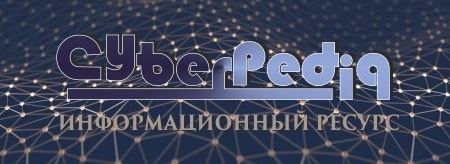
Опора деревянной одностоечной и способы укрепление угловых опор: Опоры ВЛ - конструкции, предназначенные для поддерживания проводов на необходимой высоте над землей, водой...
Механическое удерживание земляных масс: Механическое удерживание земляных масс на склоне обеспечивают контрфорсными сооружениями различных конструкций...
Топ:
Комплексной системы оценки состояния охраны труда на производственном объекте (КСОТ-П): Цели и задачи Комплексной системы оценки состояния охраны труда и определению факторов рисков по охране труда...
Установка замедленного коксования: Чем выше температура и ниже давление, тем место разрыва углеродной цепи всё больше смещается к её концу и значительно возрастает...
Интересное:
Берегоукрепление оползневых склонов: На прибрежных склонах основной причиной развития оползневых процессов является подмыв водами рек естественных склонов...
Уполаживание и террасирование склонов: Если глубина оврага более 5 м необходимо устройство берм. Варианты использования оврагов для градостроительных целей...
Влияние предпринимательской среды на эффективное функционирование предприятия: Предпринимательская среда – это совокупность внешних и внутренних факторов, оказывающих влияние на функционирование фирмы...
Дисциплины:
![]() |
![]() |
5.00
из
|
Заказать работу |
|
|
Проектирование машиностроительных цехов и заводов
Основные стадии проектирования промышленного предприятия.
Первичным документом, на основании которого ведется дальнейшая подробная разработка рабочих чертежей зданий и сооружений является генеральный план.
Генеральным планом завода называется чертеж, на котором нанесено расположение всех его зданий и сооружений, рельсовых и безрельсовых дорого, подземных и наземных сетей, увязанных с рельефом и благоустройством территории.
Состав цехов предприятия может быть определен исходя из следующего производственного деления заводов:
1 вид – машиностроительные заводы с полным производственным циклом, включающим все этапы изготовления машины; такие заводы имеют все три основные группы цехов – заготовительные, обрабатывающие и сборочные.
2 вид – машиностроительные заводы, выпускающие только заготовки для различных деталей машин, т.е. отливки, поковки, штамповки, которыми они снабжают другие машиностроительные заводы. Основные цеха – крупные литейные и кузнечные, кроме того в ряде случаев на таких предприятиях производится предварительная мех. обработка (обдирка) для выявления поверхностных дефектов, а также для снижения объема транспортируемого металла.
3 вид – заводы производящие механическую обработку заготовок, полученных с других предприятий и сборку машин, а также заводы, производящие только сборку машин из деталей, узлов и агрегатов, полученных с других заводов («отверточная сборка» - часто применяется при начале продвижения продукции на новом рынке). В состав таких заводов входят обрабатывающие (механические) и сборочные цехи, во втором случае – только сборочные.
|
Выбор вида завода осуществляется на основе анализа различных экономических факторов.
Проектирование механических цехов.
Классификация механических цехов.
При классификации механических цехов учитывают следующие признаки, которые существенно влияют на структуру цеха:
1. Тип (характер) производства.
2. Характер конструкции и вес изделия (4 класса цехов);
3. Размер цеха (по условному количеству металлорежущих станков).
Классификация по типу производства.
Для каждого типа производства характерны свои особенности ТП и форма организации производства.
Вид (тип) производства | Количество обрабатываемых в год деталей одного наименования и типоразмера. | ||
Крупных (>2 т) | Средних (от 100 кг до 2 т) | Легких (менее 100 кг) | |
Единичное | до 5 | до 10 | до 100 |
Серийное | 5 – 1000 | 10 – 5000 | 100 – 50000 |
Массовое | свыше 1000 | свыше 5000 | свыше 50000 |
Единичное производство: (характерно для тяжелого машиностроения, судостроения, химического машиностроения, ремонтных и инструментальных цехов).
- Изделия изготовляются в малых количествах, с небольшой повторяемостью или вообще без повторяемости;
- Используются универсальные станки, оснастка и инструмент.
Серийное производство: (самый распространенный тип производства)
- Изготовление деталей производится партиями. В зависимости от типоразмера детали и размера партий выделяют мелко- средне- и крупносерийное производство. В серийном производстве ТП разделен на отдельные операции, закрепленные за определенными станками.
- Применяется самое разнообразное оборудование от универсального до специализированного и агрегатных станков.
Массовое производство – дальнейшее развитие серийного способа производства (наиболее совершенная организация производственного процесса). Изготовление изделий происходит путем непрерывного выполнения на рабочих местах одних и тех же постоянно повторяющихся операций.
Рабочий состав цеха и определение его численности.
|
В работе механического цеха участвуют:
1. Производственные рабочие (гл. образом станочники).
2. Вспомогательные рабочие
3. МОП – младший обслуживающий персонал,
4. Служащие,
5. ИТР – инженерно-технические работники,
6. СКП – счетно-конторский персонал.
В зависимости от типа производства и требуемой точности применяются различные методы расчета количества производственных рабочих.
Планировка оборудования и рабочих мест в цехе. Определение размера площади цеха.
Планировка оборудования.
Состав производственных отделений и участков механических цехов определяется характером изготовляемых изделий, тех. процессом, объемом и организацией производства.
В поточно-массовом производстве, например в автотракторном, цех называется по наименованию выпускаемого узла или агрегата. Например, цех двигателей имеет участки: «Блок цилиндров», «Коленчатые и кулачковые валы», «Шатуны» и т.п. Участок разбивается на станочные линии по наименованию деталей, например участок «Блок цилиндров» имеет линии «Блок», «Направляющие втулки клапана», «Крышки коренных подшипников» и т.д.
В серийном производстве механический цех разбивается на участки (или пролеты) по размерам деталей (участок крупных деталей, участок мелких деталей, участок средних деталей) или по характеру и типу деталей (участок валов, участок зубчатых колес и т.д.)
Пролетом называется часть здания, ограниченная в продольном направлении двумя параллельными рядами колонн. Металлорежущие станки участков и линий механического цеха располагают в цехе одним из двух способов:
- по типам оборудования;
- в порядке технологических операций.
По типам оборудования – этот способ характерен для единичного, мелкосерийного и отдельных деталей серийного производства. Создаются участки станков: токарных, фрезерных, шлифовальных. Последовательность расположения подобных участков однородных станков на площади цеха определяется последовательностью обработки большинства типовых деталей.
Так по ходу технологического процесса обработки деталей типа шкив, муфта, фланцы, диски, зубчатые колеса, втулки и т.д. располагаются участки станков в следующей последовательности:
1. Токарные станки
2. Фрезерные
3. Строгальные
4. Радиально и вертикально-сверлильные
|
5. Шлифовальные (круглошлифовальные).
При обработке плоскостных деталей (плита, рама, станина и т.п.) последовательность расположения оборудования будет следующая:
1. Разметочные плиты,
2. Продольно-строгальные,
3. Продольно-фрезерные,
4. Расточные,
5. Сверлильные,
6. Плоскошлифовальные.
При размещении станков необходимо стремиться к достижению прямоточности производства и к наилучшему использованию подкрановых площадей. Мелкие станки располагают на площадях, не обслуживаемых кранами.
По порядку технологических операций – этот способ характерен для цехов серийного и массового производства. Станки располагаются в соответствии с технологическими операциями для обработки одноименных или нескольких разноименных деталей, имеющих схожий порядок операций. В мелкосерийном и среднесерийном производстве каждая группа станков выполняет обработку нескольких деталей, имеющих аналогичный порядок операций, т.к. загрузить полностью все станки линии одной деталью не всегда возможно.
Необходимо предусматривать кратчайшие пути движения каждой детали, не допускать обратных, кольцевых или петлеобразных движений, создающих встречные потоки или затрудняющих транспортирование.
Основные принципы при размещении станков:
1. Участки, занятые станками, должны быть по возможности наиболее короткими. В машиностроении длина участка составляет 40 – 80 м.
2. Станки вдоль участка могут располагаться в 2, 3 и более рядов. При расположении станков в 2 ряда между ними оставляется проход (проезд) для транспорта. При трехрядном расположении станков может быть два или один проход. В последнем случае продольный проход образуется между одинарными и сдвоенным рядами станков. Для подхода к станкам сдвоенного ряда (станки расположены друг к другу тыльными сторонами), расположенным у колонн, между станками оставляют поперечные проходы. При 4-х рядном расположении устраивают 2 прохода: у колонн станки располагают в один ряд, а сдвоенный ряд – посередине (см. рис. 3).
3. Станки могут располагаться по отношению к проезду вдоль, поперек и под углом (рис. 4). При поперечном расположении станков затрудняется их обслуживание, т.к. нужно предусматривать поперечные проезды. Загрузочная сторона прутковых станков должна быть обращена к проезду, у остальных же станков сторона с приводом обращена к стене или колоннам. Для лучшего использования площади револьверные станки, автоматы, протяжные, расточные, продольно-фрезерные и продольно-шлифовальные располагают под углом.
|
4. В поточных линиях станки также могут устанавливаться в один или в два ряда. В последнем случае деталь в процессе обработки переходит с одного ряда на другой. В поточных линиях с применением рольгангов или других конвейеров станки могут устанавливаться относительно них параллельно, перпендикулярно, а также могут быть встроены в линию.
5. Расстояние между станками, а также между станками и элементами зданий для различных вариантов расположения оборудования, а также ширина проездов в зависимости от различных видов транспорта регламентирована нормами технологического проектирования.
При вычерчивании габаритов станка принимается его контур по крайним выступающим частям, причем в габарит входят крайние положения движущихся частей станка. Каждому типу станка дается условное графическое изображение в М 1:100 или 1:200.
Заготовительное отделение.
Служит для разрезки отрезки, центровки, правки и обдирки прутковых материалов.
Может быть совмещено со складом материалов и заготовок и является частью его хозяйства или же для крупных предприятий может быть самостоятельным.
Оборудование – отрезные станки, дисковые пилы, приводные ножовки, центровальные и фрезерно-центровальные станки, правильные, обдирочные станки, прессы для правки и др.
Удельная площадь обычно составляет 25 – 30 м2.
Площадь считается:
Заточное отделение.
С целью улучшения качества заточки режущего инструмента заточка выполняется централизованно. Основное оборудование – заточные станки.
Точный расчет заточных станков как правило не производится из-за большой трудоемкости расчетов и отсутствия полных исходных данных.
Потребное количество заточных станков общего назначения в среднем составляет 4 – 6% от количества станков, обслуживаемых заточкой.
Удельная производственная площадь заточного отделения составляет 8 – 10 м2, а уд. общая площадь этого отделения – 10 – 12 м2 на 1 станок.
Заточное отделение следует располагать смежно с инструментальным складом.
Кол-во рабочих – 1,7 – 2 чел. на один заточной станок при работе в 2 смены.
Планировка оборудования в цехе.
Планировка цеха – это план расположения производственного, подъемно-транспортного и др. оборудования, инженерных сетей, рабочих мест, проездов, проходов и др.
Разработка планировок является наиболее ответственным и сложным этапом проектирования, когда одновременно должны быть решены вопросы технологии, экономики, организации производства, техники безопасности, выбора транспортных средств, механизации и автоматизации производства, НОТ и производственной эстетики.
|
При разработке планировки должны учитываться следующие основные требования:
1. Оборудование в цехе должно размещаться в соответствии с принятой формой организации технологических процессов. Необходимо стремиться к расположению производственного оборудования в последовательности технологического процесса, контроля и сдачи изделий или деталей.
2. Расположение оборудования, проходов и проездов должно гарантировать удобство и безопасность работы, возможность монтажа и демонтажа, ремонта оборудования; удобство подачи заготовок и инструмента; удобство уборки отходов.
3. Планировка должна быть увязана с применяемыми подъемно-транспортными средствами.
4. В планировках должны быть предусмотрены кратчайшие пути перемещения заготовок, деталей, узлов в процессе производства, исключающие возвратные движения. Грузопотоки должны не пересекаться между собой, а также не пересекать и не перекрывать основные проезды, проходы и дороги, предназначенные для движения людей.
5. На планировке вычерчивается все оборудование и все устройства, относящиеся к рабочему месту, а именно:
- металлорежущие станки, автоматические линии и другое производственное оборудование;
- место расположения рабочего места у станка во время работы;
- верстаки, рабочие столы, подставки;
- места у станков для обработанных деталей, заготовок и материалов;
- транспортные устройства, относящиеся к рабочему месту (наклонные скаты, склизы и т.д.);
- площадки для контроля и временного хранения деталей;
- места для мастеров;
- все виды оборудования нумеруются сквозной нумерацией слева направо сверху вниз.
- нумерация подъемно-транспортного оборудования дается после технологического и продолжает нумерацию последнего;
- производственный инвентарь (плиты разметочные, верстаки, столы, стеллажи) изображаются на плане по контуру габарита с простановкой внутри контура условных обозначений;
- к плану прилагается спецификация;
- обозначаются наименования отделений, участков, вспомогательных помещений.
6. При разработке планировки должна быть рационально использована не только площадь, но и весь объем цеха. Высота здания используется для размещения подвесных транспортных устройств, инженерных коммуникаций, размещения механизированных складов.
7. План цеха выполняется в масштабе 1:100. Для больших цехов (С > 250 станков) его можно выполнять в М 1:200.
8. В строительной части изображаются:
- колонны с осями и обозначением № колонны (горизонтальные разбивочные оси здания обозначают снизу вверх по оси ординат заглавными буквами русского алфавита; вертикальные оси нумеруют слева направо арабскими цифрами).
- наружние и внутренне стены (капитальные и легкие), а также перегородки; окна, ворота, двери.
- на плане даются все необходимые размеры:
Ú ширина пролета, шаг колонн, общая ширина цеха, общая длина пролетов и всего цеха, ширина поперечных и продольных проходов и проездов;
Ú длина и ширина каждого вспомогательного помещения;
Ú тоннели, каналы, люки и др. проемы в полах;
Ú привязка оборудования.
9. Все станки, автоматические линии и др. оборудование, складские и контрольные площадки, грузоподъемные и транспортные устройства, изображенные на плане, обозначаются порядковыми номерами и вносятся в спецификацию.
Планировка оборудования и рабочих мест сборочного цеха.
Расположение участков сборки должно соответствовать последовательности прохождения деталей и узлов по стадиям сборки. В соответствии с этим участки сборки должны располагаться в следующем порядке: Слесарная обработка деталей, если она предусматривается сборка механизмов, общая сборка машины, испытания, окраска. Сборка узлов и изделий высокой точности выделяется в изолированных термоконстантных отделениях.
В том случае, когда узловая и общая сборка производится в одном цехе или отделении, направление потоков сборки отдельных узлов располагают, как правило, перпендикулярно линии общей сборки машины с тем, чтобы конечная операция сборки узла совершалась вблизи места установки его на линии сборки. Окрасочные и сушильные камеры могут располагаться как в линии общей сборки, так и в линиях узловой сборки.
Планировка сборочного цеха.
При планировке отделений, участков и рабочих мест сборки должно быть предусмотрено следующее оборудование:
- верстаки, столы;
- сборочные автоматы и полуавтоматы;
- стенды;
- рельсовые и безрельсовые тележки, конвейеры, наземные рельсовые пути, автоматические и полуавтоматические сборочные станки и линии, а также другое необходимое в конкретных условиях оборудование.
- Следует также предусмотреть места расположения сборщиков и возможность их перемещения.
Ширина пролетов сборочных цехов принимается в зависимости от габаритных размеров собираемых машин, оборудования и площадей рабочих мест и других условий.
Расстояние между колоннами в продольном направлении (шаг колонн) 6, 9 и 12 м. Длина пролета определяется также, как и для механического цеха, т.е. суммой размеров (по длине), считая по его оси, последовательно расположенных производственных и вспомогательных отделений, проходов и других участков цеха. Длина пролета должна быть кратна размеру шага колонн. Высота сборочных цехов (от пола до головки подкранового рельса) при наличии мостовых кранов должна быть не менее 6,15 м; при отсутствии мостовых кранов высота не менее 6 м.
Компоновка сборочного цеха.
Сборочный цех располагается обычно в одном здании с механическим цехом, реже – в отдельном здании. Наиболее рационально расположение цехов в одном здании; в этом случае уменьшается пробег деталей, быстрее осуществляется подача деталей к сборочным местам, упрощается и удешевляется транспорт. Кроме того, в этом случае возможно объединение промежуточных и других складов, обслуживающих помещений; облегчается и ускоряется взаимосвязь между обоими цехами.
Наикратчайший пробег детали после обработки будет в том случае, если место окончательной операции механической обработки примыкает к сборочному конвейеру в той его позиции, где эта деталь ставится в собираемый агрегат или машину.
Этому расположению отвечает такая компоновка механического и сборочного цехов, когда сборочный цех расположен в пролете, перпендикулярном пролетам механического цеха.
Классификация зданий.
Производственные здания в зависимости от процессов происходящих в них делятся на:
· основные производственные;
· обслуживающие;
· вспомогательные
По планировочным решениям и эксплуатационным режимам различают:
· одно- и многоэтажные;
· со световыми фонарями и безфонарные;
· крановые и бескрановые;
· отапливаемые и неотапливаемые (горячие цеха);
· с плоским и скатными кровлями;
· с наружным отводом атмосферных вод и с внутренними водостоками.
Проектирование машиностроительных цехов и заводов
|
|
Типы оградительных сооружений в морском порту: По расположению оградительных сооружений в плане различают волноломы, обе оконечности...
Организация стока поверхностных вод: Наибольшее количество влаги на земном шаре испаряется с поверхности морей и океанов (88‰)...
Биохимия спиртового брожения: Основу технологии получения пива составляет спиртовое брожение, - при котором сахар превращается...
История создания датчика движения: Первый прибор для обнаружения движения был изобретен немецким физиком Генрихом Герцем...
© cyberpedia.su 2017-2024 - Не является автором материалов. Исключительное право сохранено за автором текста.
Если вы не хотите, чтобы данный материал был у нас на сайте, перейдите по ссылке: Нарушение авторских прав. Мы поможем в написании вашей работы!