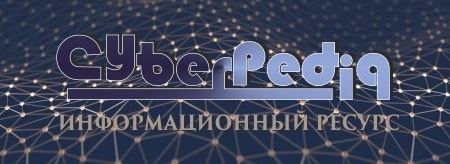
Адаптации растений и животных к жизни в горах: Большое значение для жизни организмов в горах имеют степень расчленения, крутизна и экспозиционные различия склонов...
Механическое удерживание земляных масс: Механическое удерживание земляных масс на склоне обеспечивают контрфорсными сооружениями различных конструкций...
Топ:
Особенности труда и отдыха в условиях низких температур: К работам при низких температурах на открытом воздухе и в не отапливаемых помещениях допускаются лица не моложе 18 лет, прошедшие...
Марксистская теория происхождения государства: По мнению Маркса и Энгельса, в основе развития общества, происходящих в нем изменений лежит...
Комплексной системы оценки состояния охраны труда на производственном объекте (КСОТ-П): Цели и задачи Комплексной системы оценки состояния охраны труда и определению факторов рисков по охране труда...
Интересное:
Влияние предпринимательской среды на эффективное функционирование предприятия: Предпринимательская среда – это совокупность внешних и внутренних факторов, оказывающих влияние на функционирование фирмы...
Искусственное повышение поверхности территории: Варианты искусственного повышения поверхности территории необходимо выбирать на основе анализа следующих характеристик защищаемой территории...
Как мы говорим и как мы слушаем: общение можно сравнить с огромным зонтиком, под которым скрыто все...
Дисциплины:
![]() |
![]() |
5.00
из
|
Заказать работу |
|
|
Свойства обрабатываемых материалов: s b = 500…1200 МПа;
модуль упругости Е = 210 000 МПа; коэффициент трения m = 0,3.
Режимы резания: V = 0,5…40 м/мин; Sz = 0,005…0,3 мм/зуб.
Геометрия режущего клина инструмента: g = –10°; 0°; +10°;
a = 3…8°; l = 0…20°; радиус округления r = 0…0,02 мм.
Условия резания (деформирования),
принятые при моделировании
Свойства обрабатываемых материалов: s b = 500…1200 МПа;
Е = 210 000 МПа; m = 0,3.
Режимы резания: V = V деф ® min; а = Sz = 0,1; 0,5; 1,0 мм;
b = t > 10 мм.
Геометрия режущего клина инструмента: g = –10°; 0°; +10°;
a = 5°; l = 0°; r = 0; 0,3; 0,6 мм.
Объекты исследования
I – краевая зона обрабатываемой детали;
II – зона контакта стружки с инструментом;
III – режущий клин инструмента.
Математическое моделирование
деформации краевой зоны детали
Приведем пример математического моделирования деформации краевой зоны детали при выходе инструмента из заготовки
(рис. 32, 33).
Рис. 32. Схема краевой зоны при выходе инструмента из заготовки: а – толщина срезаемого слоя; b – угол сдвига; U – перемещение инструмента | Рис. 33. Расчетная схема дефор- мирования краевой зоны |
Математические зависимости
Характеристики напряженно-деформированного состояния (НДС):
u (r) – поля векторов перемещения точек тела;
r ÎW – точка тела, заданная своим радиус-вектором;
e(r) – компоненты тензора деформации;
s(r) – компоненты тензора напряжений;
s (r) – степень деформации материала.
В образце реализуется плосконапряженное состояние:
s33 = t13 = t23 = g13 = g23 = 0.
При деформировании должны выполняться следующие условия:
– уравнение равновесия ;
– физические соотношения ;
– геометрические соотношения
– граничные условия:
|
для точек левой стороны области
для точек свободной поверхности
для точек, контактирующих с инструментом:
Результаты изменения предела прочности представлены на рис. 34.
I = 4 мм | I = 3 мм | I = 2 мм | |
s b = 50 + 300 S | ![]() | ||
s b = 50 + 200 S | |||
s b = 50 + 100 S |
Рис. 34. Влияние модуля упрочнения материала на степень деформации краевой зоны детали
2.2. Процесс стружкообразования
2.2.1. Типы стружек при резании пластичных
и хрупких материалов
В 1870 году И.А. Тиме была предложена классификация типов стружек, образующихся при резании различных материалов. Классификация оказалась настолько удачной, что, несмотря на то, что со времен И.А. Тиме появились совершенно новые конструкционные материалы, обрабатывающиеся с иными режимами резания, ею пользуются и в настоящее время. Согласно классификации И.А. Тиме
при резании конструкционных материалов в любых условиях образуются четыре вида стружек: элементная, суставчатая, сливная
и стружка надлома. Элементную, суставчатую и сливную стружку называют стружками сдвига, так как их образование связано с напряжениями сдвига. Стружку надлома иногда называют стружкой отрыва, так как ее образование связано с растягивающими напряжениями. Внешний вид всех перечисленных типов стружки изображен на рис. 35.
a б в г
Рис. 35. Типы стружек, образующихся при резании пластичных и хрупких материалов: а – элементная, б – суставчатая, в – сливная, г – стружка надлома
Элементная стружка (см. рис. 35, а) состоит из отдельных элементов 1 приблизительно одинаковой формы, несвязанных или слабо связанных друг с другом. Границу тп, отделяющую образовавшийся элемент стружки от срезаемого слоя, называют поверхностью скалывания. Физически она представляет собой поверхность, по которой
в процессе резания периодически происходит разрушение срезаемого слоя.
У суставчатой стружки (см. рис. 35, б) разделения на отдельные части не происходит. Поверхность скалывания только наметилась, но она не пронизывает стружку по всей толщине. Поэтому стружка состоит как бы из отдельных суставов 1 без нарушения связи между ними.
|
Основным признаком сливной стружки (см. рис. 35, в) является ее сплошность (непрерывность). Если на пути движения сливной стружки нет никаких препятствий, то она сходит непрерывной лентой, завиваясь в плоскую или винтовую спираль, пока часть стружки не отламывается под действием собственного веса. Поверхность 1 стружки, прилегающую к передней поверхности инструмента, называют контактной стороной (поверхностью). Она сравнительно гладкая, а при высоких скоростях резания отполирована в результате трения о переднюю поверхность инструмента. Ее противоположную поверхность 2 называют свободной стороной (поверхностью) стружки. Она покрыта мелкими зазубринками-насечками и при высоких скоростях резания имеет бархатистый вид. Стружка соприкасается
с передней поверхностью инструмента в пределах площадки контакта, ширина которой обозначена через с, а длина равна рабочей длине главного лезвия. В зависимости от рода и свойств обрабатываемого материала и скорости резания ширина площадки контакта
в 1,5…6 раз больше толщины срезаемого слоя.
Стружка надлома (см. рис. 35, г) состоит из отдельных, не связанных друг с другом кусочков различной формы и размеров. Образованию стружки надлома сопутствует мелкая металлическая пыль. Поверхность разрушения тп может располагаться ниже поверхности резания, в результате чего последняя покрыта следами от выломанных из нее кусочков стружки.
Тип стружки во многом зависит от рода и механических свойств обрабатываемого материала. При резании пластичных материалов возможно образование первых трех типов стружки, элементной, суставчатой и сливной. По мере увеличения твердости и прочности обрабатываемого материала сливная стружка переходит в суставчатую, а затем в элементную. При обработке хрупких материалов образуется или элементная стружка (чаще), или стружка надлома (реже).
С повышением твердости материала, например чугуна, элементная стружка переходит в стружку надлома.
Из геометрических параметров инструмента наиболее сильно на тип стружки влияют передний угол и угол наклона главного лезвия. При обработке пластичных материалов влияние углов g и lпринципиально одинаково: по мере их увеличения элементная стружка переходит в суставчатую, а затем в сливную. При резании хрупких материалов при больших передних углах может образовываться стружка надлома, которая по мере уменьшения переднего угла переходит
в элементную. При увеличении угла наклона главного лезвия стружка постепенно превращается в элементную.
|
На тип стружки оказывают влияние подача (толщина срезаемого слоя) и скорость резания. Глубина резания (ширина срезаемого слоя) на тип стружки практически не влияет. Увеличение подачи (толщины срезаемого слоя) приводит при резании пластичных материалов
к последовательному переходу от сливной стружки к суставчатой
и элементной. При резании хрупких материалов с увеличением подачи элементная стружка переходит в стружку надлома.
Наиболее сложно на тип стружки влияет скорость резания.
При резании большинства углеродистых и легированных конструкционных сталей, если исключить зону скоростей резания, при которых образуется нарост (о чем речь пойдет ниже), по мере увеличения скорости резания стружка из элементной становится суставчатой, а затем сливной. Однако при обработке некоторых жаропрочных сталей
и сплавов, а также титановых сплавов повышение скорости резания, наоборот, превращает сливную стружку в элементную. Физическая причина этого явления до настоящего времени полностью не выяснена. Повышение скорости резания при обработке хрупких материалов сопровождается переходом стружки надлома в элементную стружку с уменьшением размеров отдельных элементов и упрочнением связи между ними.
При применяемых в производстве геометрических параметрах инструментов и режимах резания основными типами стружки при резании пластичных материалов являются сливная (чаще) и суставчатая (реже). Основным типом стружки при резании хрупких материалов является элементная. В настоящее время наиболее подробно изучен процесс сливного стружкообразования. Образование элементной стружки при резании как пластичных, так и хрупких материалов изучено недостаточно.
2.2.2. Деформированное состояние
зоны стружкообразования
при элементной и сливной стружке
|
Образование элементной стружки изучено значительно хуже, чем образование сливной. Кинограммы процесса резания и наблюдения за искажением ячеек делительной сетки n показывают, что прежде чем произойдет разрушение по плоскости скалывания тп (рис. 36)
в объеме будущего элемента стружки, имеют место значительные деформации сжатия, вызывающие течение материала срезаемого слоя
![]() | ![]() |
Рис. 36. Искажение делительной сетки в элементе стружки | Рис. 37. Схема превращения срезаемого слоя в элемент стружки |
по передней поверхности перпендикулярно и параллельно лезвию инструмента.
С учетом этого превращение срезаемого слоя в элемент стружки происходит следующим образом (рис. 37). При перемещении инструмента на расстояние D L передняя поверхность воздействует на некоторый объем срезаемого слоя, ограниченный параллелограмом m 0 mnn 0.
Когда напряжения сжатия превзойдут предел текучести материала обрабатываемой детали, начнется его течение по передней поверхности и точка m 0 окажется не в точке k, куда она попадает при образовании сливной стружки, а в точке q. Одновременно происходит укорочение стороны параллелограмма m 0 n 0 до размера qp. В результате этого параллелограмм m 0 mnn 0 срезаемого слоя превращается в элемент стружки mnpq. Когда запас пластичности материала обрабатываемой детали будет исчерпан, происходит разрушение по плоскости скалывания, и сколотый элемент перемещается вверх по передней поверхности. Чем больше степень деформации срезаемого слоя, тем больше отличаются по длине стороны трапеции mn и qp
и тем больше форма элементной стружки приближается к треугольной. Сжимающие деформации вызывают значительное уширение основания элемента стружки, намного большее, чем уширение сливной стружки.
Исследования, проведенные
с помощью метода делительной сетки (рис. 38), а также измерение микротвердости корней стружки (рис. 39) показали, что между срезаемым слоем и образовавшейся стружкой существует более или менее отчетливо выраженная переходная зона.
Схема, поясняющая процесс образования сливной стружки, представлена на рис. 40. Режущий клин инструмента через площадку контакта шириной с действует на срезаемый слой толщиной а.
Рис. 39. Переходная зона, выявленная по изменению микротвердости | Рис. 40. Зоны первичной и вторичной деформации при превращении срезае- мого слоя в сливную стружку |
Сосредоточенная сила Р,с которой передняя поверхность инструмента давит на срезаемый слой, получила название силы стружкообразования. Линией ОK обозначена нейтральная линия, разграничивающая области сжимающих и растягивающих напряжений в обрабатываемом материале ниже поверхности резания. Левее нейтральной линии расположена область сжимающих напряжений,
а правее – растягивающих.
|
Перед передней поверхностью инструмента расположена зона I первичной деформации. Зона ОАВСО первичной деформации имеет форму клина с вершиной на лезвии инструмента. Ее нижняя граница ОFА вогнута и пересекает продолжение поверхности резания. Верхняя граница ОВ зоны выпукла и ее длина в 2...4 раза меньше длины линии ОА. Линия АВ плавно сопрягает предыдущую поверхность
резания со свободной стороной стружки. Левее линии ОА находятся еще недеформированные зерна материала срезаемого слоя, а правее линии OB – зерна материала, принадлежащие стружке. Зерно срезаемого слоя, перемещающееся относительно инструмента со скоростью резания V, начинает деформироваться в точке F и, проходя по траектории своего движения, получает все большую степень деформации. Деформация зерна заканчивается в точке Q, где зерно приобретает скорость V c, равную скорости стружки.
Многочисленные эксперименты показывают, что ширина стружки по сравнению с шириной срезаемого слоя даже при свободном резании увеличивается незначительно; при несвободном резании уширение стружки еще меньше. Поэтому можно считать, что деформированное состояние в зоне стружкообразования является плоским и срезаемый слой в процессе резания претерпевает деформацию сдвига. На основании этого линия ОА физически представляет собой поверхность сдвига (скольжения), на которой сдвигающие напряжения t равны пределу текучести s s материала на сдвиг: t = s s. Вся зона I состоит из подобных поверхностей, на каждой из которых сдвигающие напряжения равны пределу текучести материала, уже получившего определенную степень упрочнения в результате предшествующей деформации. Линия ОВ представляет собой поверхность, на которой осуществляется последняя сдвиговая деформация; на ней сдвигающие напряжения t равны пределу текучести s s на сдвиг окончательного упрочненного в результате превращения срезаемого слоя в стружку материала.
Если бы между передней поверхностью инструмента и контактной поверхностью стружки отсутствовало трение, то на этом деформирование зерен срезаемого слоя закончилось бы. Но поскольку
между указанными поверхностями всегда имеется трение, то зерна материала, находящиеся в непосредственной близости к контактной поверхности стружки, продолжают деформироваться и после выхода их из зоны первичной деформации.
Так возникает зона II вторичной деформации, ограниченная передней поверхностью и линией CD. Ширина OD зоны вторичной деформации приблизительно равна половине ширины площадки контакта с /2, а максимальная высота D1 в среднем составляет 0,1 толщины а с стружки. Как показал Н.Н. Зорев, зерна срезаемого слоя, проходя через зону вторичной деформации, деформируются исключительно сильно: степень деформации в зоне II может в 20 раз и более превышать среднюю деформацию стружки. Наличие зоны вторичной деформации приводит к неоднородности конечной деформации стружки по ее толщине. На большей части толщины стружки степень деформации зерен одинакова, а в слое толщиной D1 наблюдается резкое увеличение степени деформации. Размеры зоны вторичной деформации и степень деформации зерен материала в этой зоне определяются интенсивностью трения на передней поверхности. Чем меньше сила трения на передней поверхности, тем меньше размеры зоны вторичной деформации и интенсивность деформации. При уменьшении толщины срезаемого слоя, увеличении переднего угла и применении хорошо смазывающих жидкостей размеры зоны II уменьшаются и она становится исчезающе малой. В этом случае степень деформации зерен стружки по ее толщине практически одинакова.
Сложность физических процессов, происходящих в зонах первичной и вторичной деформации, не позволяет дать простых математических методов их количественного описания. Поэтому при инженерных расчетах реальный процесс стружкообразования заменяют его упрощенной моделью. Правомерность использования упрощенной модели связана со следующими обстоятельствами. Зона первичной деформации по своей толщине соизмерима с толщиной срезаемого слоя только при малых передних углах инструмента, больших толщинах срезаемого слоя и низких скоростях резания. При передних углах инструмента, толщинах срезаемого слоя и скоростях резания, применяемых в производственных условиях, протяженность FQ зоны первичной деформации резко уменьшается, ее границы ОА
и ОВ сдвигаются, приближаясь к некоторой линии ОЕ, наклонной
к поверхности резания под углом b. Это позволяет считать, что сдвиговые деформации локализуются в очень тонком слое толщиной D х,
а семейство поверхностей скольжения можно заменить единственной плоскостью ОЕ, называемой условной плоскостью сдвига. При такой идеализации процесс превращения срезаемого слоя в стружку можно представлять как процесс последовательных сдвигов тонких слоев обрабатываемого материала вдоль условной плоскости сдвига. Поскольку деформированное состояние практически является плоским, то, следовательно, процесс стружкообразования должен подчиняться закономерностям простого сдвига. Экспериментальная проверка хорошо подтверждает это положение. Средняя конечная интенсивность деформации, рассчитанная по измерению размеров искаженной в результате резания ячеек квадратной делительной сетки, мало отличается от интенсивности деформации простого сдвига, определенной на основании размеров стружки (табл. 1).
Таблица 1
Сравнение измеренной и расчетной интенсивности деформации
при резании латуни Л70; а = 3 мм и V = 5 м/мин
Передний угол g, град. | Интенсивность деформации | Интенсивность деформации простого сдвига | Прцент отклонения |
1,390 0,940 0,737 | 1,460 0,985 0,750 | 5 11 7 |
К такому же выводу приходит и Г.Л. Куфарев, определив при резании меди величину угла b вида деформированного состояния по размерам эллипсов стружки, в которые превратились окружности, нанесенные на срезаемый слой. При резании со скоростью V =
= 19 мм/мин были получены углы b (табл. 2).
Таблица 2
Влияние переднего угла g на изменение угла сдвига b
Угол | Значение угла | ||
g | 17° | 27° | 37° |
b | 36°32¢ | 31°24¢ | 37°37¢ |
Наблюдаемое незначительное уширение стружки, т.е. наличие
деформации в направлении второй главной оси, свидетельствует
о том, что помимо деформации простого сдвига при резании имеет место деформация сжатия. Однако приведенные экспериментальные данные показывают, что доля деформации сжатия по сравнению
с деформацией простого сдвига невелика. Поэтому при инженерных расчетах, особенно при несвободном резании, можно пользоваться упрощенной моделью с единственной плоскостью сдвига, принимая деформированное состояние простого сдвига.
Рассмотрим механику образования сливной стружки при единственной условной плоскости сдвига.
На рис. 41 представлена схема превращения срезаемого слоя
в стружку при единственной условной плоскости сдвига. В срезаемом слое толщиной а выделим параллелограмм mnpq с малой высотой D х, прилегающий к условной плоскости сдвига тп. Угол b, под которым условная плоскость сдвига наклонена к поверхности резания, называют углом сдвига. Пусть режущий инструмент переместится из положения I в положение II, пройдя вдоль боковой стороны параллелограмма mnpq расстояние D L. В результате этого перемещения точка q срезаемого слоя, лежащая на поверхности резания, ока жется в точке q 1, лежащей на передней поверхности, а точка р,лежащая на предыдущей поверхности резания, окажется в точке p 1, лежащей на
свободной стороне стружки. Таким образом, параллелограмм mnpq, сдвигаясь вдоль основания тп на величину D s, превращается в параллелограмм mnp 1 q 1.Очевидно, что параллелограмм тпр 1 q 1 принадлежит уже не срезаемому слою, а стружке, образовавшейся в результате перемещения инструмента на расстояние D L. При каждом последующем перемещении инструмента на то же расстояние процесс повторяется. Таким образом, превращение срезаемого слоя в сливную стружку происходит в результате последовательных и непрерывных сдвигов весьма тонких слоев материала по условной плоскости сдвига без нарушения связи между сдвинутыми слоями, т.е. без нарушения сплошности материала стружки. Если схему деформирования параллелограмма mnpq сравнить со схемой деформирования при простом сдвиге, изображенной на рис. 41, то видно, что они совпадают, и расстояние D s есть не что иное, как абсолютный сдвиг.
Что же вызывает сдвиг слоя материала вдоль условной плоскости сдвига и когда этот сдвиг начнется? Передняя поверхность инструмента действует на срезаемый слой с нормальной силой N. По закону трения Амонтона нормальная сила создает силу трения F = m N (где m – коэффициент трения скольжения между стружкой и инструментом).
Складывая силы N и F, получим силу стружкообразования R, наклоненную к поверхности резания под углом действия w. Разложим силу стружкообразования на две: силу PN,перпендикулярную
к условной плоскости сдвига, и силу P t, действующую вдоль плоскости сдвига. Сила PN сжимает сдвигаемый слой толщиной D x, а сила P t сдвигает его. Таким образом, сдвиговый процесс при образовании
стружки вызывает сила P t, получившая название силы сдвига. Как указывалось выше, сдвиговая деформация начнется в том случае, когда напряжение сдвига станет равным пределу текучести на сдвиг. При прямоугольном резании сдвигающее напряжение на условной плоскости сдвига
,
где b – ширина срезаемого слоя.
Так как , то получим t =
sin b, но сила сдвига P t = = R cos(w + b). Подставляя последнее, получим
t =
cos(w + b) · sin b.
Процесс образования стружки начнется в том случае, когда
t ³ t s, где t s – предел текучести
обрабатываемого материала на сдвиг.
На рис. 42 изображена схема напряженного состояния малого объема материала, расположенного на условной плоскости сдвига, и эпюры изменения касательных и нормальных напряжений вдоль указанной плоскости.
Независимо от рода и свойств обрабатываемого материала, величины переднего угла инструмента, толщины срезаемого слоя
и скорости резания касательные напряжения вдоль условной плоскости сдвига имеют постоянную величину.
Нормальные напряжения распределяются по-иному. При больших передних углах инструмента и малых коэффициентах трения на передней поверхности (резание с хорошо смазывающими жидкостями) нормальные напряжения (см. рис. 42, а) уменьшаются по мере приближения к лезвию и в некоторой точке условной плоскости сдвига могут изменить свой знак на обратный. По мере уменьшения переднего угла инструмента и увеличения коэффициента трения указанный эпюр постепенно переходит к виду эпюра, изображенного на рис. 42, б, на котором нормальные напряжения, сохраняя постоянство знака, увеличиваются при приближении к лезвию. Таким образом,
в общем случае нормальные напряжения вдоль условной плоскости сдвига, в отличие от касательных напряжений, непостоянны. Особенностью процесса является отсутствие влияния нормальных напряжений на величину касательных напряжений.
Условная плоскость сдвига разделяет области недеформированного материала, принадлежащего срезаемому слою, и уже полностью отдеформированного материала стружки. В результате пластического деформирования в стружке образуется характерная текстура деформации в виде полос или строчек, расположенных под некоторым углом к условной плоскости сдвига, называемым углом текстуры. Линии текстуры представляют собой цепочки зерен деформированного материала стружки, получивших после прохождения через условную плоскость сдвига определенную форму и ориентацию.
Образование текстуры деформации можно представить себе следующим образом (рис. 43). Сфероидальное зерно материала срезаемого слоя впишем в куб со стороной, равной толщине сдвигаемого слоя. Тогда в сечении плоскостью, перпендикулярной к лезвию инструмента, будем иметь круг с радиусом, равным п. В результате деформации простого сдвига верхняя плоскость сдвигаемого слоя переместится относительно нижней на величину абсолютного сдвига D s. Квадрат mnpq, в который вписан круг, превратится в параллелограмм тпр 1 q 1, а сам круг превратится в эллипс, сопряженными диаметрами которого являются стороны параллелограмма. На основании рис. 43 угол текстуры y, представляющий собой угол наклона большей оси эллипса к условной плоскости сдвига, может быть определен с помощью выражения
сtg y = ,
где e – относительный сдвиг при превращении срезаемого слоя
в стружку.
![]() | ![]() |
Рис. 43. Схема превращения сфероидального зерна в эллипсовидное | Рис. 44. Схема линии текстуры деформации |
Цепочки эллипсов в направлении их больших осей (рис. 44)
и представляют собой линии текстуры деформации стружки. Как видно из формулы, угол текстуры y зависит от степени деформации срезаемого слоя. Чем больше степень деформации, определяемая относительным сдвигом e, тем меньше угол текстуры, и наоборот. Превращение сфероидального зерна в эллипсовидное, очевидно, является следствием первичной деформации срезаемого слоя при прохождении зерна через зону первичной деформации, или условную плоскость сдвига.
В большей части стружки линии текстуры идут параллельно друг другу, сохраняя неизменным угол текстуры. Однако в слое стружки, прилегающем к ее контактной стороне, линии текстуры теряют свою правильную ориентацию, изгибаясь в сторону, обратную движению стружки. Как указывалось выше, это явление связано
с тормозящим действием, оказываемым передней поверхностью инструмента. Чем больше сила трения F, действующая на передней поверхности, тем сильнее тормозится контактный слой стружки и тем больше искривление линий текстуры и толщина слоя D1, в котором это искривление наблюдается. В пределах слоя стружки толщиной D1 эллипсовидные зерна, деформированные на первой стадии, теряют свою правильную форму тем больше, чем ближе они расположены
к передней поверхности инструмента. Искривление линий текстуры в контактном слое является следствием вторичной контактной деформации срезаемого слоя при прохождении деформированных зерен через зону вторичной деформации.
Когда условия трения на передней поверхности особенно тяжелы, тормозящее действие, оказываемое инструментом, становится настолько сильным, что это приводит к плотному присоединению части стружки к передней поверхности и образованию так называемого заторможенного слоя. На участке контакта размером с 1 контактная поверхность стружки настолько плотно присоединилась
к передней поверхности инструмента, что основная часть стружки перемещается не по инструменту, а по заторможенному слою, прикрывающему переднюю поверхность. О плотности присоединения заторможенного слоя к передней поверхности и отсутствии взаимного перемещения между ними свидетельствуют отпечатки на заторможенном слое рисок, параллельных лезвию, образовавшихся на инструменте при его заточке. Только после выхода за пределы ширины с 1 заторможенного слоя стружка непосредственно трется о переднюю поверхность инструмента, что видно по продольным рискам на контактной поверхности стружки, параллельным ее боковым сторонам. Заторможенный слой образуется при резании пластичных
и вязких материалов при малых передних углах инструмента и отсутствии смазочно-охлаждающей жидкости (СОЖ) (рис. 45).
Мерой деформации простого сдвига является относительный сдвиг. Определим его при резании. На основании рис. 43 величина абсолютного сдвига D s = +
Выразим отрезки
и через толщину D x сдвигаемого слоя:
= D x ·ctg b;
= D x ·ctg d = D x ·ctg[90° – (b – g)].
Тогда
D s = D x [ctg b + tg(b – g)].
Так как e = D s /D x, то выражение для определения относительного сдвига принимает вид
e = ctg b + tg (b – g). (2)
Из формулы (2) следует, что при известном переднем угле инструмента для определения относительного сдвига необходимо знать величину угла сдвига. Угол сдвига можно определить по длине стружки. При перемещении инструмента на расстояние D L (рис. 46) длина образовавшейся стружки будет равна D L с. Из треугольника mnq имеем
и
.
Отношение получило название коэффициента усадки или укорочения стружки, а выражение
(3)
называют формулой Тиме. Используя формулу Тиме, выразим угол
сдвига через коэффициент усадки стружки:
Отсюда
(4)
Несмотря на значительную идеализацию процесса превращения срезаемого слоя в стружку при замене зоны первичной деформации единственной плоскостью сдвига, формула Тиме совершенно точно выражает связь между коэффициентом усадки стружки и углом сдвига, так как отражает условие сплошности материала сливной стружки. Поэтому формулы хорошо подтверждаются экспериментом. Таким образом, если по длинам срезаемого слоя и стружки определить коэффициент усадки стружки, то с помощью формул (2)
и (4) можно подсчитать угол сдвига и относительный сдвиг.
Используя формулу (2), можно найти непосредственную связь между относительным сдвигом и коэффициентом усадки стружки. Подставив формулу (4) в выражение (2), получим
Имея величину относительного сдвига можно определить интенсивность деформации е.
Процессу резания свойственна очень высокая степень деформации и, соответственно, большая величина сдвигающих напряжений на условной плоскости сдвига. Величина относительного сдвига при резании в 2,5…3 раза, а сдвигающих напряжений в 1,5 раза больше, чем при растяжении и сжатии. Характерным является то, что при такой высокой степени деформации срезаемого слоя напряжение сдвига не зависит от условий резания, а определяется только свойствами материала обрабатываемой детали. Например, по данным Н.Н. Зорева, при резании детали из стали 30Х в случае изменения переднего угла резца в пределах 0…40° и скорости резания 45…145 м/мин значения двигающих напряжений на условной плоскости сдвига колеблются в пределах всего ±7 %. Незначительное влияние степени деформации на сопротивление деформации по условной плоскости сдвига объясняется тем, что при резании материал обрабатываемой детали претерпевает столь высокую деформацию, что его запас пластичности исчерпывается, а упрочнение приближается к пределу.
2.2.3. Взаимосвязь явлений стружкообразования
в процессе резания
Различные факторы, действующие при резании, по-разному влияют на деформационные и контактные процессы в зоне резания. Одни факторы непосредственно влияют на процесс стружкообразования, другие – косвенно, через те факторы, которые влияют непосредственно. Косвенное влияние оказывают почти все факторы, причем это влияние в большинстве случаев вызывает цепочку взаимосвязанных явлений, обусловливающих, в конечном счете, действие фактора, влияющего непосредственно. Например, изменение величины переднего угла увеличивает или уменьшает средние контактные нормальные напряжения на передней поверхности, что приводит к изменению среднего коэффициента трения и угла трения. Последнее оказывает влияние на угол действия, изменение которого вызывает изменение угла сдвига и работы стружкообразования.
Действие какого-либо фактора через цепочку взаимосвязанных факторов может усиливаться или ослабляться в зависимости от того, существует ли двустороннее взаимное влияние факторов друг на друга и совпадают или не совпадают результаты активного и реактивного действия. Например, увеличение среднего коэффициента трения сопровождается увеличением ширины площадки контакта стружки с передней поверхностью, что приводит к снижению средних контактных нормальных напряжений. При наличии двух участков трения это вызовет еще большее увеличение среднего коэффициента трения.
Факторы, действующие при резании, можно разделить на внешние и внутренние. К внешним факторам относятся свойства обрабатываемого и инструментального материалов, геометрические параметры инструмента, параметры режима резания, свойства смазочно-охлаждающей жидкости. К внутренним факторам можно отнести угол действия, температуру на передней поверхности, средний коэффициент трения, ширину площадки контакта, действительный передний угол с учетом нароста и др.
Непосредственное влияние на процесс стружкообразования при прямоугольном резании оказывают только четыре фактора: угол действия, передний угол инструмента, скорость резания и свойства обрабатываемого материала. Все остальные факторы влияют косвенно. Рассмотрим влияние некоторых факторов, действующих наиболее сильно.
Влияние угла действия. Важнейшей характеристикой процесса стружкообразования является угол сдвига b, от величины которого зависят коэффициент усадки стружки, относительный сдвиг и работа стружкообразования. Все то, что увеличивает угол сдвига, уменьшает степень деформации срезаемого слоя и работу стружкообразования. Используя условие равновесия инструмента, К.А. Зворыкин теоретически получил уравнение для определения угла сдвига в зависимости от переднего угла и угла трения V на передней поверхности:
2b + V – g = С,
где С – постоянная величина, близкая для стали и чугуна к 80°.
Если учесть, что V – g = w, то уравнение принимает вид
2b + w = С,
где w – угол действия.
Таким образом, угол сдвига непосредственно зависит от угла действия, уменьшаясь при увеличении последнего.
При увеличении угла действия угол сдвига уменьшается, что приводит к увеличению степени деформации срезаемого слоя и работы стружкообразования. Ухудшение условий стружкообразования связано с изменением напряженного и деформированного состояния зоны стружкообразования. При увеличении угла w вектор силы стружкообразования поворачивается против часовой стрелки, что приводит к повороту в том же направлении осей главных напряжений и соответствующему уменьшению угла сдвига.
Влияние переднего угла. Непосре
|
|
Типы сооружений для обработки осадков: Септиками называются сооружения, в которых одновременно происходят осветление сточной жидкости...
Археология об основании Рима: Новые раскопки проясняют и такой острый дискуссионный вопрос, как дата самого возникновения Рима...
Индивидуальные и групповые автопоилки: для животных. Схемы и конструкции...
Механическое удерживание земляных масс: Механическое удерживание земляных масс на склоне обеспечивают контрфорсными сооружениями различных конструкций...
© cyberpedia.su 2017-2024 - Не является автором материалов. Исключительное право сохранено за автором текста.
Если вы не хотите, чтобы данный материал был у нас на сайте, перейдите по ссылке: Нарушение авторских прав. Мы поможем в написании вашей работы!