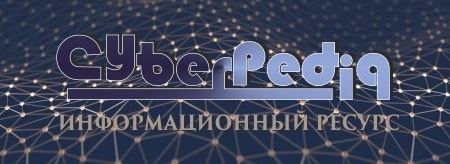
Семя – орган полового размножения и расселения растений: наружи у семян имеется плотный покров – кожура...
Опора деревянной одностоечной и способы укрепление угловых опор: Опоры ВЛ - конструкции, предназначенные для поддерживания проводов на необходимой высоте над землей, водой...
Топ:
Техника безопасности при работе на пароконвектомате: К обслуживанию пароконвектомата допускаются лица, прошедшие технический минимум по эксплуатации оборудования...
Генеалогическое древо Султанов Османской империи: Османские правители, вначале, будучи еще бейлербеями Анатолии, женились на дочерях византийских императоров...
Определение места расположения распределительного центра: Фирма реализует продукцию на рынках сбыта и имеет постоянных поставщиков в разных регионах. Увеличение объема продаж...
Интересное:
Уполаживание и террасирование склонов: Если глубина оврага более 5 м необходимо устройство берм. Варианты использования оврагов для градостроительных целей...
Лечение прогрессирующих форм рака: Одним из наиболее важных достижений экспериментальной химиотерапии опухолей, начатой в 60-х и реализованной в 70-х годах, является...
Аура как энергетическое поле: многослойную ауру человека можно представить себе подобным...
Дисциплины:
![]() |
![]() |
5.00
из
|
Заказать работу |
|
|
ОТЧЕТ ПО ПРАКТИЧЕСКИМ РАБОТАМ
по дисциплине Горячая обработка материалов и упрочняющие
технологии
Специальность: 15.02.04 «Специальные машины и устройства»
.
Выполнил: студент гр. Зверев А.М Принял:
__________(______________) _______Семирикова Н.Г.
(подпись) (подпись)
«___»_______________20__г. «___»_______________20__г.
Ковров 2022
ЛАБОРАТОРНАЯ РАБОТА 1
Формовочные смеси, их приготовление и классификация
Формовочные и стержневые смеси составляют из свежих формовочных материалов (природных песков и глин), оборотного формовочного материала, получаемого в результате разрушения (выбивки) форм после затвердения в них отливок, и специальных добавок.
Все необходимые компоненты (песок, глина, вода, связующие и др.) формовочной смеси засыпают в смесеприготовительные бегуны. После перемешивания получают формовочную смесь. Полученные смеси должны соответствовать необходимым требованиям.
Формовочные смеси (основные компоненты: песок, глина, графит, вода и др.; связующий элемент - графит) используются для приготовления литейных форм.
Их классифицируют:
- по роду металла: на смеси для чугунного, стального или цветного литья;
- по состоянию формовочного материала в форме: на сырые и сухие формы;
|
- по назначению: на единые, облицовочные и наполнительные.
Единой называют формовочную смесь, применяемую обычно в массовом производстве при машинной формовке для изготовления всей формы в целом.
Облицовочные или модельные смеси служат для образования слоя формы толщиной 20-30 мм непосредственно соприкасающегося с металлом. Облицовочную смесь при формовке распределяют ровным слоем по поверхности модели.
Наполнительная смесь используется совместно с облицовочной и служит для заполнения всего остаточного объема опок. Она состоит, в основном, из оборотной смеси с добавкой для освежения глинистых и иногда кварцевых песков.
Стержневые смеси(основные компоненты: песок, глина, графит, жидкое стекло и др.; связующий элемент - жидкое стекло) используются для приготовления стержней.
Стержни в форме почти полностью находятся в расплавленном металле с высокой температурой, который поднимает их вверх, при значительной длине изгибает, а при охлаждении сжимает вследствие усадки. Образующиеся газы могут проводиться только через знаки стержней. Поэтому стержневые смеси должны обладать повышенной по сравнению с формовочными смесями прочностью, газопроницаемостью, огнеупорностью, податливостью, и возможно малой газотворной способностью. Кроме того, они должны легко удаляться (высыпаться) из отливки после ее извлечения из формы.
Технологический процесс изготовления отливок в песчано-глинистых формах
1. Изготовление чертежей отливки, модели, стержней,формы.
2. Изготовление модели.
3 Изготовление стержней
4. Изготовление литейной формы.
5. Выплавка жидкого металла в печи.
6. Заливка жидкого металла в литейную форму.
7. Остывание отливки до комнатной температуры.
8. Извлечение (выбивка) отливки из литейной формы.
9. Обрубка и отчистка отливки.
10. Контроль качества отливки
11.Термическая обработка
Вывод: я изучил технологию ручной формовки в парных опоках по разъемной модели
ПРАКТИЧЕСКАЯ РАБОТА 2
|
Специальные способы литья
Цель : Изучить специальные способы литья и возможность применения этих способов для литья различных металлов и сплавов
МЕТОДИЧЕСКИЕ УКАЗАНИЯ
Специальные способы литья
В современном литейном производстве все более широкое применение получают специальные способы литья: в оболочковые формы, по выплавляемым моделям, кокильное, под давлением, центробежное и другие.
Эти способы позволяют получать отливки повышенной точности, с малой шероховатостью поверхности, минимальными припусками на механическую обработку, а иногда полностью исключают ее, что обеспечивает высокую производительность труда. Каждый специальный способ литья имеет свои особенности, определяющие области применения.
Литье в оболочковые формы
Литье в оболочковые формы - процесс получения отливок из расплавленного металла в формах, изготовленных по горячей модельной оснастке из специальных песчано-смоляных смесей.
Формовочную смесь приготовляют из мелкого кварцевого песка с добавлением термореактивных связующих материалов.
Технологические операции формовки при литье в оболочковые формы представлены на рис.6.1.
Металлическую модельную плиту 1 с моделью нагревают в печи до 200…250 0C.
Затем плиту 1 закрепляют на опрокидывающемся бункере 2 с формовочной смесью 3 (рис. 6.1. а) и поворачивают на 180 0 (рис. 6.1.б). Формовочную смесь выдерживают на плите 10…30 секунд. Под действием теплоты, исходящей от модельной плиты, термореактивная смола в приграничном слое расплавляется, склеивает песчинки и отвердевает с образованием песчано-смоляной оболочки 4, толщиной 5…15 мм. Бункер возвращается в исходное положение (рис. 6.1. в), излишки формовочной смеси осыпаются с оболочки. Модельная плита с полутвердой оболочкой 4 снимается с бункера и прокаливается в печи при температуре 300…350 ᵒC, при этом смола переходит в твердое необратимое состояние. Твердая оболочка снимается с модели с помощью выталкивателей 5 (рис.6.1.г). Аналогичным образом получают вторую полуформу.
Для получения формы полуформы склеивают или соединяют другими способами (при помощи скоб).
Рис 6.1. Технологические операции формовки при литье в оболочковые формы
|
Собранные формы небольших размеров с горизонтальной плоскостью разъема укладывают на слой песка. Формы с вертикальной плоскостью разъема 6 и крупные формы для предохранения от коробления и преждевременного разрушения устанавливают в контейнеры 7 и засыпают чугунной дробью 8 (рис.6.1.д).
Преимущества Литье в оболочковые формы обеспечивает высокую геометрическую точность отливок, малую шероховатость поверхностей, снижает расход формовочных материалов (высокая прочность оболочек позволяет изготавливать формы тонкостенными) и объем механической обработки, является высокопроизводительным процессом.
В оболочковых формах изготавливают отливки массой 0,2…100 кг с толщиной стенки 3…15 мм из всех литейных сплавов для приборов, автомобилей, металлорежущих станков.
Литье по выплавляемым моделям
Литье по выплавляемым моделям – процесс получения отливок из расплавленного металла в формах, рабочая полость которых образуется благодаря удалению (вытеканию) легкоплавкого материала модели при ее предварительном нагревании.
Технологические операции процесса литья по выплавляемым моделям представлены на рис. 6.2.
Выплавляемые модели изготавливают в пресс-формах 1 (рис. 6.2.а) из модельных составов, включающих парафин, воск, стеарин, жирные кислоты. Состав хорошо заполняет полость пресс-формы, дает четкий отпечаток. После затвердевания модельного состава пресс-форма раскрывается и модель 2 (рис. 6.2.б) выталкивается в холодную воду.
Затем модели собираются в модельные блоки 3 (рис. 6.2.в) с общей литниковой системой припаиванием, приклеиванием или механическим креплением. В один блок объединяют 2…100 моделей.
Формы изготавливают многократным погружением модельного блока 3 в специальную жидкую огнеупорную смесь 5, налитую в емкость 4 (рис.6.2.г) с последующей обсыпкой кварцевым песком. Затем модельные блоки сушат на воздухе или в среде аммиака. Обычно наносят 3…5 слоев огнеупорного покрытия с последующей сушкой каждого слоя.
Модели из форм удаляют, погружая в горячую воду или с помощью нагретого пара. После удаления модельного состава тонкостенные литейные формы устанавливаются в опоке, засыпаются кварцевым песком, а затем прокаливают в печи в течение 6…8 часов при температуре 850…950 0C для удаления остатков модельного состава, испарения воды (рис. 6.2.д)
|
Рис.6.2. Технологические операции процесса литья по выплавляемым моделям
Заливку форм по выплавляемым моделям производят сразу же после прокалки в нагретом состоянии. Заливка может быть свободной, под действием центробежных сил, в вакууме и т.д.
После затвердевания залитого металла и охлаждения отливок форма разрушается, отливки отделяют от литников механическими методами, направляют на химическую очистку, промывают и подвергают термической обработке.
Преимущества Литье по выплавляемым моделям обеспечивает получение точных и сложных отливок из различных сплавов массой 0,02…15 кг с толщиной стенки 0,5…5 мм.
Недостатком является сложность и длительность процесса производства отливок, применение специальной дорогостоящей оснастки.
Литьем по выплавляемым моделям изготавливают детали для приборостроительной, авиационной и другой отраслевой промышленности. Используют при литье жаропрочных труднообрабатываемых сплавов (лопатки турбин), коррозионно-стойких сталей, углеродистых сталей в массовом производстве (автомобильная промышленность).
Технологический процесс автоматизирован и механизирован.
Литье в металлические формы
Литье в металлические формы (кокили) получило большое распространение. Этим способом получают более 40% всех отливок из алюминиевых и магниевых сплавов, отливки из чугуна и стали.
Литье в кокиль – изготовление отливок из расплавленного металла в металлических формах-кокилях.
Формирование отливки происходит при интенсивном отводе теплоты от расплавленного металла, от затвердевающей и охлаждающейся отливки к массивному металлическому кокилю, что обеспечивает более высокие плотность металла и механические свойства, чем у отливок, полученных в песчаных формах.
Схема получения отливок в кокиле представлена на рис. 6.3.
Рабочую поверхность кокиля с вертикальной плоскостью разъема, состоящую из поддона 1, двух симметричных полуформ 2 и 3 и металлического стержня 4, предварительно нагретую до 150…180ᵒC покрывают из пульверизатора 5 слоем огнеупорного покрытия (рис. 6.3.а) толщиной 0,3…0,8 мм. Покрытие предохраняет рабочую поверхность кокиля от резкого нагрева и схватывания с отливкой.
Покрытия приготовляют из огнеупорных материалов (тальк, мел, графит), связующего материала (жидкое стекло) и воды.
Рис. 6.3 Технологические операции изготовления отливки в кокиль
Затем с помощью манипулятора устанавливают песчаный стержень 6, с помощью которого в отливке выполняется полость (рис.6.3.б).
|
Половинки кокиля соединяют и заливают расплав. После затвердевания отливки 7 (рис. 6.3.в) и охлаждения ее до температуры выбивки кокиль раскрывают (рис.6.3.г) и протягивают вниз металлический стержень 4. Отливка 7 удаляется манипулятором из кокиля (рис.6.3.д).
Отливки простой конфигурации изготовляют в неразъемных кокилях, несложные отливки с небольшими выступами и впадинами на наружной поверхности – в кокилях с вертикальным разъемом. Крупные, простые по конфигурации отливки получают в кокилях с горизонтальным разъемом. При изготовлении сложных отливок применяют кокили с комбинированным разъемом.
Расплавленный металл в форму подводят сверху, снизу (сифоном), сбоку. Для удаления воздуха и газов по плоскости разъема прорезают вентиляционные каналы.
Преимущества Все операции технологического процесса литья в кокиль механизированы и автоматизированы. Используют однопозиционные и многопозиционные автоматические кокильные машины.
Литье в кокиль применяют в массовом и серийном производствах для изготовления отливок из чугуна, стали и сплавов цветных металлов с толщиной стенки 3…100 мм, массой от нескольких граммов до нескольких сотен килограммов.
Литье в кокиль позволяет сократить или избежать расхода формовочных и стержневых смесей, трудоемких операций формовки и выбивки форм, повысить точность размеров и снизить шероховатость поверхности, улучшить механические свойства.
Недостатки кокильного литья: высокая трудоемкость изготовления кокилей, их ограниченная стойкость, трудность изготовления сложных по конфигурации отливок.
Изготовление отливок центробежным литьем
При центробежном литье сплав заливается во вращающиеся формы. Формирование отливки осуществляется под действием центробежных сил, что обеспечивает высокую плотность и механические свойства отливок.
Центробежным литьем изготовляют отливки в металлических, песчаных, оболочковых формах и формах для литья по выплавляемым моделям на центробежных машинах с горизонтальной и вертикальной осью вращения.
Металлические формы изложницы изготовляют из чугуна и стали. Толщина изложницы в 1,5…2 раза больше толщины отливки. В процессе литья изложницы снаружи охлаждают водой или воздухом.
На рабочую поверхность изложницы наносят теплозащитные покрытия для увеличения срока их службы. Перед работой изложницы нагревают до 200 0C.
Схемы процессов изготовления отливок центробежным литьем представлены на рис.6.4.
Рис.6.4. Схемы процессов изготовления отливок центробежным литьем
При получении отливок на машинах с вращением формы вокруг вертикальной оси (рис. 6.4.а) металл из ковша 4 заливают во вращающуюся форму 2, укрепленную на шпинделе 1, который вращается от электродвигателя.
Под действием центробежных сил металл прижимается к боковой стенке изложницы. Литейная форма вращается до полного затвердевания отливки. После остановки формы отливка 3 извлекается.
Отливки имеют разностенность по высоте – более толстое сечение в нижней части. Применяют для получения отливок небольшой высоты – коротких втулок, колец, фланцев.
При получении отливок типа тел вращения большой длины (трубы, втулки) на машинах с горизонтальной осью вращения (рис. 6.4.б) изложницу 2 устанавливают на опорные ролики 7 и закрывают кожухом 6. Изложница приводится в движение электродвигателем 1. Расплавленный металл из ковша 4 заливают через желоб 3, который в процессе заливки металла перемещается, что обеспечивает получение равностенной отливки 5. Для образования раструба трубы используют песчаный или оболочковый стержень 8. После затвердевания металла готовую отливку извлекают специальным приспособлением.
Скорость вращения формы зависит от диаметра отливки и плотности сплава, определяется по формуле:
,
где: – плотность сплава;
– внутренний радиус отливки.
Центробежным литьем изготавливают отливки из чугуна, стали, сплавов титана, алюминия, магния и цинка (трубы, втулки, кольца, подшипники качения, бандажи железнодорожных и трамвайных вагонов).
Масса отливок от нескольких килограммов до 45 тонн. Толщина стенок от нескольких миллиметров до 350 мм. Центробежным литьем можно получить тонкостенные отливки из сплавов с низкой текучестью, что невозможно сделать при других способах литья.
Недостаток: наличие усадочной пористости, ликватов и неметаллических включений на внутренних поверхностях; возможность появления дефектов в виде продольных и поперечных трещин, газовых пузырей.
Преимущества – получение внутренних полостей трубных заготовок без применения стержней, экономия сплава за счет отсутствия литниковой системы, возможность получения двухслойных заготовок, что получается поочередной заливкой в форму различных сплавов (сталь – чугун, чугун – бронза).
Используют автоматические и многопозиционные карусельные машины с управлением от ЭВМ.
Литье под давлением
Литьем под давлением получают отливки в металлических формах (пресс-формах), при этом заливку металла в форму и формирование отливки осуществляют под давлением.
Отливки получают на машины литья под давлением с холодной или горячей камерой прессования. В машинах с холодной камерой прессования камеры прессования располагаются либо горизонтально, либо вертикально.
На машинах с горизонтальной холодной камерой прессования (рис. 7.1) расплавленный металл заливают в камеру прессования 4 (рис. 7.1.а). Затем металл плунжером 5, под давлением 40…100 МПа, подается в полость пресс-формы (рис.7.1.б), состоящей из неподвижной 3 и подвижной 1 полуформ. Внутреннюю полость в отливке получают стержнем 2. После затвердевания отливки пресс-форма раскрывается, стержень 2 извлекается (рис. 7.1.в) и отливка 7 выталкивателями 6 удаляется из рабочей полости пресс-формы.
Рис.7.1. Технологические операции изготовления отливок на машинах с горизонтальной холодной камерой прессования
Перед заливкой пресс-форму нагревают до 120…320 0C. После удаления отливки рабочую поверхность пресс-формы обдувают воздухом и смазывают специальными материалами для предупреждения приваривания отливки. Воздух и газы удаляются через каналы, расположенные в плоскости разъема пресс-формы или вакуумированием рабочей полости перед заливкой металла. Такие машины применяют для изготовления отливок из медных, алюминиевых, магниевых и цинковых сплавов массой до 45 кг.
На машинах с горячей камерой прессования (рис. 7.2) камера прессования 2 расположена в обогреваемом тигле 1 с расплавленным металлом. При верхнем положении плунжера 3 металл через отверстие 4 заполняет камеру прессования. При движении плунжера вниз отверстие перекрывается, сплав под давлением 10…30 МПа заполняет полость пресс-формы 5. После затвердевания отливки плунжер возвращается в исходное положение, остатки расплавленного металла сливаются в камеру прессования, а отливка удаляется из пресс-формы выталкивателями 6.
Получают отливки из цинковых и магниевых сплавов массой от нескольких граммов до 25 кг.
Рис.7.2. Схема изготовления отливки на машинах с горячей камерой прессования
При литье под давлением температура заливки сплава выбирается на 10…20 0C выше температуры плавления.
Литье под давлением используют в массовом и крупносерийном производствах отливок с минимальной толщиной стенок 0,8 мм, с высокой точностью размеров и малой шероховатостью поверхности, за счет тщательного полирования рабочей полости пресс-формы, без механической обработки или с минимальными припусками, с высокой производительностью процесса.
Недостатки: высокая стоимость пресс-формы и оборудования, ограниченность габаритных размеров и массы отливок, наличие воздушной пористости в массивных частях отливки.
Дефекты отливок и их исправление
Дефекты отливок по внешним признакам подразделяют: на наружные (песчаные раковины, перекос недолив); внутренние (усадочные и газовые раковины, горячие и холодные трещины),
Песчаные раковины – открытые или закрытые пустоты в теле отливки, которые возникают из-за низкой прочности формы и стержней, слабого уплотнения формы и других причин.
Перекос –смещение одной части отливки относительно другой, возникающее в результате небрежной сборки формы, износа центрирующих штырей, несоответствия знаковых частей стержня на модели и в стержневом ящике, неправильной установке стержня.
Недолив –некоторые части отливки остаются незаполненными в связи с низкой температурой заливки, недостаточной жидкотекучести, недостаточным сечением элементов литниковой системы.
Усадочные раковины –открытые или закрытые пустоты в теле отливки с шероховатой поверхностью и грубокристаллическим строением.
Возникают при недостаточном питании массивных узлов, нетехнологичной конструкции отливки, заливки перегретым металлом, неправильная установка прибылей.
Газовые раковины –открытые или закрытые пустоты с чистой и гладкой поверхностью, которая возникает из-за недостаточной газопроницаемости формы и стержней, повышенной влажности формовочных смесей и стержней, насыщенности расплавленного металла газами.
Трещины горячие и холодные – разрывы в теле отливки, возникающие при заливке чрезмерно перегретым металлом, из-за неправильной конструкции литниковой системы, неправильной конструкции отливок, повышенной неравномерной усадки, низкой податливости форм и стержней.
Методы обнаружения дефектов
Наружные дефекты отливок обнаруживаются внешним осмотром после извлечения отливки из формы или после очистки.
Внутренние дефекты определяют радиографическими или ультразвуковыми методами дефектоскопии.
При использовании радиографических методов (рентгенография, гаммаграфия) на отливки воздействуют рентгеновским или гамма-излучением. С помощью этих методов выявляют наличие дефекта, размеры и глубину его залегания.
При ультразвуковом контроле ультразвуковая волна, проходящая через стенку отливки при встрече с границей дефекта (трещиной, раковиной) частично отражается. По интенсивности отражения волны судят о наличие, размерах и глубине залегания дефекта.
Трещины выявляют люминесцентным контролем, магнитной или цветной дефектоскопией.
![]() |
.
Вид обработки | Схема обработки | Характеристика отливок | Преимущества | Недостатки |
Центробежное литье | ![]() | отливки из чугуна, стали, сплавов титана, алюминия, магния и цинка (трубы, втулки, кольца, подшипники качения, бандажи железнодорожных и трамвайных вагонов).Масса отливок от нескольких килограммов до 45 тонн. Толщина стенок от нескольких миллиметров до 350 мм. | 1. получение внутренних полостей трубных заготовок без применения стержней, 2. экономия сплава за счет отсутствия литниковой системы, 3. возможность получения двухслойных заготовок, что получается поочередной заливкой в форму различных сплавов (сталь – чугун, чугун – бронза). | 1.наличие усадочной пористости, ликватов и неметаллических включений на внутренних поверхностях; 2 возможность появления дефектов в виде продольных и поперечных трещин, газовых пузырей |
Литье в металлической форме | ![]() | изготовление отливок из расплавленного металла в металлических формах-кокилях. | Все операции технологического процесса литья в кокиль механизированы и автоматизированы. Используют однопозиционные и многопозиционные автоматические кокильные машины. | кокильного литья: высокая трудоемкость изготовления кокилей, их ограниченная стойкость, трудность изготовления сложных по конфигурации отливок. |
Литье по выплавляемой модели | ![]() | Получение отливок из расплавленного металла в формах, рабочая полость которых образуется благодаря удалению легко плавного материала модели при ее предварительном нагревании | Обеспечивает получение точных и сложных отливок из различных сплавов массой 0.2…15 кг с толщиной стенки 0.5…5 мм | сложность и длительность процесса производства отливок, применение специальной дорогостоящей оснастки. |
Литье в оболочковой форме | ![]() | Получение отливок из расплавленного металла в формах, изготовленных по горячей модельной оснастке из песчано - смоляных смесей | повышенная точность отливок и хорошее качество ее поверхности процесс хорошо автоматизируется облегчение условия труда рабочих | ограниченность применения- массой отливок до 50…60 кг дороговизна использованных смесей из - за высокой стоимости смолы |
Литье под давлением | ![]() | Получают отливки в металлических формах. При Литье под давлением температура заливки сплава выбирается на 10…20 градусов | Литье под давлением используют в массовом и крупносерийном производствах отливок с минимальной толщиной стенок 0,8 мм, с высокой точностью размеров и малой шероховатостью поверхности, за счет тщательного полирования рабочей полости пресс-формы, без механической обработки или с минимальными припусками, с высокой производительностью процесса. | Высокая стоимость пресс-формы и оборудования, ограниченность размеров и массы отливок, наличие воздушной пористости в массовых частях отливок |
Вывод: Я изучил специальные способы литья и возможность применения этих способов для литья различных металлов и сплавов
ПРАКТИЧЕСКАЯ РАБОТА 3
Холодная листовая штамповка
Цель работ
Изучить основные операции холодной листовой штамповки, оборудование и инструмент
Задание:
1 Ознакомиться с методическими указаниями
2 Ответить на контрольные вопросы.
3 Составить отчет
Методические указания
Сущность холодной листовой штамповки
Холодной листовой штамповкой называют способ получения изделий плоской и объемной формы с помощью специального оборудования из листов, полос и лент металла, не подвергаемых нагреву.
Для холодной листовой штамповки используют листовые и полосовые заготовки из низкоуглеродистой стали и из цветных сплавов, которые являются продукцией прокатного производства. При этом листы имеют ширину от 1000 до 5000 мм и толщину от 4 до 10 мм, а полосы имеют ширину от 500 до 2500 мм с толщиной от 1,5 до 10 мм.
Достоинством холодной обработки давлением являются высокие точность и чистота поверхности изделий при обеспечении высокой производительности труда.
К недостаткам можно отнести низкую стойкость инструмента из-за больших нагрузок.
Основным оборудованием для холодной листовой штамповки являются прессы (механические и гидравлические), а инструментом штампы различного назначения.
Операции листовой штамповки можно разделить на две группы:
− разделительные, в результате которых происходит полное отделение одной части заготовки от другой;
− формоизменяющие, в результате которых путем пластической
деформации исходной заготовки получают изделия, имеющие про странственную форму.
ОТЧЕТ ПО ПРАКТИЧЕСКИМ РАБОТАМ
по дисциплине Горячая обработка материалов и упрочняющие
технологии
Специальность: 15.02.04 «Специальные машины и устройства»
.
Выполнил: студент гр. Зверев А.М Принял:
__________(______________) _______Семирикова Н.Г.
(подпись) (подпись)
«___»_______________20__г. «___»_______________20__г.
Ковров 2022
ЛАБОРАТОРНАЯ РАБОТА 1
|
|
Организация стока поверхностных вод: Наибольшее количество влаги на земном шаре испаряется с поверхности морей и океанов (88‰)...
Эмиссия газов от очистных сооружений канализации: В последние годы внимание мирового сообщества сосредоточено на экологических проблемах...
Механическое удерживание земляных масс: Механическое удерживание земляных масс на склоне обеспечивают контрфорсными сооружениями различных конструкций...
Историки об Елизавете Петровне: Елизавета попала между двумя встречными культурными течениями, воспитывалась среди новых европейских веяний и преданий...
© cyberpedia.su 2017-2024 - Не является автором материалов. Исключительное право сохранено за автором текста.
Если вы не хотите, чтобы данный материал был у нас на сайте, перейдите по ссылке: Нарушение авторских прав. Мы поможем в написании вашей работы!