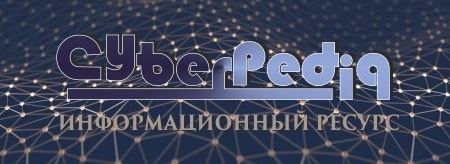
Поперечные профили набережных и береговой полосы: На городских территориях берегоукрепление проектируют с учетом технических и экономических требований, но особое значение придают эстетическим...
История развития пистолетов-пулеметов: Предпосылкой для возникновения пистолетов-пулеметов послужила давняя тенденция тяготения винтовок...
Топ:
Процедура выполнения команд. Рабочий цикл процессора: Функционирование процессора в основном состоит из повторяющихся рабочих циклов, каждый из которых соответствует...
Марксистская теория происхождения государства: По мнению Маркса и Энгельса, в основе развития общества, происходящих в нем изменений лежит...
Выпускная квалификационная работа: Основная часть ВКР, как правило, состоит из двух-трех глав, каждая из которых, в свою очередь...
Интересное:
Национальное богатство страны и его составляющие: для оценки элементов национального богатства используются...
Наиболее распространенные виды рака: Раковая опухоль — это самостоятельное новообразование, которое может возникнуть и от повышенного давления...
Уполаживание и террасирование склонов: Если глубина оврага более 5 м необходимо устройство берм. Варианты использования оврагов для градостроительных целей...
Дисциплины:
![]() |
![]() |
5.00
из
|
Заказать работу |
|
|
Исходная влажность массы
Для определения данной влажности глиняной массы используется весовой метод определения. Для этого отбирают пробу массой 15 г от исходного сырья, укладывают на предварительно высушенное и взвешенное стекло или вбюкси взвешивают на технических весах. Затем навески помещают в сушильный шкаф, где их высушивают при температуре 105…120 °С в течение 2–4 ч до постоянной массы. После охлаждения в эксикаторе до комнатной температуры навески вновь взвешивают.
Вычисления производят по формуле:
W = ,
где g0 – масса влажной пробы, г; g1 – масса высушенной пробы, г.
Разжижение глин при помощи электролитов
Для изучения разжижения глинистых шликеров используют сухие молотые глины с размером частиц < 0,5 мм и растворы электролитов (Na2CO3, Na2SiO3, NaOH) с исходной концентрацией 2 %. Для приготовления шликера применяется пропеллерная мешалка, а для определения вязкости (текучести) глиняных шликеров – специальный вискозиметр. Он представляет собой цилиндрический сосуд емкостью 600 мл с калиброванным отверстием в дне, через которое вытекает шликер. Вискозиметр имеет устройство, позволяющее быстро открывать и закрывать это отверстие. Вязкость характеризуется временем истечения (в секундах) определенного объема шликера (в условиях практикума 100 мл).
Готовят шликер из глины и дистиллированной воды. Для этого в фарфоровый стакан заливают 300 мл воды и при помешивании стеклянной палочкой всыпают отвешенное количество глины. Относительная влажность шликера должна составить 40-50 %. Перемешивают шликер при помощи пропеллерной мешалки в течение 15 мин. Для лучшего перемешивания пропеллер мешалки нужно располагать возможно ближе ко дну стакана. Выливают шликер из стакана в вискозиметр и по секундомеру определяют время истечения его в мерную колбу емкостью 100 мл. Для получения надежных результатов опыт повторяют трижды и берут среднее время. Консистенция шликера должна быть такой, чтобы время истечения составляло 20–30 с. Если шликер слишком густой или жидкий, готовят новый, соответственно меняя количество глины при том же количестве воды. Необходимы следующие условия получения сопоставимых результатов: постоянная температура шликера при определении, так как она сильно влияет на вязкость; рекомендуется проводить определение при температуре 20 °С. Для приведения температуры шликера к заданной вискозиметр имеет водяную рубашку: пропуская через нее горячую или холодную воду и одновременно перемешивая шликер, приводят его температуру к заданной; – постоянная высота столба шликера (или постоянный его объем) в вискозиметре, так как давление столба шликера влияет на скорость его истечения; – ввиду того, что шликер при спокойном стоянии загустевает (тиксотропное упрочнение), определение текучести необходимо проводить сразу же после окончания перемешивания.
|
Когда нужная консистенция шликера найдена, определяют влияние электролита на разжижение. В условиях практикума характер электролита задан и ставится задача найти его оптимальную концентрацию. В этом случае вместо воды берут определенное количество раствора электролита с концентрацией от 0,01 до 1,0 %. При добавлении к глинистому шликеру электролита текучесть (вязкость) определяют по методике, описанной выше. Опыты проводятся при 4–5 различных концентратах электролита. Полученные зависимости вязкости (по времени истечения) от содержания электролита изображают на графике, откладывая на оси абсцисс количество сухого вещества электролита в мл (г) на 100г сухого вещества. Для каждого электролита выявляют минимум вязкости и участок соответствующих концентраций. В конце, проведя серии опытов, можно дать окончательную оценку разжижаемости исследуемой массы и подобрать параметры шликера, характеризующегося требуемой текучестью.
|
Экспериментальная часть
4.1. Характеристика исходных материалов.
В качестве основного сырья в работе была использована санитарно-фаянсовая масса для керамических изделий старооскольского завода ООО «ОСМиБТ».
Химический состав глины приведен в табл. 1
Таблица 1.
SiO2 | Al2O3 | K2O | Na2O | TiO2 | F2O3 | CaO | MgO | п.п.п. | ∑, % |
59.82 | 28.31 | 1.73 | 1.08 | 0.64 | 0.48 | 0.43 | 0.41 | 7,04 |
На первом этапе работы был изучен минералогический состав исходной глины. На рис. 1 приведены данные рентгенофазового анализа.
Рис.1. Пиктограмма ренгенофазового анализа
Как следует из рис. 1 основным глинистым минералом исследованной глины является каолинит. В качестве основного примесного минерала в глине присутствует кварц.
4. 2. Опрдеделение влажности керамических шликеров
Влажности шликера рассчитывают исходя из следующей формулы:
, %
= 40,4 %
4.3. Исходная влажность массы
Вычисления производят по формуле:
W = ,
где g0 – масса влажной пробы, г; g1 – масса высушенной пробы, г.
= 21 %
4.4. Разжижение глин при помощи электролитов
Для разжижения шликера были использованы электролиты: NaHCO3 (кальцинированная сода), Na2SiO3 (жидкое стекло), реотан.
Испытания разжижения шликера электролитами приведены в табл.
Таблица.
№ испытания | Общее количество добавляемого электролита | Время истечения 100мл шликера, с | |||
Содержание в % | На 100 г сухого вещ-ва, мл | Стекло | Сода | Реотан | |
0,1 | 0,1 | - | - | - | |
0,2 | 0,2 | ||||
0,3 | 0,3 | ||||
0,4 | 0,4 | ||||
0,5 | 0,5 |
Данные таблицы отображают на графике
Рис.. Зависимость истечения времени от количества добавляемого электролита
За оптимальное количество добавки электролита принимают величину, соответствующую количеству добавки, при которой скорость истечения шликера составляет τ =12 с. Из данных графика следует, что минимальной вязкостью обладает жидкое стекло, т.к. время истечения и количество вводимого электролита соответствует оптимальным показателям.
4.5. Определение коэффициента загустеваемости шликеров
Рассчитывают коэффициент загустеваемости по формуле:
Kз = Т2 / Т1,
где Т1- время истечения шликера после 30 с выстаивания, Т2 - время истечения шликера после 30 мин выстаивания.
|
Стекло:
Kз = 28 / 13 = 22 с
Сода:
Kз = 16 / 12 =1,3 с
Реотан:
Kз = 36/ 14 = 2,6 с
Результаты испытаний приведены в таблице 3.
Таблица 3.
Электролит | Температура опыта, ![]() | Скорость (время) истечения шликера после выстаивания а приборе в течение | ||
τ1=30 сек | τ2=30 мин | Число загус-теваемости | ||
Стекло | 2,2 | |||
Сода | 1,3 | |||
Реотан | 2,6 |
По данным таблицы оптимальным электролитом является стекло, т.к для высококачественных шликеров, применяемых в тонкой керамике, коэффициент загустеваемости находится в пределах 1,8–2,2
4.6. Определение скорости набора черепка
Массу набранного на гипсовый стержень слоя g (в г) определяют по формуле:
G = (m – mo) (100 – wшл) / 100,
где m o – масса высушенного гипсового стержня, г; m – масса стержня с набранным слоем, г; w шл – относительная влажность шликера, %.
1. Стекло
G = (20,9 – 13,84) (100 – 40) / 100 = 4,24 г
G = (39 – 30,39) (100 – 40) / 100 = 5,17 г
G = (43,5 – 31,5) (100 – 40) / 100 = 7,47
Сода:
G = (20 – 14,1) (100 – 40) / 100 = 3,54 г
G = (36,9 – 30,3) (100 – 40) / 100 = 3,96 г
G = (41,1 – 32,2) (100 – 40) / 100 = 5,34 г
Реотан:
G = (19,2– 13,8) (100 – 40) / 100 = 3,24 г
G = (36,1 – 30,4) (100 – 40) / 100 = 3,42 г
G = (39,7 – 31,2) (100 – 40) / 100 = 5,1 г
Поверхность гипсового стержня, сопрекасаемого со шликером:
,
где d – диаметр стержня, см; h – глубина погружения стержня в шликер, см.
= 19
=18,3
= 19
Скорость набора массы V н, , находят по формуле:
Vн = G / (S τ),
где τ – продолжительность набора массы, мин; S – поверхность гипса, соприкасающаяся со шликером, см2.
Стекло:
V = 4,24 / (19
3) = 0,07
V = 5,17 / (18,3
5) = 0,06
V = 7,47 / (19
7) = 0,06
Сода:
V = 3,54 / (19
3) = 0,06
V = 3,42 / (18,3
5) = 0,04
V = 5,34 / (19
7) = 0,04
Реотан:
V = 3,24 / (19
3) = 0,06
V = 3,42 / (18,3
5) = 0,04
V = 5,1 / (19
7) = 0,04
Результаты исследований приведены в таблице 4.
Таблица 4.
Электролит | Номер стержня | Диаметр стержня d, мм | Высота погружаемой части, h мм | Поверхность гипсо-вого тела S, см3 | Время набора массы τ, мин | Масса стержня, г | Скорость набора массы Vн, г/ см2 мин) | ||||
Высушенного, mo | с набранным сло- ем, m | ||||||||||
Стекло | 16,16 | 34,29 | 19,0 | 13,84 | 20,90 | 0,07 | |||||
14,75 | 34,83 | 18,3 | 30,39 | 37,00 | 0,04 | ||||||
15,88 | 34,01 | 19,0 | 31,05 | 43,50 | 0,06 | ||||||
Сода | 16,16 | 34,29 | 19,0 | 14,10 | 20,00 | 0,06 | |||||
14,75 | 34,83 | 18,3 | 30,30 | 34,90 | 0,03 | ||||||
15,88 | 34,01 | 19,0 | 32,20 | 41,10 | 0,04 | ||||||
16,16 | 34,29 | 19,0 | 13,80 | 19,20 | 0,06 | ||||||
Реотан | 14,75 | 34,83 | 18,3 | 30,40 | 33,10 | 0,02 | |||||
15,88 | 34,01 | 19,0 | 31,20 | 39,70 | 0,04 | ||||||
|
Рис. 4. Зависимость скорости набора массы от времени набора
Из данных, представленных в таблице и на графике, следует, что жидкое стекло является более подходящим электролитом для качественного набора массы шликера, т.к. скорость набора массы происходит интенсивнее, чем у остальных разжижителей.
4.7. Определение линейной воздушной и огневой усадки
Расчет усадки производится по следующим формулам:
, %;
, %;
, %;
где – расстояние между метками на свежесформованном образце;
– расстояние между метками на воздушно-сухом образце;
– расстояние между метками на обожженном образце.
= 3,05%;
= 8,5%;
= 11,3 %;
Результаты исследования приведены в таблице
Таблица
№ обр. | Температура
обжига, ![]() | Расстояние между метками, мм | Усадка, % | ||||
после | Воз-душная | Ог-невая | Пол-ная | ||||
формо-вания | сушки | обжига | |||||
65,5 | 63,0 | 58,2 | 8,5 | 11,3 | |||
65,5 | 63,9 | 58,1 | |||||
65,5 | 63,5 | 58,0 | |||||
65,0 | 63,1 | 57,6 | |||||
65,0 | 63,2 | 57,5 |
Приготовление шликера
Из шликера с определенной текучестью и фильтрующей способностью отливают изделия в гипсовых формах. Этот способ позволяет получать тонкостенные и сложные по форме изделия. Для метода литья используют пористые, чаще всего гипсовые формы, а суспензии - в виде текучего шликера с содержанием воды 30-40%. Шликер содержит твердую, жидкую и газообразные составляющие и добавки (электролиты, КМЦ), которые улучшают его свойства.
Шликер отвечает следующим требованиям: должен иметь заданный химический и минералогический состав твердых материалов и минимальную влажность, которая обеспечивает необходимую текучесть; обладать оптимальной загустеваемостью и высокой фильтрующей способностью; быть устойчивым против расслаивания при длительном хранении; обеспечивать достаточную механическую прочность на изгиб отлитых изделий.
В производстве фаянсовых продуктов домашнего предназначения используют для изготовления шликера прессовый метод при отдельном помоле сырьевых материалов. Коржики фильтр-прессовой массы, незапятнанные отрезки и сушье, которые получают при формовании и оправке продуктов, распускают в воде в пропеллерных мешалках либо шаровых мельницах.
Шликер из мешалок либо шаровых мельниц соединяется через сито (4- 9 отв/см2) в сборники, оснащенные перемешивающими приборами (пропеллерными мешалками). Шликер подвергается поочередно ситовому и магнитному обогащению на обогатительных установках. Ситовое обогащение исполняется на ситах с медными либо латунными сетками № 02 (918 отв/см2). Для удаления подключений воздуха из шликера его вакуумируют в вакуумных резервуарах, куда его подают повторяющий вид деликатных потоков.
|
На протяжении установленного лабораторией срока выстаивания шликер сохраняют в сборниках-смесителях, традиционно более 3 суток.
Качество шликера увеличивают: выстаивание, подогревание, вакуумная обработка, вибрация и обработка ультразвуком. Получению шликера размеренной вязкости и загустеваемости содействует выстаивание. Уменьшает время набора требуемой толщины отливки при литье в гибсовые формы - обогрев. Избавляют включения воздуха из шликера - вакуумирование и вибрация. На 1-2% понижают вязкость шликера и влажность отливок использование вибрации (3000-6000 шатаний за минуту) и обработка шликера ультразвуком (частота колебаний 20 кГц), а на 15-20% увеличивают их крепкость впоследствии сушки. Вибрация приводит до совершенства внутреннюю структуру продуктов, убавляет вероятность образования раковин в отливках благодаря ускоренному набору стенок продуктов.
Прессовой способ приумножает качество шликера благодаря устранению в процессе фильтр-прессования вредных веществ, которые растворены в воде, отрицательно влияющие на его положительные свойства. Способ трудоемкий и дорогостоящий.
Формование изделий литьем
Один из старейших способов формовки фарфоровых и фаянсовых изделий - литье изделий в пористых формах (шликерное литье).
![]() | ![]() |
Принцип литья керамических изделий в гибсовые формы основан на умении шликера заполнять форму и отдавать влагу пористой форме с появлением на ее поверхности уплотненного слоя массы.(рис. 38). Чаще всего применяются два способа литья: сливной и наливной. Имеют место быть еще доливной, либо комбинированный способ литья, применяемый редко, для изготовлении продуктов непростой формы.
В ходе работы применялся сливной способ изготовления изделия.
При сливном способе шликер заливают в пористую форму, заполняя всю ее внутреннюю полость (рис. 39, с). Благодаря способности гипсовой пористой формы отсасывать влагу через определенное время из шликера на границе форма - шликер появляется плотный слой массы. Его толщина зависит от свойств шликера и гипсовых форм. Лишний шликер сливается, оставляя уплотненный слой. При сливной способе полуфабрикат имеет постоянную толщину стенки. Шликер должен сохранять повышенную текучесть и удовлетворять требованиям, приведенным в табл. 11.
Таблица 11. Свойства шликера | |
Показатели | Масса |
фаянсовая | |
Остаток на сите № 0056, % Влажность, % Плотность, г/см3 Коэффициент загустеваемости | 12 29-40 1,75-1,76 2,0-2,5 |
При разливе шликера по формам (сливной способ) струя не должна бить в стенку формы, захвтывать воздух. Необходимо, чтобы шликер равномерно заполнял форму без вспенивания. При помощи специального наконечника - литейного конуса (рис.), который прикрепляется к резиновому шликеропроводу, можно избежать образующихся дефектов. Конструкция конуса позволяет частично удалять воздушные мвссы при выходе шликера.
Скорость всасывания жидкой фазы шликера стенками пористой формы должна быть выше или соответствовать скорости подхода ее к поверхности формы. На наружном слое отливки образуется более уплотненный слой, препятствующий проходу влаги из шликера в форму, если используются пересушенные гипсовые формы или шликер с недостаточной плотностью, при этом возможно отхождение изделия от стенок формы и появление трещин. Нельзя использовать густой шликер, т.к. скорость поглощения влаги уменьшается, вода накапливается на поверхности формы. Это приводит к прилипанию изделий к форме и к размыванию толщины слоя набранной стенки изделия.
От содержания в массе отощающих материалов и их зернового состава зависит влагопроницаемость набранного слоя изделия. Регулирование процесса набора стенок затрудняет увеличение размеров частиц отощающих материалов и способствует слишком быстрой скорости набора стенок. К резкому снижению скорости набора стенки изделий приводит очень тонкий помол компонентов шликера и соответственно к прилипанию их к форме. Снижает вязкость воды повышение температуры шликера и форм до 35-40 °. Гипсовым формас необходимо обладать влажностью 4-6% и пористостью 40-45%. Чтобы не замедлять время образования стенки изделия при последующей заливке форм, вода должна быть удалена сушкой гипсовой формы.
После окончания фильтрационного процесса движение влаги из набранного слоя массы в форму не прекращается. При этом отделению изделий от стенок формы способствует воздушная усадка изделия.
Отливка изделий на стендах или конвейерах зависит от размеров и формы изделия.
Для упрощения ручного труда на заводах используют поворотные четырехполочные литейные стенды, а также конвейерные люлечные сушилки с выносными ветвями для выполнения заливки и слива излишнего шликера, формования с обогревом горячим воздухом, разборки и сборки форм. Люлечные конвейеры допускают расположить их ветви по вертикали и с высоким эффектом использовать заводские площади.
Для механизированного процесса литья используются установки, изготовленные в виде кольцевых или прямолинейных конвейеров, а также ротационных столов, работающих в комплекте с сушильными устройствами.
Последовательность технологических операций, которые выполняются при сливном способах литья изделий, приведена на рис. 53.
Обжиг фаянсовых изделий
В производстве фаянсовых и фарфоровых изделий обжиг обеспечивает получение черепка с необходимыми физическими и химическими свойствами (высокая прочность, плотность, химическая и термическая устойчивость, белизна, просвечиваемость и др.) и закрепление декора на поверхности глазури или под глазурью. Режим обжига фаянсовых и фарфоровых изделий отличаются.
Фаянсовый или фарфоровые изделия подвергают преимущественно двукратному обжигу. Первый обжиг они проходят после сушки; затем их при необходимости декорируют, покрывают глазурью и отправляют на второй (политой) обжиг. Изделия, декорированный по глязури (надглязурное декорирование) подвергаются и третьему обжигу. Существует и однократный обжиг изделий.
Назначение первого обжига фаянса – придать черепку механическую прочность, необходимую для выполнения последующих технологический операций и эксплкатации готовых изделий.
При двукратном обжиге фаянсовой посуды, поступающей из формовочного цеха после сушки, первый обжиг проводят при 1230-1280 (для твердого фаянса), Второй обжи зделий, покрытых глязурью, - при 1500-1150.
Первый обжиг фаянсовых изделий разделяют на ряд периодов.
Первый период. Полуфабрикат досушивается с целью удаления воды из пор и гидроскопической влаги, которая остается в изделиях после сушки (2-4%, и выше). В этот период медленно поднимает температура до 250, далее изделие выдерживают (это необходимо для того, чтобы влага испарялась равномерно по всей толщине черепка изделия. Быстрый перегрев поверхности изделий при температуре интенсивного преобразования 200-240 приводит к их разрушению из-за высоких внутренних напряжений, которые возникают в черепке. Стремительный подъем температуры может привести ко взрыву изделия из-за неравномерности прогрева наружных и внутренних слоем черепка.
Рис. 54. Кривые режимов двукратного обжига фаянсовой посуды в туннельной печи: 1 — первого, 2 — второго
Второй период. Температура обжига поднимается до крайней температурной точки, которая обеспечивает получение изделий с заданными физико-химическими свойствами. Для фаянса она составляет 1130-1280. С повышением температуры обжига выше оптимальной для конкретной массы уменьшается качество физико-технических свойств продукта. Происходит сильное спекание черепка, что уменьшает пористость и не дает прикрепляться глазури при глазуровке.
В начале этого периода (300 начинается выгорание органических примесей (остатки растительного и животного происхождения из сырья), которое заканчивается при небыстром подъеме температуры до 450, при быстром – примерно 700-800. Скорость испарения конструкционной воды зависит от природы глинистых материалов, их свойств и скорости подъема температуры в интервале 450- 500. При это наблюдается небольшая усадка изделий (до 0,5-1%), не вызывающая больших напряжений.
Каолинит теряет кристалически связанную воду. На сколько быстро будет удаляться конституционная вода завит от природы глинистого сырья, его структуры и скорости подъема температуры в интервале 450-1000. При этом процессе наблюдается значительная усадка изделий (до 0,5-1%), не вызывающая больших напряжений.
При температуре 573 происходит модификационное превращение бетта-кварца в альфа кварц. Этот модификационный перомежуток, который сопутствуется увелечение объема кварца (+ 0,82%), происходит моментально. Объемное увеличение кварца уменьшает усадку, которая происходит за счет конструкционной воды. При обжиге толстостенный изделий при такой температуре (550-600) производят выдержку для обеспечения равномерного перехода кварца из одной модификации в другую по всей толщине черепка, иначе могут появиться микродеффекты в виде трещин.
При 700-800 в материале происходит диссоциация карбонатов CaCO3 и MgCO3 с удалением углекислого газа, которая прекращается при 950-1000, которая сопровождается увеличениеи пористости изделия.
При температуре от 200 до 400 в поры обжигаемого изделия проникает сажистый углерод из домовых газов. Выгорание углерода начинается при 400 и заканчивается при 1000. В изделии могут появиться вздутия из-за заплавления жидкой фазой части капилляров в том случае, если при 1000 в черепке не удаляется полностью углерод или сохраняются остатки воды.
При температуре 900-1050 появляютя первичные кристаллы муллита, которые способствуют увеличению прочности фаянсового черепка. Рост нитевидных кристаллов муллита активно происходит при температурах выше 1100.
При возрастании температуры до 1280 в черепке появляется некоторое количество стекловидной фазы (расплава), цементирущая зерна дегидратированного глинистого вещества и кварца в поверхностях соприкосновения. Черепок фаянсовых изделий, который обжигается при 1230-1280, упрочняется, сохраняя достаточную пористость (18-20%), которая необходима для глазурования.
Для того, чтобы обеспечить равномерное прохождение представленных выше процессов, располагаемых в различных местах по пересечению печного канала, производится выдержка при дохождении максимальной температуры.
С высокой скоростью протекает процесс охлаждения изделий до температуры 600-550 и здесь же заканчивается выдержкой, которая необходима для обратного модификационного перехода альфа кварца в бетта кварц. Затем производится ускоренное охлаждение. Полная усадка фаянсовых изделий составляет 9-13%
Второй обижиг фаянсовых изделий производят после наложения подглазурного декора и глазурования. Температуре плавления глазури соответствует температура второго обжига. Для декоративных изделий используется глазурь с низкой температурой плавления (1050).
Оба обжига фаянсовых изделий выполняют в окислительной газовой среде.Чтобы глазурь плавилась одновременно на всех черепках, перед последней выдержкой выравнивают температуру по всей площади канала. Протяженность выдержки в конце обжига и плавления глазури определяется плавкостью и вязкостью последней и варьируется в пределах 0,3-1ч. Слабому блеску глазури и неравномерному растеканию способствует малая выдержка. Образованию дефекта, как «сухой» край, может способствовать слишком длительная выдержка при заданной конечной температуре.
К первому обжигу не допускаются изделия, которые имеют следующие дефекты: помарки подглазурными красками, неблежнонанесенная подглазурная краска, щербины, трещины, зашибины, влажность, неплотно приставленные детали и т.д.
Полые изделия ставят на этажерки вагонеток в один ряд.
После первого обжига полые изделия вынимают из ячеек вагонетки и сортируют в ящики по ассортименту. При выгрузке полуфабрикат распределяют для того, чтобы отделить изделия, недопустимые к следующей обработке, а также выяснить характер дефекта и принять меры для устранения. Сортировку осуществляют путем визуального осмотра изделий и перезвонки (по краю ударяют палочкой, треснувшие изделия издают дребезжащий звук). По степени обжига изделия разделяют на три группы в зависимости от степени их водопоглощения (%): крепкообоженные – ниже 8,5; Нормально обоженные – 8,5 – 11,5; слабообоженные – 11,5. Слабообожженные изделия направляют на повторный обжиг, пережженные покрывают глазурью большей плотности. Отдельно ставят изделия с исправленными деффектами: наибольшими зашибами, которые можно зачистить шлифовальной шкуркой или абразивным камнем без искажения формы изделия; плохо оплавленными краями, которые нуждаются в повышенной зачистке поверхности; подрывом деталей, устраняемые подмазкой специальной мастикой.
Изделия, прошедшие подглазурное декорирование и глазурование загружаются в капсели и на этажерки вагонеток для второго обжига.
Полые и некотрые плоские изделия утанавливают на полки этажерочных вагонето или в капсели на клинышки или крестики таким образом, чтобы после обжига на глазури не не оставались заметные следы (плешины).
Обоженые изделия выгружают из капселей или этажерок на транспортные устройства и направляют на расортировку. Полые изделия составляют в ящики, сортируя по ассортименту и величине.
Браованные изделия (отходы производства) направляют в массозаготовительный цех на переработку.
Глазурование изделий
Глазурование изделий - процесс, обеспечивающий нанесение на изделие глазурной суспензии.
Глазурование изделий осуществляют погружением, поливом и пульверизацией.
В данной работе использовался метод полива.
Глазурь наносят на обожженные или хорошо высушенные изделия в виде тонкодисперсной водной суспензии, плотность которой изменяется в значительных пределах в зависимости от водопоглощения глазуруемого полуфабриката.
Глазурь внедряется в поры подсушенного изделия, закрепляясь на поверхности полуфабриката с определенной толщиной. Расплавляясь в процессе обжига, глазурь образует на поверхности изделий при дальнейшем охлаждении тонкий стекловидный слой толщиной 0,01-0,03 мм.
Прежде чем наносить глазурь, поверхность изделий должна быть обезжирена и отчищена. В противном случае из-за остатков пыли образуются дефекты, такие как «плешины», «наколы» и др. Чистку изделий выполняют в специализированных кабинах, которые снабженны вытяжной вентиляцией.
Перед глазурованием выполняют мокрую чистку изделий (рис. 50): неглазурованные участки покрывают машинным маслом или расплавленным парафином. Изделия устанавливают ножкой или краем на пропитанное жировым веществом техническое сукно или тонкий войлок конвейера.
![]() | Рис. 50. Мокрая зачистка глазури: а - общий вид, б - зачистка вибрацией, в - зачистка двумя противоположно движущимися лентами; 1 - изделие, 2 - транспортер, 3 - барабан, 4 - ванна с водой |
Глазурование поливом
Глазурование поливом используют чаще всего при глазуровании полых.
Рис. 52. Установка АСФ-30 для глазурования полых изделий: 1 — транспортер зачистки ножки и края изделий, 2 — транспортер-удлинитель, 3 — полуавтомат глазурования, 4 — насосная станция глазури, 5 — общая рама
Принцип работы установки АСФ-30 заключается в следующем. Изделие помещается на транспортерное устройство полуавтомата глазурования 3, проходит камеру обдувки и камеру глазурования. В камере обдувки с его поверхности сжатым воздухом убирается пыль. Глазурь наносится методом полива в камере глазурования. Далее изделие поступает на смоченную ленту транспортера-удлинителя 2. Влажная лента впитывает часть глазури с края изделия и отправляет его на зачистную ленту транспортера зачистки 1. Непрерывно движущаяся и вибрирующая лента зачистного транспортера выполняет окончательную чистку края изделия. Отглазурованные и зачищенные изделия снимаются в конце транспортера зачистки.
Все перечисленные операции производятся автоматически, кроме установки и съема изделий.
Сортировка изделий
В производстве фаянсовых изделий бытового назначения при исполнении отдельных технологических процессов возникают разнообразные виды брака, обнаруживаемые методом промежуточного контроля. Итоговую сортировку изделий выполняют после политого обжига. Для каждого ассортимента отводится специальное место. Сортировку зачастую производят в две стадии:
1) первичная сортировка изделий после политого обжига;
2) окончательная сортировка с исправленными дефектами.
При первой сортировке изделия разделяют на: сортные, которые после декорирования соответствуют предусмотренным в ТУ группам сортности; нуждающиеся в дополнительной обработке (зачистки, шлифования и полирования); дефектные.
На второй стадии сортировки изделия разделяют по сортам, отбирают для соответствующего декорирования. Внешний вид, показатели физико-механических свойств, величина и количество дефектов обработки при формовании, сушке, обжиге и декорировании являются критериями для отнесения изделий к тому или иному сорту.
Фаянсовые продукты сортируют методом внешнего осмотра, инструментов и приспособлений. В ходе сортировки дают оценку по их цвету, качеству глазурного покрытия, устанавливают отклонения от формы и размеров. Для упрощения и большей объективности сортировки используют эталоны.
Деформацию полых изделий устанавливают по разности высшего и минимального диаметров. Для этого используют вставляемыми в зазор специализированные калибры в виде ступенчатых клиньев с утолщением ступени постепенно на 0,5 мм. Изделия ставят на диск вверх дном и прижимают к нему вертикальным штифтом, который надавливается на центр дна. Сигнальные лампы включают в зависимости от степени искривления борта отдельные клавиши опускаются на различную глубину, которые показывают к какому сорту по признаку деформации следует приложить изделие.
Размеры изделий устанавливают при помощи линейки миллиметровой, толщиномера или штангенциркуля. Емкость изделий определяют в литрах воды; полых - по количеству воды, заполняющей изделие полностью. Объем воды рассчитывается мерным цилиндром.
Физико-механические свойства испытываемых изделий (белизна, твердость механическая прочность, термостойкость, химическая стойкость глазури, пористость) проверяют в лаборатории циклично выборочным путем (один раз в квартал). Требования к физико-механическим свойствам указываются в технических условиях.
Сортировка фаянсовых изделий, мало отличающихся весьма разнообразным ассортиментом, осуществляется вручную.
Маркировка изделий
На готовых фарфоровых и фаянсовых изделиях должны быть указаны марка завода, товарный знак, обозначающий их сортность (иногда приводится номер, сложность разделок), и цена.
Для маркировки фарфоровых изделий используют штампы (резиновые или желатиновые), на которых изображена марка завода и обозначен сорт изделия. Товарный знак может быть выполнен декалькоманией (переводная картинка). Товарный знак ставят в центре дна готовых изделий с внешней стороны надглазурными красками: на продукцию высшего и I сортов - красной краской, II - синей, III -зеленой. Сухую надглазурную краску смешивают со скипидаром и скипидарным маслом на палитре, разравнивают тонким слоем и с помощью штампа наносят на изделие. Товарный знак должен быть четким, без помарок. Закрепляется он на изделиях посредством обжига на температуру 820 °С.
Для клеймения холодным способом используют надглазурные краски, расправленные на связке, состоящей из терпентина (50%) и скипидарного масла (50 %) или вареной олифы (70 %) и терпентина (30 %). Кр
|
|
Археология об основании Рима: Новые раскопки проясняют и такой острый дискуссионный вопрос, как дата самого возникновения Рима...
Папиллярные узоры пальцев рук - маркер спортивных способностей: дерматоглифические признаки формируются на 3-5 месяце беременности, не изменяются в течение жизни...
Особенности сооружения опор в сложных условиях: Сооружение ВЛ в районах с суровыми климатическими и тяжелыми геологическими условиями...
Таксономические единицы (категории) растений: Каждая система классификации состоит из определённых соподчиненных друг другу...
© cyberpedia.su 2017-2024 - Не является автором материалов. Исключительное право сохранено за автором текста.
Если вы не хотите, чтобы данный материал был у нас на сайте, перейдите по ссылке: Нарушение авторских прав. Мы поможем в написании вашей работы!