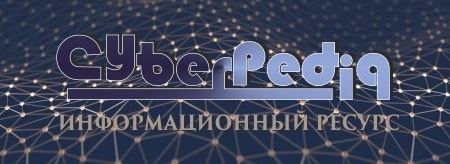
Историки об Елизавете Петровне: Елизавета попала между двумя встречными культурными течениями, воспитывалась среди новых европейских веяний и преданий...
Эмиссия газов от очистных сооружений канализации: В последние годы внимание мирового сообщества сосредоточено на экологических проблемах...
Топ:
Характеристика АТП и сварочно-жестяницкого участка: Транспорт в настоящее время является одной из важнейших отраслей народного...
Эволюция кровеносной системы позвоночных животных: Биологическая эволюция – необратимый процесс исторического развития живой природы...
Интересное:
Наиболее распространенные виды рака: Раковая опухоль — это самостоятельное новообразование, которое может возникнуть и от повышенного давления...
Принципы управления денежными потоками: одним из методов контроля за состоянием денежной наличности является...
Влияние предпринимательской среды на эффективное функционирование предприятия: Предпринимательская среда – это совокупность внешних и внутренних факторов, оказывающих влияние на функционирование фирмы...
Дисциплины:
![]() |
![]() |
5.00
из
|
Заказать работу |
|
|
Основные узлы и механизмы деревообрабатывающих станков
Все станки состоят из трех основных механизмов — двигательного (электродвигатель), передаточного и исполнительного. Передаточный механизм — совокупность устройств, служащих для передачи движения от двигателя к исполнительным органам — к столу, к суппорту с режущим инструментом, к шпинделю и т. д.
Станочное оборудование имеет ряд узлов и деталей, ко-торые предназначены для выполнения аналогичных для всех классов оборудования функций, хотя они и отличаются по кон-структивному исполнению.
К таким деталям и узлам станка относятся: станина — корпусная часть станка, на которой закрепляются остальные детали и узлы станка. Изготавливается литьем из чугуна или сваркой из стальных листов;
стол — часть станка, служащая для установки заготовки; суппорт — узел для закрепления заготовки или инструмента и передачи им движения;
шпиндель — вал, на котором закрепляется в патроне инструмент или заготовка.
Подшипник — опорная деталь из прочного сплава, используемая для уменьшения трения между движущимися элементами механизма. Они подразделяются на подшипники качения и подшипники скольжения. В подшипниках качения для передачи движения используются шарики или ролики, в подшипниках скольжения используется антифрикционный материал, вставляемый в виде цилиндра между поверхностями вращающейся и неподвижной детали.
Для передачи движения от двигателя к исполнительным механизмам служат передачи (рис. 4.28).
Фрикционная передача (рис. 4.28, а, б, в) пред-ставляет собой передачу, в которой вращательное движение передается с помощью сил трения, возникающего между дис-ками, конусами или колесами, насаженными на валы и при-жимаемыми друг к другу. Передача широко применяется в технике для исключения резких торможений и пусков (например, в автомобиле — диск сцепления, в радиоприемниках — диск настройки и т.д.).
|
Цепная передача осуществляется с помощью специальной цепи 3 и двух звездочек — 1 и 2 (например, в велосипеде).
Ременная передача осуществляется плоскими, клиновыми, иногда круглыми ремнями 2 через закрепленные на двух валах шкивы 1 и 3.
Зубчатая передача осуществляется с помощью зубчатых колес (шестерен), обеспечивает постоянное передаточное число и широко используется в металлорежущих станках.
Червячная передача состоит из червячного колеса 1 и червяка 2 и используется для резкого изменения скорости (до 300 раз).
Для преобразования вращательного движения в воз-вратно-поступательное наиболее часто применяются реечные, винтовые, кулачковые и кривошипные механизмы.?
Реечный механизм состоит из соединенных в пару рейки и зубчатого колеса.
При вращении колеса рейка совершает поступательное движение (например, в токарно-винторезном станке).
В винтовом механизме при вращении неподвижно ус-тановленного винта (или гайки) поступательное движение со-вершает вращающаяся гайка (или, соответственно, винт), со-единенная с исполнительным механизмом.
В кривошипном механизме вращающееся звено — кривошип или коленчатый вал приводит в возвратно
поступательное движение спаренные с ним (шарнирно) звенья (в приведенном примере вращательное движение кривошипа 1 передается через шатун 2 на двигающийся поступательно и свя-занный с исполнительным органом ползун 3).
В кулачковом механизме расположенные на распределительном валу вращающиеся выступы 1 — кулачки приводят в возвратно-поступательное движение соединенные с ними стойки 2.
Раскрои пиломатериалов
Существуют два способа раскроя досок. По первому способу, прежде чем раскраивать доску, производят ее разметку, с тем чтобы наиболее экономично выкроить из нее большее число деталей заданных размеров. Для того чтобы лучше вскрыть пороки древесины, не всегда хорошо видимые, и более наглядно произвести разметку, доски предварительно острагивают. При этом способе затрачивается лишнее время, но повышается процент использования древесины, что очень важно (особенно при раскрое досок из твердых лиственных ценных пород).
|
Рис. 1. Лобзиковый станок АЖС-3: 1 — станина, 2 — пилка, 3 — рабочий стол, 4 — педаль включения и выключения
Раскрой по второму способу производят без разметки. При раскрое без разметки рабочий сам определяет, как лучше выкроить заготовки, что требует большого навыка, а при ускоренных темпах работы и большого напряжения внимания.
Поперечный раскрой пиломатериалов
При поперечном безразметочном раскрое от доски прежде всего отрезают конец, если он имеет какой-либо дефект. Затем доску продвигают ца нужную длину до упора станка. Оценивая доски на глаз по размерам, качеству древесины и наличию пороков, станочник определяет, какую длину отрезать из числа заданных. Сделав второй рез, он укладывает полученный отрезок в штабель, расположенный рядом со столом; продвигает доску вновь на нужную величину и повторяет операцию.
Раскрой досок на круглопильных станках для поперечного распиливания без разметки производится с применением ограничителей (упоров).
При поперечном раскрое пиломатериалов на круглопильных станках в течение рабочего дня проходит большое количество сырья. На перемещение досок и отрезков затрачиваются большие физические усилия рабочего, обслуживающего станок. Поэтому процесс поперечного раскроя стараются механизировать. Прежде всего механизируется подача досок к пиле. Для этой цели подающий стол станка снабжают приводными роликами, по которым доска катится к направляющей линейке.
Доска подается по столу до концевого электрифицированного упора, установленного заранее на заданную длину заготовки. При нажатии торцом доски на концевой упор происходит отключение подающего стола и движение доски прекращается. Одновременно с этим электрифицированный привод производит подачу пильного диска на доску также на определенное (заданное) расстояние, соответственно ширине распиливаемого пиломатериала. При этом автоматически включается пусковое устройство обратного движения диска и пила возвращается.в исходное положение. При обратном движении пилы включается контакт механического сбрасывателя и отрезок перемещается на ленточный транспортер.
|
После сбрасывания заготовки концевой упор, освобожденный от давления торца доски, отжимается пружиной; при этом вновь приводится в действие подающий стол и все операции повторяются.
Продольный раскрой досок и отрезков
Раскрой на заданную толщину брусков производится при помощи направляющей линейки. Направляющую линейку следует устанавливать параллельно пильному диску. За линией оси диска линейка должна отступать от его плоскости на 1 мм, чтобы древесину не зажимало между расклинивающим ножом и линейкой.
Рекомендуется устанавливать направляющие линейки, перемещаемые рукояткой или с помощью штурвала.
Первый рез станочник производит на глаз, обрезая кромку с обзолом или вырезая дефектную часть бруска. Затем он распиливает брусок, плотно прижимая его к линейке. В том случае, когда из здоровой части доски можно выпилить узкий брусок, распил производят с применением закладки между линейкой и распиливаемой доской.
Станочник производит раскрой, устанавливает закладку, направляет и надвигает брусок на пилу. Подсобный рабочий помогает производить подачу бруска при пилении, укладывает получаемые заготовки и отходы, возвращает станочнику брусок для следующего реза.
Устройство токарных станков
Станина
Все узлы токарного станка монтируются на станине, стоящей на двух тумбах (ножках).
Станина (рис. 24) состоит из двух продольных стенок 2 и 8, соединенных для большей жесткости поперечными ребрами 1, и имеет четыре направляющие, три из которых призматические 3
и одна плоская 4. На левом конце станины 5 крепят переднюю бабку,-а на другом, на внутренней паре направляющих, устанавливают заднюю бабку. Заднюю бабку можно перемещать по направляющим вдоль станины и закреплять в требуемом положении. По двум крайним призматическим направляющим станины перемещается нижняя плита суппорта, называемая кареткой. Направляющие станины должны быть точно обработаны по рабочим плоскостям. Кроме того, направляющиe быть строго прямолинейными и взаимно параллельными, так как от этого зависит точность обработки деталей.
|
Передняя бабка
Передней бабкой называется часть токарного станка, служащая для поддержания обрабатываемой детали и приведения ее во вращение. В корпусе передней бабки в подшипниках скольжения или качения вращается шпиндель, который передает вращение обрабатываемой детали при помощи кулачкового или поводкового патрона, навертываемого на правый конец шпинделя с резьбой.
На наружной стенке корпуса передней бабки расположены рукоятки коробки скоростей (см. рис. 23), служащие для переключения числа оборотов шпинделя. Как надо повернуть эти рукоятки, чтобы получить нужное число оборотов шпинделя в минуту, указано на металлической табличке, прикрепленной на наружной стенке передней бабки.
Для предохранения зубчатых колес коробки скоростей от преждевременного износа переключение рукояток нужно производить только после выключения шпинделя, когда его скорость незначительна.
Шпиндель
Конструкция шпинделя. Шпиндель (рис. 25, а) является наиболее ответственной частью токарного станка. Он представляет собой стальной пустотелый вал 1, в коническое отверстие которого вставляют передний центр 5, а также различные оправки, приспособления и др. Сквозное отверстие 7 в шпинделе служит для пропускания прутка при выполнении прутковой работы, а также для выбивания переднего центра.
На переднем конце шпинделя нарезана точная резьба 4, на которую можно навернуть патрон или планшайбу, а за резьбой имеется шейка 6 с буртиком 3 для центрирования патрона; у станка 1А62, кроме того, имеется канавка 2 для предохранителей патрона, предотвращающих его самопроизвольное свертывание при быстром торможении шпинделя.
Шпиндель вращается в подшипниках передней бабки и передает вращение обрабатываемой детали. В токарных станках шпиндели обычно вращаются в подшипниках скольжения, но шпиндели скоростных станков вращаются в подшипниках качения (шариковых и роликовых), обладающих более высокой жесткостью по сравнению с подшипниками скольжения.
Одно из главных условий точной обработки деталей на токарных станках — это правильное вращение шпинделя. Необходимо, чтобы шпиндель под действием нагрузки не имел в подшипниках никакого люфта — ни в осевом, ни в радиальном направлениях — и вместе с тем равномерно, легко вращался. Наличие слабины между шпинделем и подшипниками вызывает биение шпинделя, а это в свою очередь приводит к неточности обработки, дрожанию резца и обрабатываемой детали. Устойчивость шпинделя обеспечивается применением нового типа массивных регулируемых подшипников качения.
|
Передний подшипник шпинделя. На рис. 25, в показано устройство переднего (правого) подшипника шпинделя токарного станка. Коническая шейка 8 шпинделя вращается в двухрядном роликовом подшипнике 9, получающем принудительную смазку от особого насоса, расположенного в коробке скоростей. Внутреннее коническое кольцо 10 роликоподшипника расточено по шейке шпинделя.
При регулировании подшипника ослабляют стопорный винт 11 и повертывают гайку 12, благодаря чему кольцо 10 перемещается вдоль оси. При этом в силу конусности шейки 8 зазор между нею и коническим кольцом изменяется. При повертывании гайки 12 вправо происходит затягивание подшипника, а при повертывании влево — его ослабление. Перемещение кольца 10 производят настолько, чтобы шпиндель с патроном можно было провернуть вручную. После регулирования затягивают стопорный винт 11, предохраняющий гайку 12 от отвертывания.
Задний подшипник шпинделя. Задний подшипник шпинделя нагружен значительно меньше переднего. Его главное назначение— воспринимать усилия, действующие на шпиндель в осевом направлении.
Задняя шейка шпинделя обычно вращается в коническом роликовом подшипнике 14 (рис. 25, б). Осевое усилие, действующее на шпиндель справа налево, воспринимается упорным шариковым подшипником 13, расположенным у задней опоры шпинделя. Если же осевое усилие направлено слева направо, стремясь как бы вытянуть шпиндель из коробки скоростей, то оно воспринимается коническим роликовым подшипником 14. Этот подшипник служит также опорой в поперечном направлении для заднего конца шпинделя. Регулируется он с помощью гайки 15 таким же образом, как и передний подшипник.
Задняя бабка
Задняя бабка служит для поддержания правого конца длинных деталей при обработке их в центрах. В ряде случаев она используется также для установки в ней сверл, разверток, метчиков и других инструментов.
Задняя бабка с обычным центром. Корпус 1 задней бабки (рис. 26, а) расположен на плите 9, лежащей на направляющих станины. В отверстии корпуса может продольно перемещаться пиноль 6 с закрепленной в ней гайкой 7. С переднего конца пиноль снабжена коническим отверстием, в которое вставляется центр 3, а иногда хвостовая часть сверла, зенкера или развертки. Перемещение пиноли 6 производится посредством маховичка 8, вращающего винт 5; винт при вращении перемещает гайку 7, а вместе с ней и пиноль. Рукоятка 4 служит для жесткого, закрепления пиноли в корпусе бабки. Посредством винтов 10 можно смещать корпус 1 относительно плиты 9 в поперечном направлении и тем самым смещать ось пиноли задней бабки относительно оси шпинделя. К этому прибегают иногда при точении пологих конусов.
Для обтачивания в центрах деталей разной длины плиту 9 перемещают вместе с корпусом задней бабки вдоль станины и закрепляют в нужном положении. Закрепление бабки на станине производится зажимными болтами или с помощью эксцентрикового зажима и скобы 11. Рукояткой 2 поворачивают эксцентриковый валик и отпускают или затягивают скобу 11. Отпустив скобу, передвигают заднюю бабку и, установив ее в нужном положении, снова затягивают скобу.
Чтобы удалить задний центр из конического гнезда пиноли, поворачивают маховичок 8 таким образом, чтобы втянуть пиноль в корпус задней бабки до отказа. В крайнем положении конец винта 5 выталкивает центр 3.
Задняя бабка со встроенным вращающимся центром. В токарных станках для скоростного резания находят применение задние бабки со встроенным вращающимся центром. На рис. 26, б показана одна из конструкций такой задней бабки.
В передней части пиноли 5 расточено отверстие, в котором запрессовывают подшипник 3 с коническими роликами, передний упорный шариковый подшипник 4 и задний шариковый подшипник 6 для втулки 2. Эта втулка имеет коническое отверстие, в которое вставляют центр 1. Осевая сила воспринимается упорным шарикоподшипником 6. Если при помощи стопора соединить втулку 2 с пинолью 5, втулка вращаться не будет. В этом случае в заднюю бабку можно установить сверло или другой центровой инструмент (зенкер, развертку).
Механизм подач
Механизм для передачи движения от шпинделя к суппорту (рис. 27) состоит: из трензеля I, предназначенного для изменения направления подачи; гитары II со сменными зубчатыми колесами, которая дает возможность совместно с коробкой подач получать различные подачи (крупные и мелкие); коробки подач III; ходового винта 1; ходового вала 2; фартука IV, в котором расположены механизмы, превращающие вращательное движение ходового вала и ходового винта в поступательное движение резца.
Не во всех станках имеются все перечисленные механизмы. Например, в станках, предназначенных исключительно для нарезания точных резьб, отсутствует коробка подач, подачи здесь изменяют сменой зубчатых колес на гитаре. С другой стороны, на некоторых станках узел подач имеет два реверсирующих механизма: один служит только для изменения направления вращения ходового винта (что требуется, например, для перехода от нарезания правых резьб к нарезанию левых резьб), а другой изменяет направление вращения ходового вала, изменяя таким образом направления продольной или поперечной подачи.
Трензель. На рис. 28 показан трензель, широко применявшийся в токарно-винторезных станках старых типов. На конце шпинделя закреплено зубчатое колесо 1, с которым посредством рычага А можно сцеплять либо колесо 4, либо колесо 2. Зубчатое колесо 2 находится постоянно в зацеплении с колесом 4 и с колесом 3. Если, повернув рычаг А вниз, сцепить с колесом 1 колесо 4, то вращение колесу 3 будет передаваться через два промежуточных колеса 4 и 2 (рис. 28, в). Повернув рычаг А вверх (рис. 28, а), сцепим колесо 1 непосредственно с колесом 2. В последнем случае колесо 5 получит вращение только через одно промежуточное колесо, следовательно, будет вращаться в другом направлении, чем в первом случае. Если рычаг А закрепить в среднем положении, как показано на рис. 28, 6, то зубчатые колеса 4 и 2 не сцепляются с колесом 1 и механизм подачи будет выключен.
В современных токарных станках применяются механизмы для направления движения, более удобные в отношении управления, чем описанный трензель. Схема современного реверсирующего Механизма, составленного из цилиндрических зубчатых колес, показана на рис. 29, а. На ведущем валу I закреплены на шпонках колеса z1 и z3. На ведомом валу II на шлицах скользит блок из двух колес z2 и z4, который может быть сцеплен либо с паразитным колесом z, либо с колесом z3(показано пунктиром). Таким образом, ведомый вал II получает вращение либо в одном, либо в другом направлении.
На рис. 29, б. показана другая конструкция реверсирующего механизма из цилиндрических колес. На ведущем валу I свободно сидит блок из двух колес 1 и 3 для сообщения прямого хода ведомому валу II и колесо 5— для обратного хода. Колеса 1, 3 и 5 могут быть жестко связаны с валом I при помощи пластинчатой фрикционной муфты М.
На ведомом валу II находится передвижной блок, состоящий из колес 2 и 4 — слева, и колесо 6, жестко закрепленное на шпонке, справа.
При включении фрикционной муфты М влево вал II получает два различных числа оборотов, осуществляя прямой ход; при включении муфты М вправо вал II получает обратное вращение через зубчатое колесо 5 — паразитное колесо 7 — колесо 6.
Коробка подач. У большинства современных токарно-винторезных станков имеются коробки подач; они служат для быстрого переключения скорости вращения ходового винта и ходового вала, т. е. для изменения подачи. Сменные же колеса у этих станков используются лишь тогда, когда требуемой подачи нельзя достигнуть переключением рукояток коробки подач.
Существует много различных систем коробок подач. Весьма распространенным типом является коробка подач, в которой применяется механизм накидного зубчатого колеса (рис. 30).
Первый валик 7 коробки подач получает вращение от сменных колес гитары. Этот валик имеет длинную шпоночную канавку 6, в которой скользит шпонка зубчатого колеса 3, расположенного в рычаге 2. Рычаг 2 несет ось 5, на которой свободно вращается накидное колесо 4, постоянно сцепленное с колесом 3. Посредством рычага 2 колесо 3 вместе с колесом 4 можно перемещать вдоль валика 7; поворачивая рычаг 2, можно сцепить накидное колесо 4 с любым из десяти колес зубчатого конуса 8, закрепленных на валике 9.
Рычаг 2 может иметь десять положений по числу колес зубчатого конуса 8. В каждом из этих положений рычаг удерживается штифтом 1, входящим в одно из отверстий передней стенки 15 коробки подач.
При перестановке рычага 2 благодаря сцеплению колеса 4 с различными колесами зубчатого конуса 8 изменяется скорость вращения валика 9. На правом конце этого валика, на скользящей шпонке, расположено колесо 10, имеющее на правом торце ряд выступов. В левом положении колесо 10 сцеплено с колесом 14, закрепленным на ходовом валу 13. Если колесо 10 сместить вправо, вдоль валика 9, то оно выйдет из зацепления с колесом 14 и торцовыми выступами сцепится с кулачковой муфтой 11, жестко сидящей на ходовом винте 12. При этом вал 9 будет непосредственно соединен с ходовым винтом 12. При включении ходового винта ходовой вал 13 остается неподвижным; наоборот, при включении ходового вала остается неподвижным ходовой винт.
На стенке коробки подач обычно имеется табличка, указывающая, какие именно подачи или какие шаги резьб получаются при каждом из десяти положений рычага 2 при определенном подборе «венных колес гитары.
Суппорт
Суппорт токарного станка (рис. 31) предназначен для перемещения резцедержателя с резцом в продольном, поперечном и наклонном к оси станка направлениях. Резцу можно сообщить движение вдоль и поперек станины как механически, так и вручную.
Нижняя плита 1 суппорта, называемая кареткой или продольными салазками, перемещается по направляющим станины механически или вручную, и резец движется в продольном направлении. На верхней поверхности каретки 1 имеются поперечные направляющие 12 в форме ласточкина хвоста, расположенные перпендикулярно к направляющим станины. На направляющих 12 перемещается нижняя поперечная часть 3 — поперечные салазки суппорта, посредством которых резец получает движение, перпендикулярное к оси шпинделя.
На верхней поверхности поперечных салазок 3 расположена поворотная часть 4 суппорта. Отвернув гайки 10, можно повернуть эту часть суппорта под нужным углом относительно направляющих станины, после чего гайки 10 нужно завернуть.
На верхней поверхности поворотной части расположены направляющие 5 в форме ласточкина хвоста, по которым при вращении рукоятки 13 перемещается верхняя часть 11 — верхние салазки суппорта.
Регулировка суппорта. После некоторого срока работы станка, когда на боковых поверхностях ласточкина хвоста появляется зазор, точность работы станка снижается. Для уменьшения этого зазора до нормальной величины необходимо подтянуть имеющуюся для этих целей клиновую планку (на рис. 31 не показана).
Излишний зазор, возникающий после некоторого периода работы между гайкой и поперечным ходовым винтом, следует также уменьшить до нормальной величины.
Как видно из рис. 32, гайка, охватывающая поперечный винт 1, состоит из двух половин 2 и 7. Для уменьшения зазора между гайкой и винтом до нормальной величины необходимо проделать следующее. Отвернуть слегка винты 3 и 6, при помощи которых обе половины гайки привинчены к нижней части суппорта, затем посредством винта 5 сдвинуть вверх односторонний клин 4, при этом обе половины гайки раздвинутся и зазор между поперечным винтом и гайкой уменьшится. Отрегулировав зазор, нужно снова затянуть винты. 3 и 6, крепящие обе половины гайки.
Резцедержатели. На верхней части суппорта устанавливают резцедержатель для закрепления резцов. Резцедержатели бывают различных конструкций.
На легких станках применяется одноместный резцедержатель (рис. 33, а). Он представляет собой цилиндрический корпус 1, в прорезь которого вставляют резец и закрепляют болтом 2. Резец опирается на подкладку 3, нижняя сферическая поверхность которой соприкасается с такой же поверхностью кольца 4. Такое устройство позволяет наклонять подкладку с резцом и устанавливать его режущую кромку по высоте центров. Нижняя часть 5 резцедержателя, имеющая Т-образную форму, вставляется в паз верхней части суппорта. Закрепление резца в резцедержателе данного типа производится быстро, однако недостаточно прочно, поэтому такой резцедержатель применяют главным образом для мелких работ.
Более прочно закрепляется резец в резцедержателе, показанном на рис. 33, б. Резцедержатель 5, снабженный Т-образным сухарем 1, закрепляется на верхней части суппорта гайкой 4. Для регулирования положения режущей кромки резца по высоте в резцедержателе имеется подкладка 2, нижняя сферическая поверхность которой опирается на такую же поверхность колодки резцедержателя. Закрепляют резец двумя болтами 3. Резцедержатель этого типа применяется как на малых, так и на больших станках.
На больших токарных станках применяются одноместные резцедержатели (рис. 33, б). В этом случае резец устанавливают на плоскость 7 верхней части суппорта и закрепляют планкой 2, затягивая гайку 4. Для предохранения болта 3 от изгиба планка 2 поддерживается винтом, опирающимся на башмак 6. При отвертывании гайки 4 пружина 1 приподнимает планку 2.
Чаще всего на токарно-винторезных станках средних размеров применяют четырехгранные поворотные резцовые головки (см. рис. 31).
Резцовая головка (резцедержатель) 6 устанавливается на верхней части суппорта 11; в резцедержателе можно закрепить винтами 8 четыре резца одновременно. Работать можно любым из установленных резцов. Для этого нужно повернуть головку и поставить требуемый резец в рабочее положение. Перед поворотом головки необходимо ее открепить, повернув рукоятку 9, связанную с гайкой, сидящей на винте 7. После каждого поворота головку нужно снова зажать с помощью той же рукоятки 9.
Фартук
К нижней поверхности каретки 1 (см. рис. 31) прикреплен фартук 17 — так называется часть станка, в которой заключены механизмы для продольного и поперечного перемещений резца (подачи) и механизмы управления подачи. Эти перемещения могут совершаться вручную или механически.
Поперечная подача резца производится перемещением нижней части 3 суппорта. Для этого рукояткой 14 вращают винт, гайка которого скреплена с нижней частью суппорта.
Маховичок 16 служит для сообщения суппорту вручную продольной подачи по направляющим станины. Для более точного механического перемещения суппорта пользуются ходовым винтом (рис. 34). Винт 1 приводится во вращение от коробки подач. По нему перемещается разъемная гайка 2 и 8, установленная в фартуке суппорта и называемая маточной. При нарезании резьбы резцом обе половины гайки 2 и 8 сближают при помощи рукоятки 5; они захватывают нарезку винта 1 так, что при его вращении фартук, а вместе с.ним и суппорт, получают продольное перемещение.
Механизм для сдвигания и раздвигания половин разъемной гайки устроен следующим образом. На валике рукоятки 5 (рис. 34) закреплен диск 4 с двумя спиральными прорезями 6, в которые входят пальцы 7 нижней 8 и верхней 2 половин гайки. При повороте диска 4 прорези заставляют пальцы, а следовательно, и половины гайки сближаться или расходиться. Половины гайки скользят по направляющим 3 фартука, имеющим форму ласточкина хвоста.
При всех токарных работах, кроме нарезания резьбы резцом, продольная подача осуществляется при помощи жестко скрепленной со станиной зубчатой рейки и катящегося по ней зубчатого колеса, установленного в фартуке (см. рис. 36 а). Это колесо получает вращение либо вручную, либо от ходового вала.
На токарном станке нельзя включать механизм продольной подачи от ходового вала одновременно с замыканием маточной гайки на ходовом винте: это ведет к неизбежной поломке механизма фартука или коробки подачи.
Для предотвращения таких неправильных включений на станке имеется специальный механизм, называемый механизмом блокировки.
Резцы токарные по дереву
Назначение токарных резцов и их виды
Токарные резцы по дереву – предназначенные для ручной обработки вращающейся в станке детали. Они состоят из двух основных частей: рабочей (металлической) и ручки (обычно деревянной). В свою очередь, рабочую часть можно условно разделить на:
· режущую (лезвие) – это та часть, которая затачивается и вступает во взаимодействие с заготовкой;
· тело – основная часть, за которую токарь удерживает резец «нерабочей» рукой на подлокотнике станка;
· хвостовик – зауженная часть, в которую плавно переходит тело. Хвостовик предназначен для крепления на нём ручки.
Ручку можно условно разделить на две части:
· основа – это большая часть, которую токарь держит в «рабочей» руке;
· шейка – маленькая цилиндрическая часть с металлическим крепёжным кольцом, которое предотвращает растрескивание ручки при набивании её на хвостовик рабочей части.
Виды токарных резцов
В зависимости от вида выполняемой работы, токарные резцы по дереву имеют различную конфигурацию, чем сложнее изделие, тем изощрённей будет и их конструкция, которая будет определять специфическую заточку лезвия. У каждого мастера могут быть свои особенные, эксклюзивные, узкоспециальные токарные инструменты, предназначенные для выполнения какой-то особенной работы. Поэтому изучать конструкцию каждого отдельного резца нет никакой необходимости.
Для успешной работы начинающего токаря достаточно будет двух видов: рейера и мейселя.
Из всех технологических операций, производимых над заготовками из металла, обработка на токарном оборудовании является наиболее распространенной. Именно поэтому заточка резцов для токарного станка, предназначенных для работы по металлу, является очень важным процессом, выполнять который следует правильно. Особенности осуществления такой процедуры зависят как от материала, который предстоит обрабатывать, так и от типа самого режущего инструмента (фасонный, проходной, резьбонарезной, расточной и другие).
Порядок заточки поверхностей резца
Самый важный элемент любого резца (в том числе и для токарного станка по металлу) — его режущая кромка — формируется в месте пересечения задней основной и передней поверхностей. В конструкции любого резца присутствует и вспомогательная кромка, образованная пересечением его задних поверхностей: основной и вспомогательной. Вершина инструмента, которая упоминается в специальной литературе, — это место пересечения его режущей и вспомогательной кромок.
Основными характеристиками токарных резцов по металлу, определяющими их функциональные возможности, являются углы заточки, подразделяемые на главные и вспомогательные. Для того чтобы определить значения главных, их измерение производят в плоскости, которая формируется при проецировании режущей кромки на главную плоскость.
Вообще, для определения углов режущего инструмента используют две плоскости:
· основную, накладываемую на опорную сторону токарного резца, расположенную в его нижней части (по отношению к направлению подач станка такая плоскость является параллельной);
· плоскость резания, располагаемую по касательной относительно поверхности обрабатываемой заготовки (данная плоскость пересекается с основной режущей кромкой инструмента).
Элементы и плоскости токарного резца
В конструкции рабочей части токарного резца различают углы нескольких типов:
· заострения — расположенные между передней поверхностью резца и задней основной;
· задние главные — находящиеся между задней основной поверхностью и плоскостью резания;
· передние главные — расположенные между передней стороной инструмента и плоскостью, перпендикулярной к плоскости резания.
Проверить правильность их определения достаточно просто: их сумма всегда составляет 90 градусов.
Кроме вышеперечисленных, конструкцию рабочей головки токарного резца характеризует еще несколько углов между:
· направлением подачи и проекцией, которую откладывает основная режущая кромка;
· плоскостью обработки и передней поверхностью резца;
· проекциями, которые откладывают основная и вспомогательная режущие кромки.
Инструменты для токарного оборудования
Для того чтобы разбираться в правилах заточки резцов для токарных станков по металлу, недостаточно просто посмотреть обучающее видео. Необходимо иметь представление о том, как классифицируются такие инструменты. Самым главным параметром, по которому токарные резцы относят к различным видам, является тип обработки, выполняемой с их помощью. По этому признаку выделяют следующие виды токарных резцов.
Основные типы токарных резцов
Проходные
Такими резцами заготовки обрабатываются вдоль оси вращения.
Подрезные
Используя эти резцы на токарном станке, уменьшают уступы и выполняют торцевание заготовок.
Канавочные
Как следует из названия, ими формируют наружные и внутренние канавки на поверхностях цилиндрической формы. Создавать канавки на наружных сторонах заготовок можно и при помощи отрезных резцов по металлу. Кроме того, такие резцы позволяют отрезать части заготовки под прямым углом.
Расточные
С помощью таких инструментов на станках выполняют обработку отверстий.
Резьбонарезные
Такие резцы специально предназначены для нарезания резьбы.
Фасонные
С помощью резцов этого вида на внешней стороне цилиндрических заготовок формируют фасонные выступы или канавки.
Фасочные
С помощью этих резцов на заготовках снимаются фаски.
Операции, проводимые резцами различного типа
Токарные резцы также подразделяются на виды в зависимости от того, в каком направлении с их помощью выполняется обработка заготовки. Так, среди них бывают правые (обработка выполняется по направлению к передней бабке) и левые (обработка по направлению к задней бабке).
Классифицируется токарный инструмент и по материалу изготовления, по способу соединения режущей части с державкой, а также по ряду других параметров.
Правила заточки токарного инструмента
Чтобы обработка заготовок на токарных станках по металлу была эффективной, качественной и точной, следует регулярно выполнять заточку резцов, тем самым придавая их рабочей части необходимую форму и получая углы с требуемыми параметрами. В заточке не нуждается только инструмент, режущая часть которого выполнена в виде одноразовой твердосплавной пластины. Для выполнения такой важной процедуры в условиях крупных производственных предприятий используются станки со специальными приспособлениями, а занимается этим отдельное структурное подразделение.
Для того чтобы заточить токарный инструмент своими руками на домашнем станке или сделать это в условиях небольшого предприятия, можно использовать различные методики. Выполнение этой процедуры возможно с помощью химических реактивов или с применением обычных точильных кругов. Следует отметить, что заточка токарного инструмента на специализированных или универсальных станках, в которых используется абразивный круг, является самым недорогим, но эффективным методом придания резцам требуемых геометрических параметров.
Варианты заточки резцов с режущими пластинами
Конечно, наиболее качественно токарные резцы по металлу затачиваются на специально предназначенном для выполнения такой процедуры станке. Если же подобного оборудования в вашем распоряжении нет, можно воспользоваться универсальным станком с точильным кругом. Подбирая такой круг, важно обращать внимание на материал, из которого изготовлена рабочая часть обрабатываемого инструмента. Так, чтобы эффективно заточить твердосплавный резец, вам понадобится круг из карборунда, имеющий характерный зеленый цвет. Инструменты, рабочая часть которых изготовлена из углеродистой или быстрорежущей стали, прекрасно обрабатываются на станках с кругами средней твердости, изготовленными из корунда.
Заточку токарных резцов по металлу м<
|
|
Опора деревянной одностоечной и способы укрепление угловых опор: Опоры ВЛ - конструкции, предназначенные для поддерживания проводов на необходимой высоте над землей, водой...
Состав сооружений: решетки и песколовки: Решетки – это первое устройство в схеме очистных сооружений. Они представляют...
Индивидуальные очистные сооружения: К классу индивидуальных очистных сооружений относят сооружения, пропускная способность которых...
Архитектура электронного правительства: Единая архитектура – это методологический подход при создании системы управления государства, который строится...
© cyberpedia.su 2017-2024 - Не является автором материалов. Исключительное право сохранено за автором текста.
Если вы не хотите, чтобы данный материал был у нас на сайте, перейдите по ссылке: Нарушение авторских прав. Мы поможем в написании вашей работы!