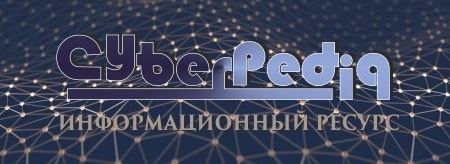
Механическое удерживание земляных масс: Механическое удерживание земляных масс на склоне обеспечивают контрфорсными сооружениями различных конструкций...
Состав сооружений: решетки и песколовки: Решетки – это первое устройство в схеме очистных сооружений. Они представляют...
Топ:
Марксистская теория происхождения государства: По мнению Маркса и Энгельса, в основе развития общества, происходящих в нем изменений лежит...
Процедура выполнения команд. Рабочий цикл процессора: Функционирование процессора в основном состоит из повторяющихся рабочих циклов, каждый из которых соответствует...
Интересное:
Финансовый рынок и его значение в управлении денежными потоками на современном этапе: любому предприятию для расширения производства и увеличения прибыли нужны...
Распространение рака на другие отдаленные от желудка органы: Характерных симптомов рака желудка не существует. Выраженные симптомы появляются, когда опухоль...
Наиболее распространенные виды рака: Раковая опухоль — это самостоятельное новообразование, которое может возникнуть и от повышенного давления...
Дисциплины:
![]() |
![]() |
5.00
из
|
Заказать работу |
Внимание: ВСН 440 -83, ГОСТ 16310 -80 касается труб из неметаллических материалов.
ВСН 362-87 Изготовление, монтаж и испытание технолог.трубопроводов на РУ до 10 Мпа
6.8. Газовую (ацетилено-кислородную) сварку допускается производить нейтральным пламенем только для трубопроводов из углеродистых и низколегированных сталей Ду до 80 мм и толщиной стенки до 3,5 мм.
6.9. В зависимости от диаметра и толщины стенки трубы газ. сварку можно выполнять в правом или левом направлении: стыки труб диаметром 14-48 мм - в левом, диаметром 57-89 мм - в правом.
6.10. Для ацетилено-кислородной сварки следует применять сварочную проволоку марок Св-08, Св-08А, Св-08АА, Св-08ГА. Диаметр сварочной проволоки принимается в зависимости от толщины стенки труб, мм:
Толщина стенки труб, мм:
1-2 | 2; |
2-4 | 2-3; |
4-8 | 3-4. |
6.17. Св. материалы необходимо доставлять к месту св.работ в количестве, необходимом для обеспечения только сменной потребности. Оставшиеся на следующий день электроды и флюс следует вновь прокалить.
8.3. К самостоятельным работам по термической обработке сварных соединений следует допускать термистов-операторов, имеющих квалификацию не ниже 4-го разряда.
8.9. Перерывы в процессе термической обработки не допускаются. При вынужденных перерывах необходимо обеспечить медленное охлаждение сварного соединений до 300 °С.
ОСТ 26-01-1434-87 СВАРКА СТАЛЬНЫХ ТЕХНОЛОГИЧЕСКИХ ТРУБОПРОВОДОВ НА ДАВЛЕНИЕ Ру СВЫШЕ 10 ДО 100 МПа (СВЫШЕ 100 ДО 1000 КГС/СМ2)
5.2. Обработка кромок труб и деталей трубопроводов под сварку должна производиться механическим способом. Шероховатость обработанных кромок должна быть не более Rz 80
5.3. Разделительную резку труб допускается производить любым промышленным способом. Огневая резка труб из стали 14ХГС при температуре окружающего воздуха ниже 0 С должна производиться с предварительным подогревом места реза до температуры 100 – 150град.С, хромомолибденовых, хромомолибденованадиевых и хромомолибденованадиевовольфрамовых сталей - до температуры 200 - 250 С. При огневой резке труб должен быть предусмотрен припуск на механическую обработку.
5.4. Величина припуска на механическую обработку после огневой резки должна быть не менее:1)3 мм - для труб из углеродистых, марганцевокремнистых, хромокремнемарганцовистых сталей; 2) 10 мм - для труб из хромомолибденовых, хромомолибденованадиевых, хромомолибденованадиевовольфрамовых сталей; 3) 2 мм - для труб из аустенитных сталей.
7.4. При сварке трубопроводов высокого давления из сталей 20, 20ЮЧ со стенкой толщиной от 4.5 до 30 мм подогрев не требуется, сталей 15ГС (16ГС), 14ХГС со стенкой толщиной свыше 30 мм -. 150 -200градС, сталей 18Х3МВ, 20Х3МВФ со стенкой толщиной от 4.5 до 60 мм. 350 – 400град С.
7.6. Ширина зоны нагрева, до температуры указанной в табл. 1, должна быть равной двум толщинам стенки, но не менее 100 мм. Зона нагрева должна располагаться симметрично относит. разделки шва.
СТО 00220368-008-2006 Изготовление деталей и узлов из коррозионностойких сплавов на железоникелевой и никелевой основе, разнородных соединений и двухслойных сталей с плакирующим слоем из сплавов марок 06ХН28МДТ, ХН65МВ и Н70МФВ-ВИ. Типовой технологический процесс
Настоящий стандарт распространяется на изготовление деталей и узлов из коррозионностойких сплавов на железоникелевой основе марок 03ХН28МДТ, 06ХН28МДТ, ХН30МДБ, ХН32Т, ХН35ВТ, ХН35ВТЮ, ХН38ВТ и на никелевой основе ХН63МБ, ХН65МВ, ХН65МВУ, Н65М-ВИ, Н70МФВ-ВИ, ХН75МБТЮ, ХН78Т, разнородных соединений и двухслойных сталей с плакирующим слоем из сплавов марок 06ХН28МДТ, ХН65МВ и Н70МФВ-ВИ при изготовлении сосудов, аппаратов и технологических трубопроводов толщиной до 30 мм для химической и других смежных отраслей промышленности, работающих при температурах от –70 до 900°С, подведомственных Ростехнадзору.
Таблица 6.1,6.2, 6.3. Для аргонодуговой сварки сплавовХН30МДБ применяют проволоку Св-ХН30 МДБ – ВИ, для РДС сплавов ХН65МВ применяют электроды ОЗЛ – 21, флюсы применять для автоматической сварки под флюсом сплавов марок 03ХН28МДТ, 06ХН28МДТ - АН -18 ГОСТ Р 52222, автоматическая сварка под флюсом сплавов на железоникелевой и никелевой основе применяется с толщины металла 5 – 20мм, для РДС Ст3+06ХН28МДТ электроды ОЗЛ – 36, ЭА – 395/9, АНЖР 3У, АНЖР – 1, АНЖР – 2.
6.9. Св. проволока для аргонодуговой сварки должна быть зачищена и промыта ацетоном.
6.11. Вольфрамовые электроды должны быть заточены под углом 14 град.+2град.
9.3.2. Максимальная величина прогиба свариваемых кромок днищ из сплавов на железоникелевой и никелевой основе на всей длине, собираемых под автоматическую сварку под флюсом - не более 3мм на всей длт\ине
10.1.7. Защита обратной стороны шва при ручной аргонодуговой сварке коррозионностойких сплавов на никелевой и железоникелевой основе выполняется поддувом аргона.. Если нет защиты – то часть корня шва удалить..
10.1.15. Максимальную степень проплавления основного слоя двух-слойной стали при наплавке переходного слоя не должна превышать 30%.
10.1.16. Исправление дефектов в одном месте сварного шва - не более 2 раз.
10.2.7. Величина угла между вольфрамовым электродом и поверхностью изделия при сварке – 60 – 80 град. |
11.6. Термическая обработка выполняется после сварки и исправления недопустимых дефектов.
СТО 00220368-009-2006 Ремонт отслоений плакирующего слоя из коррозионностойких сталей и сплавов, выявленных в процессе изготовления двухслойных листов и биметаллических аппаратов с основным слоем из
углеродистых, низколегированных и хромомолибденовых сталей. Типовой технологический процесс
4.5 Сплошность сцепления слоев проверяют ультразвуковым контролем (УЗК) по ГОСТ 22727 методами с чувствительностью контроля в условных обозначениях 8Э, 8ЭС, 20Т. Контроль сплошности соединения слоев выполнять в соответствии с СТП 26.260.487.
4.12 Ремонту подлежат двухслойные листы, заготовки и элементы изделия, имеющие отслоения на площади не более 15 % общей площади, при этом:
- каждое отслоение, выходящее на кромки заготовки, подвергающейся сварке с последующей штамповкой, вальцовкой или гибкой, имеет площадь не более 150 см или при большей площади ширину не более 50 мм;
- суммарная длина отслоений, выходящих на кромки, не превышает 25 % общей длины кромок данной заготовки (элемента изделия);
- каждое отдельное отслоение (независимо от расположения) имеет площадь не более 2500 см2, а расстояние между отдельными отслоениями не менее 200 мм.
Ремонту также подлежат трубопроводы с отслоениями, выходящими на торцы труб.
5.3 В сертификате на поставляемые материалы должны быть указаны химический состав, механические свойства, результаты испытаний на МКК, способ выплавки, вид и режимы термической обработки и другие требования и виды испытаний по техническим условиям.
6.4 Термическая резка труб из двухслойной стали производится со стороны углеродистого слоя. Однако, по сравнению с резкой монолитной углеродистой сталью той же толщины наконечник выбирается на один номер больше, а скорость резки снижается на 10 - 15 %. 7.3 Границы обнаруженных отслоений должны быть обозначены на детали плакирующего слоя краской, отступив от границы отслоения в сторону качественного металла на 5 - 10 мм.
8. 3 Отслоения, выходящие на кромку заготовки (элемента изделия), которая должна подвергаться сварке, а затем штамповке, вальцовке или гибке (п. 4.12) должны ремонтироваться только наплавкой. Ремонт таких отслоений должен производиться до сварки.
9.1 Ремонт отслоений с помощью электрозаклепок применяется для заготовок труб, днищ и обечаек, а также для деталей аппаратов, работающих в вакууме или с небольшим рабочим давлением (не более 0,05 МПа) при малоагрессивной среде.
9.4. По всей площади внутри контура электрозаклепок, ограничивающих распространение отслоения (п. 9.3), ставятся электрозаклепки в шахматном порядке с шагом не более 100 мм. При этом расстояние между центрами этих электрозаклепок и электрозаклепок, ограничивающих отслоение, должно быть не менее 40 мм (рисунок 9.2) и не более 70 мм.
10.1 Ремонт отслоений с шпоночными швами допускается во всех случаях, кроме аппаратовI группы.
Разделка пазов под шпоночные швы выполняется шлифовальным кругом или воздушно-дуговой строжкой с последующей зачисткой шлифовальным кругом на глубину не менее 1 мм от линии сплавления слоев для удаления науглероженного слоя. Поверхность плакирующего слоя вокруг мест воздушно-дуговой строжки должна быть покрыта раствором мела или другого вещества, исключающего прилипание брызг расплавленного металла.
10.8. Наплавка переходного слоя на основной слой теплоустойчивой стали типа 12ХМ производится с предварительным подогревом 150 - 200 °С. При этом суммарная высота наплавки переходного слоя должна быть 3 ± 0,5 мм.
14.1. Отслоения и другие дефектные участки ремонтируются с применением ручной дуговой (РДС), автоматической сварки под флюсом (АФ) и ручной аргонодуговой сваркой неплавящимся электродом (РАД).
Применение других видов сварки допускается по согласованию со специализированной организацией по сварке.
14.10. Диаметр электродов выбирается по табл. 14.3 в зависим. от толщины плакирующего слоя.
Таблица 14.3 - Выбор диаметра электродов при РДС
Толщина плакирующего слоя | Переходный слой | Плакирующий слой | ||
Диаметр электрода, мм | Количество слоев | Диаметр электрода, мм | Количество слоев | |
2,6 - 3,2 | 3,0 | 1 - 2 | 4,0 | 1 - 2 |
3,2 - 4,5 | 3,0 | 1 - 2 | 4,0 | 1 - 2 |
4,5 - 6,0 | 4,0 | 1 - 2 | 5,0 | 2 - 3 |
15.3 Контроль качества мест ремонта осуществляется в зависимости от технических условий на изделие следующими методами, предусмотренными ГОСТ 3242:
- внешним осмотром всех мест ремонта;
- механическими испытаниями образцов наплавленного металла, вырезанных из контрольных пластин (испытания на ударный изгиб);
- металлографическими исследованиями наплавленного металла, проводимыми на образцах, вырезанных из контрольных пластин;
- стилоскопированием на наличие Cr и Мо, ультразвуковым контролем.
СТО 00220368-011-2007 Сварка разнородных соединений сосудов, аппаратов и трубопроводов из углеродистых, низколегированных, теплоустойчивых, высоколегированных сталей и сплавов на железоникелевой и никелевой основах
Настоящий стандарт распространяется на изготовление, монтаж и ремонт сосудов, аппаратов толщиной до 60 мм и технологических трубопроводов толщиной до 30 мм из разнородных сталей (сплавов) для химической, нефтехимической, нефтеперерабатывающей, газовой и других смежных отраслей промышленности, работающих при температурах от минус 60 до 900°С, подведомственных Ростехнадзору.
При выполнении сварочных работ на открытых площадках должны быть приняты меры защиты места сварки от воздействия атмосферных осадков и ветра. Минимально допустимая температура окружающего воздуха и подогрева устанавливаются с учетом свариваемости менее технологичной стали, входящей в данное сварное соединение.
4.2. Все сборочные и сварочные работы производят в закрытых отапливаемых помещениях на специальных изолированных участках, обеспечивающих соблюдение чистоты сварочных работ, отсутствие сквозняков и температуру окружающего воздуха не ниже 0°С.
5.10 Термообработка разнородных сварных соединений, включающих неаустенитные материалы и выполняемых аустенитными сварочными материалами, не допускается. В исключительных случаях термообработка производится по указанию в техническом проекте.
Термообработка разнородных сварных соединений, выполняемых неаустенитными сварочными материалами, производится по режимам более легированных сталей.
6.2.При проектировании ответственных (нагруженных) конструкций из разнородных сталей разных структурных классов рекомендуется:
- предпочитать стыковые соединения другим видам: угловым, тавровым, нахлесточным. Расположение швов должно обеспечивать удобство сварки, надежность ее выполнения;
6.10 Температура подогрева контролируется контактными или бесконтактными инфракрасными термометрами, термокарандашами, термокрасками, цифровыми контактными и лазерными бесконтактными термопарами. Замер температуры производятся в пределах зоны равномерного нагрева на расстоянии не менее двух толщин стенки изделия в каждую сторону от оси шва.
7.8 Колебания напряжения питающей сети, к которой подключено сварочное оборудование, допускается не более ±5 % от номинального значения.
8.2 В качестве неплавящегося электрода при аргонодуговой сварке применять вольфрамовые прутки лантанированные по ГОСТ 23949 диаметром 2-4 мм.
8.4 При аргонодуговой сварке в качестве защитной среды применяется аргон высшего сорта по ГОСТ 10157.
8.1. При ручной дуговой сварке разнородных соединений из сталей группы С-02 (16ГС) и С-04-1 (12ХМ). Применять электроды типа Э50А
8.13. Перед использованием каждого нового баллона производится пробная наплавка валика длиной 100-200 мм на пластину с последующим визуальным контролем на отсутствие недопустимых дефектов или на «технологическое пятно» путем расплавления пятна диаметром 15-20 мм.
11.3.3 Начинать и заканчивать сварку продольных стыков необходимо на выводных планках. Длина участка шва на планках должна быть не менее 100 мм.
11.3.4 Выводные планки изготавливаются:
- из менее легированной стали при сочетании сталей перлитного класса или перлитного класса со сталями мартенситного класса;
- из аустенитной стали типа 12Х18Н10Т при использовании аустенитных сварочных материалов или сплавов на железо-никелевой (никелевой) основе.
11.4.2.. При полуавтоматической сварке в положениях, отличных от нижнего, применяется проволока диаметром не более 1,4 мм; род тока постоянный, полярность обратная.
11.4.12 При ручной аргонодуговой сварке неплавящимся электродом для улучшения условия возбуждения дуги и повышения ее стабильности рекомендуется:
- затачивать конец вольфрамового электрода на конус длиной, равной 3-4 диаметра электрода;
- применять осциллятор или специализированное оборудование.
13.17 Исправление одного и того же дефектного участка сварного соединения допускается не более двух раз.
СТО 00220368-012-2008 Сварка сосудов, аппаратов и трубопроводов
из углеродистых и низколегированных сталей
6.6 При отсутствии сопроводительных сертификатов на материалы или данных об отдельных видах испытаний должны быть проведены испытания на предприятии-изготовителе аппаратов в соответствии с требованиями стандартов или технических условий на эти материалы и требованиями настоящего стандарта.
6.7 Низколегированные стали повышенной прочности 15Г2СФ, 09Г2ФБ, 10Г2ФБ, 09Г2БТ, 16Г2АФ, 16ГНМА могут поставляться как в нормализованном, так и в термоупрочненном состоянии.
Термоупрочненные стали, применяемые для аппаратов, эксплуатируемых при температуре свыше 200°С и давлении более 5 МПа, должны проходить полистное испытание на заводе-изготовителе.
7.12 Прокалку флюса рекомендуется производить слоем толщиной не более 80 мм в специальных противнях из жаропрочных или окалиностойких сталей, при этом допускается неоднократная его прокалка.
7.14 В качестве неплавящегося электрода при аргонодуговой сварке применять вольфрамовые прутки лантанированные по ГОСТ 23949 диаметром 2-4 мм.
Для улучшения условий возбуждения дуги при аргонодуговой сварке и повышения ее стабильности рекомендуется затачивать конец вольфрамового электрода на конус под углом 14°+2°. При разрушении или загрязнении конца электрода следует произвести восстановление заточки.
8.10 Колебание напряжения питающей сети, к которой подключено сварочное оборудование, допускается не более ±5% от номинального значения.
8.15 Шланги подачи газа следует не реже одного раза в квартал промывать горячей водой в течение 10 минут с каждого конца с последующей продувкой сухим очищенным воздухом в течение 10-15 минут.
10.5 Свариваемые кромки и поверхность металла по внешней и внутренней поверхностям на ширине не менее 20 мм, а при ЭШС - на ширину не менее 50 мм, и по торцу должны быть зачищены механическим способом до металлического блеска и обезжирены ацетоном, уайт-спиритом или другим растворителем с применением протирочных материалов.
10.9 При толщине листового проката более 36 мм зону, прилегающую к кромкам, дополнительно контролировать ультразвуковым методом на ширину не менее 50 мм для выявления трещин, расслоений и т.д.
Перед установкой и приваркой штуцеров «впритык» следует выполнить контроль качества основного металла методом УЗД в объеме 100% на ширину не менее 100 мм от кромки стыка для выявления внутренних дефектов (трещин, расслоений и т.д.).
11.1.13 Удаление временных технологических планок следует производить по их металлу пневмозубилом, кислородной, плазменной или воздушно-дуговой резкой. При этом необходимо оставлять технологический припуск 3-5 мм. Технологический припуск удаляют шлифмашинкой, а места удаления контролируют внешним осмотром.
При изготовлении сосудов из углеродистых и низколегированных сталей толщиной 120 мм и более, а также сосудов, работающих в средах, вызывающих коррозионное растрескивание металла, места удаления временных технологических креплений контролируются цветной дефектоскопией.
Вырывы основного металла в при удалении временных креплений не допускаются.
12.3.2 Автоматическую сварку под флюсом сварных соединений без скоса кромок рекомендуется применять при толщине стенки до 20 мм, а при толщине стенки от 20 мм и выше рекомендуется применять швы с V-образной или Х-образной разделкой кромок.
14.7. При изготовлении изделия с применением автоматической сварки на каждое изделие сваривается один образец.
СТО 00220368-019-2011 Настоящий стандарт содержит требования и основные технологические рекомендации по термической обработке сварной нефтехимической, химической и газовой аппаратуры, её элементов и сборочных единиц, технологических трубопроводов, изготавливаемых из углеродистых, низколегированных, теплоустойчивых высоколегированных, двухслойных, разнородных сталей, а также сплавов на железоникелевой и никелевой основах. Классификация свариваемых материалов приведена в таблице Б1 Приложении Б.
СТО распространяется на проектировать, изготовление, монтаж и ремонт сосудов, аппаратов толщиной до 250 мм и технологических трубопроводов толщиной до 30 мм, работающих при температурах не ниже минус 70°С. Сосуды и аппараты работают под избыточным давлением до 16,0 МПа, технологические трубопроводы - до 320 МПа и подконтрольны Ростехнадзору, как опасные технические устройства.
СТО 00220575.063-2005 СОСУДЫ, АППАРАТЫ И БЛОКИ ТЕХНОЛОГИЧЕСКИЕ УСТАНОВОК ПОДГОТОВКИ И ПЕРЕРАБОТКИ НЕФТИ И ГАЗА, СОДЕРЖАЩИХ СЕРОВОДОРОД И ВЫЗЫВАЮЩИХ КОРРОЗИОННОЕ РАСТРЕСКИВАНИЕ
Настоящий стандарт распространяется на сосуды, аппараты и блоки технологические, проектируемые, изготавливаемые в соответствии с ОСТ 26 291 и ОСТ 26.260.18, предназначенные для работы в средах, содержащих сероводород с парциальным давлением равным или более 0,0003 МПа и вызывающих коррозионное растрескивание.
Настоящий стандарт не распространяется на сосуды, аппараты и блоки технологические, работающие в средах, содержащие сероводород при парциальном давлении менее 0,0003 МПа или других средах.
7.2.2 Технологическая документация на выполнение сварочных работ должна разрабатываться с учетом требований ОСТ 26 291, настоящего стандарта и конструкторской документации.
7.2.3 Ручная дуговая сварка покрытыми электродами применяется при выполнении криволинейных швов и швов малой протяженности, когда применение механизированных способов сварки невозможно или нерационально - приварка штуцеров и люков, исправление дефектов сварных соединений, а также выполнение подварочных швов.
Ручная дуговая сварка должна выполняться ниточными валиками шириной не более 3dэл, высота единичного валика (dэл + 1), где dэл - диаметр электрода, равный 3-4 мм. Каждый последующий валик должен перекрывать предыдущий на 1/3 ширины.
7.2.4 Автоматическая сварка под флюсом применяется при выполнении продольных и кольцевых швов сосудов и аппаратов, а также при выполнении подварочного (корневого) шва при комбинированном способе сварки.
Конструктивные элементы сварных соединений, техника и режимы автоматической сварки под флюсом должны соответствовать требованиям РД 26-17-77.
7.2.5 Электрошлаковая сварка применяется при выполнении продольных швов обечаек и изготовлении заготовок днищ сосудов и аппаратов их стали 20ЮЧ.
7.2.6 Аргонодуговая сварка неплавящимся электродом применяется при сварке корневого слоя односторонних швов, выполнении сварных соединений трубных проводок средств измерения, контроля и автоматизации, при обварке труб в трубных решетках теплообменной аппаратуры.
7.3.2 Сварные соединения трубопроводов обвязки аппаратов, блоков технологических подлежат термической обработке при наружном диаметре 57 мм и более.
ГОСТ 32569-2013 ТРУБОПРОВОДЫ ТЕХНОЛОГИЧЕСКИЕ СТАЛЬНЫЕ Требования к устройству и эксплуатации на взрывопожароопасных и химически опасных производствах
12.3.6. Контроль сварных соединений методом РД (ГОСТ 7512) или УЗД (ГОСТ 14782) следует проводить после устранения дефектов, выявленных внешним осмотром и измерениями, а для трубопроводов I категории, а также для трубопроводов с группой сред А(а) или работающих при температуре ниже минус 70°С - после контроля на выявление выходящих на поверхность дефектов методами магнитопорошковым (ГОСТ 21105) или капиллярным (ГОСТ 18442).
6.7.1.2. В трубопроводах, предназначенных для работы под давлением до 35 МПа (350 кгс/см2) включительно, допускается вварка штуцеров на прямых участках, а также применение тройников, сваренных из труб и штампосварных колен с двумя продольными швами при условии проведения 100% контроля сварных соединений методом УЗД или РД.
6.7.1.3. Вварка штуцеров в гнутые элементы (в местах гибов) трубопроводов не доПУСКАЕТСЯ. В обоснованных случаях на гибах трубопроводов, работающих под давлением до 35 МПа, может быть допущена вварка одного штуцера внутренним диаметром не более 25 мм.
10.1.22. Трубопроводы, проходящие через стены или перекрытия зданий, следует заключать в специальные гильзы или футляры. Сварные и разъемные соединения трубопроводы внутри футляров оводов внутри футляров или гильз не допускаются. Внутренний диаметр гильзы принимают на 10-12 мм больше наружного диаметра трубопровода (при отсутствии изоляции) или наружного диаметра изоляции (для изолированных трубопроводов.
10.4.11. Подвижные и неподвижные опоры трубопроводов с сероводородсодержащими средами должны применяться, как правило, хомутовые. Применение приварных к трубопроводу деталей опор без последующей термообработки мест приварки к трубопроводу не допускается.
11.1.4. Отклонение линейных размеров сборочных единиц трубопроводов не должно превышать ±3 мм на 1 м, но не более ±10 мм на всю длину, если в проектной документации нет других указаний.
13.1.7. Перед проведением испытаний вся запорная арматура, установленная на трубопроводе, должна быть полностью открыта, сальники уплотнены; на месте 84ГОСТ 32569-2013 регулирующих клапанов и измерительных устройств должны быть установлены монтажные катушки; все врезки, штуцера, бобышки для контрольно-измерительных при боров должны быть заглушены.
12.1.2. Газовая сварка допускается для труб из углеродистых и низколегированных неподкаливающихся сталей (17ГС, 09Г2С и др.) с условным диаметром до 80 мм и толщиной стенки не более 3,5 мм при давлении до 10 МПа (100 кгс/см2).
12.1.3 Газовая сварка стыков из низколегированных закаливающихся сталей (15ХМ, 12Х1МФ и др.) допускается при монтаже и ремонте труб с номинальным диаметром DN < 40 и толщиной стенки не более 5 мм при давлении до 10 МПа (100 кгс/см2).
12.1.8 Сварочные материалы должны быть аттестованы, иметь сертификаты и удовлетворять требованиям стандартов или ТУ.
12.1.9. При отсутствии сертификатов сварочные материалы допускается использовать только после проверки химического состава и механических свойств наплавленного металла на соответствие требованиям стандартов или ТУ.
12.2.2. К проведению работ по термической обработке сварных соединений допускаются термисты-операторы, прошедшие специальную подготовку, выдержавшие соответствующие испытания и имеющие удостоверение на право производства этих работ.
12.2.3 Обязательной термообработке подлежат:
- стыковые соединения элементов из углеродистых сталей с толщиной стенки более 36 мм;
- сварные соединения штуцеров с трубами из углеродистых сталей при толщине стенки трубы и штуцера более 36 и 25 мм соответственно;
- стыковые соединения элементов из низколегированных марганцовистых и кремнемарганцовистых сталей с толщиной стенки более 30 мм;
- сварные соединения штуцеров с трубами из низколегированных марганцовистых и кремнемарганцовистых сталей при толщине стенки трубы и штуцера более 30 и 25 мм соответственно;
12.2.6. Для трубопроводов из хромоникелевых аустенитных сталей независимо от величины рабочего давления применение газопламенного нагрева не допускается.
12.2.9. Режимы нагрева, выдержки и охлаждения при термической обработке труб и других элементов должны регистрироваться самопишущими приборами
12.3.2. Пооперационный контроль предусматривает проверку: качества и соответствия труб и сварочных материалов требованиям стандартов и ТУ на изготовление и поставку; качества подготовки концов труб и деталей трубопроводов под сварку и качества сборки стыков (угол скоса кромок, совпадение кромок, зазор в стыке перед сваркой, правильность центровки труб, расположение и число прихваток, отсутствие трещин в прихватках); температуры предварительного подогрева; - качества и технологии сварки (режима сварки, порядка наложения швов, качества послойной зачистки шлака);- режимов термообработки сварных соединений.
12.3.14. Определение сод. ферритной фазы должно проводиться в св. соединениях трубопроводов из аустенитных сталей на PN> 100 в объеме 100 % на сборочных единицах, предназначенных для работы при температуре выше 350 °С, а в остальных случаях - по требованию проекта.
12. 3. 15. Сварные соединения трубопроводов из легированных сталей для трубопроводов I категории или содержащих среды группы А(а), либо работающих с давлением PN > 100, подлежат стилоскопированию в объеме 100 %.
12.3.16. Измерение твердости проводят для сварных соединений трубопроводов, изготовленных из хромокремнемарганцовистых, хромомолибденовых, хромомолибденованадиевых, хромованадиевольфрамовых и хромомолибденованадиевольфрамовых сталей. Твердость необходимо измерять на каждом термообработанном сварном соединении по центру шва, в зоне термического влияния, по основному металлу. Результаты измерения твердости должны соответствовать требованиям НД.
12.3.17. При выявлении методами неразрушающего контроля дефектных сварных соединений контролю подвергают удвоенное от первоначального объема число сварных соединений на данном участке трубопровода, выполненных одним сварщиком.
12.3.21. Число контрольных сварных соединений для проведения механических испытаний и металлографических исследований должно соответствовать указанному в таблице 12.8.
Таблица 12.8 - Число контрольных сварных соединений
Номинальный диаметр трубы DN | Число контрольных соединений |
От 6 до 32 | |
От 50 до 150 | |
От 175 и более |
12.1.15. Резку труб и подготовку кромок под сварку необходимо проводить механическим способом. Допускается применение газовой резки для труб из углеродистых, низколегированных и теплоустойчивых сталей, а также воздушно-дуговой и плазменной резки для труб из всех марок сталей. При огневой резке труб должен быть предусмотрен припуск на механическую обработку.
11.2.7. Вварка штуцеров, бобышек, муфт и других деталей в местах расположения сварных швов, в гнутые и штампованные детали трубопроводов не допускается.
ФНП ОИД Федеральные нормы и правила в области промышленной безопасности "Правила промышленной безопасности опасных производственных объектов, на которых используется оборудование, работающее под избыточным давлением "
10. Установка, размещение и обвязка оборудования под давлением на объектах, для применения на которых оно предназначено, должны осуществляться на основании проектной документации, разработанной специализированными проектными организациями с учетом требований законодательства в области промышленной безопасности и законодательства о градостроительной деятельности. Отклонения от проектной документации не допускаются.
92. Техническое перевооружение ОПО, монтаж (демонтаж), ремонт, реконструкцию (модернизацию), наладку оборудования под давлением должны осуществлять специализированные организации, имеющие статус юридического лица и организационную форму, соответствующую требованиям законодательства Российской Федерации, а также индивидуальные предприниматели 94. Реконструкция (модернизация) оборудования под давлением должна быть осуществлена по проекту, разработанному организацией - изготовителем оборудования или проектной организацией. Если реконструкция (модернизация) проводится с отступлениями от требований руководства (инструкции) по эксплуатации, то эти отступления должны быть согласованы с разработчиком руководства (инструкции) по эксплуатации.
106. Монтаж, ремонт и реконструкция (модернизация) оборудования под давлением с применением сварки и термической обработки должны быть проведены по технологии и рабочим чертежам, разработанным до начала производства работ специализированной организацией, выполняющей соответствующие работы.
109. Резка листов, труб и других полуфабрикатов, а также вырезка отверстий могут быть выполнены любым способом (механическим, газопламенным, электродуговым, плазменным).
114. При доизготовлении на месте эксплуатации, монтаже, ремонте, реконструкции (модернизации) оборудования под давлением должна быть применена технология сварки, аттестованная в соответствии с установленными требованиями.
130. Сварочные материалы должны быть проконтролированы: на наличие соответствующей сопроводительной документации; каждая партия электродов - на сварочно-технологические свойства, а также на соответствие содержания легирующих элементов нормированному составу путем стилоскопирования металла, выполненного легированными электродами; каждая партия порошковой проволоки - на сварочно-технологические свойства; каждая бухта (моток, катушка) легированной сварочной проволоки - на наличие основных легирующих элементов путем стилоскопирования или другим спектральным методом, обеспечивающим подтверждение наличия в металле легирующих элементов;
137. Не допускается применение газовой сварки для деталей из аустенитных сталей и высокохромистых сталей мартенситного и мартенситно-ферритного класса.
141. Термическая обработка элементов оборудования при монтаже, ремонте, реконструкции (модернизации) проводится в случаях, установленных технологической документацией с учетом рекомендаций изготовителя, указанных в руководстве (инструкции) по эксплуатации.
142. При доизготовлении на месте эксплуатации, монтаже, ремонте, реконструкции (модернизации) оборудования под давлением должна быть применена система контроля качества сварных соединений, гарантирующая выявление недопустимых дефектов, высокое качество и надежность эксплуатации этого оборудования и его элементов.
144. Контроль качества сварных соединений должен быть проведен в порядке, предусмотренном проектной и технологической документацией.
147. Визуальный и измерительный контроль, а также предусмотренное технологической документацией стилоскопирование (или другой спектральный метод, обеспечивающий подтверждение фактической марки металла или наличие в нем легирующих элементов) должны предшествовать контролю другими методами.
151. Методы и объемы контроля сварных соединений приварных деталей, не работающих под внутренним давлением, должны быть установлены технологической документацией.
156. Ультразвуковую дефектоскопию и радиографический контроль проводят в целях выявления в сварных соединениях внутренних дефектов (трещин, непроваров, шлаковых включений).
159. Ультразвуковая дефектоскопия и радиографический контроль стыковых сварных соединений по согласованию с разработчиком проектной документации может быть заменен другими методами неразрушающего контроля, позволяющими выявлять в сварных соединениях внутренние дефекты.
160. Класс и уровень чувствительности капиллярного и магнитопорошкового контроля должны быть установлены технологической документацией.
162. Измерение твердости металла сварного соединения проводят в целях проверки качества выполнения термической обработки сварных соединений.
163. Механические испытания проводят при: аттестации технологии сварки; контроле сварных стыковых соединений, выполненных газовой и контактной сваркой; входном контроле сварочных материалов, используемых при сварке под флюсом и электрошлаковой сварке.
166. Испытание сварных соединений на стойкость против межкристаллитной коррозии должно быть произведено для сосудов и их элементов, изготовленных из сталей аустенитного, ферритного, аустенитно-ферритного классов и двухслойных сталей с коррозионно-стойким слоем из аустенитных и ферритных сталей.
169. Гидравлическое испытание в целях проверки плотности и прочности оборудования под давлением, а также всех сварных и других соединений проводят: после монтажа (доизготовления) на месте установки оборудования, транспортируемого к месту монтажа (доизготовления) отдельными деталями, элементами или блоками; после реконструкции (модернизации), ремонта оборудования с применением сварки элементов, работающих под давлением; при проведении технических освидетельствований и технического диагностирования.
РЕКОМЕНДАЦИИ ПО УСТРОЙСТВУ И БЕЗОПАСНОЙ ЭКСПЛУАТАЦИИ ТЕХНОЛОГИЧЕСКИХ ТРУБОПРОВОДОВ (РБ технологич. трубопроводов)
1. Руководство по безопасности «Рекомендации по устройству и безопасной эксплуатации технологических трубопроводов» (далее – Руководство по безопасности) содержит общие рекомендации по обеспечению требований промышленной безопасности, предупреждению аварий, инцидентов, случаев производственного травматизма при проектировании, устройстве, изготовлении, испытаниях, монтаже, эксплуатации, экспертизе промышленной безопасности стальных трубопроводов, предназначенных для транспортирования в пределах промышленных предприятий химической, нефтехимической, нефтяной, нефтеперерабатывающей, газовой и других смежных отраслей промышленности газообразных, парообразных и жидких сред, с расчетным давлением до 320 МПа, вакуумом с абсолютным давлением не ниже 665 Па (5 мм рт. ст.) при температуре среды от минус 196 оС до 700 оС, и не является нормативным правовым актом.
9. Трубопроводы в зависимости от класса опасности транспортируемого вещества (взрыво-, пожароопасность и вредность) рекомендуется подразделять на группы (А, Б, В) и в зависимости от расчетных параметров среды (давления и температуры) – на пять категорий (I, II, III, IV, V).
48. Бесшовные трубы рекомендуется в целях безопасности изготавливать из катаной, кованой, непрерывной или центробежнолитой заготовки.
Электросварные трубы с продольным или спиральным швом
Состав сооружений: решетки и песколовки: Решетки – это первое устройство в схеме очистных сооружений. Они представляют...
Историки об Елизавете Петровне: Елизавета попала между двумя встречными культурными течениями, воспитывалась среди новых европейских веяний и преданий...
Опора деревянной одностоечной и способы укрепление угловых опор: Опоры ВЛ - конструкции, предназначенные для поддерживания проводов на необходимой высоте над землей, водой...
Организация стока поверхностных вод: Наибольшее количество влаги на земном шаре испаряется с поверхности морей и океанов (88‰)...
© cyberpedia.su 2017-2024 - Не является автором материалов. Исключительное право сохранено за автором текста.
Если вы не хотите, чтобы данный материал был у нас на сайте, перейдите по ссылке: Нарушение авторских прав. Мы поможем в написании вашей работы!