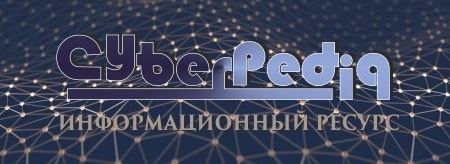
Таксономические единицы (категории) растений: Каждая система классификации состоит из определённых соподчиненных друг другу...
Типы оградительных сооружений в морском порту: По расположению оградительных сооружений в плане различают волноломы, обе оконечности...
Топ:
Оценка эффективности инструментов коммуникационной политики: Внешние коммуникации - обмен информацией между организацией и её внешней средой...
Процедура выполнения команд. Рабочий цикл процессора: Функционирование процессора в основном состоит из повторяющихся рабочих циклов, каждый из которых соответствует...
Интересное:
Финансовый рынок и его значение в управлении денежными потоками на современном этапе: любому предприятию для расширения производства и увеличения прибыли нужны...
Уполаживание и террасирование склонов: Если глубина оврага более 5 м необходимо устройство берм. Варианты использования оврагов для градостроительных целей...
Подходы к решению темы фильма: Существует три основных типа исторического фильма, имеющих между собой много общего...
Дисциплины:
![]() |
![]() |
5.00
из
|
Заказать работу |
|
|
Логистическая концепция организации производства. Производственный цикл изготовления изделия. Производственный цикл. Длина производственного цикла. Продолжительность производственного цикла. Расчет и анализ продолжительности производственного цикла простого процесса.
Производственный процесс представляет собой совокупность отдельных процессов труда и естественных процессов, в результате которых исходные материалы превращаются в готовые изделия.
Процесс изготовления отдельных детале-сборочных единиц (ДСЕ) называется простым процессом, а процесс производства изделий – сложным.
Производственный процесс протекает в пространстве и во времени. Его рациональное осуществление в пространстве обеспечивается рациональной производственной структурой участка, цеха, предприятия. А согласование и планомерное протекание во времени – правильным построением его производственного цикла.
Производственным циклом Тп называется календарный период времени от начала до окончания производственного процесса.
Основные задачи в организации производственного процесса во времени: выбрать наиболее рациональный способ передачи ДСЕ с операции на операцию (вид движения ДСЕ), определить длительность производственного цикла простого процесса по отдельным ДСЕ на этапе заготовительных работ, механообработки и др. и длительность цикла сложного процесса изготовления изделия с тем, чтобы можно было определять сроки запуска ДСЕ в производство.
Простой процесс. Производственный цикл простого процесса складывается из следующих составляющих:
Тп=Тт+Тпер+Те, (2.1)
Где Тт – технологический цикл обработки ДСЕ;
Тпер – межоперационные перерывы и перерывы, связанные с режимом работы;
|
Те – естественные процессы.
Технологический цикл состоит из операционных циклов. Операционный цикл - это продолжительность обработки партии ДСЕ на данной, i -й операции;
(2.2)
где n – размер партии ДСЕ, шт.;
ti – штучно-калькуляционная норма времени на операцию, мин/шт.;
сi – число рабочих мест на i -й операции.
Технологический цикл многооперационного процесса не есть арифметическая сумма операционных циклов. Его величина зависит от способа передачи ДСЕ с операции на операцию (вида движения). Идея о видах движения: последовательном, параллельно-последовательном, параллельном, являющаяся фундаментом теории организации производственных процессов, принадлежит профессору Ленинградского политехнического института О.И.Непоренту.
При последовательном виде движения каждая последующая операция над партией ДСЕ начинается только после обработки всех ДСЕ на предыдущей операции. Таким образом, партия не дробится, технологический цикл определяется (рис.2.1) так:
Рис.2.1 График технологического цикла при последовательном движении
Время в последовательном движении определяется по формуле 4.3.
(2.3)
При параллельно-последовательном виде движения партия ДСЕ в n штук обрабатывается на каждой операции непрерывно, но с операции на операцию передается частями – передаточными партиями в р штук. Это обеспечивает сокращение технологического цикла за счет частичного совмещения времени выполнения смежных операций. (рис.2.2):
(2.4)
где - совмещение операционных циклов между i -й и (i+ 1)-й операциями вследствие работы передаточными партиями.
Анализ и
на рис. 2.2 показывает, что в общем случае
определяется по формуле:
= p
(2.5)
где р – размер передаточной партии, шт.;
- время выполнения (с учетом числа рабочих мест) более короткой операции при сравнении двух смежных операций.
Так, из операций №1 и 2 более коротким операционным циклом обладает первая, из операций №2 и 3 – третья.
|
Рис.2.2. График технологического цикла при параллельном движении ДСЕ
Следовательно, вторая операция (поскольку она длиннее первой) может начаться сразу после окончания обработки на первой операции первой передаточной партии ДСЕ (р =2 шт.). Остальные передаточные партии успевают попасть на вторую операцию, не нарушая непрерывности их выполнения.
Но непрерывность обработки ДСЕ на третьей операции может быть достигнута лишь при накоплении перед ее началом минимально необходимого числа ДСЕ. Поэтому момент начала выполнения третьей операции графически может быть определен исходя из условия, что последняя передаточная партия со второй операции сразу поступает на третью, а все предыдущие передаточные партии должны быть непрерывно обработаны к этому моменту на третьей операции.
Подставив значение в формулу (2.4), получим выражение для расчета технологического цикла при параллельно-последовательном виде движения ДСЕ:
(2.6)
При параллельном виде движения передаточные партии передаются с предыдущей операции на последующую немедленно после окончания их обработки на предыдущей. Поэтому непрерывно выполняется только одна операция, имеющая наибольшую продолжительность. Но каждая передаточная партия движется по операциям непрерывно, не пролеживая в ожидании обработки (рис. 2.2).
Характеристики различных видов движения ДСЕ приведены в табл. 2.1.
Из графика видно, что
(2.7)
где - время выполнения с учетом числа рабочих мест самой продолжительной операции.
Таблица 2.1
Характеристика видов движения ДСЕ
Виды движения | Преимущества | Недостатки | Целесообразные области применения |
Последовательный | Простота планирования производства | Длительный цикл производства | Мелкосерийное, единичное производство при малых партиях ДСЕ и невсокой трудоемкости |
Параллельно-последовательный | Сокращение цикла производства | Увеличение числа планово-учетных единиц | Серийное производство |
Параллельный | Короткий цикл производства | При отсутствии синхронизации операций – простои оборудования | Крупносерийное и массовое производство |
Аналитический метод определение длительности производственного цикла обработки партий ДСЕ. В соответствии с формулой (2.1) от величины технологического цикла к величине производственного цикла, измеренной в рабочих днях, можно перейти, располагая данными о межоперационных перерывах в обработке партий ДСЕ и длительности естественных процессов:
|
(2.8)
где Тт – длительность технологического цикла обработки партии ДСЕ, определенная в зависимости от принятого вида движений партии ДСЕ по формулам (2.3), (2.6), (2.7), мин;
- время межоперационного перерыва между i -й и (i +1)-й операциями, мин.;
Тсм – продолжительность рабочей смены, мин.;
S – число смен в сутки.
Заметим, что межоперационное время максимально при последовательном виде движения может достигать величины технологического цикла, при параллельно-последовательном сокращается, а при параллельном виде движения отсутствует.
Существует несколько способов определения межоперационного времени, наиболее распространенным среди которых является использование регрессионного уравнения, полученного К.Г. Татевосовым [3]:
(2.9)
где - среднее межоперационное время, час;
- число детале-операций, выполняемых на одном рабочем месте, на участке или в цехе;
Определение длительности производственного цикла обработки партии ДСЕ на основе коэффициента характера производственного процесса.
Использование аналитического метода для расчета длительности производственного цикла обработки партии ДСЕ требует знания вида движения ДСЕ по операциям. В условиях многономенклатурного производства в машиностроении, когда одна и та же партия ДСЕ на участке на разных операциях может иметь разные виды движения, пользоваться аналитическим методом крайне сложно даже в условиях применения компьютеров.
Поэтому разработаны другие методы расчета длительности производственного цикла простого процесса. Одним из них является метод, базирующийся на использовании коэффициента характера производственного процесса ДСЕ:
(2.10)
где Кпар – коэффициент параллельности выполнения операций;
Кпот – коэффициент потерь времени при межоперационных пролеживаниях.
Как видим, формула (2.10) аналогична формуле (2.8). Но вид движения ДСЕ по операциям задается не явно, а устанавливается коэффициентами параллельности работ и потерь времени. Они, в свою очередь (табл. 2.2), определяются в зависимости от коэффициента характера производственного процесса Кхп, введенного в теорию организации производства профессором А. Ж. Огняновичем.
|
Таблица 2.2
Величины коэффициентов параллельности работ и потерь рабочего времени.
Характер производственного процесса | ![]() | ![]() | ![]() |
Массовый | 0,9-1,00 0,57-0,89 0,50-0,56 | 1/m | 1,05 1,10 1,15 |
Крупносерийный | 0,40-0,49 0,30-0,39 0,20-0,29 | 0,4 0,45 0,6 | 1,20 1,25 1,30 |
Среднесерийный | 0,14-0,19 0,10-0,13 0,05-0,09 | 0,6 0,65 0,70 | 1,35 1,40 1,5 |
Мелкосерийный | 0,04-0,049 0,033-0,039 0,025-0,032 | 0,80 0,85 0,90 | 1,55 1,60 1,65 |
Единичный | 0,013-0,024 0,011-0,012 0,000-0,010 | 0,93 0,96 1,00 | 1,70 1,75 2,00 |
Кхп показывает среднюю загрузку рабочих мест на участке конкретной ДСЕ в планируемом периоде, т.е. показывает характер (тип) производства этой ДСЕ на участке: массовый, серийный или единичный.
В упрощенном виде Кхп определяется по формуле
, (2.11)
где Кхп i – коэффициент характера производственного процесса на i-й операции обработки ДСЕ;
m – количество операций обработки ДСЕ на участке.
, (2.12)
где Ср i – расчетное количество рабочих мест на i-й операции.
, (2.13)
где Nсут – среднесуточная программа обработки ДСЕ на участке, шт.
Знание характера производственного процесса анализируемой ДСЕ позволяет правильно выбрать вид его движения (например, при Кхп=0,88 – параллельный). Форму организации производственного процесса, т.е. вид потока, решить другие вопросы организации производства и управления производством.
Используемая литература: осн. 1; доп.2.
Контрольные вопросы:
1. Длина производственного цикла.
2. Логистическая концепция организации производства.
3. Производственный цикл.
4. Длина производственного цикла.
5. Расчет и анализ продолжительности производственного цикла простого процесса.
6. Основные задачи в организации производственного процесса.
7. Технологический цикл многооперационного процесса.
8. Характеристика видов движения ДСЕ.
9. Аналитический метод определение длительности производственного цикла.
10. Как определяется Кхп?
11. Как определяется количество рабочих мест?
Тема лекции 3. Методы определения цикла сложного производственного процесса.
Определение длительности производственного цикла сложного процесса методами линейных (цикловых) графиков и сетевого планирования и управления.
Для определения цикла сложного производственного процесса (процесса изготовления изделия) в зависимости от наличия исходной информации используют разные по точности методы. В устойчивом производстве массового, крупносерийного, серийного типов существуют операционные нормы штучного времени. В мелкосерийном и единичном – укрупненные нормы времени на обработку ДСЕ. Поэтому в первом случае циклы изготовления изделий считают достаточно точно, во втором – приближенно, с определенной степенью вероятности.
|
![]() |
Рис. 3.1. Схема разузловки изделия М.
Рис.3.2 Линейный график изготовления М
Из точных методов рассмотрим методы линейных и сетевых графиков, из приближенных – корреляционно-регрессивный анализ, следует отметить, что первые два метода можно использовать и при наличии укрупненных норм времени на обработку отдельных составных частей изделия.
Определение длительности производственного цикла сложного процесса методом линейных (цикловых) графиков. Исходным документом для построения линейного графика изготовления изделия является разузловка изделия (рис. 3.1). Она показывает порядок входимости ДСЕ в изделие и маршруты их изготовления. Предварительно одним из рассмотренных выше методов определяют производственные циклы простых процессов. На рис. 3.1 длительность простых процессов в рабочих днях показана в правом нижнем углу. Межстадийные перерывы приняты равными одному дню. На рис. 3.2 приведен линейный график изготовления изделия М в календарных днях.
Для построения графика определяется самая длительная цепочка последовательно связанных между собой простых процессов и межоперационных перерывов. Она и определяет длительность цикла сложного процесса, т.е.
, (3.1)
где U – количество последовательных связанных между собой простых процессов;
- длительность производственного цикла простого процесса, рабочие дни;
- длительность перерыва между и -й и (и +1)-й стадиями, рабочие дни;
Так, для рассматриваемого процесса изготовления изделия М длительность цикла определяется в 14 рабочих дней:
Все другие цепочки простых процессов выполняются параллельно самой длинной (Тм-Ту-1-Тд-11) и имеют меньшую длительность, обладая резервами времени в начале выполнения первых процессов. Например, резерв времени для Д-1 составляет 14-9=5 дней.
Определение длительности производственного цикла сложного процесса методами сетевых графиков.
Четко определить величину резервов выполнения простых процессов в сложном процессе можно, используя при расчете цикла сложного процесса методы сетевого планирования и управления (СПУ).
Для этого надо перейти от схемы разузловки изделия к сетевому графику на изготовление изделия.
В сетевом графике (рис.3.3) выделяют два элемента: работы и события. Работами называют любые процессы, приводящие к достижению определенных результатов (событий). Например работа – 5,11. Кроме работ действительных, требующих затрат времени, существуют так называемые фиктивные работы. Это связь между событиями, не требующими затрат времени.
Рис. 3.3. Сетевой график на изготовление изделия М
Работа на графике изображена стрелкой, над которой указывается затрачиваемое время. Длина стрелки и ее ориентация на графике не имеют значения. Желательно только выдержать направление стрелок так, чтобы начальное событие для работы i располагалось слева на сетевом графике, а конечное j – справа. Для отображения фиктивных работ используют пунктирные стрелки, над которыми время не указывается или проставляется 0.
Таким образом, событие – это результат выполненной работы. Применительно к схеме разузловки изделия М события представлены ДСЕ, а работы – процессами их изготовления. Так, событие – это М,Д-1,У-1,Д-12 и т.д. Они связаны между собой работами, т.е. процессами изготовления этих ДСЕ и схемой разузловки. Поэтому работа Д-1,М – это изготовление Д-1, а работа Д-11,У-1 – это изготовление Д-11.
Для перехода от разузловки к сетевому графику изготовления изделия необходимо все события закодировать в цифровых кодах, соблюдая логику нахождения ДСЕ в разузловке изделия. Для более быстрого кодирования в разузловке следует выделить уровни входимости ДСЕ. В рассматриваемом примере изделий М их четыре:
- нулевой уровень – М;
- первый уровень – Д-1, У-1, У-2;
- второй уровень – Д-11, Д-12, Д-13, У-21, Д-21;
- третий уровень – Д-211, Д-212;
Начиная с третьего уровня, проводим кодирование событий (табл. 3.3)
Таблица 3.3 Кодирование событий
ДСЕ | Д-211 | Д-212 | Д-11 | Д-12 | Д-13 | Д-21 | У-21 | Д-1 | У-1 | У-2 | М |
Код события |
Вводим исходное событие с кодом 0 и завершающее – со следующим за 11-м, 12-м кодами. Получаем картотеку работ по изготовлению изделия М, где продолжительность работы Т i j, определена как сумма длительности соответствующей стадии и межстадийного времени в рабочих днях (табл. 4). Например, для работы 9,11 (изготовление У-1) продолжительность 1+5=6 рабочих дней.
Строим сетевой график: вначале отмечаем кружком нулевое событие, правее – события третьего уровня, еще правее – в соответствии со схемой разузловки и взаимосвязью ДСЕ события второго уровня, еще правее – события первого уровня и нулевого, т.е. 11-е событие, а за ним завершающее 12-е событие.
В соответствии со схемой разузловки соединяем события в работы. Так, работа 1,7 означает изготовление ДСЕ «Д-211» и ее пролеживание перед изготовлением ДСЕ «У-21». Поэтому продолжительность работы 1,7 составит (1+1)=2 рабочих дня. Эту величину проставляем над стрелкой, соединяющей события 1 и 7.
Таблица 3.4
Картотека работ на изготовление изделия М.
Работа | Содержание работы | Продолжительность, дни | |
i | j | ||
Фиктивная работа —“— —“— —“— —“— —“— Изготовление Д-211 Изготовление Д-212 Фиктивная работа Изготовление Д-11 Изготовление Д-12 Изготовление Д-13 Изготовление Д-21 Изготовление У-21 Изготовление Д-1 Изготовление У-1 Изготовление У-2 Изготовление М |
Все события, не имеющие входов (на рис.3.3 это 1,2,3,4,5,6,8), надо соединить фиктивными работами с нулевым событием, и сетевой график готов. Длина критического пути для данного случая равна – 14
Критический путь проходит через события: 0 3 9 11 12. Длина критического пути, т.е. самого большого пути, соединяющего исходное и завершающее события, и есть искомая длительность цикла изготовления изделия в рабочих днях. В графах Rп(i,j), Rс(i,j) представлены резервы времени, которыми обладают простые процессы изготовления ДСЕ, не попавшие в критический путь. Их можно использовать при установке сроков запуска-выпуска ДСЕ в обработку в соответствующих стадиях производства.
Определение длительности производственного цикла сложного процесса методами корреляционно-регрессионного анализа. В условиях единичного, мелкосерийного и зачастую серийного производства длительности циклов изготовления изделий целесообразно определять не точными, а приближенными методами, исходя из накопленной статистики прошлых лет.
В качестве такой статистики следует использовать отчетные данные о фактических циклах изготовления выпускавшихся ранее изделий в различных характеристиках производства, влияющих на длительность циклов. В табл. 3.5 представлена информация о таких характеристиках. Анализ статистических рядов (они обозначены через Х1,Х2,Х3,Х4,Х5,Х6) показывает, например, что чем больше масса изделия, тем больше цикл его изготовления. Но цикл уменьшается при увеличении доли унифицированных ДСЕ в общем количестве их и т.д. Эта связь параметров, выраженная не явно, а в среднем, называется корреляционной.
Исследованием степени устойчивости корреляционных связей занимается корреляционный анализ, а основным показателем степени тесноты связи является коэффициент парной корреляции . Он изменяется в пределах от –1 до +1. Знак «+» указывает на наличие прямой связи, знак «-» - на обратную связь чем выше значения коэффициента корреляции, тем теснее связь между переменными и тем с большим основанием найденная впоследствии связь может быть использована в прогнозировании.
Таблица 3.5
Статистические данные о циклах изготовления изделий и влияющих на них характеристиках
№ п/п | Шифр изделия | Цикл изготовления Х1, дни | Масса изделия Х2, т. | Количество входящих ДСЕ Х3, шт. | Доля унифицированных ДСЕ Х4, % | Трудоемкость изделия Х5, н/ч | Программа выпуска Х6, шт. |
АВС АВМ АВВ АВЕ АВФ АВК АВС АВН АВЕ АВС АВЕ АВР АВО | ? | 3,1 2,8 3,2 3,4 3,3 3,2 3,3 3,4 3,5 3,5 3,5 3,2 |
Корреляционные связи математически описываются уравнениями регрессии. Уравнение множественной линейной регрессии имеет вид:
х1 = в 1 + в2 х 2 +в 3х3 + в 4х4 + … +вр х р (3.2)
где в1 – свободный член;
в2,в3,…,вр – коэффициенты регрессии.
Для данных табл. 3.5 уравнение имеет вид:
Х1=86,72+5,57Х2+0,103Х3-1,25Х4+0,002Х5-11,4Х6 (3.3)
Имея это уравнение и зная параметры Х2,Х3,Х4,Х5,Х6 для нового изделия, можно прогнозировать длительность цикла этого изделия. Например, для изделия АВО цикл составляет 193 дня. Он получен при подстановке в уравнение 16 характеристик этого изделия из табл. 3.5;
Х1=86,75+5,57*3,2+0,103*1050-1,25*10+0,002*2200-11,4*1=193,19 раб. дн.
Используемая литература: осн. 1 [ 15-23 ]; доп.3.
Контрольные вопросы:
Тема лекции 4. Логистическая организация основного производственного процесса в пространстве и во времени.
Формы специализации основных цехов предприятия. Производственная структура основных цехов предприятия. Логистические процессы основного производства. Основные принципы управления производством.
Формы специализации основных цехов предприятий машиностроения (радиоэлектронного приборостроения) зависят от стадий, в которых происходят производственные процессы, а именно: заготовительной, обрабатывающей и сборочной. Соответственно специализация принимает следующие формы: технологическую, предметную или предметно-технологическую.
При технологической форме специализации в цехах выполняется определенная часть технологического процесса, состоящая из нескольких однотипных операций при весьма широкой номенклатуре обрабатываемых деталей. При этом в цехах устанавливается однотипное оборудование, а иногда даже близкое по габаритам. Примером цехов технологической специализации могут служить литейные, кузнечные, термические, гальванические и др.; среди механообрабатывающих цехов ― токарные, фрезерные, шлифовальные и др. В таких цехах, как правило, изготавливается вся номенклатура заготовок или деталей, либо если это сборочный цех, то в нем собираются все изделия, выпускаемые заводом.
Технологическая форма специализации цехов имеет свои преимущества и недостатки. При небольшом разнообразии операций и оборудования облегчается техническое руководство и создаются более широкие возможности регулирования загрузки оборудования, организации обмена опытом, применения рациональных технологических методов производства (например, литье под давлением, кокильное и центробежное литье и т. д.). Технологическая форма специализации обеспечивает большую гибкость производства при освоении выпуска новых изделий и расширении изготавливаемой номенклатуры без существенного изменения уже применяемых оборудования и технологических процессов.
Однако эта форма специализации имеет и существенные недостатки. Она усложняет и удорожает внутризаводское кооперирование, ограничивает ответственность руководителей подразделений за выполнением только определенной части производственного процесса.
По технологическому принципу преимущественно формируются цехи на предприятиях единичного и мелкосерийного производства, выпускающих разнообразную и неустойчивую номенклатуру изделий. По мере развития специализации производства, а также стандартизации и унификации изделий и их частей технологический принцип формирования цехов, как правило, дополняется предметным, при котором основные цехи создаются по признаку изготовления каждым из них определенного изделия либо его части.
Предметная форма специализации цехов характерна для заводов узкой предметной специализации. В цехах полностью изготавливаются закрепленные за ними детали или изделия узкой номенклатуры, например, одно изделие, несколько однородных изделий или конструктивно-технологически однородных деталей.
Для цехов с предметной формой специализации характерны разнообразные оборудование и оснастка, но узкая номенклатура деталей или изделий. Оборудование подбирается в соответствии с технологическим процессом и располагается в зависимости от последовательности выполняемых операций, т.е. используется принцип прямоточности. Такое формирование цехов наиболее характерно для предприятий серийного и массового производства.
Предметная форма специализации цехов, так же как и технологическая, имеет свои преимущества и недостатки. Преимущества: повышается производительность труда рабочих и ритмичность производства; снижается себестоимость продукции; рост прибыли и рентабельности; улучшение других технико-экономических показателей.
Недостатки: расширение номенклатуры выпускаемой продукции, увеличение разнообразия применяемого оборудования, дорогостоящая реконструкция.
Технологическая и предметная формы специализации в чистом виде используются довольно редко. Чаще всего на многих предприятиях машиностроения (радиоэлектронного приборостроения) применяют смешанную (предметно-технологическую) специализацию, при которой заготовительные цехи строятся по технологической форме, а обрабатывающие и сборочные цехи объединяются в предметно-замкнутые цехи или участки.
Под производственной структурой цеха понимают состав входящих в него производственных участков, вспомогательных и обслуживающих подразделений, а также связи между ними. Эта структура определяет разделение труда между подразделениями цеха, т.е. внутрицеховую специализацию и кооперирование производства.
Производственный участок как объединенная по тем или иным признакам группа рабочих мест представляет собой структурную единицу цеха, которая выделяется в отдельную административную единицу и возглавляется мастером при наличии в одну смену не менее 25 рабочих.
Рабочее место является первичным структурным элементом участка, это закрепленная за одним рабочим или бригадой рабочих часть производственной площади с находящимися на ней орудиями и другими средствами труда, в том числе инструментами, приспособлениями, подъемно-транспортным и иными устройствами соответственно характеру работ, выполняемых на данном рабочем месте.
В основу формирования производственных участков, так же как и цехов, может быть положена технологическая или предметная форма специализации.
При технологической специализации участки оснащаются однородным оборудованием (групповое расположение станков) для выполнения определенных операций технологического процесса. Так, механический цех может включать токарный, фрезерный, револьверный, сверлильный и другие участки.
Преимущества и недостатки технологической формы специализации участков такие же, как и при формировании цехов в соответствии с этой формой специализации. |
При предметной форме специализации цех разбивается на предметно-замкнутые участки, каждый из которых специализирован на выпуске относительно узкой номенклатуры изделий, имеющих схожие конструктивно-технологические признаки, и реализует законченный цикл их изготовления. Оборудование этих участков различное и располагается так, чтобы обеспечивалась более полная реализация принципа прямоточности движения закрепленных за участком деталей. В практической деятельности, как правило, выделяют три вида предметно-замкнутых участков:
•предметно-замкнутые участки по производству конструктивно и технологически однородных деталей (например, участки шлицевых валиков, пинолей, втулок, фланцев, шестерен и т.п.-);
•предметно-замкнутые участки по производству конструктивно разнородных деталей, весь технологический процесс изготовления которых состоит, однако, из однородных операций и одинакового технологического маршрута (например, участок круглых деталей, участок плоских деталей и т. п.);
•предметно-замкнутые участки по производству всех деталей узла, подузла мелкой сборочной единицы или всего изделия (применяется покомплектная система оперативного планирования, в которой за планово-учетную единицу принимается узловой комплект).
Организация предметно-замкнутых участков обусловливает почти полное отсутствие производственных связей между участками, обеспечивает экономическую целесообразность использования высокопроизводительного специализированного оборудования и технологической оснастки, позволяет получать минимальную продолжительность производственного цикла изготовления деталей, упрощает управление производством внутри цеха. Другие преимущества и недостаткипредметной формы специализации участков аналогичны преимуществам и недостаткам при формировании цехов по этой форме специализации.
В цехах предметной специализации могут быть созданы участки как предметной, так и технологической специализации, а в цехах технологической специализации ― участки технологические, сформированные по группам оборудования и габаритам изделий.
Важной частью производственной структуры цеха является состав вспомогательных и обслуживающих подразделений. К ним относятся: участок ремонта оборудования и технологической оснастки, участок централизованной заточки инструмента. Эти участки разгружают вспомогательные цехи (ремонтно-механический, инструментальный и др.) от выполнения мелких заказов и срочных работ.
В состав обслуживающих структурных подразделений цехов основного производства входят: складские помещения (материальные и инструментальные кладовые), внутрицеховой транспорт (тележки, электрокары, конвейеры и др.) и пункты для осуществления технического контроля качества продукции, оснащенные контрольно-измерительной техникой.
Логистическая концепция организации производства, характерная для «рынка покупателя», включает в себя следующие основные положения:
· отказ от избыточных запасов;
· отказ от завышенного времени на выполнение основных транспортно-складских операций;
· устранение нерациональных внутризаводских перевозок;
· отказ от изготовления серий деталей, на которые нет заказа покупателей;
· устранение простоев оборудования;
· обязательное устранение брака;
· превращение поставщиков из противостоящей стороны в доброжелательных партнеров.
Традиционная концепция организации производства, характерная для «рынка продавца», предполагает:
· никогда не останавливать основное оборудование и поддерживать во что бы то ни стало высокий коэффициент его использования;
· изготавливать продукцию как можно более крупными партиями;
· иметь максимально большой запас МР «на всякий случай».
Производство в условиях рынка может выжить лишь в случае, если оно способно быстро менять ассортимент и количество выпускаемой продукции. В традиционной концепции производства эта задача решается за счет наличия на складах запасов ГП. Логистическая концепция предусматривает адаптацию к изменению спроса за счет запаса производственной мощности, который может быть обеспечен за счет количественной или качественной гибкости производственных систем.
Характеристику типа производства дополняет характеристика производственного цикла. Производственный цикл — это период времени между моментами начала и окончания производственного процесса применительно к конкретной продукции в рамках логистической системы (предприятия). Производственный цикл состоит из рабочего времени и времени перерывов при изготовлении продукции. В процессе организации производства важно изначально определить оптимальную партию изделий. Оптимальная партия изделий (продукции) представляет собой партию, при которой затраты в расчете на одно изделие составляют минимальную величину. На практике часто оптимальная партия определяется прямым счетом, но при формировании логистических систем более эффективным является применение методов математического программирования. В предыдущей лекции по организации производственного процесса во времени мы познакомились с методами расчета длительности производственного цикла обработки изделия в целом и партии детале-сборочных единиц (ДСЕ) на участке предприятия. Этот параметр тесно связан с другими параметрами организации производства во времени: нормативным размером партии обрабатываемых ДСЕ, периодичностью запуска-выпуска партий ДСЕ в обработку на участке, уровнем заделов ДСЕ на участке и между смежными участками, а также системой опережений запуска-выпуска ДСЕ по отношению к выпуску готовых изделий.
Перечисленная совокупность параметров образует систему календарно-плановых нормативов (КПН) движения ДСЕ.
Используя КПН, рассчитанные для каждой ДСЕ, решают ряд задач о<
|
|
Своеобразие русской архитектуры: Основной материал – дерево – быстрота постройки, но недолговечность и необходимость деления...
Индивидуальные очистные сооружения: К классу индивидуальных очистных сооружений относят сооружения, пропускная способность которых...
Состав сооружений: решетки и песколовки: Решетки – это первое устройство в схеме очистных сооружений. Они представляют...
Двойное оплодотворение у цветковых растений: Оплодотворение - это процесс слияния мужской и женской половых клеток с образованием зиготы...
© cyberpedia.su 2017-2024 - Не является автором материалов. Исключительное право сохранено за автором текста.
Если вы не хотите, чтобы данный материал был у нас на сайте, перейдите по ссылке: Нарушение авторских прав. Мы поможем в написании вашей работы!