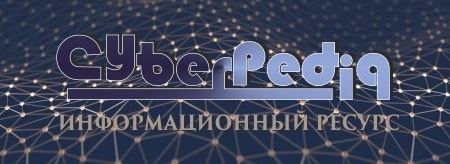
Своеобразие русской архитектуры: Основной материал – дерево – быстрота постройки, но недолговечность и необходимость деления...
Индивидуальные очистные сооружения: К классу индивидуальных очистных сооружений относят сооружения, пропускная способность которых...
Топ:
Проблема типологии научных революций: Глобальные научные революции и типы научной рациональности...
Техника безопасности при работе на пароконвектомате: К обслуживанию пароконвектомата допускаются лица, прошедшие технический минимум по эксплуатации оборудования...
Интересное:
Что нужно делать при лейкемии: Прежде всего, необходимо выяснить, не страдаете ли вы каким-либо душевным недугом...
Отражение на счетах бухгалтерского учета процесса приобретения: Процесс заготовления представляет систему экономических событий, включающих приобретение организацией у поставщиков сырья...
Наиболее распространенные виды рака: Раковая опухоль — это самостоятельное новообразование, которое может возникнуть и от повышенного давления...
Дисциплины:
![]() |
![]() |
5.00
из
|
Заказать работу |
|
|
Ремонтопригодность входит в понятие надежности. Однако высокая надежность машины, не всегда означает высокую ремонтопригодность.
Ремонтопригодность – это свойство объекта, заключающееся в приспособленности к предупреждению и обнаружению причин возникновения его отказов, повреждений и устранению их последствий путем проведения ремонтов и технического обслуживания.
Ремонтопригодность характеризуется контролепригодностью, ремонто-доступностью и ремонтоспособностью.
Контролепригодность определяется возможностью удобного контроля состояния узлов и деталей.
Ремонтодоступность определяется доступностью и легкосъемностью узлов и деталей.
Ремонтоспособность определяется способностью машины к замене деталей и способностью деталей к восстановлению.
Основной показатель ремонтопригодности – среднее время восстановления (вынужденного простоя), необходимое для обнаружения и устранения отказа.
Основные требования к ремонтопригодности оборудования можно разделить на две группы.
К первой группе относятся требования, обеспечивающие ремонтопригодность оборудования при осмотре и ремонте на месте:
- свободный доступ к узлам и деталям, подлежащим осмотру, регулировке или замене;
- быстрая замена изнашивающихся деталей;
- наладка взаимодействия узлов и деталей, нарушенного в процессе работы;
- проверка качества смазки, ее замена или пополнение на месте работы оборудования;
- быстрое определение причин аварий и отказов в работе оборудования и их устранение.
Ко второй группе относятся требования, обеспечивающие ремонтопригодность при ремонте оборудования в РМЦ предприятий:
- простота разборки и сборки узлов, а также их комплексов;
|
- применение простых средств механизации на операциях разборки и сборки;
- максимальная возможность восстановления номинальных размеров изнашивающихся элементов корпусов, сложных и базовых деталей;
- экономически оправданная возможность восстановления номинальных размеров изнашивающихся элементов остальных деталей;
- простота проверки состояния деталей и узлов после стендовых испытаний;
- возможность проверки взаимодействия всех частей оборудования после ремонта.
Износ оборудования
Уменьшение надежности и снижение долговечности оборудования обусловливаются ухудшением его состояния, наступающим в результате физического или морального износа.
Моральный износ оборудования определяется отставанием его технического и конструктивного назначения или состоятельности от уровня передовой техники. Причины морального износа – низкая производительность, низкое качество выпускаемой продукции, низкий коэффициент полезного действия, пониженная надежность и т.д.
Под физическим износом следует понимать изменение формы, размеров, целостности и физико-механических свойств деталей и узлов, устанавливаемое визуально или путем измерений и анализов.
Физический износ подразделяют на:
- механический;
- коррозионный;
- тепловой.
Механический износ выражается в изменении размеров или формы детали, нарушении ее целостности, появлении задиров, царапин, трещин. Косвенными признаками механического износа являются снижение показателей работы машины, появление вибраций, заклиниваний и т.д.
Механический износ зависит от следующих факторов:
1) качества металла трущихся поверхностей;
2) чистоты обработки трущихся поверхностей;
3) наличия и качества смазки деталей трущихся пар.
Коррозионный износ выражается в разрушении металлов при химическом или электрохимическом взаимодействии их с окружающей средой. Металлы разрушаются при взаимодействии с жидкими и газообразными продуктами, а также в результате окислительно-восстановительных процессов взаимодействия с окружающей атмосферой.
|
Для аппаратов химической промышленности коррозионный износ является наиболее частой причиной выхода их из строя.
По характеру разрушений коррозия может быть сплошной (по всей поверхности металла) и местной (в виде отдельных язвин, пятен, сквозных отверстий, трещин). При сплошной коррозии долговечность аппарата определяется припуском на коррозию; при местной коррозии долговечность аппарата может быть определена только с помощью методов теории надежности.
В химической промышленности отказы аппаратуры распределяются по видам коррозии следующим образом:
1) коррозионное растрескивание – 35 %;
2) дырочная коррозия – 20 %;
3) общая (равномерная) коррозия – 18 %;
4) межкристаллитная коррозия – 16 %;
5) другие виды коррозии – 11 %.
В наибольшей степени коррозии подвержены:
1) места с высокой линейной скоростью среды (например, у входного и выходного штуцеров при большой скорости среды происходит разрушение защитных пленок металла);
2) участки с остаточными напряжениями, в которых имеет место коррозионное растрескивание (чаще всего это сварные швы, а также штампованные или точеные детали, с которых не снято напряжение);
3) застойные зоны, в которых может скапливаться жидкость (поэтому в аппаратах необходимо предусматривать сливные отверстия);
4) зоны нагрева (при повышении температуры скорость коррозии резко увеличивается);
5) узлы трения (механический износ при воздействии агрессивной среды усиливается, изменяются также свойства смазки).
Тепловой износ выражается в разрушении металлов под действием высоких температур.
глава 4
Ремонт и монтаж валов
Ремонт валов
Вали и оси, применяемые в оборудовании, характеризуются большим разнообразием форм, размеров и материалов, из которых они изготовлены.
В процессе эксплуатации валов изнашиваются посадочные места шеек валов, шпоночные канавки, шлицы, резьба, появляется изгиб вала.
Способ ремонта изношенного вала выбирают в зависимости от характера и размеров дефекта, а также технической оснащенности ремонтной базы.
Шейки валов, имеющие небольшие царапины, риски, овальность до 0,1 мм, ремонтируют шлифованием. Если износ значительный, шейки валов протачивают и шлифуют под очередной ремонтный размер, при этом диаметр шеек при ударной нагрузке не должен уменьшаться более 5 %, а при спокойной нагрузке более 10 %.
|
В тех случаях, когда необходимо восстановить первоначальные размеры шеек, на шейки после их обточки напрессовывают переходные втулки, которые затем обтачивают и шлифуют. Изношенные поверхности валов можно ремонтировать также наращиванием металла металлизацией, хромированием, наплавкой и другими методами.
Рисунок – Способы наплавки поверхностей валов
а – вдоль вала; б – по спирали.
Трещины на валах заделываются сваркой. Для этого участок, охваченный трещиной, на всю глубину обрабатывают под сварку (снимают фаски, зачищают свариваемые поверхности). Сварку трещин следует проводить как можно быстрее, чтобы предотвратить закалку металла шва и околошовной зоны, иначе шов может оказаться хрупким.
Поломанные валы восстанавливают сваркой. Прочность восстановленного вала на участке сварки обычно не превышает 60 % прочности целого вала. Поэтому ответственные, сильно нагруженные валы при поломке не ремонтируются, а заменяют новыми.
Рисунок – Способы сварки поломанных валов
а – только с подготовкой шва; б – с центрирующим шплинтом; в – с центрирующей шпилькой; г – со вставкой.
Рисунок – Кондуктор для сварки поломанных валов
1 – поломанный вал; 2, 3 – крепежные планки; 4 – жесткая рама; 5 – центровочная линза
Погнутые валы выправляют механическим способом в холодном состоянии или при нагреве. Правку проводят в центрах с помощью пресса или домкрата.
Рисунок – Пресс для правки валов
1, 6 – подвижные винты; 2, 4 – призмы; 3 – выпрямляемый вал; 5 - рама
Незначительную погнутость небольших валов (до 0,05% длины) можно выправить молотком с шаровой головкой.
Валы больших диаметров можно выправить путем местного нагрева пламенем горелки до 200 – 600 °С. Температура нагрева и время выдержки при этой температуре должны быть тем выше, чем больше диаметр и прогиб вала. Нагревают только участок прогиба, остальные поверхности защищают от действия пламени горелок. Вал должен остывать медленно, поэтому его оборачивают асбестом. При исправлении больших прогибов методом нагрева восстановленный вал следует отжечь, чтобы снять остаточные напряжения.
|
Изношенные шпоночные пазы ремонтируют:
- обработкой пазов обеих деталей до следующего по стандарту большего размера шпоночного соединения (кроме пазов в ответственных деталях);
- заваркой шпоночных пазов электронаплавкой с обработкой новых в другом месте;
- заваркой стенок изношенных пазов больших размеров с последующим фрезерованием до стандартного размера.
При износе шлицев их можно ремонтировать путем раздачи зубьев вручную, на токарном или строгальном станках.
Сорванную и забитую резьбу на валу прорезают на другой диаметр, а если это сделать нельзя, то ее заваривают и нарезают новую. Возможна также посадка втулки на проточенное место и нарезание не ней резьбы прежнего размера.
Рисунок – Установка резьбовой втулки на вал
1 – вал; 2 – втулка; 3 – стопорный штифт
Монтаж валов
Валы и оси устанавливают при сборке таким образом, чтобы они занимали правильное положение в пространстве по отношению к базовой детали и другим валам и осям. Это обычно достигается правильной сборкой опор, в которых они покоятся.
Тяжелые валы устанавливают в опоры с помощью подъемных механизмов. При этом валы стропятся пеньковым канатом или стальным тросом, но обязательно с деревянными подкладками, что позволяет предохранить обработанную поверхность валов и деталей, закрепленных на них, от повреждений.
Установка и выверка валов почти всегда связаны с регулированием положения, а иногда и соответствующей обработкой (подшабриванием) подшипников. Одновременно с точным соблюдением положения оси вала добиваются такого сопряжения подшипников с валом, чтобы в пределах допустимых зазоров между ними он проворачивался вокруг своей оси легко и плавно. Шейки валов должны прилегать к соответствующим вкладышам равномерно по всей опорной поверхности. Равномерность контакта проверяют по отпечаткам как на вкладыше, так и на поверхности вала (проверка на краску).
При сборке машин очень важно точно выдержать взаимное расположение валов.
Параллельность валов проверяют штангенциркулем. С его помощью измеряют расстояние между образующими проверяемых валов в нескольких точках, добиваясь равенства результатов замеров путем регулировки положения осей, т. е. подшипников.
Перпендикулярность валов проверяют с помощью специальных угольников.
Горизонтальность валов проверяют уровнемером с призматической опорной поверхностью.
|
Вертикальность валов проверяют с помощью отвеса.
В монтажной и ремонтной практике часто приходится проверять соосность совместно работающих валов. Соосность валов может быть нарушена в результате радиального смещения осей валов, остающихся параллельными друг другу, или наклона осей, вследствие чего валы оказываются расположенными в разных плоскостях, пересекающихся друг с другом.
Выверка соосности валов называется центровкой. Плохая центровка является причиной быстрого выхода из строя подшипников, узлов уплотнения (сальников), деталей соединительных муфт и самих валов.
Центрируемые валы проверяют одновременно на радиальное смещение и перелом осей в месте соединения. Способ центрирования зависит от конструкции и размеров валов, а также от деталей, насаженных на их концы.
Если на стыкуемые концы валов насажены детали, наружные цилиндрические поверхности которых обработаны концентрично посадочным отверстиям (полумуфты, шкивы), достаточная точность центровки достигается с помощью линейки. К поверхности детали на конце одного из валов прикладывают жесткую линейку и измеряют расстояние между ней и поверхностью детали на другом валу и расстояние между торцами этих деталей в плоскости линейки по периферии. Если валы не смещены и являются соосными, то при совместном их проворачивании эти расстояния должны быть постоянными в любом положении.
Если на концах валов нет точно обработанных деталей, то для их центровки используют специальные приспособления.
Рисунок – Проверка соосности вала.
а – центровка вала по муфтам; б – центровка с использованием индикаторов;
в – схема измерения
Подшипники скольжения
Ремонт
В процессе работы у подшипников скольжения нарушается геометрическая форма трущихся поверхностей, появляются риски и задиры, расслаивается и выкрашивается баббитовый слой и т.д.
Рисунок – Подшипник скольжения
1 – корпус подшипника; 2 – маслоподающее кольцо;
3 – вырез в верхнем вкладыше; 4 – масло.
Когда износ трущихся поверхностей достигает предельно допустимой величины, вал и подшипник ремонтируют (вал шлифуют, а у подшипника восстанавливают правильную геометрическую форму).
Неразъемные (глухие) подшипники скольжения восстанавливают расточкой с последующей запрессовкой новой втулки.
Разъемные подшипники скольжения восстанавливают шабрением или перезаливкой вкладышей.
Если износ не большой, то выполняют шабрение. Шабровка осуществляется путем соскабливания неровностей с поверхности баббитовой заливки.
Рисунок – Крепление вкладыша подшипника к постели для шабрения
1 – прижим; 2 – постель; 3 – вкладыш
При значительном износе вкладышей или расслоении баббита их перезаливают.
Восстанавливая баббитовые вкладыши, необходимо удалить старый слой баббита. Для этого вкладыши подогревают до температуры 250 – 300 °С. Подогрев ведут с тыльной стороны вкладыша, чтобы уменьшить процесс межкристаллитной коррозии баббита. После удаления старого баббита внутреннюю поверхность вкладыша тщательно очищают механическим путем и протравливают в 10 –15 %-ном растворе серной или в 50%-ном растворе соляной кислоты, затем промывают теплой водой и обезжиривают 80%-ным раствором каустической соды с последующей промывкой и сушкой.
Для получения качественной заливки баббита поверхности вкладыша лудят чистым оловом или третником (70% свинца и 30% олова), в результате чего поверхность вкладыша должна иметь чистый блестящий вид.
После лужения вкладыши собирают в заливочной форме, подогревают до 200 – 250 °С и при строго определенной температуре заливают баббитом.
Заливку подшипников осуществляют вручную или центробежным способом в специальной форме.
При ручном способе возможна одновременная заливка двух половинок подшипника в сборе или каждой половинки отдельно. Перед заливкой вкладыш прогревается на стальном листе до температуры 180 – 200 °С. Расплавленный баббит, объем которого несколько больше объема заливки, перегревается на 25 – 50 °С выше температуры плавления и быстро заливается непрерывной струей. После заливки поверхность баббита протыкается нагретым докрасна стальным прутком для выхода газа.
При центробежной заливке оба вкладыша в сборе устанавливаются на специальных станках или приспособлениях. Заливка баббита ведется при вращении вкладышей. Центробежная заливка уменьшает газонаполнение слоя.
Рисунок – Приспособление для центробежной заливки вкладышей подшипников
1 – крепежная планшайба; 2 – торцевая крышка; 3 – вкладыш;
4 – задняя крышка; 5 – барабан; 6 – заливной бункер.
После остывания подшипники подвергаются контролю. Поверхность их должна иметь ровный серебристый цвет. Плотность сцепления баббита с поверхностью подшипника проверяют простукиванием молотком.
В залитых вкладышах фрезеруются смазочные канавки, сверлятся смазочные отверстия, затем осуществляется шабровка.
Монтаж
При монтаже подшипников скольжения решающее значение имеет установление нормального зазора между верхним и нижним вкладышами. От этого зависит степень затяжки подшипника. На плоскость разъема кладут свинцовую проволоку и затягивают подшипник до тех пор, пока не будет устранен люфт в сопряжении с валом при свободном проворачивании последнего. По толщине деформированной проволоки подбирают металлическую прокладку, окончательно устанавливаемую при сборке.
Подшипники качения
Ремонт
В процессе эксплуатации за подшипниками качения должно быть установлено систематическое наблюдение. Основные факторы, характеризующие условия эксплуатации, – это температура корпуса, характер шума подшипников и эффективность уплотняющих устройств. При отклонении от норм эксплуатации необходимо остановить агрегат, вскрыть подшипниковый узел, выявить причины, вызвавшие дефекты в работе узла, и только после полного их устранения допустить агрегат к дальнейшей эксплуатации.
Подшипники качения в ремонтных цехах предприятий не ремонтируют, а только восстанавливают посадочные поверхности деталей, сопрягаемых с подшипниками, т. е. корпусов и валов.
При выявлении признаков усталостного износа на беговых дорожках и телах качения, выкрашивания бортов, деформации сепаратора, ржавчины на рабочих поверхностях подшипник следует заменить.
Монтаж
Поступающие на монтаж подшипники качения промывают бензином для удаления консистентной смазки, высушивают на воздухе и тщательно осматривают. При осмотре обращают внимание на то, чтобы на поверхностях деталей не было трещин, забоин, царапин и цветов побежалости. Кольца подшипника должны вращаться относительно друг друга легко, без заеданий и стука.
Монтаж подшипников выполняют в строгом соответствии с рабочими чертежами. Нельзя произвольно заменять подшипники только по признаку равенства монтажных размеров. Необходимо использовать подшипники только проектных номеров. Подшипник устанавливают в узел так, чтобы торец с клеймом был обращен наружу.
Порядок сборки подшипника следующий: сначала его насаживают на вращающуюся деталь, затем вместе с деталью, устанавливают на неподвижной детали.
Запрессовку колец в большинстве случаев осуществляют в холодном состоянии. Однако при монтаже с большим усилием натяга подшипник (при посадке внутреннего кольца) или корпус (при посадке наружного кольца) нагревают в масляной ванне до 100 – 150 °С.
Подшипники устанавливают в корпус и на вал вручную с помощью медной выколотки и ручника, а также пресса.
Рисунок – Посадка подшипников качения
а – на вал; б – на вал и во втулку одновременно
1 – вал; 2 – оправка.
§ 3 Ремонт и монтаж зубчатых передач
Ремонт
В процессе эксплуатации зубчатые передачи могут иметь следующие дефекты:
- износ зубьев по рабочему профилю;
- излом одного или нескольких зубьев;
- трещины в венце, ступице или спицах;
- смятие поверхностей отверстия или шпоночной канавки в ступице;
- смятие шлицев, торцов зубьев;
- осповидные разрушения на поверхности под действием контактных напряжений.
Эти дефекты определяют измерением и внешним осмотром.
Методы ремонта зубчатых колес выбирают в зависимости от назначения передачи, класса точности и условий производства. Зубчатые колеса можно ремонтировать наплавкой изношенных зубьев, установкой зубьев-шипов или зубьев-штифтов. Однако эти способы ремонта являются временными мерами.
Рисунок – Ремонт зубчатых колес
а – крепление зубьев винтами; б – крепление зубьев сваркой;
в – наплавка зубьев, основа которых образована ввернутыми шпильками;
г – наплавка зубьев по медным шаблонам;
1 – крепежный винт; 2 – шпильки; 3 – вставной зуб;
4 – планка для соединения медных шаблонов;
5 – планки для соединения шаблонов с венцом шестерни
Ремонт трещин на ступице, ободе, спицах выполняют заваркой или стяжкой накладками и болтами. Однако эти способы ремонта следует применять лишь в качестве временной меры.
Рисунок – Восстановленная ступица
1 – ступица; 2, 3 – бандажи.
Изношенные зубчатые передачи следует заменять новыми парами даже в тех случаях, когда одно колесо в заменяемой паре существенного износа не имеет (кроме зубчатых колес с большой разностью диаметров).
В червячных передачах наибольшему износу подвергаются зубья червячного колеса. Их ремонт не представляет значительных трудностей, так как у большинства колес бронзовый венец выполняется легкосъемным. Изношенный червяк заменяют новым.
Монтаж
Детали зубчатых передач работают в различных условиях. От точности монтажа деталей передач зависит их долговечность, а также долговечность других узлов оборудования (валов, подшипников).
Перед монтажом цилиндрических зубчатых колес проверяют: соответствие фактических размеров передачи данным чертежа; концентричность отверстия в ступице под посадку на вал и наружной поверхности (окружности, выступов); постоянство шага зацепления и высоты зуба; наличие необходимых фасок на торцах зубьев, а также посадочных отверстий.
Валы, на которые насаживают сопрягаемую пару цилиндрических шестерен, должны быть строго параллельны, и расположены так, чтобы расстояние между их осями находилось в пределах допусков. Межцентровое расстояние проверяют штангенциркулем или калибрами.
Если сопрягаемая пара изготовлена и собрана правильно, то зубья приходят в контакт по всей их длине. Контакт зубьев проверяют краской (на окрашенных поверхностях в местах хорошего сопряжения появляются отчетливые пятна). По краске можно узнать и качество контакта по высоте зуба. Радиальные и боковые зазоры в зацеплениях, проверяют щупом.
При монтаже конических шестерен требуется точное соблюдение угла между осями зацепляющейся пары, а также обязательное пересечение этих осей. Положение осей проверяют с помощью различных приспособлений (в зависимости от конструкции сопряжения).
Монтаж червячной передачи должен отличаться высокой точностью. Важно соблюдать межцентровое расстояние, ось червяка должна совпадать с осью средней плоскости колеса. Совпадение осей легко определяется по отпечаткам краски на зубьях червячного колеса после проворачивания червяка на несколько оборотов.
|
|
Общие условия выбора системы дренажа: Система дренажа выбирается в зависимости от характера защищаемого...
Типы сооружений для обработки осадков: Септиками называются сооружения, в которых одновременно происходят осветление сточной жидкости...
История развития хранилищ для нефти: Первые склады нефти появились в XVII веке. Они представляли собой землянные ямы-амбара глубиной 4…5 м...
Кормораздатчик мобильный электрифицированный: схема и процесс работы устройства...
© cyberpedia.su 2017-2024 - Не является автором материалов. Исключительное право сохранено за автором текста.
Если вы не хотите, чтобы данный материал был у нас на сайте, перейдите по ссылке: Нарушение авторских прав. Мы поможем в написании вашей работы!