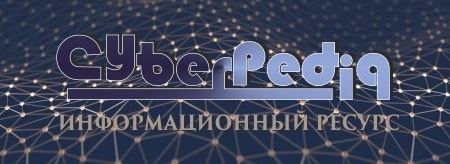
Кормораздатчик мобильный электрифицированный: схема и процесс работы устройства...
Историки об Елизавете Петровне: Елизавета попала между двумя встречными культурными течениями, воспитывалась среди новых европейских веяний и преданий...
Топ:
Техника безопасности при работе на пароконвектомате: К обслуживанию пароконвектомата допускаются лица, прошедшие технический минимум по эксплуатации оборудования...
Комплексной системы оценки состояния охраны труда на производственном объекте (КСОТ-П): Цели и задачи Комплексной системы оценки состояния охраны труда и определению факторов рисков по охране труда...
Проблема типологии научных революций: Глобальные научные революции и типы научной рациональности...
Интересное:
Лечение прогрессирующих форм рака: Одним из наиболее важных достижений экспериментальной химиотерапии опухолей, начатой в 60-х и реализованной в 70-х годах, является...
Уполаживание и террасирование склонов: Если глубина оврага более 5 м необходимо устройство берм. Варианты использования оврагов для градостроительных целей...
Что нужно делать при лейкемии: Прежде всего, необходимо выяснить, не страдаете ли вы каким-либо душевным недугом...
Дисциплины:
![]() |
![]() |
5.00
из
|
Заказать работу |
|
|
Физико-механические параметры, оценивающие свойства инструментальных материалов.
Материалы, отвечающие определенным физико-механическим свойствам и способные осуществлять резание, называются инструментальными.
Твердость – способность материала сопротивляться внедрению в него инородного тела. Необходима для проникновения инструментального материала в конструкционный.
Прочность – способность материала сопротивляться внешним нагрузкам без разрушения.
В процессе резания на рабочую часть инструмента действуют силы резания, под действием этих сил в материала рабочей части возникают напряжения. Что бы эти напряжения не приводили к разрушению – инструментальные материалы должны быть прочными.
Износостойкость – количественное выражение работы сил трения, затраченной на превращение некоторой массы лезвия в продукт износа в конкретных условиях взаимодействия с конкретным контортелом [ Дж]
B=A/m
А – работа потраченная на превращения в стружку; m – масса стружки резца.
Температуростойкость –способность материала сохранять механические свойства при повышенииили понижении температуры. Характеризуется предельными температурами применения, при которыхв материале обнаруживаются неупругие деформации (при повышении температуры) или разрушение структуры (при понижении температуры) под сжимающей нагрузкой.
Теплопрово́дность — способность материальных тел к переносу энергии (теплообмену) от более нагретых частей тела к менее нагретым частям тела, осуществляемому хаотически движущимися частицами тела.
Увеличение работы инструмента может быть достигнуто не только повыш теплопроводности, но и улучшению условий отвода теплоты.
|
Химический состав, маркировка и основные свойства синтетических алмазов.
Синтетические поликристаллические алмазы содержат небольшое количество примесей тугоплавких металлов – вольфрама, титана и молибдена. Эти металлические включения располагаются по межкристаллическим плоскостям. Маркируются они АС – 600, АС – 500 (500 обозначает размер зерна в мкм), Температурастойкость составляет 650 С. Этот недостаток компенсируется высокой теплопроводностью. Теплота выделяющееся в процессе резания на трущихся поверхностях, хорошо отводится в глубь алмаза, и таким образом температура на его рабочих поверхностях не превышает его температуростойкости. Применяются они для прецизионной обработки алюминиевых и медных сплавов, пластмасс, стеклопластиков, полупроводниковых материалов. Большие скорости резания 1000 … 1200 м/мин.
Химический состав, маркировка и основные свойства быстрорежущих инструментальных сталей.
Основным легирующим элементом многих марок быстрорежущих сталей является вольфрам. Присутствие в стали вольфрама приводит к тому что углерод целиком оказывается связанным в сложные карбиды и благодаря этому сталь приобретает высокую твердость темпиратуро и износостойкость. К недостаткам вольфрама можно отнести лишь некоторое уменьшение теплопроводности. Кроме вольфрама, быстрорежущие стали легируют с молибденом, ванадием и кобальтом.
Маркируются Р6М5, Р18, Р9К10 и тд, Р6М5К5 – Первая буква Р – обозначает что это быстрорежущая сталь, цифра 6 – обозначает % содержания вольфрама, М5 – молибден 5%, К5 – кобальт 5%. Около 1% углерода.
Кроме M, быстрорежущие стали могут содержать в своей маркировке такие обозначения: «К» — кобальт, «Ф» — ванадий, «Т» — титан, «Ц» — цирконий.
Температурастойкость 800 – 850 С, Применяются для инструментов работающих в условиях динамических нагрузок.
Химический состав, маркировка и основные свойства низколегированных инструментальных сталей
|
К низколегированным сталям относятся В2, Ф, 9ХС и ХВГ, по содержанию углерода соответствуют углеродистым сталям (1,0…1,2%), но дополнительно легированы небольшим количеством вольфрама, вонадия и др элементов.
Маркировка В2 – 2% вольфрама около 1% углерода.
Углерод (У) Вольфрам (В) Ванадий (Ф) Хром(Х) Марганец (Г) Кремний (С).
Температуростойкость составляет 220 С, максимальная скорость резания 20 …25 м/мин. Применяются из них изготавливают напильники, надфили и ножовочные полотна. Так же реж инструменты работающие с малыми скоростями резания – мелкоразмерные сверла, зенкеры, развертки метчики и круглые плашки.
Системы координат
Инструментальная система координат - прямоугольная система координат с началом в вершине лезвия, ориентированная относительно геометрических параметров режущего лезвия, принятых за базу.
Статическая система координат - прямоугольная система координат с началом в рассматриваемой точке режущего лезвия, ориентированная относительно направления скорости главного движения резания.
Кинематическая система координат - прямоугольная система координат с началом в рассматриваемой точке результирующего движения резания.
Виды неровностей
Качество поверхностного слоя при обработке резанием характеризуется его шероховатостью, физико-механическим состоянием, микроструктурой и остаточными напряжениями. На практике, для оценки качества обработанной поверхности, наиболее часто используется первая характеристика - шероховатость.
Конструкция шнековых сверл
Такие сверла применяют для сверления отверстий длиной до 30Д в стальной заготовки и до 40Д в чугунной. Эти сверла изготавливают из быстрорежущих сталей. Для лучшего отвода стружки угол наклона винтовых канавок (амега) = 60 град. Стружечные канавки имеют в осевом сечении прямолинейный треугольный профиль с закруглением во впадине.
При обработке чугуна 2фи= 120…130 град. передний угол 12 - 18, сталей 2фи=120 град. передний угол 12 – 15.
Для уменьшение трения в процессе работы калибрующая часть сверла имеет утонение 0,03 -0,10 мм по направлению к хвостовику.
Для придания сверлам жесткости диаметр сердцевины принимают равным 0,3 – 0,35 диаметра сверла и затем производят подточку перемычки до 0,1 – 0,15 диаметра сверла.
|
Данная конструкция обеспечивает удаление стружки без вывода сверла
Число зубьев развертки
Для улучшения качества обработанной поверхности число зубьев у разверток делается больше чем у зенкеров, и в зависимости от диаметра его применяют равным 6 – 14 зубьев.
Для ручных и машинных разверток диаметром от 3 – 50 мм число зубьев для машинных разверток сборной конструкции
Классификация фрез
Классификацию фрез проводят по следующим показателям:
По расположению зубьев относительно оси различают: фрезы цилиндрические с зубьями, расположенными на поверхности цилиндра; фрезы торцевые с зубьями, расположенными на торце цилиндра; фрезы фасонные с зубьями, расположенными на поверхности с фасонной образующей; С выпуклым и вогнутым профилем.
Некоторые фрезы имеют зубья как на цилиндрической, так и на торцевой поверхности, например дисковые двух- и трехсторонние; концевые; шпоночные.
По направлению зубьев: прямозубые – в которых направляющая линия передней поверхности прямолинейна и перпендикулярна скорости главного движения резания. Косозубые – у которых направляющая линия передней поверхности прямолинейна и наклонена под углом к скорости главного движения резания. С винтовым зубом – у которого направляющая линия передней поверхности является винтовой.
По конструкции: фрезы могу быть: цельными; составными и сборными
По конструкции зубьев: с острозаточеными и затыловаными.
По способу крепления на станке: фрезы насадные – с отверстием под оправку, и фрезы концевые – с коническим или цилиндрическим хвостовиком.
Конструкция протяжек
Протяжка – многолезвийный инструмент с рядом последовательно выступающих одно над другим лезвий в направлении, перпендикулярном к направлению скорости главного движения, предназначенный для обработки при поступательном или вращательном главном движении лезвия и отсутствии движения подачи.
Протяжки обеспечивают обработку поверхностей с высокой точностью (до шестого квалитета) и низкой шероховатостью обработанной поверхности (Ra до 0,32 мкм).
Используют протяжки в массовом и крупносерийном производствах.
|
Основные конструктивные элементы протяжки показаны на рис. 3.1 а:
передний хвостовик с длиной l1 служат для закрепления протяжки в патроне протяжного станка и передачи силы резания;
шейка длиной l2 - связующая часть между хвостовиком и рабочей частью протяжки. Длина шейки определяется из условия размещения детали между столом протяжного станка и первым зубом d2=d1 =1 мм;
направляющий конус длиной l3 служит для облегчения ввода протяжки в обрабатываемое отверстие, обычно l3= 20 мм;
передняя направляющая длиной l4 служит для центрирования оси заготовки относительно оси протяжки перед протягиванием. Длина передней направляющей равна длине обрабатываемой поверхности заготовки, при большой длине последней - уменьшается до 0,6 длины обрабатываемой поверхности;
рабочая часть длиной l5 служит для срезания всего припуска на протягивание и обеспечение необходимых формы, размеров и шероховатости обработанного отверстия. Рабочая часть состоит из участков длиной l6 с черновыми зубьями, длиной l7 с чистовыми зубьями и длиной l8 с калибрующими зубьями;
задняя направляющая длиной l9=l4 служит для центрирования протяжки в отверстии при прохождении через него калибрующих зубьев по окончании процесса обработки. Диаметр d9 принимают равным диаметру калибрующих зубьев с допуском f7; задний хвостовик l10 служит для поддержания протяжки в процессе обработки на горизонтально-протяжных станках с целью предотвращения провисания протяжки под действием собственного веса.
У протяжек, работающих на станках с автоматическим возвратом в рабочее положение (обычно это вертикально-протяжные станки), задний хвостовик по форме и размерам аналогичен переднему хвостовику. Важнейшей частью протяжки является ее рабочая часть. Форма черновых и чистовых зубьев в сечении, проходящем через ось протяжки, изображена на рис.4.1. Черновые зубья предназначены для снятия основного припуска с обрабатываемой поверхности. Чистовые зубья служат для окончательного образования профиля обрабатываемой поверхности, получения необходимой точности размеров и шероховатости поверхности.
Чистовые зубья имеют меньший подъем зуба, чем черновые. Между зубьями расположены стружечные канавки.
Фрезы насадные цельные
Широко используют насадные фрезы, отличительная особенность которых-- отверстия для насадки на шпиндель станка или непосредственно на вал электродвигателя.
Насадные фрезы в зависимости от конструктивного исполнения разделяют на цельные и сборные. В свою очередь цельные насадные фрезы могут быть одинарными и в виде наборов фрез (составные). Набор цельных фрез чаще всего представляет собой группу фрез, подобранных для обработки профилей деталей, получение которых одинарными фрезами трудно, непроизводительно или невозможно. Набор цельных фрез закрепляют на одном общем валу. В набор могут входить фрезы одинаковые по параметрам или разные. Цельные, фрезы изготавливают из одной заготовки легированной стали или из конструкционной стали с припаянными пластинками твердого сплава или легированной стали. По оформлению задней поверхности зуба цельные фрезы разделяют на затылованные и с прямой задней гранью (с остроконечными зубьями). Затылованные цельные фрезы чаще всего предназначены для фасонного фрезерования различных профилей, режущая кромка у них фасонная.
|
Фрезы сборной конструкции
Фрезы сборной конструкции обеспечивают экономию быстрорежущей стали и снижение эксплуатационных расходов из за возможности многоразового использования корпуса и замены ножей после их изнашивания. Большое влияние на эффектность конструкции сборных фрез имеет способ крепления зубьев. Наиболее простым и надежным способом является применение рефлений обеспечивающих компактность крепления и возможность размещения значительного числа зубьев.
Вариантов конструктивного оформления креплений много. Например нож и паз имеют угол 5град, при расположение рефелей ножа. Нож забивают в паз. Данный способ позволяет регулировать высоту зуба путем выдвижения на несколько шагов рифелей.
Для регулирования и восстановления вылета ножа по диаметру и относительно торца применяют для крепления клин.
В тех случаях когда требуется восстановление диаметра и одновременно вылета ножа относительно торца корпуса применяют нож двойной клиновидности. Ножи с рефлениями применяют на двух – трехсторонних фрезах (80-160мм Д), цилиндрических фрезах (75-110 мм Д), торцовых фрезах Д (80-250мм).
Фрезы сборной конструкции изготовляют сравнительно больших диаметров и оснащают ножами из быстрорежущей стали или твердого сплава
Конструкция червячных фрез
Червячные фрезы применяют для изготовления деталей зубчатого типа с повторяющимися профилями по окружности, например, эвольвентные и не эвольвентные зубчатые колёса, шлицевые валы и т.д.
Червячная фреза (рис. 9.1) представляет собой червяк с продольными винтовыми или прямыми стружечными канавками для образования передних поверхностей зубьев и затылованными задними поверхностями зубьев для образования задних углов. Пересечения передних поверхностей стружечных канавок и затылованных задних поверхностей образуют режущие кромки. Они расположены на поверхности основного червяка, сопряженного с поверхностями зубьев колеса.
Червячные фрезы имеют на каждом зубе три режущие кромки: одну на вершине зуба и две боковые. Учитывая, что при переточке фрез с передним углом не равным нулю и затылованными зубьями получаются искажения в образованном профиле, у чистовых червячных фрез передний угол равен нулю.
К основным конструктивным элементам червячных фрез относятся:
наружный диаметр и длина фрезы, диаметр отверстия, число и форма зубьев,
направление стружечных канавок, геометрические параметры, размеры и форма режущих кромок и др. Диаметральные размеры фрезы влияют на ее конструкцию, точность получаемых зубьев колес, погрешности конструкции фрезы и производительность процесса обработки. С увеличением диаметра фрезы можно увеличить число зубьев, при этом уменьшатся углы подъёма витков фрезы, уменьшится волнистость и огранка поверхностей зубьев нарезаемого колеса, увеличится в процессе резания угол контакта зубьев фрезы и заготовки, а, следовательно, повысится равномерность фрезерования.
Углы резания у метчиков
Углы резания у метчиков имеют весьма важное значение, так как они работают в трудных условиях образования внутренней резьбы. На режущей части передний угол γ должен быть положительным. По ГОСТ 3266-81 рекомендуется для чугуна, твердой стали, хрупкой латуни и бронзы γ = 0–5; для стали средней твердости и латуни γ = 8–10°; для вязкой стали и меди γ = 12 – 15°; для алюминия и других вязких цветных металлов γ = 16 – 25.
Главные кромки на режущей части являются вершинными и срезают основную часть металла, боковые режущие кромки на каждом зубе вспомогательными. Поэтому задний угол α должен быть оптимальным, прежде всего, на вершинных кромках. Рекомендуется α = 6 – 12°. Меньшие значения принимают для ручных метчиков и при нарезании резьбы в легких сплавах. Задний угол получают затылованием задней поверхности по архимедовой кривой. У метчиков, не шлифуемых по профилю, задние углы не создают на боковых режущих кромках, так как они являются вспомогательными. Для нарезания более точной и качественной резьбы применяют шлифованные метчики.
Разновидности метчиков
По конструкции и применению метчики делят на следующие типы:
1) машинно-ручной метчик для нарезания резьбы диаметром более 5,5 мм,
2) ручной метчик с винтовой канавкой. Угол подъема винтовой канавки делают от 30 до 45°;
3) калибровочный метчик применяют для окончательной обработки или зачистки крупных резьб; их изготовляют как хвостовыми, так и насадными
4) гаечный метчик изготовляют с прямым и изогнутым хвостовиками;
5) машинный метчик
6) плашечный метчик для предварительного нарезания резьбы в плашках
7) маточный метчик для окончательной обработки резьбы в плашках
8) специальные - для нарезания резьб различных профилей: трапецеидальных, круглых, упорных и т.д.,
Метчики сборной конструкции
В целях экономии инструментального материала, улучшения геометрии и повышения качества рабочей части инструмента, а также для повышения производительности труда при резьбонарезании отверстий диаметром более 36 мм применяют метчики сборной конструкции. Их подразделяют на: нерегулируемые, регулируемые и регулируемые, автоматически выключающиеся. Нерегулируемые метчики представляют собой сборную конструкцию, состоящую из корпуса и четырех или шести вставных плоских гребенок, закрепленных механическим способом. Регулируемые метчики более универсальны и долговечны. Они позволяют изменять диаметральный размер в пределах 1 – 2 мм. Резьба у таких метчиков винтовая. Длина режущей части и ее угол φ определяются так же, как для машинных метчиков. Регулируемые метчики, выключающиеся автоматически, позволяют сходиться гребенкам к центру нарезания резьбы и без свинчивания свободно выходить из отверстия. Вследствие этого не портится окончательно сформированная резьба, как это в ряде случаев имеет место при вывинчивании инструмента, и повышается производительность, так как исключается время на процесс вывертывания метчика.
Углы резания у плашек
Углы резания. На режущей части α = 6 – 9, на калибрующей α = 0 Передний угол назначают в зависимости от материала детали от 10 до 30 град.
Для обработки высокопрочных сталей 2φ= 30, для легких сплавов и цветных металлов 2φ=50.
Допуск на резьбу у плашек
Так же как для метчиков, поле допуска плашки лежит внутри поля допуска винта. По среднему диаметру поле допуска плашки находится примерно посередине поля допуска винта. По наружному диаметру верхнее отклонение плашки не ограничивается, т.е. может доходить до вершины треугольника резьбы. Нижнее отклонение плашки примерно соответствует номинальному наружному диаметруболта, т.е. расположено так, чтобы наружный диаметр плашки не участвовал в резании даже в том случае, если происходит выпучивание резьбы по наружному диаметру болта. По внутреннему диаметру нижнее отклонение плашки не ограничивается. Но по условиям изнашивания вершины зубьев плашки не должны быть заостренными. Нижнее отклонение располагается ниже верхнего отклонения болта и отстоит от теоретического профиля почти так же, как и по среднему диаметру. Допуски на шаг и на половину угла профиля назначают из условия, что плашка может нарезать резьбу степени точности не выше 6g. Окончательно качество плашек проверяется нарезанном пробной детали и измерением ее резьбы по диаметрам, шагу и половине угла профиля.
Конструкция долбяков
Долбяк – точный режущий инструмент, дающий возможность получать зубчатые колеса 7 и 8-й степеней точности. Долбяки разделяют на долбяки для прямозубых колес и долбяки для косозубых и шевронных колес.
Долбяк представляет собой режущий инструмент, выполненный в виде зубчатого колеса, имеющего режущие кромки. Зубчатое колесо обрабатывают долбяком на зубодолбежном станке. Долбяк и обрабатываемая деталь обкатываются по начальным окружностям без скольжения. Кроме движения обкатки долбяк имеет возвратно-поступательное движение вдоль оси заготовки, которое и является главным движением – движением резания.
Конструктивные элементы и геометрические параметры зуборезных долбяков:
Схема работы прямозубого долбяка при нарезании прямозубого колеса
Деталь 1 закрепляют на столе станка, и она получает вращательное движение, а долбяк 2 имеет, кроме вращательного, также возвратно-поступательное движение. При движении долбяка вниз совершается рабочий ход, при движении вверх — холостой ход.
Долбяк представляет собой зубчатое колесо конической формы (рисунок 30). Такую форму придают ему для того, чтобы обеспечить режущим кромкам положительные задние углы.
Зуб долбяка имеет три режущие кромки: одну при вершине 1 и две боковые 2, очерченные по эвольвенте.
Рис. 30. Конструктивные параметры долбяка
У долбяка различают передние и задние углы для вершинной и боковых режущих кромок.
Углы α и g являются соответственно задним и передним углами при вершине, здесь они рассматриваются в диаметральной плоскости долбяка.
Углы αб и gб являются задним и передним углами боковой режущей кромки; они рассматриваются в плоскости NN. проходящей через точку Р на делительной окружности и являющейся касательной к основной окружности диаметром D 0.
Долбяк характеризуется:
- модулем m;
- углом зацепления α0;
- наружным диаметром D e;
- внутренним диаметром D i;
- делительным диаметром Dt;
- высотой головки h 1;
- высотой ножки h 2;
- высотой зуба h;
- углом наклона зуба w;
- шагом t;
- толщиной зуба по делительной окружности S (рисунок 31).
Физико-механические параметры, оценивающие свойства инструментальных материалов.
Материалы, отвечающие определенным физико-механическим свойствам и способные осуществлять резание, называются инструментальными.
Твердость – способность материала сопротивляться внедрению в него инородного тела. Необходима для проникновения инструментального материала в конструкционный.
Прочность – способность материала сопротивляться внешним нагрузкам без разрушения.
В процессе резания на рабочую часть инструмента действуют силы резания, под действием этих сил в материала рабочей части возникают напряжения. Что бы эти напряжения не приводили к разрушению – инструментальные материалы должны быть прочными.
Износостойкость – количественное выражение работы сил трения, затраченной на превращение некоторой массы лезвия в продукт износа в конкретных условиях взаимодействия с конкретным контортелом [ Дж]
B=A/m
А – работа потраченная на превращения в стружку; m – масса стружки резца.
Температуростойкость –способность материала сохранять механические свойства при повышенииили понижении температуры. Характеризуется предельными температурами применения, при которыхв материале обнаруживаются неупругие деформации (при повышении температуры) или разрушение структуры (при понижении температуры) под сжимающей нагрузкой.
Теплопрово́дность — способность материальных тел к переносу энергии (теплообмену) от более нагретых частей тела к менее нагретым частям тела, осуществляемому хаотически движущимися частицами тела.
Увеличение работы инструмента может быть достигнуто не только повыш теплопроводности, но и улучшению условий отвода теплоты.
|
|
Биохимия спиртового брожения: Основу технологии получения пива составляет спиртовое брожение, - при котором сахар превращается...
Особенности сооружения опор в сложных условиях: Сооружение ВЛ в районах с суровыми климатическими и тяжелыми геологическими условиями...
Индивидуальные очистные сооружения: К классу индивидуальных очистных сооружений относят сооружения, пропускная способность которых...
Наброски и зарисовки растений, плодов, цветов: Освоить конструктивное построение структуры дерева через зарисовки отдельных деревьев, группы деревьев...
© cyberpedia.su 2017-2024 - Не является автором материалов. Исключительное право сохранено за автором текста.
Если вы не хотите, чтобы данный материал был у нас на сайте, перейдите по ссылке: Нарушение авторских прав. Мы поможем в написании вашей работы!