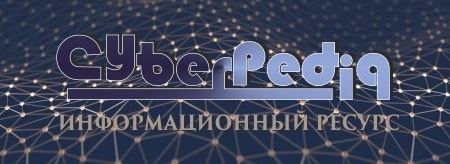
Историки об Елизавете Петровне: Елизавета попала между двумя встречными культурными течениями, воспитывалась среди новых европейских веяний и преданий...
История развития пистолетов-пулеметов: Предпосылкой для возникновения пистолетов-пулеметов послужила давняя тенденция тяготения винтовок...
Топ:
Оснащения врачебно-сестринской бригады.
Характеристика АТП и сварочно-жестяницкого участка: Транспорт в настоящее время является одной из важнейших отраслей народного...
Организация стока поверхностных вод: Наибольшее количество влаги на земном шаре испаряется с поверхности морей и океанов...
Интересное:
Мероприятия для защиты от морозного пучения грунтов: Инженерная защита от морозного (криогенного) пучения грунтов необходима для легких малоэтажных зданий и других сооружений...
Как мы говорим и как мы слушаем: общение можно сравнить с огромным зонтиком, под которым скрыто все...
Наиболее распространенные виды рака: Раковая опухоль — это самостоятельное новообразование, которое может возникнуть и от повышенного давления...
Дисциплины:
![]() |
![]() |
5.00
из
|
Заказать работу |
|
|
Проектирование машиностроительного производства
Методические указания к выполнению практических работ
для студентов направления 15.03.05 «Конструкторско-технологическое обеспечение
машиностроительных производств»
всех форм обучения
Сарапул
Кафедра «Технология машиностроения, металлорежущие станки и инструменты»
Составитель: Ярхов Юрий Борисович, к.т.н., доцент, Сухих Сергей Викторович, старший преподаватель,
Методические указания составлены на основании государственного образовательного стандарта высшего образования, приказ Минобрнауки России от 11.08.2016 N 1000, и утверждены на заседании кафедры
Протокол №__ от «__» ________ 201__г.
Проектирование машиностроительного производства: Методические указания к выполнению практических работ по дисциплине «Проектирование машиностроительного производства/ Составитель Ярхов Юрий Борисович, к.т.н., доцент, Сухих Сергей Викторович, старший преподаватель, - Сарапул, 2016 – 21с.
СОДЕРЖАНИЕ
1. Общие положения. 4
1.1 Цель проведения практических работ. 4
1.2 Задачи проведения практических работ. 4
1.3 Значение практических занятий в процессе обучения по дисциплине «Автоматизация производственных процессов». 4
1.4 План проведения занятий. 5
2. Порядок организации проведения практических занятий (работ) 6
2.1 Краткая характеристика рабочих мест в аудитории. 6
2.2 Правила общения студентов с преподавателем и друг с другом.. 6
2.3 Требования к технике безопасности. Инструктаж.. 6
2.4 Порядок выполнения практических занятий. 6
3. Структура и состав практикума. 8
Практическая работа №1. 8
Практическая работа №2. 25
Практическая работа №3. 33
Общие положения
|
Цель проведения практических работ
Ведущей дидактической целью практических работ является;
формирование практических умений - профессиональных (выполнять определенные действия, операции, необходимые в последующем в профессиональной деятельности) или учебных (решать задачи по экономике, статистике, математике, информатике и др.), необходимых в последующей учебной деятельности по общепрофессиональным и специальным дисциплинам.
Практические занятия занимают преимущественное место при изучении общепрофессиональных и специальных дисциплин.
Проведения практических занятий способствует овладению студентами следующими компетенциями:
способностью осваивать и применять современные методы организации и управления машиностроительными производствами,
выполнять работы по доводке и освоению технологических процессов, средств и систем технологического оснащения, автоматизации, управления, контроля, диагностики в ходе подготовки производства новой продукции, оценке их инновационного потенциала, по определению соответствия выпускаемой продукции требованиям регламентирующей документации, по стандартизации, унификации технологических процессов, средств и систем технологического оснащения, диагностики, автоматизации и управления выпускаемой
создание новых и применение современных средств автоматизации, методов проектирования, математического, физического и компьютерного моделирования технологических процессов и машиностроительных производств;
обеспечение высокоэффективного функционирования технологических процессов машиностроительных производств, средств их технологического оснащения, систем автоматизации, управления, контроля, диагностики и испытания продукции, маркетинговые исследования в области конструкторско-технологического обеспечения машиностроительных производств.
План проведения занятий
Тематика и трудоемкость выполнения работ определена в таблице 1.1.
|
Таблица 1.1. Наименование тем практических работ, их содержание и объем в часах
№ п/п | № раздела дисциплины* | Наименование практических работ | Трудоем-кость (час) |
1. | Планировка механического участка | ||
2. | Расчет транспортной системы. | ||
3. | Расчет площадей служебных и бытовых помещений. | ||
4. | Проектирование вспомогательных отделений | ||
Всего |
* Согласно рабочей программе
Порядок организации проведения практических занятий (работ)
Требования к технике безопасности. Инструктаж
При выполнении практических работ необходимо соблюдать правила требований к технике безопасности согласно следующим инструкциям:
- ИОТ 01/03-2008 «Инструкция по охране труда для пользователей персональным компьютером».
Инструктаж проводится на рабочем месте, после чего студент оставляет отметку об ознакомлении с правилами охраны труда в журнале инструктажа.
Выполнение заданий
Студент приступает к выполнению задания по мере ознакомления с целью, задачами, требованиями к практической работе. По мере выполнения задания преподаватель останавливает самостоятельную работу студентов с методическими указаниями для оценки эффективности принятых студентом решений. Оценка может проводится коллективно в виде дискуссии при участии всех присутствующих на занятии, после чего самостоятельная работа студентов продолжается. Оценка проводится по разделам предусмотренным в методических указаниях по темам.
Представление результатов (оформление)
Результаты проведенной работы представляются преподавателю для проверки в машинописном, либо в рукописном виде.
Результаты должны быть четко сформулированными в результате анализа и расчетов. Для анализа задачи желательно использование таблиц, учитывающими влияющие факторы.
Критерии оценки
По результатам работы на занятии формируется отчет о проделанной работе. Преподаватель выставляет оценку «зачтено» или «не зачтено». Для получения оценки «зачтено» в отчете должны содержаться вывод, составленный на основе решения задачи, подробное решение поставленной задачи с обоснованием критериев выбора принятых решений. В случае получения оценки «не зачтено» необходимо провести работу над ошибками.
|
Практическая работа №1.
Тема: Планировка механического участка
Цель работы: Изучение методики разработки планировки механического участка по точной программе и нормативной удельной площади.
Задачи:
использование современных информационных технологий при проектировании машиностроительных производств
закрепление, углубление и обобщение теоретических знаний студента, полученных во время изучения курса, а так же приобретение практических навыков в профессиональной области.
Краткие сведения из теории
Исходными данными при разработке планировки участка (цеха) является:
- тип производства
- технологический процесс и технологичность конструкции.
Технологичность конструкции изделия – совокупность свойств изделия, определяющих
- приспособленность его конструкции к достижению минимальных затрат ресурсов при производстве, ремонте и эксплуатации
- для заданных показателей качества, объема выпуска и условий его изготовления.
Основным показателем производственной технологичности изделия является себестоимость его изготовления.
Пути обеспечения технологичности:
· снижение номенклатуры изготовляемых изделий путем унификации и стандартизации;
· уменьшение числа деталей в узлах за счет их объединения;
· развитие конструктивного подобия и унификация поверхностей и комплектов поверхностей с целью типизации технологических процессов;
· проработка конструктивных форм деталей для обеспечения необходимой точности, устойчивости и жесткости
· целенаправленное конструктивное оформление единых технологических баз, позволяющих изготовить детали при минимальном числе операций;
· конструирование деталей с учетом использования при их изготовлении минимальной номенклатуры стандартного инструмента;
· конструирование сборочных единиц с учетом возможности автоматической сборки
Основные показатели технологичности:
· Коэффициент серийности kc (определяется по таблице 1)
· Коэффициент унификации kу (зависит от числа поверхностей изделия)
· Коэффициент точности kт (определяется по таблице 2)
|
· Коэффициент использования материала kим (зависит от массы изделия)
Комплексный показатель технологичности сборочной единицы определяют по формуле
где ki — значения i-го частного показателя технологичности сборочной единицы; φi — коэффициент весомости i-го частного показателя технологичности сборочной единицы.
(Таблица 1)
(Таблица 2)
Производства
Масса детали, кг | Тип производства | ||||
единич. | мелкосер. | среднесер. | крупносер. | масс. | |
< 1,0 | < 10 | 10-2000 | 1500-100 000 | 75 000-200 000 | 200 000 |
1,0-2,5 | < 10 | 10-1000 | 1000-50 000 | 50 000-100 000 | 100 000 |
2,5-5,0 | < 10 | 10-500 | 500-35 000 | 35 000-75 000 | 75 000 |
5,0-10 | < 10 | 10-300 | 300-25 000 | 25 000-50 000 | 50 000 |
> 10 | < 10 | 10-200 | 200-10 000 | 10 000-25 000 | 25 000 |
Конструкцию машины или детали принято называть технологичной, если она позволяет в полной мере использовать для изготовления наиболее экономичный технологический процесс, обеспечивающий ее качество при надлежащем количественном выпуске. Являясь одним из свойств конструкции, технологичность дает возможность снизить трудоемкость изготовления изделия и его себестоимость. Опыт машиностроения показывает, что путем повышения технологичности конструкции машины можно получить дополнительно сокращение трудоемкости ее изготовления на 15 – 25 % и снижения себестоимости на 5 – 6 %. Это определяет важность учета возможностей технологии при конструировании машины, ее сборочных единиц и деталей.
Цель отработки конструкции детали на технологичность - выявление недостатков конструкции детали, а также возможное ее улучшение. Основные задачи анализа технологичности конструкции обрабатываемой детали сводятся к возможному уменьшению трудоемкости и металлоемкости, возможности обработки детали высокопроизводительными методами.
В общем случае, конструкция детали, отработанная на технологичность, должна удовлетворять следующим основным требованиям:
1) конструкция детали должна состоять из стандартных и унифицированных конструктивных элементов или быть стандартной в целом;
2) детали должны изготовляться из стандартных или унифицированных заготовок;
3) размеры и поверхности детали должны иметь соответственно оптимальные экономически и конструктивно обоснованные точность, шероховатость, обеспечивающие точность установки, обработки и контроля;
4) заготовки должны быть получены рациональным способом с учетом определенного ранее типа производства;
5) форма и габариты детали, основные и вспомогательные базы и их сочетания, схемы простановки размеров, конструктивные элементы, материалы, покрытия, требования и упрочнению должны максимально соответствовать принятым методам и средствам обработки;
|
6) конструкция детали должна обеспечивать возможность применения типовых технологических процессов ее изготовления.
Из-за большого разнообразия конструкций деталей и условий производства невозможно дать всеобъемлющие рекомендации по поводу того, какую конструкцию изделия считать технологичной. Некоторые примеры, поясняющие понятие технологичности, представлены на рисунке 4.1.
Организация технологического процесса. Расчет оперативного времени
Важным этапом при проектировании маршрутной технологии является выбор структуры операции по оперативному времени, от которого зависит производительность процесса изготовления изделия. В свою очередь, оперативное время tОП складывается из основного времени tО и вспомогательного времени tB, т. е.
Топ = tо + tв (1)
Основное время затрачивается на изменение размеров, формы, состояния поверхностного слоя (или других физико-механических свойств) полуфабриката или на изменение его положения при сборке.
Вспомогательное время затрачивается на приемы, сопутствующие изменению качественных характеристик полуфабриката. Оно складывается из следующих составляющих: времени, затрачиваемого на съем и установку полуфабриката tcу; времени вспомогательного перемещения инструментов — подводов, отводов, поворотов инструмента tви, времени вспомогательного перемещения полуфабриката tвп
tв = tсу + tви + tвп (2)
При рассмотрении временных структур выполнения операции можно выделить следующие способы их реализации: последовательный, параллельно-последовательный и параллельный. Рассмотрим их поподробнее
· Последовательная обработка. Она характеризуется последовательным протеканием основного и вспомогательного времени. При этом каждый режущий инструмент обрабатывает полуфабрикат последовательно по переходам, а времена, затрачиваемые на установ и съем полуфабриката, на смену, подвод и отвод инструмента, на вспомогательные перемещения полуфабриката, не совмещены между собой и с основным временем. Формула для подсчета оперативного времени будет иметь вид:
Tоп = Σ(tсу + tви + tвп) + Σtoi (3)
где toi – основное время на каждой операции.
· Последовательно-параллельная обработка. Она осуществляется параллельно-последовательным способом, вспомогательные приемы совмещены, а основные и вспомогательные приемы не совмещены, т. е. протекают последовательно во времени. Такая структура операции характерна для случая, когда ряд технологических переходов выполняется одновременно, а остальные последовательно. Основное время одновременно выполняемых нескольких переходов будет определяться по времени наиболее продолжительного перехода toj max, а вспомогательные времена на этих станках могут совмещаться. Формула для подсчета оперативного времени будет иметь вид:
TОП = Σ(tсу, tви, tвп)max + Σtoi + Σtoj max (4)
· Параллельная обработка. Она характеризуется параллельным способом выполнения всех основных и вспомогательных приемов, а также их совмещением во времени. Это значит, что все инструменты и на всех позициях, если их несколько, работают одновременно, а вспомогательные процессы совмещены со временем формообразования. Формула для подсчета оперативного времени будет иметь вид:
Tоп = Σ(tсу, tви, tвп, toi, Σtoj max)max (5)
Производительность основного оборудования зависит не только от оперативного времени, но и от структуры штучно-калькуляционного времени:
Tшт.к. = (tоп + tто + tоо + tен + tпз) (6)
где tто — время технического обслуживания оборудования, отнесенное к одному изготовляемому изделию (время на замену, настройку и поднастройку инструмента, устранение неисправностей и т. п.), мин; tоо — время, затрачиваемое на организационное обслуживание основного оборудования (время на подготовку оборудования к работе, простои, связанные с несвоевременным получением полуфабриката, сбои с доставкой инструмента и т. п.), мин; teн — время на отдых и естественные надобности оператора, мин; tпз — среднее подготовительно-заключительное время, затрачиваемое на подготовку к переналадке и саму переналадку основного оборудования, мин; n — размер партии полуфабрикатов.
В связи с отсутствием данных на начальном этапе проектирования величину размера партии запуска полуфабрикатов в первом приближении можно принять в зависимости от годового объема выпуска Nг:
Nг/100 — для мелких полуфабрикатов;
Nг/250 — для средних полуфабрикатов;
Nг/500 — для крупных.
Организация технологического процесса. Состав и количество основного оборудования в поточном производстве.
Одним из этапов технологического проектирования машиностроительного производства является определение состава и количества основного оборудования, которое должно обеспечивать высокую эффективность производственного процесса. При выборе состава основного оборудования следует ориентироваться на основные организационно-технические направления, причем следует иметь в виду, что за счет выравнивания времени выполнения операций одновременно достигается и сокращение количества основного оборудования.
Поточное производство характеризуется:
· незначительной номенклатурой выпуска продукции
· высокой интенсивностью технологических процессов, которая может быть достигнута только при использовании параллельной и параллельно-последовательной структуры выполнения операции, что следует учесть при выборе типажа оборудования.
· вследствие интенсивного развития техники необходима быстрая смена выпускаемой продукции, что, в свою очередь, также накладывает отпечаток на выбор основного оборудования для поточного производства, которое должно обеспечить возможность эффективного изготовления более широкой номенклатуры изделий. Этому требованию удовлетворяют агрегатные переналаживаемые станки с ЧПУ.
Расчет количества основного оборудования для поточного производства производится по точной программе и предусматривает разработку подробного технологического процесса обработки или сборки с техническим нормированием выполнения каждой операции на все изготовляемые изделия, входящие в программу выпуска.
Расчет числа станков, необходимых для каждой операции, выполняют на основании штучно-калькуляционного времени и объема выпуска каждого наименования изделия, проходящего эту операцию, по формуле:
(7)
где n — число наименований изделий, проходящих данную операцию; tшт.к. iNi — соответственно время изготовления изделия на данной операции, мин, и ее годовой объем выпуска, шт.; Фэ — эффективный годовой фонд времени работы основного оборудования, ч.
Штучно-калькуляционное время определяется по формуле (6), а при отсутствии данных по составляющим можно пользоваться формулой
tшт.к. i = tоп i(1 + α/100)
где α — процент потерь времени (внецикловых) от оперативного времени, α = 6...18% в зависимости от сложности наладки. При непрерывно-поточном производстве эта составляющая штучно-калькуляционного времени не учитывается, так как в данном случае отсутствует переналадка оборудования на другие наименования изделий.
Особенности расчета числа станков:
· Вычисленное значение Ср округляют до ближайшего большего целого числа, получая при этом количество основного оборудования Спр, принятое для выполнения данной операции.
· Обязательно рассчитывается коэффициент загрузки основного оборудования на данной операции k3 = Ср/Спр.
· Коэффициент загрузки всегда меньше единицы. Желательно, чтобы при проектировании поточного производства kз был больше 0,65.
При выборе состава и количества основного оборудования необходимо предусмотреть построение технологической системы в виде автоматической линии.
Классификация автоматических линий:
По технологическому назначению | · Однотипные - линии для выполнения операции одного типа (например, механообработка, сборка, окраска и т. д.) · Комбинированные - линии для выполнения операций различных типов (например, сборка изделий совместно с окраской на одном конвейере, механическая обработка со сборкой и т. д.) |
По типу используемого оборудования | · Из специального оборудования - используют в поточном производстве в том случае, когда изделия изготовляют в течение нескольких лет в большом объеме, что позволяет значительно сократить станкоемкость изготовления изделий · Из агрегатного и специализированного оборудования - применяют преимущественно в поточном производстве с более широкой номенклатурой выпускаемых изделий. · Из многоцелевого оборудования - используют в гибких производственных системах (ГПС). Они позволяют осуществлять быстрый переход с изготовления изделий одного типоразмера на изготовление изделий другого типоразмера |
Вследствие того, что в поточном производстве используют специальное оборудование и автоматические линии, очень важен выбор оптимальной структурно-компоновочной схемы оборудования, на базе которой выдается техническое задание на его проектирование.
Основание выбора: обычно производится при комбинаторном, пошаговом решении задачи с поиском оптимального варианта.
Критерий оптимальности: минимум приведенных затрат, который учитывает:
- объем выпускаемой продукции,
- станкоемкость выполнения переходов при изготовлении изделия,
- нормативный коэффициент экономической эффективности,
- потери времени на отказы оборудования, зависящие от его сложности,
- затраты на заработную плату обслуживающего персонала,
- стоимость оборудования и ряд других факторов.
Ограничения: условия обеспечения требуемого качества изделий и производительности. Важным этапом проектирования автоматической линии является разработка структурно-компоновочного варианта линии, обеспечивающего наилучшие технико-экономические показатели. Поэтому из множества вариантов построения линии, отличающихся числом позиций, участков, потоков, типом накопителей, должен быть выбран один, который обеспечит заданную производительность при минимальных приведенных затратах. Эти затраты рассчитываются по формуле:
Сп = KiEн + Сi
Сп → min
где Ki — стоимость оборудования i-го варианта; Ен — нормативный коэффициент эффективности капитальных вложений; Ci — годовые эксплуатационные затраты для данного варианта (себестоимость годового выпуска изделий).
Зависимость типа оборудования от годовой программы выпуска изделий и их номенклатуры представлена на графике слева
1 — механизированная сборка;
2 — одно- и двухпозиционные роботизированные сборочные комплексы;
3 — круговые сборочные машины с цикловым программным управлением;
4 — линии с цикловым программным управлением;
5 — гибкие автоматические линии из одно- и двухпозиционных сборочных модулей;
6 — многоцелевые сборочные машины
После определения состава и количества основного оборудования разрабатывают технические задания на специальное оборудование. В условиях поточного производства количество специального оборудования составляет 30...80% от общего количества ОО.
Организация технологического процесса. Состав и количество основного оборудования в непоточном производстве.
При выборе состава основного оборудования для непоточного производства следует в первую очередь ориентироваться на результаты расчета экономической эффективности, а также учитывать возможность встраивания его в автоматический комплекс с учетом как автоматизации его загрузки и разгрузки, так и стыковки системы управления оборудования с централизованной ЭВМ. Таким образом, в состав участков непоточного производства следует включать оборудование, отвечающее заданным требованиям для конкретных условий изготовления продукции, при использовании которого будет достигнута минимальная себестоимость изготовления. Для ориентации при выборе состава оборудования в зависимости от типа производства можно пользоваться графиком, приведенным ниже
Из графика видно, что стоимость изготовления деталей в непоточном производстве в 5...9 раз выше, чем в поточном, что объясняется в основном высокой частотой переналадок, а следовательно, и повышением времени, затрачиваемого на их проведение. Использование автоматических комплексов с ЧПУ вместо универсального оборудования позволит сократить число операторов и повысить производительность труда в 4 раза и более.
Особенность определения количества основного оборудования в непоточном производстве, характеризующегося широкой и порой нестабильной номенклатурой выпускаемых изделий, заключается в том, что в большинстве случаев невозможно разработать технологические процессы на каждое наименование изделия. В то же время для расчета количества основного оборудования необходимо знать суммарную станкоемкость обработки или машиноемкость в условиях автоматизированной сборки по операциям TΣ, таким образом, количество основного оборудования:
(8)
Для расчета количества оборудования в непоточном производстве используют различные методы приведения программы выпуска изделий, сущность которых заключается в том, что суммарную станкоемкость или машиноемкость определяют для выбранных изделий-представителей в каждой группе изделий, на которые разрабатываются технологические процессы изготовления.
Первый метод. Поскольку известно значение машиноемкости в крайних интервалах (размах) и закон распределения (логарифмически нормальный), можно определить математическое ожидание машиноемкости по каждой операции и, умножив ее на число изделий, изготовляемых на данной операции, определить машиноемкость на годовую программу выпуска.
Второй метод. Трудоемкости изготовления изделий-представителей ТМi по типам используемого оборудования в технологическом процессе изготовления делят на массу Mi соответствующих изделий-представителей, определяют машиноемкость изготовления одного килограмма изделия, которую и принимают как среднюю для всей рассматриваемой группы.
Третий метод. Определяют общий коэффициент приведения knp, характеризующий отношение станкоемкости (машиноемкости) изготовления приводимого изделия к станкоемкости (машиноемкости) изделия-представителя.
Четвертый метод. Проектирование экспериментальных сборочных и механических производств выполняют по условной программе, так как для них характерна нестабильность номенклатуры выпускаемых изделий. В этом случае выбирают условные изделия, на которые имеются чертежи, в таком количестве, чтобы их масса была равна массе изделий, планируемых к выпуску в данном производстве
Пятый метод. При реконструкции или техническом перевооружении действующих цехов используют способ расчета количества основного оборудования, основывающийся на наличии заводских данных о станкоемкости изготовления изделий и планируемого снижения станкоемкости за счет внедрения прогрессивной технологии и повышения уровня автоматизации проектируемого производства.
Шестой метод. На стадии предпроектного периода при технико-экономическом обосновании проекта используют укрупненный способ определения количества основного оборудования, основанный на использовании технико-экономических показателей. При этом способе в качестве исходных данных должны быть известны показатели продукции по массе, габаритным размерам, сложности, точности и соответствующие нормативные технико-экономические показатели. Последние устанавливают на основании анализа изготовления аналогичных изделий на передовых заводах страны и за рубежом, проведенного специальными отраслевыми технологическими институтами. Суммарная машиноемкость изготовления всех изделий рассчитывается по формуле:
TΣ = ТнМиNkсер
где Тн — нормативная машиноемкость изготовления 1 т изделий, маш-ч; Ми — масса изделия, т; N — годовой объем выпуска данного изделия, шт.; kсер — коэффициент серийности (0,73 … 0,99)
Разработка планировки
Разработка планировки — сложный и ответственный этап проектирования, когда системно решаются вопросы осуществления технологических процессов, организации производства, экономики, техники безопасности, выбор транспортных средств, механизации и автоматизации производства, научной организации труда и
производственной эстетики.
Планировка участка (цеха) — это план расположения производственного, подъемно-транспортного и другого оборудования, инженерных сетей, рабочих мест, проездов, проходов и т. д.
Технологическая планировка производится при проектировании участков (цехов) и коренной перестройке (реконструкции) технологического процесса. При создании производственных участков возможны два варианта размещения технологического оборудования: линейный и круговой.
При создании производственных участков возможны два варианта размещения технологического оборудования: линейный и круговой.
Рисунок 1 – Варианты размещения станков относительно транспортных средств: а – продольное; б – поперечное; в – угловое; г – кольцевое.
При этом линейный вариант размещения оборудования может быть реализован при расположении оборудования вдоль, поперек трассы межоперационного транспорта и под углом к ней. Преимущества линейного способа размещения оборудования следующие: наличие свободных зон для обслуживания оборудования; рациональное размещение оборудования с учетом прямоугольной сетки колонн.
Наиболее удобное и распространенное расположение технологического оборудования — вдоль транспортной трассы.
Поперечное расположение применяют в случае, когда достигается лучшее использование площади или когда при продольном расположении получаются слишком длинные линии.
Под углом к транспортной трассе технологическое оборудование располагают
в случае, когда длина оборудования значительно превышает его ширину, например для расточных, продольно-фрезерных, продольно-строгальных, прутковых автоматов и револьверных станков. Такое расположение оборудования обеспечивает лучшее использование площадей. Револьверные станки и автоматы при прутковой работе ставят под углом 15—20° или несколько больше в зависимости от ширины и длины отводимой под них площади; при этом их располагают загрузочной стороной к транспортной магистрали.
Кольцевое расположение технологического оборудования целесообразно для многостаночного обслуживания с помощью промышленных роботов, работающих в цилиндрической системе координат, но создает трудности для использования межоперационного транспорта и инженерных коммуникаций, а также требует больших площадей.
Нецелесообразность размещения рядом станков, изготовляющих высокоточные и детали низкой точности.
Нецелесообразность размещения шлифовальных станков рядом со сборочным оборудованием.
При размещении технологического оборудования должны быть соблюдены нормы, регламентирующие ширину проходов и проездов (не магистральных), расстояние между станками и станков от стен и колонн.
Рисунок 2 – Варианты размещения станков
Правила и приемы размещения станков
1. Участки, занятые станками, должны быть, по возможности, наиболее короткими. В машиностроении длина участков составляет 40—80 м. Зоны заготовок и готовых деталей включаются в длину участка.
2. Технологические линии на участках располагают как вдоль пролетов, так и
поперек их.
3. Станки вдоль участка могут быть расположены в два, три и более рядов. При расположении станков в два ряда между ними оставляется проход для транспорта. При трехрядном расположении станков может быть два или один проход. В последнем случае продольный проход образуется между одинарным и сдвоенным рядами станков. Для подхода к станкам сдвоенного ряда (станки расположены друг к другу тыльными сторонами), находящимися у колонн, между станками оставляют поперечные проходы. При расположении станков в 4 ряда устраивают два прохода: у колонн станки располагают в один ряд, а сдвоенный ряд – посередине.
4. Станки располагают по отношению к проезду вдоль, поперек и под углом. Наиболее удобное расположение – вдоль проезда и при обращении станков к проезду фронтом.
При поперечном расположении станков затруднено их обслуживание (подача
заготовок, обмен инструментов, приемка деталей и т.д.) так как приходится предусматривать поперечные проходы для доставки деталей на тележках или электрокарах к рабочим местам.
Для лучшего использования площади револьверные станки, автоматы и другие станки для обработки прутковых материалов, а также протяжные, расточные, продольно фрезерные и продольно-шлифовальные станки располагают под углом.
Станки для прутковой работы ставят загрузочной стороной к проезду, а другие станки так, чтобы сторона с приводом была обращена к стене или колоннам, что удобнее для складирования заготовок и исключает поломку привода при транспортировке деталей.
Станки для прутковой работы размещают также в шахматном порядке, причем в этом случае необходимо обеспечить возможность подхода к ним с двух сторон.
5 Станки по отношению друг к другу располагают фронтом, «в затылок» и
тыльными сторонами. При расположении станков вдоль участка более выгодно используется площадь с тыльным расположением станков.
6 Крупные станки не следует устанавливать у окон, так как это приводит к затемнению цеха.
Таблица 1 – Нормативные расстояния по рисунку 2.
*Значения: в числителе для непоточного, в знаменателе — для поточного
производства.
Расстояния между станками, до стен и колонн здания:
1 Расстояния берутся от наружных габаритных размеров станков, включающих крайние положения движущихся частей, открывающихся дверок и постоянных ограждений станков.
2 Для тяжелых и уникальных станков (габаритом свыше 16000 Ч 6000 мм) необходимые расстояния устанавливаются применительно к каждому конкретному случаю.
3 При установке станков на индивидуальные фундаменты (жесткие или виброизолированные) расстояния станков от колонн, стен и между станками принимаются с учетом конфигурации и глубины фундаментов станков, колонн и стен.
4 При разных размерах двух рядом стоящих станков расстояние между ними принимается по большему из этих станков.
5 При обслуживании станков мостовыми кранами или кран - балками расстояние от стен и колонн до станков принимают с учетом возможности обслуживания станков при крайнем положении крюка крана.
В зависимости от условий планировки, монтажа и демонтажа станков нормы расстояний могут быть, при соответствующем обосновании, увеличены.
Основные требования к оформлению планировок.
Планировка оформляется согласно требований ЕСКД. Элементы здания на технологической планировке можно не штриховать. Строительные размеры конструкций здания, оконных и дверных проемов и т. п. на технологических планировках не указывают.
На планировке показываются:
— строительные элементы: стены наружные и внутренние, колонны, перегородки (с указанием их типа), дверные и оконные проемы, ворота, подвалы, тоннели, основные каналы, антресоли, люки, галереи и т. п.;
—технологическое оборудование и основной производственный инвентарь: расположение станков, машин и прочих видов обор
|
|
Опора деревянной одностоечной и способы укрепление угловых опор: Опоры ВЛ - конструкции, предназначенные для поддерживания проводов на необходимой высоте над землей, водой...
Адаптации растений и животных к жизни в горах: Большое значение для жизни организмов в горах имеют степень расчленения, крутизна и экспозиционные различия склонов...
Особенности сооружения опор в сложных условиях: Сооружение ВЛ в районах с суровыми климатическими и тяжелыми геологическими условиями...
Типы сооружений для обработки осадков: Септиками называются сооружения, в которых одновременно происходят осветление сточной жидкости...
© cyberpedia.su 2017-2024 - Не является автором материалов. Исключительное право сохранено за автором текста.
Если вы не хотите, чтобы данный материал был у нас на сайте, перейдите по ссылке: Нарушение авторских прав. Мы поможем в написании вашей работы!