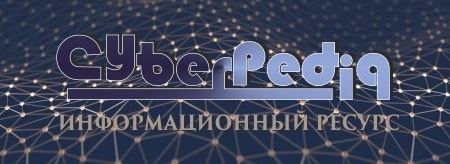
Своеобразие русской архитектуры: Основной материал – дерево – быстрота постройки, но недолговечность и необходимость деления...
Эмиссия газов от очистных сооружений канализации: В последние годы внимание мирового сообщества сосредоточено на экологических проблемах...
Топ:
Устройство и оснащение процедурного кабинета: Решающая роль в обеспечении правильного лечения пациентов отводится процедурной медсестре...
Особенности труда и отдыха в условиях низких температур: К работам при низких температурах на открытом воздухе и в не отапливаемых помещениях допускаются лица не моложе 18 лет, прошедшие...
Интересное:
Уполаживание и террасирование склонов: Если глубина оврага более 5 м необходимо устройство берм. Варианты использования оврагов для градостроительных целей...
Берегоукрепление оползневых склонов: На прибрежных склонах основной причиной развития оползневых процессов является подмыв водами рек естественных склонов...
Распространение рака на другие отдаленные от желудка органы: Характерных симптомов рака желудка не существует. Выраженные симптомы появляются, когда опухоль...
Дисциплины:
![]() |
![]() |
5.00
из
|
Заказать работу |
|
|
Дизель 5-26ДГ
Описание, эксплуатация и ремонт.
Технические данные.
Условное обозначение дизель-генератора -- 5-26ДГ с фильтром грубой очистки масла и с полнопоточным фильтром.
-- 5-26ДГ-01 с самоочищающимся фильтром и терморегулятором масла (при модернизации М62 терморегулятор не ставится.)
Полная мощность ДГУ -- 1360 квт
При параметрах среды
Температура -- 20о С
Атмосферное давление -- 760 мм. Рт. Столба
Влажность -- 70%
Противодавление на выхлопе -- 200 мм вод. Ст.
Разряжение на всасывании -- 300 мм вод. Ст.
Температура воды на охладитель -- 45оС
Температура топлива перед ТНВД -- 30оС
Мощность на минимальных оборотах -- 210 квт
Обороты 15 позиции -- 750 ± 10
Обороты 0 позиции -- 350 ± 15
Температура наружного воздуха -- от - 50 до + 45
Высота над уровнем моря -- 2000 м
Расход топлива на номинальной мощности -- 218,9 + 10,9
Расход топлива на минимальных оборотах -- 11 кг.
Расход масла в % от расхода топлива -- 1,5%
Вес с генератором ГП-312 -- 24000 кг
Вес с генератором ГП-320 -- 23300 кг
Обозначение дизеля -- 12ЧН26/26
Нумерация цилиндров
6Л | А2 5Л | А3 4Л | А4 3Л | А5 2Л | А6 1 Л | ||
![]() | В2 5ПР | В3 4ПР | В4 3ПР | В5 2ПР | В6 1ПР |
Порядок работы цилиндров
1-12-2-11-4-9-6-7-5-8-3-10
Вращение по часовой со стороны генератора.
Параметры работы дизеля
Температура выпускных газов -- 540оС
Температура на входе в ТК -- 560оС
Разность температур по цилиндрам -- 80оС
Максимальное давление сгорания Pz -- 130±10 кг/см2
Давление воздуха в рессивере -- 1,4-1,75 кг/см2
Вода из дизеля -- 75-85 о С
Мах -- 90-95 о С
Масло на входе в дизель -- 60-70 о С
Мах -- 73-75 о С
Мин. При запуске -- 8 о С
|
Защиты дизеля
Остановка.
Давление масла на входе -- 0,5 ± 0,05 кг/см2
Давление в картере -- > 60-70 мм. Вод. Ст.
Обороты дизеля -- > 840-880 об/мин
Снятие нагрузки
Температура масла -- 73-75 о С
Температура вода -- 90-95 о С
Давление масла на 12 позиции -- < 2 ± 0,15 кг/см2
Блокировка пуска
Включен валоповоротный механизм
При прокачке маслом нет давления -- 0,25 кг/см2
Масса основных узлов дизеля
Наименование сборочной единицы | Масса, кг | ||
Блок цилиндров | |||
Подвеска | 38,4 | ||
Вал коленчатый | |||
Крышка цилиндра | 117,4 | ||
Поршень |
| ||
Лоток с распределительным механизмом | |||
Вал распределительный | |||
Привод насосов | |||
Привод распределительного вала | |||
Коллектор и газовый трубопровод | |||
Турбокомпрессор с воздушной захлопкой | |||
Комплект цилиндра (втулка, крышка, поршень, шатун) | |||
Муфта | |||
Генератор |
Состав изделия
Дизель-генератор 5-26ДГ состоит из дизеля 12Д49 и о генератора
постоянного тока ГП-312 или ГП-320, установленных на общей раме и соединенных между собой муфтой пластинчатого типа.
Дизель представляет собой четырехтактный, двенадцатицилиндровый двигатель внутреннего сгорания с V-образным расположением цилиндров, газотурбинным наддувом и охлаждением наддувочного воздуха.
Торец дизеля со стороны турбокомпрессора, водяных и масляных насосов именуется передним, а торец со стороны генератора - задним. Если смотреть на дизель со стороны заднего торца, то ряд цилиндров, расположенных справа принято называть рядом В, а слева - рядом А. Нумерация цилиндров каждого ряда начинается от заднего торца.
Обозначение цилиндров состоит из обозначения ряда и номера по порядку: (А1, А2) (первый левый, второй левый) и т. д.
Рама под дизель и генератор - сварная. В раме имеется емкость, в которую заливают масло. Блок цилиндров сварно-литой конструкции с плоским разъемом подвесок коленчатого вала. Коленчатый вал - стальной с двенадцатью противовесами. Рабочие поверхности коренных и шатунных шеек упрочнены.
|
Для уменьшения напряжений, возникающих вследствие крутильных колебаний в системе "коленчатый вал дизеля - ротор генератора", на переднем конце коленчатого вала.установлен демпфер вязкостного трения.
Шатунный механизм состоит из главного и прицепного шатунов. Прицепной шатун крепится болтами к пальцу, установленному в проушинах главного шатуна.
Поршень составной. Головка к тропку крепится шпильками. В отверстия бобышек тронка вставлен палец плавающего типа. Осевое перемещение пальца ограничивается стопорными кольцами.
Поршни охлаждаются маслом, поступающим через шатуны из масляной системы дизеля.
В каждой крышке расположены по два впускных и по два выпускных клапана, форсунка и индикаторный кран. На крышке установлены рычаги привода клапанов. Крышка нижней плоскостью опирается на блок и крепится к нему шпильками, ввернутыми в плиту блока цилиндров. Втулка цилиндра подвесного типа крепится к крышке цилиндра шпильками. Стык между крышкой и втулкой (газовый стык) уплотнен стальной омедненной прокладкой. На втулку напрессована стальная рубашка, которая образует полость для прохода охлаждающей жидкости
Лоток с распределительным валом установлен на верхней части блока. На лотке установлены топливные насосы.
Распределительный вал приводится во вращение от коленчатого вала шестеренчатой передачей, расположенной на заднем торце блока цилиндров, которая одновременно является приводом регулятора, предельного выключателя, возбудителя, генератора и распределительного редуктора привода электрических машин вентиляторов обдува главного генератора и тяговых двигателей передней тележки тепловоза.
Топливная система состоит из топливоподкачивающего агрегата, топливоподогревателя, фильтров грубой (устанавливаются на тепловозе) и тонкой очистки, двенадцати индивидуальных топливных насосов, двенадцати форсунок и перепускного клапана, обеспечивающего необходимое давление топлива. Топливо от топливных насосов поступает к форсункам по топливопроводам высокого давления, а слив топлива производится по топливопроводу низкого давления.
Предельный выключатель, в случае повышения частоты вращения коленчатого вала выше допустимой, посредством рычажной передачи выключает подачу топлива в цилиндры дизеля и одновременно подает импульс давления масла к механизму воздушной захлопки, перекрывающей поступление воздуха из воздушной улитки турбокомпрессора в охладитель наддувочного воздуха и ресивер. В случае необходимости, остановку дизеля можно произвести с помощью аварийных кнопок предельного выключателя или воздушной захлопки.
|
Все агрегаты и трубопроводы масляной системы, кроме фильтра масла и маслопрокачивающего насоса (устанавливаются на тепловозе) расположены на дизеле.
Дизель оборудован одним масляными насосом шестеренного типа с подшипниками скольжения, водомасляный теплообменник установлен на тепловозе.
Система охлаждения дизеля двухконтурная, принудительная, замкнутого типа. Циркуляция охлаждающей жидкости в системе обеспечивается двумя центробежными насосами.
Картер дизеля вентилируется путем отсоса газов турбокомпрессором. Величина разрежения в картере регулируется автоматически.
В целях предотвращения скопления масла в ресивере наддувочного воздуха, на дизеле предусмотрена система для удаления масла из ресивера в емкость, расположенную в раме со стороны ряда А. Для контроля за работой этой системы на раме имеется специальный штуцер. На переднем торце дизеля установлены привод насосов, водяные, масляный насосы, турбокомпрессор с воздушной захлопкой, охладитель наддувочного воздуха, датчики-реле давления масла, заслонка управляемая системы вентиляции картера.
Со стороны ряда А дизеля расположены центробежный фильтр. Со стороны ряда В дизеля расположены фильтр тонкой очистки топлива, предельный выключатель, маслоотделительный бачок с установленными на него заслонкой управляемой и жидкостным манометром системы вентиляции картера.
Рисунок 1
Поперечный разрез дизель-генератора
Рисунок 2
Продольный разрез дизель-генератора
УСТРОЙСТВО ДИЗЕЛЯ
|
Рама сварной конструкции предназначена для установки на ней дизеля, генератора, установочного оборудования и крепления дизель-генератора к раме тепловоза. К боковым и торцевым листам рамы приварен поддон, образующий емкость для масла. Сверху емкость закрыта сетками. В нижней части рамы установлен заборник масла с сетками, через который масло по трубе и каналам в приводе насосов поступает к насосу масла. Со стороны ряда В на раму установлен корпус для заливки масла в раму с сеткой и измеритель уровня масла. Со стороны ряда А в раме расположена полость, в которую сливается масло скопившееся в ресивере блока. Слив масла из полости производится через вентиль. На передней стенке рамы предусмотрен штуцер для отвода масла к маслопрокачивающему насосу и штуцер для слива масла в раму из гидромуфты и редуктора.
Блок цилиндров представляет собой сварно-литую конструкцию V-образной формы. Для размещения втулок цилиндров блок разделен на шесть секций.
В развале блока образован ресивер надувочного воздуха и канал для прохода масла к подшипникам коленчатого вала.
Для повышения работоспособности нижнего пояса блока и предохранения его от коррозии в отверстия блока запрессованы втулки из нержавеющей стали.
Для перетока охлаждающей жидкости из водяных коллекторов к втулкам цилиндров и предохранения блока от коррозии установлены втулки из нержавеющей стали.
Подвод охлаждающей жидкости к коллекторам блока производится через привод насосов по проставкам с уплотнительными кольцами.
В нижней части боковых продольных листов блока, против каждого цилиндра имеются отверстия для контроля герметичности полости охлаждения втулок цилиндров.
Проставок, по которому подводится воздух из ресивера к впускные клапанам крышки цилиндра, состоит из колец, обечайки и болтов. При завертывании болтов кольца и раздвигаются и уплотняют стык между проставком, ресивером и крышкой цилиндра резиновыми кольцами.
Каждая крышка цилиндра крепится к опорной плите блока шпильками.
К стойкам блока прикреплены болтами подвески, подвеска выносного подшипника крепится болтами. Гайки болтов опираются на шайбы.
В отверстия, образованные стойками блока и подвесками, установлены вкладыши коренных подшипников. На седьмой стойке и подвеске установлены полукольца упорного подшипника, препятствующие перемещению коленчатого вала в осевом направлении.
В переднем торцовом листе имеется отверстие, по которому масло подводится в центральный масляный канал, откуда по каналам в стойках блока поступает на смазку коренных подшипников. К восьмому коренному подшипнику масло поступает из полости коленчатого вала. Со стороны заднего торца канал закрывается заглушкой с уплотнительной прокладкой. В седьмой стойке устанавливается на резьбе выступающая в канал трубка шлицевая, предохраняющая от возможности попадания грубых грязевых частиц в седьмой и восьмой коренные подшипники.
|
По каналу масло поступает на смазку привода насосов.
Трубки и проставки с уплотнительными кольцами предназначены для слива масла из крышек цилиндров в раму. Масло, скопившееся в ресивере, сливается по отверстию в блоке и трубопроводу в полость рамы.
Доступ в картер дизеля обеспечивается через люки, закрытые крышками.
Со стороны ряда В блока, крышки имеют предохранительные клапаны, которые открываются в аварийных случаях при повышении давления в картере дизеля.
Коренной подшипник состоит из верхнего и нижнего стальных вкладышей, залитых свинцовистой бронзой, на которую нанесено гальваническое покрытие.
Верхний и нижний вкладыши невзаимозаменяемые. Верхний вкладыш на рабочей поверхности имеет канавку и отверстие, через которое масло поступает из канала в стойке блока цилиндров в подшипник. Нижний вкладыш в районе стыка имеет карманы, которые служат для поступления смазки к трущимся поверхностям и для непрерывной подачи масла к шатунным подшипникам и поршню.
Прилегание вкладышей к постели всей поверхностью обеспечивается постановкой их с гарантированной величиной выступания поверхности стыков. Величина выступания поверхности стыков определяется в специальном приспособлении на предприятии-изготовителе, указана в миллиметрах на боковой поверхности вкладышей. Положение верхнего и нижнего вкладышей фиксируется штифтом 3, запрессованным в подвеску.
Контрольные обмеры блока
Деталь и место обмера | Чертежный размер в мм | Допустимый размер При выпуске из ТР3 и ТР2 в мм | Браковочный размер при выпуске из ТР1 и внепланового ремонта в мм | ||||||||||||||||||
3. Пояса блока:
| 340 +0,057 320 +0,089 295 +0,052 |
|
| ||||||||||||||||||
2. Износ верхних плит блока под крышками цилиндров | - | 0,3 | 0,4 | ||||||||||||||||||
3. Вкладыш коренного подшипника · Толщина с освинцеванием · Величина выступания поверхности стыков вкладыша · Сумарная для двух вкладышей (одного подшипника) величина выступания поверхности стыков | 7,405 –0,028 0,18-0,22 0,36 – 0,44 | 7,32 0,13 0,26 | Менее 7,3 Менее 0,11 Менее 0,22 | ||||||||||||||||||
4. Размер по стыку в свободном состоянии | 236+2 | 235,5+2,5 | Более 238 Менее 235,4 | ||||||||||||||||||
5. Зазор на масло между подшипником и коренной шейкой коленчатого вала. | По обмеру 0,19 – 0,321 | По обмеру 0,19 – 0,38 | По обмеру Более 0,40 | ||||||||||||||||||
6. Зазор между подшипником и коренной шейкой коленчатого вала в районе стыка не менее | По щупу 0,06 | По щупу 0,06 | По щупу менее 0,06 | ||||||||||||||||||
7. Зазор в упорном подшипнике между полукольцом и буртом коленчатого вала | 0,20-0,50 | 0,20-0,65 | 0,80 | ||||||||||||||||||
8. Штифт в подвеске выступание | 2.5-3,5 |
Затяжка вертикальных болтов подвесок блока.
1. Гайка 1 болта по динамометру 45-50 кг/м или 450 мм 1 человек до упора.
4. Гайка 2 болта по динамометру 85-90 кг/м или 850 мм 1 человек до упора.
5. Гайка 1 болта по динамометру 85-90 кг/м или 850 мм 1 человек до упора.
6. 1 Верх. Горизонтальный болт по дин. 30-35 кг/м или 350 мм 1 человек до упора
7. 2 Верх. Горизонтальный болт по дин. 60-65 кг/м или 700 мм 1 человек до упора
8. 1. Ниж. Горизонтальный болт по дин. 30-35 кг/м или 350 мм 1 человек до упора
9. 2 Ниж. Горизонтальный болт по дин. 60-65 кг/м или 700 мм 1 человек до упора
10. 1 Верх. Горизонтальный болт по дин. 60-65 кг/м или 700 мм 1 человек до упора
11. 1 Ниж. Горизонтальный болт по дин. 30-35 кг/м или 700 мм 1 человек до упора
Это отправные точки затяжки. После отправных точек проверить прилегание гаек, шайб, и подвесок, прохождение 0,3 мм не допускается.
Основная затяжка
Вертикальные болты на 14 шлиц (чередуя)
1 выносной подшипник на 8 шлиц.
Горизонтальные болты на 7 шлиц чередуя.
Проверка укладки коленчатого вала, при присоединенном главном генераторе.
Допускается прохождение щупа не более 0,05 мм под 3 и 4 коренными шейками.
В остальных случаях прохождение 0,05 мм на глубину не более 10 мм.
Боковой зазор в коренном подшипнике не менее 0,06 мм.
Коренной подшипник состоит и верхнего и нижнего стальных вкладышей, залитых тонким слоем свинцовистой бронзы, на которую нанесен тонкий слой сплава олово-медь-свинец с подслоем никеля.
3. Коленчатый вал.
Коленчатый вал предназначен для преобразования (вместе с шатунами) поступательного движения поршней во вращательное движение коленчатого вала и передачи крутящего момента дизеля валу генератора. Для уменьшения внутренних моментов от сил инерции деталей движения на всех щеках коленчатого вала имеются противовесы, прикрепленные к валу шпильками, шайбами и гайками. Штифт-втулка предназначена для центровки противовеса на щеке.
У первой коренной шейки имеются упорные бурты Е, которые ограничивают осевое перемещение коленчатого вала.
На фланец КВ устанавливается демпфер вязкостного трения. Демпфер заполнен силиконовой жидкостью с вязкостью от 70000 до 180000 сст при 200С При отборе пробы жидкости заглушка зятягивается моментом 2,5 кгм и раскернивается. Заполнение пробника проичсходит за время от нескольких минут до 3 часов.
На фланец отбора мощности устанавливается ведущий диск муфты. После установки биение ведущего диска не более 0,1 мм. После сборки ведомого не более 0,15 мм. Втулка с противоположного конца вала через шлицевой вал передает вращение шестерням привода насосов. Она крепится к коленчатому валу болтами и стопорится штифтами.
Между нулевой и первой коренными шейками коленчатый вал имеет фланец, к которому болтами прикреплена шестерня, передающая вращение шестерням привода распределительного вала.
Масло из коренных подшипников по отверстиям в шейках коленчатого вала поступает на смазку шатунных подшипников.
Подвод масла для смазки выносного коренного подшипника осуществляется следующим образом: масло с наружной поверхности первой коренной шейки по отверстиям попадает во внутрь шейки и полости Ж, а затем по отверстиям в нулевой коренной шейке выходит на рабочую поверхность. Заглушка 16 служит для уплотнения полости Ж. Заглушка 16 крепится к валу при помощи болтов 17, уплотняется прокладкой 15. Болты I7 попарно обвязаны проволокой.
Масло на смазку шлицев шлицевой втулки подводится от седьмой коренной шейки по отверстиям в полости.
Деталь и место обмера | Чертежный | Допустимый при выпуске из ТР-3 и ТР-2 | Браковочный |
Диаметр шатунной шейки | 190 –0,029 | 190 –0,13 с серийными шатунными вкладышами 189,9 -0,13 с вкладышами 1-ой ремонтной градации 189,8 -0,13 с вкладышами 2-ой ремонтной градации 189,7 -0,13 с вкладышами 3-ой ремонтной градации 189,6 -0,13 с вкладышами 4-ой ремонтной градации | Менее 189,4 |
Диаметр коренной шейки | 220 -0,029 | 220 –0,13 с серийными вкладышами 219,9 - 0,13 с вкладышами 1 ремонтной градации 219,8 - 0,13 с вкладышами 2 ремонтной градации 219,7 - 0,13 с вкладышами 3 ремонтной градации 219,6 - 0,13 с вкладышами 4 ремонтной градации | Менее 219,4 |
Допуск овальности, конусообразности, седлообразности, бочкообразности шатунных и коренных шеек (полуразность диаметров) | 0,01 | 0,04 | Более 0,04 |
Шероховатость коренных и шатунных шеек | Rα< 0,16мкм | Rα< 1,25мкм Допускаются риски глубиной и шириной до 0,3 мм в количестве 10 шт (или сумарной шириной до 3 мм) | Rα>1,25мкм Или риски глубиной и шириной более 0,3 мм или в количестве более 10 шт (или сумарной шириной более 3 мм) |
Допуск радиального биения коренных шеек | 0,05 | 0,1 мм При относительном радиальном биении смежных шеек не более 0,05 | Более 0,1 |
При установке на фланец шестерни коленчатого вала призонные болты устанавливаются с сопряжением зазор 0,006/натяг 0,028, при необходимости допускается увеличение диаметра отверстия под призонные боллты до 22 мм. При перестановке вала из блока в блок переставлять вместе с упорными кольцами. Прилегание шестерни щуп 0,05 не должен проходить.
Коленчатый вал | ||
Щека шестого колена | Порядковый номер, | Вал 249 |
номер плавки, | пл. 45085 | |
обозначение чертежа, | 26ДГ 8СПЧ | |
дата изготовления, | 4-02-2002 | |
4 клейма: клеймо приемщика, | ||
клеймо проверяющего качество материала, | ||
клеймо ОТК | ||
клеймо мастера цеха |
Продолжение таблицы 6
Место маркировки | Содержание маркировки | Пример |
Противовесы | Обозначение чертежа, | 6Д49.8.15-1 |
масса, | 41, 250 | |
2 клейма: клеймо мастера цеха | ||
клеймо ОТК |
Втулка цилиндра
В тулка цилиндра крепится к крышке цилиндра шпильками. Стык между крышкой и втулкой цилиндра уплотнен стальной омедненной прокладкой. В блоке втулка фиксируется верхним опорным поясом и нижним опорным поясом.
На втулку цилиндра напрессована стальная рубашка. Между втулкой и рубашкой образована полость для прохода охлаждающей жидкости. Полость уплотнена резиновыми кольцами.
В отверстия верхнего торца втулки цилиндров запрессованы втулки. С внешней стороны втулки покрыты теплоизолирующим слоем. Бурты втулок уплотнены снизу прокладками, а сверху резиновыми прокладками.
Охлаждающая жидкость по отверстию в блоке цилиндров поступает в полость между втулкой и рубашкой и через втулки перетекает в крышку цилиндра.
В нижней части втулки имеются два отверстия для крепления приспособления, удерживающего поршень во втулке цилиндра при подъеме и опускании цилиндрового комплекта. Отверстие в нижнем бурте втулки предназначено для поставки монтажного болта, который удерживает рубашку, в случае сползания ее с втулки при транспортировании.
При ремонте втулки уступ в месте остановки верхнего кольца поршня более 0,1 мм или фаска шириной до 2 мм и глубиной до0,2 мм зачистить мелким наждачным или алмазным камнем поперек оси втулки. К дальнейшей эксплуатации не допускаются: втулки имеющие задиры на длину хода поршня, а также кавитационые разрушения на наружной поверхности глубиной более 6 мм. Рубашки, имеющие трещины и кавитационные разрушения глубиной более 2,5 мм.
Деталь и место обмера ВТУЛКА ЦИЛИНДРА | Чертежный размер в мм | Допустимый размер При выпуске из ТР3 и ТР2 в мм | Браковочный размер при выпуске из ТР1 и внепланового ремонта в мм | ||||||
Внутренний диаметр 1) в районе остановки верхнего компрессионного кольца 2) на остальной части |
| 260,40 260,40 | 260,50 260,50 | ||||||
Овальность верхнего опорного пояса втулки (полуразность диаметров) | 0,04 | 0,10 | 0,13 | ||||||
Диаметр нижнего опорного пояса втулки цилиндра |
| 294,70 | 294,60 | ||||||
Овальность нижнего опорного пояса втулки цилиндра (полуразность диаметров | 0,026 | 0,10 | 0,13 | ||||||
Втулка цилиндра в сборе с крыщкой цилиндра (полуразность диаметров) замеряется на расстоянии 360 мм от нижнего торца втулки. | 0,035 | 0,08 | 0,10 |
Втулка цилиндра | ||
Верхний торец втулки | Месяц и год изготовления | 4 02 |
порядковый номер детали | ||
Испытание водой с давлением 200 бар | ГИ 200 | |
Нижний торец втулки | Порядковый номер детали |
Крышка цилиндра
Крышка цилиндра литая из высокопрочного чугуна. В крышке установлены два впускных клапана и два выпускных клапана (посадочные фаски клапанов наплавлены специальным сплавом), направляющие втулки и с уплотнительными кольцами.
Каждый клапан удерживается в закрытом состоянии двумя пружинами. Пружины опираются на нижнюю тарелку и удерживаются верхней тарелкой, в которую установлены два сухаря.
Для предохранения верхнего торца клапана от расклепывания установлен колпачок.
Для удержания колпачка в верхней тарелке установлено стопорное кольцо. К крышке цилиндра крепится закрытие. Между закрытием и лотком установлен патрубок. Стык патрубка уплотняется кольцами.
В закрытии установлены оси с рычагами привода клапанов. Оси фиксируются втулками.
Стыки закрытия с крышкой цилиндра, закрытия с крышкой закрытия и патрубка с лотком дополнительно могут уплотняться герметизирующим составом - "жидкой прокладкой".
Впускные клапаны в закрытом состоянии прилегают посадочными фасками к фаскам днища крышки, выпускные клапаны к фаскам седел, которые удерживаются в днище крышки пружинными кольцами из жаростойкой стали.
Каждая пара одноименных клапанов открывается одним рычагом через толкатели.
Гидротолкатель состоит из втулки, упора, пружин, шарика, толкателя и колпачка. От выпадания толкатель удерживается кольцом, а колпачок - шплинтом.
Масло в гидротолкатель поступает из масляной системы дизеля через отверстие в штанге, отверстие в рычаге и отверстие во втулке в полость гидротолкателя, когда клапан закрыт. В момент нажатия гидротолкателя на клапан давление масла в полости мгновенно повышается, шарик препятствует выходу масла через отверстие и усилие рычага передается на клапан через масляную подушку.
Рычажно-клапанный механизм смазывается разбрызгиваемым маслом, поступающим из лотка через патрубок.
Оси рычагов смазываются маслом, поступающим по отверстиям в рычагах. Из крышки цилиндра по отверстию и трубе в блоке цилиндров масло стекает в раму дизеля.
В крышке имеется полость для прохода охлаждающей жидкости. Жидкость поступает из втулки цилиндра по переливным втулкам и отводится в выхлопные коллектора. Есть контрольное отверстие предназначеное для контроля плотности уплотнения крышки цилиндров со втулкой.
Перед установкой на дизель крышку опресовать давление до 13 кгсм в течении 5 минут при наличии трещин крышку заменить, просачивание по пробкам пробки высверлить и заменить.
Гидротолкатели проверить на стенде При усилии 10 кг гидротолкатель должен опускаться на 5 мм в течении 3-8 сек (проверка на керосине) Протекание керосина через шариковый клапан не допускается.
Гайки крепления корзины затягиваются 16-18 кгм. Начинать с крепления рычагов.
Деталь и место обмера КРЫШКА ЦИЛИНДРА | Чертежный размер в мм | Допустимый размер При выпуске из ТР3 и ТР2 в мм | Браковочный размер при выпуске из ТР1 и внепланового ремонта в мм |
Зазор между седлом и крышкой цилиндра | 0,24-0,325 | 0,10-0,50 | 0,55 |
Осевой ход седла | 0,16-0,33 | 0,16-0,60 | 0,70 |
Зазор между направляющей втулкой и стержнем клапана (замер на расстоянии 30мм от нижнего торца втулки:
| 0,132-0,194 0,174-0,236 | 0,1-0,45 0,15-0,55 | 0,65 0,75 |
Допуск биения элементов клапана относительно стержня:
| 0,03 0,05 | 0,15 0,10 | 0,20 0,15 |
Ход клапана впускного или выпускного | Не менее 24 | Не менее 24 | Не менее 24 |
Зазор между осью и втулкой рычага | 0,05-0,145 | 0,05-0,35 | Более 0,40 |
Зазор между торцем втулки гидротолкателя и рычагои | Прохождение щупа более 0,03 не допускается | ||
Толщина цилиндрической части тарелки клапана под фаской:
| 4,85-5,0 3,2-3,5 | Не менее 2,8 Не менее 2,5 | Менее 2,5 Менее 2,0 |
Утопание нового (не работавшего клапана) гнездо (седло)
| 0,0-0,3 0,015-0,26 | Не более 2,2 Не более 4,0 | Более 2,5 Более 4,0 |
Крышка цилиндра | ||
На поверхности крышки цилиндра со стороны выпускных клапанов | Номер чертежа, | 5 Д49 78 СПЧ 10 |
номер цилиндра, | 5 А | |
месяц и год изготовления, | 1 02 | |
номер крышки | ||
На торце тарелки клапана | Номер крышки | 1 02 114 |
цифры 1 и 3 на выпускных клапанах | 1 02 114-1 | |
цифры 2 и 4 на впускных клапанах | 1 02 114 – 2 | |
На рычаге впускного клапана | Номер крышки | 1 02 114 |
На рычаге выпускного клапана | Номер крышки и буквы «ВЫП» | 1 02 114 ВЫП |
На наружной конусной поверхности втулки гидротолкателя | Номер крышки и номер клапана | 1 02 114 – 1 |
На плоскостях разъема сухарей | Номер цилиндра, номер пары сухарей | |
На верхней конусной поверхности колпачка | Размер толщины опорной части в мм | |
На наружной поверхности закрытия крышки цилиндра | Номер крышки цилиндра | 1 02 114 |
Кран индикаторный
Индикаторный кран, устанавливаемый на каждой крышке цилиндра, служит для продувки цилиндра, а также присоединения приборов для замера давлений сгорания и сжатия в цилиндре.
Шпиндель и наконечник крана имеют конусы А и Б.
Конус А служит для закрытия канала в корпусе, когда индикаторный кран закрыт.
Конус Б служит для уплотнения полости шпинделя I и штуцера 2 во время замеров, когда кран открыт.
Механизм шатунный
Шатунный механизм предназначен для преобразования поступательного движения поршня во вращательное движение коленчатого вала. Шатунный механизм состоит из стержня главного и прицепного шатунов.
Шатуны соединены между собой пальцем, который установлен во втулке, запрессованной в проушины главного шатуна.
Прицепной шатун крепится к пальцу двумя болтами со шлицевыми головками.
В верхние головки обоих шатунов запрессованы стальные втулки и, покрытые свинцовистой бронзой. Для прокачки масла к поршневому пальцу в средней части каждой втулки имеется канал с отверстием.
Нижняя головка главного шатуна имеет съемную крышку, которая крепится к стержню четырьмя болтами.
Разъем нижней головки стержня и крышки имеет зубцы трапецеидальной формы, препятствующие поперечному смещению крышки.
В нижнюю головку главного шатуна установлены верхний и нижний тонкостенные стале-бронзовые вкладыши. На антифрикционный слой свинцовистой бронзы нанесено гальваническое покрытие. Наружная поверхность вкладыша бронзирована. Вкладыши устанавливаются с гарантированной величиной выступания поверхности стыков, положение их фиксируется штифтами и запрессованными в стержень и крышку.
Верхний и нижний вкладыши – невзаимозаменяемы. В нижнем вкладыше в отличие от верхнего имеются отверстия для перетока масла.
Шатунный подшипник смазывается и охлаждается маслом, поступающим из коренных подшипников через каналы коленчатого вала. По отверстиям в нижнем вкладыше и по канавке в крышке масло перетекает в канал нижней головки шатуна и по втулке 5, уплотненной резиновым кольцом, в канал стержня главного шатуна. Далее часть масла поступает через продольный канал в стержне главного шатуна к втулке.
Другая часть масла поступает к втулке прицепного шатуна и через отверстие в пальце и продольному каналу в стержне прицепного шатуна к верхней втулке щатуна.
Из верхних втулок шатунов через дросселирующие отверстия шатуна масло поступает на охлаждение поршней.
Установка гаек болтов сторона стержня Бурт удален от опоры. Сторона шапки бурт ближе к опоре. После затяжки прилегание щуп 0,03 не должен проходить.
Установка шапки шатуна: Перед сборкой смазать резьбы и опорные поверхности пастой ВНИИ НП – 232 Гост 14068-79. Прижать шатун к одной сторон, контролировать положение вкладышей шатунного подшипника относительно упорных штифтов и плотность их посадки, установку резинового кольца масляного канала.
Сторона А оба болта 15 кгм, сторона Б оба болта 30 кгм, сторона А оба болта на 30 кгм. Окончательная затяжка на 10 шлиц по 5 шлиц.
Отправная динамометрическим ключом 23 кгм.
После сборки проверить осевой разбег шатуна норма 0,40-0,96 брак более 1,3 мм.
Внимание! За сборкой особенный контроль (осевой разбег проверять небольшой отверткой, перемещение практически без усилий) После сборки при запуске контроль на нагрев не более чем через 2 мин. работы.
При сборке прицепного шатуна совместить отверстия для прохода масла в пальце прицепного шатуна с каналом в прицепном шатуне с учетом метки впуск на поршне. Дополнительно контролируется прохождением масла при прокачке.
Затяжка: правый болт 15 кгм, левый 30 кгм, правый 30 кгм предваритьельная обтяжка после оба болта отвернуть и затянуть по новой правый 10 кгм, левый 20 кгм, правый 20 кгм. Эта затяжка считается отправной потом по 2 шлица на 10 шлиц.
Деталь и место обмера МЕХАНИЗМ ШАТУННЫЙ | Чертежный размер в мм | Допустимый размер При выпуске из ТР3 и ТР2 в мм | Браковочный размер при выпуске из ТР1 и внепланового ремонта в мм | |||||||||
Втулка в проушинах главного шатуна, внутренний диаметр. |
|
|
| |||||||||
Шатунный подшипник,зазор на масло в плоскости перпендикулярной разъему, по обмерам | 0,14-0,26 | 0,14-0,35 | 0,36 | |||||||||
Втулка верхней головки шатуна зазор на масло | 0,072-0,148 | 0,07-0,38 | 0,40 | |||||||||
Втулка в проущинах главного шатуна зазор на масло | 0,06-0,12 | 0,06-0,35 | 0,40 | |||||||||
Прицепной палец диаметр | 70 -0,019 |
| 69,78 | |||||||||
Толщина вкладыша шатунного подшипника в среднем сечении с учетом толщины гальванического покрытия | 5,9-5,93 | Вкладыш заменить на новый при износе до бронзы | Вкладыш заменить на новый при износе до бронзы | |||||||||
Вкладыш размер по стыку в свободном состоянии | 202,7 +2 | 202,3-205,0 | 202,2 | |||||||||
Вкладыш величина выступания поверхности стыков в приспособлении | 0,12-0,16 | 0,08 | 0,07 | |||||||||
Суммарная величина выступания поверхностей стыков двух половинок вкладышей. | 0,24-0,32 | 0,20 | 0,18 | |||||||||
Допуск прямолинейности образующей затылка вкладышей | 0,02 | 0,04
![]() Общие условия выбора системы дренажа: Система дренажа выбирается в зависимости от характера защищаемого... ![]() Типы оградительных сооружений в морском порту: По расположению оградительных сооружений в плане различают волноломы, обе оконечности... ![]() Биохимия спиртового брожения: Основу технологии получения пива составляет спиртовое брожение, - при котором сахар превращается... ![]() Механическое удерживание земляных масс: Механическое удерживание земляных масс на склоне обеспечивают контрфорсными сооружениями различных конструкций... © cyberpedia.su 2017-2024 - Не является автором материалов. Исключительное право сохранено за автором текста. |