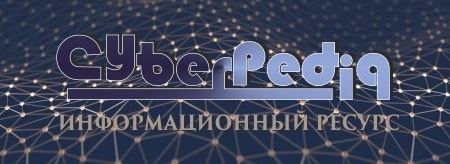
Адаптации растений и животных к жизни в горах: Большое значение для жизни организмов в горах имеют степень расчленения, крутизна и экспозиционные различия склонов...
Типы оградительных сооружений в морском порту: По расположению оградительных сооружений в плане различают волноломы, обе оконечности...
Топ:
Комплексной системы оценки состояния охраны труда на производственном объекте (КСОТ-П): Цели и задачи Комплексной системы оценки состояния охраны труда и определению факторов рисков по охране труда...
Организация стока поверхностных вод: Наибольшее количество влаги на земном шаре испаряется с поверхности морей и океанов...
Интересное:
Аура как энергетическое поле: многослойную ауру человека можно представить себе подобным...
Мероприятия для защиты от морозного пучения грунтов: Инженерная защита от морозного (криогенного) пучения грунтов необходима для легких малоэтажных зданий и других сооружений...
Лечение прогрессирующих форм рака: Одним из наиболее важных достижений экспериментальной химиотерапии опухолей, начатой в 60-х и реализованной в 70-х годах, является...
Дисциплины:
![]() |
![]() |
5.00
из
|
Заказать работу |
|
|
Для производства полых и объемных изделий из термопластов — канистр, бочек, бутылей, флаконов, игрушек и т. п. — наибольшее распространение получил метод выдувного формования. Производство изделий этим методом осуществляется в две стадии: сначала получают заготовку, которую затем раздувают сжатым воздухом. В отличие от большинства методов получения изделий из пластмасс, где формование осуществляется из расплава, т.е. в вязкотекучем состоянии, в основе этой технологии лежит использование не только пластической, но и преимущественно высокоэластической деформации.
В зависимости от выбранного способа получения заготовки различают два метода раздувного формования:
экструзионный метод, называемый также экструзионно-выдувным формованием;
литьевой метод, называемый литьем с раздувом, инжекционно-выдувное формование.
- Общие сведения.
В этом методе с помощью экструдера формуется заготовка в виде трубки (называемой также рукавом или чулком), которая затем поступает в форму, где и происходит процесс формования изделия за счет создания внутри заготовки повышенного давления воздуха.
Благодаря высокой производительности и высокому уровню автоматизации этот метод является в настоящее время основным способом формования полых изделий и позволяет получать изделия объёмом от нескольких миллилитров до нескольких сотен литров.
-Технологическая схема экструзионно-выдувного формования
Технологический процесс состоит из следующих операций:
1) подготовка расплава (плавление, гомогенизация и дозирование);
2) выдавливание трубчатой заготовки;
3) смыкание формы и обрезка трубчатой заготовки;
|
4) формование изделия (раздув);
5) охлаждение изделия;
6) раскрытие формы и извлечение изделия.
Операционная схема процесса показана на рис. 6.1.
Рис. 6.1. Операционная схема изготовления изделий выдуванием из трубчатых заготовок:
а — выдавливание трубчатой заготовки; б — смыкание формы; в — формование изделия; г — размыкание формы.
Для изготовления полых изделий применяются, как правило, экструдеры сравнительно небольших размеров, с диаметром шнека 50-90 мм. Поскольку сопротивление головки сравнительно невелико, а основным требованием является получение расплава с высокой однородностью, длина шнека также не превышает 15-18 D. Схематически процесс производства полых изделий можно представить следующим образом (рис. 9.1). Расплавленный и гомогенизированный в экструдере материал выдавливается из головки вниз в виде трубчатой заготовки, которая попадает в открытую к этому моменту форму. После того, как длина заготовки достигнет необходимой величины, полуформы смыкаются, зажимая нижний и верхний края заготовки своими буртами (пресс-кантами). При этом происходит сварка нижнего конца заготовки и оформление отверстия на ее верхнем конце (или наоборот). После замыкания формы в нее через дорн или ниппель подается сжатый воздух, под действием которого размягченный материал рукава принимает конфигурацию внутренней полости формы. В результате соприкосновения с холодными стенками формы полимер затвердевает; далее форма раскрывается, готовое изделие извлекается и направляется на окончательную обработку (удаление приливов, снятие заусенцев и т. п.).
Производство полых изделий осуществляется на специальных агрегатах, снабженных (помимо экструдера) механизмом перемещения, разъема и смыкания формы с гидравлическим или пневматическим приводом. Так как процесс формования распадается на две неравные по продолжительности стадии: короткую стадию выдавливания заготовки и длительную — формования и охлаждения изделия, то для повышения производительности большинство агрегатов выполняется либо многопозиционными, с несколькими формами, либо — особенно при производстве изделий небольшого объема — снабжается двух- и более канальной формующей головкой, иногда с несколькими мундштуками на каждом из каналов. В первом случае процессы получения заготовки и оформления изделия разобщены и происходят в одной форме, но в различных позициях агрегата; во втором — поток материала из экструдера поступает периодически в один или группу соединенных параллельно мундштуков, через которые заготовки попадают в форму.
|
- Плавление гранул и гомогенизация расплава.
Данная операция осуществляется как правило в шнековых экструзионных агрегатах. Гранулы из бункера захватываются нарезкой шнека и, перемещаясь вдоль цилиндра, плавятся за счет теплоты от нагретых стенок и диссипации механической энергии трения. По мере движения гранулы уплотняются и создается давление. Расплавленная часть полимера благодаря сдвиговому течению перемешивается, приобретая в зоне дозирования необходимую однородность (гомогенизируется).
Для обеспечения непрерывной работы узел смыкания снабжается механизмом для отвода формы с зажатой в ней заготовкой вниз или в сторону, чтобы в период охлаждения изделия можно было производить выдавливание последующей трубчатой заготовки.
В тех случаях, когда изготавливаются крупногабаритные изделия, а производительность экструзионной машины мала, чтобы накопить большую дозу расплава и уменьшить время выдавливания заготовки, используют агрегаты с копильником (рис. 6.2). В период охлаждения изделия расплав из цилиндра 1 поступает в копильник 2, соединенный с патрубком формующей головки 4. По мере накопления дозы расплав поступает в копильник и плунжер 3 поднимается вверх. В момент получения трубчатой заготовки расплав выдавливается в головку из копильника плунжером 3 и одновременно нагнетается шнеком из цилиндра. Вследствие этого расплав с большой скоростью выдавливается через формующую щель головки и время получения заготовки уменьшается.
При изготовлении малогабаритных изделий, чтобы полностью использовать производительность агрегата, применяются многофильерные (многоручьевые) головки. Расплав выдавливается одновременно через несколько формующих каналов, расположенных в общем корпусе головки (рис. 6.3). Из патрубка расплав поступает в распределительный коллектор, а затем вытекает через несколько формующих каналов. В этом случае для выравнивания скоростей течения во входных каналах всех фильер предусматривают дросселирующие краны. При таком способе формования трубчатых заготовок формы также делают многогнездными. Применение многоручьевых головок повышает производительность агрегата и снижает трудоемкость.
|
![]() | |
Рис. 6.2. Узел выдувного агрегата с копильником: 1 — цилиндр экструдера; 2 — копильник; 3 — плунжер копильника; 4 — формующая головка. | Рис. 6.3. Многоручьевая формующая головка: 1 — корпус головки; 2 — трубчатая заготовка; 3 — цилиндр смыкания формы; 4 — многогнездная форма. |
В целом операции плавления и гомогенизации осуществляются аналогично рассмотренным ранее для процесса экструзии. Вязкость расплава должна быть такой же или несколько выше, чем при производстве труб, поэтому по зонам экструдера устанавливается соответственно меньшая температура.
- Выдавливание трубчатой заготовки.
Формование заготовки является важнейшей операцией, которая во многом предопределяет свойства и качества готового изделия. Поступающий в мундштук расплав должен быть гомогенным, иметь постоянную температуру по всему периметру заготовки и выдавливаться равномерно (без пульсации). При получении изделий, имеющих в сечении форму прямоугольника, эллипса и т. п., а также изделии сложной конфигурации, сечение формующей щели делают неодинаковым — для получения готового изделия со стенками одинаковой толщины участки заготовки, которые раздуваются больше, должны иметь большую толщину. Следует иметь в виду, что выдавливаемая заготовка имеет большую толщину, чем сечение формующего зазора вследствие так называемого «разбухания» экструдата, носящего релаксационный характер.
«Разбухание» зависит от скорости сдвига, длины формующего канала и вязкости расплава, что затрудняет управление процессом.
Кроме того, при формовании продолговатых и длинных изделий было отмечено, что из-за вытягивания пластичной заготовки под действием собственного веса толщина стенок верхней части изделия оказывается меньшей, чем нижней части.
|
Разнотолщинность заготовки зависит от скорости выдавливания расплава, его вязкости и веса заготовки. Обычно формование заготовки ведут при минимально возможной температуре расплава и высокой скорости экструзии. Поэтому в современных машинах для управления формой, размерами и толщиной стенок заготовки используются микропроцессоры, позволяющие за счет изменения скорости подачи расплава и осевого перемещения конического дорна формировать заготовку с необходимой степенью разнотолщинности. Минимальная разнотолщинность достигается при коэффициенте раздува 3-3,5. Соответствующая программа составляется заранее с учетом геометрии изделия, температурных параметров процесса и реологических характеристик расплава полимера. Перед началом формования следующей заготовки дорн автоматически возвращается в исходное положение.
- Смыкание формы и формование изделия.
Полуформы закреплены на плитах узла смыкания и могут перемещаться навстречу друг другу в горизонтальном направлении. Обычно в разомкнутом состоянии полуформы подводятся к трубчатой заготовке, чтобы она расположилась симметрично формующей полости, после чего происходит их смыкание. В момент смыкания часть заготовки, выступающая за габариты формующей полости, зажимается пресс-кантами. В месте нажатия пресс-кантов под действием усилия смыкания происходит пережатие расплава, которое сваривает заготовку в виде замкнутой полости и обрезает за контуром формующего гнезда избыток материала. Поскольку форма охлаждена, то по контуру пресс-канта образуется тонкая перемычка, по которой в дальнейшем проводится механическая доработка изделия. Толщина перемычки зависит от усилия смыкания, температуры формы и расплава, а также от ширины пресс-канта и вязкости полимера. Чем ниже температура расплава и формы, а также чем больше ширина пресс-канта, тем толще образуется перемычка. При уменьшении ширины канта улучшается обжатие заготовки и образуется тонкая перемычка, что облегчает последующее удаление приливов. Под приливом подразумевается избыток заготовки за контуром формы, который отжимается кантом. Однако при очень малой ширине канта ухудшается сваривание заготовки, что снижает прочность изделия. Ухудшается свариваемость также при понижении температуры расплава, особенно это заметно при изготовлении заготовок с малой скоростью выдавливания. За счет длительного течения нижняя часть заготовки охлаждается воздухом, поэтому ее формование и свариваемость затрудняются. Размеры и форму пресс-кантов обычно выбирают по справочным данным, наиболее широко применяемые из них приведены на рис. 6.10.
|
Усилие смыкания формы не должно допускать раскрытия формы под действием сжатого воздуха в момент формования изделия.
В момент смыкания формы трубчатая заготовка отрезается от формующей головки. Обрезка обычно производится ножницами или раскаленной нихромовой лентой. При движении ленты, нагретой электрическим током, в месте контакта происходит сильный перегрев расплава и получается ровный срез.
Рис. 6.10. Разновидности пресс-кантов формы.
После окончания смыкания сразу же начинается формование изделия, для чего внутрь заготовки подается сжатый воздух. В зависимости от конструкции изделия и формующего инструмента подача сжатого воздуха для формования изделия может производиться через дорн (сверху), через специальный ниппель (снизу) или через полую дутьевую иглу (рис. 9.2). Последний способ применяется главным образом при производстве замкнутых изделий (без отверстия), так как формующее отверстие в этом случае очень мало и затягивается после удаления иглы разогретым материалом.
Наиболее часто осуществляется подвод воздуха через ниппель, перемещающийся от отдельного привода. Форма после смыкания отводится вниз или в сторону, а затем в горловину ее вводится ниппель. При изготовлении сосудов, отверстие которых закрывается пробкой, ниппель делается ступенчатым. Будучи введенным в форму, ниппель обеспечивает ровную поверхность горловины изделия.
Качество изделий зависит от давления воздуха. С увеличением давления понижается шероховатость изделий и их коробление, однако при чрезмерно высоком давлении требуется большое усилие смыкания формы. При высоком давлении заготовка плотно прижимается к поверхности формы и время ее охлаждения уменьшается. Обычно давление выбирается в пределах 0,2-1 МПа.
С целью удаления воздуха из полости между заготовкой и формующей поверхностью в полуформах предусматривают воздушные каналы, просверленные в местах, где затруднен выход воздуха. Диаметр отверстий обычно составляет 1-2 мм, но не более половины толщины стенки изделия. При изготовлении малогабаритных изделий объем воздуха в полости невелик, поэтому воздух свободно удаляется в зазор между пресс-кантами на боковых стенках формы, где отсутствует пережатие расплава. Сверление в этом случае не делают.
Для того чтобы обеспечить небольшую разнотолщинность, коэффициент раздува должен быть равен Кр = 3÷3,5, при большем его значении повышается разнотолщинность изделия по периметру. Степень раздува влияет также на усадку изделия. При увеличении коэффициента раздува усадка возрастает, что объясняется увеличением ориентации макромолекул.
При изготовлении изделий сферической или кубической конфигурации для уменьшения разнотолщинности трубчатые заготовки перед смыканием формы предварительно раздувают. Нижний конец заготовки заваривают, после чего она равномерно раздувается воздухом. При этом заготовка принимает сферическую конфигурацию. Этим достигается также сокращение расхода полимера, так как масса заготовки, срезаемая пресс-кантами в виде приливов, уменьшается.
-Охлаждение изделия.
Стадия охлаждения начинается с момента контакта заготовки с поверхностью охлаждаемой формы и заканчивается после охлаждения наиболее толстых участков изделия, примыкающих к горловине или днищу. Преждевременное извлечение изделий сопровождается размягчением соседних с горловиной участков и их необратимым деформированием.
Основным фактором на этой стадии является температура формы. Она не только отражается на качестве готовых изделий, но и определяет производительность процесса, так как охлаждение составляет от 50 до 75 % времени цикла формования. Поэтому широко используют интенсивное охлаждение форм различными хладагентами, подачу в полость изделия охлажденного воздуха, водяного тумана, жидкого азота и углекислоты. Однако охлаждение формы ниже 0-5 °С нецелесообразно из-за опасности ухудшения качества поверхности готовых изделий вследствие образования конденсата на поверхности формы.
Время охлаждения можно сократить понижением температуры расплава (может сопровождаться ухудшением качества поверхности готовых изделий) и повышением давления воздуха, что способствует улучшению теплоотдачи от изделия к стенке формы.
В результате охлаждения изделий их объем уменьшается вследствие естественной усадки. Наибольшая усадка наблюдается в диаметральном направлении, поскольку здесь развивается максимальная деформация при формовании изделия. Для получения выдувных изделий с одинаковой усадкой в продольном и поперечном направлениях необходимо, чтобы степень вытяжки была равна коэффициенту раздува.
-Раскрытие формы и извлечение изделия.
Форма раскрывается с помощью узла смыкания. Перед раскрытием формы из горловины изделия вынимается ниппель, а при автоматическом режиме одновременно отрываются приливы.
Изделия из раскрытой формы извлекаются под действием собственного веса, а в тех случаях, когда на боковых стенках возникают большие усилия, применяются толкатели (рис. 6.17). Вместо толкателей можно использовать сжатый воздух, который подается в форму через воздушные каналы в боковой стенке. При извлечении изделий толкателем в момент раскрытия формы 4 (рис. 6.17) выступающая часть толкателей 2 упирается в неподвижную плиту 5 и они останавливаются, а полуформа продолжает двигаться дальше, как бы отделяясь от изделия 3. Толкатель и изделие в момент выталкивания неподвижны, а форма относительно них перемещается. Приливы 1 выталкиваются толкателями одновременно с изделием.
![]() | |
Рис. 6.17. Извлечение изделия и приливов с помощью толкателей: 1 — приливы; 2 — толкатели; 3 — изделие; 4 — форма; 5 — неподвижная плита. | Рис.6.18. Способ отделения прилива от изделия: 1 и 5 —левая и правая полуформы; 2 —толкатель; 3 — бобышка; 4 —прилив. |
Чтобы оторвать изделие от прилива, на плоскости разъема формы предусматривают замок (рис. 6.18). При смыкании формы избыток материала затекает в отверстие с обратным конусом и после охлаждения там образуется удерживающая бобышка 3. В момент раскрытия формы прилив 4 остается на полуформе 1, а изделие движется вместе со второй полуформой 5. В результате прилив 4 отрывается от изделия. При последующем движении левой полуформы 1, толкатель 2, упирается в ограничитель и бобышка 3 прилива выталкивается из гнезда. Применение подобных приспособлений снижает трудоемкость и исключает ручные операции по доработке изделий. Для отделения приливов от изделия перед раскрытием формы можно также использовать специальные захваты.
- Литье с раздувом.
- Общие сведения.
Литьевой метод раздувного формования предполагает получение заготовки методом литья под давлением. Заготовки, полученные таким способом, называют преформами.
В процессе литья с раздувом преформы выдуваются в бутылки или другую тару. При выдуве горлышко преформы не нагревается для сохранения его размеров. Этот способ используется для производства тары, которая имеет жесткий размерный допуск, широкое горлышко и нестандартную форму. При литье с раздувом материал хорошо распределен. Другим преимуществом технологии по сравнению с экструзионно-выдувным формованием является отсутствие облоя. Литьем с раздувом производят емкости объемом от 1 мл до 1 л из разнообразных пластмасс для упаковки широкого ряда продуктов: косметических, фармацевтических, хозяйственных и автомобильных товаров.
При этом методе расплав из цилиндра термопластавтомата впрыскивается в литьевую форму и трубчатая заготовка оформляется в зазоре между стенками формы и внутренним пустотелым сердечником. Заготовке может быть придана необходимая форма, причем горловина, ручки, необходимые приливы на наружной поверхности оформляются сразу при литье. После окончания процесса литья форма размыкается, и сердечник вместе с горячей заготовкой перемещается в другую форму, где после смыкания полуформ осуществляется процесс раздува за счет подачи сжатого воздуха во внутреннюю полость. При этом размер изделия увеличивается, а толщина стенок уменьшается. Так как геометрическая форма заготовки задается заранее, этот метод позволяет получать сложные по конфигурации изделия, изделия с равномерной толщиной стенок и необходимым соотношением толщины стенок в разных его частях, но из-за необходимости переоборудования литьевых машин, а также из-за высокой стоимости литьевых и раздувных форм этот метод находит ограниченное применение.
- Технологическая схема литья с раздувом
Технологический процесс состоит из следующих операций:
1) плавление, гомогенизация и дозирование расплава;
2) установка оправки в форму для литья;
3) смыкание литьевой формы и подвод узла впрыска;
4) впрыск расплава и выдержка;
5) размыкание литьевой формы и смыкание формы для выдувания;
6) выдувание изделия;
7) охлаждение;
8) размыкание формы и извлечение изделия.
Схема процесса приведена на рис. 6.19.
Рис. 6.19.Операционная схема изготовления изделий выдуванием из литьевых заготовок: а — смыкание литьевой формы; б — впрыск расплава; в — размыкание литьевой формы; г — смыкание формы для выдувания; д — формование изделия; е — размыкание формы и извлечение изделия.
В последние годы получил распространение вариант этой технологии, когда стадии отливки заготовки и ее раздува разделены. Заготовка, называемая преформой, отливается в многогнездной форме на термопластавтомате и полностью охлаждается. Нередко преформы являются самостоятельной товарной продукцией. Раздув заготовки осуществляется воздухом на специальном агрегате после ее предварительного разогрева, с последующим охлаждением в форме.
- Гомогенизация и дозирование расплава
Эта операция осуществляется на литьевой машине. При движении шнека к соплу литьевой машины создается высокое давление (80-160 МПа), вращение шнека прерывается, а для исключения обратного течения расплава по каналам нарезки на хвостовике шнека устанавливают клапан. Кроме того, при гомогенизации расплава по зонам цилиндра литьевой машины задается более высокая температура расплава, чем при получении заготовок экструзионным методом. Это необходимо для снижения потерь давления при впрыске расплава через литниковые каналы формы и сопла. При высокой вязкости расплава большая часть давления впрыска расходуется на преодоление сопротивления течения полимера в литниках, поэтому происходит медленное заполнение формы расплавом и возможно некачественное формование оболочки.
- Впрыск расплава и выдувание изделия
Впрыск расплава в форму осуществляется за счет перемещения шнека машины под действием усилия, создаваемого поршнем узла впрыска. Расплав под давлением, возникающим в цилиндре, течет с высокой скоростью через сопло и литниковую систему и впрыскивается в формующую полость, т. е. заполняет свободное пространство между оправкой и стенками формы. После заполнения формующей полости расплав под действием давления уплотняется и в таком состоянии выдерживается определенное время. За счет холодных стенок расплав частично охлаждается, при этом к моменту размыкания формы его средняя температура должна быть несколько выше температуры плавления (текучести). Это необходимо для того, чтобы расплав обладал способностью к последующей деформации при выдувании изделия.
На процессе литья под давлением подробно остановимся на следующей лекции, поэтому остановимся здесь лишь на рассмотрении некоторых особенностей.
В отличие от производства изделий литьем под давлением, вданном случае внутренняя формующая полость формы представляет собой специальную оправку (рис. 6.20). Оправка состоит из цилиндрического корпуса 5, в который вставляется пустотелый стержень клапана 6, прижимаемый пружиной 4. Стержень клапана имеет продольные пазы для подвода воздуха из штуцера 1, а внутрь его вставляется трубка для подачи охлаждающей воды из штуцера 3. Во время отливки оболочки клапан 6 закрыт, поэтому расплав внутрь оправки не попадает. В дальнейшем, когда происходит выдувание изделия, внутрь оправки подается сжатый воздух, пружина 4 сжимается и клапан открывается, пропуская воздух внутрь полимерной оболочки.
Рис. 6.20. Оправка для литья оболочки:
1 — штуцер для сжатого воздуха; 2,3— каналы для подачи воды; 4 — пружина; 5 — корпус; 6 — клапан.
По окончании выдержки литьевая форма размыкается, оправка с заготовкой переносится в форму для выдувания, и форма смыкается. При работе на роторных автоматах заготовка перемещается на следующую позицию, где и происходит смыкание формы для выдувания.
Операция выдувания осуществляется сжатым воздухом, который подается внутрь оправки. Под действием создаваемого усилия клапан 6 открывается (см. рис. 6.20), и воздух растягивает полимерную оболочку, плотно прижимая ее к стенкам формы; происходит оформление изделия, а затем его охлаждение.
Дальнейшие операции не отличаются от операций смыкания формы, формования изделий и охлаждения для экструзионно-выдувного формования.
Изделия извлекаются после раскрытия формы под действием сжатого воздуха, подаваемого в оправку, или с помощью толкателей. В последнем случае вначале из формы вынимается оправка, а затем происходит раскрытие формы и извлечение изделия.
При изготовлении пустотелых изделий выдуванием из литьевых заготовок сокращается расход материала, так как отсутствуют приливы, и не требуется последующей механической доработки деталей, поскольку при смыкании формы не происходит пережатия расплава пресс-кантами. На деталях отсутствуют сварные швы, поэтому прочность их повышается, и они имеют лучший внешний вид.
Преимуществом метода также является отсутствие разнотолщинности изделия как по периметру, так и по высоте, поскольку исключается вытяжка заготовки перед выдуванием. Кроме того, литьевая форма может быть изготовлена с учетом несимметричности в конфигурации изделия, т. е. заготовка делается в соответствующих местах толще или тоньше в зависимости от степени ее вытяжки. К недостаткам данного метода следует отнести более высокую стоимость оборудования, литьевых и раздувных форм и увеличение длительности цикла, поэтому этот метод находит ограниченное применение.
Лекция №5.
|
|
Семя – орган полового размножения и расселения растений: наружи у семян имеется плотный покров – кожура...
Типы сооружений для обработки осадков: Септиками называются сооружения, в которых одновременно происходят осветление сточной жидкости...
Механическое удерживание земляных масс: Механическое удерживание земляных масс на склоне обеспечивают контрфорсными сооружениями различных конструкций...
Типы оградительных сооружений в морском порту: По расположению оградительных сооружений в плане различают волноломы, обе оконечности...
© cyberpedia.su 2017-2024 - Не является автором материалов. Исключительное право сохранено за автором текста.
Если вы не хотите, чтобы данный материал был у нас на сайте, перейдите по ссылке: Нарушение авторских прав. Мы поможем в написании вашей работы!