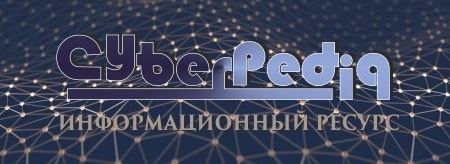
Кормораздатчик мобильный электрифицированный: схема и процесс работы устройства...
Организация стока поверхностных вод: Наибольшее количество влаги на земном шаре испаряется с поверхности морей и океанов (88‰)...
Топ:
Оснащения врачебно-сестринской бригады.
Оценка эффективности инструментов коммуникационной политики: Внешние коммуникации - обмен информацией между организацией и её внешней средой...
Комплексной системы оценки состояния охраны труда на производственном объекте (КСОТ-П): Цели и задачи Комплексной системы оценки состояния охраны труда и определению факторов рисков по охране труда...
Интересное:
Национальное богатство страны и его составляющие: для оценки элементов национального богатства используются...
Принципы управления денежными потоками: одним из методов контроля за состоянием денежной наличности является...
Лечение прогрессирующих форм рака: Одним из наиболее важных достижений экспериментальной химиотерапии опухолей, начатой в 60-х и реализованной в 70-х годах, является...
Дисциплины:
![]() |
![]() |
5.00
из
|
Заказать работу |
|
|
После сборки дробилки проверяют на параллельность впадин и вершин футировочных плит дробящих конусов. При движении подвижного конуса не должно быть задеваний о неподвижный конус и бронефутеровку. Эксцентриковый вал должен вращаться без усилия и постороннего шума, а также не должен иметь осевого люфта. Все составные части должны стоять на своем месте без перекосов, изгибов и хорошо протянуты. Ремни должны быть натянуты так, чтобы не было проскальзывания по рабочей поверхности шкивов. Кожуха должны быть исправны, и стоять на своих местах. При работе дробилки не должна издавать посторонних шумов (стук, скрип, гул и т.д.) Обеспечение правильного взаимного расположения сборочных единиц во многом определяет надежную и долговечную работу оборудования.
Включение по окончанию ремонта можно осуществлять только по указанию и в присутствии лица, ответственного за ремонт.
Перед включением оборудования это лицо обязано предупредить рабочих работающих на этом оборудовании и проследить, чтобы они находились в безопасном месте.
Приемку и пуск оборудования после ремонта осуществляется персонал цеха, в ведении которого находится оборудование. При приемке проверяется выполнение работ в соответствии с ведомостью дефектов.
Изм. |
Лист |
№ докум. |
Подпись |
Дата |
Лист |
КП.151031.03.ПЗ |
Изм. |
Лист |
№ докум. |
Подпись |
Дата |
Лист |
КП.151031.03.ПЗ КП 151031.05. ПЗ |
Грузоподъемность m=4000 кг, скорость подъема V=0,2 м/с, высота подъема H=6м, режим нагружения L1, группа классификации механизма M2, число зубьев шестерни Z=21.
Продолжительность включения механизма подъема груза определена в расчетах ВНИИПТМаш. Приравнивая умеренный режим нагружения к среднему имеем ПВ.
|
Таблица 3 – Режимы работы
В процентах
Легкий | Средний (умеренный) | Тяжелый | Весьма тяжелый |
25;40 |
Принимаем ПВ 15%.
Грузоподъемная сила
, (1)
где g = 9,81 – ускорение свободного падения.
.
Статическая мощность электродвигателя при продолжительности включения в час ПВ 40%, принятой в каталогах:
, (2)
где – предварительное значение КПД механизма
Изм. |
Лист |
№ докум. |
Подпись |
Дата |
Лист |
КП.151031.03.ПЗ |
Выберем электродвигатели по ближайшей большей мощности
Таблица 4 – Большая мощность
Тип двигателя | P, кВт | n, об/мин |
4АВ132А4У3 | 5,5 | |
4АВ132А6У3 | 5,5 | |
4АВ132В8У3 | 5,5 |
Расшифровка обозначения:
4 – символ соответствия стандарту МЭК;
А – асинхронный общепромышленный;
В – встраиваемый;
100 – высота вала,
А; В – длина сердечника статора (А - короткий, В - длинный);
4;6;8 – число полюсов;
У3 – климатическое исполнение (умеренный климат, неотапливаемое помещение)
Угловая скорость электродвигателя:
, (3)
Получим для чисел полюсов e = 4, 6, 8
Изм. |
Лист |
№ докум. |
Подпись |
Дата |
Лист |
КП.151031.03.ПЗ |
Минимальный диаметр барабана
Минимальный диаметр барабана (по средней линии каната), из условия размещения электродвигателя
, (4)
где = 225 мм – диаметр статора;
=19 мм – глубина воздушного зазора;
d=10…20 мм – предварительное значение диаметра каната
Примем D=320 из ряда Ra40 (допускается округлять до четного числа).
Коэффициент полезного действия полиспаста:
, (5)
где a – кратность полиспаста;
– КПД блока.
Получим:
Наибольшее натяжение ветви каната
Наибольшее натяжение ветви каната, указываемое в паспорте электрической тали
, (6)
Имеем:
;
|
;
Изм. |
Лист |
№ докум. |
Подпись |
Дата |
Лист |
КП.151031.03.ПЗ |
Разрывное усилие каната в целом, принимаемое по сертификату
, (7)
где z=3.35 – минимальный коэффициент использования каната для заданной группы классификации механизма (приложение);
S – наибольшее натяжение ветви каната.
Выберем канат типа ЛК-РО 6 19 + 1 о.с
Изм. |
Лист |
№ докум. |
Подпись |
Дата |
Лист |
КП.151031.03.ПЗ |
Таблица 5 – Наибольшее значение каната
ai | d, мм | ![]() | ![]() | ![]() |
11,5 | 7,51 | 1,96 | 6,570 | |
11,5 | 7,51 | 1,99 | 6,660 | |
9,0 | 4,54 | 1,34 | 4,515 | |
9,0 | 4,54 | 0,99 | 3,330 |
Диаметр каната уменьшается по мере увеличения произведения zS
Расчет барабана
Минимальный расчетный диаметр барабана
Минимальный расчетный диаметр барабана (по средней линии каната) из условия прочности
где – коэффициент выбора диаметра барабана по ИСО (приложение), т.е. отношение диаметра барабана к диаметру каната для заданной группы классификации механизма М2;
d – диаметр каната.
Получим:
Изм. |
Лист |
№ докум. |
Подпись |
Дата |
Лист |
КП.151031.03.ПЗ |
Отношение минимального конструктивного диаметра барабана
, (8)
где D – диаметр барабана из условия размещения электродвигателя;
– наибольшее значение диаметра каната.
Очевидно, что число x превышает число более, чем на 2 шага по таблице выбора диаметра каната.
Полагаем, что возможно увеличение коэффициента более, чем на 2 шага, однако значение z может быть снижено не более, чем на 2 шага. В нашем случае диаметр барабана увеличен более, чем на 2 шага. Уменьшим
на 2 шага, т.е. до значения z=3.15 и вновь выберем диаметры канатов таблица 6.
Таблица 6 – Диаметры канатов
ai | d, мм | ![]() | ![]() | ![]() |
11,5 | 7,51 | 1,96 | 6,18 | |
11,5 | 7,51 | 1,99 | 6,27 | |
9,0 | 4,54 | 1,34 | 4,24 | |
9,0 | 4,54 | 0,99 | 3,13 |
Вновь выбранные диаметры каната меньше, первоначальные. Это позволяет уменьшить длину барабана или увеличить его канатоемкость (высоту подъема).
Изм. |
Лист |
№ докум. |
Подпись |
Дата |
Лист |
КП.151031.03.ПЗ |
Одна из основных мер борьбы с износом деталей машин – это своевременное смазывание трущихся поверхностей. Слой смазочного материала разделяет трущиеся поверхности, поэтому они не соприкасаются между собой имеющимися мельчайшими выступами, которые и характеризуют шероховатость. Уменьшению трения благоприятствует подвижность смазки. Кроме того, смазка хорошо отводит теплоту, уносит частицы металла, обладающего абразивным свойством, и предохраняет детали от коррозии.
|
Конусные дробилки являются быстроходными тяжело нагруженными машинами. Производительная и безаварийная работа их возможна только при надежном и бесперебойном смазывании всех трущихся частей. Даже кратковременный перерыв в подаче масла к смазываемым точкам машины влечет за собой серьезную аварию — разрушение бронзовых втулок, прижоги на шейках валов и т. п. Смазывание всех трущихся частей циркуляционное жидкими маслами. Масло из бака 12 подается насосом 11 через пластинчатый 10 и войлочный 9 фильтры, трубу 7 и под давлением поступает в подпятник 17 эксцентрикового вала 15. Смазав все диски подшипника, масло поднимается вверх по зазорам между наружными стенками вала 15 и внутренними поверхностями цилиндрических втулок, а также между валом 18 и конусными втулками. Кроме того, по каналу, просверленному в валу 18 и в теле подвижного дробящего конуса 4, масло поступает на сферический подпятник 9. Затем омывает конические шестерни и поступает в сливную трубу 6 соединенную с масляным баком 12. В баке масло, пройдя через сетчатый фильтр 8, поступает в отстойники. В привод дробилки масло поступает через подводящую трубу 5, а сливается через трубу 6. В зимнее время перед пуском дробилки масло подогревают электронагревателями 1.
Изм. |
Лист |
№ докум. |
Подпись |
Дата |
Лист |
КП.151031.03.ПЗ |
2 — предохранительный клапан
3 — устройство микропереключателя
4 — тепловое реле
5,6,7 — трубы (подводящая, сливная нагнетательная)
8,9,10 — фильтры
11 — масляный насос с электродвигателем
12 — масляный бак
Рисунок 2 - Смазочная система конусной дробилки
Смазочная система оборудована предохранительным клапаном, предназначенным для сброса масла в случае повышения давления в маслопроводе сверх установленного. Для контроля масла в сливной трубе £ имеется устройство, автоматически отключающее дробилку при прекращении слива масла в бак. Для автоматического контроля температуры масла служит тепловое реле.
|
Для нормальной работы в бак дробилки КСД-900 заливают не менее 260 л масла, дробилки КСД-600 — не менее 140 л.
Для смазывания дробилок применяют следующие масла (ГОСТ 20799—75): летом — индустриальное И-40А, зимой — индустриальное И-ЗОА.
Резьбу конуса смазывают солидолом.
Масляный бак всегда должен быть заполнен маслом, чтобы оно могло отстаиваться. Фильтры систематически очищают от грязи: промывают керосином и продувают сжатым воздухом. При сильном загрязнении масло становится серым, а на дне бака образуется слой шлама. Такое масло уже не пригодно для смазки, его заменяют свежим, а масляный бак промывают. Заменяют масло после 1000… 2000 ч работы.
Система смазки обеспечивает:
1) нагнетание, очистку, ручную регулировку количества масла в точке смазки, сбор, возврат, нагрев и охлаждение масла;
Изм. |
Лист |
№ докум. |
Подпись |
Дата |
Лист |
КП.151031.03.ПЗ |
3) автоматический контроль и поддержание температуры масла в баке;
4) автоматический контроль давления масла в нагнетательном трубопроводе с включением резервного насоса.
5) автоматический контроль движения соответствующего количества масла в смазочном трубопроводе.
ЗАКЛЮЧЕНИЕ
В данном курсовом проекте произведено описание, принцип работы, организация ремонта и необходимый перечень оснастки для ремонта оборудования, необходимые расчёты для ремонта Конусной дробилки крупного дробления.
Изм. |
Лист |
№ докум. |
Подпись |
Дата |
Лист |
КП.151031.03.ПЗ |
Правильно организованный и проведенный капитальный ремонт дробилки в дальнейшем обеспечивает и продлевает работоспособность и приносит в дальнейшем предприятию прибыль.
Изм. |
Лист |
№ докум. |
Подпись |
Дата |
Лист |
КП.151031.03.ПЗ |
Разраб. |
Булатов В.И. |
Провер. |
Ланчикова А.С. |
Н. Контр. |
Конева Л.М. |
Организация капитального ремонта конусной дробилки Пояснительная записка |
Лит. |
Листов |
УГК ТК-401/ВПФ |
|
Введение 5
|
|
Механическое удерживание земляных масс: Механическое удерживание земляных масс на склоне обеспечивают контрфорсными сооружениями различных конструкций...
Эмиссия газов от очистных сооружений канализации: В последние годы внимание мирового сообщества сосредоточено на экологических проблемах...
Общие условия выбора системы дренажа: Система дренажа выбирается в зависимости от характера защищаемого...
Своеобразие русской архитектуры: Основной материал – дерево – быстрота постройки, но недолговечность и необходимость деления...
© cyberpedia.su 2017-2024 - Не является автором материалов. Исключительное право сохранено за автором текста.
Если вы не хотите, чтобы данный материал был у нас на сайте, перейдите по ссылке: Нарушение авторских прав. Мы поможем в написании вашей работы!