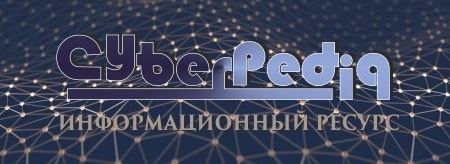
Семя – орган полового размножения и расселения растений: наружи у семян имеется плотный покров – кожура...
Типы оградительных сооружений в морском порту: По расположению оградительных сооружений в плане различают волноломы, обе оконечности...
Топ:
Когда производится ограждение поезда, остановившегося на перегоне: Во всех случаях немедленно должно быть ограждено место препятствия для движения поездов на смежном пути двухпутного...
Марксистская теория происхождения государства: По мнению Маркса и Энгельса, в основе развития общества, происходящих в нем изменений лежит...
Установка замедленного коксования: Чем выше температура и ниже давление, тем место разрыва углеродной цепи всё больше смещается к её концу и значительно возрастает...
Интересное:
Подходы к решению темы фильма: Существует три основных типа исторического фильма, имеющих между собой много общего...
Уполаживание и террасирование склонов: Если глубина оврага более 5 м необходимо устройство берм. Варианты использования оврагов для градостроительных целей...
Аура как энергетическое поле: многослойную ауру человека можно представить себе подобным...
Дисциплины:
![]() |
![]() |
5.00
из
|
Заказать работу |
|
|
ЛЕКЦИИ ПО ДЕТАЛЯМ МАШИН
Передачи в машинах и механизмах. Основные характеристики передач.
Для приведения в движение рабочих машин необходимо передать им энергию от двигателя. Вал двигателя с валом рабочей машины соединять не всегда целесообразно, поэтому между ними устанавливают устройства, называемые передачами. Передачи бывают механические, электрические, гидравлические и т.д. Мы будем изучать только механические передачи.
Механические передачи классифицируются по способу передачи движения [1, с. 299-302]:
а) – передача трением. Сюда относят фрикционные, ременные, канатные.
б) – передача зацеплением. Это зубчатые и червячные, винтовые, цепные.
Основные характеристики передач, необходимые для выполнения проектировочного расчета: мощность на входном (Р1) и на выходном (Р2) валах, угловая скорость входного (ω1) и выходного (ω2) валов, частота вращения (n1) и (n2). Кроме того, используются и производные характеристики: передаточное отношение, передаточное число, крутящий момент, коэффициент полезного действия [2, с. 135-136].
· Передаточным отношением u ij называется отношение угловых скоростей двух любых звеньев, номера которых обозначаются соответствующими индексами
u ij = ωi / ωj.
Передаточное отношение показывает, во сколько раз скорость вращения i –го звена (вала) больше или меньше скорости j –го звена.
· Передаточное число u – это более узкая характеристика передачи, применяется она для редукторов, либо ременных и цепных передач. Это понятие учитывает направление потока мощности, т.е. определяется всегда от входного вала к выходному, поэтому индексы в обозначении не ставятся, а величина передаточного числа всегда больше единицы.
|
u = ω1 / ω2 ≥ 1.
При расчете одноступенчатых цилиндрических редукторов величину передаточного числа определяют как отношение числа зубьев колеса Z2 к числу зубьев шестерни Z1.
u = Z2 / Z1
Шестерней называют меньшее из двух сопряженных зубчатых колес; она находится на входном валу и часто выполняется как одна деталь с валом (вал-шестерня).
Если передача движения от двигателя к рабочему органу машины осуществляется в несколько ступеней, например: ременная и зубчатая, несколько зубчатые ступеней, сочетание зубчатых и цепной передач и т. д., то в этом случае общее передаточное число механизма u определяется как произведение передаточных чисел отдельных ступеней
u = u1 ∙ u2 ∙ u3 ∙ …. ∙ un.
Как известно из физики, мощность при вращательном движении определяется произведением крутящего момента (Т) на угловую скорость
Р = Т ∙ ω.
Очевидно, что если угловую скорость на выходном валу снизить в u раз по сравнению с входным валом, то во столько же раз возрастает крутящий момент. Поэтому основное назначение всякого редуктора – не только снизить скорость до величины, заданной технологическим процессом, но и увеличить крутящий момент на выходном валу.
Коэффициент полезного действия (КПД), определяемый отношением мощностей выходного и входного валов η = Р2 / Р1, для многоступенчатых передач определяется по формуле
η = η1 ∙ η2 ∙ η3 ∙….∙ ηn,
где η1 , η2 , η3 …. ηn – КПД каждой кинематической пары (зубчатой, ременной, подшипников, муфт), т.е. соединений, в которых происходят потери мощности.
П Р И М Е Р – расчет энергосиловых параметров привода (практ. занятие – по своим заданиям, по методичкам рассчитать КПД, Рвых, крутящие моменты, диаметры валов, составить таблицу.
Передача трением
§ Фрикционная передача состоит из двух катков, насаженных на валы и прижатых силой Q. Движение передается благодаря силе трения Fтр, которая равна окружной силе F. Во избежание проскальзывания создают силу трения в k раз больше, чем окружная сила.
|
Достоинства фрикционных передач: простота конструкции, плавность работы, возможность плавного регулирования скорости. Передачи с переменной угловой скоростью ведомого вала называют вариаторами.
Недостатки: повышенный износ рабочих тел, непостоянство передаточного числа в связи с возможным проскальзыванием, сравнительно низкий КПД, большая нагрузка на валы и опоры, ограниченная передаваемая мощность.
Применяются фрикционные передачи в кузнечно-прессовом оборудовании, в лебедках, конвейерах.
Передача зацеплением
§ Цепная передача основана на зацеплении тягового органа, выполненного в виде цепи, со звездочками, представляющими собой колеса с зубьями специального профиля [1, с. 391-393]. Применяется цепная передача в тех случаях, когда надо передать вращение на большие расстояния без проскальзывания между валами.
Достоинства ее по сравнению с ременной: компактность, меньшие нагрузки на валы от натяжения цепи, более высокий КПД (до 0,98).
Недостатки: непостоянство передаточного числа и скорости выходного вала в пределах оборота звездочки и дополнительные динамические нагрузки; высокая стоимость, поэтому цепные передачи применяют при мощностях до 100 кВт. Передаточное число обычно не превышает 10, а скорость цепи – не более 25 м/с.
§ Зубчатые передачи – это наиболее распространенный тип механических передач. Движение передается посредством боковых поверхностей зубьев при наличии качения со скольжением. Основные достоинства зубчатых передач: высокий КПД (до 0,98), компактность по сравнению с ременными и цепными, большой диапазон передаваемых мощностей (от десятых долей до десятков тысяч киловатт). К недостаткам можно отнести шум, особенно при высоких скоростях; сложность изготовления в сравнении с ременными передачами.
Зубчатые передачи делятся по признаку взаимного расположения осей на цилиндрические, которые передают вращение между параллельными осями; конические – для передачи вращения между пересекающимися осями; червячные – для передачи вращения между перекрещивающимися осями.
Виды разрушения зубьев
В процессе работы на зубья действует циклическая нагрузка, а также контактные и изгибающие напряжения.
|
Повторно-переменные напряжения вызывают усталостное выкрашивание зубьев. Давление смазки способствует развитию микротрещин, начинается «питтинг», искажается профиль зуба, прогрессирует износ. Это основной вид закрытых передач.
При заклинивании, которое возникает из-за нагрева передачи, частицы металла как бы привариваются одна к другой, и отрываясь от поверхности, образуют задиры. При загрязнении смазки твердые частицы способствуют истиранию поверхностей зубьев. Износ – это основной вид разрушения открытых передач.
Поломка зубьев – возникает вследствие деформации изгиба, ударного, а также усталостного разрушения грубой обработки, длительного действия переменных нагрузок [4, с. 296-297].. Для надежной эксплуатации зубчатых передач имеет большое значение точность изготовления, правильность монтажа, доброкачественная смазка.
Пространственные передачи
Коническая передача.
Червячная передача
Оси и валы
Подшипники.
Выбор типа подшипника
Подшипники качения представляют собой сборочную единицу или узел, основными деталями которого служат тела качения – шарики или ролики различной формы, установленные между кольцами, и сепаратор, разделяющий тела качения Внутреннее кольцо насаживается на вал, наружное – устанавливается в корпусе машины.
По форме тел качения подшипники бывают шариковые и роликовые; по направлению воспринимаемой нагрузки – радиальные, радиально-упорные; по числу тел качения – однорядные и многорядные [4, с.413-417].
Для опор цилиндрических прямозубых и косозубых колес редукторов и коробок передач применяют чаще всего шариковые однорядные радиальные подшипники. Если по расчету получаются чрезмерно большие размеры, то используют конические роликовые подшипники. Конические и червячные колеса должны быть жестко и точно зафиксированы в осевом направлении. Поэтому в силовых передачах для опор валов конических и червячных колес применяют конические роликовые подшипники. Первоначально выбирают легкую серию [4, с. 49-53]. Для опор конического вала-шестерни применяют конические роликовые, а при частоте вращения n > 1500 об/мин шариковые радиально-упорные подшипники.
|
Опоры червяка нагружены значительными осевыми силами, поэтому используют в основном конические роликовые подшипники, при длительной непрерывной работе применяют также шариковые радиально-упорные подшипники.
Для опор плавающих валов шевронных передач применяют радиальные подшипники с короткими цилиндрическими роликами; первоначально при проектировании также выбирают легкую серию.
Основные критерии работоспособности подшипников качения – это статическая и динамическая грузоподъемность. Расчет на статическую грузоподъемность имеет смысл делать только при частоте вращения до
10 об/мин, в остальных случаях подшипники подбирают по динамической грузоподъемности. При этом определяют номинальный ресурс в млн. оборотов
,
где С – динамическая грузоподъемность по каталогу, кН;
Р – эквивалентная нагрузка, кН;
р – показатель степени: для шарикоподшипников р = 3, для роликоподшипников р = 10/3.
Номинальная долговечность в часах
.
Эквивалентная нагрузка определяется в зависимости от типа подшипника и от соотношения осевой и радиальной силы [3, с. 211-220].
По ГОСТ 16162-85 минимальная долговечность подшипников для зубчатых редукторов Lh = 10 000 ч., для червячных – 5000 ч.
Если первоначально выбранный по посадочному диаметру подшипник легкой серии не удовлетворяет расчетам на долговечность, то переходят к средней серии того же диаметра.
Если вычисленный ресурс (долговечность) подшипников шариковых и радиальных с цилиндрическими роликами значительно выше, чем каталожное значение, даже для легкой серии, то диаметр цапфы вала не следует уменьшать, т.к. он определен из расчета на прочность. Расчетная долговечность в этом случае будет превышать регламентированную.
Для радиально-упорных шариковых и конических роликовых подшипников выбор осуществляется иначе: если долговечность меньше требуемой, то выбирают подшипники других серий и типов; в этом случае увеличивают диаметр цапфы вала[3, с. 221-223].
Схемы установки подшипников
По способности фиксировать осевое перемещение вала различают опоры фиксирующие и плавающие. Фиксирующие ограничивают осевое перемещение вала в одном или в обоих направлениях; они воспринимают и радиальную и осевую нагрузку. Плавающие опоры воспринимают только радиальную нагрузку.
При выборе опор учитывают следующие рекомендации: если на вал действует не только радиальная, но еще и осевая сила, то в качестве плавающей выбирают опору, нагруженную большей радиальной силой. Если имеются только радиальные силы, то осевое перемещение плавающей опоры, обусловленное температурными деформациями вала, вызывает повышенный износ. Поэтому в таких случаях в качестве плавающей выбирают менее нагруженную опору.
|
Если вал зафиксирован в двух опорах, причем в каждой опоре - только в одном направлении, то возможны две схемы установки подшипников: враспор или врастяжку.
При установке враспор наружные кольца подшипников упираются в крышки, а внутренние кольца – в буртики вала. Во избежание защемления вала вследствие температурных деформаций предусматривают небольшой зазор а = 0,2…0,5 мм [3, с.181-182]. Применяется такая схема при относительно коротких валах (отношение l / d ≈8…10).
|
При схеме врастяжку вероятность защемления подшипников меньше, т.к. при увеличении длины вала осевой зазор в подшипниках увеличивается. Для шариковых радиальных подшипников l / d ≈ 10…12 [5, с.52-53].
|
Регулирование зазоров в подшипниках производится за счет перемещений внутренних или наружных колец.
Схема установки враспор может применяться в цилиндрических прямозубых, косозубых, конических, червячных передачах при небольшой длине валов.
Опоры конической шестерни преимущественно устанавливают врастяжку. Это обусловлено тем, что расстояние от опор до точки зацепления несколько меньше по сравнению со схемой враспор. Подшипники устанавливают в специальном стакане, по одну сторону от шестерни. Осевая регулировка производится при помощи набора прокладок между торцом стакана и корпусом редуктора.
В редукторах с шевронными колесами подшипники тихоходного вала фиксируют, а быстроходный вал выполняют плавающим. Осевая фиксация передачи осуществляется самим зубчатым зацеплением.
Вал червяка устанавливают на радиально-упорные подшипники (преимущественно – роликовые, т.к. они обеспечивают меньшие габариты). При относительно коротких валах применяется схема враспор. Расстояние между опорами при установке враспор не должно превышать величины, рассчитанной по формуле
,
где с – эмпирический коэффициент, равный 35 мм 1/2 для узлов с шариковыми радиально-упорными подшипниками; 50 мм 1/2 для узлов с коническими роликоподшипниками [9, с.64-65];
dп – диаметр вала под подшипником.
Если на червяк действуют значительные осевые нагрузки, и расстояние между опорами превышает величину, рассчитанную по приведенной выше формуле, то в фиксирующей опоре устанавливают два роликовых конических или шариковых радиально-упорных подшипника, а вторую опору делают плавающей.
ВЫБОР ПОДШИПНИКОВ, СЕРИЯ, НОМЕР __ В МЕТОДИЧКЕ «КОНСТРУИРОВАНИЕ…..»
6. Соединения
Соединения деталей в машинах делятся на две основные группы: разъемные и неразъемные.
Разъемные соединения (резьбовые, шпоночные, шлицевые и др.) допускают многократную сборку и разборку без разрушения соединительных деталей.
Неразъемные соединения (заклепочные, сварные, клеевые и др.) могут быть разобраны лишь путем разрушения соединяющих деталей (заклепок, сварного шва и др.).
Разъемные соединения
6.1.1. К резьбовым относятся соединения, выполненные с помощью винтов, болтов, гаек, шпилек. Основным скрепляющим элементом служит резьба. Резьбы бывают различны по назначению и по профилю: метрическая, дюймовая, трубная; крепежная и уплотнительная и т.д.
Наиболее распространенными крепежными деталями являются болт и гайка. Болтовые соединения не требуют нарезания резьбы в соединяемых деталях. Болты могут входить в отверстия с зазором, либо плотно, без зазора.
Для соединения деталей винтами одно из отверстий в соединяемых деталях делается гладким, сквозным, а другое – резьбовым.
Шпильки применяются в тех случаях, когда поставить болт или винт невозможно по конструктивным условиям или по эксплуатационным соображениям нецелесообразно.
Шпильки и болты применяются в тех случаях, когда в процессе эксплуатации соединяемые детали приходится многократно разбирать и вновь собирать. Винты в этих случаях мало пригодны, т.к. резьба в отверстии детали при многократном завинчивании повреждается.
Под гайку или головку болта или винта для увеличения опорной поверхности при необходимости подкладывают шайбу.
Болты и винты изготавливают с различными головками [1, с.272-273] (шестигранные, сферические, со стопорными элементами, цилиндрические, потайные и т.д.)
Болтовые соединения применяются главным образом в сборочных узлах, когда это вызвано требованиями перевозки (ограничения габаритов), монтажа.
Предельная толщина соединяемых элементов не должна превышать 5 d (где d - диаметр стержня болта). При общей толщине соединяемых элементов более 5d в ответственных соединениях, работающих на срез, следует применять болты повышенной точности. В соединениях, работающих на сдвиг, при больших усилиях применяют высокопрочные болты.
В рабочих элементах конструкций число болтов, расположенных по одну сторону стыка должно быть не менее двух.
При осевом воздействии усилий на болтовое соединение распределение усилий между болтами принимается равномерным и требуемое число их рассчитывается по формуле
n = N / N0,
где N - осевое продольное усилие, действующее на элемент конструкции;
N0 – допускаемое осевое усилие на чистый болт, определяемое из условий смятия или среза.
Из расчета на смятие:
[ N0 ] = d S d Rсм или [ N0 ] = d S d [ s см],
где d – наружный диаметр болта;
S d - наименьшая суммарная толщина элементов, сминаемых в одном направлении;
Rсм и [ s см] - расчетное сопротивление и допускаемое напряжение смятия, принимаемые равными 1,8 R и 1,8 [s] - для болтовых соединений.
Из расчета на срез:
или
где nc - число плоскостей среза;
Rср и [t] - расчетное сопротивление и допускаемое напряжение среза, принимаемое равным 0,85R или 0,85 [s] для чистых болтов.
В стыках изгибаемых элементов, например, в стенках балок, болты работают неравномерно, так как силы распределяются прямо пропорционально расстоянию от нейтральной оси. При этом наиболее нагружены крайние болты, усилия в которых принимаются равными допускаемому усилию N0. Число вертикальных рядов болтов nв принимается из условия равенства внешнего момента МС, приходящегося на стенку балки, сумме моментов сил, воспринимаемых всеми болтами полустыка относительно центра О
Рис. 6.1. Схема распределения нагрузок в болтовых соединениях,
работающих на изгиб
6.1.2. Шпоночные соединения. Служат для передачи вращающего момента от вала к установленным на нем деталям (зубчатым колесам, маховикам, муфтам). Шпонки можно подразделить на три основных вида: призматические, сегментные и клиновые. Размеры шпонок и допуски на них стандартизованы.
Призматические шпонки служат для неподвижных соединений ступиц с валами. Размеры пазов под шпонки и поперечные сечения шпонок принимают в зависимости от диаметра вала.
Длину шпонки уточняют после выполнения расчета на смятие и на срез.
Сегментные шпонки устанавливают преимущественно на концевых участках валов цилиндрической или конической формы. Размеры их выбирают по таблицам стандарта, также в зависимости от диаметра вала. Сегментные шпонки удобны при сборке, но глубокий шпоночный паз значительно ослабляет вал.
Клиновые шпонки изготавливают с уклоном 1:100. Такую шпонку запрессовывают ударами молотка между валом и соединяемой с ним деталью. При этом образуется напряженное состояние соединения, в отличие от предыдущих двух. Применяется редко, т.к. может вызвать смешение ступицы относительно ости вала и вызвать нежелательный дисбаланс.
6.1.3. Шлицевые соединения можно представить как многошпоночные, у которых шпонки выполнены как одно целое с валом. По сравнению со шпоночными эти соединения могут передавать большие крутящие моменты, обеспечивают лучшее центрирование соединяемых деталей. Широко распространены в автомобильной, тракторной, станкостроительной отраслях. В зависимости от профиля шлицев различают три типа соединений: прямобочные, эвольвентные и треугольные. Первые два типа стандартизованы и применяют их в подвижных и неподвижных соединениях. Соединения с треугольными шлицами применяют главным образом как неподвижные в установках с незначительными нагрузками.
Расчет шпонок
Условие прочности шпоночного соединения имеет вид:
,
где FТ - окружная сила, передаваемая шпонкой;
Sсм = (h – t) l - площадь смятия (l – рабочая длина шпонки, т.е. без учета закругленных концов; (h – t)- высота площадки смятия, т.е. высота шпонки за вычетом зазора).
[ ϭсм ] – допускаемое напряжение смятия. Для стали принимается в пределах 90…150 МПа.
Размеры стандартных шпонок подобраны по критерию среза, но при необходимости можно проверить на срез следующим образом:
,
где b – ширина шпонки,
[τ ср ] – допустимое напряжение на срез; для стали принимается 70…80 МПа.
Неразъемные соединения
К этой группе соединений относятся заклепочные, сварные и клеевые. Применяются они главным образом для соединения элементов металлоконструкций (листового, полосового материала, фасонных прокатных профилей). Широко используются в самолетостроении, кораблестроении, строительстве мостов и т.д.)
6.3.1. Заклепочные соединения образуются расклепыванием стержня заклепки длиной L и диаметром d, вставленной в отверстие do, в соединяемых деталях. При этом do = d + (0,2 …2) м, в зависимости от диаметра и точности сборки. Замыкающая головка заклепки образуется вследствие пластической деформации выступающей из отверстия части стержня заклепки. Клепка может производиться вручную, либо механизированным способом. Заклепки общего назначения нормальной точности стандартизованы. Существуют заклепки с полукруглой, полупотайной, потайной, плоской головкой.
По расположению заклепок бывают швы однорядные и многорядные. В многорядных швах заклепки могут располагаться рядами или в шахматном порядке. Шаг t между рядами, расстояние е1 между рядами и расстояние е до края листа выбирают в зависимости от типа шва и толщины соединяемых листов.
Расчет заклепочных швов
Под воздействием внешней нагрузки может произойти срез заклепок или смятие листов и заклепок.
Прочность заклепок на срез
,
где z – число заклепок; k – число плоскостей среза.
Прочность стенок отверстий и заклепок на смятие:
ϭсм = F / (s min d 0 ∙ z) ≤ [ϭсм],
[ϭсм] принимают для стали 280…320 МПа.
6.3.2. Сварные соединения по сравнению с заклепочными имеют ряд преимуществ: экономия металла, меньшая трудоемкость и возможность механизации и автоматизации технологического процесса, плотность соединений, бесшумность технологического процесса.
Сварные соединения бывают стыковыми, нахлесточными, угловыми, тавровыми. Сам шов стыкового соединения называют стыковым; остальные швы называют угловыми. Швы нахлесточного соединения называют фланговыми, если они расположены параллельно линии действия приложенной силы, лобовыми – если они расположены перпендикулярно линии действия силы; косыми – если они расположены под углом к направлению приложенной силы. Стыковые швы рассчитывают на растяжение или сжатие.
Основной расчетной характеристикой угловых швов является расчетный катет. [1, 294-296].
Напряжение в шве прямого стыка проверяется по формулам:
- при сжатии
где R ссв и [ sссв ] - расчетное сопротивление и допускаемое напряжение при сжатии.
- при растяжении
где R рсв и [ sрсв ] - расчетное сопротивление и допускаемое напряжение при растяжении.
Рис.6. Сварные соединения встык, выполненные швами:
а) – прямым; б) - косым
Прочность швов косых стыков может быть проверена расчетом на действие нормальных и касательных напряжений по формулам:
- на растяжение
- на срез
где N - расчетная осевая продольная сила;
d - наименьшая толщина соединяемых элементов;
l ш - расчетная длина стыкового шва;
α - угол между направлением продольной силы и швом.
Соединения внахлестку осуществляются при помощи угловых швов – фланговых или лобовых
Рис.7. Сварные соединения внахлестку.
Наибольшая расчетная длина фланговых швов ограничивается величиной, равной 60 hш , наименьшая – 4 hш,, но не менее 40 мм
(hш – катет углового шва). Исключение составляют сопряжения, в которых усилие воспринимается фланговым швом на всем его протяжении (например, поясные швы балок), при этом длина шва не ограничивается.
Сварные угловые швы, воспринимающие продольную силу, рассчитываются по формуле
где hу - катет шва; e - коэффициент, зависящий от вида сварки:
e = 1 для автоматической сварки, однопроходной;
e = 0,8 – для полуавтоматической, однопроходной;
e = 0,7 – для ручной и многопроходной автоматической и
полуавтоматической сварки.
Rусв = 0,7 R – расчетное сопротивление углового шва срезу;
[ t усв] = 0,7 s - допускаемое напряжение углового шва при срезе.
ПРАКТИКА (ЗАДАЧИ НА СОЕДИНЕНИЯ _ В БЛОКНОТЕ). ОНИ ЖЕ МОГУТ БЫТЬ НА ЭКЗАМЕНЕ
Литература
1. Курсовое проектирование деталей машин: Учеб. пособие для учащихся машиностроительных специальностей техникумов /С.А. Чернавский и др.
2. Машнев М.М., Красковский Е.Я., Лебедев П.А. Теория механизмов и машин и детали машин: Учеб. пособие для студентов немашиностроительных специальностей вузов.- 2-е изд., перераб. и доп.- Л.; Машиностроение, Ленингр. отд-ние, 1980.- 512 с., ил.
3. Дунаев П.Ф., Леликов О.П. Детали машин. Курсовое проектирование: Учеб. пособие для машиностроит. спец. учреждений среднего профессионального образования. – 5-е издание, дополн.- М.: Машиностроение, 2004, - 560 с., ил.
4. Аркуша А.И. Техническая механика. Теоретическая механика и сопротивление материалов: Учеб.для средних спец. Учеб.заведений/ - 4-е изд., испр.- М.: Высш.шк., 2002.- 352 с., ил.
ЛЕКЦИИ ПО ДЕТАЛЯМ МАШИН
Передачи в машинах и механизмах. Основные характеристики передач.
Для приведения в движение рабочих машин необходимо передать им энергию от двигателя. Вал двигателя с валом рабочей машины соединять не всегда целесообразно, поэтому между ними устанавливают устройства, называемые передачами. Передачи бывают механические, электрические, гидравлические и т.д. Мы будем изучать только механические передачи.
Механические передачи классифицируются по способу передачи движения [1, с. 299-302]:
а) – передача трением. Сюда относят фрикционные, ременные, канатные.
б) – передача зацеплением. Это зубчатые и червячные, винтовые, цепные.
Основные характеристики передач, необходимые для выполнения проектировочного расчета: мощность на входном (Р1) и на выходном (Р2) валах, угловая скорость входного (ω1) и выходного (ω2) валов, частота вращения (n1) и (n2). Кроме того, используются и производные характеристики: передаточное отношение, передаточное число, крутящий момент, коэффициент полезного действия [2, с. 135-136].
· Передаточным отношением u ij называется отношение угловых скоростей двух любых звеньев, номера которых обозначаются соответствующими индексами
u ij = ωi / ωj.
Передаточное отношение показывает, во сколько раз скорость вращения i –го звена (вала) больше или меньше скорости j –го звена.
· Передаточное число u – это более узкая характеристика передачи, применяется она для редукторов, либо ременных и цепных передач. Это понятие учитывает направление потока мощности, т.е. определяется всегда от входного вала к выходному, поэтому индексы в обозначении не ставятся, а величина передаточного числа всегда больше единицы.
u = ω1 / ω2 ≥ 1.
При расчете одноступенчатых цилиндрических редукторов величину передаточного числа определяют как отношение числа зубьев колеса Z2 к числу зубьев шестерни Z1.
u = Z2 / Z1
Шестерней называют меньшее из двух сопряженных зубчатых колес; она находится на входном валу и часто выполняется как одна деталь с валом (вал-шестерня).
Если передача движения от двигателя к рабочему органу машины осуществляется в несколько ступеней, например: ременная и зубчатая, несколько зубчатые ступеней, сочетание зубчатых и цепной передач и т. д., то в этом случае общее передаточное число механизма u определяется как произведение передаточных чисел отдельных ступеней
u = u1 ∙ u2 ∙ u3 ∙ …. ∙ un.
Как известно из физики, мощность при вращательном движении определяется произведением крутящего момента (Т) на угловую скорость
Р = Т ∙ ω.
Очевидно, что если угловую скорость на выходном валу снизить в u раз по сравнению с входным валом, то во столько же раз возрастает крутящий момент. Поэтому основное назначение всякого редуктора – не только снизить скорость до величины, заданной технологическим процессом, но и увеличить крутящий момент на выходном валу.
Коэффициент полезного действия (КПД), определяемый отношением мощностей выходного и входного валов η = Р2 / Р1, для многоступенчатых передач определяется по формуле
η = η1 ∙ η2 ∙ η3 ∙….∙ ηn,
где η1 , η2 , η3 …. ηn – КПД каждой кинематической пары (зубчатой, ременной, подшипников, муфт), т.е. соединений, в которых происходят потери мощности.
П Р И М Е Р – расчет энергосиловых параметров привода (практ. занятие – по своим заданиям, по методичкам рассчитать КПД, Рвых, крутящие моменты, диаметры валов, составить таблицу.
Передача трением
§ Фрикционная передача состоит из двух катков, насаженных на валы и прижатых силой Q. Движение передается благодаря силе трения Fтр, которая равна окружной силе F. Во избежание проскальзывания создают силу трения в k раз больше, чем окружная сила.
Достоинства фрикционных передач: простота конструкции, плавность работы, возможность плавного регулирования скорости. Передачи с переменной угловой скоростью ведомого вала называют вариаторами.
Недостатки: повышенный износ рабочих тел, непостоянство передаточного числа в связи с возможным проскальзыванием, сравнительно низкий КПД, большая нагрузка на валы и опоры, ограниченная передаваемая мощность.
Применяются фрикционные передачи в кузнечно-прессовом оборудовании, в лебедках, конвейерах.
|
|
Папиллярные узоры пальцев рук - маркер спортивных способностей: дерматоглифические признаки формируются на 3-5 месяце беременности, не изменяются в течение жизни...
История развития хранилищ для нефти: Первые склады нефти появились в XVII веке. Они представляли собой землянные ямы-амбара глубиной 4…5 м...
Таксономические единицы (категории) растений: Каждая система классификации состоит из определённых соподчиненных друг другу...
Поперечные профили набережных и береговой полосы: На городских территориях берегоукрепление проектируют с учетом технических и экономических требований, но особое значение придают эстетическим...
© cyberpedia.su 2017-2024 - Не является автором материалов. Исключительное право сохранено за автором текста.
Если вы не хотите, чтобы данный материал был у нас на сайте, перейдите по ссылке: Нарушение авторских прав. Мы поможем в написании вашей работы!