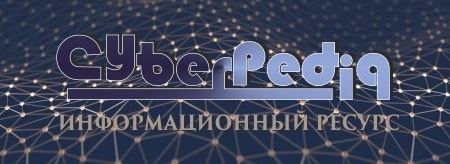
Архитектура электронного правительства: Единая архитектура – это методологический подход при создании системы управления государства, который строится...
Биохимия спиртового брожения: Основу технологии получения пива составляет спиртовое брожение, - при котором сахар превращается...
Топ:
Характеристика АТП и сварочно-жестяницкого участка: Транспорт в настоящее время является одной из важнейших отраслей народного хозяйства...
Установка замедленного коксования: Чем выше температура и ниже давление, тем место разрыва углеродной цепи всё больше смещается к её концу и значительно возрастает...
Комплексной системы оценки состояния охраны труда на производственном объекте (КСОТ-П): Цели и задачи Комплексной системы оценки состояния охраны труда и определению факторов рисков по охране труда...
Интересное:
Лечение прогрессирующих форм рака: Одним из наиболее важных достижений экспериментальной химиотерапии опухолей, начатой в 60-х и реализованной в 70-х годах, является...
Влияние предпринимательской среды на эффективное функционирование предприятия: Предпринимательская среда – это совокупность внешних и внутренних факторов, оказывающих влияние на функционирование фирмы...
Уполаживание и террасирование склонов: Если глубина оврага более 5 м необходимо устройство берм. Варианты использования оврагов для градостроительных целей...
Дисциплины:
![]() |
![]() |
5.00
из
|
Заказать работу |
СОДЕРЖАНИЕ
Введение_______________________________________________________7
1. Общая часть_________________________________________________10
1.1.Назначение установки каталитическогориформинга для
производства компонентов современных бензинов_____________________10
1.2. Характеристика существующих установок и методов
каталитического риформинга_______________________________________11
1.3.Особенности процесса каталитического риформинга____________13
2. Технологическая часть_______________________________________16
2.1.Технологическая схема работы установки каталитическогориформинга со стационарным катализатором __________________________16
2.2. Химизм процесса каталитического риформинга_______________18
2.3.Реакции каталитическогориформинга________________________20
2.4 Катализаторы каталитическогориформинга___________________35
2.5. Факторы влияющие на работу установки каталитического риформинга_______________________________________________________42
3.Расчетная часть______________________________________________45
3.1 Расчет материального баланса каталитического риформинга______________________________________________________45
3.2 Ректификационнаяколонна________________________________48
3.3 Трубчатаяпечь___________________________________________53
4.Охрана труда_________________________________________________59
4.1. Техника безопасности при работе установки каталитическогориформинга_______________________________________________________ 59
4.2Электробезопасность_______________________________________62
Изм. |
Лист |
№ докум. |
Подпись |
Дата |
Лист |
5 |
ДП 5.05130103 10 – 1Т 2014 ПЗ |
Разраб. |
Гулько. В.М. |
Провер. |
Федоров Н.А |
Консультант |
Овсова Г.В, |
Каталитическийриформинг тяжелой бензиновой фракции |
Лит. |
Листов |
ТГНП ОНАПТ |
Экономическаячасть
5.1 Расчет расходов на сырье__________________________________64
5.2 Расчет затрат на материалы________________________________65
5.3 Расчет дохода зароботной платы_____________________________66
5.4 Отчисление ЕСВ в Пенсионный фонд_________________________67
5.5 Расчет амортизационных отчислений_________________________67
5.6 Расчет отчислений в ремонтный фонд_________________________68
5.7 Расчет прочих денежных расходов ___________________________68
5.8 Расчет себестоимости переработки 1т тяжелой бензиновой
фракции_____________________________________________________69
6.Выводы________________________________________________
6.1.Результаты дипломного проекта
7. Использованнаялитератур а_________________________________
Графическая часть
Установка каталитическогориформинга со стационарным катализатором. Технологическая схема. Лист А1
Р ектификационная колонна. Сборочный чертеж Лист А1
Т рубчатаяпечь. Сборочный чертеж Лист А1
ВВЕДЕНИЕ
Переработка нефти начинается с перегонки или фракционирования сырой нефти в отдельные углеводородные группы. Полученные в результате продукты
непосредственно связаны с характеристиками обрабатываемой сырой нефти. Большая часть этих продуктов перегонки далее преобразуются в более полезныепродуктыпутем изменения их физических свойств и структур молекул под действием крекинга, реформинга и других процессов преобразования. Эти продуктыпоследовательно подвергаются различным процессам очистки и разделения, таким как извлечение, гидроочистка и очистка от активной серы, с цельюобразования конечных продуктов. В то время как самые простые операции по нефтепереработке обычно ограничиваются атмосферной и вакуумной перегонкой,большие нефтеперерабатывающие заводы осуществляют фракционирование, преобразование, обработку и смешивание со смазочным материалом,производство тяжелого топлива и асфальта; они могут также производить обработку нефтепродуктов.
Первый нефтеперерабатывающий завод, который открылся в 1861, производил керосин путем простой атмосферной перегонки. Побочными продуктами былигудрон и нефть (сырая нефть). Вскоре было обнаружено, что высококачественные смазочные материалы могут быть произведены путем перегонки нефти ввакууме. Однако, на протяжении следующих 30 лет керосин был тем продуктом, который потребители хотели иметь больше всего. Два наиболее значимыхсобытия, которые изменили данную ситуацию, были:
· Изобретение двигателя внутреннего сгорания создало спрос на дизельное топливо и бензин.
С появлением массового производства и первой мировой войны резко увеличило число транспортных средств, использующих бензин и спрос на это топливо. Однако, только определенное количество бензина могло быть получено из сырой нефти с помощью процессов атмосферной и вакуумнойперегонки. Первый процесс термического крекинга был разработан в 1913 году. Термический крекинг подвергал тяжелое нефтяное сырье действию давления и высокой температуры, разделяя физически его большие молекулы на меньшие по размеру, производя дополнительный бензин и дистиллятные топлива. Сложнаяформа термического крекинга, легкого крекинга была разработана в конце1930-ых годов с целью получения более желанных и ценных продуктов.
Когда были разработаны бензиновые двигатели с более высоким сжатием, появился спрос на бензин с более высоким октановым числом, имеющий лучшиеантидетонационные характеристики. Внедрение процессов каталитического крекинга и полимеризации в середине-конце 1930-х удовлетворило этот спрос путемобеспечения повышенного выхода бензина с более высокими октановыми числами. Алкилирование, другой каталитический процесс, был разработан в начале1940-ых для производства авиационного бензина с более высоким октановым числом и использование исходного сырья нефтепродуктов, начальных материаловдля взрывчатых веществ и синтетического каучука. Впоследствии был разработан процесс каталитической изомеризации, преобразующий углеводороды сцелью производства повышенных количеств исходного сырья для алкилирования.
После Второй мировой войны были внедрены различные процессы риформинга, которые улучшили качество и выпуск бензина, и произвели продукты болеевысокого качества. Некоторые из них использовали катализаторы и водород с целью изменения молекул и удаления серы. Улучшенные катализаторы итехнологические методы, такие как гидрокрекинг и риформинг, создавались на протяжении 1960-ых с целью увеличения выпуска бензина и улучшения егоантидетонационных характеристик. В каталитические процессы также производили молекулы с двойной связью (алкены), формируя основы современнойнефтехимической промышленности.
Число и типы различных процессов, используемых на современных нефтеперерабатывающих заводах, зависят, прежде всего, от природы исходного сырьясырой нефти и требований к конечному продукту. На процессы также оказывают влияние экономические факторы, включая стоимость сырой нефти, стоимостипродуктов, наличие коммунальных услуг и транспорта.
Каталитический риформинг - это процесс каталитического превращения под давлением водорода низкооктановых тяжелых бензиновых фракций в продукты, содержащие большое количество простых ароматических и изоалканових углеводородов. Риформинг предназначено для улучшения антидетонационных свойств бензинов и производства большого количества ароматических углеводородов (бензола, толуола, ксиолу), которые применяются в химической промышленности. При каталитическомриформинга производят газообразные продукты, содержащие до 80-90% по объему водорода, общий выход которого составляет 1.7-2% веса сырья. Водород применяется для установок гидроочистки, что значительно улучшает экономические показатели процесса риформинга. Улучшение детонационных свойств бензинов позволяет применить их на двигателях с повышенной степенью сжатия, улучшает к.п.д. снижает расход топлива, дает возможность создавать мощные, форсированные малогабаритные двигатели. Современные автомобильные бензины имеют октановое число по исследовательскому методу около 100 ед.
Каталитическийриформинг бензинов является важнейшим процессом современной нефтепереработки и нефтехимии. Он служит для одновременного получения высокооктанового базового компонента автомобильных бензинов, ароматических углеводородов - сырья для нефтехимического синтеза - и водородосодержащего газа - технического водорода, используемого в гидрогенизационных процессах нефтепереработки. Каталитическийриформинг является в настоящее время наиболее распространенным методом каталитического облагораживания прямогонных бензинов. Установки каталитическогориформинга имеются практически на всех отечественных и зарубежных нефтеперерабатывающих заводах.
Бензины являются одним из основных видов горючего для двигателей современной техники. Автомобильные и мотоциклетные, лодочные и авиационные поршневые двигатели потребляют бензины. В настоящее время производство бензинов является одним из главных в нефтеперерабатывающей промышленности и в значительной мере определяющим развитие этой отрасли.
Развитие производства бензинов связано со стремлением улучшить основное эксплуатационное свойство топлива - детонационную стойкость бензина, оцениваемую октановым числом.
ОБЩАЯ ЧАСТЬ
ТЕХНОЛОГИЧЕСКАЯ ЧАСТЬ
2.1 Технологическая схема работы установки каталити- ческогориформинга со стационарным катализатором
Исходное сырье подается насосом 21 на смешение с циркулирующим газом гидроочистки и избыточным водородом риформинга. Полученная газосырьевая смесь после нагрева в теплообменнике 10 и печи 12 поступает в реактор гидроочистки 11. Далее смесь газа и гидроочищенного бензина отдает свою теплоту в кипятильнике 22, теплообменнике 10, холодильнике 8 и направляется в сепаратор высокого давления гидроочистки 9, где газ отделяется от гидрогенизата. В водородсодержащем газе присутствует сероводород, выделяющийся при гидроочистке. Из сепаратора газ поступает в колонну 2, где сероводород отмывается 15 %-ным раствором моноэтаноламина.
Очищенный газ разделяется на две неравные части: большая — циркуляционный газ гидроочистки — поступает на прием циркуляционного компрессора 6 и вновь смешивается с сырьем, меньшая — избыточный водород — выводится с установки. Жидкая фаза в сепараторе 9 содержит гидроочищенный бензин с растворенными в нем сероводородом, углеводородным газом и водой. Поэтому гидрогенизат поступает через теплообменник 23 в отпарную колонну 7, где происходит отпарка газа, воды и сероводорода от бензина за счет теплоты потока из реактора 11, подводимого в кипятильник 22.
Стабильный гидрогенизат с низа колонны 7 проходит теплообменник 23 и насосом 24 направляется на смешение с циркулирующим водородом блока платформинга. Смесь бензина и газа нагревается в теплообменнике 25 и во второй секции печи 12, а затем последовательно проходит реактор 13, третью секцию печи 12, реактор 14, четвертую секцию печи 12 и реактор 15.
Продукт риформинга из реактора 15 направляется в теплообменник 25 и холодильник 26, охлаждается и поступает в сепаратор высокого давления платформинга 27, где происходит разделение газа и бензина.
Газ поступает на прием компрессора 28. Большая часть его возвращается на смешение с гидрогенизатом, а избыточный водород платформинга направляется в блок гидроочистки. Жидкий продукт из сепаратора 27 попадает в сепаратор низкого давления 29, где из платформата выделяется растворенный углеводородный газ. Окончательно платформат стабилизируется в колоннах 16 и 20. Углеводородный газ гидроочистки и риформинга из сепараторов 3 и 29 смешивается и подается во фракционирующий абсорбер 16.Нестабильный бензин из сепаратора 29 двумя потоками поступает в абсорбер 16: часть холодного бензина подается на верх абсорбера, другая часть нагревается в теплообменнике 30 и подается в низ абсорбера. С верха абсорбера 16 уходит сухой углеводородный газ, с низа — бензин в колонну стабилизации 20 после предварительного нагрева в теплообменнике 34 за счет стабильного бензина. С верха колонны 20 с установки выводится головка стабилизации, с низа колонны 20 через теплообменники 30 и 34 и холодильник 33 — стабильный бензин. Подвод теплоты в низ колонн 16 и 20 осуществляется методом горячей струи через двухкамерную печь 32. При полном выделении из бензина этана (режим деэтанизации) в верху колонны 20 поддерживается 70 °С, при полном удалении пропана (режим депропанизации) — 45 °С. В обоих случаях температура низа колонны 220 °С, давление 11,5МПа.
В качестве сырья для каталитического риформинга обычно используют бензиновые фракции первичной перегонки нефти. Пределы выкипания этих фракций колеблются в широком интервале— от 60 до 210°С. Для получения ароматических углеводородов в большей части используют фракции, выкипающие при 60— 105 или при 60—140°С, а для получения высокооктановых автомобильных бензинов — фракции 85—180 °С. Иногда широкую фракцию, выделяемую на установке первичной перегонки нефти, дополнительно разгоняют на более узкие фракции на установках вторичной перегонки. Однако раздельный каталитическийриформинг бензиновых фракций имеет некоторые преимущества:-большая продолжительность работы катализатора без регенерации,-лучшаяманевренность в работе и т. д. Поэтому выбор того или иного варианта получения высокооктанового бензина определяется с учетом конкретных условий работы нефтеперерабатывающего завода. Весьма важно учитывать возможность и целесообразность получения ароматических углеводородов.
2.2Химизм процесса каталитического риформинга Каталитический риформинг — сложный процесс, включающий разнообразные превращения углеводородов. Прямогонные бензиновые фракции, служащие сырьем каталитическогориформинга, содержат парафиновые, нафтеновые и ароматические углеводороды. В результате рёакцийт протекающих на катализаторах риформинга, происходят глубокие изменения углеводородного состава. Ароматизация углеводородов является основным и важнейшим направлением процесса. Перед тем как рассмотреть основные реакции, протекающие при каталитическом риформинге, необходимо отметить, что катализаторы риформинга отличаются наличием двух видов каталитически активных центров: дегидрирующихгидрирующих центров на платине и изомеризующих и расщепляющих кислотных центов на носителе.Одна из основных реакций процессадегидрирование (дегидрогени-зация) нафтеновых углеводородов.
Дегидрирование пятичленных нафтеновых углеводородов идет через образование циклоолефиновых углеводородов с перестройкой кольца.
Второй основной реакцией является дегидроциклизация парафиновых углеводородов; механизм этой реакции еще не совсем ясен. Ароматизация парафиновых углеводородов возможна как через образование нафтеновых, так и через образование олефиновых и циклоолефиновых углеводородов.
К основным реакциям процесса также относится изомеризация парафиновых углеводородов, которая протекает через промежуточную стадию образования ионов карбония; в условиях риформинга изомеризация приводит к образованию малоразветвленных изомеров. Параллельно с этими реакциями на катализаторах риформинга идут реакции гидрокрекинга. Гидрокрекингу подвергаются парафиновые углеводороды и, в меньшей степени, нафтеновые. Гидрокрекинг парафинов идет в несколько стадий через образование и распад карбониевых ионов. Среди продуктов : реакции превалирует, пропан и более высокомолекулярные углеводороды. Гидрокрекинг протекает на кислотных центрах катализатора, однако начальная и конечная стадия процесса— образование олефинов и гидрирование продуктов распада — протекают на металлических участках катализатора, которым свойственна функция «гидрированиядегидрирования». Гидрокрекинг парафиновых углеводородов приводит к образованию двух и более углеводородов с меньшей молекулярной массой.
В некоторых случаях заметное развитие в процессе риформинга получает реакция гидрогенолиза, протекающая на металлических участках катализатора. В отличие от гидрокрекинга гидрогенолиз ведет к преимущественному образованию газообразных углеводородов, особенно метана. При гидрогенолизе разрыв углеродуглеродных связей метилциклопентана приводит к образованию парафиновых углеводородов. Кроме того, в условиях риформинга протекают реакции, оказывающие существенное воздействие на активность и стабильность .катализаторов; к, ним относятся реакции, приводящие к образованию кокса на катализаторе, а также реакции гидроразложения сернистых, азотистых и хлорсодержащих соединений.
Процесс образования кокса связан с протеканием реакций уплотнения на поверхности катализатора. З^го обусловливает не только снижение активности катализатора, но и ухудшение селективности процесса. Коксообразованию способствует понижение "парциального давления водорода и мольного отношения водород/сырье, отравление катализатора контактными ядами, нарушение баланса гидрирующей и кислотной функцией катализатора, переработка сырья с повышенным содержанием легких (С5—С6), а также присутствие тяжелых (выше С10) углеводородов.
Среди основных реакций риформинга с наибольшей скоростью протекает реакция дегидрирования алкилциклогексанов в соответствующие ароматические углеводороды, с наименьшей — дегидроциклизация парафиновых углеводородов.Скорости конверсии нафтеновых и парафиновых углеводородов С6—С10 возрастают в гомологических рядах с увеличениеммолекулярной массы.Реакции риформинга, ведущие к образованию ароматических углеводородов из нафтеновых и парафиновых, идут с поглощением теплоты; реакции гидрокрекинга и гидрогенолиза — с выделением теплоты; реакции изомеризации парафиновых и нафтеновых углеводородов имеют слабовыраженный тепловой эффект. Для углеводородов С6—С10 мольные тепловые эффекты почти не зависят от молекулярной массы и мало изменяются в температурном интервале 470—500 °С.
Реакции дегидрирования
Дегидрирование шестичленных нафтенов - основное направление их превращения в условиях каталитического риформинга. Скорости дегидрирования шестичленных нафтенов на платиновых катализаторах риформинга весьма велики и намного превышают скорости их дегидрирования на других металлических и оксидных катализаторах, показанную в таблице 2.
Таблица 2 − Сравнительная активность катализаторов в реакции дегидрирования циклогексана.
Катализатор | * r, моль/(г с) | Катализатор | * r, моль/(г с) |
34% Сr2O3/Al2O3 | 0,5 | 1% Pd/Al2O3 | 200 |
10% MoO3/Al2O3 | 3 | 5% Ni/SiO2 | 320 |
5% Ni/Al2O3 | 13 | 1% Rh/Al2O3 | 890 |
5% Co/Al2O3 | 13 | 0.5 Pt/Al2O3 | 1400-4000 |
Достаточно отметить, что скорость дегидрирования циклогексана на платиновых катализаторах в 500-1300 раз больше скорости той же реакции на алюмомолибденовом катализаторе, который сравнительно недавно еще применялся в процессе риформинга бензиновых фракций. При таких скоростях реакции степень дегидрирования шестичленных нафтенов может в значительной мере предопределяться условиями химического равновесия для той реакции.
Химическое равновесие. Реакции дегидрирования шестичленных нафтенов в ароматические углеводороды обратимы, формула 9
(9)
Зная константу равновесия Кр, можно вычислить равновесные концентрации реагирующих веществ, формула 10
(10)
Ниже приведены логарифмы констант равновесия для реакций дегидрирования циклогексана и некоторых его гомологов при температурах от 400 до 550 °С, таблица 3
Таблица 3 – Логарифмы констант равновесия для реакций дегидрирования циклогексана и некоторых его гомологов
Углеводороды | 408 °С | 450 °С | 500 °С | 550 °С |
Циклогексан | 3,70 | 4,88 | 5,91 | 6.82 |
Метилциклогексан | 4,19 | 5,36 | 6,33 | 7,28 |
Этилциклогексан | 4,23 | 5.36 | 6,34 | - |
н – Пропилциклогексан | 4,26 | 5,39 | 6,37 | - |
1, 2, 4 – Триметилциклогексан | 5,11 | - | - | - |
Константы равновесия для реакций дегидрирования гомологов циклогексана с одной алкильной группой (метилциклогексана, этилциклогексана, н-пропилциклогексана), при одинаковой температуре, значительно больше соответствующей константы для реакции дегидрирования циклогексана. Дальнейший рост константы равновесия идет при наличии нескольких замещающих алкильных групп в молекуле циклогексана (1,2,4-триметилциклогексан). Из этих данных можно заключить, что равновесие для реакций дегидрирования гомологов циклогексана сдвинуто в сторону ароматических углеводородов в большей степени, чем для циклогексана. Следовательно, условия, обеспечивающие полноту дегидрирования цикдогексана, в полной мере обеспечат также возможность исчерпывающего дегидрирования его гомологов.
Наибольшей полноте дегидрирования углеводородов способствуют высокие температуры и низкие давления водорода. При прочих равных условиях степень дегидрирования циклогексана существенно меньше, чем метилциклогексана. Так, при 425 °С и парциальном давлении водорода 2 МПа молярное содержание бензола в равновесной смеси углеводородов равна 68%, а толуола 81%, рисунок 2.
Рисунок 1 − Зависимость содержания бензола и толуола в равновесной смеси с циклогексаном от температуры и парциальном давления водорода
Пользуясь кривыми на рисунке 2, можно определить степень превращения шестичленных нафтенов в условиях каталитического риформинга. Обычно процесс проводят в реакционном блоке, состоящем из трех-четырех реакторов, работающих в условиях, близких к адиабатическим. При наиболее широко применяемых параметрах (температура на входе в реакторы около 500°С, давление от 1,5 до 3 МПа, молярное отношение водород: сырье = 6-7), вследствие эндотермичности процесса температура газосырьевой смеси понижается в первом по ходу сырья реакторе на 40-60°С, т. е. до 460-440°С. Степень дегидрирования шестичленных нафтенов в первом по ходу сырья реакторе может достигнуть или превысить 90%.
Реакции изомеризации
При изомеризации на бифункциональных металлических катализаторах, в том числе на платиновых, шестичленные нафтены могут подвергаться следующим превращениям:
1) изомеризации шестичленного цикла в пятичленный
2) перемещению алкильных заместителей в кольце
3) изменению числа алкильных заместителей в цикле
Реакции изомеризации нафтенов протекают по карбкатионному механизму. Промежуточный продукт реакции - циклоолефин, образующийся в результате дегидрирования нафтена на металлическом участке катализатора. Циклоолефин мигрирует на кислотный участок носителя, где превращается в карбкатион. Реакции карбкатиона ведут к образованию изомерного циклоолефина, в результате гидрирования которого на металлическом участке получается углеводород, изомерный исходному. Так, схему изомеризации циклогексана в метилциклопентан можно представить как показано на рисунке 3 (М -металлические участки катализатора, А -кислотные)
Рисунок 3 − Схема изомеризации циклогексана в метилциклопентан
Третичный карбкатион наиболее устойчив и не всегда способен к перегруппировкам. Поэтому протеканию перегруппировок может способствовать образование менее устойчивого, но более реакционноспособного вторичного карбкатиона. Исходя из этого, перемещение алкильных заместителей в кольце цикдогексана можно представить в следующем виде как показано на рисунке 4
Рисунок 4 − Перемещение алкильных заместителей в кольце цикдогексана.
Реакции 1,2,3.
Реакции типа (1) и (2) протекают значительно легче, чем реакции (3), ведущие к увеличению числа алкильных заместителей в цикле. Так, скорость изомеризации этилциклогексана меньше по сравнению со скоростью изомеризации других шестичленных нафтенов состава C8. Косвенным подтверждением служат результаты, полученные при каталитическомриформинге бензиновой фракции, состоящей из углеводородов С8 и обогащенной этилциклогексаном. Относительные количества ксилолов в катализате отвечали равновесию. Что же касается этилбензола, то выход его соответствовал содержанию этилцикдогексана в сырье и намного превышал равновесное содержание в смеси ароматических углеводородов состава С8.
Предложена схема изомеризации этилциклогексана в диметилциклогексаны, в соответствии с которой циклопентановые углеводороды являются промежуточными продуктами реакции, формула 14
(14)
Были изучены превращения метилциклогексана на платиновом катализаторе в условиях, при которых углеводород подвергался как изомеризации, так и дегидрированию (452°С, 4,9 МПа, подача углеводорода 2 ч-1, отношение водород углеводород = 6,6). Выход, в моль (на 100 моль метилциклогексана) составил
Таблица 4 − Превращения метилциклогексана на платиновом катализаторе
Углеводороды С1—С6 | 6 |
Алкилциклопентаны (1,1-, 1,2- и 1,3 диметилциклопентаны + этилциклопентан) | 31 |
Метилциклогексан (непревращенный) | 6 |
Толуол | 56 |
Другие углеводороды | 1 |
Таким образом, количество алкилциклопентанов в продуктах реакции в 5 раз превышало количество метилциклогексана.
Равновесие для реакции изомеризации циклогексана при 460-500 °С целиком сдвинуто в сторону метилциклопентана (содержание его в равновесной смеси с циклогексаном 93-94%). С другой стороны, при этих же температурах и парциальном давлении водорода до 2 МПа равновесие для реакции дегидрирования циклогексана также сильно смещено в сторону бензола. В этих условиях избирательность превращения циклогексана и других шестичленных нафтенов предопределяется относительными скоростями их дегидрирования и изомеризации, В соответствии с изложенным выше механизмом этих реакций, схему превращения циклогексана в бензол и метилциклопентан можно представить в следующем виде, как показано на рисунке 5
Рисунок 5 − схема превращения циклогексана в бензол
При чрезмерной кислотности катализатора скорости образования бензола и метилциклопентана становятся соизмеримыми, что должно привести к снижению селективности ароматизации циклогексана. Иллюстрацией подобного эффекта могут служить данные, полученные при каталитическом риформинге смеси этилциклогексана и диметилциклогексанов на двух типах платиновых катализаторов (495°С, 2МПа), таблица 5
Таблица 5 − каталитическийриформинг смеси этилциклогексана и диметилциклогексанов на двух типах платиновых катализаторов
Степень превращения, % | Селективность ароматизации, % | |
Стандартный катализатор риформинга | 97 | 97 |
Катализатор с высокой кислотностью | 94 | 65 |
При близкой степени превращения сырья селективность его ароматизации оказалась значительно ниже при осуществлении процесса на платиновом катализаторе с высоким уровнем кислотности.
Обычно скорость ароматизации циклогексана значительно больше скорости его изомеризации на алюмоплатиновом катализаторе (приблизительно на два порядка).
Исходя из относительных скоростей дегидрирования и изомеризации циклогексана можно было ожидать, что наибольшая селективность его превращения в бензол будет достигнута при больших объемных скоростях пропускания углеводорода.В промышленных условиях в первом по ходу сырья реакторе обычно поддерживают объемную скорость подачи сырья в пределах 10-15 ч-1, что способствует селективному превращению шестичленных нафтенов в ароматические углеводороды.
Дегидроизомеризация
Дегидроизомеризацияметилциклопентана явилась предметом многих исследований. Значительно меньше данных о том, как протекает эта реакция при превращении других алкилциклопентанов.
Изучалась дегидроизомеризацияалкилциклопентанов С7-С9 на алюмоплатиновом катализаторе в мягких условиях (350 °С; 0,5 МПа), при которых реакция протекает достаточно селективно, а состав и строение получаемых ароматических углеводородов зависят от состава и строения исходных алкилциклопентанов.
Проведенные исследованиям показали, что преимущественное расширение циклопентанового кольца происходит за счет метиленовой, а не метильной группы, формула 15 (15)
Существует определенная взаимосвязь между расположением алкильных групп в алкилциклопентанах и получаемых ароматических углеводородах. Так, из 1,3-метилалкилциклопентанов получают главным образом мета-замещенные, а из 1,2-метилалкилциклопентанов орто-замещенные бензола, формула 16
(16)
Скорости дегидроизомеризации зависят от характера замещающих алкильных групп и их взаимного расположения в алкилциклопентанах. Вероятно эти зависимости играют определенную роль и для дегидроизомеризацииалкилциклопентанов при более высоких температурах (~500°С), свойственных процессу каталитического риформинга. Однако вследствие интенсивной изомеризации углеводородов в условиях этого процесса, состав образующихся алкилбензолов значительно меньше зависит от состава и строения исходных алкилциклопентанов. Например, если при дегидроизомеризации н-пропилциклопентана при 350 °С получают только этилбензол, то в случае осуществления реакции при 480°С, наряду с этим углеводородом образуются также изомеры ксилола.
Химическое равновесие. На рисунке 2 показано изменение состава равновесной смеси углеводородов в зависимости от температуры и парциального давления водорода для реакции, формула 17
(17)
1 − бензол; 2 − метилциклопентан; 3 − циклогексан
Рисунок 2 − Зависимость содержания бензола, циклогексана и метилциклопентана в их равновесной смеси при парциальном давлении водорода 1,9 МПа от температуры и 495°С от парциального давления водорода
Повышение температуры от 400 до 500 °С при постоянном Рн2 1,9 МПа ведет к значительному изменению концентрации метилциклопентана и бензола в равновесной смеси. При 400 °С равновесие сильно сдвинуто в сторону метилциклопентана, а при 500 °С - в сторону бензола.
Молярное содержание бензола в равновесной смеси при 495 °С увеличивается от 45 до 90% при снижении Риз от 3,6 до 1,5 МПа и возрастает при дальнейшем его уменьшении. Равновесное молярное содержание циклогексана весьма низко и при 495°С, в зависимости от значения Рн2 лежит в пределах от 1 до 3%. Это, однако, не препятствует быстрому протеканию реакции дегидроизомеризации, что обусловлено большой скоростью превращения циклогексана в бензол на платиновых катализаторах риформинга.
Таким образом, если дегидроизомеризациюметилциклопентана проводить при обычных температурах каталитического риформинга (~500 °С), достаточно полное превращение углеводорода в бензол может быть достигнуто при значении Рн2 не превышающем 1,5 МПа. Эти условия в равной мере благоприятны для дегидроизомеризации других пятичленных нафтенов.
Кинетика и механизм реакции.Кинетические закономерности реакции дегидроизомеризацииметилциклопентана были изучены как на алюмоплатиновом, так и на алюмоплатинорениевом катализаторах, не было обнаружено существенных различий в протекании реакции на этих катализаторах. При каталитическомриформингеметилциклопентана основными продуктами реакции являются бензол и гексаны, формула 18
(18)
В значительно меньших количествах образуются метилциклопентены, циклогексан, а также парафины С1-С5.
Независимо от того, проводят ли реакцию на алюмоплатиновом или адюмоплатинорениевом катализаторах выход метилциклопентенов закономерно уменьшается с увеличением степени превращения метилциклопентана. Следовательно, метилциклопентены служат одним из промежуточных продуктов реакции дегидроизомеризацииметилциклопентана.
Отношение МЦПа: МЦПе-величина постоянная и не зависит от степени превращения МЦПа, если температура и значение Pн2 постоянны.
На металлическом компоненте платинового катализатора риформинга происходит только дегидрирование метилциклопентана до соответствующихциклоолефинов. Превращение же метилциклопентена в бензол достигается в результате совместного действия металлического и кислотного компонентов. Поэтому исследование влияния каждого из компонентов катализатора на скорость реакции дегидроизомеризацииМЦПа может выявить, какая из стадий этой реакции - лимитирующая.
Поскольку промышленные катализаторы риформинга обычно содержат от 0,3 до 0,6% платины, следует прежде всего отметить, что изменение ее содержания в этих пределах практически не оказывает влияния на скорость дегидроизомеризацииметилциклопентана.Данные, полученные при использовании в качестве носителя фторированного оксида алюминия (0,77% F), показали, что степень превращения метилциклопентана в бензол увеличивается только при повышении содержания платины в катализаторе от 0,012 до 0,075%. По-видимому, при большем содержании платины устанавливается равновесная концентрация метилциклопентена и стадия дегидрирования метилциклопентана не влияет на скорость образования бензола.
Влияние кислотной функции катализатора можно проследить, изменяя в нем содержание галогена. При том содержании платины в катализаторе (0,3%), при котором стадия дегидрирования метилциклопентана не является лимитирующей, последовательное увеличение содержания фтора от 0,05 до 1,0% приводит к повышению выхода бензола в 2,8 раза. Это означает, что определяет скорость дегидроизомеризацииметилциклопентана стадия изомеризации метилциклопентена в циклогексан, протекающая на кислотных участках катализатора. Такое утверждение основано также на том, что дегидрирование циклогексена в бензол, как показано выше, протекает с чрезвычайно большой скоростью, а потому не может влиять на скорость превращения метилциклопентана в бензол.
Реакция дегидроизомеризацииметилциклопентана может быть схематически представлена следующим образом, рисунок 9
Рисунок 9 − Реакция дегидроизомеризацииметилциклопентана
Кислотно-катализируемая лимитирующая стадия реакции протекает по карбкатионному механи
Адаптации растений и животных к жизни в горах: Большое значение для жизни организмов в горах имеют степень расчленения, крутизна и экспозиционные различия склонов...
Организация стока поверхностных вод: Наибольшее количество влаги на земном шаре испаряется с поверхности морей и океанов (88‰)...
Архитектура электронного правительства: Единая архитектура – это методологический подход при создании системы управления государства, который строится...
Эмиссия газов от очистных сооружений канализации: В последние годы внимание мирового сообщества сосредоточено на экологических проблемах...
© cyberpedia.su 2017-2024 - Не является автором материалов. Исключительное право сохранено за автором текста.
Если вы не хотите, чтобы данный материал был у нас на сайте, перейдите по ссылке: Нарушение авторских прав. Мы поможем в написании вашей работы!