,
- труб из стали 12Х1МФ, работающих при температуре до 510 градС – электроды марки ЦУ – 2Х, трубопроводов и элементов котлов из 12Х1М1Ф, работающих при температуре среды до 570 град С.
6.2.9. Для сварки корневых слоев шва стыков труб на остающемся подкладном кольце используют электроды диаметром 2,5 – 3 мм.
3.10. На заводе, монтажном (ремонтном) участке необходимо оборудовать в теплом помещении склад (кладовую) для электродов, сварочной проволоки и флюса. В нем должна поддерживаться температура не ниже 15 °С при относительной влажности не более 50%. На складе (или в другом подходящем месте) должны быть установлены печь для прокалки электродов при температуре до 400 °С и сушильный шкаф с температурой 80-115 °С, обеспечивающие потребность организ. в электродах.
Требования к сварке
К сварке допускаются аттестованные сварщики.
3.12. Место сварки и термообработки необходимо защитить от ветра, сквозняков и атмосферных
осадков и обеспечить первичными средствами для тушения.
6.4.1. Необходимость и температура подогрева стыковых соединений перед прихваткой и сваркой при положительной температуре окружающего воздуха регламентируется данными табл. 6.3.
Таблица 6.3
Температура подогрева стыков труб перед прихваткой и
сваркой дуговыми способами при положительной температуре окружающего воздуха
#G0Марка стали свариваемых деталей | Номинальная толщина свариваемых деталей, мм | Температура подогрева, °С | |
Ст2, Ст3, Ст3Г, Ст4, 08, 10, 15Л, 20, 20Л | До 100 включительно Свыше 100 | - 100-150 | |
25Л, 10Г2 | До 60 включительно | - | |
Свыше 60 | 100-150 | ||
15ГС, 16ГС, 17ГС, 14ГН, 16ГН, 09Г2С, 10Г2С1, 17Г1С, 17Г1СУ, 14ХГС | До 30 включительно Свыше 30 | - 100-150 | |
20ГСЛ | До 30 включительно | - | |
Свыше 30 | 150-200 | ||
12MX, 15XM | До 10 включительно | - | |
Свыше 10 до 30 включительно | 150-200 | ||
Свыше 30 | 200-250 | ||
12Х1МФ*, 12Х2М1, 20ХМЛ | До 10 включительно | - | |
* Для стыков труб из стали 12Х1МФ с толщиной стенки 11-14 мм температypa подогрева должна быть 100-150 °С. | |||
Свыше 10 до 30 включительно | 200-250 | ||
Свыше 30 | 250-300 | ||
20ХМФЛ, 15Х1М1ФЛ, 15Х1М1Ф-ЦЛ, 15Х1М1Ф | До 10 включительно Свыше 10 | - 300-350 | |
12Х2МФСР, 12Х2МФБ | До 6 включительно | - | |
Свыше 6 | 300-350 | ||
Примечание. Аргонодуговую сварку корневой части шва стыков труб из стали 15Х1М1Ф с толщиной стенки более 10 мм следует выполнять с подогревом 200-250 °С, из других марок стали - без подогрева.
|
Таблица 6.4
Требования к температуре окружающего воздуха при сварке и
прихватке элементов котлов и трубопроводов
#G0Сталь свариваемых элементов | Номинальная толщина металла, мм | Минимальная температура окружающего воздуха, °С |
Ст2, Ст3, Ст3Г, Ст4, 08, 10, 20 | Независимо | -20 |
15Л, 20Л, 25Л, 20ГСЛ, углеродистая сталь с содержанием углерода более 0,24% | Независимо | -10 |
10Г2, 09Г2С, 10Г2С1, 15Г2С, 16ГН, 14ГН, 14ХГС, 17Г1С, 17Г1СУ, 15ГС, 16ГС,17ГС | ![]() | -20 -10 |
12МХ, 15ХМ, 12Х1МФ | ![]() | -15 -10 |
15Х1М1Ф, 15Х1М1Ф-ЦЛ, 12Х2МФСР, 12Х2МФБ, 12Х2М1, 10Х9МФБ (ДИ 82-Ш) | ![]() | -10 |
20ХМЛ, 20ХМФЛ, 15Х1М1ФЛ, 12Х11В2МФ, 20Х13, 13Х11Н2В2МФ, 20Х12ВНМФ, 18Х12ВМБФР, ХН35ВТ | Независимо | |
12Х18Н12Т, 12Х18Н10Т, 31Х19Н9МВБТ, 10Х13Г12БС2Н2Д2 | Независимо | -20 |
Таблица 7.1
Рекомендуемые значения сварочного тока для электродов различных диаметров
#G0Покрытие электрода | Диаметр электрода, мм | Ток, А |
Основное (электроды УОНИ-13/55, ЦУ-5, ТМУ-21У, ТМЛ-3У, ТМЛ-1У, ЦЛ-39 и др.) | 2,5 3,0 | 70-90 90-110 |
4,0 | 120-170 | |
5,0 | 170-210 | |
Рутиловое (электроды ОЗС-4, АНО-6 и др.) | 2,5 | 70-90 |
3,0 | 90-130 | |
4,0 | 140-190 |
6.5.2.Перерыв в процессе сварки низколегированных теплоустойчивых сталей перлитного и мартенситно-ферритного классов не допускается
6.5.9.Металл в зоне сварного соединения труб поверхностей нагрева с толщиной стенки 6 мм из стали 12Х1МФ при температуре окружающего воздуха -10 град С должен быть просушен и прогрет с доведением его температуры до положительной.
16.1.4. Сварку продольных швов по плавникам, вварку уплотнительных вставок и гребенок из хромомолибденованадиевых и хромомолибденовых сталей (12Х1МФ, 12Х2М1 и др.) следует производить с предварительным подогревом мест сварки до 150-200 °С на ширину не менее 50 мм по обе стороны от места наложения шва. независимо от способа сварки и марки свариваемой стали:
|
при РДС - электродами Э50А (УОНИ-13/55, ЦУ-5, ТМУ-21У) диаметром не более 4 мм;
16.4.1. Для приварки гребенок и накладок в узле разъема применяются электроды типа Э50А независимо от марки стали труб и уплотняющих элементов.
7.1.7. Неповоротные (вертикальные и горизонтальные) стыки труб диаметром 219 мм и более могут сваривать в зависимости от диаметра труб одновременно два, три или четыре сварщика.
7.1.9. 11.8. Вертикальные неповоротные стыки сваривают в направлении снизу вверх.
Рекомендуемая последовательность сварки корня шва вертикальных неповоротных стыков диаметром более 219мм - снизу вверх по четвертям; до 219мм – снизу вверх участками, равными половине окружности. Сварку первых 3х слоев в стыках труб диаметром более 219мм следует выполнять обратноступенчатым способом, при этом длина каждого участка – 200-250мм. Длина участков последующих слоев может составлять половину окружности стыка.
7.2.6.Вертикальные стыки труб поверхностей нагрева сваривает один сварщик участками по четверти периметра
13.2. Выполненную часть шва перед сваркой следующего слоя при сварке труб из сталей аустенитного класса необходимо охладить до температуры ниже 100 °С.
13.2. Ручную дуговую сварку вести почти без поперечных колебаний электрода узкими валиками шириной не более трех диаметров электрода; при диаметре электрода 2,5.
13.4. Перед сваркой сталей аустенитного класса во избежание образования мелких поверхностных трещин поверхность металла защитить не менее100мм от брызг металла при сварке. Каждый следующий валик при сварке сталей аустенитного класса необходимо накладывать только после снижения температуры металла в зоне сварки ниже 100град
15.5. Сварка разнородных сталей перлитного класса выполняется с подогревом, если таковой требуется, согласно данным табл.6.3 для более легированной из свариваемых сталей. Сварка сталей разных структурных классов с использованием аустенитного присадочного материала выполняется без предварительного подогрева стыка с минимальным тепловложением в соответствии с рекомендациями раздела 13. Сварка разнородных сталей перлитного класса выполняется с подогревом, если таковой требуется, согласно данным табл.6.3 для более легированной из свариваемых сталей.
Ремонт барабана.
Дефектный участок из стенки барабана удалить ручной дуговой строжкой. Каждый наплавленный валик места выборки дефектного шва должен перекрыть соседний на 1/3 – ½ ширины валика.
Исправлять наплавкой коррозионные раковины на стенках барабанов котлов допускается в случае когда глубина раковины не превышает 50% толщины стенки барабана. Если глубина выборки дефектного металла из стенки барабана котла менее 1% толщины стенки барабана, то это место можно оставить без наплавки. Рекомендуемый размер стороны квадрата участка, наплавляемого во взаимно перпендикулярном направлении, при наплавке выбранного участка стенки барабана котла площадью более 200 – 250кв.см: 50 -100мм. Валики квадратных участков места выборки дефектного металла стенки барабана котла наплавляются под углом 90 град к валикам соседних участков.
|
ПБ10 -575 -03 «Основные требования к безопасной эксплуатации электродных котлов и электрокотельных» не действуют с 2014г.
ПУБЭ ПК и ВК
Распространяются на паровые и водогрейные котлы – утилизаторы, если их параметры отвечают требованиям настоящих Правил.
Изготовление котлов по ПУБЭ ПК и ВК допускается при температуре не ниже -10град.
Контрольные св. соединения для мех.испытаний свариваются в количестве не менее одного на все однотипные производственные соединения, выполненные каждым сварщиком в течение 3 месяцев;
РД 34.17.310-96 «Осн о вные требования при сварке, термообработке и контроле при РЕМОНТЕ сварных соединений трубных систем котлов и паропроводов в период эксплуатации»
2.1. Технологические операции выполняются аттестованными электросварщиками 5‑6-го разрядов, проводящими ремонт сварных соединений и имеющими право на производство сварочных работ по трубопроводам I категории 1-й и 2-й групп, подведомственных Госгортехнадзору России;
2.2. Перед началом сварочных работ каждый электросварщик, занятый на ремонтных операциях, должен сварить контрольное сварное соединение со стыковым или угловым швом в зависимости от конструкции ремонтируемой детали (изделия). Качество и свойства сварного соединения должны быть оценены в соответствии с нормативными требованиями РД 34 15.027‑93.
4.1. В качестве сварочных материалов для ремонта сварных соединений применяются покрытые металлические электроды (табл. 4.1).
Таблица 4.1.
Тип электрода | Марка электрода | Типы ремонтируемых сварных соединений и трубных элементов котлов и паропроводов | Необходимость послесварочной термической обработки |
Э-09Х1М | ТМЛ-1У, ЦУ-2ХМ, ЦЛ-38 | Штуцерные соединения труб поверхностей нагрева из стали 12Х1МФ; штуцерные соединения водопароперепускных труб с коллекторами из стали 12Х1МФ для температур эксплуатации до 510 °С; стыковые соединения и паропроводные трубы наружным диаметром до 219 мм с толщиной стенки до 20 мм из стали 12Х1МФ для температур эксплуатации до 510 °С | Без термической обработки |
Э-09Х1МФ | ТМЛ-3У, ЦЛ-20, ЦЛ-45, ЦЛ-39 | Стыковые, штуцерные и тройниковые соединения паропроводов и коллекторов из хромомолибденованадиевых сталей 12Х1МФ, 15Х1М1Ф, 20ХМФЛ, 15Х1М1ФЛ для температуры эксплуатации до 570 °С | С термической обработкой |
Э-11Х15Н25М6АГ2 | ЭА-395/9, ЦТ-10 | Штуцерные соединения труб поверхностей нагрева и водопароперепускных труб с коллекторами из стали 12Х1МФ котлов для температуры эксплуатации до 560 °С, наплавка кромок в штуцерных соединениях труб Ду-100 с коллекторами для температуры эксплуатации до 545 °С | Без термообработки |
Э-08Н60Г7М7Т | ЦТ-36 | Наплавка кромок в штуцерных соединениях пароперепускных труб с коллекторами из стали 12Х1 МФ для температуры эксплуатации до 560 °С | Без термообработки |
6.4.2. Поврежденный металл удаляется только механическим способом (вышлифовкой).
7.5.4.К перерыву во времени между окончанием сварки подварочного шва и выполнением усиливающей наплавки при ремонте тройников применяются следующие требования (п. 7.5.4)
8.2.3. Заполнение места выборки выполняют многослойным способом кольцевыми валиками толщиной 4-6 мм и шириной 16 - 20 мм с использованием электродов диаметром 2,5 и 3 мм на режимах, указанных в табл. 8.1. Сварка выполняется с подогревом деталей при температ. 250-300 или 300-350°
7.6, 8.3. При заполнении разделки необходимо, чтобы крайние валики усиления шва перекрывали на 2 - 4 мм кромку со стороны фасонной детали и на 3 - 5 мм кромку паропроводной трубы.
Табл. 8.1
Рекомендуемые режимы ручной дуговой сварки
Сварочная операция | Диаметр электрода, мм | Сила тока, А | Толщина валиков, мм | Ширина валиков, мм | Номер рисунка |
Сварка подварочного шва | 2,5 | 70 - 90 | 4 - 6 | 16 - 20 | 8.3 |
3,0 | 90 - 110 | 4 - 6 | 16 - 20 | 8.3 | |
Выполнение усиливающей поверхностной наплавки | 3,0 | 90 - 110 | 5 - 8 | 16 - 20 | 8.5 |
4,0 | 120 - 160 | 6 - 8 | 18 - 25 | 8.5 |
ТУ 34-38-20092-94.
СО 153-34.26.608-2003
«Инструкция по обследованию и технологии ремонта барабанов котлов высокого давления».
6.3. Все сварочные электроды должны быть диаметром не более 4 мм.
Для ручной дуговой сварки и наплавки барабанов следует применять покрытые электроды 2,5 - 4 мм, а марку электродов выбирать в зависимости от марки стали ремонтируемого барабана:
- для барабанов из сталей 22К, 20К, 20Б, 16М, 15М - электроды типа Э42А (УОНИ-13/45, ЦУ-6) или типа Э50А (УОНИ-13/55, ТМУ-21У, ИТС-4С);
- для барабанов из сталей 16ГНМ и 16ГНМА - электроды типа Э50А марки УОНИ-13/55, ТМУ-21У, ИТС-4С, ЦУ-5, ЦУ-7, ЦУ-8.
ПБ 10-574-03
«Правила устройства и безопасной эксплуатации паровых и водогрейных котлов».
5.3.10. Подготовка кромок и поверхностей под сварку должна выполняться механической обработкой либо путем термической резки или строжки (кислородной, воздушно-дуговой, плазменно-дуговой) с последующей механической обработкой (резцом, фрезой, абразивным инструментом
5.3.3. К производству работ по сварке и прихватке котлов ОИАЭ допускаются сварщики, прошедшие проверку знания Правил по котлам в соответствии с ПБ 03-273-99), и имеющие удостоверение на право выполнения данных сварочных работ.
5.3.13. Приварка и удаление вспомогательных элементов (сборочных устройств, временных креплений и др.) должна выполняться сварщиком, допущенным к сварке данного изделия.
2.4. Непосредственно перед сборкой изготовленные под сварку кромки и прилегающие к ним участки поверхностей деталей должны быть зачищены до металлического блеска и обезжирены. Ширина зачищенных участков, считая от кромки разделки, должна быть не менее 20 мм с наружной и не менее 10 мм с внутренней стороны детали. Перед установкой штуцера (трубы) в коллектор или трубопровод поверхность вокруг отверстия должна быть зачищена на расстоянии 15 - 20 мм со стороны наложения сварного шва, а поверхность очка - на всю глубину.
5.3.21. Не допускается применение газовой сварки для деталей из аустенитных и высокохромистых сталей мартенситного и мартенситно-ферритного классов.
5.3.22. Сварка элементов, работающих под давлением, должна проводиться при положительной температуре окружающего воздуха. При монтаже и ремонте допускается выполнять сварку в условиях отрицательной температуры при соблюдении требований НД (ПТД) и создании необходимых условий для сварщиков (защита от ветра, дождя, снегопада).
При отрицательной температуре окружающего воздуха металл в районе сварного соединения перед сваркой должен быть просушен и прогрет с доведением температуры до положительной.
16.1.4. Сварку продольных швов по плавникам, вварку уплотнительных вставок и гребенок из сталей 12Х1МФ, 12X2M1 и др. следует производить с подогревом мест сварки до 150 - 200 °С газопламенными.горелками на ширину не менее 50 мм по обе стороны от места наложения шва.
16.3.1. Продольные швы (по плавникам) выполняют ручной дуговой сваркой, механизированной сваркой в углекислом газе или механизированной сваркой порошковой проволокой.
Сварка производится углеродистым присадочным материалом независимо от способа сварки и марки свариваемой стали:
при РДС - электродами Э50А (УОНИ-13/55, ЦУ-5, ТМУ-21У) диаметром не более 4 мм;
при сварке в углекислом газе – св. проволокой Св-08Г2С или Св-08ГС диаметром 1,2 - 1,6 мм;
при механизированной сварке порошковой проволокой - проволокой марок, указанных в табл. П9.2 приложения 9.
16.3.3. Зазор между свариваемыми плавниками независимо от способа сварки должен быть не менее 1,5 и не более 3мм
16.4.1. Для приварки гребенок и накладок в узле разъема применяются электроды типа Э50А независимо от марки стали труб и уплотняющих элементов.
7.2.4. Стыки труб с толщиной стенки более 2 мм следует сваривать не менее чем в два слоя.
7.2.6. Вертикальные стыки труб поверхностей нагрева сваривает один сварщик участками по четверти периметра. Чтобы уменьшить перелом трубы в месте стыка вследствие неравномерной усадки, участки необходимо сваривать в последовательности, указанной на рис.7.14,
Рис.7.14. Схема сварки одним сварщиком вертикального (а) и
горизонтального (б) стыков труб поверхностей нагрева:
1-4 - последовательность наложения участков
20.2.1.Исправлять наплавкой коррозионные раковины на стенках барабанов котлов допускается в случае когда глубина раковины не превышает 50% толщины стенки барабана.
20.2.1.Если глубина выборки дефектного металла из стенки барабана котла менее 1% толщины стеннки барабана, то это место можно оставить без наплавки.
Рекомендуемый размер стороны квадрата участка, наплавляемого во взаимно перпендикулярном направлении, при наплавке выбранного участка стенки барабана котла площадью более 200 – 250кв.см: 50 -100мм. Валики квадратных участков места выборки дефектного металла стенки барабана котла наплавляются под углом 90 град к валикам соседних участков.
Дефектный участок из стенки барабана удалить ручной дуговой строжкой. Каждый наплавленный валик места выборки дефектного шва должен перекрыть соседний на 1/3 – ½ ширины валика.
5.3.24. После сварки шов и прилегающие участки должны быть очищены от шлака, брызг металла и других загрязнений. Внутренний грат в стыках труб, выполненных контактной сваркой, должен быть удален для обеспечения заданного проходного сечения.
5.6.2. Перед визуальным контролем поверхности изделия и сварных соединений должны быть очищены от загрязнений и шлака. При контроле сварных соединений зачистке подлежат поверхность шва и прилегающие к нему участки основного металла шириной не менее 20 мм в обе стороны от шва, при электрошлаковой сварке - 100 мм.
2.1. При визуальном и измерительном контроле сварных соединений не допускаются:
- трещины всех видов и направлений; непровары (несплавления) между основным металлом и швом, а также между валиками шва; непровары в корне шва (кроме случаев, оговоренных в НД); наплывы (натеки) и брызги металла; незаверенные кратеры; свищи;
- прожоги; скопления; подрезы (кроме случаев, оговоренных в НД); отклонения размеров шва сверх установленных норм.
4.3.6. Св. соединения элементов, работающих под давлением, с толщиной стенки более 6 мм подлежат маркировке (клеймению), позволяющей установить фамилию сварщика, выполнившего сварку. Необходимость и способ маркировки сварных соединений с толщиной стенки менее 6мм устанавливаются требованиями ПТД. Способ маркировки должен исключать наклеп, подкалку или недопустимое утонение толщины металла и обеспечивать сохранность маркировки в течение всего периода эксплуатации изделия. Если все сварные соединения данного изделия выполнены одним сварщиком, то маркировку каждого св.соединения можно не производить. В этом случае клеймо сварщика следует ставить около фирменной таблички или на другом открытом участке изделия и место клеймения заключить в рамку, наносимую несмываемой краской. Место клеймения должно быть указано в паспорте изделия. Если сварное соединение выполнялось несколькими сварщиками, то на нем должны быть поставлены клейма всех сварщиков, участвовавших в его выполнении.
ГОСТ Р 52630 -2012 (КО 3)
В маркировке листа, плиты должна быть марка стали, номер плавки, номер листа, клеймо ОТК. При сварке змеевиков место клеймения сварного стыка - на основном металле, на расстоянии не более 100мм, при сварке элементов сосуда место клеймения – 20 -50мм от кромки шва.
Кромки элементов сосуда должны быть зачищены на расстоянии не менее 20мм
Выпуклость св. швов корпусов сосудов, изготовленных из двухслойных сталей снимать не нужно
Для проверки качества поверхностей на отсутствие закатов, расслоений, трещин выполняют визуальным осмотром. На поверхности обечаек риски, забоины, царапины допускаются, если глубина не превышает минусовые предельные отклонения.
Величина отклонения от перпендикулярности торца трубы с наружным диаметром не более 100мм относительно торца трубы при газовой сварке: 0,6мм.
Сварщики должны быть аттестованы, имеющие удостоверения.
Вместо клеймения разрешается прилагать к паспорту сосуда схему расположения швов при толщине стенки 4мм.
| 6.1.2 |
| |||||
| 6.2.3 |
| |||||
| 6.6.5 |
| |||||
| 6.6.6 |
| |||||
| 6.8.5 |
| |||||
| 6.8.6 |
| |||||
| 8.1.2 |
| |||||
| 6.1.4 |
| |||||
| 6.8.1 |
| |||||
| 6.8.6 |
|
ОТУ 3-01/2 « Сосуды и аппараты. Общие технические условия на ремонт корпусов»
1.1 Настоящие технические условия являются руководящим документом при ремонте и реконструкции стальных сварных сосудов и аппаратов с толщиной стенки от 4 до 120мм. работающих под давлением до 16 МПа (160 кгс/см2) и температуре не ниже минус 70"С, и не выше 540"С. на нефтеперерабатывающих, нефтехимических, химических и других взрывопожароопасных производствах.
5.5.3. Расстояние между прихватками для продольных швов корпуса стального сосуда или аппарата при его ремонте должно быть 100-500 мм, в зависимости от толщины металла, длина прихваток для продольных швов корпуса стального сосуда или аппарата при его ремонте - 20-100 мм.
5.5.5. Количество прихваток для трубных соединений диаметром от 250 до 450 мм и приварки их к корпусу стального сосуда или аппарата при его ремонте - четыре, для трубных соединений диаметром от 25 до 200 мм и приварки их к корпусу стального сосуда или аппарата при его ремонте – три, для трубных соединений диаметром до 25 мм и приварки их к корпусу стального сосуда или аппарата при его ремонте – две прихватки.
5.5.3. Прихватки на месте пересечения швов не допускаются. Расстояние между прихватками для продольных швов аппаратов должны выбираться в пределах 100¸500 мм в зависимости от толщины металла. Длина прихваток 20¸1ОО мм.
1.4.Сварщики впервые приступающие к сварке электродами с содержанием никеля 40% и выше при ремонте корпуса стального сосуда или аппарата должны быть аттестованы в установленном порядке и должны пройти практическую тренировку и сварку контрольной пластины 150х250х12..18 мм.
5.5.8.Слой шва с шириной разделки 15мм при ремонте корпуса аппарата из углеродистой стали рекомендуется выполнять в два прохода.
5.5.7.Сварные швы длиной свыше 1000мм выполняют обратноступенчатым способом, 300-1000мм - от середины к концам или обратноступенчатым способом, до 250-300мм – «напроход”.
5.5.10.Ремонтную наплавку корпуса стального аппарата следует выполнять не менее, чем в два слоя.
3.15. Прокаливать электроды – один раз.
5.5.8. Максимальная величина ширины валика при ремонте корпуса аппарата из хромомолибденовой стали и для аустенитной хромоникелевой стали - 2 диаметра электрода.
5.5.10. Ремонтную наплавку плакирующего слоя стального аппарата из двухслойной стали, когда предъявляются требования к межкристаллитной коррозии выполняют не менее, чем в два слоя.
5.1.2. Пересечение сварных швов, выполняемых при ремонте ручной дуговой сваркой, не допускается. Сварные швы должны быть смещены по отношению друг к другу на величину трехкратной наибольшей толщины стенки корпуса, но не менее чем на 100 мм между осями швов. Сварные швы корпусов сосудов и аппаратов, выполненных при изготовлении, допускается пересекать сварными швами, выполняемыми при ремонте (рис.6.6).
5.2.1. Демонтаж устройств, приваренных к корпусу, как правило, должен производиться по металлу устройства механической обработкой (шлиф. машинкой и т.д.). Допускается использование для этого термической резки или строжки (кислородной, воздушно-дуговой, плазменно-дуговой). В этом случае резка проводится по металлу устройства на расстоянии 20¸25 мм от поверхности корпуса.
5.2.4. Метод удаления дефектного участка корпуса выбирается в зависимости от характера, размеров и особенностей развития дефектов:
– трещины всех видов и направлений, как правило, удаляются только механической обработкой с предварительным определением концов трещины цветной дефектоскопией и засверловкой обоих концов трещины на всю глубину сверлом диаметром 5¸6 мм,
Наибольшее распространение получили методы вышлифовки и высверловки трещин. При сквозной трещине для удобства последующего заплавления целесообразно оставлять слой металла толщиной 2,0¸2,5 мм в качестве подкладки нового, который полностью переплавляется при последующей сварке корневого шва;
После удаления дефектов любым способом термической резки зачистка поверхности механическим способом производится на глубину:
– углеродистых и низколегированных сталей до металлического блеска;
– аустенитных сталей типа 08Х18Н10Т, сталей типа 12МХ, 12ХМ, 15ХМ на глубину не менее 1 мм, а сталей типа 15Х5М, 1Х2М1 на глубину не менее 3 мм, считая от наибольшей впадины реза.
5.5.10. Ремонт дефектных участков корпусов наплавкой производится в два и более слоя. Первый слой рекомендуется выполнять валиками, расположенными перпендикулярно оси корпуса. Каждый последующий валик должен перекрывать предыдущий на 1/3 его ширины. При многослойной наплавке последовательность наложения валиков рекомендуется выполнять в каждом последующем слое перпендикулярно предыдущему. Дефекты, имеющие округлую форму диаметром до 40 мм, лучше наплавлять по спирали, начиная с центра участка дефекта.
5.8.3. Клеймение сварных швов сосудов после ремонтной сварки наплавкой запрещается.
Трещины, выходящие из сварного шва в основной металл на расстояние более 100 мм устраняются путем вырезки дефектного участка с трещинами и установки вставки..
6.4.6.Внутренний шов приварки днища к обечайке корпуса выполнять электродами, указанными в таблицах приложении 5, 6, 7, 9, 25, с соблюдением требований подраздела 5.4:
- сварочные работы при ремонте корпусов аппаратов производятся при положительной температуре окружающего воздуха
- при ремонте корпусов аппаратов на открытой площадке место сварки должно быть надежно защищено от ветра и атмосферных осадков.
Сварка углеродистых сталей толщиной более 36 мм, низколегированных кремнемарганцовистых - более 30 мм, а также легированных теплоустойчивых сталей, независимо от толщины стенки, при положительной температуре окружающего воздуха производится с предварительным и сопутствующим подогревом
6.5.4. Толщина вставок («латок») и монтажных окон, их размеры и расположение на корпусах сосудов должна быть равна толщине корпуса или превышать ее не более чем на 3 мм.
6.5.8. Сварные швы вставки небольших габаритов (со стороной l не более 600 мм), показанные на рис 6.7а, могут выполняться одним сварщиком. Цифрами 1- 6 показана последовательность сварки швов вставки. Сварные швы вставки со стороной более 600 мм выполняются двумя и более сварщиками (большой объем сварочных работ, рис 6.7б).
6.5.9. При вварке вставок с горизонтальной стороной длиной более 600 мм для снижения остаточных напряжений используется обратноступенчатый метод сварки (рис. 6.7б).
РД 153-34.1-003-01.
«Сварка, термообработка и контроль трубных систем котлов и трубопроводов при монтаже и ремонте энергетического оборудования».
Настоящий руководящий документ определяет технологию сборочно-сварочных работ, термической обработки сварных стыков труб, а также объем и порядок контроля и нормы оценки качества сварных соединений; он охватывает все виды сварки, применяющиеся при монтаже и ремонте энергетического оборудования и трубных систем котлов и трубопроводов
1.1. Руководящий документ (РД) предназначен для организаций, осуществляющих монтаж и ремонт трубопроводов и трубных систем паровых и водогрейных котлов независимо от параметров рабочей среды, а также изготовление трубопроводов с рабочим давлением до 2,2 МПа (22 кгс/см2) и температурой не более 425 °С и отдельных элементов котлов.
Требования к подготовке кромок и сборке
6.1.4. Концы труб из углеродистых и низколегированных сталей разрешается обрабатывать кислородной, плазменно-дуговой или воздушно-дуговой резкой с последующей зачисткой кромок режущим или абразивным инструментом до удаления следов огневой резки. Подготовленные к сборке кромки должны быть без вырывов, заусенцев, резких переходов и острых углов.
6.2.1. Конструкции сварных соединений должны быть указаны в проектно-конструкторской документации. Рекомендуемый мин.зазор в стыке при подготовке труб с разделкой Тр-2 под РДС - 1±0,5
Основные рекомендуемые конструкции стыков св. соединений даны в табл. 6.2
6.2.4. Непосредственно перед сборкой изготовленные под сварку кромки и прилегающие к ним поверхности деталей должны быть.зачищены до металлического блеска и обезжирены. Ширина зачищенных участков должна быть не менее 20 мм с наружной и не менее 10 мм с внутренней стороны детали. Перед уста
|
|
Общие условия выбора системы дренажа: Система дренажа выбирается в зависимости от характера защищаемого...
Историки об Елизавете Петровне: Елизавета попала между двумя встречными культурными течениями, воспитывалась среди новых европейских веяний и преданий...
Адаптации растений и животных к жизни в горах: Большое значение для жизни организмов в горах имеют степень расчленения, крутизна и экспозиционные различия склонов...
История создания датчика движения: Первый прибор для обнаружения движения был изобретен немецким физиком Генрихом Герцем...
© cyberpedia.su 2017-2024 - Не является автором материалов. Исключительное право сохранено за автором текста.
Если вы не хотите, чтобы данный материал был у нас на сайте, перейдите по ссылке: Нарушение авторских прав. Мы поможем в написании вашей работы!