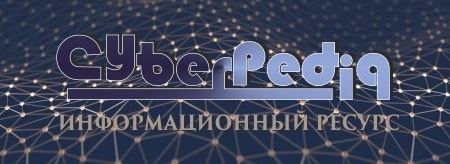
Адаптации растений и животных к жизни в горах: Большое значение для жизни организмов в горах имеют степень расчленения, крутизна и экспозиционные различия склонов...
История развития хранилищ для нефти: Первые склады нефти появились в XVII веке. Они представляли собой землянные ямы-амбара глубиной 4…5 м...
Топ:
Генеалогическое древо Султанов Османской империи: Османские правители, вначале, будучи еще бейлербеями Анатолии, женились на дочерях византийских императоров...
Марксистская теория происхождения государства: По мнению Маркса и Энгельса, в основе развития общества, происходящих в нем изменений лежит...
Интересное:
Инженерная защита территорий, зданий и сооружений от опасных геологических процессов: Изучение оползневых явлений, оценка устойчивости склонов и проектирование противооползневых сооружений — актуальнейшие задачи, стоящие перед отечественными...
Средства для ингаляционного наркоза: Наркоз наступает в результате вдыхания (ингаляции) средств, которое осуществляют или с помощью маски...
Отражение на счетах бухгалтерского учета процесса приобретения: Процесс заготовления представляет систему экономических событий, включающих приобретение организацией у поставщиков сырья...
Дисциплины:
![]() |
![]() |
5.00
из
|
Заказать работу |
|
|
Важнейшими технологическими процессами заготовительного производства в машиностроении являются обработка металлов давлением и литейное производство. Основным исходным сырьем машиностроительного производства являются металлы и сплавы на их основе.
Металлами называются непрозрачные кристаллические вещества, обладающие такими характерными свойствами, как прочность, пластичность, электропроводность, теплопроводность, блеск. Металлы традиционно подразделяются на две большие группы: черные и цветные.
К черным металлам относят железо и сплавы на его основе - сталь и чугун, а иногда также марганец и хром; к цветным — все остальные металлы и сплавы на их основе, среди которых наибольшее применение в машиностроении нашли алюминий, медь, титан, никель.
Основной задачей технологических процессов заготовительного производства является получение заготовок, приближенных по форме и размерам к готовым деталям.
Обработка материалов давлением является одним из наиболее распространенных и прогрессивных способов обработки, так как по сравнению с другими методами она обеспечивает меньшие потери металла, высокую производительность, относительно малую трудоемкость, увеличение прочности металла, широкие возможности механизации и автоматизации технологических процессов. Заготовки, получаемые обработкой давлением, имеют минимальные припуски на механическую обработку, а иногда и не требуют такой обработки.
При обработке металлов давлением происходит пластическая деформация, изменяющая форму заготовки без изменения ее массы.[5, стр.105]
На формообразование заготовок из конструкционных материалов влияет их пластичность, т.е. способность изменять форму под воздействием внешней силы, не разрушаясь, и сохранять полученную форму после прекращения действия силы. Природная пластичность различных материалов неодинакова и зависит в первую очередь от их структуры и химического состава. Одни материалы обладают высокой пластичностью в холодном состоянии и могут изменять свою форму без предварительного нагрева. Другие для повышения пластичности нагревают и подвергают пластической деформации в горячем состоянии. Исходя из этого, различают холодную и горячую обработку материалов давлением. При обработке металлов давлением широко применяются следующие технологические методы: прокатка, волочение, прессование, свободная ковка, штамповка (рис.2).
|
Прокатка является наиболее распространенным и экономичным способом обработки металлов давлением. Более 80 % выплавляемой стали поступает в прокатное производство, продукция которого стандартизирована и включает более 1000 наименований различного профиля: прокат простого профиля (круг, квадрат, шестигранник и др.), прокат фасонного профиля (швеллер, двутавр, уголок и др.), листовой прокат, трубы, периодический прокат и прокат специального профиля. Перечень прокатываемых изделий с указанием формы профилей и их размеров называется сортаментом проката.
Волочение — процесс протягивания (рис.2,б) на волочильном стане прутка через отверстие волочильной доски: при этом поперечное сечение прутка уменьшается, длина увеличивается, а обрабатываемый металл принимает форму и размеры этого отверстия. Волочением получают проволоку диаметром от 4 до 0,01 мм и менее, калиброванные валки, прутки различного профиля. Волочение применяют также для уменьшения диаметров труб.
Прессование — процесс выдавливания металла, заключенного в замкнутый объем цилиндра-матрицы через отверстие в матрице, в зависимости от формы и размеров которого получают изделия любой, даже самой сложной формы (рис.2, в). Прессование осуществляется на специальных прессах.
|
Свободная ковка (рис.2, г) — процесс горячей обработки металлов давлением, в ходе которого имеет место свободное течение металла в стороны. Исходным материалом при свободной ковке служат слитки, прокат различных профилей и прессованный металл. Изделие, полученное ковкой, называют поковкой.
Штамповка — процесс деформации металла в горячем или холодном состоянии, в ходе которого течение металла ограничено стенками рабочей поверхности специального инструмента — штампа. Штамповка может быть объемной и листовой.
Для объёмной штамповки (рис.2,д) исходными материалами служат прутки или штучные заготовки. Прогрессивным процессом горячей объёмной штамповки является безоблойная штамповка, т.е. штамповка в закрытых штампах без образования облоя, что даёт возможность значительно экономить материал.
Листовая штамповка (рис.2, е) является передовым методом обработки металлов давлением, характеризующимся высокой производительностью, простотой технологического процесса, точностью получаемых размеров изделия и низкой себестоимостью. Исходным материалом для нее служат листы, ленты, полосы. Для изготовления изделий толщиной свыше 8 мм применяют горячую листовую штамповку.
Так как при штамповке металл деформируется в заранее изготовленных формах (штампах), то заготовка получается более точной и чистой, чем при свободной ковке.
Штамповку экономически целесообразно применять в серийном и массовом производствах, так как штампы являются дорогим инструментом. Очевидно, что каждый штамп предназначен только для получения определенного типа заготовок.
Технологическое оборудование для обработки металлов давлением делят на следующие группы:
• основное: для выполнения технологических операций деформирования металла при прокатке, волочении, прессовании, ковке, штамповке (прокатные и волочильные станы, молоты, прессы и др.);
• дополнительное: оборудование и машины для резки заготовок из сортового проката (пресс-ножницы, зубчатые и фрикционные пилы, ножовочные станки, отрезные фрезерные станки и фрезерные автоматы), нагревательные печи и электронагревательные устройства, посадочные машины, кантователи, манипуляторы;
• вспомогательное: машины и механизмы для транспортировки заготовок от нагревательных устройств к основному оборудованию (мостовые краны, конвейеры, кран-балки, электротали, монорельсы, консольные краны, напольные транспортеры и др.), машины и оборудование для очистки воздуха и газов (вытяжные зонты, вентиляторы, воздуходувки и др.).
|
Другим широко используемым методом получения заготовок в машиностроении является литье[5,стр.108].
Литейное производство — совокупность технологических процессов получения фасонных изделий (отливок) путем заливки расплавленного металла в полую форму, воспроизводящую очертания и имеющую размеры будущей детали.
Литье является одним из важнейших и наиболее распространенных способов изготовления заготовок, деталей и готовой продукции. Им получают продукцию всевозможных конфигураций, размеров и массы из различных металлов и сплавов: чугуна, стали, сплавов меди, алюминия, магния и т.д.
Сущность процесса лить заключается в том, что расплавленный металл определённого химического состава заливается в заранее приготовленную литейную форму, полость которой по своим размерам и конфигурации соответствует форме и размерам требуемой заготовки. После остывания, заготовку, деталь или готовое изделие извлекают из формы. Литейные формы могут быть разового и многократного применения.
Все многообразие применяемых технологических процессов литейного производства можно разделить на 2 группы:
1)получение отливок в одноразовых(разрушаемых) формах;
2)получение отливок в формах многоразового применения.
Получение отливок в однообразных формах осуществляется при следующих технологических процессах литейного производства: литье в песчано-глинистых формах, литье в оболочковые формы, литье по выплавляемым моделям и др.[5,стр.111].
Литье в песчано-глинистые формы. Несмотря на то, что отливки, полученные этим методом, наименее точны, имеют
грубую поверхность, а сам технологический процесс отличается высокой трудоемкостью и многоэтапностью, литье в песчано-глинистые формы по-прежнему является основным технологическим методом получения отливок на отечественных предприятиях: им получают до 60 % общего объема чугунных и стальных отливок. Широкое распространение метода литья в песчано-глинистые формы объясняется таким его технико-экономическим преимуществом, как низкая себестоимость. Разовые литейные формы позволяют получать практически любые по конфигурации, сложности и массе отливки.
|
Технологический процесс получения отливок методом литья в песчано- глинистые формы включает следующие этапы:
• изготовление технологической оснастки;
• приготовление формовочных и стержневых смесей;
• изготовление разовых литейных форм и стержней;
• расплавление металла и заливка литейных форм;
• охлаждение, выбивка отливок из форм, обрубка, очистка и контроль качества отливок и др.
Рассмотрим специальные способы литья при получении отливок в формах многоразового использования (на примерах литья в кокиль, центробежного литья, литья под давлением).
Литье в кокиль. В кокилях (металлических формах) изготавливают отливки самой разнообразной конфигурации из цветных и черных сплавов. Конструкция и материал кокилей различны и зависят от металла получаемой отливки.
Центробежное литье — высокопроизводительный способ изготовления отливок тел вращения с центральным отверстием — труб, втулок и др., а также фасонного литья из чугуна, стали и цветных сплавов. Сущность центробежного литья заключается в том, что расплавленный металл заливается во вращающуюся форму. Под действием центробежных сил он отбрасывается к стенкам формы, затвердевает, получая плотную структуру без усадочных раковин. Неметаллические включения собираются на внутренней стороне отливки и удаляются при дальнейшей механической обработке. Для центробежного литья применяют 2 типа машин: с горизонтальной и вертикальной осями вращения формы(рис.3).
Литье под давлением является наиболее производительным и экономичным процессом в массовом производстве тонкостенных (от 0,8 мм и выше) отливок с массой от нескольких граммов до 25—50 кг, любой сложности и конфигурации, с большой точностью размеров и высоким качеством поверхности, исключающим механическую обработку.
Сущность процесса состоит в том, что металл под высоким давлением (от 200 до 2000 МПа) в расплавленном или полужидком состоянии со скоростью 0,5—140 м/с запрессовывается через систему литниковых каналов в рабочую полость разъемной пресс-формы. В пресс-форме металл кристаллизуется, затвердевшая отливка выталкивается из нее. Пресс-формы устанавливают на специальных машинах литья под давлением. Производительность литейных машин — от 60 до 3000 отливок в час. На рис.4 показана последовательность стадий получения отливки под давлением.
Литье в оболочковые формы — способ получения отливок и изделий свободной заливкой расплава в оболочковые формы из термореактивных смесей, представляющих собой смесь кварцевого песка с термореактивной смолой.
|
Для получения оболочковых форм широко применяется насыпной (бункерный) способ, основанный на использовании поворотного бункера (рис.5).
Литье по выплавляемым моделям представляет собой процесс получения отливок в неразъемных разовых огнеупорных формах, изготовляемых из легко плавящихся, выжигаемых или растворяемых составов. Являясь одним из древнейших методов художественного и производственного литья, данный способ получил в последние годы большое распространение в промышленности из-за высокой точности получаемых отливок.
Технологическое оборудование литейного производства подразделяется на следующие группы:
• основное: машины и оборудование для подготовки исходных материалов (сушила, мельницы, дробилки, сита), приготовления формовочных и стержневых смесей (смесители), изготовления литейных форм и стержней (формовочные и стержневые машины, пескометы, пескодувные машины), специальных методов литья, плавки металлов (вагранки, дуговые и индукционные печи и др.);
• дополнительное: транспортирующие, грузоподъемные и грузонесущие машины и механизмы (конвейеры различных типов, мостовые краны, кран-балки, электротали и др.);
• вспомогательное: оснащение для очистки воздуха, удаления газов в литейных цехах (вентиляторы, воздуходувки, вытяжные зонты и др.).
|
|
Наброски и зарисовки растений, плодов, цветов: Освоить конструктивное построение структуры дерева через зарисовки отдельных деревьев, группы деревьев...
Поперечные профили набережных и береговой полосы: На городских территориях берегоукрепление проектируют с учетом технических и экономических требований, но особое значение придают эстетическим...
Типы оградительных сооружений в морском порту: По расположению оградительных сооружений в плане различают волноломы, обе оконечности...
Папиллярные узоры пальцев рук - маркер спортивных способностей: дерматоглифические признаки формируются на 3-5 месяце беременности, не изменяются в течение жизни...
© cyberpedia.su 2017-2024 - Не является автором материалов. Исключительное право сохранено за автором текста.
Если вы не хотите, чтобы данный материал был у нас на сайте, перейдите по ссылке: Нарушение авторских прав. Мы поможем в написании вашей работы!