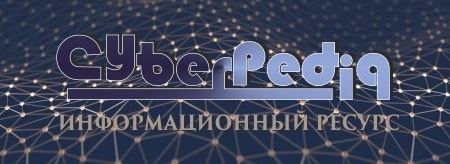
Архитектура электронного правительства: Единая архитектура – это методологический подход при создании системы управления государства, который строится...
Эмиссия газов от очистных сооружений канализации: В последние годы внимание мирового сообщества сосредоточено на экологических проблемах...
Топ:
Выпускная квалификационная работа: Основная часть ВКР, как правило, состоит из двух-трех глав, каждая из которых, в свою очередь...
Генеалогическое древо Султанов Османской империи: Османские правители, вначале, будучи еще бейлербеями Анатолии, женились на дочерях византийских императоров...
Интересное:
Принципы управления денежными потоками: одним из методов контроля за состоянием денежной наличности является...
Что нужно делать при лейкемии: Прежде всего, необходимо выяснить, не страдаете ли вы каким-либо душевным недугом...
Распространение рака на другие отдаленные от желудка органы: Характерных симптомов рака желудка не существует. Выраженные симптомы появляются, когда опухоль...
Дисциплины:
![]() |
![]() |
5.00
из
|
Заказать работу |
|
|
Технологический процесс – часть производственного процесса, которая предусматривает последовательные изменения состояния исходной заготовки до получения готовой детали согласно чертёжной документации.
При разработке техпроцесса изготовления детали решаются задачи:
1) составляется общий план обработки детали;
2) устанавливается последовательность выполнения техопераций;
3) уточняются методы обработки, базы;
4) определяется содержание операций и оснащение.
Таблица 2 – Анализ требований точности и взаимного расположения
Размер (поверхность) | Последовательность обработки | Шероховатость | Точность |
М68-8g | Точение черновое чистовое Резьбонарезание | Rа 12,5 Rа 3,2 | IT12 IT10 |
Ø80k6 | Точение черновое чистовое Шлифование | Rа 6,3 Rа 3,2 Rа1,25 | IT12 IT10 IT6 |
Ø168h12; Ø90h14; Ø110h14; | Точение черновое чистовое | Rа 12,5 Rа 6,3 | IT14 IT14 |
L 380h14; | Точение черновое | Rа 6,3 | IT14 |
10H12ר63,5h12 20±0,5 20N9ר61h12; 10±0,5 60±0,5 | Фрезерование | Rа 6,3 | IT14 |
80±1 24h12 20±0,5 66±0,5 | Точение черновое Точение чистовое | Rа 12,5 Rа 6,3 | IT14 IT14 |
Фаски 2´45° 1,5´45° Канавки b 4,5´Ø64; b 2,2´Ø76 | Точение чистовое | Rа 6,3 | IT12 |
Зубчатый венец m–3 z–38 | Зубофрезерование Зубошлифование | Rа 2,5 Rа 1,6 | IT10 IT8 |
Анализ технических требований
а) Поверхности Ø80k6 выполнены с шероховатостью Ra 1,25 - 6 кл. точности.
б) Поверхность эвольвентного профиля зубьев выполнены с шероховатостью Ra 1,6 – 7-С класса точности.
Требования к взаимному расположению поверхностей.
Базами являются поверхности Ø80k6 слева и справа.
а) радиальное биение поверхности относительно оси не более 0,03мм.
|
б) радиальное биение зубчатого венца на зуб не более 0,05мм. за оборот – 0,1 обеспечиваются в техпроцессе зубошлифованием и оснасткой.
Закалка ТВЧ предусмотрена по ходу технологического процесса.
Эффективность обработки (точность, производительность и т. д.) существенно зависит от выбранных способов установки деталей.
Таблица 3 – Маршрут обработки детали
№ оп. | Наименование операции | Станок, оборудование | Содержание операции |
000 | Заготовительная | Кривошипный горячештамповочный пресс | Горячая объемная штамповка |
005 | Токарная с ЧПУ | Токарный п/а с ЧПУ FORT мод. Д 500 | Точить поверхности предварительно с 2х сторон. |
010 | Токарная с ЧПУ | Токарно – фрезерный п/а с ЧПУ мод. NEF 400 | Точить поверхности, резьбу и канавки, фрезеровать шпоночный паз |
015 | Токарная с ЧПУ | Токарно – фрезерный п/а с ЧПУ мод. NEF 400 | Точить поверхности, резьбу и канавки, фрезеровать шпоночный паз |
020 | Зубофрезерная | Зубофрезерный п/а с ЧПУ мод. GHO-200 | Фрезеровать зубчатый венец m-3 z -38 |
025 | Слесарная | Слесарная установка | Зачистить заусенцы |
030 | Промывка | Моечная установка | Промыть деталь. |
035 | Контроль | Контрольная плита | Проверить все размеры |
040 | Термообработка | Закалочная установка ТВЧ | Калить ТВЧ h 1,0...1,3, 48...53 HRC |
045 | Шлифовальная с ЧПУ | Шлифовальный п/а с ЧПУ мод. GU-3250 | Шлифовать поверхности Ø80k6 и торец |
050 | Зубошлифовальная | Зубошлифовальный п/а с ЧПУ Reishauer мод. RZ 500 | Шлифовать зубчатый венец m-3 z -38 |
055 | Слесарная | Слесарная установка | Зачистить заусенцы |
060 | Промывка | Моечная машина | Промыть деталь. |
065 | Контроль | Контрольная плита | Проверить все размеры |
Выбор технологических баз
Технологические базы подразделяются: на установочные и измерительные. Установочные базы - поверхности, которыми она устанавливается в определенном положении относительно станка и режущего инструмента.
|
При выборе технологических баз необходимо руководствоваться следующими правилами:
1) Стремиться выполнить принцип «совмещения баз» — совместить технологическую, измерительную и конструкторскую базы. В этом случае погрешность базирования равна погрешности формы технологической базы.
2) Стремиться выполнить принцип «постоянства баз», по всему технологическому процессу использовать одни базовые поверхности.
3) Базовые поверхности должны иметь соответствующие размеры, точность их взаимного расположения, точную установку и жесткость.
4) Черновую базовую поверхность следует использовать один раз на первой установке.
Выбор баз для черновой обработки
Основные требования к поверхностям, используемым в качестве черновых баз:
1) поверхности должны иметь достаточные размеры, для обеспечения точности базирования и усилия закрепления;
2) поверхности должны иметь более высокую точность, наименьшую шероховатость и не иметь других дефектов;
3) за базы на первой операции рекомендуется принимать поверхности с наименьшими припусками;
Рисунок 2 – Схемы базирования (черновые базы).
Установочная база может быть основной или вспомогательной.
Основной установочной базой для данной детали являются центровые фаски, которые формируются на первых операциях техпроцесса.
Рисунок 3 – Схемы базирования (чистовые базы).
При выборе базовых поверхностей максимально соблюдается принцип единства и постоянства баз, что положительно отражается на погрешности базирования, качестве обработки, на конструктивных особенностях установочно-зажимных приспособлениях.
РАЗРАБОТКА ПЛАНИРОВКИ УЧАСТКА
2.1 Выбор типа планировки
Серийное производство занимает промежуточное положение между единичным и массовым. Это самый распространенный тип производства. Изготовление деталей производится партиями (сериями), состоящими из одноименных, однотипных по конструкции и одинаковых по размерам деталей, запускаемых в производство одновременно. В зависимости от типоразмера детали, размера партии, количества изделий в серии и частоты повторяемости серий в течение года выделяют мелко- средне- и крупносерийное производство.
|
В серийном производстве технологический процесс разделен на отдельные операции, закрепленные за определенными станками. Применяется самое разнообразное оборудование: универсальное, специализированное, автоматизированное и агрегатные станки. Оснастка – универсально-переналаживаемая. Квалификация рабочих – средняя.
Линейный принцип применяется при поточном производстве и характеризуется определенной последовательностью выполнения операций технологического процесса в каждый момент времени. В этом случае оборудование располагается по ходу технологического процесса.
Предметный принцип применяется при расширении номенклатуры изделий в условиях серийного производства и основан на применении однотипных технологических процессов. В этом случае группирование оборудования осуществляется по конструктивным особенностям деталей, например, участки обработки валов, зубчатых колес, корпусных деталей, в пределах которых оборудование располагается по ходу технологического процесса.
2.2 | Характеристика оборудования |
Технологическое оснащение – комплекс элементов, обеспечивающий выполнение процесса изготовления деталей заданной точности и производительности с оптимальными затратами на производство. [6]
Современное технологическое оборудование имеет жесткую конструкцию, позволяющую совмещать черновую и чистовую обработки, обеспечивая при этом высокую точность и качество обрабатываемых поверхностей. Требования к точности и жесткости станков постоянно повышаются, так как погрешности, допущенные при изготовлении станка, переносятся на обработанную деталь. При оценке возможности обеспечения заданной точности обработки заготовок учитываются индивидуальные возможности станка и степень его износа.
Выбор технологического оборудования – станков зависит от:
¾ типа производства, требуемой производительности и себестоимости;
¾ метода обработки отдельных элементов детали;
¾ габаритных и обрабатываемых размеров детали и мощности, необходимой для резания;
|
¾ возможности обеспечения требуемой точности размеров и формы и качества поверхностей изготовляемой детали;
¾ степени удобства и безопасности работы станка.
Токарный полуавтомат с ЧПУ FORT модели Д 500
Станина из высококачественного чугуна гарантирует высокую жесткость и виброустойчивость. Жесткость шпинделя обеспечивается 4-мя коническими двухрядными подшипниками. Высокоточные ШВП класса точности СЗ со сдвоенной гайкой гарантирует жесткость и точность. Увеличенный диаметр ШВП по оси 2 до 50 мм гарантирует стабильность на максимальных режимах резания.
Оси «С» и «Y» значительно расширяют технологические возможности, позволяет производить фрезерование, вне осевое сверление и нарезание резьбы и другие операции Ось «С» и фрезерная функция значительно расширяют технологические возможности станка.
Рисунок 4. Токарный п/а с ЧПУ FORT модели Д 500
Таблица 4 – Техническая характеристика
Параметры | Значение |
Максимальный диаметр обрабатываемой детали, мм: Максимальная длина обрабатываемой детали, мм: Расстояния между поверхностями двух шпинделей, мм: Перемещение по осям: "X" / "Z" / Y , мм: Мощность привода, кВт: Диапазон частот вращения, мин-1: Размер под патрон / Диаметр патрона, мм: Отверстие в шпинделе, мм: Ускоренное перемещение по оси X1, X2 / Z1, Z2 м/мин: Ускоренное перемещение по оси B / по оси Y м/мин: Количество позиций инструмента/ из них вращающихся Диаметр хвостовика (по DIN69880) / высота резца, мм: Время индексации головки на одну позицию, с: Максимальная частота вращения, мин-1: Максимальный диаметр /скорость вращения инструмента, мм/мин-1: Сечение резца, мм: Мощность приводного инструмента, кВт: Точность позиционирования, мм: Габариты станка, мм: | 190 350 750 135 / 450 / ±40 15 0 - 8000 А2-5/250 А5/55 18 18 / 24 6 / 24 12 15/20 0,14 4500 16/6000 20×20 3,5 ±0,005 3500´1600´1900 |
Рисунок 5. Токарно – фрезерный полуавтомат с ЧПУ модели NEF 400
Ключевые особенности NEF 400 Интегрированный шпиндель-двигатель ISM: увеличенное отверстие шпинделя, более высокое число оборотов, увеличенная точность/жесткость по оси С, увеличенные диаметры подшипников для повышения жесткости, жидкостное охлаждение для улучшения термической стабильности, удобство сервисного обслуживания – отсутствует необходимость периодической регулировки ремня. Увеличенный обзор рабочей зоны, удобное управление, компактная конструкция. Компактная конструкция за счет очень жесткой, массивной литой станины станка. Револьверная головка VDI 30 на 12 инструментов и задняя бабка с автоматическим управлением и гидравлическим приводом в стандартной комплектации.
|
Таблица 5 – Техническая характеристика
Параметры | Значение |
Максимальный диаметр устанавливаемой детали через станину , мм: | 385 |
Максимальный диаметр обточки через станину, мм: | 350 |
Быстрый ход (X), мм: | 255 |
Продольное перемещение (Z) мм: | 800 |
Шпиндельная головка, Size: | 170 h5 |
Диаметр в передней опоре, мм: | 87 |
Диаметр патронных заготовок, мм: | 130 |
Сверление шпинделем , мм: | 200/250 |
Мощность привода (40/100% цикла нагрузки), kW: | 11,5 / 8 |
Диапазон скорости, об/мин: : | 0 – 4 500 |
Быстрый ход (X/Z), мм: | 30/30 |
Диаметр хвостовика (DIN 69880) 30(BDI 30), | 30 (VDI 30) |
Габариты (длина´ширина´высота), мм: | 2812×2638×2810 |
3. Зубофрезерный полуавтомат модели с ЧПУ GHO-200
Зубофрезерный станок с ЧПУ GHO-200 для высокоскоростного, прецизионного зубофрезерования. На станке могут быть обработаны следующие типы колес: цилиндрические прямозубые колеса; цилиндрические косозубые колеса; звездочки; червячные колеса.
Рисунок 7 Зубофрезерный полуавтомат модели с ЧПУ GHO-200
Таблица 6 – Техническая характеристика
Параметры | Значение |
Максимальный диаметр, модуль заготовки, мм: | Ø 200/ 5,5 |
Диаметр стола Ø, мм: | 240 |
Перемещение по оси Z / оси X, мм: | 350/200 |
Угол наклона фрезы, °: | ±45 |
Конус оправки червячной фрезы | NT.№40 |
Максимальный диаметр / длина фрезы, мм: | Ø 180 / 190 |
Максимальная скорость вращения фрезы, об/мин: | 500 |
Максимальная скорость вращения стола, об/мин: | 230 |
Ход задней стойки, мм: | 380-780 |
Ускоренная подача по оси Z, X, м/мин: | 12 |
Ускоренная подача по оси Y, мм/с: | 1 |
Расстояние от поверхности стола до центра фрезы по оси Z, мм: | 200-550 |
Расстояние от поверхности стола до центра фрезы по оси X, мм: | 15-215 |
Привод оси B, вращение инструмента, кВт: | АС 12 / 16 |
Привод оси A, поворотное движение фрезерного шпинделя, кВт: | 1,6 |
Привод оси Z, верт. перемещение фрезерного шпинделя, Нм: | 27 / 2:1 |
Привод оси X, радиальное перемещение передней стойки (Нм) | 27 |
Привод оси C, вращение стола, Нм: | 410 |
Привод оси Y, тангенциальное перемещение инструмента, Нм: | 6 / 10:1 |
Привод оси Y, тангенциальное перемещение инструмента, Нм: | 0,2/0,9 |
Привод системы смазки/ СОЖ, кВт: | 3,7 / 2,2 |
Привод гидросистемы, кВт: | 7600 |
Фиксация фрезерного шпинделя, кг: | 280 -1120 |
Фиксация заготовки | (Ø цилиндра 120 мм) |
Количество управляемых от ЧПУ осей/ одновременно | 6 (X,Y,Z,A,B,C) /4 |
Габариты (длина´ширина´высота), мм: | 2812×2638×2810 |
Шлифовальный п/а с ЧПУ мод. GU-3250
Предназначен для наружного шлифования цилиндрических поверхностей изделий и конических поверхностей изделий с небольшой конусностью.
Таблица 7 – Техническая характеристика
Параметры | Значение |
Межцентровое расстояние, мм: | 500 |
Максимальный диаметр шлифования, мм: | 280 |
Предельные углы поворота стола ,° : | -0,5…+8 |
Частота вращения шпинделя бабки изделия, мин-1: | 5-750 |
Шлифовальный круг, мм: | 405´63´127 |
Окружная скорость шлифовального круга, м/сек: | 33 |
Угол поворота шлифовальной бабки,° : | +45, -15 |
Минимальная величина перемещения по оси X/Z, мм: | 0,001 |
Конус шпинделя бабки изделия / пиноли задней бабки | КМ4 |
Ход пиноли задней бабки, мм: | 35 |
Скорость подачи стола, м. мин-1: | 0,005 ÷ 5 |
Общая потребляемая мощность станка, кВт: | 8 |
Габариты (длина×ширина×высота), мм | 3810×2100×1850 |
Рисунок 8 Шлифовальный п/а с ЧПУ мод. GU-3250
Зубошлифовальный п/а с ЧПУ Reishauer RZ 500
На станке Reishauer RZ 1000 обеспечивается преимущества процесса обкатного зубошлифования Reishauer при изготовлении зубчатых колес.
Таблица 8 – Технические характеристики
Параметры | Значение |
Диаметр окружности вершин зубьев, мм: | 500 mm |
Модуль, мм: | 0,8 - 10 |
Угол наклона зубьев, °: | ±40 |
Ширина зубчатого колеса, мм: | макс 250 |
Скорость резания при шлифовании, м/с: | макс. 80 |
Диаметр окружности шлифовального колеса, мм: | 300-205 |
Ширина шлифовального колеса, мм: | 145 |
Диаметр правящего инструмента, мм: | 160 |
Габариты (длина×ширина×высота), мм: | 2800×2760×3100 |
Рисунок 9 Зубошлифовальный п/а с ЧПУ Reishauer RZ 1000
![]() | ![]() |
а | б |
![]() | ![]() |
в | г |
Рисунок 10 Рабочие позиции станка RZ 1000 |
а – позиция шлифования; б – позиция правки; в – позиция смены шлифовального круга; г – позиция контроля.
С помощью поворотной стойки станка шлифовальный шпиндель устанавливается на три различные позиции: шлифования (рис. 10 а), правки (рис. 10 б), смены шлифовального круга (рис. 10 в)
|
|
История развития пистолетов-пулеметов: Предпосылкой для возникновения пистолетов-пулеметов послужила давняя тенденция тяготения винтовок...
Своеобразие русской архитектуры: Основной материал – дерево – быстрота постройки, но недолговечность и необходимость деления...
История развития хранилищ для нефти: Первые склады нефти появились в XVII веке. Они представляли собой землянные ямы-амбара глубиной 4…5 м...
Состав сооружений: решетки и песколовки: Решетки – это первое устройство в схеме очистных сооружений. Они представляют...
© cyberpedia.su 2017-2024 - Не является автором материалов. Исключительное право сохранено за автором текста.
Если вы не хотите, чтобы данный материал был у нас на сайте, перейдите по ссылке: Нарушение авторских прав. Мы поможем в написании вашей работы!