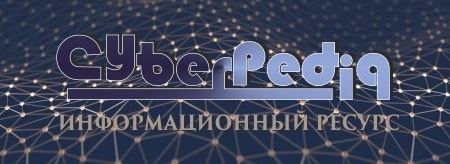
Состав сооружений: решетки и песколовки: Решетки – это первое устройство в схеме очистных сооружений. Они представляют...
Типы оградительных сооружений в морском порту: По расположению оградительных сооружений в плане различают волноломы, обе оконечности...
Топ:
Генеалогическое древо Султанов Османской империи: Османские правители, вначале, будучи еще бейлербеями Анатолии, женились на дочерях византийских императоров...
Отражение на счетах бухгалтерского учета процесса приобретения: Процесс заготовления представляет систему экономических событий, включающих приобретение организацией у поставщиков сырья...
Характеристика АТП и сварочно-жестяницкого участка: Транспорт в настоящее время является одной из важнейших отраслей народного...
Интересное:
Что нужно делать при лейкемии: Прежде всего, необходимо выяснить, не страдаете ли вы каким-либо душевным недугом...
Средства для ингаляционного наркоза: Наркоз наступает в результате вдыхания (ингаляции) средств, которое осуществляют или с помощью маски...
Отражение на счетах бухгалтерского учета процесса приобретения: Процесс заготовления представляет систему экономических событий, включающих приобретение организацией у поставщиков сырья...
Дисциплины:
![]() |
![]() |
5.00
из
|
Заказать работу |
|
|
V группа – сталь углеродистая и легированная конструкционная (качественная и высококачественная);
VI группа – сталь инструментальная, углеродистая, легированная и подшипниковая (качественная и высококачественная);
VII группа – сталь низкоуглеродистая электротехническая, динамная и трансформаторная (качественная и высококачественная, отливают только слябы);
VIII группа – сталь высоколегированная и сплавы для электродов.
Максимально допустимая продолжительность разливки металла из сталеразливочных ковшей различной вместимости для I, II, III, V, VI, VII групп марок сталей по нормам Гипромеза:
Вместимость, т 12 25 50 100 150-160 200 300
Время разливки, мин 40 50 60 75 85 90 110
Нормативные скорости разливки заготовок из сталей различных групп марок составляют:
Сечение заготовки, мм х мм 80´80 125´125 200´200
Скорость разливки стали, м/мин:
I, II, III 3,5 2,3 1,4
V, VI, VIII групп 2,75 1,8 1,10
Сечение заготовки, мм´мм 250´250 250´360 300´450
Скорость разливки стали, м/мин:
I, II, III групп 1,12 0,95 0,78
V, VI, VIII групп 0,88 0,75 0,61
В мартеновских цехах небольшой производительности устанавливаются горизонтальные МНЛЗ. Проектируется установка в ряде цехов криволинейных МНЛЗ с вертикальным кристаллизатором, наклонно-радиальные и роторные МНЛЗ.
Современные машины непрерывной разливки стали представляют собой системы, обеспечивающие получение из жидкой стали готовой литой заготовки, которая может, как правило, непосредственно направляться в прокатные станы, минуя блюминги или слябинги. При использовании МНЛЗ сталь из сталеразливочного ковша поступает в промежуточный ковш, а из него в кристаллизатор. В кристаллизаторе образуется оболочка (корочка затвердевшего металла), заполненная жидкой сталью по форме и сечению, соответствующему параметрам готовой заготовке. Частично затвердевшая заготовка с помощью транспортирующей системы – тянущей клети поступает в зону вторичного охлаждения, где происходит полное затвердевание заготовок. Затвердевший слиток – непрерывно-литая заготовка - подвергается порезке на мерные длины и готовые заготовки с помощью рольганга или других транспортных устройств транспортируются в прокатный цех или на склад.
|
При подготовке МНЛЗ к разливке в каждом кристаллизаторе с помощью специального устройства, так называемой затравки, устраивается сплошное дно. Верхний конец затравки, имеющий пазы, вводится в кристаллизатор, ее противоположный конец находится в зацеплении с тянущим устройством. По мере наполнения кристаллизатора металл затекает в пазы и, быстро затвердевая, образует прочное сцепление с затравкой. Затем включается тянущее устройство и частично затвердевший металл – твердая оболочка с жидкой сердцевиной вытягивается в зону вторичного охлаждения.
Для образования прочной оболочки – корки металла стенки кристаллизатора изготавливаются из материала, обладающего высокой тепло - и температуропроводностью, и интенсивно охлаждаются водой. Для уменьшения трения между затвердевшей корочкой (оболочкой) металла и стенками кристаллизатора, предотвращения смачивания стенок кристаллизатора жидкой сталью и создания нейтральной или восстановительной атмосферы, на поверхность металла в кристаллизаторе вводят твердую или жидкую смазку в виде различных масел, углеводородов или экзотермических, или теплоизолирующих шлаковых смесей. Наряду с этим для предотвращения разрыва оболочки и прилипания затвердевшей корочки металла к стенкам кристаллизатора последний совершает возвратно-поступательное движение (качание) с помощью специальных механизмов.
Из кристаллизатора, как указывалось выше, частично затвердевший слиток вытягивается в зону вторичного охлаждения, которая состоит из опорных элементов и устройств, обеспечивающих охлаждение непрерывной заготовки. Одновременно опорные элементы должны предотвращать деформацию оболочки слитка и искажение ее формы под действием ферростатического давления. Охлаждение заготовки осуществляется обычно орошением поверхности слитка водой, расход которой зависит от разливаемой марки стали и скорости вытягивания слитка.
|
После того как полностью затвердевший слиток в месте соединения с затравкой выходит из тянущего устройства, затравка отсоединяется от слитка и убирается специальным механизмом, а слиток поступает в устройство для резки. По окончании разливки остатки слитка выводятся из машины, убирается промежуточный ковш, поводятся контроль и настройка действия механизмов и системы охлаждения, затем вновь вводится затравка.
Таким образом, в целом современная МНЛЗ состоит из следующих элементов и узлов: сталеразливочного стенда; промежуточного ковша; тележки или стенда для промежуточного ковша; кристаллизатора; механизма возвратно-поступательного движения кристаллизатора; опорных элементов и устройств зоны вторичного охлаждения; устройства для транспортировки слитка; затравки; механизма для ввода и уборки затравки; устройств для резки непрерывно-литого слитка на заготовки мерной длины; устройства для уборки и транспортировки заготовок к прокатному цеху или в отделение отделки заготовок; устройства для подачи твердой или жидкой смазки; оборудования для подачи воды в кристаллизатор; зону вторичного охлаждения и на охлаждение элементов МНЛЗ; электрооборудования; средств контроля и автоматизации.
Начало промышленного применения непрерывного литья положили машины вертикального типа, у которых кристаллизатор, роликовая проводка, тянущее и режущее устройства расположены по вертикали на высоту 23…35 м, а в ряде случаев и до 43 м. Машины вертикального типа позволяют получать слитки высокого качества, однако их широкому использованию препятствуют присущие им крупные недостатки – большая высота и низкая скорость литья. С целью уменьшения высоты здания и возможности подачи сталеразливочных ковшей к рабочей площадке вертикальные МНЛЗ выполняют с расположением концевой части машины в железобетонном колодце. Помимо удорожания строительства, это приводит к необходимости применения сложных систем выдачи заготовок из колодца. Повышение скорости литья путем увеличения длины зоны затвердевания слитка на вертикальных машинах не может быть реализовано, так как с увеличением высоты возникает большое ферростатическое давление, приводящее к выпучиванию корки слитка и ее разрушению с прорывом наружу жидкой фазы.
|
Лекция № 9. Машины полунепрерывного литья. Литейно-прокатные комплексы. Состояние и перспективы развития. Особенности расчетов и расчеты кристаллизатора и др. частей. Кристаллизатор. Вторичное охлаждение. Тянущие устройства. Система охлаждения непрерывного слитка. Технико-экономические показатели.
Общая схема компоновки. Как было отмечено, МНЛЗ любого типа представляет собой комплекс самых разнообразных устройств, выполняющих строго определенные функции. Все эти устройства, тесно связанные работой друг с другом, должны располагаться в определенной технологической последовательности. При этом их компоновка должна обеспечивать ряд общих требований, главными из которых являются следующие:
1) стабильное положение технологической оси машины в процессе достаточно длительного периода непрерывной работы;
2) независимое функционирование всех этих устройств путем индивидуального подвода электроэнергии, воды, смазки и др.;
3) точную синхронизацию работы всех ее элементов;
4) максимально возможную скорость замены отдельных узлов или устройств целиком в случае аварийного выхода их из строя;
5) переналадку всей машины на отливку слитка другого сечения без замены ее составных элементов;
6) высокий уровень механизации и автоматизации обслуживания и управления;
7) требования охраны труда и защиты окружающей среды.
Обеспечение стабильности положения технологической оси МНЛЗ любого типа достигается определенной схемой компоновки ее основных узлов. Машина устанавливается на индивидуальном монолитном железобетонном фундаменте, располагаемом отдельно от любых строительных конструкций здания и его оборудования. Это позволяет не только сохранять в течение многих лет стабильность технологической оси, но и предотвращает получение любых дополнительных воздействий (обычно в виде вибраций) на ее положение в процессе эксплуатации от другого оборудования, действующего в цехе. На фундаменте с помощью анкерных соединений закрепляются опорные металлоконструкции, которые в зависимости от расстояний между ними, места расположения по линии машины и нагрузок и других факторов могут быть различными – от стоек различной конфигурации до литых или сварных фундаментных балок. Во избежание тепловых деформаций балки делаются определенной длины и закрепляются своими концами в шарнирных опорах, из которых одна является плавающей, а другая фиксированной. В результате перемещения балок происходит тангенциально положению технологической оси. Схема опор позволяет также компенсировать деформации рам, возникающие под действием общих усилий вытягивания, приложенных к слитку, реакция которых передается на все поддерживающие конструкции. На балках с помощью быстроразъемных соединений монтируются все технологические элементы и узлы машины, непосредственно связанные с формированием, охлаждением, поддержкой и вытягиванием непрерывного слитка.
|
Кристаллизаторы. В технологическом процессе непрерывного литья стали кристаллизатору отведена одна из самых основных функций - формирование слитка требуемого сечения, то есть в любой МНЛЗ кристаллизатор выполняет функции первичного холодильника, отводящего до 30 % теплоты расплава, и формообразователя, обеспечивающего заданную форму поперечного сечения непрерывной заготовки. По принципу работы - это теплообменник, основной задачей которого является создание необходимых условий для интенсивного отвода теплоты от жидкого металла. В результате по его периметру происходит непрерывное формирование внешней оболочки – корочки будущего слитка. Обязательным условием эффективной работы кристаллизатора является обеспечение на выходе из него оболочки с прочностью, превышающей ферростатическое давление находящегося в ней жидкого металла и усилий вытягивания.
В технологическом процессе непрерывного литья стали кристаллизатору отведена одна из самых основных функций - формирование слитка требуемого сечения.
В настоящее время наиболее полно удовлетворяют всем предъявляемым требованиям кристаллизаторы со стенками, выполненными из металлов с высокой теплопроводностью, то есть из меди и ее сплавов, но с покрытием рабочих поверхностей другими материалами, более износоустойчивыми и термостойкими и не оказывающими вредных воздействий на поверхность стального слитка. Нанесение этих материалов на рабочие поверхности стенок может осуществляться самыми различными способами: гальваническим, напылением, наплавкой, термодиффузионным насыщением поверхностного слоя, плакированием меди листовым материалом. Наибольшее распространение получил гальванический метод покрытия.
|
Хромирование позволяет значительно поднять твердость рабочих поверхностей стенок кристаллизаторов, что способствует повышению их износоустойчивости.
Никелевое покрытие дает хорошее сцепление с медью, но имеет значительно более низкую износостойкость. Обычно никель наносят более толстым слоем. В некоторых случаях покрытие выполняют переменным по высоте кристаллизатора – более тонким в районе мениска и толще в нижней части стенки.
К основным конструктивным параметрам кристаллизатора относятся внутренние размеры по сечению, определяющие профиль слитка, высоту, толщину и материал рабочих стен, их конусность, система охлаждения и система регулирования размеров.
Понятно, что кристаллизатор представляет собой сквозную водоохлаждаемую изложницу с медными полыми стенками. Для повышения жесткости и прочности такая изложница устанавливается в стальном литом или сварном корпусе. Однако, несмотря на общие принципы устройства и работы, существует очень большое количество самых разнообразных конструкций кристаллизаторов.
В настоящее время все конструкции кристаллизаторов по способу изготовления и области применения можно объединить в тир большие группы: блочные, гильзовые и сборные. Все они в зависимости от формы технологической оси МНЛЗ могут быть прямолинейными и радиальными.
Блочные кристаллизаторы изготавливаются из цельнокованных или литых медных блоков с толщиной стенок 150…175 мм. В стенках просверлены отверстия, по которым проходит вода для охлаждения. Число отверстий, их диаметр и расстояние между ними определяются условиями теплоотвода. Обычно диаметр отверстий составляет 20…22 мм с шагом 40…60 мм. Готовый медный блок крепится для повышения прочности в стальном корпусе (рис.9.1.). Кристаллизаторы такого типа характеризуются сравнительной долговечностью, отсутствие стыков между стенками обеспечивает достаточно высокую надежность их в работе. В то же время они дороги в изготовлении и в процессе эксплуатации.
Сборные кристаллизаторы изготовляются из четырех отдельных медных плит, каждая из которых для большей жесткости крепится шпильками на отдельной стальной плите. В зависимости от толщины плит кристаллизаторы делятся на тонко- (15…25 мм) и толстостенные (50…100 мм). Собранные все вместе и стянутые по боковым граням болтами они образуют изложницу с медной рабочей поверхностью, расположенную в стальном корпусе. Для снятия температурных напряжений в плитах, вызывающих их деформации, и для предотвращения образования зазоров между стенками плит стягивающие болты снабжены пружинными компенсаторами.
Такие кристаллизаторы широко применяются для отливки прямоугольных листовых заготовок – слябов и крупных блюмов, так как высокая жесткость стен позволяет выдерживать без деформации очень большое ферростатическое давление.
Характерной особенностью сборного кристаллизатора является возможность изменения ширины отливаемой заготовки. Это достигается перемещением узких стен, вставленных между широкими, с помощью различных механических или электромеханических приводов.
Как и во всех сборных кристаллизаторах каждая стенка состоит из медной плиты и прикрепленного к ней литого стального корпуса. Базовой является стенка, расположенная на стороне большего радиуса машины. Базовая стенка сборная и состоит из собственно широкой стенки 1 и прикрепленных к ней с двух сторон боковых стенок (боковин) 4, образующих в плане букву П. К боковинам подвешены узкие стенки 2 и прикреплена подвижная широкая стенка 6 малого радиуса. С помощью стяжек 3 узкие стены зажимаются между широкими стенами. Перестройка кристаллизатора по ширине производится электромеханическим механизмом 5, расположенным на внешних сторонах боковин. При этом обеспечивается как перемещение узких стен, так и изменение их конусности.
Для обеспечения свободного перемещения узких стен перед началом перестройки снимается усилие их зажима. С этой целью подвижно широкая стенка оттягивается с помощью гидроцилиндра, установленного на раме 8 механизма качания.
В стальных корпусах широких стен размещены коллекторы 7 для подвода и отвода воды, охлаждающей медные стенки.
Такая конструкция кристаллизатора позволяет, оперативно меняя конусность, снизить износ рабочих стенок и улучшить качество слитка. Кроме того, снижается парк кристаллизаторов и увеличивается производительность за счет снижения простоев машины.
Длина сборных кристаллизаторов колеблется в широких пределах от 650 до 1200 мм. За рубежом при скорости разливки до 1 м/мин получили наиболее широкое распространение короткие кристаллизаторы, длина которых 650…800 мм. При увеличении скоростей разливки до 1,2…1,8 м/мин короткие кристаллизаторы стали причиной повышенной аварийности из-за возросшего числа прорывов. Поэтому при скоростях > 1,2 м/мин рекомендуется применять кристаллизаторы длиной ³ 900 мм.
В практике металлургических предприятий СНГ наиболее стабильные режимы разливки получены на кристаллизаторах длиной 1200 мм. Кроме того, удлиненный кристаллизатор позволяет менять промежуточные ковши без снижения скоростей разливки при отливке металла методом «плавка на плавку».
При выходе заготовки из кристаллизатора ее оболочка без поддержки извне не в состоянии выдержать ферростатическое давление жидкой фазы. Поэтому на всей длине технологической линии МНЛЗ необходимы поддерживающие устройства по широким граням заготовки. Элементы поддерживающих устройств, соприкасающиеся с поверхностью заготовки, должны располагаться на определенном расстоянии друг от друга, исходя из допустимых величин выпучивания корочки оболочки от ферростатического давления.
Основной технологической функцией зоны вторичного охлаждения (ЗВО) является создание оптимальных условий ля полного затвердевания непрерывно отливаемого слитка, обеспечивающих требуемое качество металла.
Протяженность жидкой фазы в слитке на современных машинах непрерывной разливки в зависимости от сечения заготовки и скорости литья составляет 15 - 40 м. На всем этом участке одновременно с затвердеванием металла происходит воздействие на него, кроме ферростатического давления, многочисленных силовых факторов, приводящих к различным напряжениям в слитке. Основными из них являются: термические напряжения, зависящие от условий охлаждения; растягивающие напряжения, определяемые трением и усилиями вытягивания; напряжения, как отмечено выше, возникающие под действием ферростатического давления жидкого расплава, которые вызывают выпучивание корочки слитка. Значительное влияние оказывает сама форма технологической оси ЗВО, в соответствии с которой слиток подвергается воздействию различного рода усилий при его разгибе, загибе или правке.
Исходя из этого конструкция ЗВО должна отвечать следующим требованиям:
- обеспечивать тщательную поддержку слитка на выходе из кристаллизатора, где толщина оболочки минимальна, а ее механическая прочность весьма низка;
- исключать возможность выпучивания корочки слитка под действием ферростатического давления;
- уменьшать воздействие растягивающих напряжений в оболочке заготовки, возникающих под воздействием тянущих усилий;
- обеспечивать оптимальный теплоотвод и его регулирование в зависимости от скорости вытягивания и сортамента отливаемой стали;
- сохранять стабильность технологической оси и прочностные характеристики поддерживающих устройств в условиях высоких температур и нагрузок в процессе долговременной эксплуатации машины;
- обеспечивать быструю замену узлов зоны вторичного охлаждения при аварийных ситуациях, а также минимальные потери времени на переналадку, необходимую при изменении сечения отливаемой заготовки.
Основной технологической функцией зоны вторичного охлаждения (ЗВО) является создание оптимальных условий ля полного затвердевания непрерывно отливаемого слитка, обеспечивающих требуемое качество металла.
Протяженность ЗВО определяется скоростью вытягивания и размером сечения отливаемого слитка.
Протяженность собственно жидкой фазы непрерывного слитка L ж можно определить из выражения
Lж = t × w, (9.1)
где t - полное время затвердевания; w - скорость вытягивания слитка.
В связи с возможными колебаниями времени затвердевания слитка протяженность жидкой фазы увеличивается
Lж = t × w × r, (9.2)
где r - коэффициент, учитывающий возможное увеличение времени затвердевания [для сортовых заготовок r = 1,25; для прямоугольных заготовок с большим отношением сторон (слябов) r = 1,1 ].
Время затвердевания слитка с достаточной для практики точностью можно определить из выражения
τ = (а / 2k), (9.3)
где а - толщина заготовки; k - коэффициент затвердевания (для сортовой заготовки k = 28…30 мм /мин0,5, а для слябовой k = 24…26 мм/мин0,5).
Протяженность всей ЗВО может быть определена как
Lзво = Lж × r - H, (9.4)
где H - активная длина кристаллизатора.
Лекция №10. Агрегаты и установки для внепечной обработки металлов. Роль внепечной обработки металлов. Перемешивание металла и устройства для перемешивания. Обработка металла шлаками и устройства для обработки. Вакуумная обработка, вакуумирование струй и установки для вакуумирования.
Внепечное вакуумирование с начала своего применения являлось и является одним из наиболее эффективных способов улучшения качества сталей ответственного назначения. В тех случаях, когда проведение операций, обеспечивающих требуемое качество металла, непосредственно в самом агрегате связано с потерей его производительности и недостаточно эффективно, операции переносят в ковш или во вспомогательную емкость. Проведение технологических операций вне плавильного агрегата называют вторичной металлургией (ковшевой металлургией, внеагрегатной обработкой, внепечной обработкой, ковшевым рафинированием). Основную цель вторичной металлургии можно сформулировать как осуществление ряда технологических операций быстрее и эффективнее по сравнению с решением аналогичных задач в обычных сталеплавильных агрегатах.
В настоящее время методами внепечной металлургии обрабатывают сотни миллионов тонн стали массового назначения, установки для внепечной обработки имеются на всех заводах качественной металлургии. Обработке подвергают металл, выплавленный в мартеновских печах, дуговых электропечах и конвертерах.
Приоритетными способами внепечной обработки стали являются процессы порционного и циркуляционного вакуумирования, известных в металлургии как процессы DН и RН. Общим для них является вакуумирование в специальных камерах сравнительно небольших количеств металла вне ковша. Однако принцип заполнения металлом вакуумных камер и их устройство у обоих процессов различны.
Методы внепечной обработки могут быть условно разделены на простые (обработка металла одним способом) и комбинированные (обработка металла несколькими способами одновременно). К простым методам относятся:
1) обработка металла вакуумом;
2)продувка инертным газом;
3) обработка металла синтетическим шлаком в ковше;
4) введение реагентов в глубь металла;
5) продувка порошкообразными материалами.
Основными недостатками перечисленных простых способов обработки металла являются:
1) необходимость перегрева жидкого металла в плавильном агрегате для компенсации снижения температуры металла при обработке в ковше;
2)ограниченность воздействия на металл (только десульфурация или только дегазация и т.п.).
Наилучшие результаты воздействия на качество металла достигаются при использовании комбинированных способов, когда в одном или нескольких, последовательно расположенных агрегатах, осуществляется ряд операций. Для их осуществления оказывается необходимым усложнять конструкцию ковша и использовать более сложное оборудование.
При решении вопроса о выборе необходимого оборудования определяющим является выбор той или иной технологии обработки металла. Несмотря на многоплановость задач, стоящих при решении проблемы повышения качества металла методами вторичной металлургии, используемые при этом технологические приемы немногочисленны и по существу сводятся к интенсификации следующих процессов:
1. Взаимодействия металла с жидким шлаком или твердыми шлакообразующими материалами интенсивное перемешивание специальной мешалкой, продувкой газом, вдуванием твердых шлакообразующих материалов непосредственно в массу металла, электромагнитное перемешивание и т.п.).
2. Газовыделения (обработка металла вакуумом или продувка инертным газом).
3. Взаимодействия с вводимыми в ванну материалами для раскисления и легирования (подбор комплексных раскислителей оптимального состава; введение реагентов в глубь металла в виде порошков, блоков, специальной проволоки; с использованием патронов, выстреливаемых в глубь металла; искусственное перемешивание для улучшения условий удаления продуктов раскисления и т.д.; организация тем или иным способом перемешиивания ванны, интенсификация процессов массопереноса — обязательное условие эффективности процесса).
Внепечная обработка металла комбинированными методами может производиться: 1) в обычном сталеразливочном ковше с футеровкой из шамота и с вертикальным стопором; 2) в сталеразливочном ковше с футеровкой из основных высокоогнеупорных материалов и стопором шиберного типа; 3) в сталеразливочном ковше, снабженном крышкой; 4) в сталеразливочном ковше, оборудованном для вдувания газа или газо-порошковой струи снизу, через смонтированные в днище устройства; 5) в агрегате-ковше с крышкой (сводом), через которую опущены электроды, нагревающие металл в процессе его обработки; 6) в агрегате типа конвертера, с продувкой металла кислородом, аргоном, паром; 7) в агрегате типа конвертера, снабженном оборудованием для вакуумирования расплава и т.д.
В настоящее время в промышленно развитых странах успешно работают сотни установок внепечного вакуумирования различной конструкции. Самым простым способом является способ вакуумирования в ковше.
Схемы наиболее распространённых простейших конструкций вакууматоров представлены на ниже приведённой схеме. Самыми эффективными и распространенными являются устройства порционного и циркуляционного вакуумирования.
![]() |
Технологические основы внепечного рафинирования. Обработка металла вакуумом влияет, как известно, на протекание тех реакций и процессов, в которых принимает участие газовая фаза.
Газовая фаза образуется, в частности, при протекании реакции окисления углерода (образование СО) и процессов выделения растворенных в металле водорода и азота, а также процессов испарения примесей цветных металлов.
В стали практически всегда содержится определенное количество углерода. Равновесие реакции [С] + [О] = СОгаз. При обработке вакуумом сдвигается вправо, кислород реагирует с углеродом, образуя окись углерода.
В тех случаях, когда кислород в металле находится в составе оксидных неметаллических включений, снижение давления над расплавом приводит в результате взаимодействия с углеродом к частичному или полному разрушению этих включений:
Более слабые включения, такие например, как МnО или Сr2О3, восстанавливаются почти нацело; для восстановления более прочных включений, таких, например, как А12О3 или TiO2, требуется очень глубокий вакуум. Снижение концентрации кислорода в металле ("окисленности" металла) при обработке вакуумом за счет реакции окислениия углерода получило название "углеродное раскисление".
Обработка металла вакуумом влияет и на содержание в стали водорода и азота. Выше было сказано, что содержание водорода в металле определяется при прочих равных условиях давлением водорода в газовой фазе. При снижении давления над расплавом равновесие реакции Н2газ сдвигается вправо. Водород в жидкой стали отличается большой подвижностью, коэффициент диффузии его достаточно велик, и в результате вакуумирования значительная часть содержащегося в металле водорода быстро удаляется из металла.
Требуются более глубокий вакуум и продолжительная выдержка, чтобы достигнуть заметного очищения металла от азота.
Процесс очищения металла от водорода и азота под вакуумом ускоряется одновременно протекающим процессом выделения пузырьков окиси углерода. Эти пузырьки интенсивно перемешивают металл и сами являются маленькими "вакуумными камерами", так как в пузырьке, состоящем только из СО, парциальные давления водорода и азота равны нулю. Таким образом, при обработке металла вакуумом нем уменьшается содержание растворенных кислорода, водорода, азота и содержание оксидных неметаллических включений; в результате выделения большого количества газовых пузырьков металл перемешивается, становится однородным, происходит "гомогенизация" расплава.
Кроме того, в тех случаях, когда металл содержит в повышенных концентрациях примеси цветных металлов (свинца, сурьмы, олова, цинка и др.), заметная часть их при обработке вакуумом испаряется.
Необходимо иметь в виду, что при обработке вакуумом испаряется также и железо и полезные примеси (очень интенсивно, например, испаряется марганец). Однако эти потери становятся ощутимыми лишь при очень глубоком вакууме и очень длительной выдержке.
Продувка металла инертными газами в известной мере влияет так же, как обработка вакуумом. При продувке инертными газами массу металла пронизывают тысячи пузырьков инертного газа (обычно аргона). Каждый пузырек представляет собой маленькую "вакуумную камеру", так как парциальные давления водорода и азота в таком пузырьке равны нулю. При продувке инертным газом происходит интенсивное перемешивание металла, усреднение его состава; в тех случаях, когда на поверхности металла наведен хороший шлак, перемешивание облегчает протекание процесса ассимиляции таким шлаком неметаллических включений; если этот шлак имеет высокую основность (а также малую окисленность) происходит и десульфурация металла. Когда хотят получить сталь с особо низким содержанием углерода (например, особо качественную нержавеющую сталь), кислород, подаваемый для продувки ванны, разбавляют инертным газом, при этом равновесие реакции О2 + 2[С] = 2СОгаз сдвигается вправо, так как в газовой фазе в составе продуктов реакции, кроме оксидов углерода, будет находиться и инертный газ, и парциальное давление рсо уменьшится. Масса пузырьков инертного газа сама облегчает процессы газовыделения, так как эти пузырьки являются готовыми полостями с развитой поверхностью раздела для образования новой фазы.
Необходимо иметь в виду, что продувка инертным газом сопровождается снижением температуры металла (газ нагревается и интенсивно уносит тепло), поэтому ее часто используют для регулирования температуры металла в ковше.
Технически операция продувки больших масс металла инертными газами в ковше проще и дешевле, чем обработка вакуумом, поэтому там, где это возможно, продолжительная по времени продувка инертными газами, проводимая через пористые пробки в днище ковша или через полый стопор, заменяет обработку вакуумом. Во многих случаях продувку металла инертным газом проводят одновременно с обработкой вакуумом, так как вызываемое продувкой энергичное перемешивание металла ускоряет процессы вакуумирования, делает вакуумирование более эффективным. В качестве инертного газа чаще всего используют аргон. Когда это возможно, при производстве стали простых марок, невысоких температурах, аргон заменяют более дешевыми газами (азотом или даже паром).
Таким образом при продувке металла инертными газами достигают: 1)энергичного перемешивания расплава, облегчения протекания процессов удаления в шлак нежелательных примесей; 2) усреднения состава металла; 3) уменьшения содержания газов в металле; 4) облегчения условий протекания реакции окисления углерода; 5) снижения температуры металла.
Перемешивание металла со специально приготовленным ("синтетическим") шлаком позволяет интенсифицировать переход в шлак тех вредных примесей, которые удаляются в шлаковую фазу: серы, фосфора, кислорода (в виде оксидных неметаллических включений). В тех случаях, когда основная роль в удалении примеси принадлежит шлаковой фазе, скорость процесса пропорциональна величине площади межфазной поверхности. Обычно способ обработки стали синтетическим шлаком используют прежде всего для удаления серы, поэтому основой искусственно приготовляемого ("синтетического") шлака является СаО; для снижения температуры плавления в состав шлаковой смеси вводят А12О3 или другие добавки. Поскольку в таком шлаке практически нет оксидов железа, он является одновременно хорошим раскислителем. Если ставится задача очистки металла от неметаллических включений определенного состава, то соответственно подбирают состав синтетического шлака. Во всех случаях задача заключается, во-первых, в получении шлака нужного состава и, во-вторых, в разработке способа получения максимальной поверхности контакта шлаковой и металлической фаз.
Продувка металла порошкообразными материалами (или вдувание в металл порошкообразных материалов) также имеет целью обеспечить максимальный контакт вдуваемых твердых реагентов с металлом. Вместе с тем положительная сторона метода состоит в том, что реагент в металл вдувается струей газа-носителя, который сам оказывает определенное воздействие на металл. Газом-носителем может быть и окислитель (например, кислород или воздух), и восстановитель (например, природный газ), и нейтральный газ (например, аргон). Для удаления фосфора в струе кислорода в металл вдувают твердую смесь, состоящую из извести, железной руды и плавикового шпата, для удаления серы в металл вдувают в струе аргона смесь извести и плавикового шпата. Плавиковый шпат вводится в состав смесей для повышения жидкотекучести шлака. Этим способом можно вдувать в металл (в струе нейтрального или восстановительного газа) такие сильнодействующие реагенты, которые из-за больших энергий взаимодействия и соответствующего пироэффекта обычными способами вводить в металл нельзя (кальций, магний) или из-за их вредного действия на здоровье опасно (свинец, селен, теллур).
Ускоренная или направленная кристаллизация металла имеет целью улучшить структуру слитка, ликвидировать или уменьшить ликвацию, центральную рыхлость и пористость и тому подобные пороки. Скорость кристаллизации слитка пропорциональна разности температур у фронта кристаллизации и на поверхности слитка. Чем больше масса слитка, тем медленнее он кристаллизуется и тем сильнее в обычных условиях развиваются ликвационные и другие неприятные явления. Искусственное охлаждение слитков (применяемое, например, при непрерывной разливке стали) ускоряет процесс кристаллизации и положительно влияет на качество слитка. Регулируя время пребывания металла в жидком состоянии в изложнице или кристаллизаторе и интенсивность охлаждения металла, можно обеспечить получение такого слитка, у которого вообще не будет центральной менее плотной и более обогащенной ликватами зоны беспорядочно ориентированных кристаллов.
Обычно для интенсивного охлаждения поверхности слитка (непосредственно или через стенки кристаллизатора) пользуются водой.
Эти общие положения на практике реализуют в результате использования того или иного способа и агрегата из большого многообразия их.
Лекция № 11. Установки порционного и циркуляционного вакуумирования, Установка для нагрева металла в ковше с одновременным вакуумированием. Установка «печь-ковш». Другие установки и устройства. Особенности расчетов устройств и установок внепечной обработки металлов.
Существующие способы внепечного рафинирования по типу рафинирующих средств основаны на использовании одного или одновременно нескольких технологических приемов:
- обработки металла вакуумом;
- продувки металла инертными газами;
- вдувании порошкообразных материалов;
- перемешивании металла со специально приготовленными шла
|
|
История развития пистолетов-пулеметов: Предпосылкой для возникновения пистолетов-пулеметов послужила давняя тенденция тяготения винтовок...
Типы оградительных сооружений в морском порту: По расположению оградительных сооружений в плане различают волноломы, обе оконечности...
Семя – орган полового размножения и расселения растений: наружи у семян имеется плотный покров – кожура...
Особенности сооружения опор в сложных условиях: Сооружение ВЛ в районах с суровыми климатическими и тяжелыми геологическими условиями...
© cyberpedia.su 2017-2024 - Не является автором материалов. Исключительное право сохранено за автором текста.
Если вы не хотите, чтобы данный материал был у нас на сайте, перейдите по ссылке: Нарушение авторских прав. Мы поможем в написании вашей работы!